Industrial blades and knives play a critical role in manufacturing, metal processing, paper production, and many other industries. Their performance and longevity directly affect efficiency, maintenance costs, and overall production output. One of the key factors that determine blade durability is the industrial blade hardening process.
Choosing the right hardening method can make a significant difference in blade wear resistance, cutting precision, and cost-effectiveness. The two most common hardening techniques are through hardening and surface hardening. Each offers distinct advantages and is suited for different applications. This article will provide an in-depth comparison of these two methods, helping businesses select the best hardening process for their industrial cutting blades.
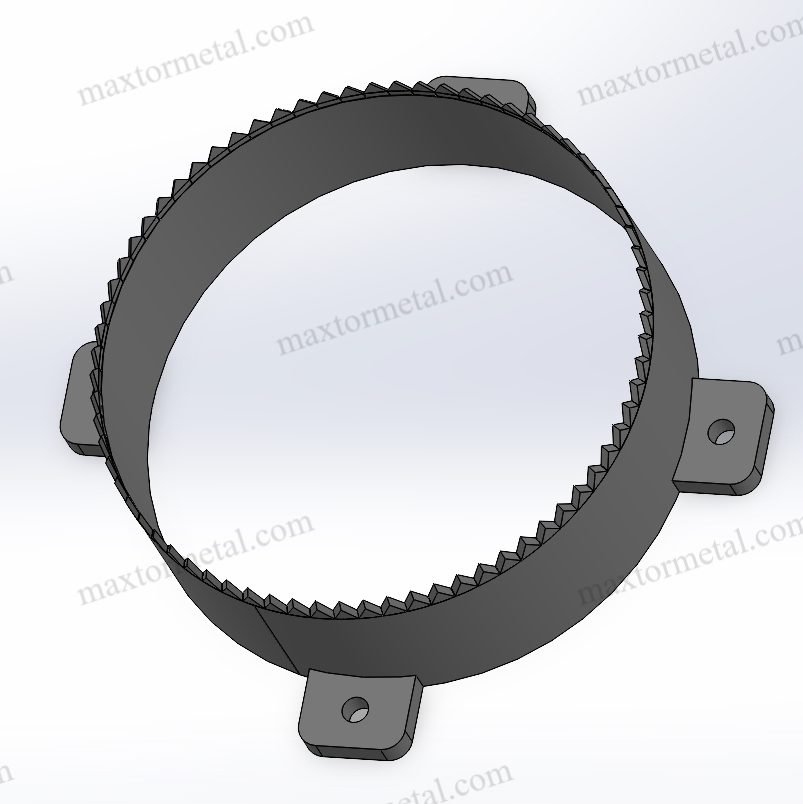
1. Understanding Blade Hardening
Industrial blades and knives endure intense stress during cutting, slicing, and processing tasks. Without proper industrial blade hardening, they wear down quickly, reducing cutting precision and increasing operational costs. To maximize blade lifespan, manufacturers use blade heat treatment techniques like through hardening and surface hardening to enhance hardness, wear resistance, and overall performance.
How Hardening Improves Blade Performance
Industrial knives must be hard enough to withstand abrasion and maintain a sharp edge while being tough enough to absorb impacts without breaking. The blade hardening process strengthens the metal structure, making the cutting edge more resistant to deformation and fracture.
Benefits of Blade Hardening:
✔ عمر افتراضي ممتد – Reduces wear and tear, lowering replacement frequency.
✔ Improved Wear Resistance – Withstands continuous friction from cutting abrasive materials.
✔ تحسين أداء القطع – Maintains sharpness for consistent, precise cuts.
✔ Higher Cost Efficiency – Reduces maintenance, downtime, and replacement costs.
Without hardening, machine blades made from high-carbon or alloy steels would wear out rapidly, leading to frequent downtime and increased production costs.
The Metallurgical Science Behind Hardening
Hardening alters the microstructure of steel blades, typically converting the soft ferrite and pearlite structure into hard martensite through rapid cooling. The process generally involves:
- التدفئة – The blade is heated to a critical temperature (typically 800–1000°C, depending on the steel type).
- التبريد – The blade is rapidly cooled in water, oil, or air to trap the hard martensitic structure.
- هدأ (optional) – The blade is reheated at a lower temperature to balance hardness and toughness.
Different hardening methods determine how much of the blade undergoes transformation, affecting its overall performance.
Basic Principles of Hardening Methods
Both through hardening and surface hardening strengthen industrial blades but in different ways. The primary difference lies in how much of the blade structure is hardened:
Hardening Method | عملية | Hardness Distribution | Core Toughness | التطبيقات الشائعة |
Through Hardening | Entire blade is heated and quenched | Hard throughout | صلابة أقل | High-impact cutting, heavy-duty applications |
Surface Hardening | Only the outer layer is hardened | Hard exterior, softer core | Higher toughness | Wear-resistant, impact-absorbing applications |
Which Industries Rely on Blade Hardening?
Industrial blade wear resistance is critical in sectors such as:
- Metal Processing – Cutting, stamping, and shearing of hard metals.
- Paper & Printing – Slitting and perforating blades in high-speed paper production.
- إعادة تدوير البلاستيك – Granulator blades processing hard plastics.
- Wood & Textile – Cutting woven materials and lumber with minimal fraying.
By choosing the right blade heat treatment, manufacturers ensure their industrial knives perform efficiently while minimizing downtime and costs.
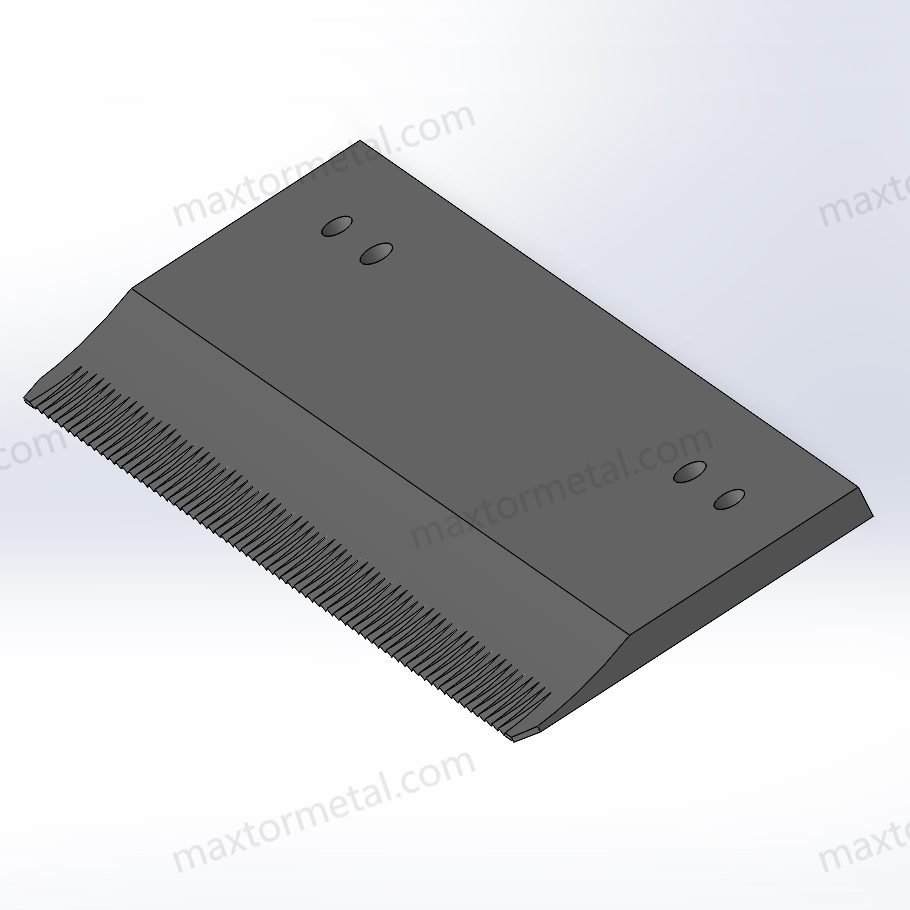
2. Through Hardening
Definition and Process
Through hardening, also called deep hardening, is a metal heat treatment process that ensures uniform hardness throughout the entire blade structure. This is achieved by heating the blade above its critical transformation temperature and then rapidly cooling it (quenching) to lock in a fully hardened martensitic structure.
The quenching medium significantly affects the final properties:
Quenching Medium | Cooling Rate | التأثير على الشفرة |
ماء | Very fast | Highest hardness but increased brittleness |
زيت | معتدل | Good balance of hardness and toughness |
هواء | Slow | Lower hardness but increased toughness |
After quenching, the blade may be tempered to fine-tune its hardness and prevent excessive brittleness.
Key Features, Advantages, and Disadvantages
Features of Through Hardening
✔ Full martensitic transformation, ensuring a consistently hard structure.
✔ Enhances blade durability for high-load applications.
✔ Ideal for thick industrial blades requiring uniform wear resistance.
Advantages of Through Hardening
✔ Uniform Hardness – Maintains consistent cutting performance.
✔ Excellent Wear Resistance – Reduces edge degradation over time.
✔ Longer Blade Lifespan – Fewer replacements mean lower long-term costs.
Disadvantages of Through Hardening
✘ Less Impact Resistance – More prone to cracking under shock loading.
✘ Higher Initial Cost – Requires specialized heat treatment equipment.
Industries and Applications
Through-hardened blades are widely used in industries requiring high-wear resistance and consistent hardness across the cutting edge.
صناعة | طلب | Why Use Through Hardening? |
Metal Processing | Shearing, slitting, stamping | Maintains sharpness while cutting tough metals |
النجارة | Saw blades, chipper knives | Ensures durability under high-speed cutting |
إعادة التدوير | آلات التقطيع والحبيبات | Withstands heavy-duty plastic and rubber processing |
Paper & Textile | Perforation, slitting | Requires fine, precise cutting with minimal deformation |
Case Study: Improving Productivity with Through-Hardened Blades
A steel processing company used surface-hardened knives for slitting thick metal sheets but experienced frequent blade chipping. After switching to through-hardened industrial cutting blades, they:
✔ Increased blade lifespan by 40%.
✔ Reduced blade breakage incidents by 60%.
✔ Lowered downtime costs by $20,000 per year.
This demonstrates how the right heat treatment method significantly impacts operational efficiency.
When Should You Choose Through Hardening?
✅ If your application demands consistent hardness across the blade.
✅ If you need high wear resistance in extreme cutting conditions.
✅ If your blade thickness allows for deep penetration of hardness.
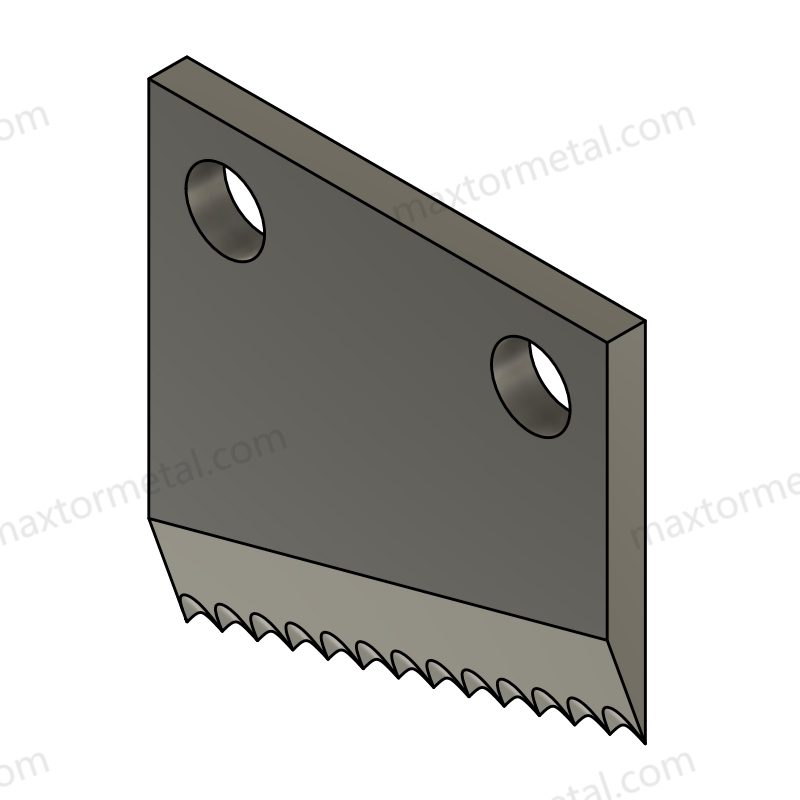
3. Surface Hardening
Definition and Process
Surface hardening, also known as case hardening, is a metal heat treatment process designed to enhance the blade wear resistance by increasing hardness only at the outer layer while keeping the core tough and flexible. This method is widely used in industrial cutting blades, where impact absorption and edge retention are critical.
Unlike through hardening, which alters the entire blade structure, surface hardening applies heat or chemical diffusion only to the outermost layers. The most common surface hardening techniques include:
Common Surface Hardening Methods
طريقة | عملية | Hardness Depth | Key Applications |
Induction Hardening | Uses electromagnetic fields to heat the blade surface before rapid quenching. | 1–5 mm | High-wear applications like saw blades, shear knives. |
التكرير | Carbon is diffused into the blade’s surface at high temperatures, then quenched. | 0.5–2 mm | Gears, cutting tools, and impact-resistant blades. |
نيترة | Introduces nitrogen into the steel surface to form a hard layer without quenching. | 0.2–1 mm | Applications requiring extreme wear resistance, such as plastic cutting knives. |
Each of these processes offers unique benefits depending on the blade’s intended cutting conditions and material requirements.
Key Features, Advantages, and Disadvantages
Features of Surface Hardening
✔ Only hardens the outer layer, leaving the core tough and ductile.
✔ Provides excellent blade wear resistance for prolonged edge retention.
✔ Reduces the risk of blade breakage under sudden impact.
Advantages of Surface Hardening
✔ متانة معززة – The hard outer shell resists abrasion, improving performance.
✔ Improved Shock Absorption – The soft inner core prevents sudden fractures.
✔ Cost-Efficient Manufacturing – Lower energy consumption compared to through hardening.
Disadvantages of Surface Hardening
✘ Limited Hardness Depth – Only a thin layer of the blade is hardened.
✘ Not Ideal for Heavy-Duty Cutting – Can wear down faster under extreme pressure.
Industries and Applications
Surface hardening is widely used in industries where abrasion resistance and impact absorption are essential.
صناعة | طلب | Why Use Surface Hardening? |
معالجة الأغذية | Meat slicing, packaging knives | Maintains a sharp edge without chipping under impact. |
إعادة تدوير البلاستيك | Shredder and granulator knives | Enhances blade lifespan for cutting tough plastics. |
زراعة | Harvesting, mowing, and processing blades | Improves cutting efficiency while resisting dirt and debris wear. |
Textile & Paper | Perforation, slitting blades | High-speed precision cutting with minimal wear. |
Case Study: Improving Productivity with Surface-Hardened Blades
A plastic recycling plant used through-hardened knives for cutting rigid plastic materials but faced frequent blade replacements due to impact-related fractures. After switching to nitrided surface-hardened knives, they observed:
✔ 50% longer blade life, reducing replacement costs.
✔ 30% less downtime, improving operational efficiency.
✔ Enhanced cutting performance, with sharper edges maintained for longer.
This example highlights how choosing the right blade heat treatment optimizes both durability and cost-effectiveness.
When Should You Choose Surface Hardening?
✅ If impact absorption is essential to avoid chipping or blade failure.
✅ If cost-effectiveness and lower initial investment are priorities.
✅ If you need a balance between hardness and flexibility.
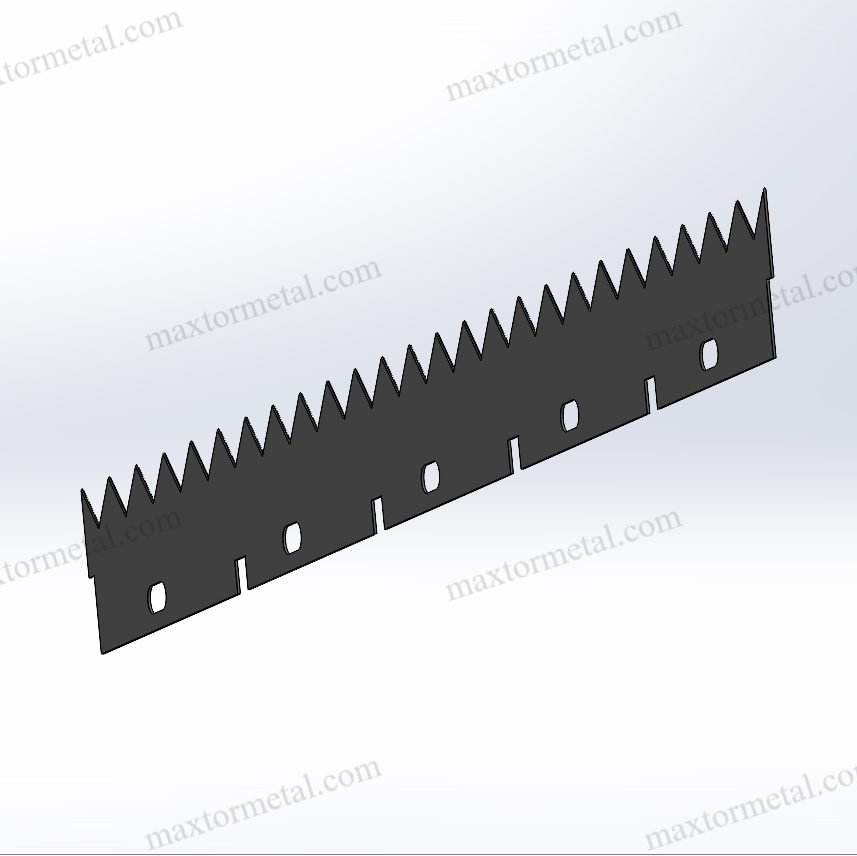
4. Choosing the Right Hardening Method
Selecting the right industrial blade hardening method requires analyzing multiple factors, including blade material, cutting conditions, and cost-effectiveness.
العوامل الرئيسية التي يجب مراعاتها
عامل | Through Hardening | Surface Hardening |
نوع المادة | Best for high-carbon, high-alloy steels | Works well with low-alloy steels |
Cutting Conditions | Best for high-wear, high-load environments | Ideal for impact-prone applications |
سمك الشفرة | Best for thick knives and saw blades | Best for thin, flexible knives |
طول العمر | Typically 30–50% longer lifespan | Moderate lifespan but lower cost |
Cost Considerations | Higher initial cost but fewer replacements | Lower upfront cost but may require more frequent replacements |
Cost Analysis: Short-Term vs. Long-Term Investment
While surface-hardened blades have a lower initial investment, they may wear out faster than through-hardened knives in high-stress environments. Businesses must evaluate whether short-term savings outweigh long-term operational costs.
Cost Comparison Example:
نوع الشفرة | Initial Cost per Blade | متوسط العمر | Annual Replacement Cost (for 100 Blades) |
Through-Hardened Knife | $100 | 12 شهرًا | $10,000 |
Surface-Hardened Knife | $60 | 6 أشهر | $12,000 |
🔹 While through-hardened blades require a higher upfront investment, their longer lifespan leads to cost savings over time.
Case Study: Choosing the Best Hardening Method
A woodworking company needed to choose between through hardening vs. surface hardening for industrial saw blades. Their requirements included:
- Long cutting cycles with minimal downtime.
- High-wear resistance for cutting hardwood.
- Balanced cost-efficiency.
After analysis, they opted for through-hardened saw blades, leading to:
✔ 35% fewer blade replacements annually.
✔ 20% lower maintenance costs.
✔ Consistent cutting precision over longer periods.
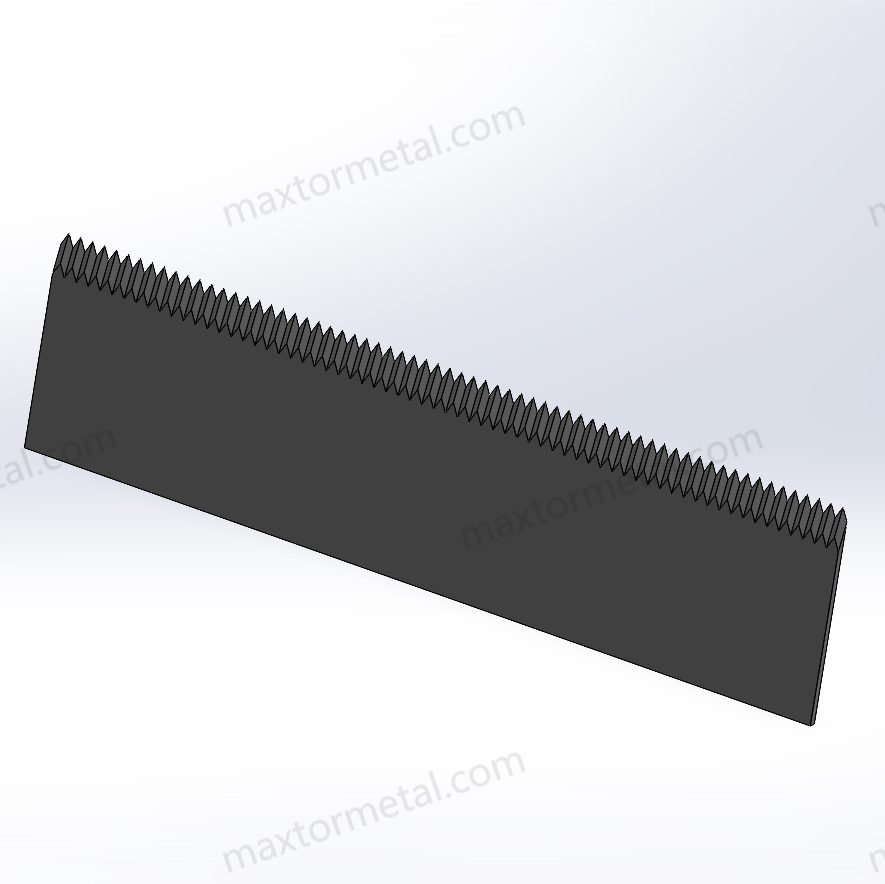
5. Industry Trends & Advanced Hardening Technologies
The field of industrial blade hardening is evolving rapidly as industries demand higher performance, wear-resistant materials, and cost-efficient manufacturing processes. Advances in heat treatment technology are making machine blades and industrial cutting blades more durable and effective while improving energy efficiency in production.
New Hardening Methods Transforming the Industry
Traditional through hardening and surface hardening remain widely used, but newer methods are gaining traction. These advanced processes provide better hardness control, reduced energy consumption, and enhanced blade durability.
1. Laser Hardening
✔ Uses a high-intensity laser to heat the blade’s surface rapidly.
✔ Creates a precisely controlled hardened layer without requiring quenching.
✔ Ideal for: Thin, high-precision industrial knives (e.g., paper cutting, food processing).
2. Plasma Nitriding
✔ Infuses nitrogen into the steel under a vacuum environment.
✔ Produces an ultra-hard surface (higher wear resistance than carburizing).
✔ Ideal for: Granulator blades, shredder knives, and high-wear cutting tools.
3. Cryogenic Hardening
✔ Involves deep-freezing blades to temperatures as low as -196°C (-320°F).
✔ Enhances metal microstructure, reducing internal stresses.
✔ Ideal for: High-impact blades used in metal shearing and plastic cutting.
Hardening Method | عملية | مزايا | أفضل التطبيقات |
Laser Hardening | Rapid laser heating of blade surface | Precise control, no quenching needed | Thin industrial knives |
Plasma Nitriding | Nitrogen diffusion at high temperatures | Extreme wear resistance, eco-friendly | Granulator and shredder knives |
Cryogenic Hardening | Freezing steel to ultra-low temperatures | Improves toughness, reduces stress | High-impact blades |
Growing Demand for High-Wear-Resistant Materials
The increasing demand for longer-lasting industrial knives is driving manufacturers toward superior wear-resistant materials. Some trends include:
✔ High-Speed Steel (HSS) Blades – Improved cutting precision and longevity.
✔ Carbide-Tipped Blades – Extreme hardness for metal-cutting applications.
✔ Ceramic-Coated Knives – High wear resistance for food processing and textiles.
These advancements allow machine blades to operate longer between replacements, reducing maintenance costs and improving efficiency.
Smart Manufacturing & Automation in Heat Treatment
Modern heat treatment facilities now incorporate automation and AI-driven precision controls, ensuring:
✔ Consistent hardness levels across large production batches.
✔ Reduced energy consumption, making the process more eco-friendly.
✔ Improved quality control, reducing material waste and ensuring uniform blade hardness.
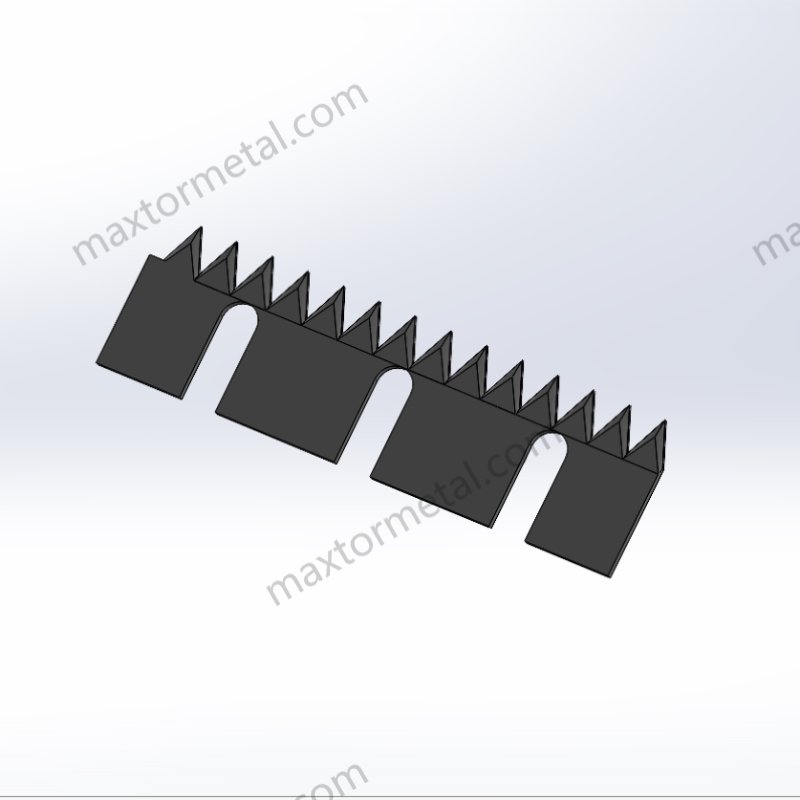
6. نانجينغ Metal’s Professional Blade Solutions
With 18 years of experience, Nanjing Metal specializes in custom industrial cutting blades and high-performance heat treatment solutions. We provide:
- Custom industrial cutting blades– We design blades for metal cutting, paper slitting, plastic shredding, and food processing.
- Advanced hardening technologies – We use advanced through hardening and surface hardening techniques tailored to different applications.
- Expert consulting – Every blade undergoes rigorous hardness testing to ensure durability.
7. الأسئلة الشائعة
1. What is the main difference between through hardening and surface hardening?
✔ Through Hardening: Hardens the entire blade, offering uniform wear resistance.
✔ Surface Hardening: Only hardens the outer layer, improving shock absorption.
2. How do I determine the right hardening method for my industrial knives?
Consider the following:
🔹 Material Type – Harder materials benefit from through hardening, softer steels work well with surface hardening.
🔹 Cutting Conditions – High-impact environments require surface hardening for flexibility.
🔹 Budget Considerations – Through-hardened knives last longer but have higher initial costs.
3. How does blade hardening impact long-term costs?
نوع الشفرة | Initial Cost per Blade | عمر | Annual Replacement Costs (for 100 blades) |
Through-Hardened Knife | $100 | 12 شهرًا | $10,000 |
Surface-Hardened Knife | $60 | 6 أشهر | $12,000 |
🔹 Through hardening saves costs over time due to its longer durability.
4. How does Nanjing Metal ensure blade quality?
✔ State-of-the-art heat treatment facilities.
✔ Strict hardness testing and quality inspections.
✔ Industry-specific expertise in metal cutting, paper processing, plastic recycling, and food slicing.
اختيار الصحيح industrial blade hardening method depends on your application, material, and budget. Whether you need through-hardened knives for high-stress cutting or surface-hardened blades for impact absorption, making the right choice will improve performance and reduce costs.
🔹 Need expert advice? اتصل بنا اليوم للحصول على استشارة مجانية!
مراجع
- ASM International. (2022). “Heat Treatment Handbook.”
- Metal Cutting Institute. (2023). “Blade Durability Research Report.”