Introduction: Why Durability in Plastic Crusher Blades Matters
In the plastic recycling and manufacturing industries, plastic crusher blades are essential for reducing plastic waste into manageable pieces for reprocessing. However, frequent blade wear leads to high maintenance costs, frequent replacements, and production downtimes, significantly affecting efficiency and profits. For those aiming to enhance productivity while minimizing expenses, improving the lifespan of their plastic shredding blades is crucial. In this article, we’ll explore proven strategies to extend blade durability and keep your equipment operating efficiently.
1. Choose High-Quality Materials: The Foundation of Durability
The first step to improving plastic crusher blade durability is selecting the right material. Blade materials must be tough and wear-resistant to withstand the demands of crushing hard plastics. Some popular choices include:
- SKD-11 Steel: Known for its balance between hardness and toughness, SKD-11 steel can handle intensive crushing tasks without frequent chipping or wear.
- High-Speed Steel (HSS): This material is ideal for high-impact applications and is valued for its durability and resistance to wear.
- Tungsten Carbide Coated Steel: Often used in plastic grinding blades, this material combines extreme hardness with a high tolerance for friction and wear.
Choosing a material with suitable hardness and toughness not only enhances the blade’s lifespan but also reduces the need for frequent replacements, cutting down on operational costs.
Pro Tip: Consider Application-Specific Materials
Different plastics demand different properties from blades. For instance, brittle materials like polystyrene may wear down blades more quickly, while softer plastics like polyethylene can cause different types of stress. By aligning the material with the blade’s intended application, you can significantly reduce wear and tear.
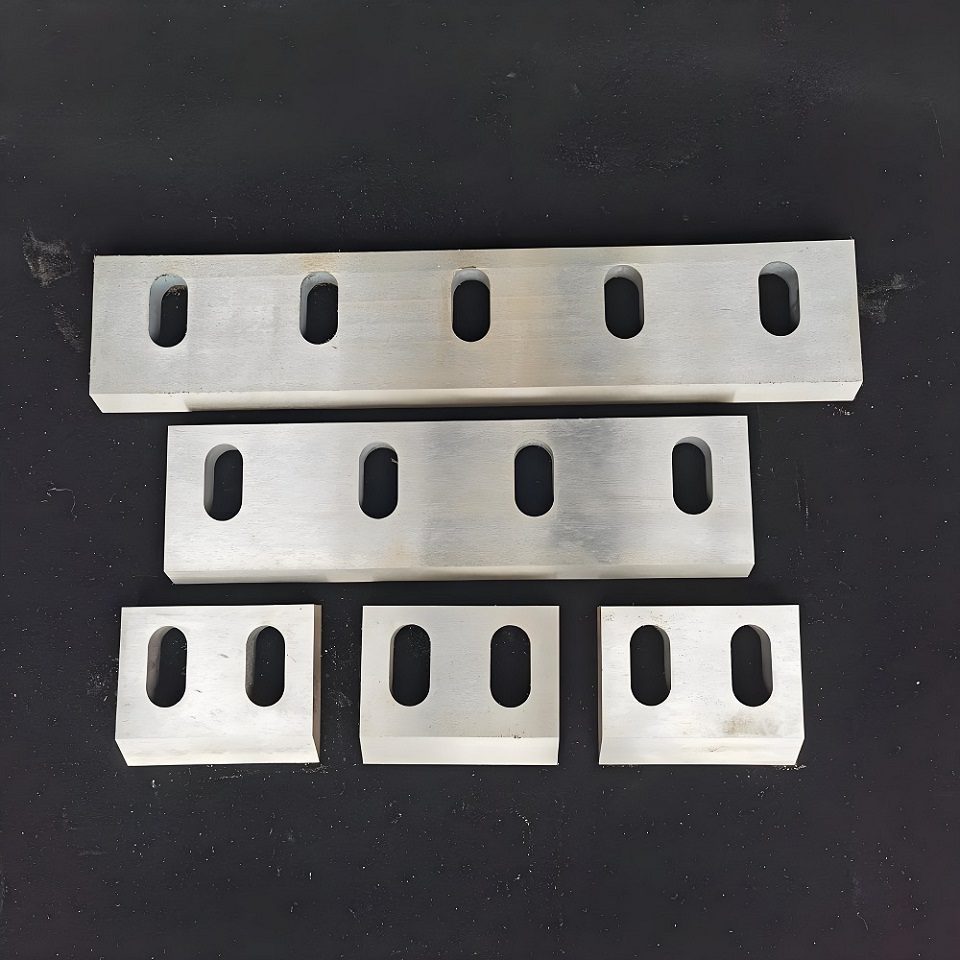
2. Optimize Blade Design for Lasting Performance
The design of plastic crusher blades directly impacts their durability, cutting efficiency, and wear resistance. Well-designed blades perform longer, reduce energy consumption, and produce finer and more consistent crushed material. When considering the design, specific elements such as blade angle, thickness, and edge type play significant roles.
Blade Angle and Shape: Striking the Balance
Blade angles affect how efficiently a blade cuts through different plastics. A study from the Journal of Materials Processing Technology indicates that optimizing the angle can improve energy efficiency by up to 15% while reducing wearmple:
- Shallow Blade Angles (25–35 degrees): Ideal for softer plastics like polyethylene, these angles offer less resistance and enable smoother cuts.
- Steeper Blade Angles (35–50 degrees): Suitable for harder plastics like ABS or PVC, steeper angles provide greater cutting force without chipping or cracking, extending blade life.
Additionally, the blade shape matters. For heavy-duty crushing, toothed edges are more effective at gripping larger plastic pieces, preventing material slippage, which reduces processing time and energy. In comparison, non-toothed edges are better for smooth, consistent cuts on smaller plastics but may wear down faster.
Thickness and Durability
Thickness also plays a role in determining how long plastic crushing knives will last. Thicker blades are generally more durable because they can withstand more impact without bending or chipping, especially under heavy loads. However, the added thickness can mean a greater need for energy to perform each cut. Optimal thickness varies by plastic type, but studies recommend a range between 6mm and 10mm for high-demand applications to ensure sufficient durability without compromising efficiency .
In ondy, blades used for PET bottle crushing showed a 20% increase in lifespan when the thickness was optimized to withstand higher pressure loads . By carefully made thickness and angle to the intended material, operators can ensure that the blades are durable yet efficient.
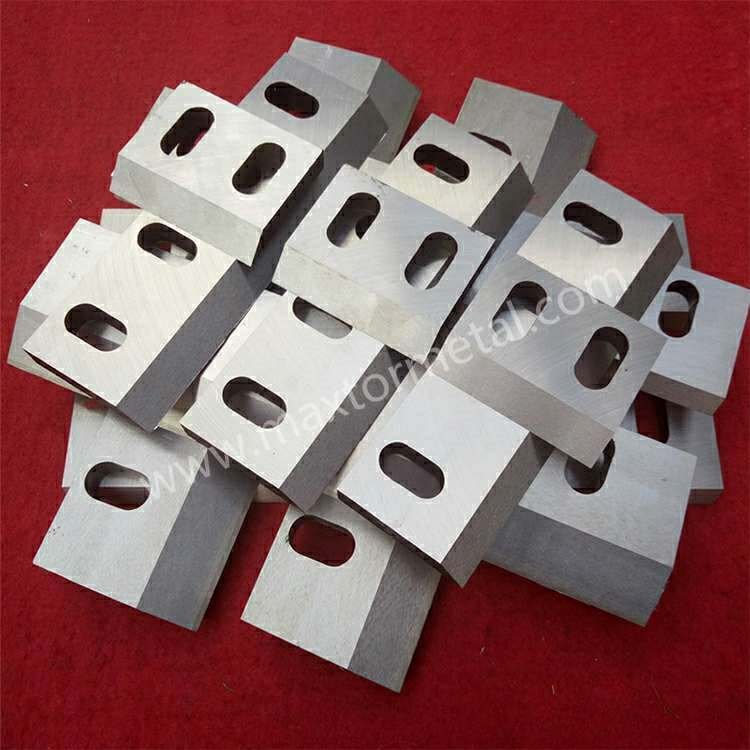
3. Maintain and Clean Blades Regularly
Routine maintenance is one of the simplest yet most effective ways to maximize plastic crusher blade lifespan. Poorly maintained blades experience friction, higher energy consumption, and increased wear, which not only shortens blade life but also raises operational costs. Studies have shown that proper blade maintenance can reduce wear rates by 30%, leading to longer service life and higher efficiency .
Daily Cleaning: Restic Residue Build-Up
1.Plastic residue build-up on blades increases friction, dulls cutting edges, and leads to overheating. A simple daily cleaning routine helps prevent these issues. Studies from industrial settings suggest that a 5-minute cleaning routine can decrease the likelihood of plastic residue buildup by over 40% and extend blade life significantly . Here’s a basic cleaning proceduree a Soft Brush or Compressed Air: Remove plastic debris from the blade surface.
2. Apply a Solvent: For sticky or melted plastic, use a safe solvent that can dissolve residues without affecting the blade material.
3. Rinse and Dry: Finish by wiping down the blade with a clean cloth to ensure no solvent residue remains, which could cause corrosion.
Lubrication: Reducing Friction for Smoother Operation
Friction between the blade and the material is a leading cause of blade wear. Regular lubrication can help reduce friction, which allows the blades to remain sharp and effective for longer. Using a specialized lubricant once a week, particularly if crushing abrasive plastics, can reduce the friction factor by up to 50% and improve cutting efficiency.
Regular Blade Inspections: Early Damage Detection
Conducting blade inspections weekly or bi-weekly allows operators to identify any potential cracks, chips, or dents. Small imperfections can worsen if not addressed, leading to increased maintenance costs. Industry data indicates that identifying and repairing small chips early can reduce total maintenance costs by nearly 25% compared to reactive maintenance .
By integrating a consistent maintenance sperators can keep plastic crusher cutting tools in optimal condition, ensuring longer blade life and fewer operational interruptions.
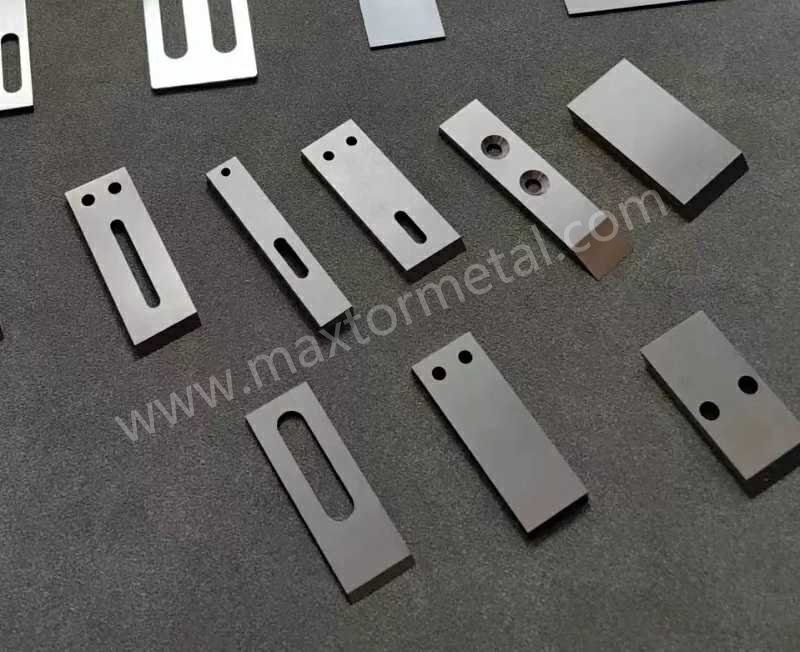
4. Proper Installation and Use: Prevent Abnormal Wear
Incorrect installation and improper use are common causes of premature wear in plastic crushing knives. Blade alignment, securing, and tension all play roles in determining whether the blade will last or degrade quickly.
Installation Best Practices:
- Ensure Proper Alignment: Misaligned blades increase the risk of uneven wear and make crushing tasks more difficult, which also puts extra stress on the equipment.
- Correct Blade Tensioning: Overly tight or loose blade tension can lead to fast wear. Make sure blades are secured according to manufacturer guidelines.
- Avoid Overloading: Overloading the machine with too much plastic at once puts excessive strain on the blades, leading to quicker degradation.
Training operators on the correct installation techniques and plastic grinding blade usage can prevent costly errors and unnecessary blade replacements.
5. Apply Coatings and Heat Treatments for Extra Protection
For operations handling a wide range of plastics, adding protective coatings or using advanced heat treatments can significantly enhance blade durability. These technologies improve the hardness, corrosion resistance, and toughness of plastic shredding blades, helping them endure harsher environments and high-impact applications.
Coating Options for Improved Blade Performance
Coatings are highly effective for enhancing blade lifespan. A study on tool wear in recycling equipment found that coated blades performed up to 60% longer than non-coated blades under the same conditions . Some effective coatings include:
- Titanium NitrCoating: Known for its extreme hardness, TiN reduces friction and offers wear resistance, making it ideal for harder plastics like HDPE or PVC. TiN-coated blades can last up to 50% longer in high-friction environments compared to uncoated blades.
- Diamond-Like Carbon (DLC) Coating: For applications involving abrasive materials, DLC offers excellent wear resistance and can extend blade life by 40% to 60%.
- Ceramic Coating: Often used in high-wear settings, ceramic coatings increase the blade’s resistance to temperature and corrosion, essential for applications where plastic grinding creates high friction heat.
These coatings are especially valuable in high-wear environments, and choosing the right one depends on the materials being processed and the desired blade lifespan.
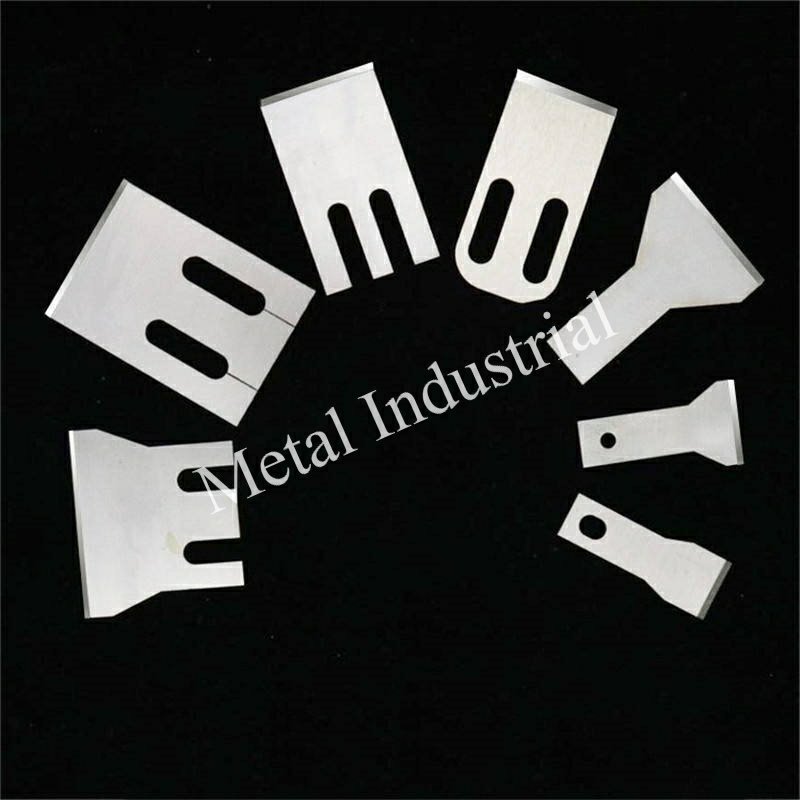
Heat Treatments to Strengthen Blade Structure
In addition to coatings, heat treatments like nitriding and cryogenic treatment can enhance blade hardness and toughness.
- Nitriding: A common choice for improving blade durability, nitriding diffuses nitrogen into the steel surface, increasing hardness without making the blade brittle. Research shows that nitrided blades can experience up to 30% slower wear rates under heavy-duty conditions .
- Cryogenic Treatment: By cooling blades to extreme low es, cryogenic treatment helps relieve internal stresses in the blade material, making it less prone to cracking under heavy loads. Studies have demonstrated that cryogenically treated blades have up to 2 times the lifespan of untreated blades when used in demanding plastic shredding applications .
Choosing the Right Treatment for Your Needs
The type of plastiess should guide your selection of coatings and heat treatments. For example:
- For soft plastics: Titanium nitride coating may be sufficient to extend lifespan without adding excessive hardness.
- For abrasive materials: Ceramic or DLC coatings, combined with cryogenic treatment, provide durability and toughness needed for high-impact crushing.
Incorporating the right combination of coatings and treatments based on the processing environment will help plastic crusher blades withstand high wear conditions, offering both economic and performance benefits.
6. Implement a Planned Replacement Strategy
Even the best industrial plastic cutting blades will eventually require replacement. Waiting until a blade is completely worn down can cause other operational issues, including increased downtime and potential damage to the machinery. Implementing a replacement plan ensures you have fresh blades ready to keep production flowing smoothly.
Steps for an Effective Replacement Strategy:
- Track Usage Time: Monitor how many hours or cycles each blade operates before it needs replacement.
- Replace Based on Plastic Type: Softer plastics may require less frequent replacement, while harder or abrasive materials will wear blades down faster.
- Schedule Downtime for Maintenance: Plan blade replacements during scheduled maintenance to minimize downtime.
A replacement plan not only extends the operational life of each blade but also ensures your plastic crushing equipment remains in optimal condition.
By leveraging high-quality materials, optimized design, routine maintenance, and advanced coatings, companies can achieve longer blade life, reduced operational costs, and better performance from their plastic shredding equipment.
Conclusion: Boosting Blade Durability Improves Efficiency and Lowers Costs
Increasing the durability of plastic crusher blades is not only about cutting costs—it’s about optimizing productivity, maintaining consistent operation, and minimizing downtime. By focusing on high-quality materials, optimized design, regular maintenance, and the right treatments, companies can significantly extend blade lifespan and improve overall equipment efficiency.
For those interested in maximizing their equipment’s lifespan and efficiency, consider evaluating your current plastic shredder blades and consult with a professional supplier to find blades that best meet your operational needs. Taking these steps will ultimately save money, reduce maintenance needs, and enhance production efficiency.