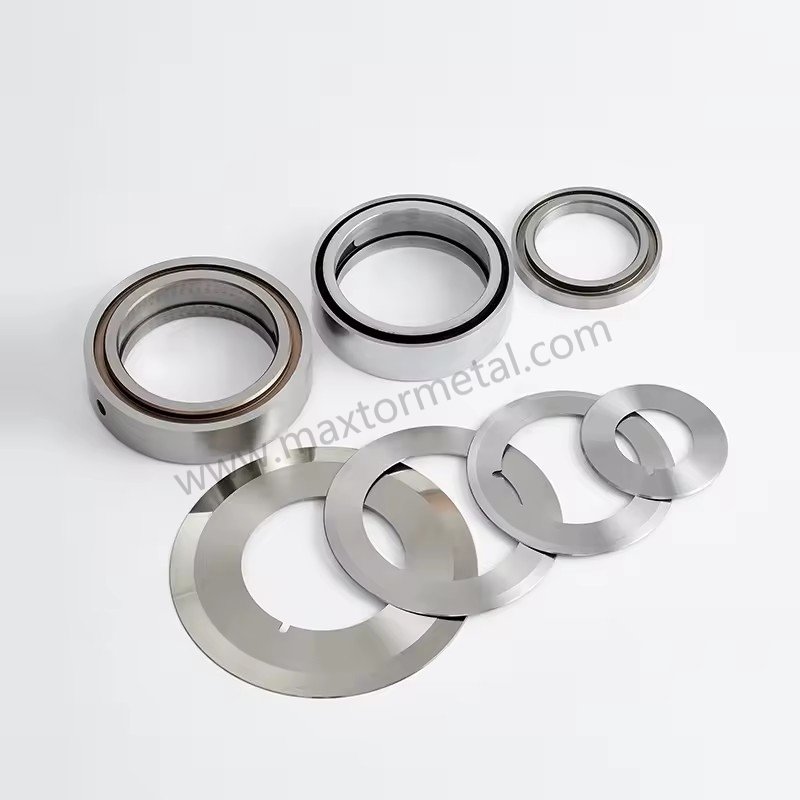
In industries like paper, plastics, and metals, circular slitting blades are essential. These blades play a crucial role in cutting materials efficiently and accurately. The performance of these blades directly impacts product quality, production speed, and cost. Yet, many companies overlook a critical factor: the material choice for the blades. Choosing the right material can reduce blade wear, lower maintenance costs, and improve overall productivity. This article will guide you through the factors to consider when choosing blade materials and explore the most common materials used for circular slitting knives.
1. The Importance of Circular Slitting Blades
Circular slitting knives are key tools on many industrial production lines. Whether you are cutting paper, plastic films, or metal sheets, these blades ensure precise, clean cuts without damaging the material. They help maintain high production efficiency and quality.
However, poor blade performance can cause issues such as uneven cuts, material waste, and frequent blade replacements. These problems often stem from choosing the wrong blade material. With the right material, blades last longer, reduce downtime, and improve cutting performance. Selecting the right blade material is a critical step in optimizing production lines.
2. Key Factors in Choosing Circular Slitting Blades Materials
Selecting the best material for a circular slitting blade depends on several important factors. Each factor affects the blade’s performance and lifespan.
2.1 The Type of Material to Be Cut
Different cutting materials have different requirements for the blade. For example, cutting metals requires a harder, more durable blade than cutting paper. If you use a blade that is too soft, it will wear out quickly. A blade that is too hard may crack when cutting softer materials. Matching the blade hardness and sharpness to the material is essential for efficient cutting.
2.2 Wear Resistance and Hardness
The wear resistance of a blade is crucial for longevity. Blades that are highly wear-resistant can endure longer periods of use, reducing the need for frequent replacements. Hardness also plays a significant role. Harder blades cut through tough materials more effectively, ensuring cleaner cuts and extended use. However, very hard blades can be more brittle, especially under heavy pressure.
2.3 Corrosion Resistance
In some industrial environments, blades are exposed to moisture or corrosive materials. This exposure can quickly degrade blades if they aren’t made of corrosion-resistant materials. Choosing a material with high corrosion resistance ensures the blade remains effective and safe to use, especially in harsh conditions.
2.4 Sharpness and Toughness
The sharpness of the blade affects how clean and quick the cut is. However, toughness is equally important. Tough blades can handle pressure and impact without breaking. Sharp blades with low toughness can wear out or crack faster. A balance between sharpness and toughness is needed to maximize both cutting efficiency and durability.
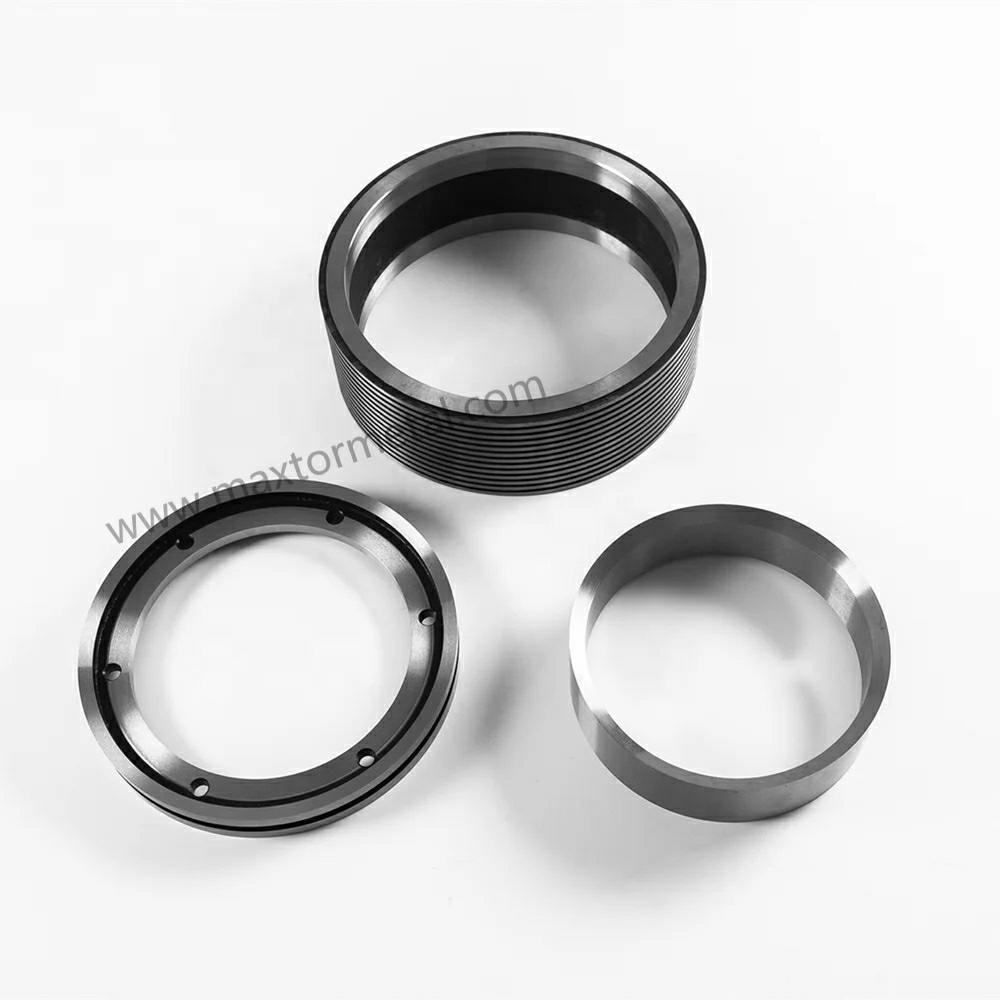
3. Common Materials for Circular Slitting Blades and Their Pros and Cons
Now that we’ve covered the key factors, let’s examine the most common materials used for circular slitting knives. Each material has its strengths and weaknesses, depending on the application.
3.1 High-Speed Steel (HSS)
Pros:
- High-speed steel (HSS) is known for its toughness and resistance to wear, making it ideal for cutting harder materials.
- HSS blades can maintain their sharpness even at high temperatures, which is beneficial for high-speed cutting applications.
Cons:
- HSS blades tend to be more expensive, and their cost may be high for applications where blades need to be frequently replaced.
- They may not be necessary for softer materials where lower-cost options are available.
3.2 Tungsten Carbide
Pros:
- Tungsten carbide blades are extremely hard and have excellent wear resistance, making them a great choice for cutting tough materials like metals.
- These blades last longer than many other options, reducing the frequency of replacements.
Cons:
- Tungsten carbide is brittle and can crack under heavy impact or pressure. It’s less suitable for applications where the blade may experience shocks or vibrations.
3.3 Ceramic
Pros:
- Ceramic blades offer outstanding resistance to wear and corrosion. They are perfect for cutting in environments with high moisture or chemical exposure.
- These blades can also maintain a very sharp edge, providing clean, precise cuts.
Cons:
- Ceramic blades are brittle and prone to breaking under impact, making them unsuitable for high-pressure applications.
3.4 Tool Steel
Pros:
- Tool steel is an affordable option with good all-around performance. It works well for general cutting tasks and can handle moderate use.
- It offers decent wear and corrosion resistance, making it versatile for different materials.
Cons:
- Tool steel doesn’t last as long as carbide or HSS when cutting harder materials, meaning more frequent blade changes are needed.
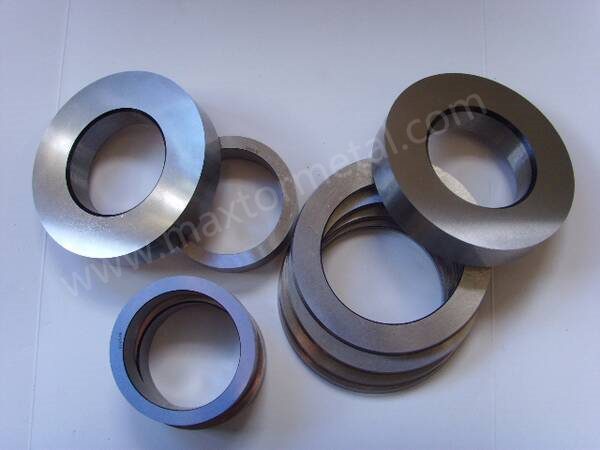
4. How to Choose the Right Material for Your Application
Selecting the best material for your circular slitting blades can significantly impact your production efficiency, blade lifespan, and overall costs. To make the best choice, you need to evaluate various factors that align with your specific operational needs. This section will guide you through each of these considerations in detail.
4.1 What Material Are You Cutting?
The first and most important factor when choosing blade material is the type of material you’ll be cutting. Each cutting material has unique characteristics that influence how the blade interacts with it.
- Soft Materials (e.g., paper, plastic, films):
When cutting soft materials, it’s crucial to use a blade that is sharp and precise but not necessarily the hardest. Blades made from high-speed steel (HSS) or tool steel work well for these applications. These materials provide sufficient sharpness for clean cuts, while maintaining an affordable cost. - Harder Materials (e.g., metals, thick plastics):
Cutting hard materials requires a blade with high wear resistance and hardness. Tungsten carbide blades are ideal for these tasks because they maintain their sharpness longer and can withstand the stress of cutting through tougher materials. Blades that are too soft for these applications will wear out quickly, leading to poor cutting quality and frequent replacements. - Abrasive or Composite Materials (e.g., fiber-reinforced plastics, laminated materials):
For highly abrasive materials, wear resistance becomes the most critical factor. Blades made from tungsten carbide or ceramic offer superior durability in these conditions, significantly extending blade life and improving the cutting process.
Matching the blade material to the hardness, thickness, and abrasiveness of the material being cut is essential. A mismatch here can lead to inefficient cuts, faster wear, and increased production downtime due to blade changes.
4.2 How Frequently Will You Use the Circular Slitting Blades?
The frequency and intensity of use also play a crucial role in selecting the right blade material. High-frequency use demands durable materials that can handle long-term wear and tear, while lower-frequency applications may benefit from less expensive options.
- High-Volume Production:
If your production line runs continuously or at high speeds, you’ll need blades with excellent durability and resistance to wear. Tungsten carbide is often the preferred material in these cases because it stays sharp for extended periods, even under heavy use. While it is more expensive upfront, the long lifespan of the blade reduces the need for frequent replacements, minimizing downtime and improving overall cost efficiency. - Low-Volume or Intermittent Use:
For operations that don’t require round-the-clock cutting or handle lower volumes of softer materials, high-speed steel or tool steel blades may be a better fit. These blades are more affordable and still perform well under moderate use. They can be replaced more frequently without significantly impacting operational costs.
Choosing the right blade material for your usage frequency ensures that you get the best value for your investment, balancing upfront costs with long-term savings.
4.3 What Is the Production Environment Like?
Your production environment can also affect the performance and lifespan of your blades. Certain environments introduce specific challenges that some materials handle better than others.
- High-Moisture or Corrosive Environments:
If your blades are exposed to moisture, chemicals, or corrosive elements, corrosion resistance becomes a key factor. Ceramic and corrosion-resistant high-speed steel are good choices in these environments. These materials are less likely to rust or degrade when exposed to moisture, ensuring a longer lifespan and maintaining cutting efficiency.
For example, in industries like food processing or chemical manufacturing, where moisture and corrosive substances are present, corrosion-resistant materials prevent the blades from wearing out prematurely. This helps maintain production quality and reduces the need for frequent replacements.
- High-Temperature Environments:
If your cutting process involves high temperatures, as in the metal industry, you’ll need a material that can withstand heat without losing its hardness or sharpness. High-speed steel (HSS) is ideal for high-temperature cutting because it retains its cutting edge even when subjected to heat.
Conversely, materials like ceramic may become brittle in high-heat applications and could crack, making them less suitable for such environments.
- Heavy Impact or Vibration:
If the blade will encounter significant impact or vibration during the cutting process, you need a material that is tough and resilient. Tool steel or toughened carbide may be better choices, as they are less likely to chip or crack under mechanical stress compared to more brittle materials like ceramic.
Evaluating the specific conditions in your production environment will help you select a blade material that performs reliably over time and in challenging conditions.
4.4 Balancing Cost and Performance
When choosing blade materials, it’s crucial to strike a balance between the cost of the blade and its expected performance and lifespan. This balance is particularly important because higher-quality materials tend to be more expensive, but they often offer better long-term value due to their durability.
- Upfront Cost:
Materials like tungsten carbide and ceramic come with higher upfront costs. However, their extended lifespan and superior cutting performance can justify the higher price, especially in high-volume, continuous production environments. They reduce the need for frequent blade replacements, which minimizes downtime and keeps your production line running smoothly. - Cost Efficiency for Lower Volumes:
For companies that don’t operate high-volume production lines, or for those that work with softer materials, using more affordable blade materials such as high-speed steel or tool steel can offer better cost efficiency. These materials still perform well under moderate conditions but are more affordable, reducing the initial investment. - Long-Term Maintenance Costs:
The longer a blade lasts, the lower your overall maintenance costs will be. High-end materials that resist wear and corrosion can significantly reduce how often you need to replace or sharpen blades. For example, tungsten carbide blades may last several times longer than tool steel in demanding applications, leading to significant savings over time. - Operational Downtime:
Frequent blade changes can disrupt production, leading to increased labor costs and lost output. More durable blade materials reduce these interruptions, maximizing operational efficiency. If minimizing downtime is a priority, investing in more expensive but longer-lasting blade materials like tungsten carbide can pay off in the long run.
By carefully considering your production needs, budget, and long-term goals, you can find the perfect balance between cost and performance. Choosing the right material can help optimize production efficiency, reduce operational downtime, and minimize overall costs, making it a smart long-term investment.
5. The Importance of Choosing a Reliable Supplier
The material is only part of the equation when selecting circular slitting blades. A trustworthy supplier can provide consistent quality and help you find the best solution for your specific needs.
5.1 Consistent Quality Control
A good supplier ensures that the blades you receive meet strict quality standards, so you get consistent performance across batches. This means better productivity and less worry about defective products.
5.2 After-Sales Support
Reliable suppliers offer ongoing support, helping you troubleshoot any issues with blade performance or replacement. Their expertise can also help you extend blade life through proper usage and maintenance.
5.3 Custom Solutions
Your cutting needs may vary depending on your industry, materials, and production environment. A good supplier can customize blades to meet your exact requirements, ensuring you have the right tool for the job.
6. Frequently Asked Questions (FAQ)
What is a circular slitting blade?
A circular slitting blade is a round blade used for cutting materials in industries like paper, plastics, and metal processing. It is known for its precision and efficiency in cutting.
Should I choose tungsten carbide or high-speed steel?
If you need to cut hard materials frequently, tungsten carbide is a better choice because of its hardness and wear resistance. For softer materials or applications where the knife will be replaced often, high-speed steel is more cost-effective.
How do I choose the right blade for different materials?
Consider the hardness and thickness of the material, as well as how frequently the blade will be used. For harder materials, choose tougher blades like tungsten carbide. For softer materials, tool steel or high-speed steel might be enough.
What affects the frequency of blade replacement?
Blade replacement depends on the type of material being cut, the environment in which the blade is used, and the blade’s material. Harder materials and harsher environments will wear blades faster.
7. Conclusion: Long-Term Benefits of Choosing the Right Material
Choosing the right material for your circular slitting blade can greatly enhance production efficiency and lower long-term costs. The right blade not only improves cutting performance but also reduces downtime and replacement frequency. Investing in high-quality blades tailored to your specific needs is a smart move for any business looking to optimize its production line.
If you need expert advice on which blade material is best for your operations, feel free to reach out to us. We offer tailored solutions to help you find the most suitable blade material for your cutting needs.
By making the right choice, you’ll ensure better product quality, lower costs, and smoother operations for your business.
3 Responses