Summary
Round slitter blades are essential tools in industrial cutting, but they face common issues like dulling, chipping, and corrosion. This article explores these wear problems, provides practical repair techniques, and shares tips to extend blade life, ensuring optimal performance and cost savings for your business.
Understanding Round Slitter Blade Wear
Industrial environments are demanding, and round slitter blades are constantly exposed to wear and tear. Factors like material hardness, cutting speeds, blade alignment, and maintenance routines play a critical role in the degradation process. Studies show that improperly maintained blades can lose up to 20% of their cutting efficiency within the first few months of intensive use.
For instance, high-speed operations, which are common in metal slitting, can lead to rapid dulling of edges. Similarly, abrasive materials like reinforced plastics or metallic laminates can significantly accelerate wear. Beyond usage, factors such as improper storage or insufficient cleaning often result in corrosion or blade warping.
Identifying these issues early is crucial. By doing so, operators can minimize costly downtime, avoid reduced productivity, and extend blade life significantly.
Common Wear Issues in Round Slitter Blades
Slitter blades encounter a range of wear problems. The most common are:
- Edge Dulling: Over 60% of wear issues in circular cutting knives involve dulling. A blunt edge increases resistance during cuts, reducing precision and efficiency.
- Chipping and Cracking: This is often caused by excessive mechanical stress or poor handling during installation or use.
- Corrosion: Moisture exposure or chemical residues can weaken the blade over time, compromising its structural integrity.
These wear patterns affect not only performance but also safety. A chipped or cracked blade could fail during operation, causing accidents or damaging equipment.
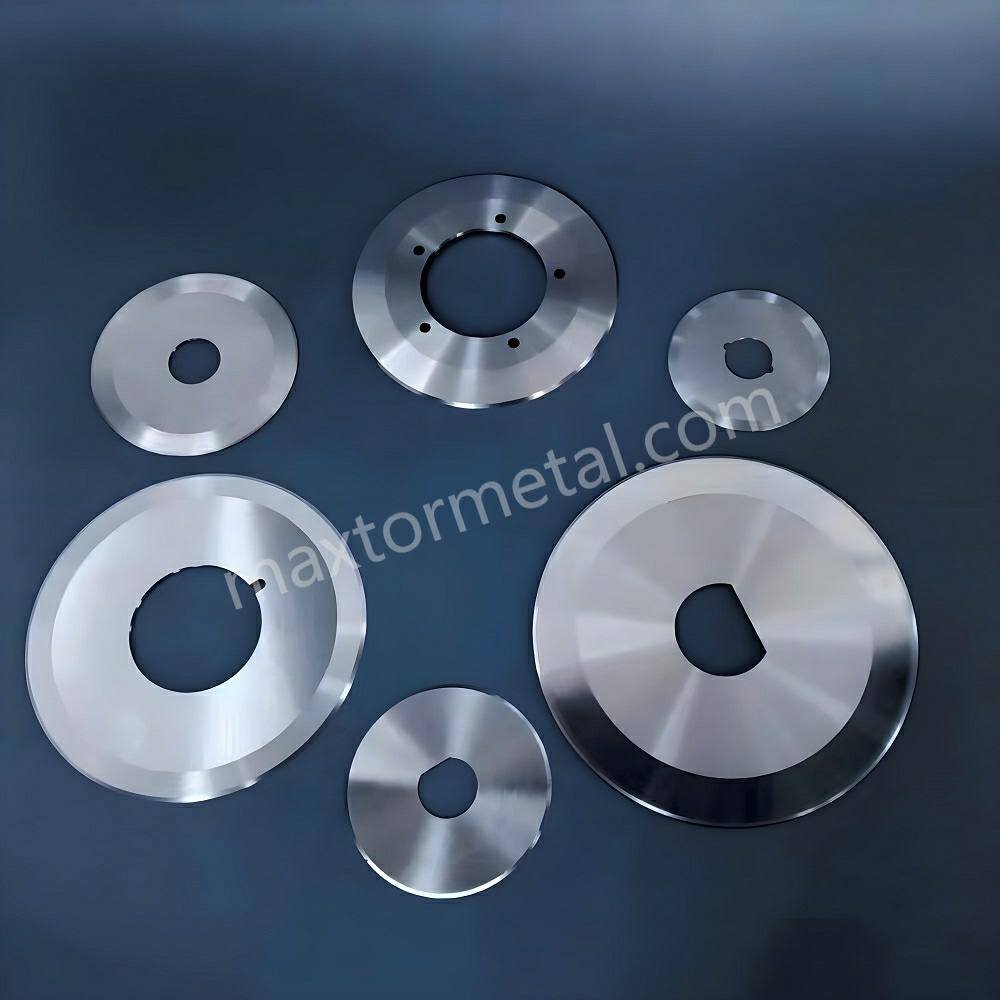
Edge Dulling: The Most Common Wear Problem
Edge dulling is the silent killer of cutting performance. When a blade’s edge loses sharpness, the quality of cuts suffers immediately. Operators often notice jagged cuts or uneven material edges, which signal the need for attention.
Data suggests that blades used in paper slitting can dull after just 10,000 operational cuts, depending on material thickness. Heat buildup from friction exacerbates this issue, softening the blade edge and further degrading performance.
Repair Tips:
- Use a precision grinding machine to sharpen edges.
- Maintain the original blade angle during sharpening for optimal results.
- Conduct regular inspections to catch dulling early and avoid costly disruptions.
Cracking and Chipping: How to Identify and Prevent It
Chipping or cracking typically stems from mechanical stress, especially when slitting tougher materials like thick plastics or sheet metal. Sudden impacts during installation or mishandling often initiate these defects.
Signs to Watch:
- Visible nicks or small fractures along the blade edge.
- Increased vibration during operation, indicating imbalance.
Prevention Tips:
- Operate at appropriate cutting speeds to avoid unnecessary strain.
- Handle blades with care during installation and storage.
For minor chips, precision grinding can remove defects. However, cracks, particularly those extending beyond the edge, often require welding or complete replacement.
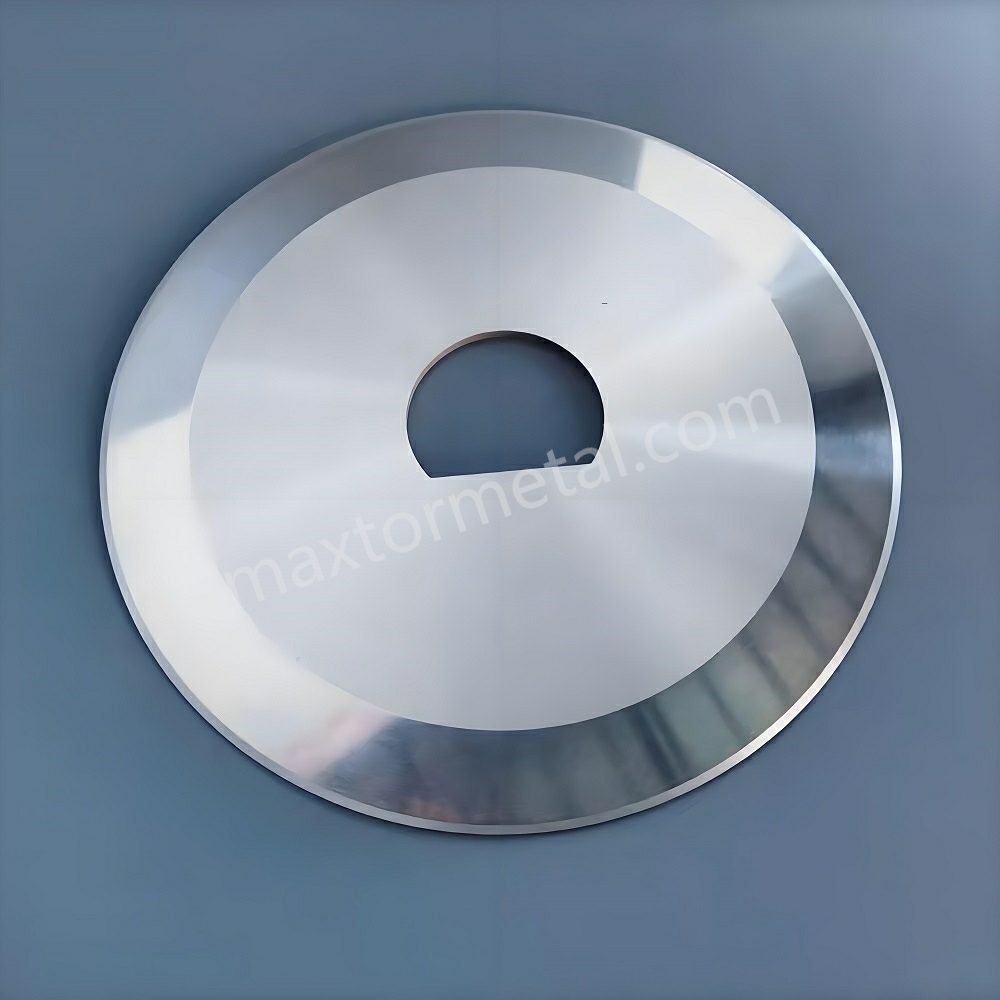
Corrosion: A Hidden Threat to Blade Longevity
Corrosion silently undermines rotary slitting blades, reducing their structural integrity and cutting performance. It often goes unnoticed until rust becomes visible or cutting efficiency drops dramatically.
Environmental conditions play a significant role. For example, blades used in humid environments or near chemicals are more prone to rust. An estimated 15% of industrial blades require early replacement due to corrosion-related damage.
Preventive Measures:
- Apply anti-corrosion coatings to the blade surface.
- Store blades in a controlled, dry environment.
- Clean blades immediately after exposure to moisture or chemicals.
How to Identify Wear Problems Early: Key Signs to Watch For
Proactive identification of wear issues can save businesses from costly production halts. Look for these signs:
- Cuts becoming uneven or jagged, which indicates dullness or imbalance.
- Increased operational noise, suggesting potential misalignment or chipping.
- Visual signs of wear like rust, cracks, or chips.
Operators who address these symptoms early can avoid larger issues, such as complete blade failure or costly equipment repairs.
When to Repair vs. Replace a Round Slitter Blade
Choosing between repair and replacement depends on the blade’s condition and operational requirements.
Consider Repair When:
- Dulling or minor chips are the primary issues.
- Repair costs are less than 50% of replacement costs.
Replace If:
- Extensive corrosion or large cracks compromise the blade’s safety.
- Blades have been repeatedly repaired but still underperform.
For instance, replacing a heavily corroded blade used in high-precision applications can prevent future quality and safety issues.
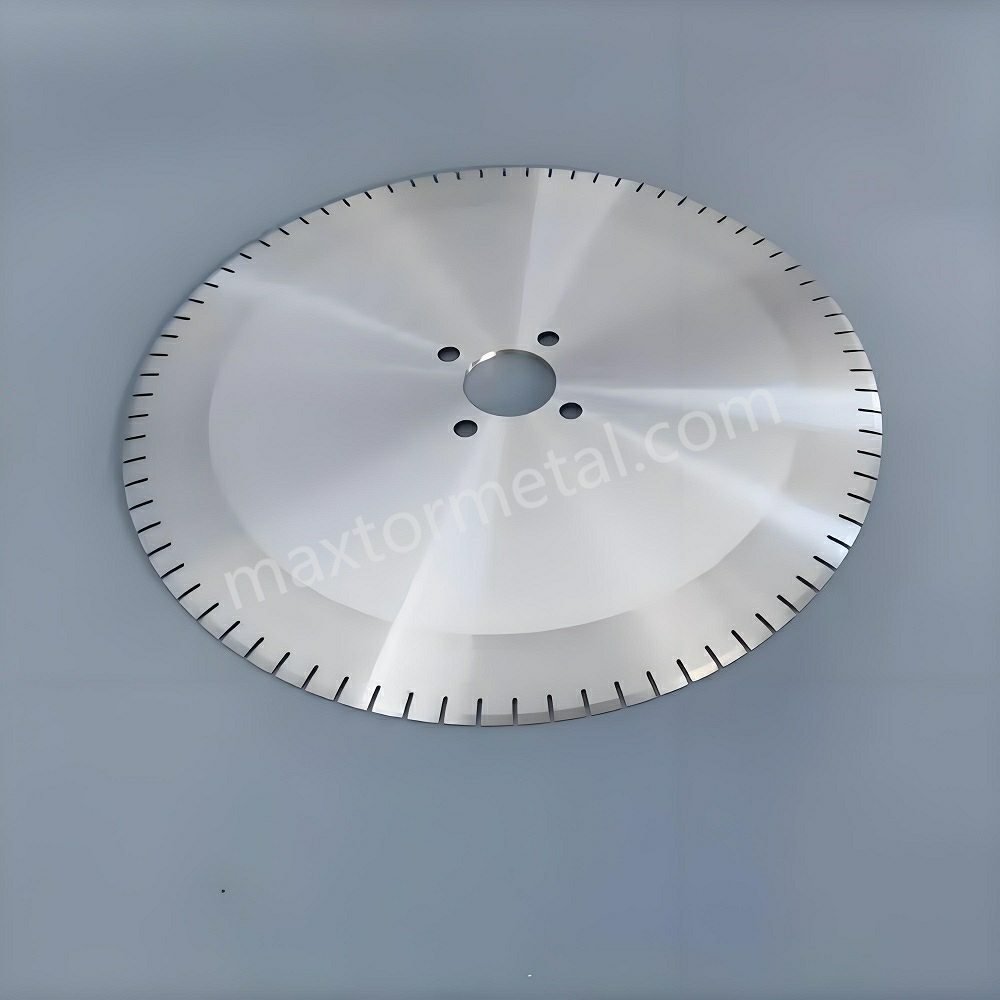
Step-by-Step Guide to Repairing Round Slitter Blades
Restoring a worn blade requires a systematic approach. Follow these steps for effective repairs:
- Inspection: Identify the extent of wear, noting cracks, chips, or dull edges.
- Cleaning: Remove residue, rust, or debris to prepare the blade for sharpening.
- Sharpening: Use high-precision grinding equipment to restore the edge.
- Balancing: Check the blade’s balance to avoid wobbling during operation.
- Testing: Perform a sample cut to ensure the blade functions correctly.
When done right, repaired blades can regain up to 80% of their original cutting performance.
Repairing Edge Dulling: Sharpening and Reprofiling Techniques
Sharpening is the most common repair method for dull edges. Advanced techniques like CNC grinding provide exceptional accuracy, maintaining blade balance and reducing wear from uneven sharpening.
Tips for Success:
- Use the correct abrasive for your blade material (e.g., diamond for tungsten carbide).
- Avoid overheating during grinding to prevent structural damage.
- Reprofile severely worn blades to restore their original geometry.
Fixing Cracks and Chips: Welding vs. Resharpening
For chipped blades, resharpening usually suffices. However, cracks require more advanced techniques like laser welding to fill the damaged area.
Steps:
- Inspect the crack to assess its depth.
- Apply laser welding for precise repairs.
- Finish with regrinding to ensure smoothness and balance.
Expert Advice: Always consult specialists for major repairs. Improper techniques can worsen the problem or reduce blade life.
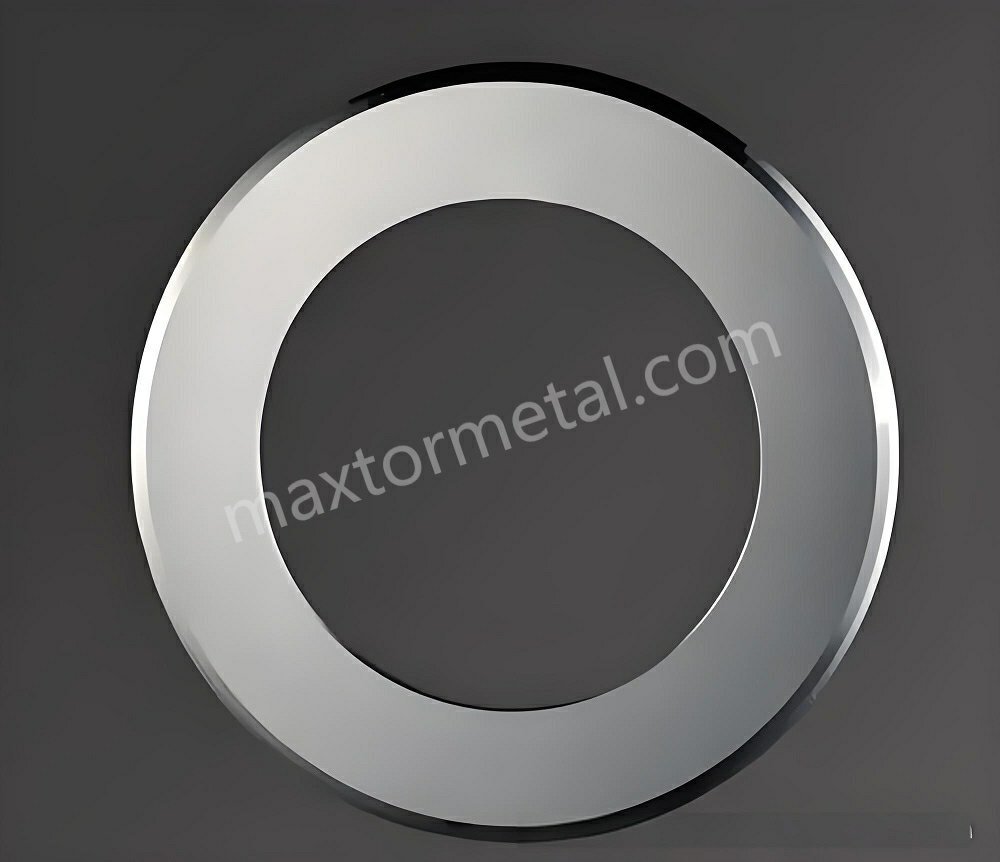
Preventing Further Wear: How to Extend the Lifespan of Slitter Blades
Preventive maintenance is the easiest way to avoid frequent repairs or replacements. Here are key strategies:
- Proper Storage: Store blades in a clean, dry area away from corrosive substances.
- Routine Cleaning: Clean blades after each use to remove debris and moisture.
- Regular Inspections: Check for signs of wear, such as dull edges or small chips, every week.
With proper care, blade lifespan can increase by 20-30%, reducing operational costs significantly.
Common Mistakes When Repairing Round Slitter Blades
Even experienced technicians can make mistakes during repairs. Avoid these errors:
- Using the wrong grinding wheel, which can damage the blade.
- Skipping the balancing process, leading to operational inefficiency.
- Overheating the blade during grinding, which weakens its structure.
Training operators in best practices can eliminate most of these issues.
Conclusion: Keeping Your Round Slitter Blades Sharp and Efficient
Round slitter blades are indispensable for industrial cutting applications. By understanding wear issues and implementing effective repair and maintenance strategies, you can maximize their lifespan and maintain optimal performance. Regular inspections and timely repairs will save costs and enhance productivity.Need expert advice on maintaining or repairing your round slitter blades? Contact us today for professional solutions!