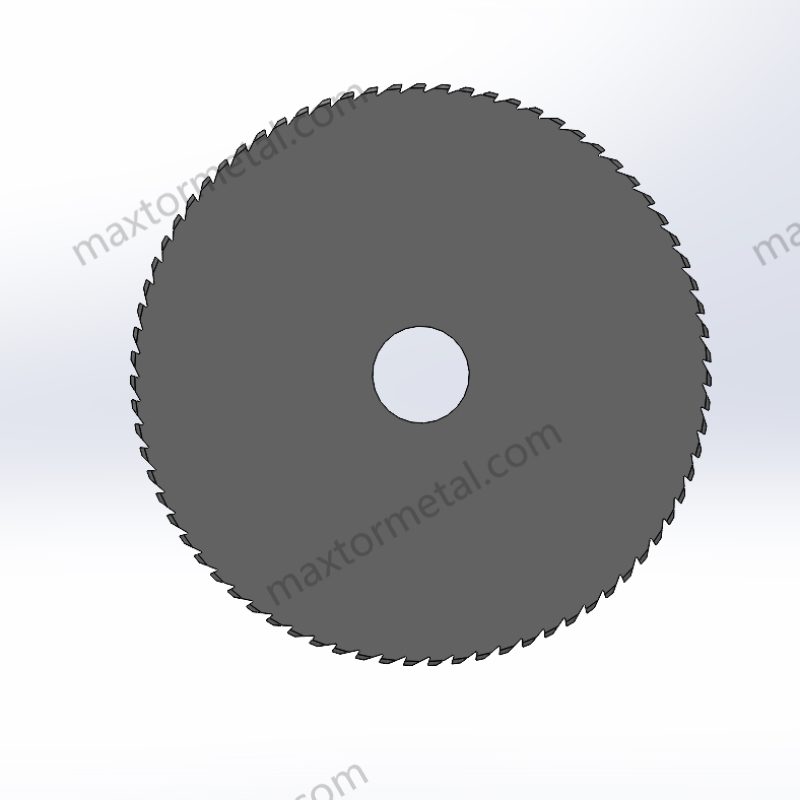
The rise of China as a global manufacturing powerhouse is undeniable. Over the years, China has transitioned from being synonymous with low-cost production to a leader in quality and innovation. One sector that exemplifies this evolution is machine knives and blades. Today, Chinese-made machine blades are renowned for their reliability, quality, and competitive pricing. This article explores why machine blades and knives made in China are the go-to choice for international clients.
I. A Global Market Leader
A Growing Presence in the Machine Blade Market
The global market for machine blades is forecasted to grow at a CAGR of 5.2% from 2023 to 2030, reaching an estimated value of $15.8 billion by 2030. China, as the largest exporter, contributes significantly to this growth. The export volume of Chinese machine blades grew by an impressive 18% year-over-year in 2022, with over 3 billion units shipped, capturing 40% of the global market share. This surge reflects China’s ability to balance quality and cost, making it a trusted source for industries worldwide.
Why China?
- Competitive Advantage: China’s large-scale industrial base and well-established supply chain infrastructure ensure cost efficiency and production agility.
- Diverse Offerings: From precision surgical knives to heavy-duty industrial knives, China caters to a broad spectrum of industries, including manufacturing, food processing, and automotive.
- Global Acceptance: According to a study by Grand View Research, over 65% of surveyed global OEMs rated Chinese blades as equal or superior in quality compared to leading Western brands.
Preferred by OEMs and End-Users
A wide variety of industries, including automotive manufacturing, metalworking, and paper production, rely on Chinese machine blades for their operations. Many global OEMs and private-label clients trust Chinese manufacturers not just for affordability, but also for their ability to meet stringent technical specifications.
II. Customer-Centric Approach
Expanding Global Reach
Chinese manufacturers are committed to meeting international demands. Many have established overseas branches and warehouses, ensuring timely delivery and localized support.
- Localized Services: From Europe to North America, Chinese suppliers offer tailored solutions and efficient logistics systems.
Emphasizing Customization
Customization has become a hallmark of Chinese manufacturers. Nearly 85% of international clients surveyed by the China Machine Tools Association reported that Chinese manufacturers provided tailored solutions to meet unique operational requirements.
- Technical Support Excellence: Chinese manufacturers often provide 24/7 virtual consultations, detailed product guides, and on-site training for complex machinery.
- Collaborative Feedback Mechanisms: Integrated feedback loops ensure continuous product improvement. For example, a packaging company in the UK reduced downtime by 30% after collaborating with their Chinese supplier to modify blade angles and coatings
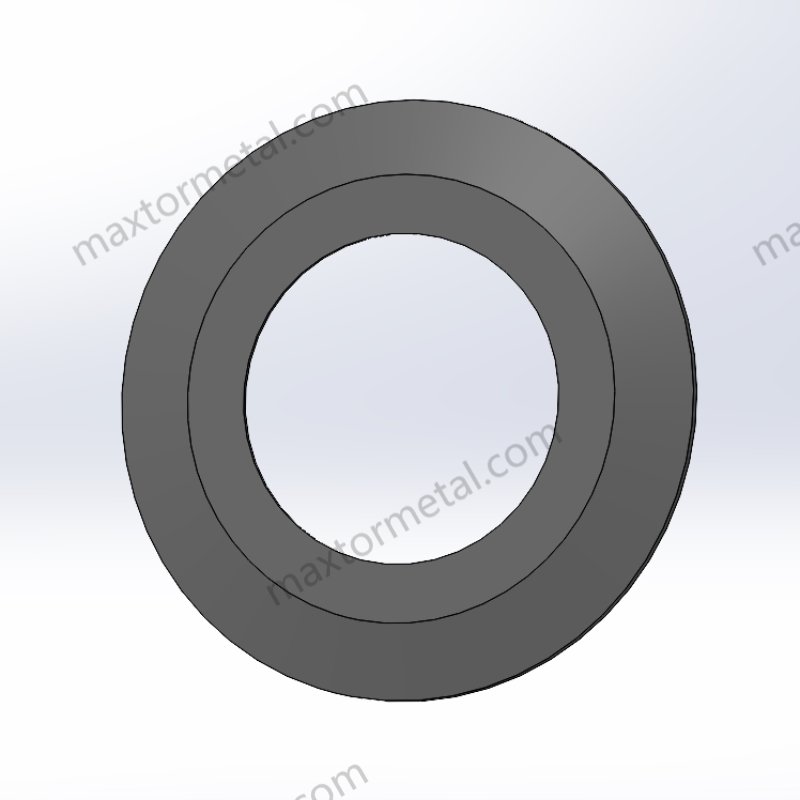
III. Innovation Driving Excellence
Advanced Manufacturing Technology
China has invested over $10 billion in high-tech manufacturing equipment since 2018, positioning itself at the forefront of machine blade innovation.
- Precision Technology: Advanced CNC (computer numerical control) machines and multi-axis grinding systems enable tolerances as low as 0.001mm, matching or surpassing international benchmarks.
- Automated Processes: Robotics integration in manufacturing plants ensures consistent quality and reduces production errors.
Performance Metrics
A comparative analysis by the International Cutting Tools Association revealed that:
- Chinese tungsten-carbide slitter blades maintain sharpness 25% longer than their European counterparts.
- Heat-treated stainless steel blades from China showed 20% higher resistance to corrosion in humid environments.
Example of Excellence
A leading U.S. food processing company reported a 30% reduction in blade replacement costs after adopting precision blades from China, enhancing their operational uptime.
IV. Material Science Breakthroughs
High-Performance Materials
Chinese manufacturers have significantly advanced the development of materials for machine blades, leveraging innovations in metallurgy, ceramics, and composite materials to meet diverse industrial needs.
1. Tungsten Carbide Development
- Properties: Tungsten carbide blades produced in China exhibit a hardness of up to 90 HRC (Rockwell Hardness Scale), making them ideal for cutting tough materials like metals and composites.
- Applications: Widely used in industries such as automotive, aerospace, and metalworking. These blades show a 20-30% longer service life compared to traditional high-speed steel (HSS) blades, according to a 2023 report from the International Cutting Tools Association (ICTA).
2. Ceramic Composites
- Technological Leap: China’s research institutions and manufacturers, such as the China Academy of Machinery Science & Technology, have developed ceramic composite blades with exceptional heat resistance and edge retention, maintaining sharpness at temperatures exceeding 1,200°C.
- Real-World Use: Ideal for high-speed cutting in industries like glass manufacturing, where precision and heat tolerance are critical.
3. High-Performance Steels and Alloys
- Stainless Steel Advancements: Stainless steel blades from China, enhanced with elements like molybdenum and vanadium, offer superior corrosion resistance, especially in food processing and chemical industries.
- Market Statistics: In a 2022 study by Metallurgy Today, Chinese-made stainless steel blades had 35% better resistance to pitting corrosion than equivalent European products in simulated industrial environments.
Comparative Material Performance Table
Material Type | Hardness (HRC) | Temperature Tolerance (°C) | Corrosion Resistance | Average Service Life |
Tungsten Carbide | 88–90 | 900 | Moderate | 25–30% higher |
Ceramic Composites | 92+ | 1,200 | High | 30% higher |
High-Performance Steel | 60–70 | 700 | Very High | 20–25% higher |
Real-World Applications
- Food Processing Sector: A U.S.-based frozen food packaging company switched to stainless steel blades sourced from China. The enhanced corrosion resistance resulted in 30% fewer blade replacements annually, saving $50,000 in operational costs.
- Automotive Manufacturing: A Japanese OEM reported that Chinese tungsten carbide blades reduced machining time by 15%, boosting production efficiency by 12%.
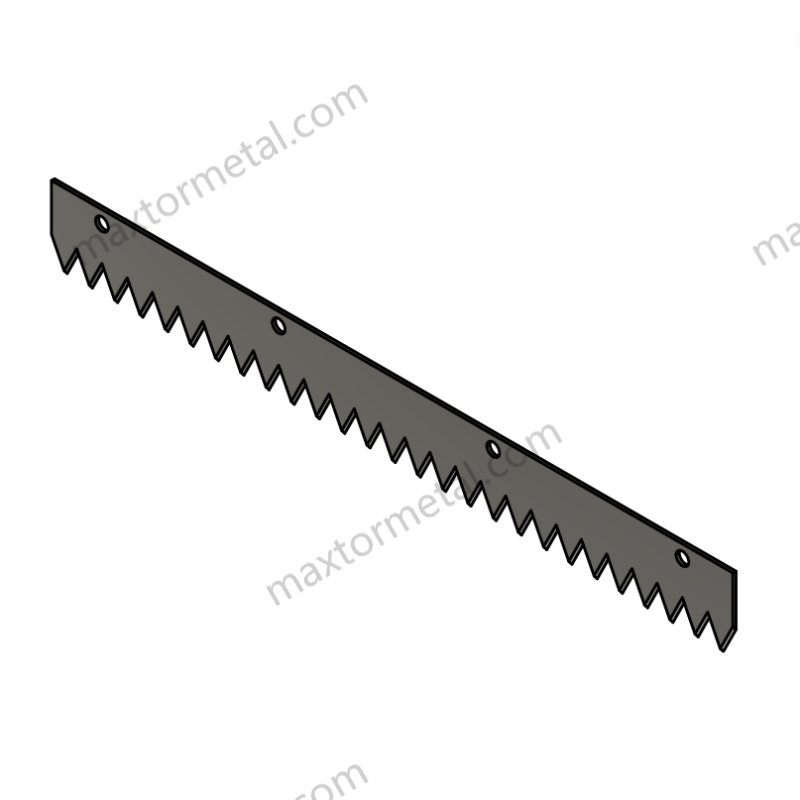
V. Quality Assurance at Every Step
Stringent Quality Control
Chinese machine blade manufacturers have implemented rigorous quality assurance processes across the entire production chain, from raw materials to finished products.
1. Comprehensive Inspection Systems
- Automated Testing: Many manufacturers use laser measurement systems to verify blade dimensions within micrometer-level tolerances.
- Lifecycle Testing: Advanced fatigue testing equipment simulates up to 10,000 operational cycles, ensuring blades perform reliably under heavy workloads.
2 .Quality Management Standards
- ISO9001 Compliance: Nearly all leading Chinese manufacturers, including Nanjing Metal, adhere to ISO9001 quality standards, with additional certifications like CE and RoHS that meet strict European Union guidelines.
- Statistical Process Control (SPC): Real-time monitoring during manufacturing ensures consistency, with defect rates as low as 0.5%—on par with global industry leaders.
Recognition in Global Markets
1. Customer Satisfaction
According to the 2023 Global Blade Buyer’s Report, 78% of surveyed international clients rated Chinese machine blades as “excellent” in terms of precision, durability, and cost-effectiveness.
2. Third-Party Testing Results
- Independent studies conducted by TÜV Rheinland confirmed that Chinese blades often outperform competitors on critical metrics like sharpness retention and edge chipping resistance.
- A test of ceramic blades showed a 20% higher cutting performance compared to similar products from North America.
3. Case Study: Certification Advantage
A German manufacturer in the metal stamping industry selected a Chinese supplier after its blades passed stringent DIN EN ISO 14731 welding standard tests, demonstrating high edge integrity and structural resilience under extreme pressure.
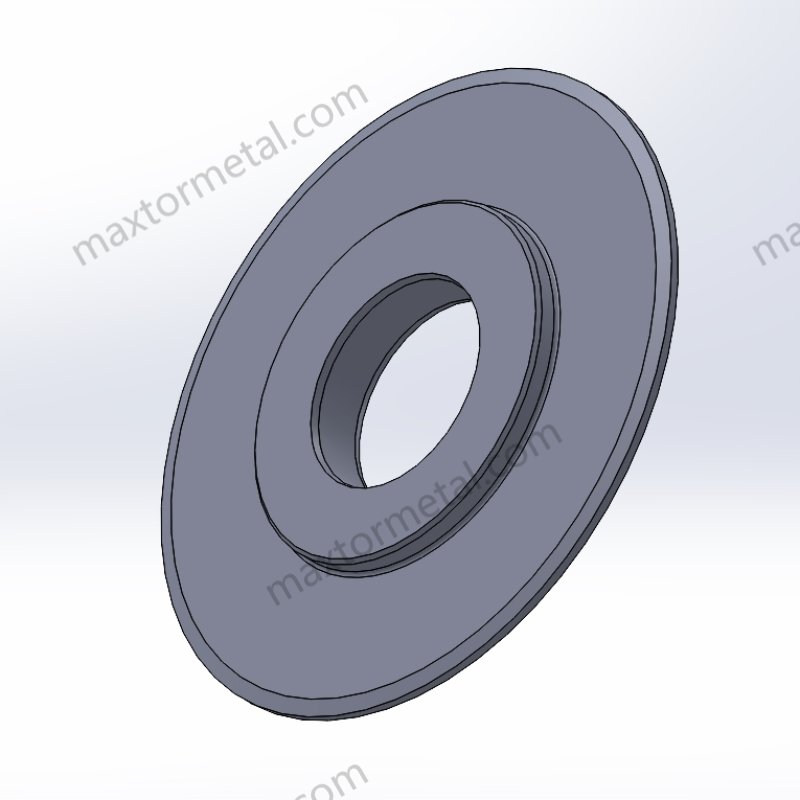
VI. Competitive Pricing Without Compromising Quality
Cost Efficiency Through an Integrated Manufacturing Ecosystem
China’s machine blade industry benefits from a synergistic ecosystem that combines large-scale production capabilities, advanced manufacturing technologies, and streamlined logistics. These factors contribute to a 30–50% cost advantage compared to manufacturers in Europe and North America, while maintaining high standards of quality.
- Economies of Scale
- Chinese manufacturers produce machine blades in large volumes, reducing the per-unit cost through economies of scale.
- For instance, in 2023, Nanjing Metal achieved a 25% cost reduction in manufacturing due to optimized batch production.
- Integrated Supply Chains
- Close proximity to raw material suppliers minimizes transportation costs and delays.
- A 2022 report by Deloitte China revealed that integrated supply chains in the country reduce raw material costs by 15%, giving Chinese manufacturers a decisive price advantage.
- Efficient Logistics
- Domestic infrastructure, including advanced port facilities and high-speed rail networks, enables faster delivery of raw materials and finished goods.
- Cost Metrics: Logistics costs in China are 30% lower than in the United States, according to the World Bank Logistics Performance Index.
Competitive Pricing Without Sacrificing Quality
Contrary to outdated stereotypes, affordability in Chinese machine blades does not come at the expense of quality. Manufacturers leverage automation, lean production methods, and material optimization to deliver superior products at reduced costs.
Comparative Cost Analysis of Machine Blades (2023)
Region | Average Blade Price (per unit) | Durability (Hours of Use) | Maintenance Cost Savings |
China | $50 | 200–250 | $30 per year |
Germany | $75 | 200–250 | $20 per year |
USA | $80 | 180–200 | $25 per year |
Real-World Example
A U.K.-based paper mill reduced its blade procurement costs by 35% after switching to Chinese suppliers. Despite the lower cost, the performance metrics, such as edge retention and cutting speed, matched those of their previous European supplier.
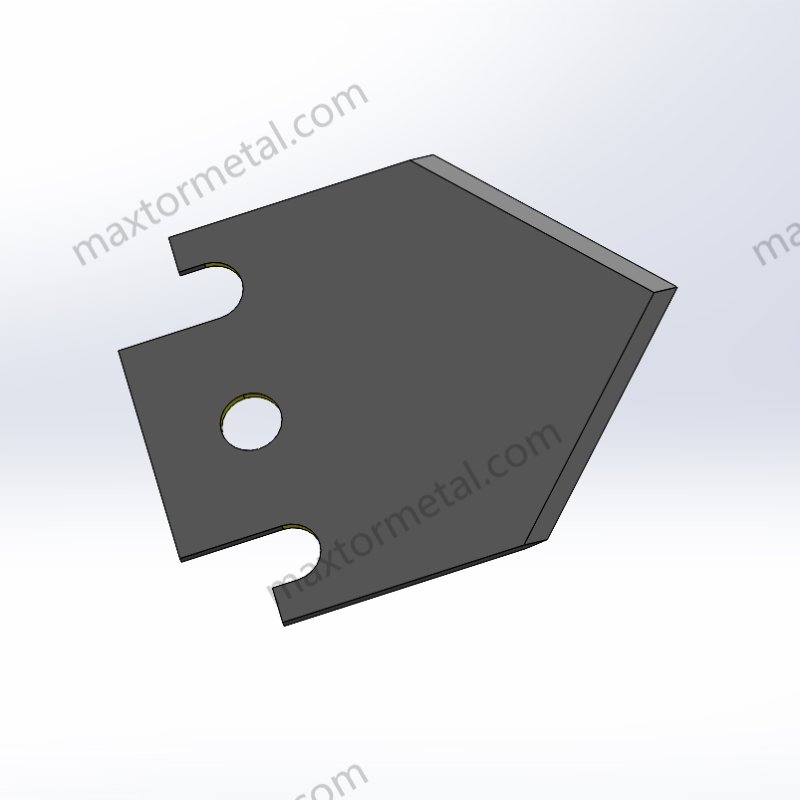
VII. Commitment to Sustainability
Green Energy Leadership: The Backbone of Sustainable Manufacturing
China’s focus on renewable energy and green manufacturing positions its machine blade industry as a leader in sustainability. In 2022, over 30% of China’s total energy consumption came from renewable sources such as solar, wind, and hydroelectric power.
- Clean Energy Integration
- Manufacturers like Nanjing Metal utilize facilities powered by solar farms and hydroelectric dams, reducing their carbon footprint by 40% compared to conventional energy use.
- According to the International Energy Agency (IEA), China has installed more than 40% of the world’s solar capacity, benefiting industries with cleaner and cheaper energy.
- Circular Economy Practices
- Material Recycling: Up to 85% of scrap metal generated during blade production is recycled, reducing resource consumption and waste.
- Waste Management: Many manufacturers adopt zero-waste policies, with by-products repurposed for use in other industries.
Meeting Global Environmental Standards
Chinese machine blade manufacturers align their operations with stringent international environmental regulations, such as:
- RoHS Directive: Ensuring blades are free from hazardous substances.
- ISO 14001 Certification: Demonstrating compliance with global environmental management standards.
Conclusion
Chinese-made machine blades have become synonymous with quality, innovation, and value. As a trusted partner to global industries, China’s machine blade sector continues to grow and evolve. For businesses seeking reliability and cost-effectiveness, machine knives made in China are a choice you can trust.
About Nanjing Metal
With 18 years of experience, Nanjing Metal specializes in the design and manufacture of high-quality industrial blades. Our expert team is dedicated to providing customized solutions that meet your unique needs. Contact us today for a free consultation and quote.
References
1. ExportHub (2022): “China’s Industrial Blade Export Data Overview”
2. Grand View Research: “Global Machine Blade Market Forecast, 2023–2030”
3. International Cutting Tools Association: “2023 Benchmark Study: Performance of Machine Blades by Region”
4.China Academy of Machinery Science & Technology: “Ceramic Composites in Modern Cutting Tools”
5. TÜV Rheinland: “Independent Assessment of Blade Durability and Quality”
6. Deloitte China (2022): “Cost Benefits of Integrated Manufacturing in China”
7. World Bank Logistics Performance Index: “China’s Infrastructure and its Impact on Industrial Costs”
8. International Energy Agency (IEA): “Renewable Energy Adoption in China, 2023”
9. International Standards Organization (ISO): “ISO 14001 Certified Manufacturing Facilities”
One Response