With the rapid development of the global packaging industry, corrugated boards have become an essential packaging material across various sectors. Slotting machines, crucial tools for processing corrugated boards, directly impact production efficiency and product quality.
Statistics show that the global corrugated board market has reached hundreds of billions of dollars and is steadily growing. According to MarketWatch, the global corrugated board market size was approximately $1.455 billion in 2019 and is expected to reach $107.8 billion by 2031, with a compound annual growth rate of 3.9%.
Against this backdrop, the technology and performance of slotting machines have garnered significant attention and scrutiny. The precision of cutting blades, machine efficiency, and safety standards are continually evolving.
This article explores the latest technologies and trends in corrugated board slotting machines to help readers understand industry dynamics and guide professionals in meeting market demands and challenges.
1. Advances in Blade Technology
Blade technology is a crucial innovation in the field of corrugated board slotting machines.
1.1 Ultra-thin Blades
In recent years, the use of ultra-thin blades for cutting corrugated boards has become a hot topic due to advancements in material science and processing technology. These ultra-thin blades, typically made of high-strength, wear-resistant tungsten carbide, have a thickness of only 1.2 millimeters, making them finer than traditional blades.
According to LANLING, ultra-thin blades produce cleaner cuts with fewer burrs, enhancing board quality. The high-precision cuts also offer more possibilities for customized packaging designs.
As technology progresses, blade materials and designs continue to innovate. Besides tungsten carbide, new blades are made from ceramic composites and high-strength steel to improve wear resistance and stability. The structural design of blades is continually optimized to meet different cutting needs, further enhancing precision and efficiency.
1.2 Key Developments in Slotting Blades:
- Improved Wear Resistance: As production speeds and cutting frequencies increase, wear resistance becomes crucial. Recent breakthroughs in blade materials, such as tool steel and hard alloys, have extended blade life and improved wear resistance.
- Enhanced Precision and Stability: Cutting precision and stability are vital for corrugated board quality. Modern blade technology focuses on material selection, design, and manufacturing processes. Optimizing blade geometry, edge angles, and edge structures achieves more precise and stable cuts.
- Multi-Functional Blade Design: As market demands diversify, slotting blade designs are becoming more multifunctional. Some blades can perform various cutting forms for different types of boards and cutting needs, such as V-shaped, U-shaped, and W-shaped blades. This multifunctional design increases equipment flexibility and adaptability.
2. Enhancing Machine Efficiency
Improving machine efficiency is another major trend in the development of corrugated board slotting machines. New models focus on high-efficiency operation while ensuring cutting precision.
2.1 High-Speed Operation and Transmission Systems
New slotting machines boost production efficiency by optimizing transmission systems and increasing operational speed. Advanced models can produce up to 350 pieces per minute due to improved transmission systems and efficient power system designs. According to Carton Machine, these efficient transmission systems use advanced roller conveyors and synchronous belt designs, ensuring stability and preventing misalignment or paper jams during high-speed operations.
2.2 Infrared Heating and Rapid Drying
To further enhance production efficiency, new slotting machines are equipped with infrared heating devices for quick drying during printing. These devices rapidly dry printing ink, ensuring continuous production and reducing wait times. Carton Machine reports that infrared heating can reduce drying times to just a few seconds, significantly boosting overall production efficiency.
2.3 Application of Automation Technology
Automation technology plays a crucial role in improving the efficiency of slotting machines. Modern slotting machines come with various automated features like automatic feeding, automatic adjustment, and automatic fault elimination. These features minimize manual intervention, ensuring a continuous and stable production process. For example, automatic feeding systems adjust feed speed and quantity based on production needs, reducing manual operation time and labor intensity.
2.4 Intelligent Control Systems
The introduction of intelligent control systems makes slotting machine operations more precise and convenient. Electronic control systems allow operators to input data on touch screens, completing machine settings and adjustments with less manual effort. Some advanced slotting machines feature PLC control systems and human-machine interfaces (HMI). Operators can input relevant parameters on the screen, and the machine automatically adjusts to the optimal state, ensuring cutting precision and stability. LANLING data shows that these intelligent control systems can reduce machine adjustment time to just a few minutes, greatly increasing production efficiency.
2.5 Modular Design
Modular design is also a key trend in enhancing slotting machine efficiency. It simplifies maintenance and part replacement, reducing downtime. With standardized modular design, production lines can quickly switch different function modules, such as cutting modules or transmission modules, based on needs. This flexibility and adaptability improve equipment efficiency and responsiveness to various production tasks.
These technological advancements and applications not only increase productivity but also lower production costs. The introduction of automation technology further reduces manual intervention, making the production process smoother and more reliable.
3. Safety and Automation
Modern corrugated board slotting machines have made significant advances in safety and automation. New machines come equipped with safety nets and comply with CE standards, ensuring operator safety (LANLING). Enhanced automation features, such as pneumatic blade sharpening, allow continuous blade maintenance during operation, significantly improving efficiency. These improvements not only boost productivity and product quality but also ensure operator safety.
3.1 Safety Devices and Standards
Modern corrugated board slotting machines are equipped with various safety devices to ensure operator safety during use. Common safety devices include:
- Safety Nets and Guards: Machines are fitted with protective nets and guards to prevent operators from coming into contact with blades or other dangerous parts during operation. These protective devices are usually made of sturdy metal materials, effectively isolating the operating area.
- Photoelectric Sensors: Photoelectric sensors are crucial safety devices that monitor the operating area in real-time. When sensors detect an operator approaching a dangerous area, they automatically stop the machine to prevent accidents. According to LANLING, these sensor systems have a response time of less than 0.1 seconds, greatly enhancing operational safety.
- Emergency Stop Buttons: Every machine is equipped with multiple emergency stop buttons. Operators can immediately stop the machine in any emergency by pressing these buttons, which are usually installed in easily accessible locations to ensure a quick response.
- CE Standard Compliance: Many corrugated board slotting machines comply with EU CE standards, ensuring their design and manufacturing meet the highest safety requirements. CE certification is essential for entering the European market and is widely regarded as a symbol of high safety and quality.
3.2 Enhanced Automation Features
The application of automation technology in slotting machines makes operations simpler and more efficient, reducing manual intervention and boosting productivity. Key automation features include:
- Automatic Feeding Systems: Automatic feeding systems adjust feed speed and quantity based on production needs, reducing manual operation time and labor intensity. These systems typically use advanced sensors and control technology to ensure accuracy and continuity in the feeding process.
- Pneumatic Blade Sharpening Systems: These systems are crucial components of modern slotting machines, continuously sharpening blades during operation to maintain sharpness, improving cutting quality and production efficiency. According to LANLING, pneumatic sharpening systems can more than double blade lifespan.
- Electronic Control Systems: The introduction of electronic control systems makes machine operation and adjustment more precise and convenient. Operators input data on touch screens to set and adjust machines, greatly reducing manual adjustment time and complexity. Many modern slotting machines feature PLC (Programmable Logic Controllers) and HMI (Human-Machine Interface) systems for precise control and real-time monitoring, enhancing reliability and stability in production processes.
- Automatic Fault Detection and Elimination: Automation systems include fault detection and elimination features. When a machine encounters a fault, the system automatically detects and records fault information, notifying operators via an alarm system. Some high-end equipment can even automatically resolve common faults, reducing downtime and maintenance costs.
3.3 Smart Technology and Remote Monitoring
With the development of IoT and Industry 4.0, smart technology and remote monitoring are increasingly applied to slotting machines:
- Data Collection and Analysis: Modern slotting machines are equipped with numerous sensors that collect real-time data on machine operation, production metrics, and environmental parameters. Data analysis can optimize production processes, improving efficiency and product quality. According to MarketWatch, smart data analysis systems can increase production efficiency by over 15%.
- Remote Monitoring and Maintenance: Remote monitoring allows operators and maintenance teams to monitor machine operation in real-time via the internet, enabling remote diagnostics and maintenance. This technology improves response speed and reduces on-site maintenance time and costs. For example, when a machine encounters a fault, the maintenance team can diagnose and provide solutions remotely, ensuring continuous production.
These advancements in safety and automation not only enhance the operational efficiency of corrugated board slotting machines but also provide a safer working environment for operators. The application of automation and smart technology makes production processes more efficient, stable, and controllable, bringing greater economic benefits and market competitiveness to enterprises.
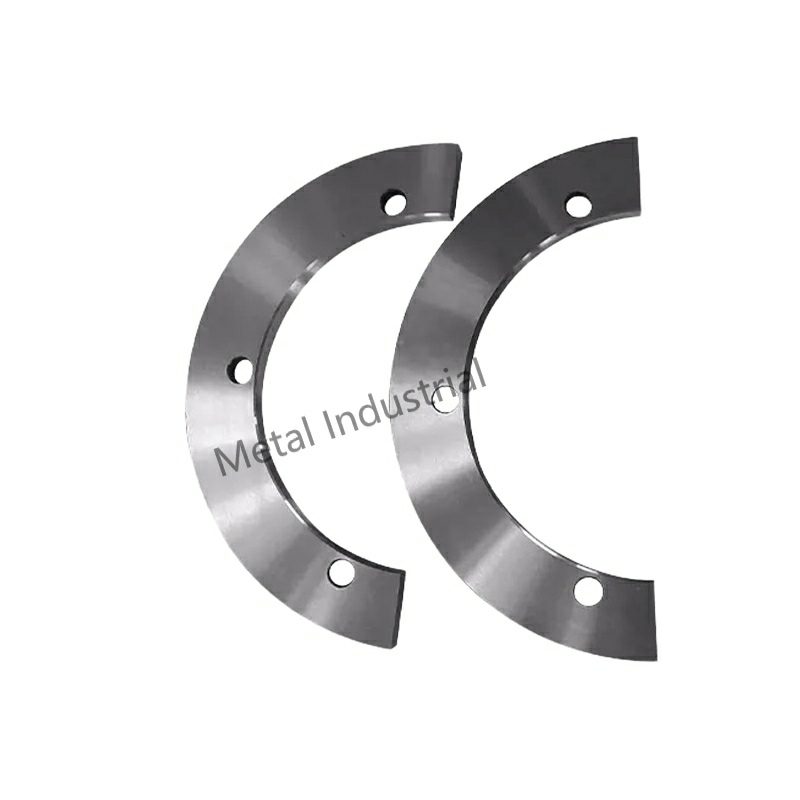
4. Application of Integrated Systems
The use of integrated systems in corrugated board production is becoming more widespread. These systems combine multiple production steps into one machine or production line, enhancing efficiency, reducing manual intervention, and ensuring consistent product quality.
4.1 Multifunctional Integrated Systems
Modern corrugated board slotting machines are no longer limited to just slotting. More and more devices integrate various functions such as printing, die-cutting, and slotting. These multifunctional integrated systems can complete multiple production steps in one go, reducing line switching and adjustment time, thereby significantly improving production efficiency.
For example, advanced equipment can perform printing, slotting, and die-cutting at speeds of up to 220 pieces per minute, thanks to a full vacuum suction transfer system that enhances efficiency and precision. According to Carton Machine, such integrated systems not only speed up production but also ensure consistent product quality.
4.2 Flexographic Printing and Slotting Integration
Flexographic printing is a crucial step in corrugated board production. Integrating flexographic printing with slotting in the same machine can significantly boost efficiency and reduce the time spent handling and stacking boards. Some new flexographic printing slotting machines use fully automatic alignment systems and high-precision servo control technology, achieving seamless integration of printing and slotting, thereby improving product accuracy and quality.
4.3 Full Vacuum Suction Transfer System
The full vacuum suction transfer system is an advanced technology that ensures the stability and accuracy of the board during high-speed operation. This system uses vacuum suction to hold the board firmly on the conveyor belt, preventing slipping or misalignment common in traditional transfer methods. According to Foshan Fuli Packaging Machinery, this system can increase production speed by over 15% while reducing board damage and increasing yield.
4.4 Automation and Intelligent Control Systems
Integrated systems also incorporate automation and intelligent control systems. Using advanced control technologies like PLC (Programmable Logic Controllers) and HMI (Human-Machine Interface), operators can monitor and adjust the entire production line from a unified control platform. These intelligent control systems can automate scheduling, fault detection, data collection, and analysis, enhancing automation and management efficiency.
For instance, some integrated systems use big data analytics and machine learning to predict potential production issues and automatically adjust production parameters, optimizing processes and improving efficiency and product quality. According to MarketWatch, integrated equipment with intelligent control systems can boost production efficiency by over 20%.
4.5 Reducing Labor Costs and Enhancing Safety
The application of integrated systems significantly reduces reliance on manual operations, lowering labor costs. With automated and intelligent equipment, operators only need to perform simple settings and monitoring, with most operations being automated. This not only improves production efficiency but also reduces the likelihood of human errors, ensuring consistent product quality.
Additionally, integrated systems usually come with comprehensive safety features such as photoelectric sensors and safety nets to protect operators. For example, when the machine detects an operator approaching a dangerous area, it automatically stops running to prevent accidents.
4.6 Ease of Maintenance and Management
Integrated systems feature modular and standardized designs, making maintenance and management more convenient. Standardized module designs allow companies to quickly replace different functional modules based on production needs, adapting to various tasks. The modular design also simplifies maintenance, reducing downtime and increasing efficiency.
For example, some integrated systems come with remote monitoring and maintenance features. Maintenance personnel can monitor equipment status in real-time over the Internet and perform remote diagnostics and maintenance. This technology not only improves response speed but also reduces on-site maintenance time and costs.
The application of integrated systems in corrugated board slotting machines enhances production efficiency and product quality, providing greater economic benefits and market competitiveness for companies. As technology continues to develop, integrated systems will play an increasingly important role in corrugated board production.
Conclusion
The advancements in blade technology, improvements in machine efficiency, enhancements in safety and automation, and the application of integrated systems are the latest trends in the development of corrugated board slotting machines. These trends indicate that the corrugated board industry is moving towards greater efficiency, safety, and technological sophistication. By understanding and applying these latest technologies, industry professionals can improve production efficiency, reduce costs, and meet the growing market demand.
5 Responses
Hi, yes this piece of writing is really nie and I have learned lot
of things from it about blogging. thanks.
I hope you find it useful.
Hi, yes this pkece oof writing is really nice and I have learned lot of things from it about blogging.
thanks.
Thank you for your endorsement and I look forward to the opportunity to work together.