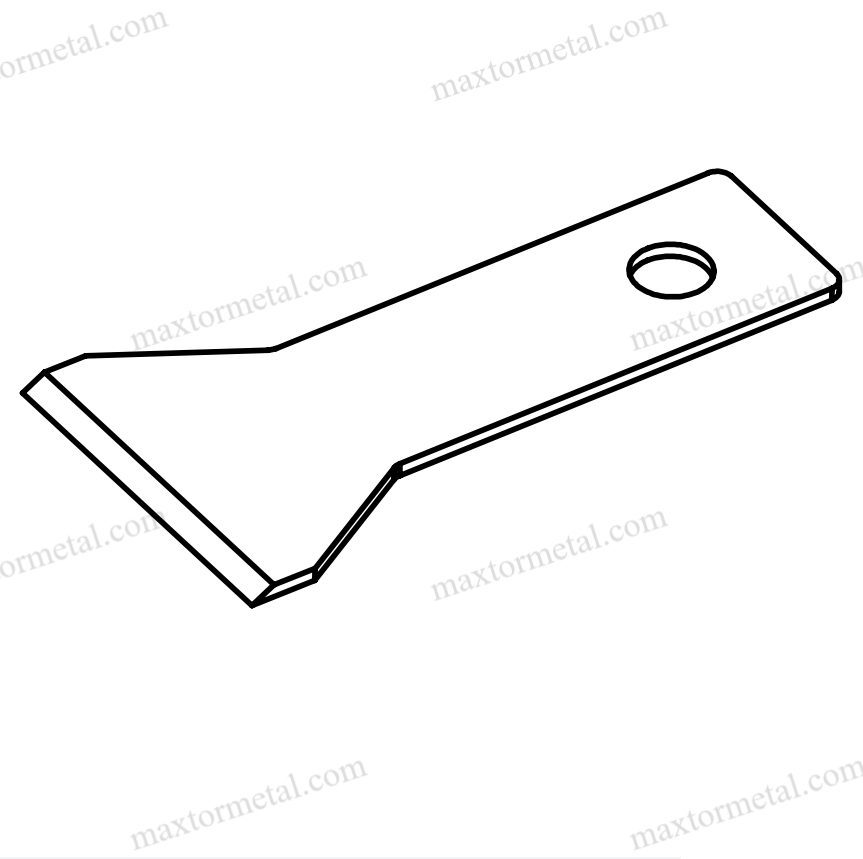
سكاكين التحبيب بالحلقة المائية cut fast and accurately, producing pellets that are uniform in size and highly dense. These systems enhance plastic processing efficiency by reducing waste and minimizing downtime. Features such as quick knife changes and self-cleaning water flow significantly improve operation. However, users must monitor water temperature closely and rely on skilled workers to maintain optimal performance. Pellet quality and maintenance costs are influenced by these factors. Water ring pelletizing and underwater pelletizing methods yield different results, with variations in pellet size and surface finish. If you are interested in a demo or need a شفرة مخصصة tailored to your specific requirements, consider your production goals carefully.
النقاط الرئيسية
- Water ring pelletizing knives use water to cool plastic pellets fast. This makes the pellets hard and the same size.
- This system makes less dust and waste. It helps make better pellets and helps the factory work better.
- Water ring pelletizing knives work with many plastics. They are quieter and easier to fix than some other systems.
- The system needs good water control and regular care. This stops pellets from sticking and keeps machines working well.
- Water ring pelletizing knives cost more at first. But they save money later by stopping long breaks and fixing costs.
- Underwater pelletizing systems make pellets more even. They work better with sticky or soft plastics. But they cost more and need trained workers.
- Picking the best pelletizing system depends on the plastics, what you want to make, and your budget.
- Custom pelletizing blades from experts like Maxtor Metal can help cut better, last longer, and make better pellets.
Advantages of Water Ring Pelletizing Knives
Efficient Cooling
Immediate Pellet Solidification
Water ring pelletizing knives cool pellets very quickly by using water. The water touches the hot pellets right after they are cut. This makes the pellets harden almost right away. Fast cooling stops the pellets from changing shape or sticking together. Slow cooling systems can cause these problems. In factories that make a lot of plastic, this technology helps every pellet keep its shape. Water ring pelletizing knives cool better than air-cooled systems. Workers see smoother and rounder pellets. There are also fewer stops in production. This helps the factory run better, even with tough thermoplastic materials.
Reduced Fines and Dust
The water ring pelletizing process makes less dust and fewer small pieces. When the knives cut the melted polymer, water cools the pellets right away. This stops the pellets from breaking or crumbling. The pellets stay cleaner and there is less waste. This means better product quality and more pellets made. Less dust also keeps other machines cleaner. It is easier to handle and pack the pellets. On busy lines, this helps the work go faster and keeps results steady.
Consistent Pellet Quality
Uniform Size
Water ring pelletizing knives make pellets that are all the same size. This is important for the next steps in making plastic products. The knives cut carefully, and the water cools the pellets right away. Every pellet meets the needed size. Pellets move easily through machines and packing systems. This makes the product better and stops jams or uneven melting later. Workers can trust the process to give the same results every time.
High Particle Density
The way water ring pelletizing knives are made helps each pellet be dense. Fast cooling keeps the shape and stops holes or odd shapes from forming. Dense pellets do not break easily when moved or handled. Data shows that strong pellets are made when energy is used just right. Factories using this method get about 90% pellet strength. Using the same amount of energy each time helps keep pellet quality the same. Industries like car or medical plastics need this kind of steady quality.
Low Noise Operation
Water ring pelletizing systems are much quieter than dry-cutting ones. The water soaks up sound and stops loud vibrations. This makes the workplace safer and less noisy for workers. It is easier for factories to follow rules about noise. Quieter machines also help workers feel better and pay attention. This helps the whole pelletizing process work well.
Tip: A quieter factory floor keeps workers’ ears safe and helps everyone work better together.
Cost-Effective Maintenance
Water ring pelletizing knives help factories spend less on repairs. The water keeps the knives cool and clean while they work. This cooling stops the blades and parts from wearing out fast. Because of this, the knives last longer and do not need to be replaced often. Workers can change or clean the knives quickly because the system is easy to open. Less downtime means factories make more pellets and work faster.
Simple jobs like checking if the blade is sharp or cleaning the water ring take less time than with dry-cutting systems. The water also stops sticky plastic from building up on the knives. This keeps the cutting area clear and helps the machine run smoothly. Factories using water ring pelletizing systems often pay less for repairs and have fewer surprise breakdowns. These savings grow over time, so the system is a good choice for companies that want to save money in the long run.
Note: Doing regular checks and easy cleaning helps the pelletizing line work well and stops expensive problems.
Versatility in Pelletizing
Water ring pelletizing knives can work with many kinds of plastics and setups. Their design lets them cut both soft and hard thermoplastic materials. This makes them useful for small labs and big factories. Companies can switch materials or change how much they make without big changes.
Knife makers use strong materials and special coatings to make the knives last longer. For example, some knives are made from high-speed steel or carbide with heat treatments. These things help the knives cut many types of thermoplastics easily. Careful machine work makes sure each knife fits right and cuts pellets to the right size.
- Water ring pelletizing knives help make lots of pellets that are the same size and have less dust.
- Special coatings and heat treatments make the knives tough, so they work with many thermoplastics.
- Careful design lets the knives fit different machines and do many jobs.
- Makers can change the blade shape and material for each customer.
- Customers from many countries say they get better pellets, longer knife life, and less downtime.
- The knives work with many pelletizing machines, like underwater, strand, and die-face systems.
- Companies can try small batches before buying a lot of knives.
This flexibility helps factories keep up with new market needs fast. Whether making pellets for cars, hospitals, or other uses, water ring pelletizing knives give steady quality. Workers can trust the system to make good pellets, even when changing to different thermoplastics.
Tip: Picking a flexible pelletizing system helps companies stay ahead and meet new needs without spending too much.
Disadvantages of Water Ring Pelletizing Knives
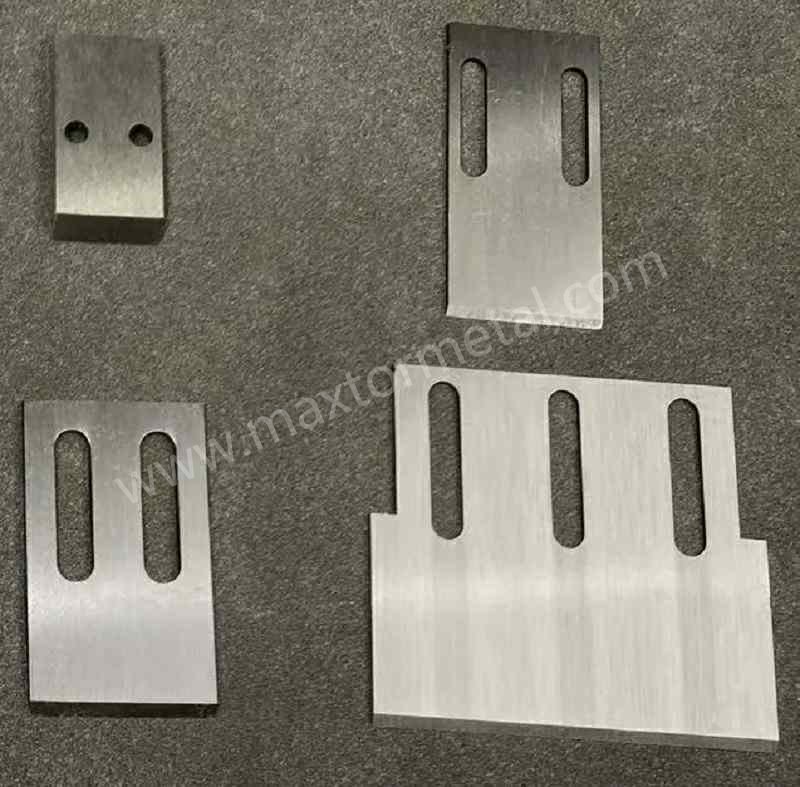
Initial Equipment Cost
Water ring pelletizing knives cost more at first than some other systems. Companies need to buy special cutting units, water systems, and control panels. These parts make the starting price higher. Many factories look at these costs and compare them to dry-cut or strand pelletizers. Water ring systems usually have a bigger price tag at the beginning.
Extra pumps, filters, and water tanks also raise the cost. Some businesses wait to switch because of this. If they have more money, they might pick underwater pelletizing systems instead. For small or new companies, the high starting cost can make them slow to upgrade.
Note: Spending more at first can save money later by making work faster and wasting less, but companies need to plan for this big cost.
احتياجات الصيانة
Water ring pelletizing knives need regular care to work well. Workers must check and fix many parts on a schedule. Scraper blades need checking every three months. Pan liners should be checked every month. Power assemblies need service once a year. These jobs stop problems like dull blades or parts wearing out.
A system that gets good care runs smoothly and does not stop often. Factories use tools to measure moisture, energy, and pellet size. They also test how strong the pellets are. These checks help workers find problems early and fix them fast.
Here is a table showing when to do maintenance:
Component | Service Interval | Common Issues Prevented |
---|---|---|
Scraper Blades | كل 3 أشهر | Dullness, misalignment |
Pan Liners | شهريا | Wear, buildup |
Power Assemblies | سنويا | Lubricant loss, mechanical wear |
Operators use math tools like standard deviation and Weibull modeling to keep cutting sharp. This helps the system work well and makes good pellets. But, doing regular checks and needing skilled workers can make labor costs go up. Some factories think underwater pelletizing systems are easier to take care of, depending on what they need.
Tip: Keeping good records of maintenance helps factories see problems early and make better pellets.
Water Management
Water management is hard for water ring pelletizing knives. The system always needs clean water to cool the pellets. Factories must set up pumps, filters, and tanks for this. If the water gets dirty, the pellets may stick or look bad.
Workers must watch water temperature and flow all the time. If water gets too hot, cooling slows down. This can hurt how the pellets look and work. Some factories use chillers to keep water cold, but this uses more energy and costs more.
Getting rid of used water is another problem. Factories must follow rules for water disposal. They may need to clean or reuse water before letting it go. This adds more steps to the job. Sometimes, underwater pelletizing systems handle water better because they reuse it in a closed loop.
Callout: Good water management keeps the process steady and pellets looking good. Bad water control can cause stops and cost more money.
Pellet Sticking Issues
Pellet sticking is a common problem in water ring pelletizing. When pellets come out of the die, they are still hot and soft. If the water gets too warm or slows down, pellets do not cool fast. This makes them stick together or form lumps. This happens more when making lots of pellets or using sticky polymers.
Pellet sticking causes many problems:
- Pellets can lump together in the water ring chamber.
- Stuck pellets might block the way out.
- Clumped pellets lower quality and make more waste.
Factories must watch water temperature and flow all the time. If the water does not cool pellets right away, sticking happens more. Some workers add surfactants to the water to help pellets not stick. Others change the knife speed or die heat to keep pellets apart. These fixes need careful control and skilled workers.
Tip: Keep water under 25°C and strong flow to stop pellet sticking.
Pellet sticking is not as common in underwater pelletizing. In these systems, the die face and cutting area stay underwater. This cools pellets faster and more evenly. Underwater pelletizers work better with sticky or soft polymers. Many factories pick underwater systems for materials that clump easily.
Pellet sticking also causes trouble for other machines. Stuck pellets can jam conveyors or block dryers. This means more stops and higher repair costs. Workers must pause production to clear jams and clean up. Underwater pelletizing lines often run longer without these problems.
Some companies use underwater pelletizing for special resins or expensive products. They want to avoid pellet sticking and keep things running smoothly. Water ring systems are good for many plastics, but underwater systems give better control for tricky materials.
Note: Picking the right pelletizing method depends on the polymer and pellet quality needed. Underwater systems help stop pellet sticking and make the process more reliable.
Setup Complexity
Setting up a water ring pelletizing system takes planning and skill. Workers must line up the die, set the knife pressure, and adjust the water ring. Each step must be done right for smooth work. If setup is wrong, pellets may be uneven or the system may stop often.
Workers need to put in pumps, filters, and water tanks. They also connect sensors to check temperature and flow. The control panel must be set up to run everything. This setup takes more time and skill than simple pelletizing systems.
Water ring pelletizing needs regular checks. Technicians must look at blade spacing and water flow. If the knife is too close or far from the die, pellet size and shape will change. Bad water flow can make hot spots, causing pellets to stick or change shape.
Callout: Good training and clear setup steps help stop mistakes during installation.
Underwater pelletizing systems also have tricky setup steps. But they often have more automation and smart controls. Underwater systems use closed water loops and better sensors to keep things steady. This makes them good for big or important production lines.
Many factories look at both water ring and underwater systems before picking one. Underwater pelletizing is easier to use with automated lines. It also needs fewer manual changes and less worker help. For companies with fewer skilled workers, underwater systems may be easier to start.
Setup complexity changes how well the factory runs. A bad setup means more stops and worse pellets. Both systems need skilled workers, but underwater systems often make routine changes easier.
Tip: Spending time on setup and training leads to fewer problems and better pellets. Underwater systems can make setup easier for tough jobs.
Water Ring Pelletizing Knives vs. Underwater Pelletizing System
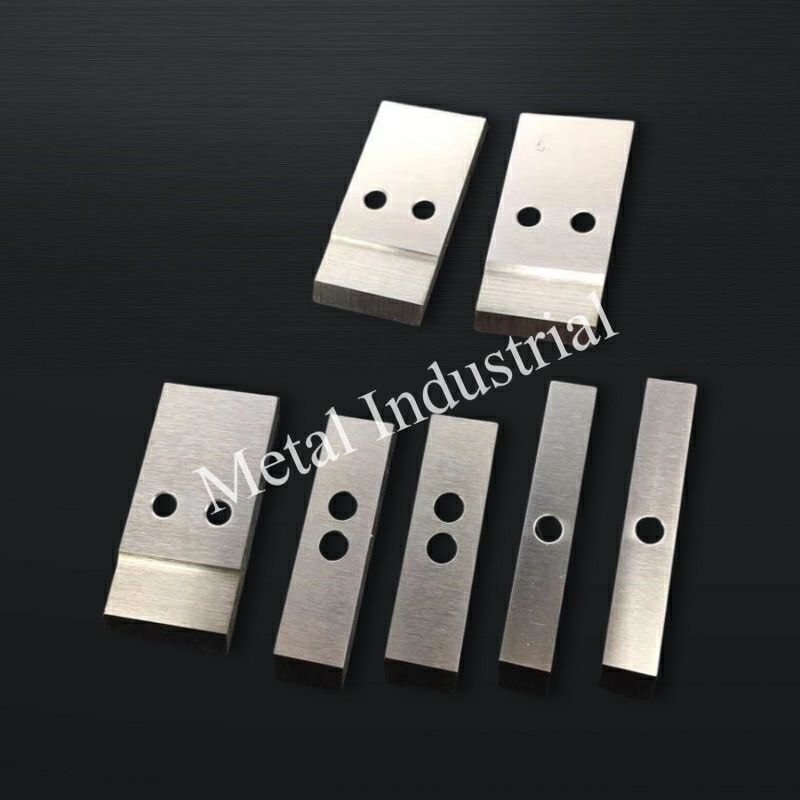
Process Differences
Cutting and Cooling Mechanism
Water ring pelletizing knives use a spinning blade to cut hot plastic at the die face. Right after cutting, water cools the pellets in a ring shape. This makes the pellets hard fast and keeps their shape. This method works for many plastics and can make lots of pellets.
The underwater pelletizing system works differently. Here, the die face and cutting area stay underwater the whole time. The system has a die plate, spinning knives, and a water chamber. The hot polymer goes into the die, and the knives cut it into pellets while underwater. The water cools the pellets right away, making them round. This gives even cooling and helps stop sticking.
When comparing strand and water ring systems, underwater pelletizing has some benefits. It works better with sticky or heat-sensitive plastics. It also lowers the chance of oxidation during pelletizing.
Pellet Discharge and Handling
In water ring pelletizing, pellets leave the die and move through a water ring. The water carries the pellets away from the blade. Workers use a centrifugal dryer to separate pellets from water. This dries the pellets so they are ready for packing or more work.
The underwater pelletizing system also uses water to move pellets to a dryer. But since everything happens underwater, pellets do not stick together as much. The round pellets are easier to handle and move. This system also makes less dust and fewer tiny pieces, so the product is better.
Underwater pelletizing systems often work better than strand systems for moving pellets. They let factories run without stopping and need less help from workers.
System Integration and Automation
Water ring pelletizing systems are easier to set up and use. They need fewer sensors and simple controls. Workers can change knife pressure and water flow with basic training. This makes water ring pelletizing good for small and medium factories.
The underwater pelletizing system has more advanced automation. It uses smart sensors, automatic controls, and closed water loops. These features help control temperature, pressure, and pellet size very well. The system is good for making lots of pellets and needs less worker help.
New technology has made underwater systems even better. Factories can now watch the process live and make quick changes. This helps keep the process steady and raises automation.
Tip: Automated systems help factories save time and make fewer mistakes.
Pellet Quality Comparison
Size Uniformity
Water ring pelletizing makes pellets that are mostly the same size. The spinning knife and water ring work together to cut and cool each pellet fast. Most pellets look alike, but at very high speeds, some may be different sizes.
The underwater pelletizing system is even better at making pellets the same size. Because cutting and cooling happen underwater, all pellets cool at the same speed. This makes pellets almost exactly the same size. This is great for factories that need very strict quality.
Compared to strand and water ring systems, underwater pelletizing gives better size control. It helps make top-quality pellets for special uses.
تشطيب السطح
Pellets from water ring pelletizing are smooth, but if the water is too warm, they can get rough. This method works well for most plastics.
The underwater pelletizing system makes pellets with a shiny, smooth surface. Cooling underwater stops surface problems. This is best for pellets used in cars or medical products.
Underwater pelletizing has helped the plastics industry by making surfaces better and with fewer flaws. New machines focus on making pellets even smoother.
Suitability for Sensitive Polymers
Water ring pelletizing works for many plastics, but not always for sensitive ones. Some materials can stick or change shape if they do not cool fast enough.
The underwater pelletizing system is better for sensitive polymers. It keeps the die face and pellets underwater, which stops damage from heat or air. This is best for plastics that need to stay clear or have special features.
Underwater pelletizing systems are better than strand systems for tricky materials. They help factories meet tough quality rules.
تكاليف التشغيل
Initial Investment
Setting up a water ring pelletizing system costs more than some other ways. Factories must buy special cutters, water rings, and control panels. The first cost is high, but the system makes lots of pellets and less dust.
The underwater pelletizing system usually costs less to start. It is easier to make bigger for large factories. But it might make more dust and has average output.
Here is a table comparing the first cost and output:
System Type | Initial Investment | Output Capacity | Pellet Dust |
---|---|---|---|
Water Ring Pelletizing | عالي | عالي | قليل |
Underwater Pelletizing System | أدنى | Average | أعلى |
Note: Factories should think about both the first cost and long-term gains when picking a pelletizing system.
Energy and Water Consumption
Water ring pelletizing systems use energy for pumps, knives, and dryers. They also need clean water all the time for cooling. Energy use is not too high, but water use can add to costs.
The underwater pelletizing system uses energy for pumps, water flow, and drying too. Some systems can save up to 20% energy, showing they can be efficient. Both systems use about the same water, but underwater systems may recycle water better.
Maintenance and Downtime
Water ring pelletizing systems are easy to take care of. Workers can change knives and clean the system fast. This means less downtime and steady production.
The underwater pelletizing system has more parts, but automation helps. Maintenance can take longer, but the system can run longer without stopping. It is good for making lots of pellets with fewer breaks.
Callout: Picking the best pelletizing process depends on what the factory needs, the plastics used, and the pellet quality wanted.
Benefits of Underwater Pelletizers
Superior Pellet Consistency
The underwater pelletizing system makes pellets that are always the same. Every pellet forms and cools at the same speed because cutting happens underwater. This stops pellets from being odd shapes or sizes. Factories throw away fewer pellets and waste less. When pellets are uniform, machines work better. The underwater process also helps stop surface problems. Workers see that finished pellets look and feel the same each time. This kind of consistency is important for car and medical plastics.
Note: When pellets are always the same, factories have fewer problems and products work better.
Enhanced Process Control
Operators can control the pelletizing process better with underwater systems. The system uses smart sensors and automatic controls to check temperature, water flow, and knife speed. These tools let workers make quick changes if needed. If something goes wrong, the system can fix it fast before pellets get bad. The underwater setup keeps the die face at the right temperature, so pellets keep their shape. This control means fewer stops and less lost time. Factories can also use data to make future runs better.
- Watching the process live helps find problems early.
- Automatic controls keep things running smoothly.
- Less hands-on work means fewer mistakes.
Broader Material Compatibility
The underwater pelletizing system works with many kinds of plastics. It can handle both soft and hard plastics easily. Some plastics need gentle cooling to stay strong. The underwater method gives this gentle cooling. Factories can switch between materials without big changes. This helps companies make many types of pellets. The system also works with plastics that might melt or change in other systems. This means factories can serve more customers and try new markets.
نوع المادة | Underwater Pelletizing System | Water Ring Pelletizing |
---|---|---|
البلاستيك اللين | ممتاز | جيد |
Hard Plastics | ممتاز | جيد |
Heat-Sensitive | ممتاز | Fair |
Filled/Engineered | ممتاز | جيد |
Tip: Using underwater pelletizing helps factories work with more plastics and stay ahead.
Reduced Operator Intervention
A big benefit of underwater pelletizers is less manual work. The system’s automation handles most changes by itself. Operators do not need to check or fix the machine as much. The underwater process also keeps the area cleaner, with less dust and fewer tiny pieces. This means less cleaning and maintenance. Workers can spend more time on other jobs. The system’s design also makes the factory safer by lowering accident risks.
- Automation saves money on labor.
- Fewer manual changes mean more time working.
- Cleaner machines help keep workers safe and efficient.
Callout: Underwater pelletizers give better pellet quality, more control, and less manual work. These benefits help factories make better products and save money.
جدول مقارنة سريع
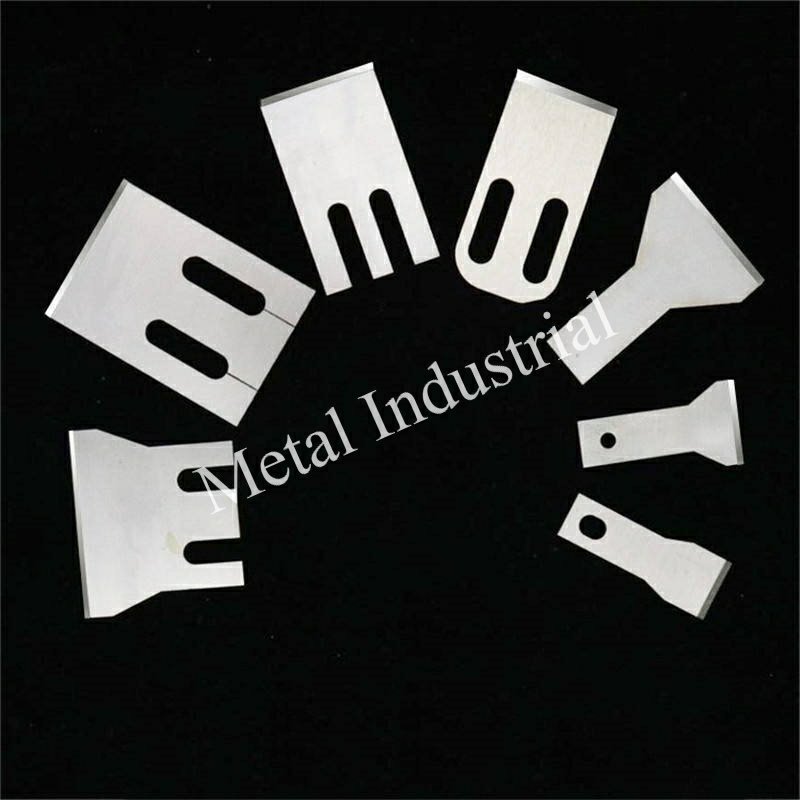
Pros and Cons Overview
Picking between water ring pelletizing knives and underwater pelletizing systems can be tough. Each system has its own good points and some downsides. The table below shows the main features. This helps factories see which system matches what they need.
ميزة | سكاكين التحبيب بالحلقة المائية | Underwater Pelletizing System |
---|---|---|
طريقة التبريد | Water ring cools pellets | Die face and cutting area stay underwater |
Pellet Size Uniformity | عالي | عالية جدًا |
تشطيب السطح | Smooth | Shiny and flawless |
مستوى الضوضاء | قليل | Very low |
Initial Equipment Cost | عالي | أعلى |
Maintenance Complexity | معتدل | Advanced |
Water Management | Needs careful control | Closed-loop, easier to manage |
Pellet Sticking Risk | Possible | نادر |
تنوع المواد | Wide range | Broader range |
مستوى الأتمتة | Basic to moderate | Advanced |
Operator Skill Needed | Skilled | Less manual intervention |
وقت التوقف | قليل | Very low |
Tip: Factories that work with sticky or sensitive polymers often pick the underwater system. This method helps stop pellets from sticking and makes better pellets.
Key Pros and Cons
Water Ring Pelletizing Knives:
- الايجابيات:
- Water ring cools pellets fast
- Pellets are the same size and dense
- Machines are not very loud
- Maintenance costs less money
- Works with many types of plastics
- سلبيات:
- Costs a lot to buy at first
- Needs workers to watch water closely
- Pellets can stick with some plastics
- Setup and care need skilled workers
Underwater Pelletizing System:
- الايجابيات:
- Pellets are always the same because of underwater cooling
- Automation gives better control
- Can handle more types of plastics, even sensitive ones
- Pellet sticking almost never happens
- Needs less help from workers and has less downtime
- سلبيات:
- Costs even more to buy and set up
- Maintenance is harder to do
- Some systems need special training for workers
Note: The underwater system is best for special or expensive plastics. It gives better control, needs less hands-on work, and makes higher quality pellets.
Summary List:
- Water ring pelletizing knives are good for general plastics and flexible jobs.
- Underwater pelletizing systems are best for tough jobs where pellet quality and steady work are important.
- Both systems use water to cool, but underwater cooling makes pellets more even.
Factories should think about what they want to make, what plastics they use, and how much money they have before picking a system. The underwater system often gives the best results when high quality is needed.
When to Choose Water Ring Pelletizing Knives
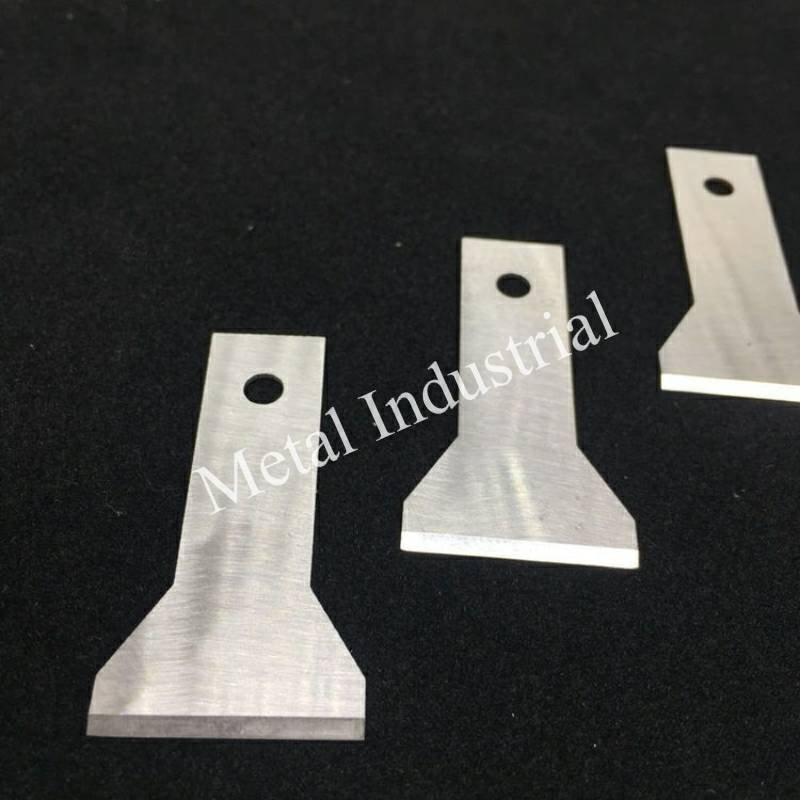
أفضل حالات الاستخدام
Water ring pelletizing knives are great for some factories. People pick this system because it is reliable and saves money. Here are times when water ring pelletizing works best:
- Factories that use high-melt-strength materials, like polyolefins and polystyrene, get good results. These materials need strong cutting and cooling, which this system gives.
- Recycling centers like water ring pelletizing because it is tough and cheap to run. The knives can cut recycled plastics, even if the plastic is not always the same.
- Factories with small spaces often use water ring pelletizing. The machines are small, so they fit in tight areas and are easy to set up.
- If workers want simple machines, this system is easy to use. One person can start, stop, and change pellet size after a little training.
- Production lines that do not need to make a lot of pellets at once do well with this system. It does not have problems like die freeze-off, which can stop other machines.
- Companies that want to spend less money at first often pick water ring pelletizing. The machines cost less than underwater systems but still make good pellets.
- The process makes pellets that are round and flat. These pellets cool fast and are easy to move with a water ring and dryer.
Tip: Water ring pelletizing knives are simple, save money, and make good pellets for many plastics.
When to Consider Alternatives
Sometimes, water ring pelletizing is not the best choice. In these cases, other systems might work better. Here are some reasons to pick something else:
- If machines break a lot or cost too much to fix, another system might be cheaper and have less downtime.
- Soft or low-melting plastics can cause trouble in water ring systems. These plastics can make pellets that are not the same size, clog the machine, and need more cleaning. This means fewer pellets and lower quality.
- If there are strict rules about water use, water ring pelletizing can be hard to manage. Factories may need to buy extra water cleaning equipment, which costs more.
- If there are not enough trained workers, the system may not run well. Water ring pelletizing needs people who can watch and adjust the machine. Without them, pellet quality can drop.
- If a factory needs to make sticky or high-heat plastics, underwater pelletizing works better. Underwater systems can handle more types of plastics and make more even pellets.
- Factories that need the best pellets, especially for special plastics, often use underwater pelletizing. These systems cool better and use more automation for top results.
- Big factories that need to make lots of pellets may find underwater pelletizing faster and easier. These systems can make more pellets and need less help from workers.
Note: Factories should pick the right pelletizing system for their plastics, quality needs, and goals. Underwater pelletizing gives better control and steady results for tough jobs.
Custom Pelletizing Blades from Maxtor Metal
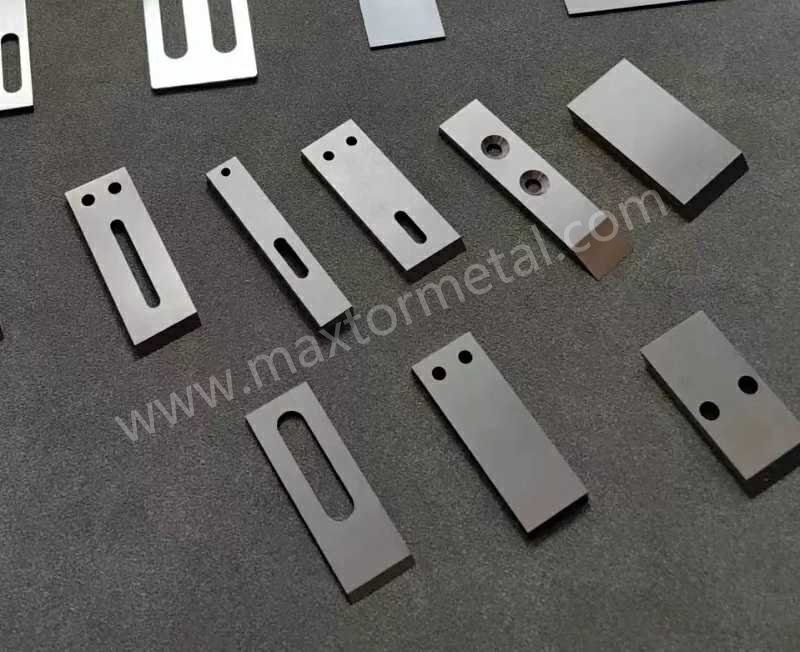
لماذا التخصيص مهم؟
Every plastic factory has its own problems to solve. Regular pelletizing blades do not always work best for every job. Custom blades are made for certain materials and needs. They can help machines work better and save money.
أ شفرة مخصصة fits the machine and material just right. This helps the blade last longer and cut more accurately. It also means less damage and fewer blade changes. For tough jobs, like mixing iron ore fines with binders, regular blades wear out fast. Special blades, like Conforma Clad, last much longer and help mixers work better. The table below shows how custom blades do better than regular ones:
نوع الشفرة | تطبيق | Blade Life Duration | Benefits Observed |
---|---|---|---|
الشفرات القياسية | Blending iron ore fines with binder | 45 days | Broke from wearing down and getting hit |
Conforma Clad Blades | Same application | 4 months | Lasted much longer, helped mixer work better, less downtime, and lower cost per blade |
Custom blades also help factories stop work less often and spend less on each pellet. Workers do not have to change blades as much. This means they can make more pellets and keep quality high. Factories run better and products stay the same.
Tip: Picking the right blade for each job saves money and keeps machines working well.
Maxtor Metal Expertise
Nanjing Metal, called Maxtor Metal, is a trusted plastic pelletizer blade maker. The company has 20 years of experience making cutting tools for factories. Their team uses strong materials like SK2, HSS, M2, and SKD11. These blades are tough and last a long time.
Maxtor Metal’s blades are very hard, from 60 to 72 HRC. This means they do not wear out fast and stay sharp for months. The team checks every blade to make sure it cuts within ±0.05 mm. Customers say these blades last from 6 to 18 months, depending on the job.
Quality is very important to Maxtor Metal. They check the first blade, inspect often, and track every order. This makes sure every blade is good. The table below shows important facts about their blades and quality:
Success Metric / Quality Control Aspect | تفاصيل |
---|---|
Years of Experience | 20 years making pelletizing blades |
المواد المستخدمة | SK2، HSS، M2، SKD11 |
دقة القطع | دقة ±0.05 مم |
صلابة الشفرة | 60-72 HRC |
عمر الشفرة | 6 to 18 months |
تدابير مراقبة الجودة | Skilled team checks, first blade checks, many inspections, order tracking |
تعليقات العملاء | Blades last long and cut well |
Service Offerings | OEM and ODM custom blade designs |
Purchasing Process | Easy to buy and import |
Maxtor Metal helps with both OEM and ODM projects. They make sure customers get blades that fit their machines and needs. Buying is simple, and they help from start to finish. Customers like the long blade life, sharp cutting, and good service.
Note: Factories that want custom pelletizing blades can trust Nanjing Metal’s experience and careful checks.
Picking the best pelletizing system depends on what plastic you use, how good you want the pellets to be, and what your factory needs. Water ring pelletizing knives cool pellets quickly and make nice shapes for many plastics. Underwater systems work better with sticky or heat-sensitive plastics. The table below shows the main points:
System Type | الأفضل لـ | الفوائد الرئيسية | Main Limits |
---|---|---|---|
حلقة الماء | PE, PP, TPE, EVA | Fast cooling, good pellets | Not for sticky materials |
تحت الماء | PA, PET, sticky resins | Uniform pellets, high output | Higher cost, complex setup |
Operators should:
- Pick the right blade material for the plastic.
- Make sure the machine fits before starting.
- Keep water clean and cool for even pellets.
- Use water ring systems for fast cooling and nice pellet shape.
- Pick underwater systems for sticky or special plastics.
For custom help, Nanjing Metal is a top pelletizing maker. Readers can talk to a sales engineer for advice that fits their needs.
التعليمات
What is a water ring pelletizing knife?
A water ring pelletizing knife is a tool that cuts hot plastic into small pellets. Water cools and hardens the pellets right after they are cut. This helps the pellets keep their shape and stay strong.
How often should operators replace water ring pelletizing knives?
Operators need to check the knives often and change them if they get dull or worn out. Most factories look at the blades every three months. How often you replace them depends on what plastic you use and how much you make.
Can water ring pelletizing knives handle all types of plastics?
These knives work with many thermoplastics, both soft and hard. But some sticky or heat-sensitive plastics might need a different pelletizing system to work best.
What causes pellets to stick together during processing?
Pellets can stick if the water gets warmer than 25°C or if the water slows down. Sticky plastics also make sticking worse. Keeping water cool and moving fast helps stop this problem.
How does water ring pelletizing compare to underwater pelletizing?
Water ring pelletizing cools pellets with a water ring. Underwater pelletizing puts the die face and cutting area under water. Underwater systems make pellets more even and work better with sensitive plastics.
What maintenance tasks keep water ring pelletizing systems running smoothly?
Operators should clean filters, check if the water is clean, look at blade sharpness, and watch water temperature. Doing these jobs often helps the machine run well and keeps pellet quality steady.
Is water management difficult with water ring pelletizing systems?
Water management needs careful attention. Operators must keep water clean, control the temperature, and take care of used water. Good water management helps the factory make good pellets all the time.
Who can help with custom pelletizing blade solutions?
Nanjing Metal is a well-known plastic pelletizer blade maker. Their team gives expert advice and makes special blades for different needs.
انظر أيضا
اعثر على سكاكين التحبيب المثالية لاحتياجات معالجة البلاستيك لديك
مقارنة شفرات التحبيب: اعثر على الشفرة المناسبة بسهولة
ما هي شفرات التحبيب وكيف تعمل في الصناعة؟
كيفية اختيار سكين التكوير المناسب لصناعتك