1.Introduction
In the metal processing industry, the longevity and wear resistance of Roll Shear Blades are crucial for maintaining operational efficiency and reducing costs. These blades, used in metal coil slitting lines, play a significant role in ensuring precise cuts while withstanding high-speed, high-pressure environments. However, premature wear and frequent replacements are common challenges, often leading to costly downtimes and increased maintenance expenses.
Understanding and implementing measures to enhance slitting blade durability can greatly benefit businesses. This article explores key factors influencing shear blade wear resistance and provides actionable strategies to extend blade lifespan.
2.Factors Affecting Wear Resistance of Roll Shear Blades
2.1 Material Selection
Material selection is a primary factor in determining slitter blade wear resistance. High-carbon tool steels and tungsten carbide are popular choices for metal coil slitting blades due to their high hardness and wear resistance. However, each material comes with trade-offs. Tool steels are generally more affordable and provide decent durability, while tungsten carbide is known for its superior wear resistance but at a higher cost.
For example, D2 tool steel, with its high chromium content, offers excellent wear resistance for most applications but may struggle with certain high-hardness metals. On the other hand, tungsten carbide, with hardness levels up to 1,500 Vickers, performs exceptionally well against tough metals like stainless steel but comes with a higher initial cost. Choosing the right material should balance cost and performance based on the specific metal slitting line requirements.
2.2 Heat Treatment Processes
The heat treatment applied to rotary shear blades directly impacts blade hardness, which is crucial for durability. Through methods like quenching, tempering, and annealing, the hardness of tool steels can increase significantly, often reaching a Rockwell hardness level of 60-65 HRC.
Quenching and tempering allow slitter knives to achieve an optimal balance between hardness and toughness, which reduces brittleness while improving wear resistance. While these methods may increase costs slightly, they often provide long-term savings by extending blade lifespan and reducing the frequency of replacements. Companies should ensure their blades undergo these critical processes to maximize durability.

3.Core Strategies to Enhance Wear Resistance of Roll Shear Blades
3.1 Applying High-Quality Coatings
One of the most effective ways to extend the lifespan of metal coil slitting blades is through advanced surface coatings. Coatings like PVD (Physical Vapor Deposition) and CVD (Chemical Vapor Deposition) offer considerable benefits by enhancing the blade’s hardness and resistance to wear, corrosion, and high temperatures. For example, Titanium Nitride (TiN) coatings can increase hardness by up to 25%, which translates to longer-lasting performance when cutting abrasive materials. This added hardness can reduce friction, lower heat build-up, and make the blades more resistant to surface damage, leading to a smoother, more durable cutting edge.
Comparing popular coatings:
- TiN Coating: This is a commonly used coating in metal slitting, known to increase hardness levels by an average of 2,200 to 2,400 HV (Vickers Hardness). TiN’s smooth finish also decreases oxidation rates, making it suitable for general-purpose metal slitting blades.
- TiAlN (Titanium Aluminum Nitride): With a hardness range of up to 3,200 HV, TiAlN provides higher heat resistance than TiN, making it ideal for high-speed metal coil slitting lines. Studies indicate TiAlN-coated blades can last up to 35% longer than uncoated blades when used for continuous, high-temperature operations.
- Diamond-Like Carbon (DLC): Known for exceptional hardness and low friction, DLC coatings are most effective for softer metals like aluminum and copper, where reducing friction is key. DLC-coated blades are shown to last up to 50% longer in low-impact, high-speed applications, making them an ideal choice for specific softer metals.
Choosing the right coating tailored to the materials being processed can greatly improve blade wear resistance, reducing the need for frequent sharpening or replacements and ultimately lowering operational costs.
3.2 Regular Maintenance and Proper Handling
Regular maintenance is an essential but often overlooked strategy for improving blade wear resistance. Proper handling, cleaning, and storage practices can protect the blade from premature wear and extend its usable life. A survey conducted by industry professionals found that well-maintained blades last an average of 20-30% longer than those not properly cared for.
Key maintenance practices include:
- Routine Cleaning: Cleaning removes debris and buildup that can dull the blade or cause corrosion. Operators should ideally clean blades after each shift, ensuring no material residues are left on the cutting edge. For example, using mild solvents and soft brushes helps maintain blade sharpness and integrity without causing surface damage.
- Regular Inspection: By inspecting blades for chips, cracks, or early signs of wear, operators can prevent potential issues from escalating. An internal study from a major metal processing company found that early detection of wear reduced downtime by approximately 15% per year.
- Lubrication: Specialized high-temperature lubricants can reduce friction on the blade’s edge, thereby decreasing the likelihood of overheating and surface wear. Regular lubrication also lowers the risk of thermal expansion, which can weaken the blade structure and reduce cutting precision. Ideally, metal slitting blades should be lubricated every 3-4 hours during continuous operation.
- Proper Storage: Keeping blades in a dry, controlled environment reduces the risk of rust and corrosion. Storage systems with individual slots or protective coverings can help protect metal slitting knives from scratches or contamination.
By following these maintenance practices, companies can optimize blade lifespan and reduce the need for premature replacements, leading to more cost-effective operations.
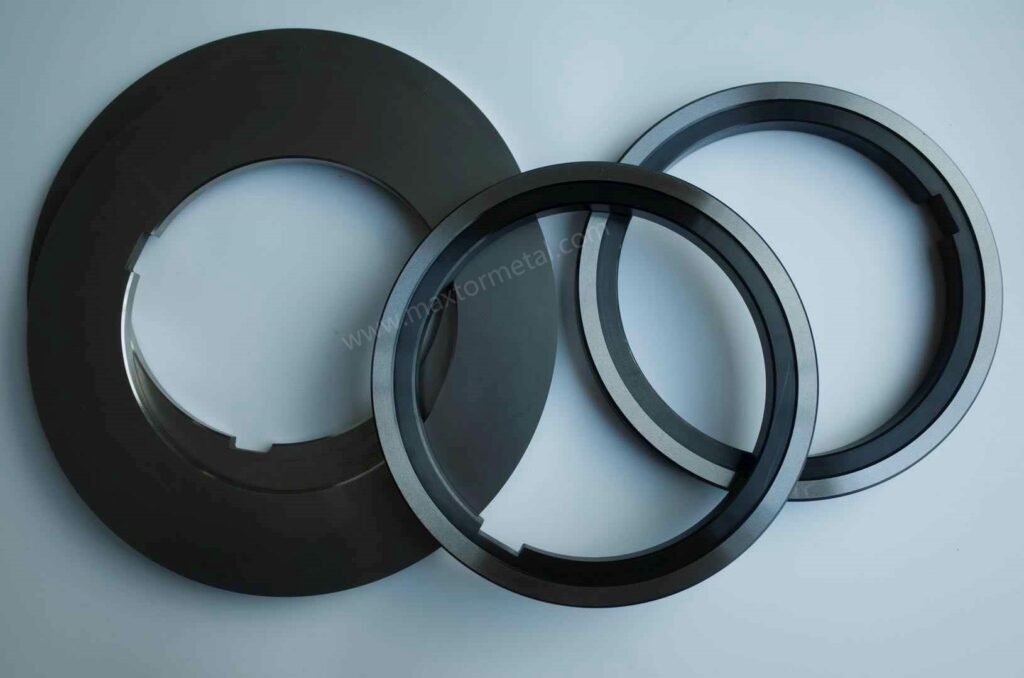
3.3 Selecting Professional Resharpening Services
Resharpening roll shear blades at regular intervals maintains cutting precision and prevents material drag, which can wear down blades prematurely. A professional resharpening service provides precision sharpening that restores the blade’s original geometry, enhancing its effectiveness and extending its wear resistance. Resharpening can increase blade life by up to 50% for certain materials, as studies on tungsten carbide and high-carbon tool steel blades indicate.
Guidelines for resharpening frequency:
- Frequency Based on Material: Blades used for high-hardness metals, such as stainless steel, should typically be resharpened every 100-150 hours of operation. In contrast, blades used for softer materials, like aluminum, can go up to 200-300 hours before requiring resharpening.
- Service Provider Selection: It’s crucial to select a reputable resharpening service with specialized equipment designed for slitter knives and metal coil slitting blades. A quality service will ensure proper edge angle and alignment, which helps reduce the force needed for cutting and, in turn, reduces wear.
Using a professional service for resharpening helps companies maintain high-quality cuts, minimizes downtime, and keeps metal slitting lines operating efficiently. While there is an associated cost, the increase in blade lifespan and the improvement in cut quality provide a significant return on investment.
4. Solutions for Different Types of Metals in Slitting Applications
4.1 Slitting Soft Metals (e.g., Aluminum, Copper)
When slitting softer metals like aluminum and copper, it’s essential to use circular slitter knives with lower hardness but higher flexibility. Softer metals require blades that can make clean cuts without excessive force, which minimizes the risk of breakage and optimizes blade life.
- Material Recommendation: Tool steel with moderate hardness (around 40-45 HRC) is typically sufficient for softer metals. This provides durability while reducing the chance of brittleness, which can cause blade edges to chip during use.
- Coating Suggestion: Titanium Nitride (TiN) coatings work well for softer metals by increasing resistance to oxidation and offering a smoother cutting experience. TiN coatings can extend blade lifespan by approximately 20-30% when used on low-friction applications like aluminum and copper.
Using these recommendations, companies can prevent wear while ensuring effective, long-lasting performance on softer metal applications.
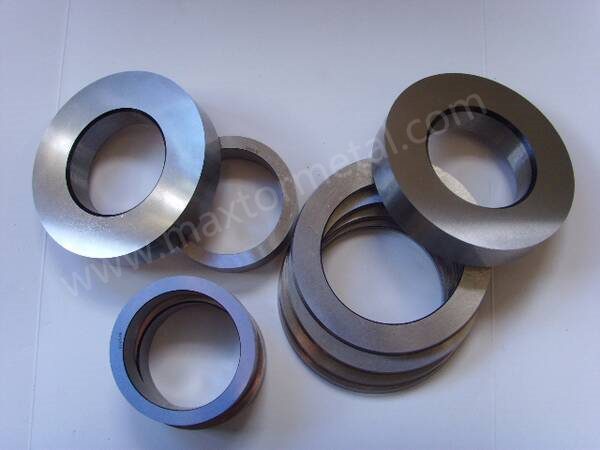
4.2 Slitting High-Hardness Metals (e.g., Stainless Steel, Carbon Steel)
High-hardness metals require rotary shear blades made from extremely durable materials, as they place greater stress on the blades due to their toughness. Tungsten carbide, with a hardness level often exceeding 70 HRC, is one of the most effective materials for slitting these types of metals.
- Material Recommendation: Tungsten carbide blades or those with high-carbon tool steel hardened to 60-65 HRC are ideal for stainless steel and other high-hardness materials.
- Coating Suggestion: TiAlN (Titanium Aluminum Nitride) or Diamond-Like Carbon (DLC) coatings offer high temperature and wear resistance, essential for continuous operations involving hard metals. Studies show that TiAlN-coated blades last up to 50% longer than uncoated options in heavy-duty applications involving stainless steel.
Adhering to these material and coating recommendations ensures that companies maximize efficiency and blade durability when working with high-hardness metals.
5. Cost-Benefit Analysis of Enhancing Blade Lifespan
Investing in high-quality wear-resistant shear blades and following proper maintenance practices can yield significant cost savings in the long run. While high-performance blades and coatings may have higher initial costs, their longer lifespan and reduced maintenance needs can provide a substantial return on investment (ROI).
- Reduced Downtime: Each blade replacement incurs downtime, typically about 30-45 minutes per replacement. For facilities that replace blades frequently, these periods add up, resulting in productivity losses and increased labor costs. Minimizing replacements through enhanced blade wear resistance can save thousands of dollars per year, especially in high-volume facilities.
- Lowered Replacement Costs: For companies processing harder metals, enhancing blade durability can result in 15-20% savings on replacement costs annually. This reduction not only decreases blade expenditure but also reduces the logistics and handling costs associated with frequent replacements.
- Increased Production Quality: With sharper, longer-lasting blades, cuts remain precise, reducing the risk of material waste and rework. A facility using high-durability slitting blades reports fewer incidents of material drag and burr formation, leading to improved product quality and customer satisfaction.
In summary, investing in durable roll shear blades, high-quality coatings, regular maintenance, and professional resharpening services is a cost-effective approach for companies. These strategies reduce operational expenses, minimize downtime, and contribute to a higher-quality output—resulting in a strong ROI for metal processing operations.

6.Conclusion
By understanding the factors that affect roll shear blade wear resistance and implementing strategies to enhance blade durability, companies can achieve greater efficiency and cost savings. From choosing the right materials and coatings to maintaining regular resharpening schedules, each step plays a crucial role in extending blade life and maintaining metal coil slitting line productivity.
Investing in wear-resistant, high-quality blades and regular maintenance measures ensures that slitter blades remain reliable assets in production. For professional guidance or to explore high-quality blade options, consider reaching out to a trusted blade supplier.
One Response