Summary
Maintaining the sharpness of a slitter blade is essential for achieving precise cuts, minimizing downtime, and improving operational efficiency. This article explores why sharpness retention matters, factors affecting blade longevity, advanced techniques for durability, and best practices for maintenance, ensuring your cutting tools perform at their best.
Introduction
In industrial applications, precision cutting is the cornerstone of efficiency and quality. The slitter blade, a critical component in industries like paper, metal, and plastic processing, must remain sharp to perform effectively. Dull blades lead to uneven cuts, wasted material, and costly downtime. This article delves into the technologies and strategies to retain the sharpness of slitting tools, helping you optimize performance and reduce costs.
By understanding the factors influencing blade sharpness and adopting advanced techniques, you can ensure your operations run smoothly. Let’s explore how you can keep your slitter blades sharp and effective for longer periods.
Why Sharpness Retention Matters for Slitter Blades
Sharpness plays a critical role in ensuring the efficiency and precision of industrial cutting processes. Whether you are cutting thin plastic films, thick metal sheets, or delicate paper rolls, maintaining a sharp edge on your slitter blade is essential. Let’s examine the specific impacts dull blades have on your operations:
1. Uneven Cuts
Dull blades fail to create clean, consistent edges, which can compromise the quality of the final product. For example, in the paper industry, jagged edges can lead to product rejection, affecting customer satisfaction and brand reputation. According to industry reports, manufacturers using dull blades experience up to 15% more defective products than those using well-maintained cutting tools.
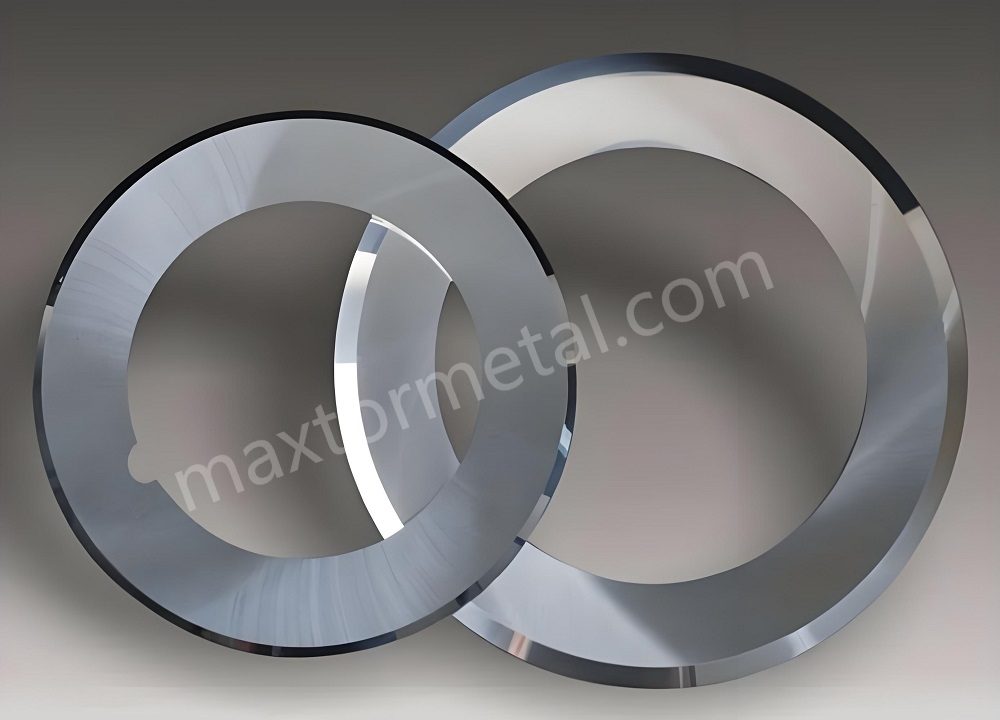
2. Material Waste
Poor sharpness often results in inaccurate cuts, generating excess material waste. In industries handling expensive raw materials like aluminum or specialty polymers, this waste can represent significant financial losses. A study in a metal processing plant found that switching to precision-sharpened slitting knives reduced scrap rates by 25%, saving approximately $100,000 annually.
3. Increased Wear on Equipment
Using a dull blade requires more force to achieve the same cuts, which puts undue stress on machinery. Over time, this can lead to faster wear and tear on mechanical components, increasing maintenance costs and the risk of equipment failure. Preventive maintenance through blade sharpness retention can lower machine repair expenses by 20%.
4. Downtime for Maintenance
Frequent blade sharpening or replacement interrupts production schedules, resulting in costly downtime. In high-volume production environments, even an hour of unscheduled maintenance can translate into thousands of dollars in lost revenue. Maintaining sharper blades significantly extends service intervals, keeping your operations running smoothly.
The Competitive Edge
Maintaining sharp blades is more than just a technical necessity—it’s a strategic advantage. Companies that invest in blade sharpness retention report up to 30% better operational efficiency, giving them an edge in competitive markets.
Keep reading to explore the factors affecting sharpness and how to address them.
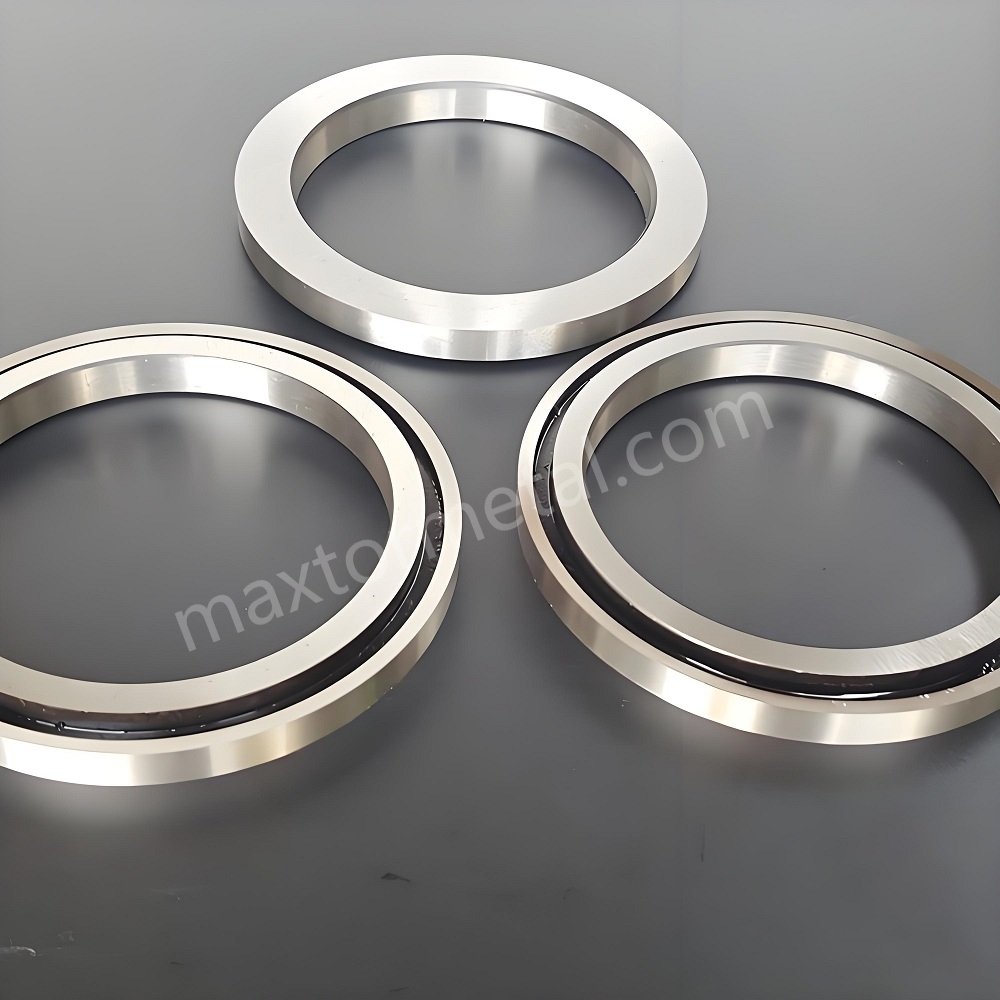
Key Factors Affecting Slitter Blade Sharpness
1. Blade Material
Blade composition significantly affects sharpness retention. High-grade alloys such as M2 tool steel, tungsten carbide, and ceramic composites offer excellent hardness and durability. A coated slitting blade can last twice as long as an uncoated one under similar conditions. For example, tungsten carbide-coated blades can withstand up to 500,000 cuts before requiring sharpening, compared to just 250,000 for standard steel.
2. Cutting Environment
The type of material being processed greatly influences blade wear. Harder materials like steel generate more friction and heat, which can quickly degrade blade edges. Additionally, cutting plastics or rubber often produces sticky residues that dull blades faster if not cleaned properly. Addressing these environmental factors with proper lubrication and cleaning can extend blade life by up to 40%.
3. Maintenance Practices
Inadequate blade maintenance is a major factor in premature dulling. For instance, incorrect sharpening angles can weaken the blade edge, while poor cleaning techniques may leave residues that accelerate wear. Implementing systematic maintenance schedules helps ensure consistent blade performance.
4. Innovative Blade Design
Advanced blade designs optimize edge geometry for specific applications. For example, beveled edges reduce cutting resistance and friction, improving durability. Laser-precision manufacturing techniques can achieve tolerances as fine as 0.001mm, creating sharper, more reliable blades.
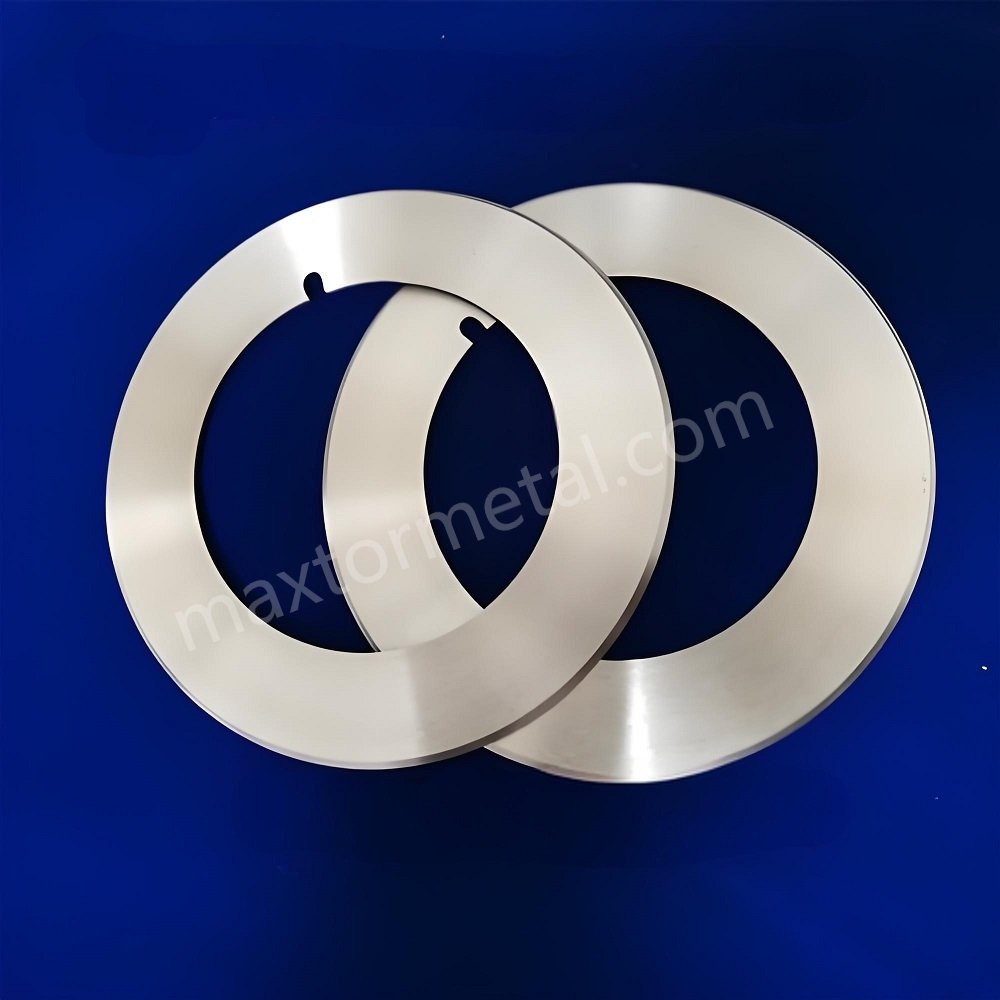
Advanced Techniques to Prolong Slitter Blade Sharpness
1. Coating Technologies
Special coatings protect blade surfaces from wear and corrosion. For example, titanium nitride coatings increase surface hardness, allowing blades to retain sharpness 50% longer in high-speed operations. Similarly, diamond-like carbon coatings reduce friction, lowering operational temperatures and improving edge retention.
2. Cryogenic Treatment
Cryogenic processing aligns the internal structure of metals, enhancing their hardness and resistance to wear. Studies show that cryogenically treated industrial cutting tools last 30% longer than untreated blades in heavy-duty environments.
3. Precision Grinding and Sharpening
Grinding machines capable of maintaining a consistent edge angle ensure that the blade delivers smooth, precise cuts. Automated sharpening systems eliminate human error, providing consistent results that increase blade longevity by up to 20%.
4. Custom Blade Design
Tailored blade solutions enhance performance for specific applications. For example, rotary knives designed for textile cutting may feature serrated edges to minimize wear while ensuring clean cuts. Custom designs reduce maintenance frequency and improve process efficiency.
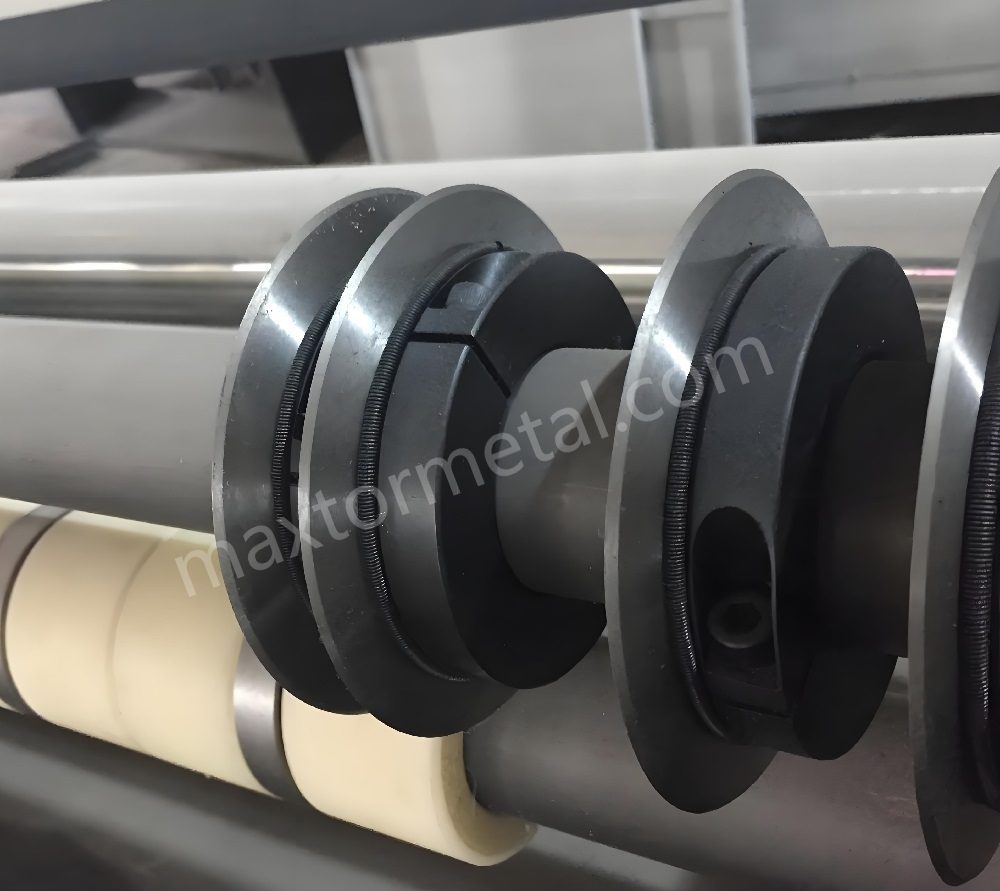
Maintenance Best Practices to Retain Blade Sharpness
Routine care and attention can drastically extend the lifespan of your slitting knives.
1. Routine Inspections
Perform regular checks for visible damage, including nicks, burrs, or uneven wear. An inspection log helps identify patterns and predict when blades require sharpening or replacement.
2. Proper Cleaning
Use non-abrasive tools and solvents to remove residues after each use. For example, a specialty blade-cleaning solution can reduce buildup by 50%, minimizing the risk of dulling.
3. Lubrication
Choose a lubricant that matches the cutting environment. For example, water-based lubricants are effective for heat-sensitive applications, while oil-based options are ideal for heavy-duty metal cutting. Proper lubrication reduces friction, extending blade life by 15%-25%.
4. Correct Storage
Preventing physical damage during storage is crucial. Blades should be kept in dry, temperature-controlled environments, and protective covers should always be used.
5. Operator Training
Ensure operators understand proper blade handling techniques, such as avoiding direct contact with edges and correctly aligning blades during installation. Trained staff are less likely to cause accidental damage, reducing blade replacements by up to 10%.
By adopting these best practices, you can ensure peak performance from your cutting tools.
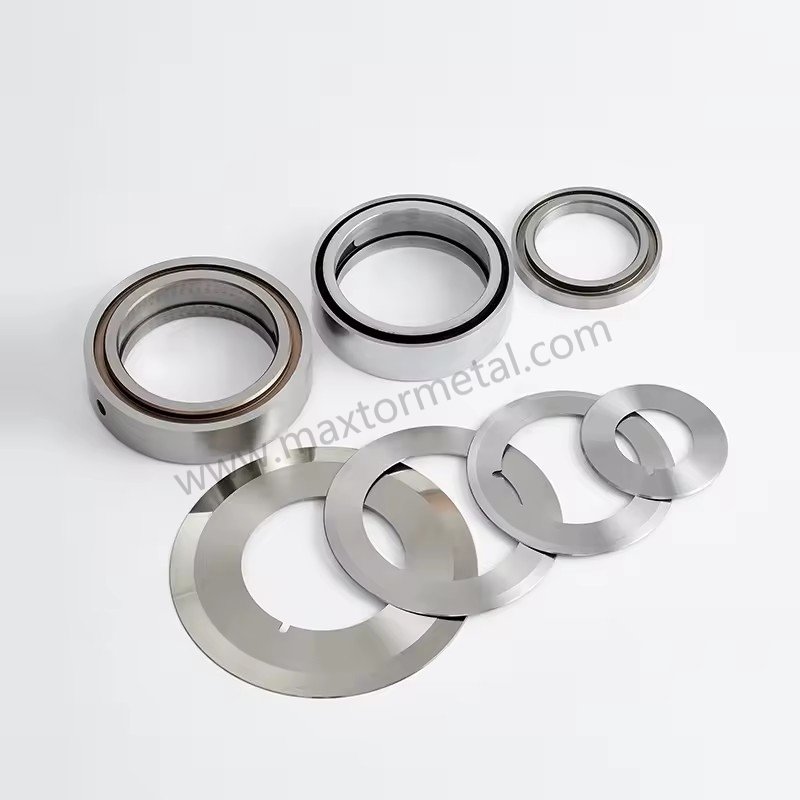
How Our Slitter Blades Stand Out in Sharpness Retention
At [Your Company Name], we prioritize precision and durability in every slitter blade we manufacture. Here’s why our products excel:
- Superior Materials: Our blades are crafted from premium alloys and coated with cutting-edge technologies to ensure unmatched sharpness retention.
- Advanced Manufacturing: We use precision grinding and laser cutting to create blades tailored to your specific needs.
- Proven Performance: Our blades have helped clients reduce downtime by 40% and improve product quality consistently.
Client Testimonial:
“We switched to Metal’s industrial cutting tools, and the difference was night and day. Less waste, smoother cuts, and longer blade life!” – Operations Manager, Packaging Industry
Our commitment to quality ensures that your cutting operations remain seamless and efficient.
Contact us today to learn how we can optimize your cutting processes.
Conclusion and Call to Action
Sharpness retention is the cornerstone of efficient and cost-effective cutting operations. By understanding the factors that affect slitter blade performance, leveraging advanced technologies, and following best maintenance practices, you can enhance blade durability and reduce operational costs.
Ready to upgrade your cutting tools? Discover how our advanced solutions can revolutionize your operations. Contact us today!
One Response
Maximizing blade sharpness improves efficiency and reduces waste. Looking forward to practical sharpening techniques!