ملخص:
الدقة في القطع أمر بالغ الأهمية للصناعات التي تستخدم شفرات التقطيع الدائرية، مما يؤثر على كل شيء من كفاءة المواد إلى جودة المنتج. تستكشف هذه المقالة طرقًا فعالة لتعزيز دقة القطع من خلال اختيار مادة الشفرة المناسبة، وتحسين الإعداد، والحفاظ على حالة الشفرة، واختيار مورد موثوق.
1. لماذا تعد دقة القطع أمرًا مهمًا
في الصناعات التي يكون فيها القطع الدقيق ضروريًا، فإن دقة شفرة تقطيع دائرية يمكن أن تؤثر بشكل كبير على الإنتاجية وجودة المنتج. تقلل القطع الدقيقة من هدر المواد وتضمن عملية تصنيع سلسة وفعالة، خاصة في الصناعات مثل الورق والتغليف والمعادن. وفقًا لدراسة أجراها معهد تكنولوجيا التصنيع، فإن زيادة دقة الشفرة بمقدار 5% يمكن أن تقلل من هدر المواد بما يصل إلى 10% سنويًا. إن فهم العوامل التي تؤثر على دقة الشفرة وتنفيذ استراتيجيات لتحسين الدقة يفيد الشركات بشكل مباشر من خلال تقليل التكاليف وزيادة جودة الإنتاج.
2. العوامل المؤثرة على دقة القطع شفرات التقطيع الدائرية
تتأثر الدقة بعوامل مختلفة، بما في ذلك مادة الشفرة، والحدة، ومستوى التآكل، ودقة الإعداد. يمكن لكل من هذه المجالات إما تعزيز أو تقليل كفاءة القطع لشفرة التقطيع الدائرية. يعد فهم هذه العوامل وتحسينها أمرًا ضروريًا للحفاظ على الدقة العالية، وتقليل هدر المواد، وتعزيز الكفاءة التشغيلية.
2.1 مادة الشفرة
تلعب المواد المستخدمة في شفرات القطع الدائري دورًا رئيسيًا في تحديد دقة القطع. يُعد الفولاذ عالي السرعة (HSS) والكربيد من أكثر المواد استخدامًا. توفر شفرات الفولاذ عالي السرعة مرونة ممتازة ومقاومة للصدمات، مما يجعلها مثالية للمواد الأكثر ليونة مثل الورق أو البلاستيك. على العكس من ذلك، توفر شفرات الكربيد، التي تتمتع بتصنيف صلابة يبلغ حوالي 90 HRC (مقياس صلابة روكويل)، متانة استثنائية وهي مناسبة بشكل أفضل للمواد الأكثر صلابة مثل المعدن والمركبات. تكشف الدراسات أن شفرات الكربيد تدوم حتى 10 مرات أطول من شفرات الفولاذ القياسية في التطبيقات الكاشطة، مما يقلل من تكرار الاستبدال ويعزز اتساق القطع بمرور الوقت.
بالإضافة إلى ذلك، تعمل مواد مثل كربيد التنغستن، التي تجمع بين الصلابة الشديدة والمرونة في درجات الحرارة المرتفعة، على تحسين دقة القطع بشكل أكبر، خاصة عند معالجة المواد الصعبة أو الحساسة للحرارة. على سبيل المثال، عند قطع الفولاذ المقاوم للصدأ، يمكن استخدام شفرات ذات أطراف كربيد لتحقيق دقة أعلى بمقدار 15% مقارنة بشفرات الفولاذ عالية السرعة، نظرًا لقدرتها على الحفاظ على الحدة لفترة أطول تحت الضغط.
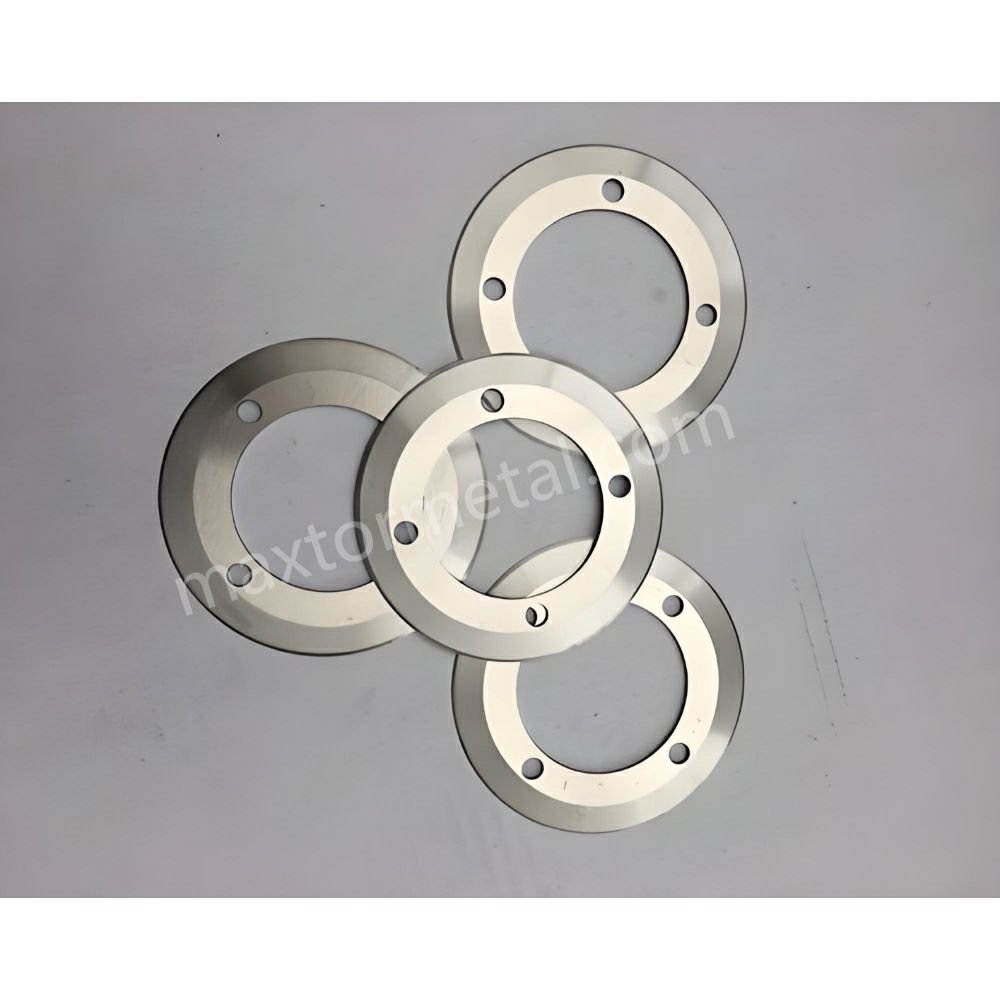
2.2 الحدة ومستوى التآكل
تؤثر حدة الشفرة بشكل مباشر على دقة القطع. وجدت دراسة أجرتها جمعية Precision Metalforming أن أخطاء القطع يمكن أن تزيد بما يصل إلى 25% عندما يتجاوز تآكل الشفرة 20%. تتطلب الشفرة الباهتة المزيد من الضغط لتحقيق قطع نظيف، مما يزيد من خطر إزاحة المادة أو تآكل الحافة أو الانحناءات غير المقصودة. يعد تنفيذ جدول صيانة يتضمن شحذ الشفرة بشكل روتيني أو استبدالها بعد عدد معين من القطع أمرًا بالغ الأهمية لتجنب مثل هذه المشكلات. على سبيل المثال، يمكن أن يضمن تحديد جدول شحذ كل 50000 قطع للمواد القياسية وكل 20000 قطع للمواد الأكثر صلابة حافة حادة باستمرار.
علاوة على ذلك، تعمل التطورات في طلاء الشفرات، مثل نتريد التيتانيوم (TiN) والكربون الشبيه بالماس (DLC)، على زيادة الحدة وتقليل التآكل. على سبيل المثال، أظهرت الشفرات المطلية بـ TiN زيادة في العمر الافتراضي بنسبة 30% في بيئات القطع عالية الكثافة، مع الحفاظ على الدقة لفترات أطول دون المساس بحافة الشفرة.
2.3 الدقة في إعداد الشفرة وتركيبها
إن الطريقة التي يتم بها تركيب شفرة القطع الدائرية لها تأثير كبير على دقة القطع. حتى عدم المحاذاة بمقدار 0.1 مم يمكن أن يؤدي إلى قطع غير متساوية وإهدار المواد. يمكن للتركيب الصحيح باستخدام أدوات محاذاة الليزر أن يقلل من معدلات الخطأ بنسبة 20%، مما يحسن دقة الإنتاج. على سبيل المثال، أفادت مرافق قطع المعادن التي تستخدم شفرات القص الدوارة المحاذية بالليزر عن انخفاض بنسبة 15% في عيوب الحافة وتحسن بنسبة 10% في سرعة القطع.
يعد توازن الشفرة عاملاً حاسماً آخر. فالشفرة التي تكون غير متوازنة قليلاً أو مثبتة بشكل فضفاض سوف تهتز، مما يعطل الدقة ويزيد من فرصة التآكل الميكانيكي. يتطلب تحقيق حامل شفرة متوازن غالبًا استخدام حوامل دقيقة ذات تسامح قوة تثبيت أقل من 0.5 مم. يمكن لمثل هذه التعديلات، على الرغم من كونها بسيطة، أن تحدث فرقًا كبيرًا في الإعدادات عالية الدقة.
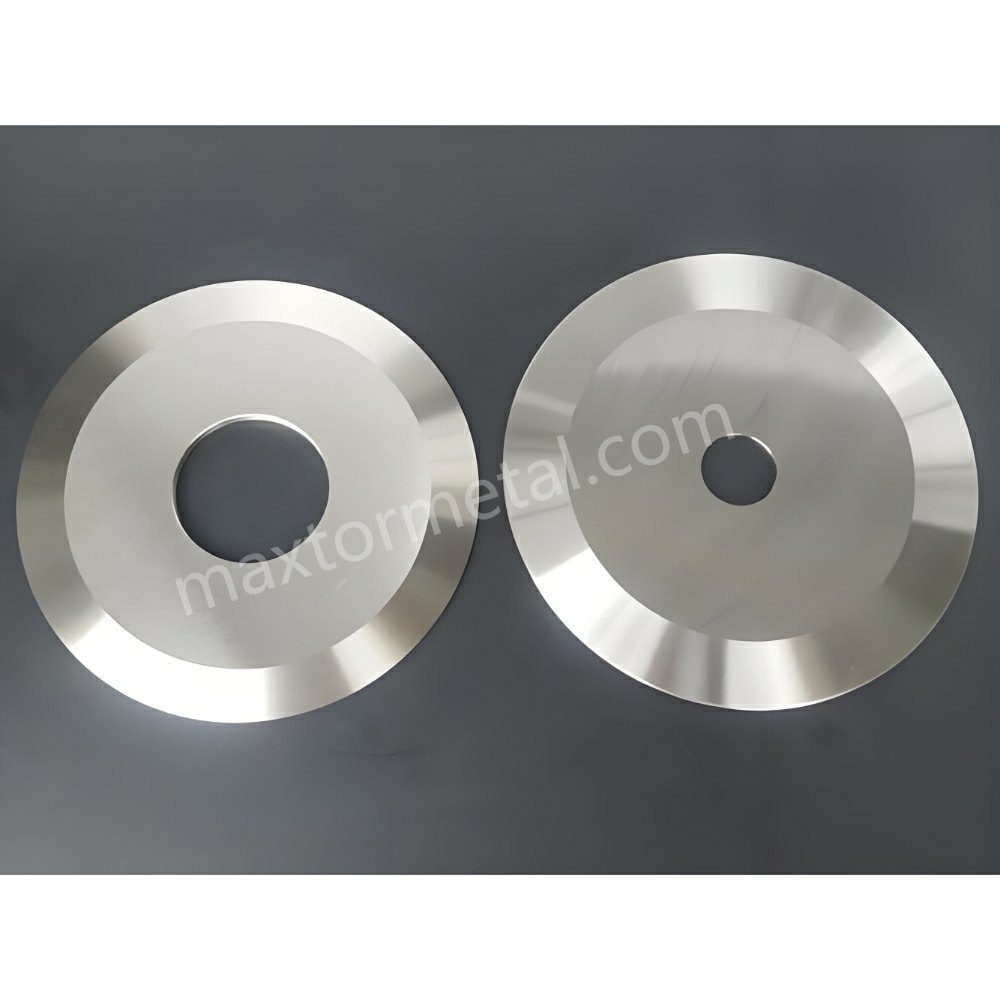
3. نصائح عملية لتحسين دقة القطع
يتطلب تحسين دقة شفرات القطع الدائري اختيار نوع الشفرة المناسب، وتحسين المعدات وملاءمة الشفرة، والاستفادة من التكنولوجيا المتقدمة. تعمل هذه الخطوات على تقليل احتمالية عدم الدقة وتعزيز الكفاءة الإجمالية لعملية الإنتاج.
3.1 اختيار نوع الشفرة والمواصفات المناسبة
يعد اختيار قطر الشفرة وسمكها وزاوية الحافة المناسبة لكل نوع من المواد أمرًا ضروريًا. على سبيل المثال، عند قطع المواد اللينة مثل الرغوة أو المطاط، يمكن للشفرة الأرق ذات زاوية الحافة الأكثر حدة أن تقلل من السحب، مما يؤدي إلى قطع أكثر سلاسة. وعلى العكس من ذلك، بالنسبة للمواد الصلبة مثل الفولاذ أو الزجاج، فإن الشفرات الأكثر سمكًا والأكثر متانة هي الأفضل. تشير الدراسات إلى أن استخدام شفرات محددة بشكل صحيح للمادة في متناول اليد يمكن أن يزيد من دقة القطع بما يصل إلى 25%.
بالإضافة إلى ذلك، تؤثر هندسة حافة الشفرة على دقة القطع. على سبيل المثال، تعد الحواف المشطوفة مثالية لقطع المواد ذات الطبقات، حيث تقلل من المقاومة. توفر الشفرة ذات الحواف المزدوجة بزاوية 30 درجة على كل جانب نتائج مثالية في القطع الدقيق للبلاستيك، مما يحسن جودة القطع بنحو 20% مقارنة بالحواف ذات الحواف المفردة.
3.2 تحسين المعدات وملاءمة الشفرة
إن الملاءمة الدقيقة للشفرة مع المعدات تقلل الاهتزاز، وهو سبب شائع لعدم دقة القطع. على سبيل المثال، تعمل التعديلات في تثبيت الشفرة على تقليل الانحراف بما يصل إلى 18% في التطبيقات عالية السرعة. تحقق العديد من المرافق الصناعية هذا من خلال استخدام حاملات الشفرة مع أنظمة المشابك الهيدروليكية التي توفر استقرارًا أعلى مقارنة بالمشابك الميكانيكية. دراسة أجرتها الرابطة الدولية وجدت دراسة أجرتها شركة Industrial Cutting أن أنظمة التثبيت الهيدروليكية تعمل على تحسين استقرار القطع بما يصل إلى 25%، مما يضمن قطعًا نظيفة ودقيقة.
علاوة على ذلك، فإن استخدام ممتصات الصدمات في إعداد التركيب يمكن أن يزيد من استقرار الشفرة. تعمل ممتصات الصدمات على تقليل التذبذبات وتساعد في الحفاظ على ضغط الشفرة بشكل متساوٍ، وهو أمر مفيد بشكل خاص في التطبيقات عالية السرعة حيث يمكن حتى للاهتزازات البسيطة أن تؤدي إلى إهدار المواد.
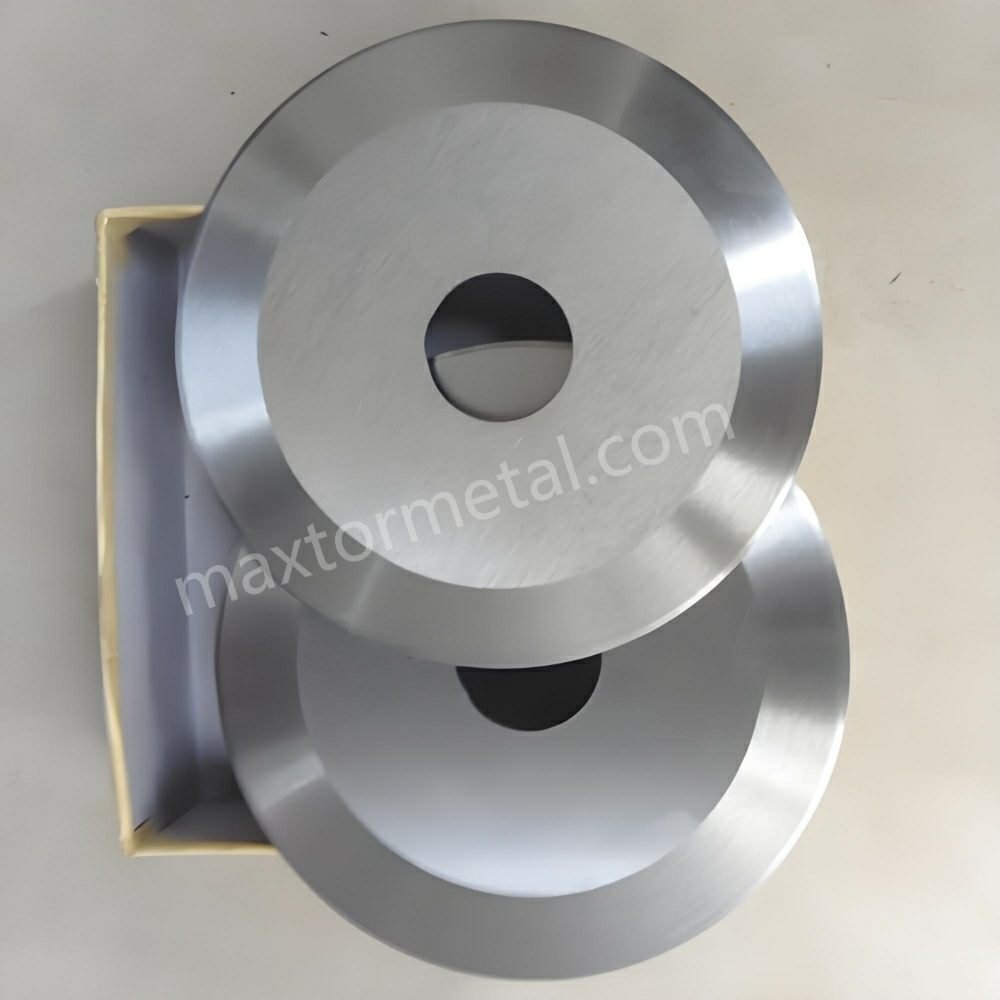
3.3 تقنية القطع المتقدمة لتحقيق دقة أعلى
التبني التكنولوجيات المتقدمة مثل تحديد موضع الشفرة تلقائيًا أو أنظمة القطع الموجهة بالليزر، تعمل على تحسين الدقة بشكل كبير. تعمل الأنظمة الآلية على ضبط موضع الشفرة بدقة شديدة، مع مراعاة حتى الاختلافات الطفيفة في سمك المادة. هذه الأنظمة فعالة بشكل خاص في صناعات تشغيل المعادن والسيارات، حيث غالبًا ما تكون التفاوتات في حدود ±0.05 مم. أفادت المنشآت التي تستخدم هذه التكنولوجيا بتحسن في الدقة بواسطة 30%، مع تحقيق انخفاض في هدر المواد أيضًا.
تُعد الأنظمة الموجهة بالليزر أداة قيمة أخرى، وخاصةً لقطع المواد غير المتجانسة أو العمل مع ركائز دقيقة. لا يعمل التوجيه بالليزر على تحسين المحاذاة المرئية فحسب، بل يساعد أيضًا في تجنب سوء محاذاة الشفرة، مما يؤدي إلى قطع أكثر دقة وتقليل إعادة العمل. في تصنيع المنسوجات، حيث تكون دقة حافة القماش أمرًا بالغ الأهمية، تعمل الشفرات الدائرية الموجهة بالليزر على تقليل الأخطاء بما يصل إلى 15%.
4. صيانة الشفرة: إطالة العمر وضمان الدقة
إن الحفاظ على حالة شفرة التقطيع الدائرية أمر ضروري للحفاظ على الدقة ومنع عمليات الاستبدال المكلفة. تعمل روتينات الصيانة المناسبة وعمليات الاستبدال المجدولة على تقليل وقت التوقف عن العمل وتعزيز الكفاءة التشغيلية.
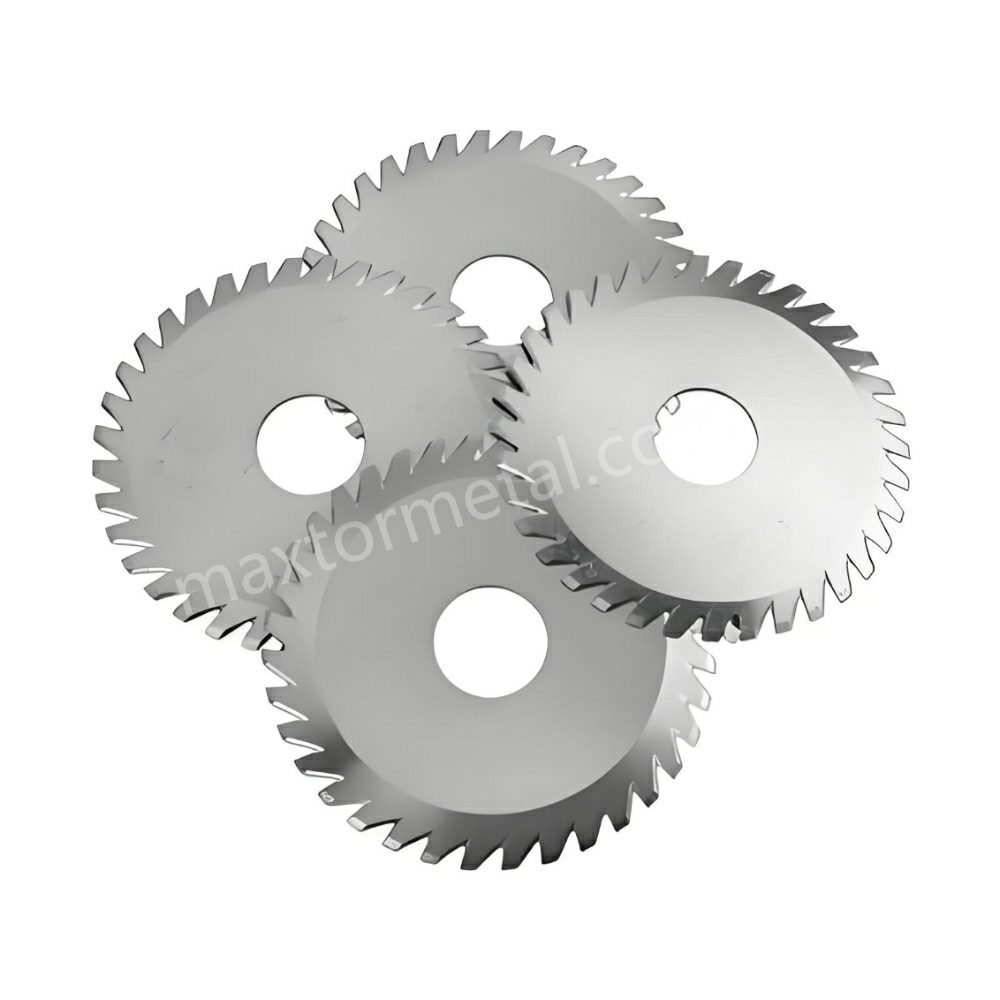
4.1 الصيانة الدورية والفحص
إن الفحص والصيانة المنتظمة أمران بالغي الأهمية لتحقيق الأداء الأمثل. وتُظهِر الدراسات أن التنظيف والتزييت الروتينيين يمكن أن يطيلا عمر الشفرة بما يصل إلى 40%. ويمكن أن يؤدي تراكم الغبار والحطام والبقايا إلى إتلاف الشفرة بشكل أسرع وتقليل كفاءتها. على سبيل المثال، في تطبيقات تغليف المواد الغذائية، حيث تقطع الشفرات بشكل متكرر المواد اللاصقة، فقد ثبت أن تنظيف الشفرة بعد كل 10000 قطع يحافظ على دقة القطع ويحسن النظافة ويقلل من التآكل.
بالإضافة إلى ذلك، يعمل استخدام مواد التشحيم على تقليل الاحتكاك وإطالة حدة الشفرة. وفي قطع المعادن، يعمل التشحيم المنتظم على تقليل التآكل بنحو 25%، مما يسمح بقطع أكثر سلاسة وتكاليف استبدال أقل.
4.2 استبدال الشفرة المجدولة
تتمتع كل شفرة بعمر افتراضي محدود، بغض النظر عن الصيانة. غالبًا ما تنتج الشفرات المستخدمة بعد حد التآكل الأمثل لها قطعًا غير منتظمة، مما قد يقلل من جودة الإنتاج وإهدار المواد. تقترح معايير الصناعة استبدال الشفرات كل ثلاثة أشهر أو بعد عدد معين من القطع - أيهما يأتي أولاً. كشف مسح صناعي حديث أن الشركات التي تتبع جدول استبدال الشفرات لمدة 90 يومًا تواجه أخطاء قطع أقل بنسبة 20%، مما يقلل من إعادة العمل المكلفة ويحسن الكفاءة.
5. اختيار القطع الدائري عالي الجودة مورد الشفرات
يعد اختيار المورد أمرًا بالغ الأهمية لضمان جودة ثابتة للشفرة. عادةً ما يوفر الموردون ذوو الجودة العالية مواد تم اختبارها لتلبية معايير الصناعة الصارمة ويمكنهم تقديم إرشادات حول أفضل أنواع الشفرات لتطبيقات محددة.
5.1 تقييم ضمان الجودة والامتثال
عند اختيار المورد، ابحث عن شهادات الجودة مثل ايزو 9001، مما يشير إلى الالتزام بالجودة والاتساق. غالبًا ما يكون لدى الموردين الحاصلين على شهادة ISO معدلات عيوب أقل بسبب عمليات مراقبة الجودة الصارمة. على سبيل المثال، أفادت مصانع التصنيع التي تعمل حصريًا مع الموردين الحاصلين على شهادة ISO بزيادة 15% في دقة الإنتاج بسبب موثوقية شفراتهم.
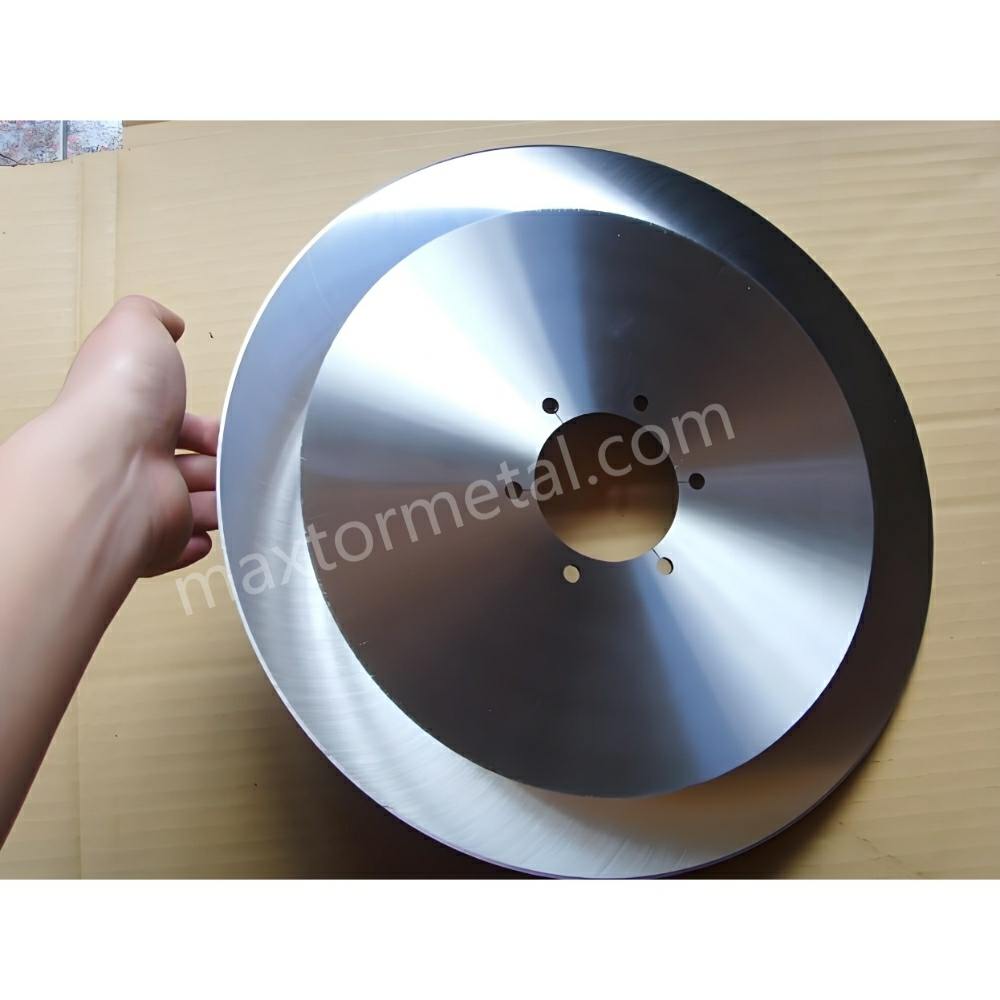
5.2 إعطاء الأولوية للتكنولوجيا والابتكار
يمكن للمورد الذي يستثمر في تقنيات التصنيع المتقدمة أن يقدم شفرات ذات متانة ودقة فائقتين. تضمن طرق الإنتاج الحديثة، مثل تقنيات التصنيع باستخدام الحاسب الآلي والقطع بالليزر، تصنيع الشفرات بتفاوتات عالية. تُظهر الدراسات أن الشفرات المنتجة باستخدام الآلات ذات التحكم الرقمي تظهر زيادة في المتانة بنسبة 20%، مما يوفر قطعًا أكثر دقة على مدى فترة أطول.
5.3 دعم العملاء وضمانات الخدمة
إن دعم العملاء الموثوق به يعد من الاعتبارات الأساسية. يقدم الموردون الذين يقدمون خدمات ما بعد البيع الشاملة، بما في ذلك تخصيص الشفرة والدعم الفني، قيمة مضافة تساعد العملاء على تحقيق نتائج قطع أفضل. وتشهد الشركات التي تقدم دعمًا مخصصًا للعملاء وخدمات استبدال الشفرة زيادة في كفاءة الإنتاج بسبب تقليل وقت التوقف عن العمل والحلول الفورية لأي مشكلات في الشفرة.
6. الخاتمة: تعزيز الكفاءة من خلال الدقة
تحسين دقة الخاص بك شفرة تقطيع دائرية يمكن أن تعمل العمليات على تعزيز الكفاءة الإجمالية وجودة المنتج واستخدام المواد بشكل كبير. من خلال اختيار مواد الشفرة المناسبة وضمان الإعداد الدقيق وصيانة الشفرات بانتظام، يمكن للشركات الاستمتاع بعمر أطول للشفرة وتحسين الدقة في القطع.
الشراكة مع مورد عالي الجودة كما تضمن حصولك على شفرات موثوقة ومتينة تناسب احتياجاتك المحددة، مما يؤدي إلى دقة ثابتة في الإنتاج. بالنسبة للشركات التي تعتمد على عمليات القطع الدقيقة، فإن هذه الاستراتيجيات ضرورية للبقاء في المنافسة وتقديم جودة استثنائية.