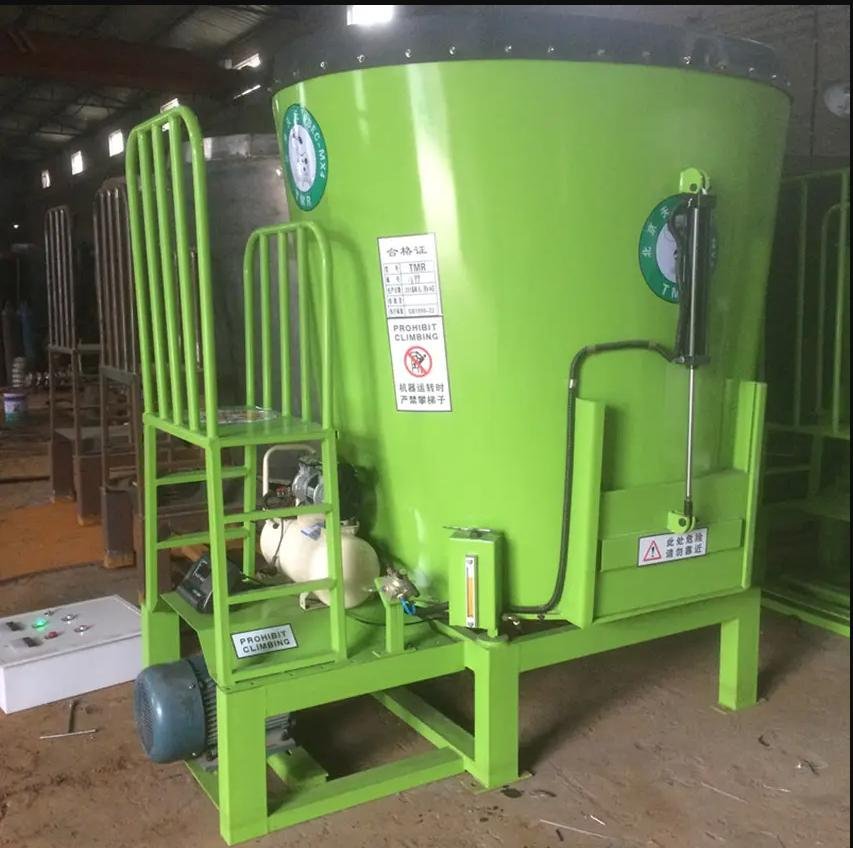
In the livestock industry, feed mixers play a crucial role, with their importance and wide-ranging applications evident in several aspects:
- Balanced Feed Mixing: Feed mixers ensure the balanced distribution of various nutrients in livestock feed by blending various raw materials. This is vital for the growth, health, and productivity of livestock. Through mixing, each portion of feed contains adequate protein, carbohydrates, vitamins, and minerals, meeting the nutritional needs of animals and enhancing production efficiency and economic benefits.
- Improved Feed Utilization: Feed mixers thoroughly blend various ingredients, making feed more uniform and aiding animals in more efficient digestion and absorption. This not only reduces feed waste and costs but also enhances feed utilization, conserving feed resources and lowering breeding costs.
- Animal Health Assurance: Balanced feed mixing ensures animals receive sufficient nutrition, enhancing their immunity and disease resistance while reducing disease incidence. Additionally, the high temperature and pressure during mixing effectively eliminate harmful microorganisms and pathogens in the feed, safeguarding animal health and reducing disease risks in breeding.
- Enhanced Production Efficiency: Using feed mixers for feed mixing significantly improves production efficiency. Compared to manual mixing, mechanical mixing is not only faster and more uniform but also saves time and effort. This is particularly crucial for large-scale breeding operations, as it effectively reduces labor costs, enhances production efficiency, and increases economic benefits.
- Applicable to Various Livestock: Feed mixers are suitable for poultry farming (such as chickens, ducks, and geese) and are widely used in the pig, cattle, and sheep industries. Whether it’s young animals during the growth phase or mature animals during the production phase, balanced feed mixing is essential to meet their different nutritional needs, making feed mixers indispensable equipment.
In conclusion, the importance of feed mixers in the livestock industry is self-evident. They not only improve feed balance and utilization, safeguard animal health, and enhance production efficiency but also meet the nutritional needs of different types of animals, playing an irreplaceable role in the development and economic benefits of the livestock industry. Therefore, the importance of purchasing and replacing feed mixer parts, especially key components like blades, is self-evident.
Importance of Purchasing and Replacing Feed Mixer Parts
Purchasing and replacing feed mixer parts, especially blades, are crucial because they directly affect the performance and production efficiency of the mixer. Blades, as critical components of feed mixers, have significant impacts on mixing effectiveness and production efficiency, as detailed below:
- Mixing Effectiveness: The design and quality of blades directly influence the uniformity and quality of feed mixing. High-quality blades effectively blend various feed ingredients, ensuring even distribution of nutrients throughout the feed. Conversely, low-quality blades may result in uneven mixing, leading to inadequate or uneven distribution of nutrients, affecting animal nutrient intake and utilization, thereby impacting breeding efficiency.
- Production Efficiency: Blade quality and condition directly affect the production efficiency of feed mixers. High-quality blades efficiently mix feed ingredients, reducing mixing time and energy consumption, thus improving production efficiency. Conversely, severely worn or poor-quality blades may prolong mixing time, result in poor mixing effectiveness, or even increase the risk of machine failure, reducing production efficiency.
- Durability and Maintenance Costs: High-quality blades typically have higher durability, enduring long periods of high-intensity use without significant wear or damage, thereby reducing the frequency of parts replacement and maintenance costs. In contrast, low-quality blades may require more frequent replacement, increasing downtime and maintenance costs, thus affecting production efficiency and economic benefits.
Therefore, purchasing and replacing high-quality blades are crucial to ensure the normal operation of feed mixers, improve mixing effectiveness, and enhance production efficiency. High-quality blades can ensure uniform and high-quality feed mixing, improve production efficiency, and reduce maintenance costs, thereby providing strong support for the development and economic benefits of the livestock industry.
Purchasing Method
When purchasing feed mixer blades, several key factors need consideration:
- Blade Material and Processing Technology: Material: High-quality blades typically use wear-resistant and corrosion-resistant materials, such as stainless steel, hard alloys, etc., to ensure long-term stable use. Processing Technology: Blade processing technology directly affects its quality and performance. Precise processing technology can ensure a smooth surface and accurate dimensions, improving blade wear resistance and service life.
- Blade Shape and Size: Shape: Different types of feed mixers may require different blade shapes, such as leaf-shaped or spiral-shaped blades. Selecting the appropriate blade shape for your machine type is crucial. Size: Blade size needs to match the specifications of the feed mixer to ensure proper installation and effective feed mixing.
- Supplier Reputation and After-sales Service: Reputation: Choose suppliers with a good reputation and extensive experience to ensure the quality and reliability of blades. After-sales Service: Ensure that the supplier provides timely and professional after-sales service, including technical support, maintenance, etc., to promptly resolve issues and ensure equipment’s normal operation.
For selecting the appropriate blade model and supplier based on production needs, here are some suggestions:
- Understand Your Production Needs: First, understand your feed mixer model and specifications, as well as specific production requirements, including the types of materials, mixing volume, mixing time, etc.
- Consult Professionals: Consult feed mixer manufacturers or professional technicians for advice based on your production needs and equipment specifications to obtain professional blade purchasing recommendations.
- Compare Products and Services from Different Suppliers: Compare the quality, price, and after-sales services of blades from different suppliers to choose the one with the best cost-performance ratio.
- Consider Long-term Cooperation: Choose a reputable supplier that provides a stable supply and good after-sales service to establish long-term cooperation, ensuring the continuous and stable supply of blades and equipment operation.
Replacement Method
Properly replacing feed mixer blades is crucial. Here are the general replacement steps:
- Check Blade Condition and Safety:
- Before replacing the blades, inspect the current blades to ensure they are in good condition and safe for use. Check for obvious wear, cracks, or other damage, as well as loose blade fastenings. This is an important step to ensure a smooth replacement process and subsequent safe use.
- Use the Correct Tools to Disassemble Old Blades:
- Refer to the manufacturer’s guidelines and user manual to select the appropriate tools, such as wrenches, screwdrivers, etc., to safely disassemble the old blades from the mixer. Ensure safety during operation to avoid personal injury or machine damage.
- Install New Blades and Ensure Correct Installation:
- Install the new blades into the feed mixer, ensuring they are correctly installed and secured. Follow the manufacturer’s installation guidelines to ensure the blades are properly aligned, fastened, and matched with the mixer’s rotor or agitator. Tighten the blade screws or other fastening devices to ensure the blades do not loosen or detach during operation.
- Test Machine Performance and Mixing Effect:
- After installing the new blades, conduct tests on machine performance and mixing effect. Start the mixer and observe whether the blades rotate smoothly and whether the mixing effect meets requirements. Perform trial runs as needed, adjusting mixer parameters to ensure the desired mixing effect.
- Emphasize the Importance of Correct Blade Replacement for Mixing Effect and Operational Safety:
- Lastly, emphasize the importance of correctly replacing the blades. Proper blade replacement not only ensures optimal mixing of feed but also safeguards operational safety. Using severely worn or improperly installed blades may result in uneven mixing, machine failure, or even safety accidents. Therefore, regularly inspecting and replacing blades, and ensuring operators have proper operating skills and safety awareness, are crucial for ensuring the normal operation and safety of feed mixers.
By strictly following the above steps for replacing feed mixer blades, the quality of mixing and operational safety can be ensured, thereby improving equipment stability and production efficiency.
Common Problems and Solutions
Here are some common problems customers may encounter:
- Uneven Blade Wear: Uneven use during production or material quality differences may result in uneven blade wear, with some blades experiencing severe wear while others show minimal wear.
- Improper Installation: Improper alignment or fastening during blade installation may cause blades to loosen or detach during operation, affecting mixing effectiveness and possibly damaging the mixer.
- Excessive Blade Wear: Blades made of inappropriate materials or subjected to prolonged, high-intensity use may experience excessive wear, reducing blade lifespan and affecting mixing effectiveness and production efficiency.
- Blade Damage: Blades may inevitably suffer damage due to accidental collisions or improper use, such as blade breakage or deformation, impacting the normal operation of feed mixers.
Methods and suggestions for solving these problems include:
- Regular Maintenance and Care of Blades: Regularly inspect blade conditions to promptly identify worn, damaged, or loose blades and perform maintenance or replacement. Methods such as cleaning, lubricating, or grinding can extend blade lifespan.
- Proper Blade Use: Avoid overloading and frequent starts and stops during use to reduce blade wear. Also, avoid putting unsuitable materials or oversized particles into the mixer to reduce blade damage.
- Select High-quality Blades: When purchasing blades, choose high-quality, wear-resistant blades to reduce wear and damage, prolonging blade lifespan.
- Correct Blade Installation: Follow manufacturer guidelines for blade replacement or installation, ensuring proper alignment, fastening, and compatibility with the mixer to avoid installation-related issues.
By regularly maintaining and caring for blades, using blades properly, selecting high-quality blades, and ensuring correct installation, blade lifespan can be maximized, ensuring mixing effectiveness and operational safety.
In The End
Purchasing and replacing feed mixer parts, especially blades, are crucial for ensuring production efficiency and stable machine operation. Only by selecting high-quality parts and properly installing and maintaining them can feed mixers operate stably for a long time, improving production efficiency and reducing maintenance costs.
Contact Us for More Information and Services
Interested in learning more about feed mixer blades and other parts? Feel free to contact our team! As a professional blade manufacturer, Nanjing Metal Industrial offers the following services:
- Product Consultation: Detailed specifications and applications of feed mixer blades and parts.
- Customization Services: Tailoring blades and parts to your specific needs.
- After-sales Services: Comprehensive support including installation guidance, maintenance advice, technical support, etc.
- Fast Delivery: Timely delivery to meet your production needs.
- Customer Support: Available to address any questions or concerns during use.
Contact us now for excellent service and support!