Plastic crushers play a crucial role in industrial recycling, waste management, and material processing. These machines break down plastic waste into smaller, manageable pieces, enabling efficient recycling and reuse. However, the performance of a plastic crusher heavily depends on the condition of its blades.
Dull or damaged blades reduce cutting efficiency, increase energy consumption, and may even cause machine failures. A poorly maintained blade can lead to inconsistent shredding, overheating, and unnecessary wear on other machine components. In extreme cases, worn-out knives can result in costly downtime and expensive repairs.
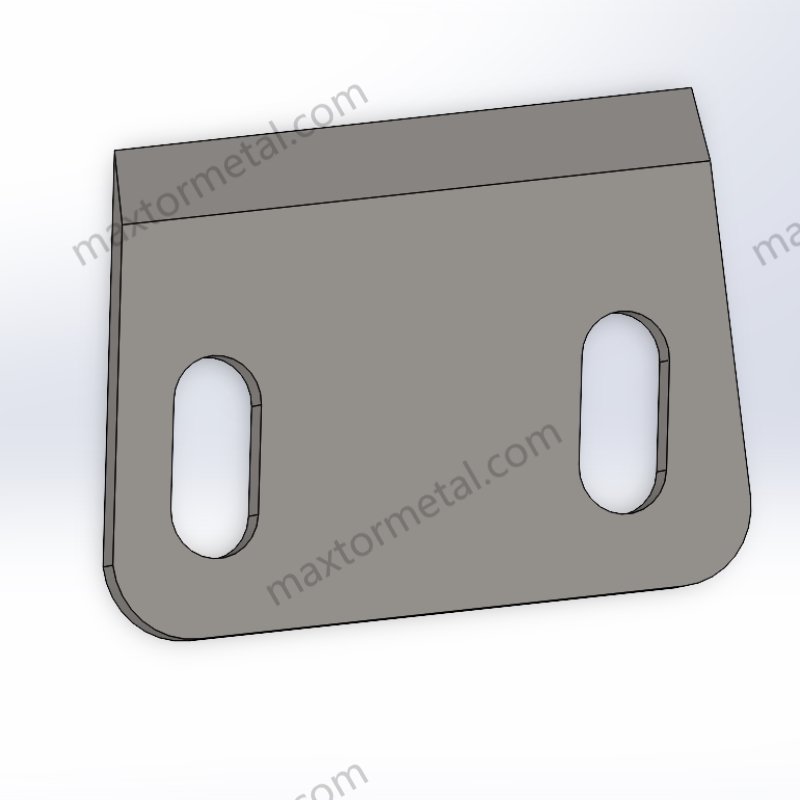
Understanding when and how to replace شفرات كسارة البلاستيك is essential for maintaining productivity and minimizing operational costs. This guide will walk you through the types of blades, signs of wear, and the step-by-step replacement process.
About Nanjing Metal
As an industry-leading manufacturer of industrial knives and blades, Nanjing Metal has been producing high-quality shredding solutions for 18 years. Our team specializes in designing and manufacturing شفرات مخصصة to meet the unique needs of various industries.
1. Types of Plastic Crusher Blades
Choosing the correct blade type is essential for ensuring efficient shredding, extending machine life, and reducing operational costs. Below, we explore the three main categories of plastic crusher blades in greater detail, including their material composition, properties, and ideal applications.
1.1 High-Speed Steel (HSS) Blades
تكوين المواد: HSS blades are made from high-carbon steel with alloying elements like tungsten, molybdenum, vanadium, and chromium to enhance hardness and heat resistance.
Properties & Advantages:
✅ Excellent toughness, making them resistant to chipping and impact forces.
✅ High wear resistance, allowing them to maintain sharpness for longer periods.
✅ Suitable for high-speed shredding applications due to their heat-resistant properties.
Best Used For:
- Hard and rigid plastics, such as ABS (Acrylonitrile Butadiene Styrene) and polycarbonate (PC).
- High-volume shredding operations that require long-lasting sharpness.
1.2 Alloy Steel Blades
تكوين المواد: Alloy blades are manufactured using high-carbon steel mixed with additional elements like nickel, manganese, and chromium for improved durability.
Properties & Advantages:
✅ A balance between toughness and hardness, making them versatile.
✅ Good wear resistance, though slightly lower than carbide blades.
✅ More cost-effective than carbide while offering superior durability compared to standard steel blades.
Best Used For:
- Medium-duty shredding of PVC (Polyvinyl Chloride) and HDPE (High-Density Polyethylene).
- General-purpose applications that require affordable yet reliable performance.
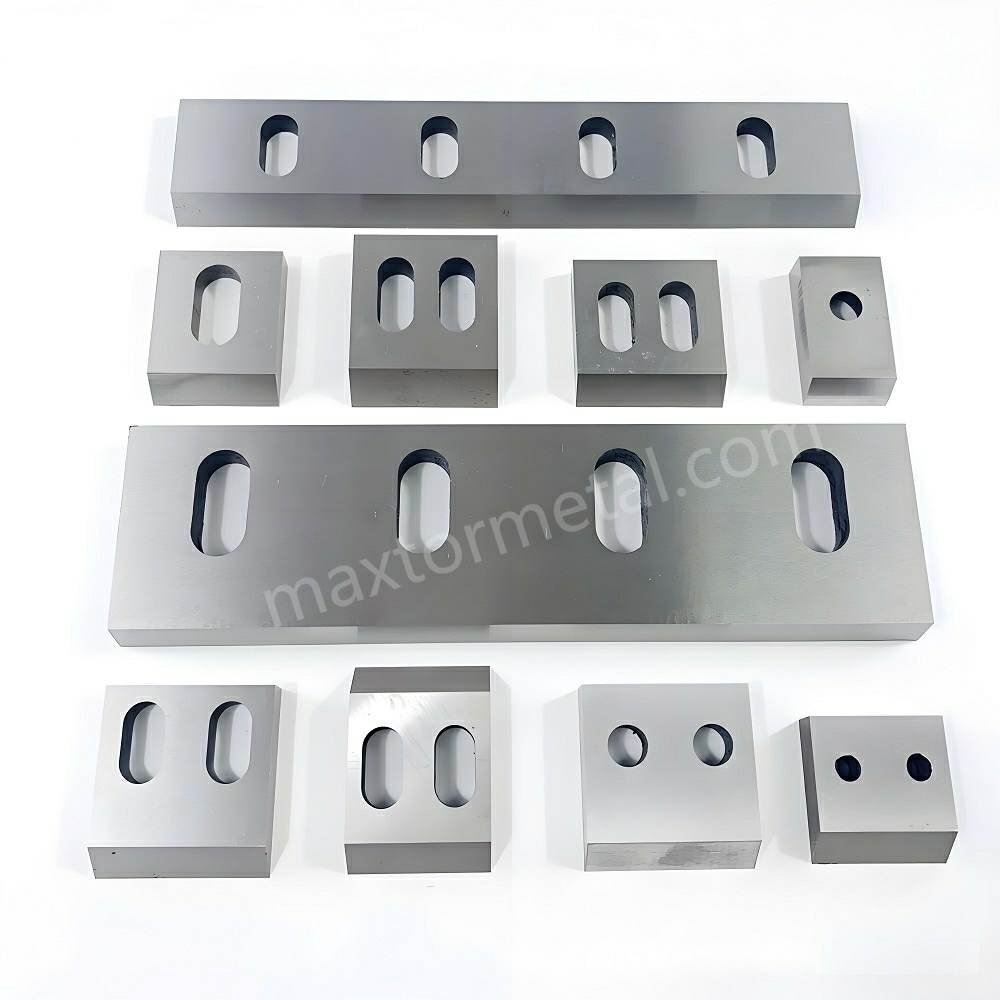
1.3 Carbide Blades
تكوين المواد: These blades feature a tungsten carbide cutting edge bonded to a steel core, offering extreme hardness and high resistance to abrasion.
Properties & Advantages:
✅ Ultra-high wear resistance, significantly extending blade lifespan.
✅ Exceptional hardness, reducing the need for frequent sharpening.
✅ Higher initial cost but lower long-term replacement expenses.
Best Used For:
- Engineering plastics and abrasive materials like fiber-reinforced polymers (FRPs).
- Heavy-duty industrial applications requiring precision cutting and minimal downtime.
1.4 How to Select the Right Blade
Choosing the right blade depends on several factors:
عامل | Best Blade Type | Example Application |
صلابة المادة | HSS أو الكربيد | Tough plastics (PC, PET, ABS) |
Wear Resistance Needed | كربيد | High-abrasion plastics (FRPs) |
Budget Considerations | خليط معدني | Medium-duty plastic shredding |
سرعة القطع | الأحرار | High-speed shredding lines |
2. How Crusher Blades Work
Understanding the mechanics of crusher blades is essential for optimizing machine performance and avoiding premature wear.
2.1 Cutting Mechanism of Plastic Crusher Blades
Plastic shredders operate using rotary و fixed blades that work together to break down plastic materials into smaller pieces. The cutting action occurs through:
- قص – The primary force applied, where rotating knives push plastic against stationary knives to create clean cuts.
- Tearing – For softer plastics, blades create small cracks that expand under mechanical stress, breaking the plastic apart.
- Compression – Some shredders use compression force before cutting to increase efficiency.
2.2 Key Factors Affecting Shredding Efficiency
Crusher performance is directly influenced by the following blade-related factors:
عامل | التأثير على الأداء |
حدة الشفرة | Dull blades increase energy consumption and cause uneven cuts. |
Blade Alignment | Misaligned knives lead to vibration, excessive wear, and lower efficiency. |
Cutting Angle & Clearance | Poorly adjusted clearance can cause excessive friction and overheating. |
مادة الشفرة | The right blade material prevents frequent wear and breakage. |
2.3 Why Blade Alignment Matters
Correct blade alignment ensures even wear distribution, reducing maintenance costs and machine stress.
- If blade clearance is too large, plastics may pass through without being properly shredded.
- If blade clearance is too tight, it increases friction, leading to excessive heat buildup and energy waste.
نصيحة احترافية: Always follow the manufacturer’s specifications for blade positioning and alignment.
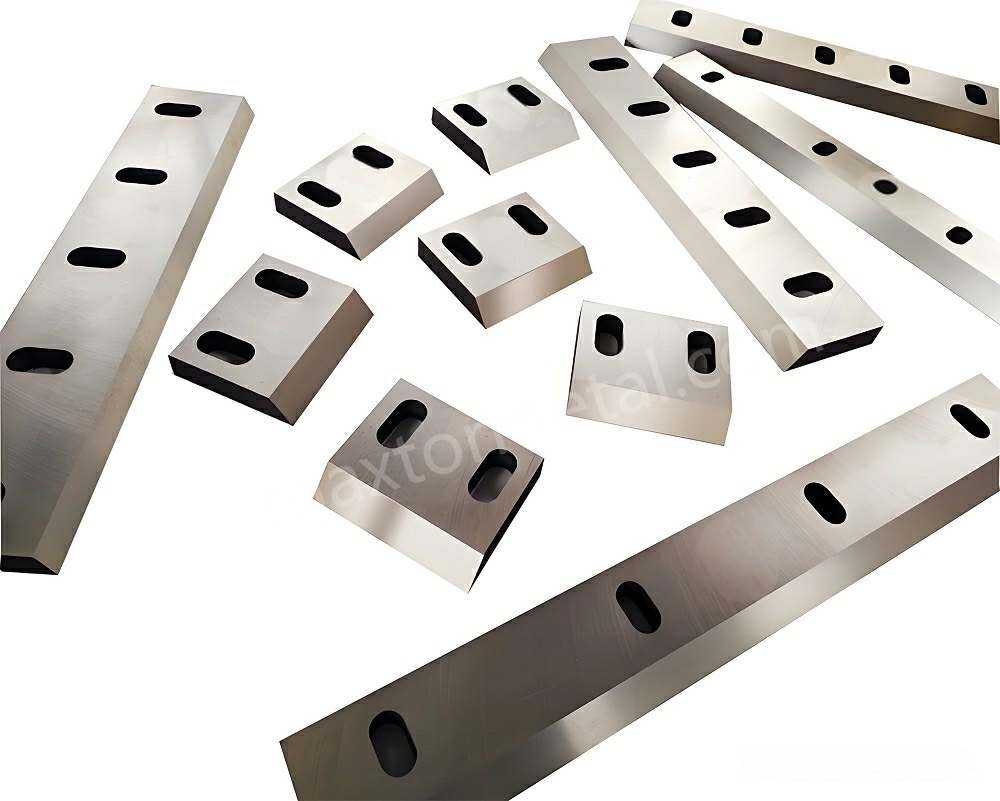
3. Signs That Indicate Blade Replacement Is Needed
Knowing when to replace plastic crusher blades helps avoid unexpected downtime and costly machine repairs.
3.1 Common Signs of Blade Wear
Wear Indicator | What It Means | حل |
Reduced cutting efficiency | Blades are dull or misaligned. | Resharpen or replace blades. |
Inconsistent shredded material size | Uneven blade wear or improper clearance. | Inspect and adjust blade alignment. |
Unusual vibrations | Loose or damaged blades. | Tighten bolts or replace damaged knives. |
Excessive heat buildup | Friction from dull blades. | Clean, lubricate, or replace blades. |
3.2 Factors That Influence Blade Lifespan
A variety of factors impact how long crusher blades last:
- Plastic Material Hardness – Harder plastics (e.g., PC, PET) cause faster wear.
- Machine Operating Conditions – High-speed shredding generates more heat and stress.
- ممارسات الصيانة – Regular lubrication and alignment checks extend blade life.
بيانات الصناعة: Studies show that regularly maintained crusher blades last 30-50% longer than those in neglected machines (Source: Manufacturing Today, 2023).
3.3 Best Practices for Blade Inspections
A structured maintenance schedule helps detect blade wear before it causes major problems:
Inspection Task | تكرار |
Visual Blade Check | يوميًا |
Bolt Tightness & Alignment Check | أسبوعي |
Full Blade Wear Analysis | شهريا |
💡 نصيحة احترافية: Keeping a log of blade replacements helps track performance trends and optimize maintenance schedules.
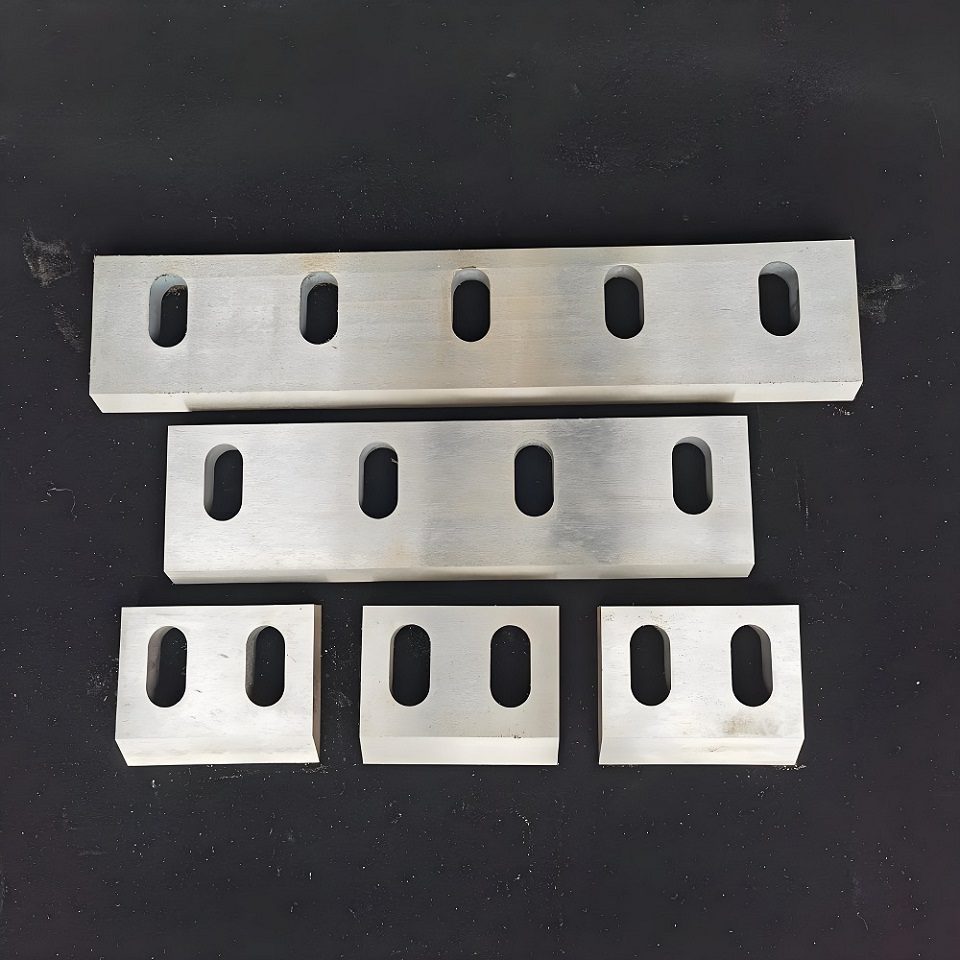
4. Step-by-Step Blade Replacement Guide
4.1 Preparation for Blade Replacement
Proper preparation reduces downtime and prevents mistakes. Before beginning, gather the required tools and safety gear:
Required Tools & Equipment
Tool/Equipment | غاية |
Safety gloves | Protect hands from sharp edges |
Safety goggles | Prevent debris from entering eyes |
Torque wrench | Ensure precise bolt tightening |
Allen wrenches & spanners | Remove blade fasteners |
Cleaning brush & cloth | Clean blade mounting surface |
Rust remover & lubricant | Remove rust and ease installation |
Replacement blades | Ensure correct size and type |
Lockout/tagout kit | Prevent accidental machine startup |
Key Preparation Steps
- Verify blade specifications – Ensure the new blades match the machine’s requirements (size, hole alignment, material type).
- Check stock of additional parts – Have spare washers, shims, and bolts ready in case replacements are needed.
- Clear the workspace – Keep all tools and parts organized in a well-lit area.
- Wear proper PPE (Personal Protective Equipment) – Gloves, goggles, and protective clothing are essential.
💡 نصيحة احترافية: Keep a printed maintenance checklist nearby to track each step.
4.2 Safety Shutdown and Lockout Procedure
Machine-related accidents are often caused by failure to follow proper shutdown procedures. Before replacing the blades, take these critical safety steps:
Step-by-Step Lockout/Tagout (LOTO) Procedure
- Power Down the Machine
- Press the emergency stop button.
- Shut off the main power switch.
- Disconnect the Power Source
- For electric crushers: Unplug from the main power supply.
- For hydraulic systems: Shut off and depressurize the system.
- Apply Lockout/Tagout Devices
- Attach a lockout device to the main power switch.
- Place a tagout label to warn others that maintenance is in progress.
- Verify the Shutdown
- Press the start button to ensure no power is flowing.
- Wait for all moving parts to fully stop before proceeding.
🚨 Warning: Never assume the machine is off. Always verify before working on it.
4.3 Accessing the Blade Compartment
Depending on the crusher model, blades may be housed in a compartment behind protective covers.
Steps to Access the Blade Compartment
- Identify the access point – Refer to the machine manual to locate the blade chamber.
- Remove safety covers or access panels – Use appropriate wrenches to remove the bolts.
- Secure loose components – Prevent screws or covers from falling into the machine.
- Inspect the blade area – Look for debris, wear patterns, and alignment issues before proceeding.
💡 نصيحة احترافية: Take a photo of the existing blade setup before removal to assist with reinstallation.
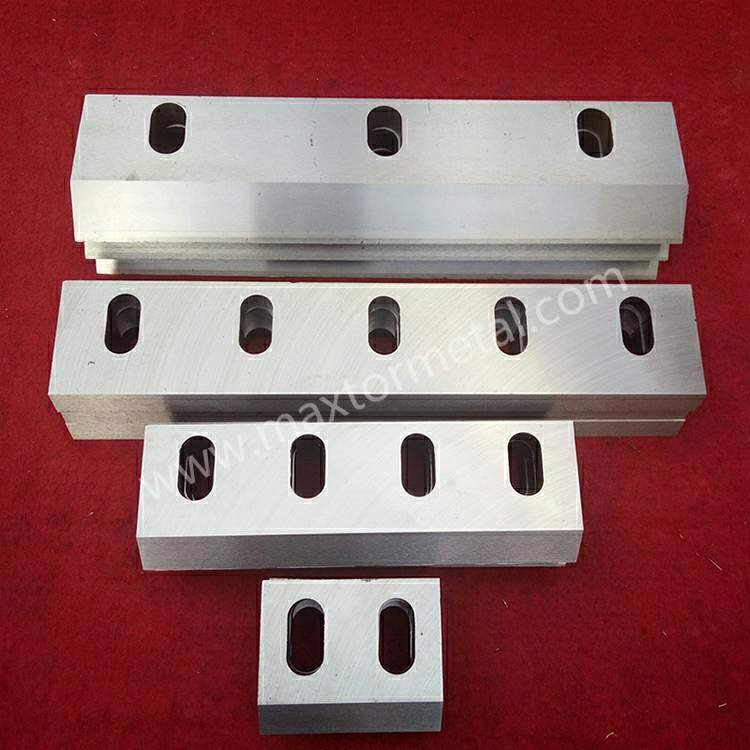
4.4 Removing the Old Blades
Incorrect blade removal can damage the mounting surface, leading to misalignment issues. Follow these precise steps:
Blade Removal Procedure
- Loosen the bolts in a crisscross pattern to prevent stress on the blade.
- Carefully remove washers and shims, keeping them organized for later use.
- Slide out the old blades slowly, avoiding sudden movements that could cause injuries.
- Inspect the removed blades for wear patterns, documenting excessive damage.
- Clean the mounting area before installing the new blades.
Common Mistakes to Avoid
❌ Using excessive force – If a bolt is stuck, apply lubricant instead of forcing it.
❌ Dropping washers or shims – Losing parts may lead to improper blade alignment.
❌ Skipping documentation – Always record observations to track blade wear trends.
4.5 Cleaning and Preparing the Mounting Surface
A clean mounting surface is essential for blade stability and cutting accuracy. Even small particles can cause misalignment, increasing blade wear.
Cleaning Steps
✅ Use a wire brush to remove rust and debris.
✅ Wipe the area with an industrial solvent to eliminate grease.
✅ Inspect for cracks or uneven surfaces that could affect blade performance.
✅ Ensure all washers and shims are in good condition; replace if necessary.
💡 نصيحة احترافية: Use a straightedge tool to check for surface irregularities before installing new blades.
4.6 Installing the New Blades
Installing the blades correctly ensures efficient shredding and extends machine life.
Installation Process
- Align the blade holes with the mounting surface.
- Insert washers and shims as per manufacturer recommendations.
- Hand-tighten bolts in place before final tightening.
- Ensure even spacing between blades to avoid uneven cuts.
⚠️ Important: Blades must be positioned in the correct rotation direction to avoid inefficiency and machine damage.
4.7 Proper Bolt Tightening
Incorrect tightening can cause blade warping or excessive vibration, leading to premature wear.
Best Practices for Tightening Blade Bolts
✅ Use a torque wrench – Follow the manufacturer’s torque specifications.
✅ Tighten bolts in a crisscross pattern – This ensures even distribution of force.
✅ Avoid over-tightening – This may damage blade edges or cause cracks.
✅ Recheck torque after initial test run – Some bolts may loosen slightly.
💡 نصيحة احترافية: Keep a torque specification chart handy for reference.
4.8 Test Run and Final Adjustments
A test run verifies the installation and ensures the crusher operates smoothly.
Test Run Procedure
- Reassemble all safety covers and panels.
- Reconnect the power supply and turn on the machine.
- Run the crusher at low speed for 5–10 minutes.
- Monitor for the following issues:
- Unusual vibrations
- Uneven noise levels
- Irregular cutting performance
- If necessary, make blade alignment adjustments.
💡 نصيحة احترافية: Have an operator monitor performance while the test run is in progress.
4.9 Maintenance Record-Keeping
Documenting each blade replacement improves maintenance efficiency and helps predict future replacements.
What to Include in Maintenance Records
📌 Replacement date – Track blade lifespan.
📌 Type of blade installed – Ensure consistency.
📌 Observed wear patterns – Identify potential machine issues.
📌 Torque values used – Verify proper installation.
📌 Next scheduled maintenance – Prevent unexpected failures.
💡 نصيحة احترافية: يستخدم digital maintenance logs to track replacement frequency and schedule preventive maintenance.
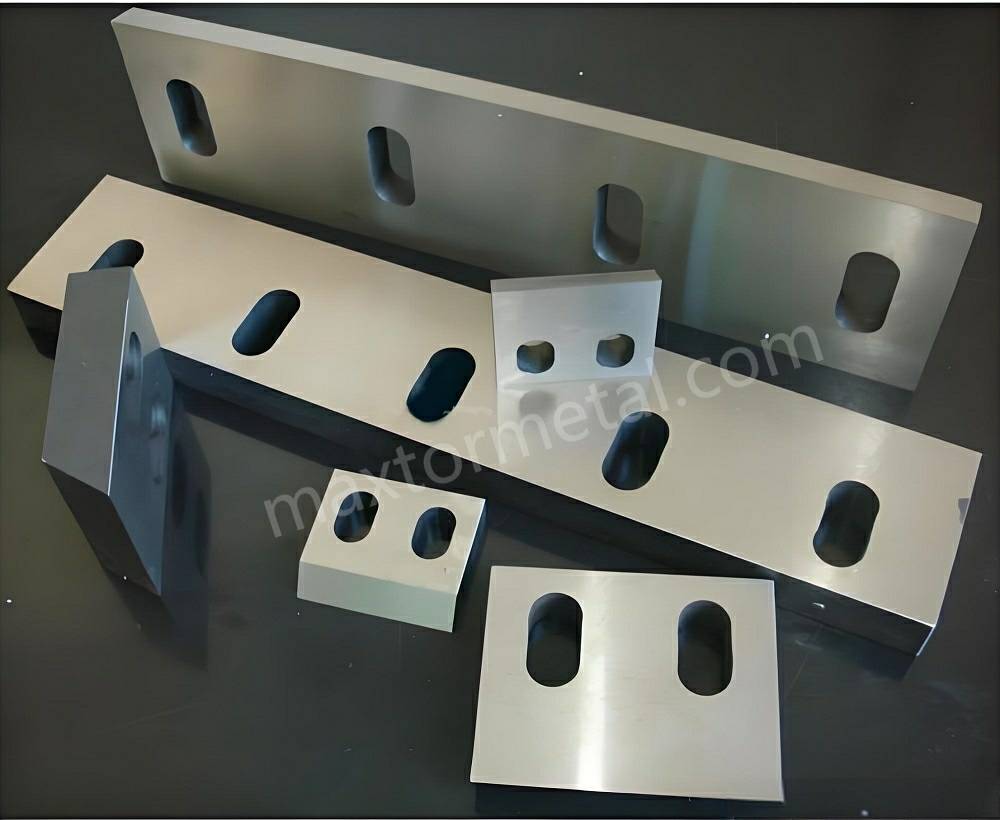
5. Regular Inspection & Maintenance Plan
A structured and proactive Plastic Crusher maintenance plan prevents unplanned downtime, reduces operational costs, and maximizes the lifespan of plastic crusher blades. Implementing a preventive maintenance strategy ensures consistent shredding performance and minimizes safety risks.
Studies show that planned maintenance reduces machine downtime by up to 45% compared to reactive maintenance (Source: Manufacturing Today, 2023).
5. 1Recommended Maintenance Schedule
The following table provides an optimal maintenance plan based on industry best practices.
مهمة الصيانة | تكرار | Procedure |
Visual Blade Inspection | يوميًا | Look for visible wear, cracks, or alignment issues. |
Check Blade Bolts & Alignment | أسبوعي | Ensure bolts are tight and blades are correctly aligned. |
Lubricate Blade Mounting Area | أسبوعي | Apply industrial lubricant to prevent corrosion. |
Clean Blade Compartment | كل أسبوعين | Remove plastic residues, dust, and debris from the machine. |
Monitor Energy Consumption | شهريا | Sudden energy spikes indicate blade dullness or misalignment. |
Blade Sharpening or Replacement | As needed | Sharpen or replace blades when cutting efficiency drops. |
Full Machine Inspection | كل 3 أشهر | Check all components, belts, bearings, and gears for wear. |
5.2 Blade Inspection Checklist
Use this checklist during weekly maintenance to ensure crusher blades are in optimal condition:
✅ Blade edges appear sharp and free of chipping
✅ No signs of corrosion or rust
✅ Blade bolts are tightened to the manufacturer’s recommended torque
✅ No abnormal vibrations or noises when the crusher is operating
✅ Blade clearance is set according to machine specifications
5.3 Common Maintenance Mistakes to Avoid
❌ Skipping regular inspections – Leads to unexpected breakdowns.
❌ Ignoring slight vibrations – Early misalignment can worsen over time.
❌ Delaying blade replacements – Worn blades increase energy usage and decrease cutting quality.
❌ Not using proper lubrication – Can cause rust buildup, leading to misalignment.
💡 نصيحة احترافية: Train operators to recognize early warning signs of blade wear to prevent costly damage.
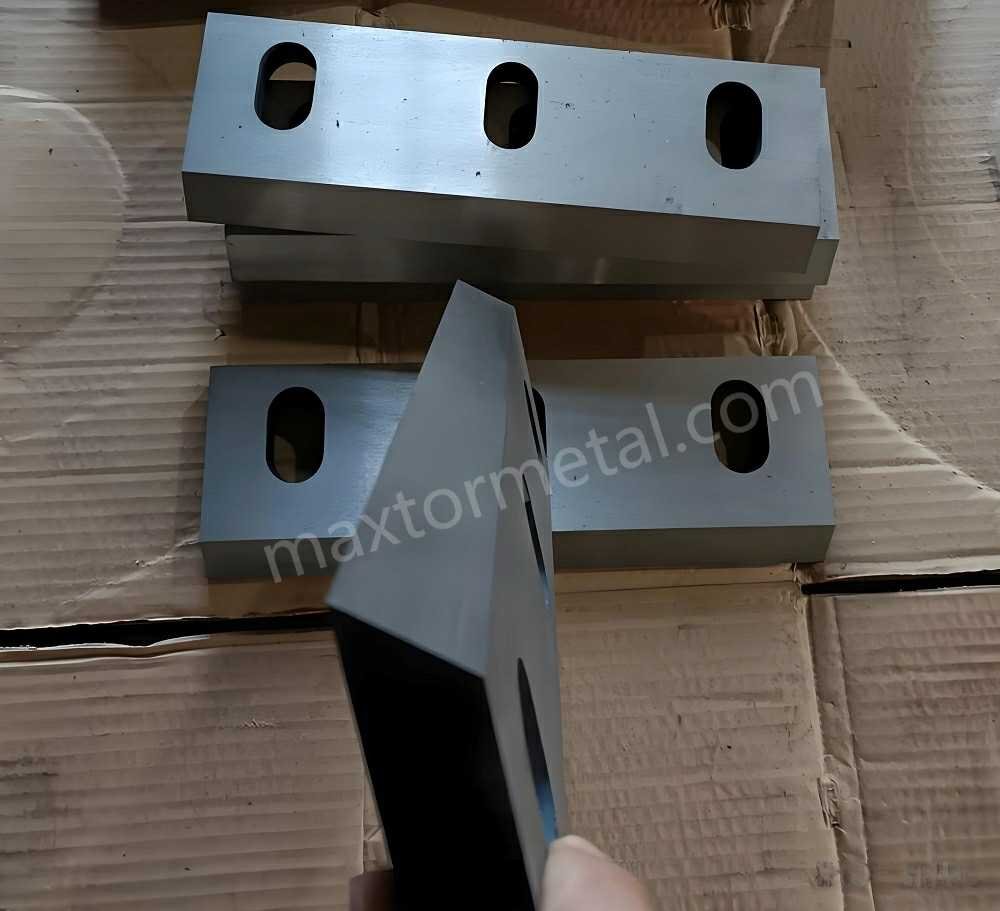
6. FAQs on Plastic Crusher Blade Replacement
Below are common questions related to crusher blade replacement and maintenance, along with detailed answers.
6.1 How Often Should Blades Be Replaced?
Answer: The replacement frequency depends on multiple factors, including:
🔹 Type of material being shredded – Hard plastics wear blades faster than soft plastics.
🔹 Shredding frequency – Continuous high-volume operations require more frequent replacements.
🔹 Blade material – HSS blades last 3-6 months, while carbide blades can last 6-12 months with proper maintenance.
💡 Best Practice: Track replacement intervals and adjust schedules based on actual wear patterns.
6.2 How Can I Extend Blade Lifespan?
Answer: Implement the following strategies to prolong the life of your crusher blades:
✅ Use the right blade material – Choose carbide blades for abrasive materials and alloy blades for general use.
✅ Avoid overloading the machine – Excess material buildup increases stress on the blades.
✅ Maintain proper lubrication – Prevents rust and improves cutting performance.
✅ Follow the correct shredding speed – Reducing excessive speeds minimizes wear.
✅ Rotate and flip blades – If applicable, use both sides of double-edged blades before replacing them.
💡 دراسة الحالة: A manufacturer who implemented weekly blade inspections saw a 40% increase in blade lifespan by reducing machine overloads and improving lubrication practices.
6.3 What Causes Frequent Blade Wear?
Answer: Several factors contribute to accelerated blade wear, including:
❌ Shredding abrasive or reinforced plastics – Materials like fiberglass-reinforced plastics (FRPs) wear down blades faster.
❌ Incorrect blade alignment – Increases friction and causes uneven wear.
❌ Poor maintenance practices – Irregular inspections lead to unnoticed damage.
❌ Excessive machine speed – High RPMs generate excess heat and stress, dulling blades prematurely.
💡 حل: Conduct a material analysis to determine the right blade type and adjust operational settings accordingly.
6.4 Why Does a New Blade Sometimes Not Perform Optimally at First?
Answer: A newly installed blade may experience initial inefficiencies due to:
🔹 Improper installation – Misaligned blades reduce cutting precision.
🔹 Insufficient break-in period – Some blades require a short “run-in” time to reach peak performance.
🔹 Incorrect torque settings – Over-tightened bolts may distort the blade, while under-tightening causes instability.
💡 Best Practice: After replacing blades, conduct a 10-minute test run at reduced speed to ensure proper performance.
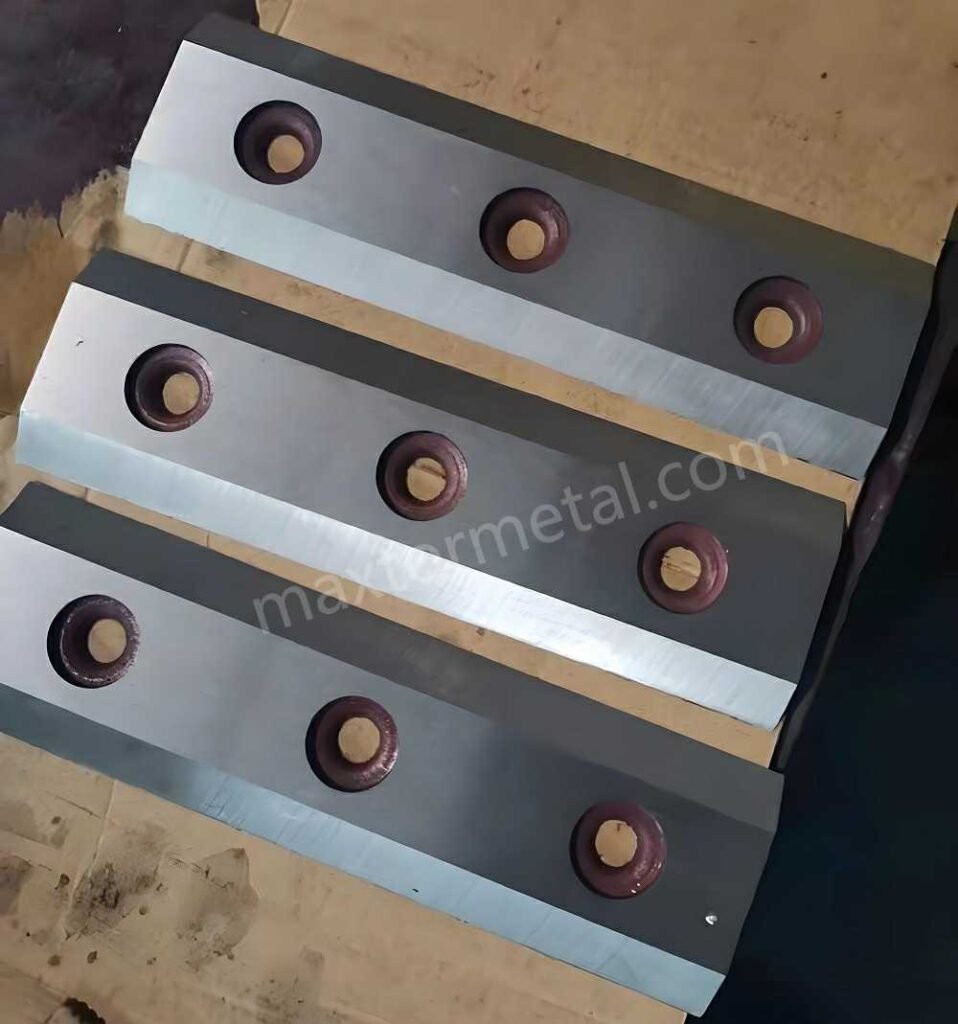
6.5 What Are the Signs of Improper Blade Installation?
Answer: If the blade is not installed correctly, you may notice:
❌ Excessive vibration or noise – Indicates misalignment or loose bolts.
❌ Uneven shredded material size – Suggests improper blade spacing.
❌ Blade overheating – Can be due to excessive friction or dull edges.
❌ Frequent jamming – Caused by incorrect blade orientation.
💡 نصيحة احترافية: If these issues occur after blade replacement, recheck alignment and torque values immediately.
6.6 What Safety Precautions Should Be Followed During Blade Replacement?
Answer: To prevent injuries and machine damage, follow these safety steps:
✅ Always shut down and lockout/tagout (LOTO) the machine before maintenance.
✅ Wear cut-resistant gloves and safety goggles to protect against sharp edges.
✅ Use proper lifting tools if blades are heavy to prevent strain injuries.
✅ Double-check blade alignment before tightening bolts to avoid operational failures.
✅ Ensure the machine is fully tested before resuming full operation.
💡 بيانات الصناعة: According to workplace safety reports, 70% of machine-related injuries occur due to improper maintenance procedures (Source: Safety & Engineering Journal, 2023).
Replacing شفرات كسارة البلاستيك correctly ensures efficient shredding, reduced downtime, and longer machine lifespan. Following this guide will help maintain optimal performance while minimizing operational costs.
🔹 Need high-quality industrial blades? Nanjing Metal offers حلول الشفرة المخصصة designed for maximum durability and performance.
📩 اتصل بنا اليوم for a free consultation!