The demand for corrugated boards continues to grow in modern industrial production. Market research indicates that the global corrugated board market is expected to expand significantly, reaching approximately $300 billion by 2025. This growth is mainly driven by the e-commerce and retail industries’ need for high-quality packaging materials.
A corrugated board is preferred for its high strength, lightweight, and recyclability. However, as market competition intensifies, manufacturers face challenges in improving production efficiency, ensuring product quality, and reducing costs. Efficient and precise production equipment is key to maintaining competitiveness.
Crosscutters and slitters play a crucial role in corrugated board production. Crosscutters ensure the board’s length meets specifications through precise transverse cuts, while slitters ensure the width meets customer requirements through flexible longitudinal cuts. The performance and stability of these machines directly affect production efficiency and product quality.
High-quality cutting blades can significantly enhance production efficiency and product quality. Superior blades extend equipment life, reduce downtime, and lower maintenance costs, leading to higher production efficiency and better product consistency. A study reports that companies using high-quality blades see a 15% increase in production efficiency and a 10% reduction in waste.
By selecting and maintaining the right crosscutters, slitters, and blades, manufacturers can stand out in a competitive market, meet growing demand, and achieve sustainable development.
2. Overview of the Corrugated Board Production Process
Corrugated board production involves several critical steps, each crucial to the final product’s quality and performance:
2.1 Raw Paper Unfolding
Production starts with unfolding raw paper, including the top liner, bottom liner, and medium. These paper rolls are placed on a paper stand, and automated equipment unfolds the paper and feeds it into the production line.
2.2 Preheating
The unfolded paper is preheated to remove moisture and increase flexibility and adhesiveness. Preheaters use steam or electric heating to evenly warm the paper to a suitable processing temperature.
2.3 Corrugating
The preheated medium is processed into a wavy structure by a single facer. This process increases the paper’s strength and rigidity, providing a foundation for bonding.
2.4 Gluing
The corrugated medium is coated with adhesive, usually starch-based, at the tips of the flutes. The adhesive bonds the medium with the top liner, and the uniformity and adhesiveness directly affect the bonding and strength of the board.
2.5 Pressing
The glued medium and liner are pressed together using a double facer, where heat and pressure ensure a strong bond. Multiple pressing rollers may be used to improve adhesion quality and flatness.
2.6 Cutting
The formed corrugated board is cut in two stages:
- Slitting: Slitters use disc blades to cut the board into required widths. Precision and clean edges are vital for the final product’s dimensions and appearance.
- Crosscutting: Crosscutters use straight or rotary blades to cut the board to specified lengths. Efficient, precise crosscutting ensures each board meets customer specifications.
2.7 Stacking
Cut boards are stacked by an automatic stacker, ensuring neat and stable piles for packaging and transportation.
2.8 Importance of Cutting Process
The cutting process determines the board’s specifications and quality. High-precision cutting ensures accurate dimensions and reduces waste. Choosing high-quality cutting blades and maintaining equipment is essential for consistent cutting quality.
3. Detailed Analysis of Slitters
Slitters are essential in corrugated board production. Their flexible cutting widths, efficient design, high-precision cutting, and advanced automation make them indispensable. Choosing and maintaining high-quality slitters can significantly improve production efficiency and product quality.
3.1 Working Principle
Slitters cut wide corrugated boards into required widths:
- Feeding: Boards enter the slitter continuously via a conveyor system.
- Positioning: Positioning devices adjust the disc blades based on preset widths.
- Cutting: High-speed rotating disc blades cut the board into strips.
- Discharging: Cut strips are conveyed to the next process or stacking.
3.2 Technical Features:
- Flexible Cutting Width: Adjustable disc blades allow for various board widths.
- Efficiency and Energy Saving: Optimized power transmission and blade design reduce energy consumption.
- High Precision: Accurate cutting ensures smooth edges and reduces waste.
4. Detailed Analysis of Crosscutters
Crosscutters are crucial in corrugated board production. Their high-speed, precise cutting and automated control systems make them vital. Choosing and maintaining high-quality crosscutters enhances production efficiency and product quality.
4.1 Working Principle
Crosscutters cut continuous corrugated boards to specified lengths:
- Feeding: Boards enter the crosscutter via a conveyor system.
- Positioning: Sensors or positioning devices determine the cutting length.
- Cutting: Blades cut the board when it reaches the set length.
- Discharging: Cut boards are conveyed to the next process or stacking.
4.2 Technical Features:
- Cutting Precision: Ensures minimal error, typically within ±0.5 mm.
- High-Speed Cutting: Capable of cutting several hundred meters per minute.
- Blade Material: High-quality materials like high-speed steel or carbide ensure durability and sharpness.
- Automation: Advanced control systems for precise, easy operation.
- Low Vibration and Noise: Designed for reduced vibration and noise for safe, comfortable operation.
- Safety Features: Emergency stops, safety covers, and sensors ensure operator safety.
- Ease of Maintenance: Simple design for easy maintenance and quick part replacement.
5. The Critical Role of Slitter Blades
Slitter blades are crucial in the production of corrugated board. High-quality slitter blades can improve production efficiency and product quality, extend equipment lifespan, and reduce maintenance costs. Here is a detailed look at the key roles of slitter blades.
5.1 Types of Blades
In corrugated board production, the main blades used are disc blades and straight blades, each for different cutting processes.
- Disc Blades:
- Use: Primarily used in slitting machines, disc blades cut the corrugated board longitudinally into the desired width.
- Features: High cutting efficiency, capable of continuous long-term cutting, suitable for high-output production. They produce smooth, neat edges, reducing burrs and waste.
- Straight Blades:
- Use: Mainly used in sheeting machines, straight blades cut the board transversely into specified lengths through up-and-down or rotary motion.
- Features: High cutting precision, ensuring consistent length in each cut. Suitable for products requiring strict dimensional control, with straight cuts that ensure product quality and appearance.
5.2 Material Selection
The choice of blade material is key to ensuring performance and longevity. Common blade materials include high-speed steel (HSS) and carbide.
- High-Speed Steel (HSS):
- Features: Good hardness and toughness, maintains sharpness at high temperatures, suitable for high-speed cutting. Good wear resistance and impact resistance, a common blade material.
- Application: Suitable for cutting harder corrugated boards requiring high cutting precision.
- Carbide:
- Features: Higher hardness, better wear resistance, longer service life. Suitable for mass production and high-intensity cutting tasks.
- Application: Widely used where blade life and cutting quality are critical, reducing blade replacement frequency and increasing production efficiency.
5.3 Manufacturing Process
The manufacturing process of blades directly affects their performance and lifespan. High-quality manufacturing involves precision heat treatment and grinding processes.
- Precision Heat Treatment:
- Purpose: Increases blade hardness and toughness to keep it sharp during high-intensity cutting.
- Process: Includes quenching and tempering. Quenching achieves high hardness, while tempering maintains hardness and increases toughness, reducing blade breakage during cutting.
- Grinding Process:
- Purpose: Precision grinding enhances the sharpness and surface finish of the blade, ensuring smooth and accurate cutting.
- Process: Involves rough grinding to remove excess material and fine grinding for detailed processing, achieving the required sharpness and finish.
5.4 Maintenance
Regular maintenance is necessary to ensure blade performance and lifespan. Maintenance includes:
- Regular Inspection:
- Content: Check blade wear, cutting quality, and equipment condition regularly, and address issues promptly.
- Frequency: Conduct a comprehensive inspection weekly or monthly, depending on production intensity and usage.
- Cleaning Maintenance:
- Content: Remove accumulated paper scraps and glue. Use special cleaning agents and tools, avoiding corrosive chemicals.
- Method: Wipe the blade surface with a soft cloth and cleaning agent to ensure no residues affect cutting performance.
- Blade Replacement:
- Content: Replace blades when they reach their service life or show severe wear. Ensure proper installation and fastening for stability.
- Method: Follow equipment manuals for blade replacement to prevent equipment malfunctions from improper installation.
- Lubrication Maintenance:
- Content: Regularly lubricate blade bearings and cutting parts to reduce friction and extend lifespan.
- Method: Use special lubricants, avoiding unsuitable ones that could damage the equipment.
In summary, slitter blades play a vital role in corrugated board production. Choosing and maintaining high-quality blades can significantly enhance cutting efficiency and product quality, creating greater economic benefits and market competitiveness for enterprises.
6. Blade Purchasing Guide
When purchasing slitter blades, consider the blade’s parameters and performance and evaluate the supplier’s qualifications and service capabilities. A scientific and rational purchasing process enables enterprises to select high-quality blades and reliable suppliers, enhancing production efficiency and product quality.
6.1 Key Parameters
Pay attention to the following key parameters when purchasing slitter blades to ensure suitable blade selection, improving production efficiency and product quality.
- Hardness:
- Description: Blade hardness determines cutting performance and wear resistance. Too low hardness leads to rapid wear, while too high hardness increases brittleness.
- Recommendation: Choose blade hardness based on the material being cut. Generally, HSS or carbide blades with hardness HRC 60-65 are recommended for cutting corrugated board.
- Sharpness:
- Description: Sharp blades reduce cutting resistance, enhancing efficiency and quality.
- Recommendation: Select highly sharp blades to ensure smooth, neat edges, minimizing waste.
- Durability:
- Description: Durability determines blade lifespan and replacement frequency. High-durability blades maintain performance in high-intensity environments, reducing downtime.
- Recommendation: Choose blades with high wear resistance and impact resistance, such as carbide or specially treated HSS blades.
- Size and Specifications:
- Description: Blade size and specifications must be compatible with the equipment, including diameter, thickness, and bore size.
- Recommendation: Select blades based on equipment model and production needs to ensure stable installation and operation.
- Coating:
- Description: Some blades have special coatings to enhance wear resistance and corrosion resistance.
- Recommendation: For long-term continuous cutting, choose coated blades, such as titanium or titanium nitride-coated blades.
- Blade Type:
- Description: Choose blade type based on specific cutting needs, e.g., disc blades for slitting and straight blades for sheeting.
- Recommendation: Select the appropriate blade type based on production processes to ensure effective cutting.
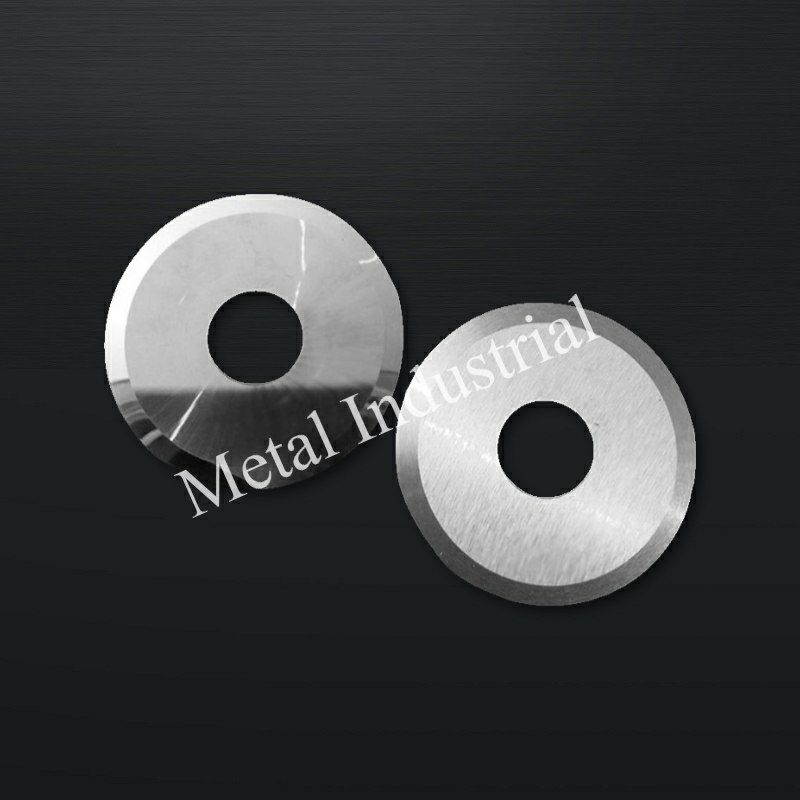
6.2 Supplier Evaluation
Choosing the right supplier is equally important. A quality supplier can provide high-quality blades and reliable after-sales service. Consider the following factors when evaluating suppliers:
- Supplier Qualifications:
- Description: Evaluate the supplier’s qualifications and reputation, including business licenses and ISO quality management system certifications.
- Recommendation: Choose suppliers with good market reputation and certification to ensure product quality and service standards.
- Product Quality:
- Description: Assess the quality of the blades provided by the supplier, including material, process, and performance.
- Recommendation: Test samples and consider customer feedback to understand the actual performance of the supplier’s products, selecting those with stable and reliable quality.
- Reasonable Pricing:
- Description: Evaluate if the blade price is reasonable and offers good value.
- Recommendation: Choose suppliers offering reasonable prices and high value, avoiding low-cost options that compromise quality.
- Delivery and Supply Capacity:
- Description: Assess the supplier’s delivery capability and timeline to ensure stable supply.
- Recommendation: Choose suppliers with timely delivery and stable supply to avoid production disruptions.
- After-Sales Service:
- Description: Evaluate the supplier’s after-sales service capabilities, including technical support, maintenance, and return policies.
- Recommendation: Choose suppliers with comprehensive after-sales service to ensure timely issue resolution and continuous production.
- Customer Reviews and Case Studies:
- Description: Learn about the supplier’s product and service quality through customer reviews and successful case studies.
- Recommendation: Choose suppliers with a good industry reputation and high customer ratings, referencing successful cases to understand product performance in practice.
- Technical Support:
- Description: Assess the supplier’s technical support, including blade selection advice, installation guidance, and user training.
- Recommendation: Choose suppliers offering extensive technical support to ensure professional assistance during purchasing and usage.
6.3 Our Advantages
Nanjing Metal Industrial has established a leading position in the market with its extensive experience, high-quality products, innovative R&D, and excellent customer service. We are dedicated to providing the best slitter blade solutions, helping customers improve production efficiency and product quality, achieving greater economic benefits and market competitiveness.
- Extensive Industry Experience: With years of experience in blade manufacturing, we understand various cutting needs and processes. We are familiar with industry standards and requirements, offering professional consultation and customized solutions to meet diverse customer needs.
- High-Quality Products: We carefully select high-quality materials, such as HSS and carbide, ensuring durability and cutting performance. Advanced heat treatment and precision grinding processes ensure blade hardness and sharpness at industry-leading levels.
- Innovative R&D Capability: Our professional R&D team continuously innovates and improves product design and manufacturing processes. Through ongoing technological innovation, our blade performance continually improves to better meet market changes and customer needs.
- Strict Quality Control: We have established a comprehensive quality management system, strictly following ISO quality standards for production and inspection. Each blade undergoes rigorous quality testing, ensuring product consistency and reliability, providing customers with stable high-quality products.
- Wide Range of Products: We offer a variety of blade types, including disc blades and straight blades, suitable for different cutting equipment and process needs. Customers can find comprehensive blade solutions with us, saving time and effort.
- Excellent Customer Service: We value customer experience, providing comprehensive pre-sales consultation, technical support, and after-sales service. We offer timely help and support during purchase, installation, and use, ensuring smooth and worry-free production processes.
- Competitive Pricing: Our products are competitively priced while maintaining high quality. By optimizing production processes and supply chain management, we offer high-value blades, helping customers reduce production costs and increase economic benefits.
- Fast Delivery: With an efficient production and logistics system, we guarantee swift delivery. Customers need not worry about production delays due to blade supply issues; our rapid delivery capability ensures production schedules are met on time.
- Successful Customer Cases: We have partnered with numerous renowned enterprises, accumulating a wealth of successful cases. These instances validate the reliability and superior performance of our products and services, offering customers peace of mind in choosing our products.
- Environmental Sustainability: We are committed to environmental protection and sustainable development, employing eco-friendly materials and processes to minimize environmental impact. Choosing our products not only boosts production efficiency but also aligns with modern corporate environmental standards, enhancing corporate image.
In The End
High-quality cross-cutting machines, slitting machines, and their blades are crucial for enhancing efficiency and quality in corrugated board production. Contact us to learn more about our products and explore customized solutions. Visit our product page or directly reach out to our sales team for professional consultation services.
2 Responses
all the time i used to read smaller content that alsо clear their motive, and that is also happening with this article
which I am reading аt thіs time.
Thank you for your comment. We appreciate your feedback and look forward to your continued interest in our articles.