Summary:
Precision in cutting is critical for industries using circular slitting blades, impacting everything from material efficiency to product quality. This article explores effective ways to enhance cutting accuracy by selecting the right blade material, optimizing setup, maintaining blade condition, and choosing a reliable supplier.
1. Why Cutting Accuracy Matters
In industries where precision cutting is essential, the accuracy of a circular slitting blade can significantly impact productivity and product quality. Precise cuts reduce material waste and ensure a smooth, efficient manufacturing process, particularly in industries like paper, packaging, and metals. According to a study by the Institute of Manufacturing Technology, even a 5% increase in blade precision can lower material waste by as much as 10% annually. Understanding the factors that influence blade precision and implementing strategies to improve accuracy directly benefits businesses by reducing costs and increasing output quality.
2. Factors Affecting the Cutting Precision of Circular Slitting Blades
Precision is influenced by various factors, including the blade’s material, sharpness, wear level, and the accuracy of the setup. Each of these areas can either enhance or reduce the cutting efficiency of a circular slitting blade. Understanding and optimizing these factors is essential for maintaining high accuracy, reducing material waste, and boosting operational efficiency.
2.1 Blade Material
The material used in circular slitting blades plays a major role in determining cutting precision. High-speed steel (HSS) and carbide are two of the most commonly used materials. HSS blades offer excellent flexibility and are resistant to impact, making them ideal for softer materials such as paper or plastics. Conversely, carbide blades, with a hardness rating of approximately 90 HRC (Rockwell Hardness Scale), provide exceptional durability and are better suited for tougher materials like metal and composites. Studies reveal that carbide blades last up to 10 times longer than standard steel blades in abrasive applications, reducing the frequency of replacements and enhancing cutting consistency over time.
Additionally, materials like tungsten carbide, which combine extreme hardness and resilience to high temperatures, further improve cutting accuracy, especially when processing challenging or heat-sensitive materials. For example, when cutting stainless steel, using carbide-tipped blades can achieve 15% higher precision compared to high-speed steel blades, due to their ability to maintain sharpness longer under stress.
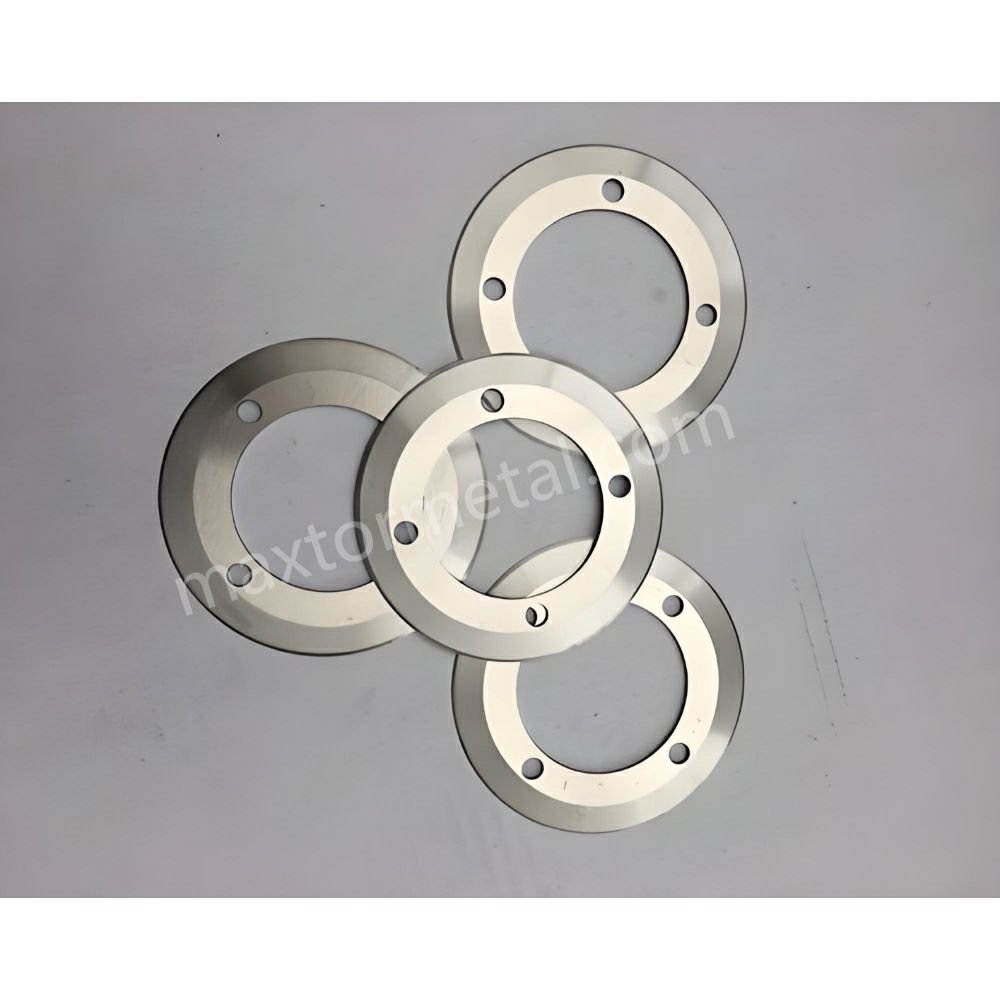
2.2 Sharpness and Wear Level
Blade sharpness directly impacts cutting accuracy. A study by the Precision Metalforming Association found that cutting errors can increase by as much as 25% when blade wear exceeds 20%. A dull blade requires more pressure to achieve a clean cut, increasing the risk of material displacement, edge fraying, or unintended bends. Implementing a maintenance schedule that involves routine blade sharpening or replacement after a certain number of cuts is critical for avoiding such issues. For example, setting a sharpening schedule every 50,000 cuts for standard materials and every 20,000 cuts for harder materials can ensure a consistently sharp edge.
Moreover, advancements in blade coatings, such as titanium nitride (TiN) and diamond-like carbon (DLC), extend sharpness and reduce wear. TiN-coated blades, for instance, have shown a 30% increase in lifespan in high-intensity cutting environments, maintaining precision over more extended periods without compromising the blade’s edge.
2.3 Precision in Blade Setup and Mounting
The way a circular slitting blade is mounted has a major impact on cutting precision. Even a 0.1 mm misalignment can result in uneven cuts and waste of material. Proper installation using laser-alignment tools can reduce error rates by 20%, improving production accuracy. For instance, metal-cutting facilities using laser-aligned rotary shear blades reported a 15% reduction in edge defects and a 10% improvement in cutting speed.
Blade balance is another critical factor. A blade that is even slightly off-balance or loosely mounted will vibrate, which disrupts precision and increases the chance of mechanical wear. Achieving a balanced blade mount often requires using precision holders with a clamping force tolerance of less than 0.5 mm. Such adjustments, although minor, can make a significant difference in high-precision settings.
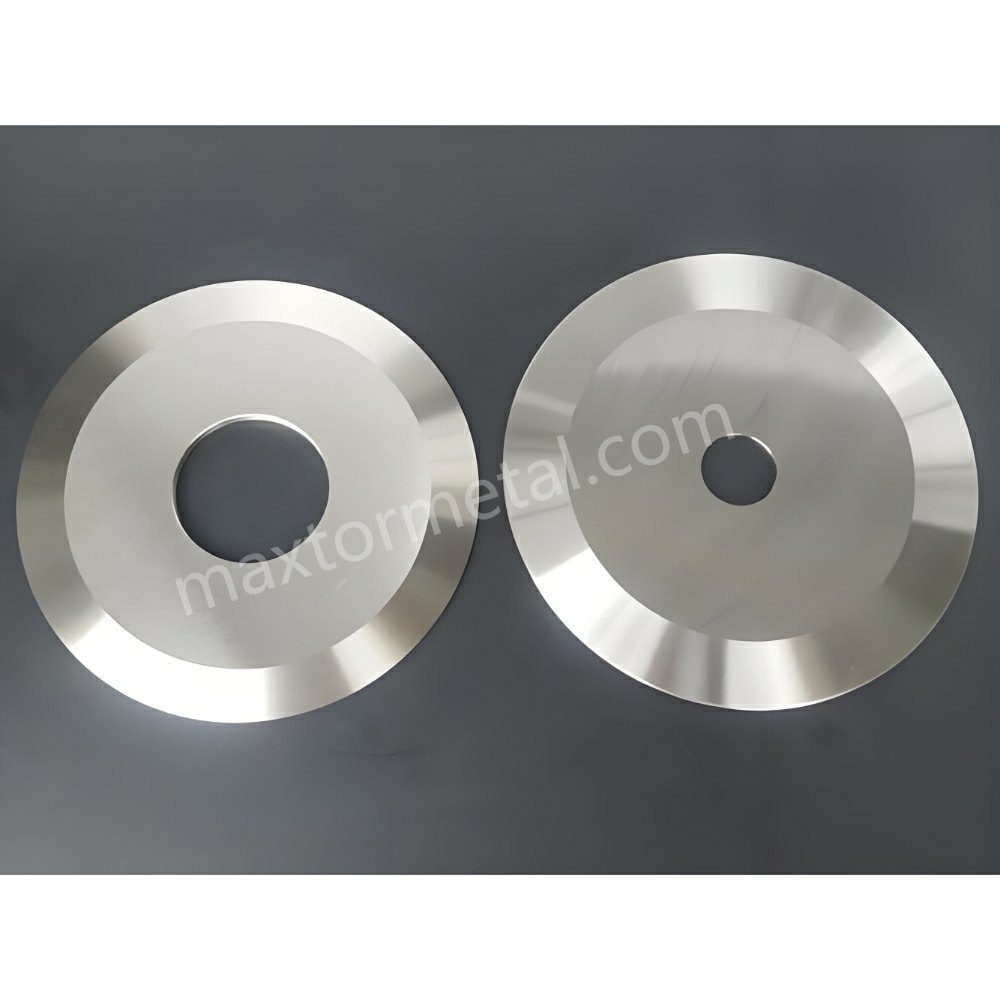
3. Practical Tips to Improve Cutting Precision
Improving the accuracy of circular slitting blades requires choosing the right blade type, optimizing the equipment and blade fit, and leveraging advanced technology. These steps reduce the likelihood of inaccuracies and enhance the overall efficiency of the production process.
3.1 Choosing the Right Blade Type and Specifications
Selecting the appropriate blade diameter, thickness, and edge angle for each material type is essential. For instance, when cutting soft materials like foam or rubber, a thinner blade with a sharper edge angle can minimize drag, resulting in smoother cuts. Conversely, for harder materials such as steel or glass, thicker, more durable blades are preferable. Studies indicate that using properly specified blades for the material at hand can increase cutting precision by as much as 25%.
In addition, the geometry of the blade edge impacts cutting accuracy. For instance, beveled edges are ideal for cutting layered materials, as they minimize resistance. A double-bevel blade with a 30-degree angle on each side provides optimal results in precision cutting of plastics, improving cut quality by around 20% compared to single-bevel edges.
3.2 Optimizing Equipment and Blade Fit
Precise blade-to-equipment fit reduces vibration, a common cause of cutting inaccuracy. For instance, adjustments in blade stabilization reduce deviation by up to 18% in high-speed applications. Many industrial facilities achieve this by using blade holders with hydraulic clamping systems that provide higher stability compared to mechanical clamps. A study by the International Association of Industrial Cutting found that hydraulic clamping systems improve cutting stability by up to 25%, ensuring clean, accurate cuts.
Moreover, using shock absorbers in the mounting setup can further stabilize the blade. Shock absorbers reduce oscillations and help maintain even blade pressure, which is particularly beneficial in high-speed applications where even minor vibrations can lead to material waste.
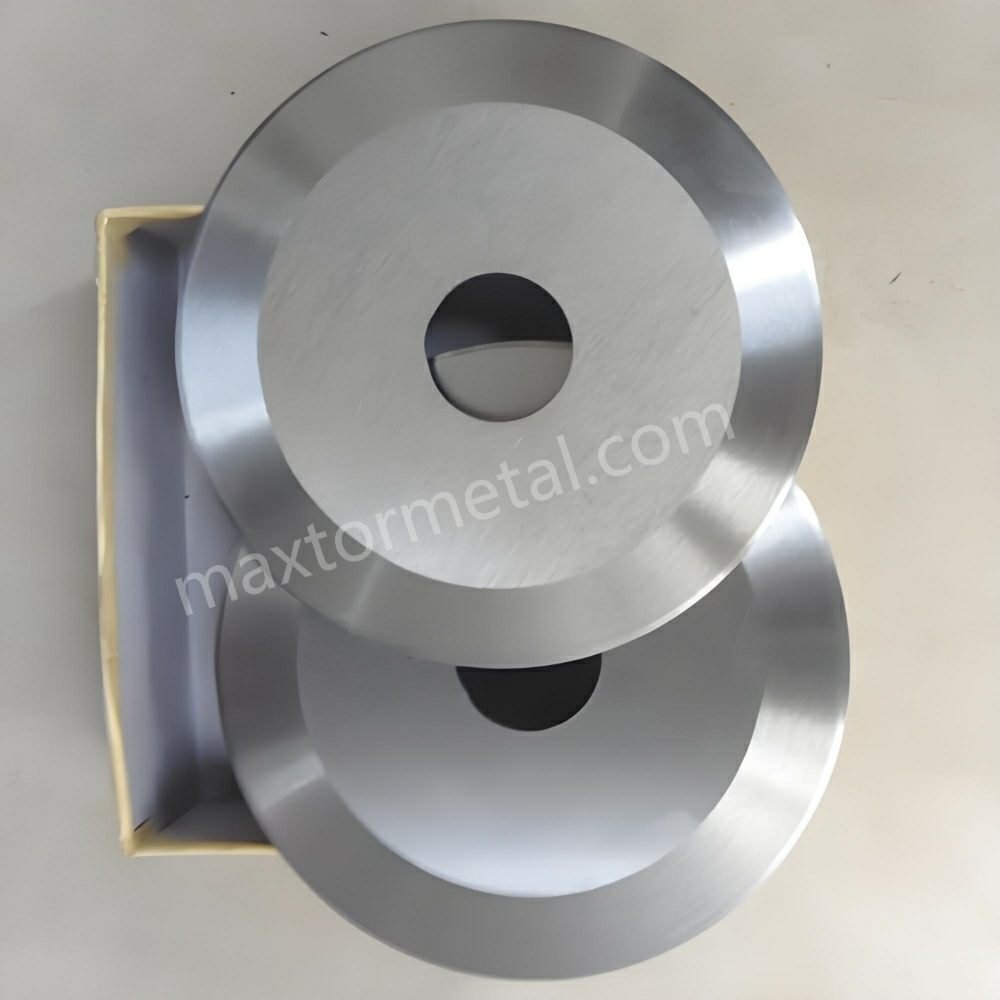
3.3 Advanced Cutting Technology for Higher Precision
Adopting advanced technologies like automated blade positioning or laser-guided cutting systems greatly enhances precision. Automated systems adjust the blade’s position with extreme accuracy, accounting for even slight variations in material thickness. These systems are especially effective in metalworking and automotive industries, where tolerances often need to be within ±0.05 mm. Facilities using such technology have reported an improvement in accuracy by 30%, while also achieving a reduction in material waste.
Laser-guided systems are another valuable tool, especially for cutting non-uniform materials or working with delicate substrates. Laser guidance not only improves the visual alignment but also helps avoid blade misalignment, resulting in more precise cuts and reduced rework. In textile manufacturing, where fabric edge precision is critical, laser-guided circular blades reduce errors by up to 15%.
4. Blade Maintenance: Extending Life and Ensuring Accuracy
Maintaining the condition of your circular slitting blade is essential to sustain precision and prevent costly replacements. Proper maintenance routines and scheduled replacements minimize downtime and enhance operational efficiency.
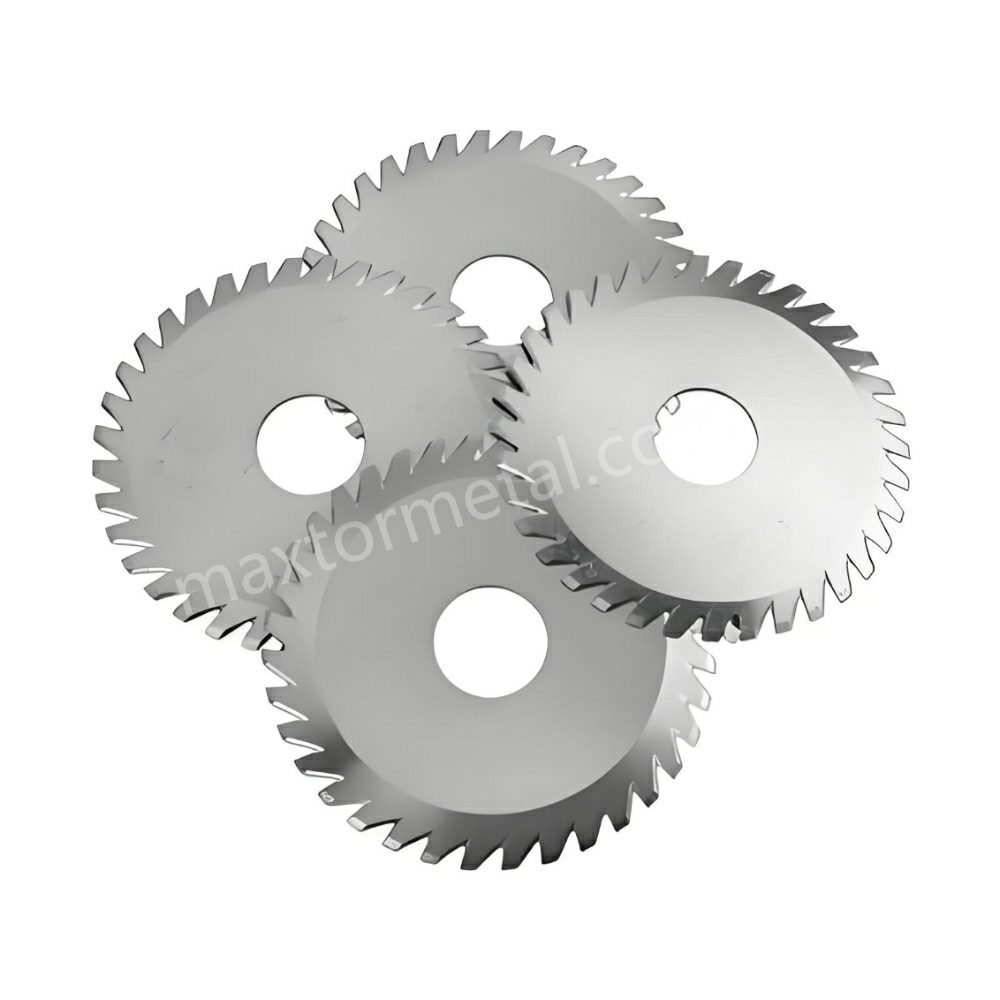
4.1 Regular Maintenance and Inspection
Regular inspection and maintenance are crucial for optimal performance. Studies show that routine cleaning and lubrication can extend blade lifespan by up to 40%. Dust, debris, and residue build-up can dull the blade faster and reduce its efficiency. For example, in food packaging applications, where blades frequently cut through adhesive materials, cleaning the blade after every 10,000 cuts has been shown to maintain cutting accuracy, improve hygiene, and reduce wear.
Additionally, applying lubricants reduces friction and extends blade sharpness. In metal cutting, regular lubrication reduces wear by around 25%, allowing for smoother cuts and lower replacement costs.
4.2 Scheduled Blade Replacement
Every blade has a limited lifespan, regardless of maintenance. Blades used beyond their optimal wear limit often produce irregular cuts, which can reduce production quality and waste materials. Industry standards suggest replacing blades every three months or after a specific number of cuts—whichever comes first. A recent industry survey revealed that companies following a 90-day blade replacement schedule experience 20% fewer cutting errors, minimizing costly rework and improving efficiency.
5. Selecting a High-Quality Circular Slitting Blade Supplier
The choice of supplier is crucial for ensuring consistent blade quality. High-quality suppliers typically provide materials tested to meet rigorous industry standards and can offer guidance on the best blade types for specific applications.
5.1 Evaluating Quality Assurance and Compliance
When selecting a supplier, look for quality certifications such as ISO 9001, which indicates a commitment to quality and consistency. Suppliers with ISO certification often have lower defect rates due to stringent quality control processes. For example, manufacturing plants that work exclusively with ISO-certified suppliers reported a 15% increase in production accuracy due to the reliability of their blades.
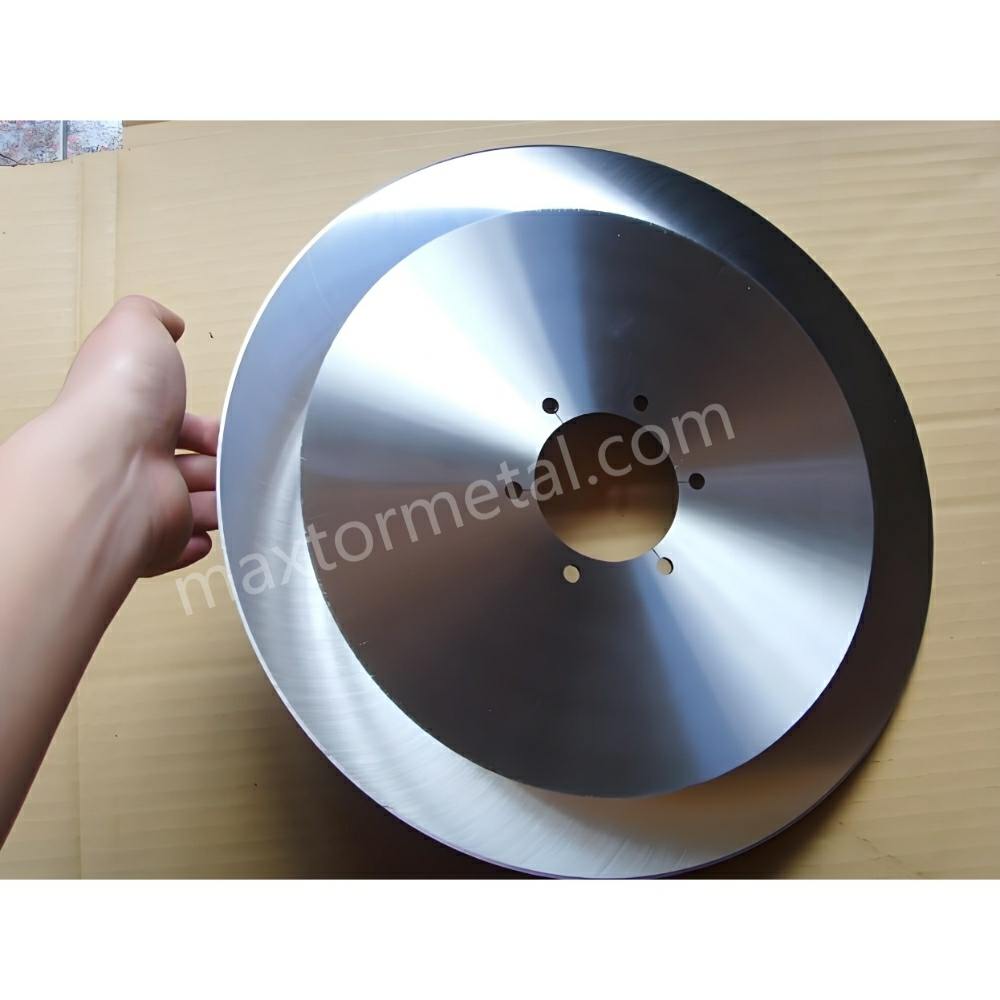
5.2 Prioritizing Technology and Innovation
A supplier invested in advanced manufacturing technologies can offer blades with superior durability and precision. Modern production methods, such as CNC machining and laser-cutting technologies, ensure that blades are manufactured with high tolerances. Studies show that blades produced with CNC machining exhibit a 20% increase in durability, providing more precise cuts over a longer period.
5.3 Customer Support and Service Guarantees
Reliable customer support is an essential consideration. Suppliers who offer comprehensive after-sales services, including blade customization and technical support, provide added value that helps customers achieve better cutting outcomes. Companies with dedicated customer support and blade replacement services experience a 10% increase in production efficiency due to reduced downtime and immediate solutions for any blade issues.
6. Conclusion: Enhancing Efficiency through Precision
Improving the precision of your circular slitting blade operations can greatly enhance your overall efficiency, product quality, and material usage. By selecting the appropriate blade materials, ensuring accurate setup, and maintaining blades regularly, companies can enjoy longer blade life and improved accuracy in cutting.
Partnering with a high-quality supplier further assures that you receive reliable, durable blades suited for your specific needs, leading to consistent precision in production. For businesses that rely on precise cutting processes, these strategies are essential to stay competitive and deliver exceptional quality.