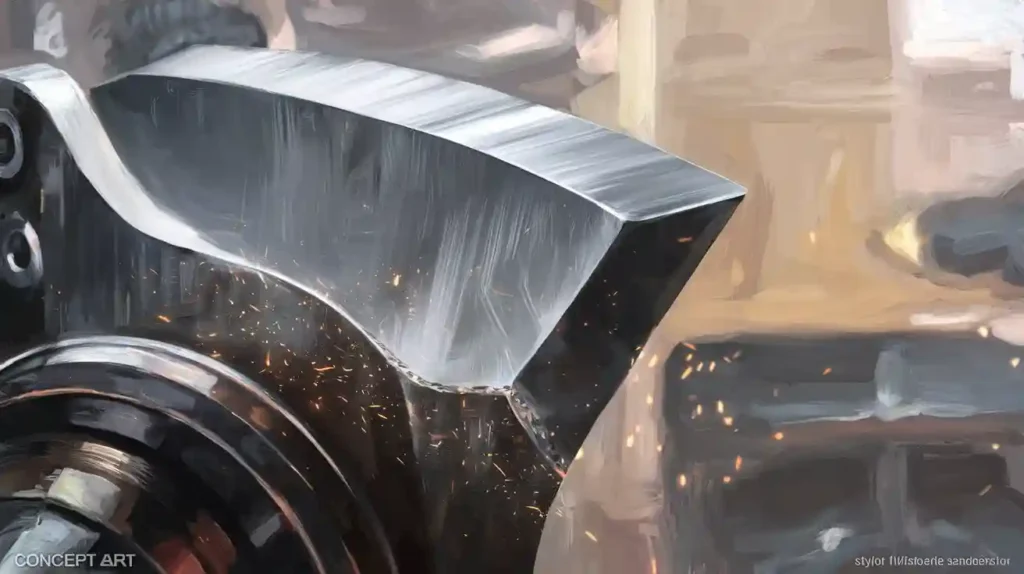
कार्बाइडिंग is very important for modern industrial knives and blades. Many industries require a कस्टम ब्लेड that cuts efficiently and maintains a sharp edge. Steel knives with carbiding can withstand repeated use in tough environments. Factories rely on blades that perform consistently, even under heavy use. Carbiding strengthens steel, preventing it from wearing out quickly, which helps blades last longer and reduces costs on replacements. Makers often choose steel for custom blades because of its strength and hardness. Carbiding ensures industrial knives deliver reliable performance every time they are used.
चाबी छीनना
- Carbiding puts a hard carbide layer on steel blades. This makes blades stronger, sharper, and last longer for hard jobs. Different carbides like tungsten and vanadium make blades harder. They also help blades resist damage and cut better. The carbiding process uses careful mixing, heating, and coating steps. This makes the blade surface tough. It means you do not need to sharpen or replace blades often. Carbided blades save money because they last longer. They also cut more exactly and cost less to take care of than regular steel blades. Many industries use carbided blades for better results. These include paper, textiles, recycling, and automotive. Carbided blades help these industries work better and save money.
Carbiding Basics
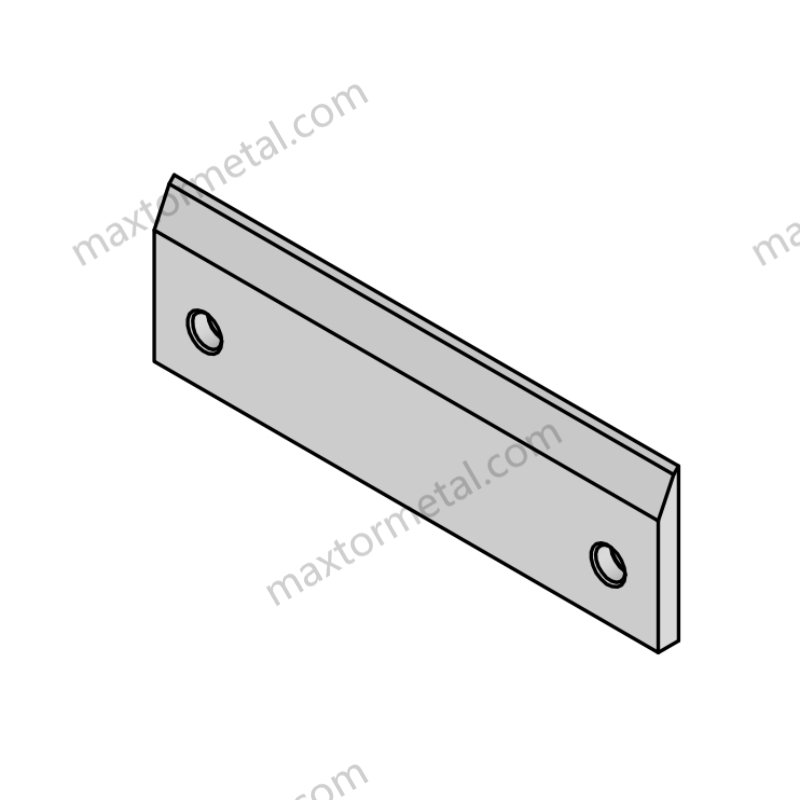
What Is Carbiding
Carbiding means putting a hard carbide layer on blades. This makes regular steel or high carbon steel much stronger. Carbiding helps blades cut better and last longer. The carbide layer is usually made from tungsten carbide or other strong materials. It sticks to the blade using special methods like powder metallurgy or thermal spraying.
Carbide materials have special features that make them great for factories. The table below shows important facts about carbide used in blades:
संपत्ति | विवरण / मूल्य |
---|---|
संघटन | Mix of tungsten carbides in cobalt metal |
कठोरता | 1700–2400 HK (Knoop hardness) |
Density | 15,630 kg/m³ |
Young’s Modulus | 668 GPa |
Tensile Strength | 344 MPa |
Compressive Strength | 2683–2958 MPa |
Melting Point | 2777°C |
Thermal Conductivity | 86 W/mK at 100°C |
प्रतिरोध पहन | Very good at stopping wear |
Chemical Resistance | Resists rust and chemicals well |
विनिर्माण प्रक्रिया | Powder metallurgy: carburizing, mixing, pressing, sintering, finishing |
आवेदन उपयुक्तता | High hardness, wear resistance, strength, heat and rust resistance |
Carbiding helps blades stay sharp and strong for a long time. This is very important for high carbon steel blades. It lets them handle tough jobs and heavy use.
Types of Carbide
Industrial blades use different types of carbide for the best results. Each type has its own strengths for hardness and wear resistance. The most common carbides for blades are:
Carbide Type | Typical Composition/Designation | कठोरता (विकर्स) | Notes on Hardness and Use |
---|---|---|---|
Chromium Carbides | M7C3, M23C6 | मध्यम | Used in stainless and wear-resistant steels |
Vanadium Carbides | VC | बहुत ऊँचा | Very hard, helps blades last longer |
Tungsten Carbides | WC, W2C | बहुत ऊँचा | Very hard, used in fast cutting blades |
Niobium Carbides | NbC | बहुत ऊँचा | Very hard, helps stop wear |
Titanium Carbides | TiC | बहुत ऊँचा | Hard, helps blades resist wear |
Tungsten carbide is the top choice for many uses. It mixes tungsten and carbon, sometimes with cobalt, for extra strength. Solid carbide blades made from this material last a long time and cut well. Makers also use vanadium, niobium, and titanium carbides to make blades even tougher. The type of carbide depends on what the blade needs to do, like cutting hard things or taking strong hits.
Solid carbide blades stay sharp longer than steel blades. They work well in fast and hot places, like metal cutting, woodworking, and mining. High carbon steel blades with carbide coatings also last longer and need less care.
Carbiding vs. Other Treatments
Carbiding is better than many other ways to treat blade surfaces. Heat treatment can make steel harder, but it does not last as long as a carbide coating. Solid carbide and carbide-coated blades work better than plain steel in tough jobs.
Other treatments, like PVD and diamond coatings, help too but have limits. PVD puts a thin, hard layer on the blade to lower friction and keep it sharp. Diamond coatings are the hardest but can break down when hot. PACVD is a cheaper way to protect carbide blades and helps them last longer.
Note: Cemented carbide blades are very tough and resist wear. They stay sharp and strong for a long time. This means you do not have to replace them often. It saves money and works better than regular steel blades for hard jobs.
Mechanical treatments, like wide peening cleaning, can make carbide tools even stronger. These treatments help coatings stick better and make tools last longer than untreated carbide blades.
How Carbiding Works
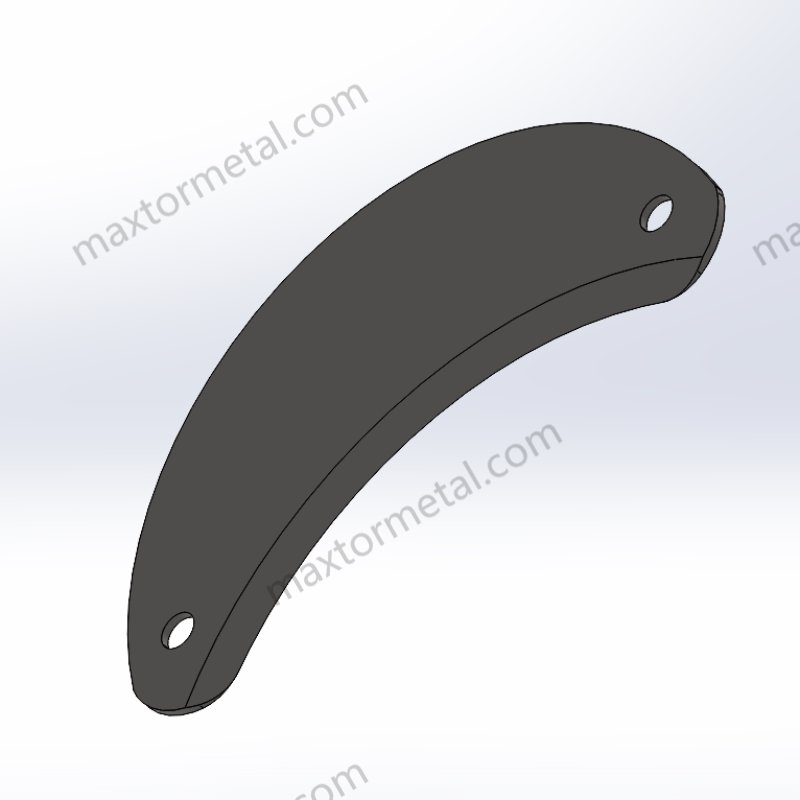
Carbide Application Process
Making industrial blades with carbide takes many careful steps. Each step helps the blade get harder and last longer. Workers use special machines to control each part of the process.
- Raw Material Preparation: Workers pick the best tungsten carbide and cobalt powders. These powders are the main part of the carbide layer.
- Powder Mixing and Compaction: The powders are mixed very well. Machines press the mix into shapes.
- Sintering: The shaped pieces go into hot ovens. The heat makes the powders stick together and become strong.
- Finishing and Grinding: Machines grind and smooth the blade. Diamond tools help make the blade the right shape.
- Treatment of Cutting Edge: Workers use brushes with silicon carbide. This step makes the edge tough and cleans it.
- गुणवत्ता नियंत्रण: Special tools check for problems. Every blade must be hard and the right size.
Safety Tip: Workers wear safety goggles and face shields. They clean and check tools before and after using them. This keeps everyone safe and stops damage.
This process makes blades that are very hard on the outside. The careful work helps blades last longer and need fewer repairs.
औद्योगिक ब्लेड कोटिंग्स
Industrial blade coatings help steel and high carbon steel blades work better. Makers pick coatings based on how hard and tough they need to be. The most used coatings are tungsten carbide, titanium carbide, and chromium carbide. Each one helps blades in different ways.
Coating Material | Hardness (Rockwell C) | Key Properties & Differences | विशिष्ट अनुप्रयोग |
---|---|---|---|
टाइटेनियम नाइट्राइड (TiN) | Up to ~80 RC | Makes blades harder and tougher; FDA approved; does not stick much. | Packaging, food handling |
Titanium Carbonitride (TiCN) | ~80 RC | Stops wear, less friction, resists chips; bonds well. | Industrial, packaging, surgical tools |
हीरा जैसा कार्बन (डीएलसी) | 80 RC+ | Very smooth, tough, and resists rust; black color. | Heavy industry, food processing |
PTFE (Teflon) | Polymer | Does not stick, low friction, keeps water off; FDA approved; can chip. | Food handling, packaging |
Chrome Plating | 66-70 RC | Makes blades harder and stops rust; not as hard as TiN or DLC; costs less. | General industrial blades |
Nickel Plating | 58-62 RC | Medium hard and stops rust; good for food; not as strong. | Food handling, general blades |
Nickel Oxide | एन/ए | Stops rust and lowers friction; good for wet places. | Food handling, seafood processing |
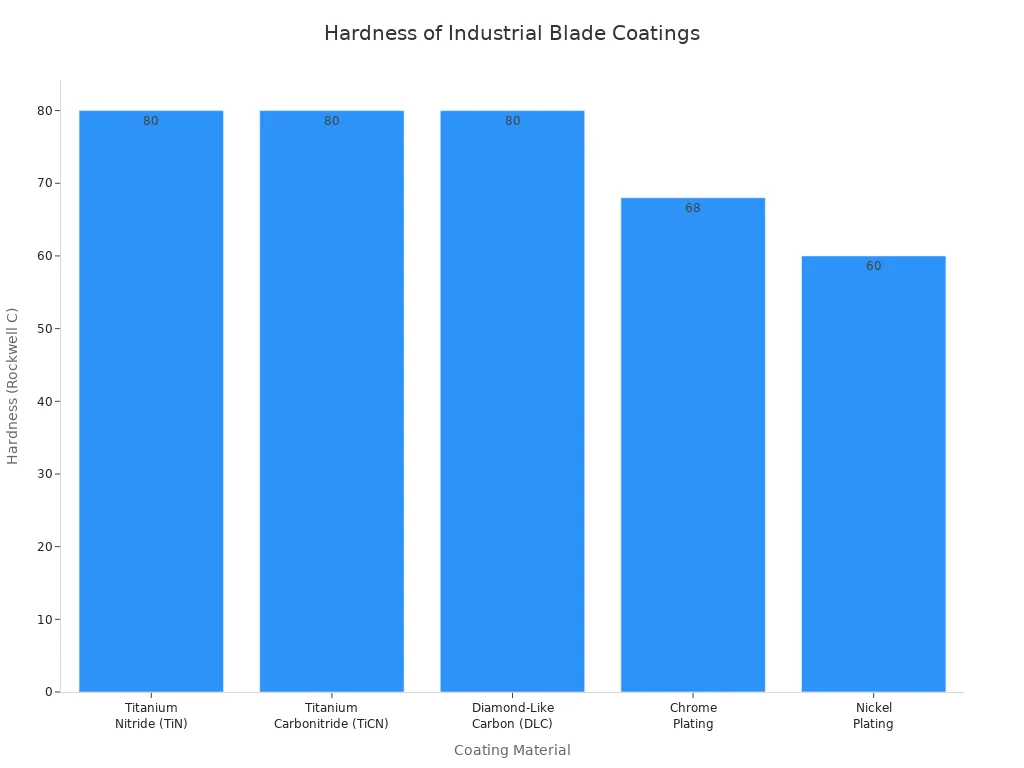
Thermal spraying, plasma spraying, and chemical vapor deposition are ways to put coatings on blades. For example, thermal spraying uses heat to stick carbide to the blade. This makes a strong layer that protects the blade from damage. The right coating keeps blades sharp and strong, even in hard jobs.
Blade coatings help blades last longer and stop rust and wear. Solid carbide blades and carbide-coated steel blades both get better with these coatings. They work well in tough places.
Heat and Cryogenic Treatment
After coating, makers use heat and cryogenic treatments to make blades even better. These steps change the inside of the steel and carbide. This makes blades harder and tougher.
Treatment Type | Temperature Range (°F) | Duration | Notes / Examples |
---|---|---|---|
Initial Cooling | -20 to -80 | Until stable temperature reached | Gets ready for the next cold step |
Cryogenic Stabilization | -220 to -240 | About 1 hour | Time depends on blade size |
Cryogenic Holding | -300 to -320 | 2 to 24 hours | Carbide saw blades stay 4 hours at -300°F |
Warming Phase | -80 to -20 | Until ready for tempering | Slowly warms up before heat step |
Heat Tempering | 300 to 500 | About 1 hour per cycle | 1 to 3 times; saw blades heated at 350-375°F twice |
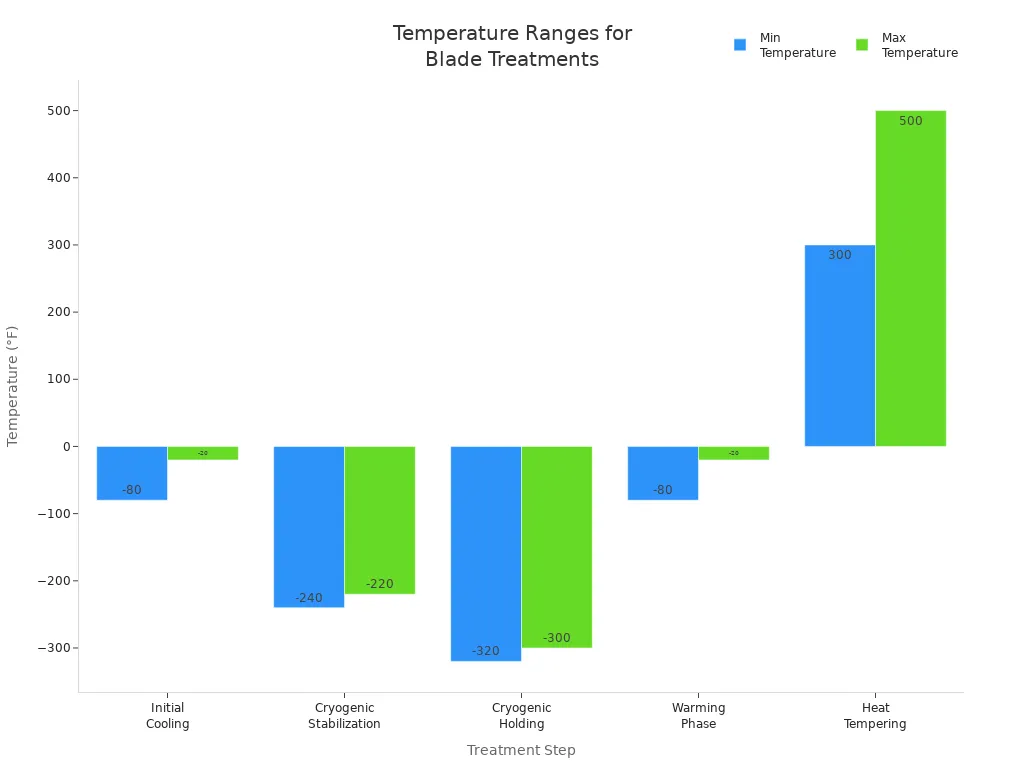
Heat treatment means heating and cooling the blade in a careful way. This helps the carbide layer get stronger and less likely to break. Cryogenic treatment makes the blade very cold, sometimes below -300°F. This step changes the steel inside to make it harder and more stable.
Studies show cryogenic treatment can take a few minutes or hours. Most of the hardness and toughness comes after about five hours. Using both heat and cryogenic treatments makes the blade’s inside better. It also lowers stress and helps tiny carbides form. These changes make the blade stronger and last longer.
For example, in laser melted H13 steel, cryogenic treatment at -196°C and then heating lowers austenite from 19.1% to 5%. This also makes tiny carbides grow inside, making the blade stronger and less likely to break. In another study, heat and cryogenic treatment made blade hardness go from 420 HV to 760 HV by making more carbides and martensite.
Note: Good heat and cryogenic treatment makes blades as hard and tough as possible. This helps blades last longer and saves money on repairs.
Why Carbiding
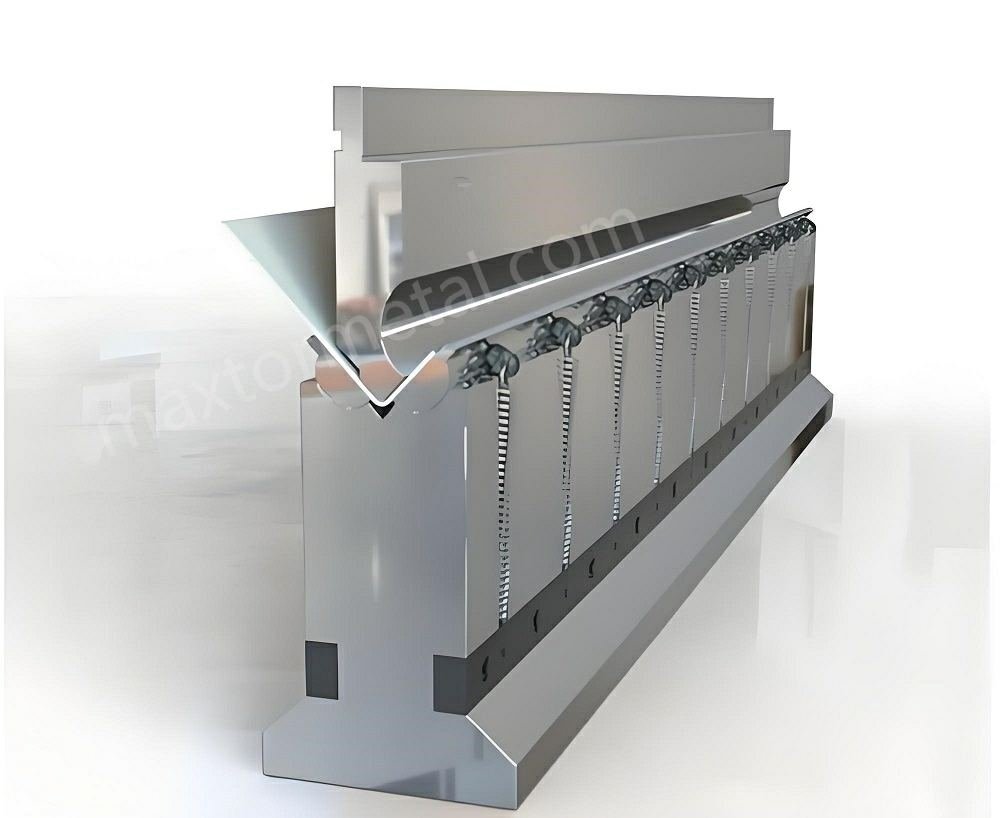
Durability and Wear Resistance
Mechanism of Enhanced Durability
Carbiding makes industrial knives and blades much tougher. It puts a thick carbide layer on the steel. This layer makes the blade harder and stops it from wearing out fast. The hard coating keeps away scratches and rust. It also helps stop tiny cracks and edge chips, even when cutting fast. The carbide layer protects the steel inside from chemicals and strong hits.
- Deep cryogenic treatment (DCT) makes cemented carbide blades last longer. DCT can lower wear by up to 41%, depending on cobalt.
- Vickers hardness tests show DCT blades are harder. This means they resist wear and get a smoother surface.
- Scanning electron microscopy (SEM) shows DCT blades have smoother surfaces. They lose fewer carbide pieces.
- DCT adds more compressive stress to carbide particles. This helps stop cracks and keeps particles in place.
- The process changes the blade inside and makes it denser. This helps stop cobalt loss and scratches.
These changes help knives stay sharp and strong for a long time. They work well even in tough places.
Real-World Performance and Industry Example
Many factories see better blade results after using carbided knives. In plastics and paper, companies get 15–201टीपी4टी more material from each cut. Over 90% of factories say cuts are more exact and there is less waste. In food plants, using carbide-coated blades cuts blade costs by 60%. This saves up to $54,000 each year for 300 blades. These facts show how carbiding helps blades last longer and work better.
Cost and Performance Benefits
Economic Comparison with Traditional Heat Treatment
Carbided blades save more money than heat-treated steel knives. The table below shows important cost and performance facts:
Metric / Benefit | Value / Description |
---|---|
Regrind cycles for high-carbon steel | 3–5 times |
Regrind cycles for premium carbide blades | 5–8 times |
Annual savings reported by 75% of manufacturers using regrinding | $50,000–$150,000 |
Material yield improvement in plastics and paper industries | 15–201टीपी4टी |
Case study: Food processing plant blade expenditure reduction | 60% reduction, saving $54,000 annually on 300 blades |
Cost of regrinding vs. new blade | 50–70% lower |
Tool life extension by regrinding | Up to 200% |
Savings in high blade usage businesses | Up to 60% annually |
CNC grinding tolerance | ±0.01 mm, ensuring factory-grade or better performance |
Switching to carbide-coated blades means tools last longer. Factories need fewer new blades and spend less on repairs. Premium carbide blades can be reground up to eight times. This makes them a good deal for any business.
Tungsten carbide blades are harder and last longer than heat-treated steel. They can be made for shock resistance or long life. This helps many different factories and gives a better return on money spent.
Performance Enhancement
Carbiding helps blades cut better and saves money. The hard surface keeps blades sharp for longer. This means cleaner cuts and less time sharpening. Better rust protection helps blades work well in wet or harsh places. CNC grinding makes sure every blade is the right size and shape.
Advantages Over Alternatives
Carbiding vs. Nitriding—A Technical Comparison
Carbiding and nitriding both make steel blades stronger. But carbiding gives a thicker, harder layer. Nitriding only makes a thin nitride layer. Carbide coatings are harder, stop more wear, and protect better from rust. Carbided knives can handle more force and stay sharp longer. This makes them best for hard jobs.
Unique Benefits of Carbiding
Carbiding has special benefits over other hardening methods:
- Carbide coatings stay hard even when hot. This helps during tough cutting jobs.
- The blade edge does not bend easily.
- Blades stay stiff and keep their shape.
- They can take lots of hits without breaking.
- High fracture toughness means blades do not snap.
- Good thermal conductivity moves heat away from the edge.
- High thermal shock resistance protects from quick temperature changes.
- Chemical stability keeps the blade strong in harsh places.
- Great wear resistance and smoothness stop stuff from sticking.
These features make carbided steel knives the top pick for tough, precise, and reliable work.
Tip: Factories can make carbided blades last even longer. They should use the right drill bit, set the best speed, and add oil. This helps stop wear, chipping, and heat cracks.
Custom Industrial Knives Manufacturer: Nanjing Metal
When picking a custom knife maker, many choose नानजिंग Metal. Nanjing Metal has made blades for 20 years. Their team is skilled at designing and making strong knives. They make custom steel knives with advanced carbide coatings. Nanjing Metal is trusted for hard, strong, and rust-resistant blades. They help clients in paper, plastics, food, and recycling.
Want to know more? Talk to a Nanjing Metal sales engineer यहाँ about your blade needs.
अनुप्रयोग
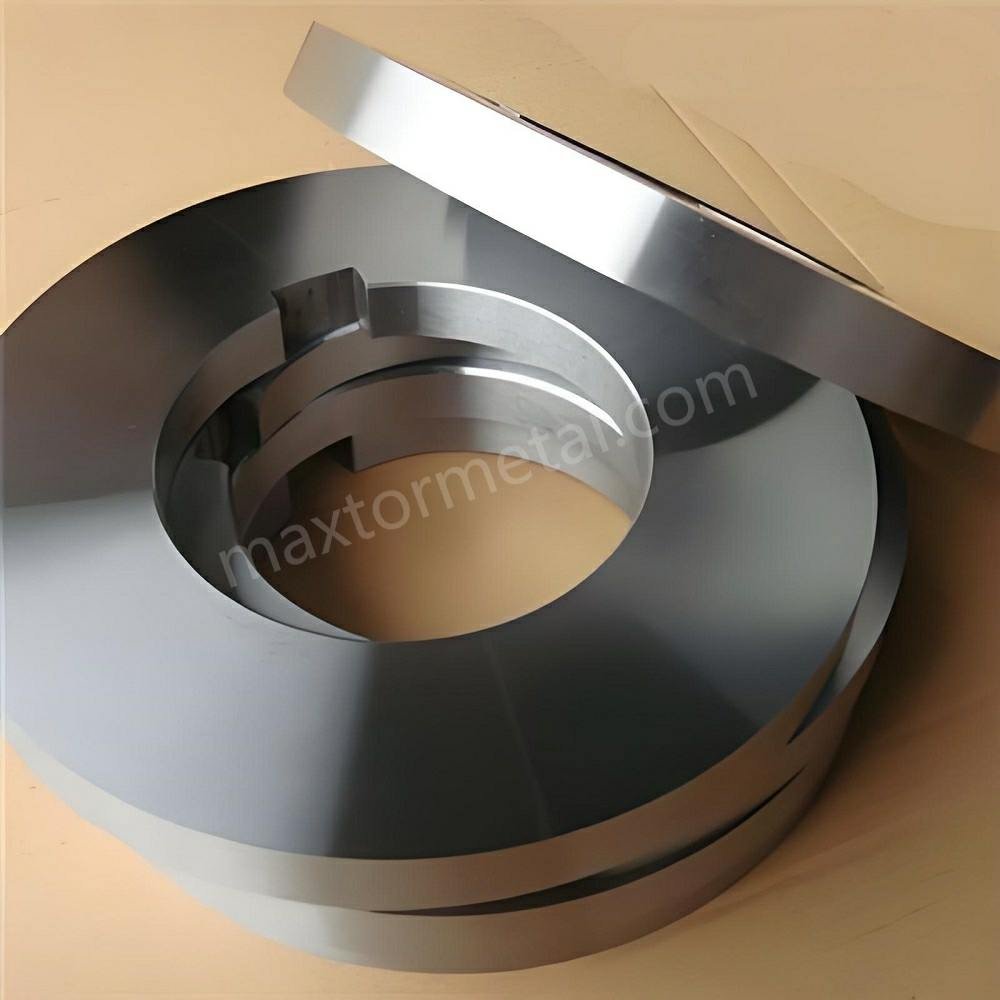
Industrial Knives
Industrial knives are very important in factories today. Carbiding has made these knives much better and more dependable. This helps them work well in tough cutting jobs. The table below shows different kinds of industrial knives. It lists what they are made of, how hard they are, how much heat they can take, and what they are used for:
Industrial Knife Type | Common Blade Material(s) | विशिष्ट कठोरता (HRC) | तापमान प्रतिरोध | Typical Applications / Operational Parameters |
---|---|---|---|---|
Large Circular Blades | Cr12MoV (D2, SKD11) | 58-60 | Up to ~250°C | Used for cutting molds, trimming, pipe molds, circular saw blades, and stamping molds |
Punching Knives | 9CrSi | एन/ए | 180-250°C | Low-speed cutting tools with good hardenability and tempering stability |
Small Round Knives | हाई-स्पीड स्टील (एचएसएस) | >60 | Up to ~500-600°C | High-speed cutting tools for metal and other materials |
Circular Blades for Metal Cutting | Cemented Carbide (TC) | 58-80 (varies) | 1000°C तक | High wear resistance and heat stability for cast iron, non-ferrous metals, glass, stone, stainless steel |
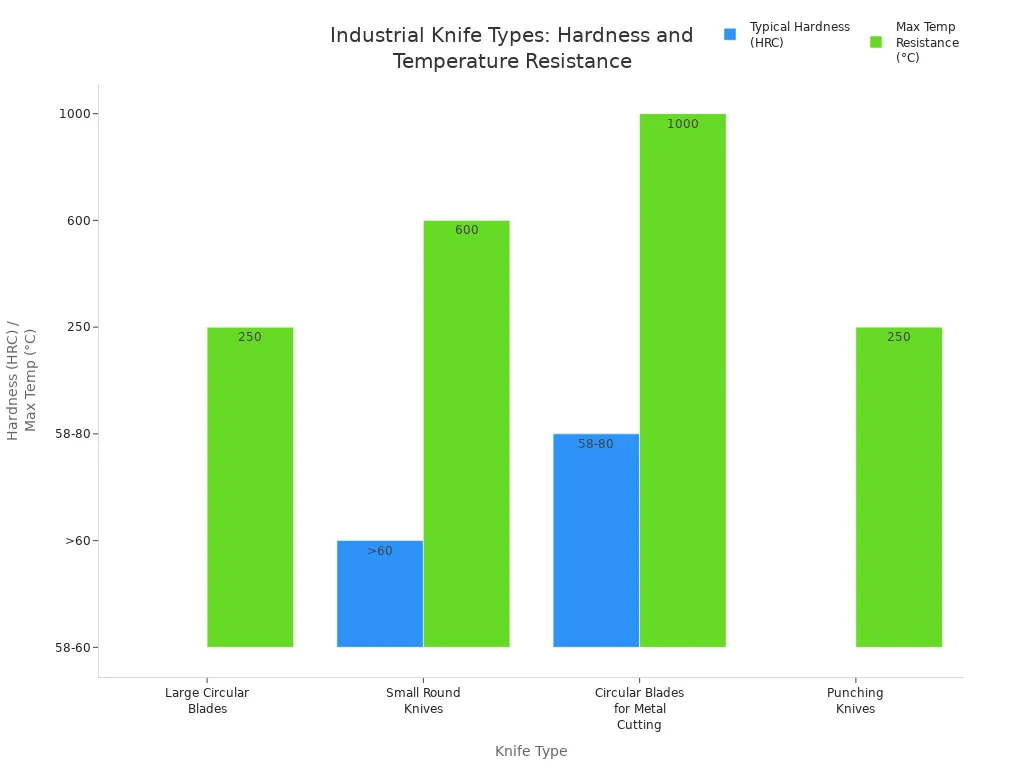
Paper Cutting Knives
Paper cutting knives are needed in the paper and packaging world. Carbiding helps these knives keep their sharp edge longer. This means workers do not have to sharpen them as much. Studies show that fine carbides in martensitic steels help knives cut deeper, up to 40–50% more than regular knives. This makes cuts cleaner and helps work go faster. These knives are usually very hard, about 70–75 HRC, and have a thin edge of 0.2–0.5 mm.
स्लिटिंग ब्लेड
Slitting blades are used in making textiles and composites. Carbide treatment makes them last longer and keeps their shape. This is important for jobs that need lots of cutting. These blades are very hard, about 68–72 HRC, and are made for tough materials. Carbided slitting blades stay sharp and cut well, even with hard or stringy stuff.
ग्रैनुलेटर ब्लेड
Granulator blades are used in recycling and plastics factories. They chop up hard things into small pieces. Carbided edges help these blades last longer and cut better, even when working hard. These blades are tough, about 65–70 HRC, and are made to take hits. Carbiding lets granulator blades cut many kinds of hard things. This means workers do not have to change blades as often, saving money.
Key Industries
Carbided industrial knives are used in many jobs and places. These industries need strong and sharp blades:
- एयरोस्पेस
- ऑटोमोटिव
- चिकित्सा उपकरण
- निर्माण
- लकड़ी
- उत्पादन
- Energy
- इलेक्ट्रानिक्स
- Healthcare
The car industry used over 32% of all carbide tools in 2023. Coated carbide inserts made up more than 58% of the market, mostly in cars and planes. These numbers show that many factories use carbided cutting tools.
कागज उद्योग
The paper industry needs carbided blades for fast cutting and slitting. Carbided knives wear out less and make cleaner cuts. This is important for making paper and packaging. Using carbide-coated blades can help workers make 20% more products. With good blades and care, surprise stops go down by 40%. The table below shows how standard steel and nano-carbide coated blades compare:
ब्लेड का प्रकार | अग्रिम लागत | ब्लेड लाइफ | रखरखाव की जरूरतें |
---|---|---|---|
मानक स्टील | कम | छोटा | Frequent |
Nano-Carbide Coated | उच्च | लंबा | न्यूनतम |
Carbide blades need less force to cut, which makes them safer and easier to use. Sharpening and changing blades on time helps workers do more and waste less.
कपड़ा उद्योग
In textile factories, carbided knives cut both fake and real fibers. These blades stop fibers from fraying and let machines run longer. Carbiding keeps knives sharp, even with rough or soft materials. This means better products and fewer stops.
Composite Processing
Cutting composite materials is hard because they are made of many parts. Sand and other rough things can wear out tools fast. Carbided blades, sometimes with TiN or CrN coatings, can handle these tough jobs. They stay sharp and last longer. Makers design these blades to stop problems like layers coming apart or fibers pulling out. Special coatings and good settings help keep the edge sharp and make the blade last longer. This is why carbided knives are needed for cutting composites.
रीसाइक्लिंग उद्योग
The recycling industry uses टंगस्टन कार्बाइड ब्लेड and alloy steel blades to cut many things. Carbided blades last longer and do not wear out as fast. This means less time changing blades and lower costs. New ideas, like using nanotechnology in cemented carbide blades, make them last up to 70% longer. This saves money and helps recycling work better.
Real-World Examples
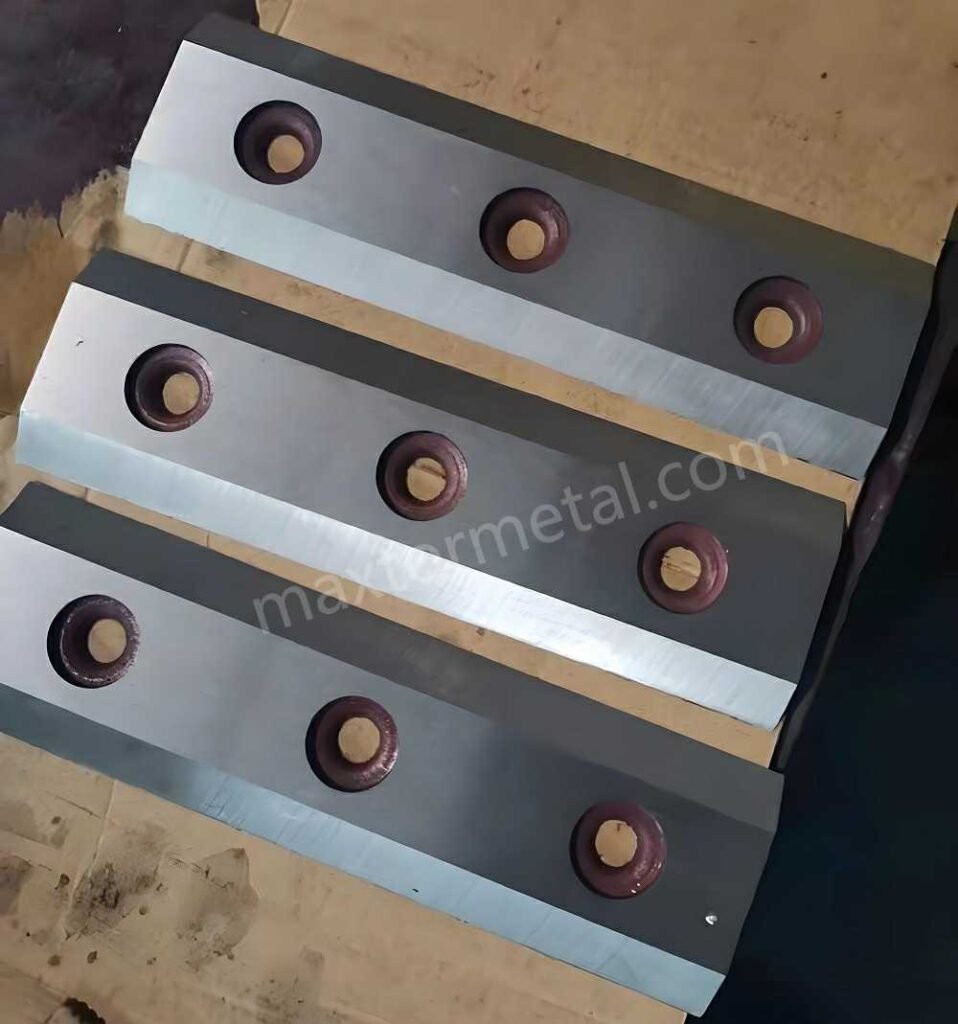
Case Study: Voith Paper
Voith Paper, a big name in paper making, started using carbided cutting knives. After this change, their blades lasted 40% longer and they had 25% less downtime for repairs. This helped them make more paper and spend less money.
Case Study: Andritz Recycling
Andritz Recycling used carbided granulator blades to cut mixed plastics and metals. They changed blades 30% less often and their cuts were more even. This shows how carbided blades help save money and work better in recycling.
Many companies see the same good results. For example, one factory made 30% more products and saved $50,000 a year after switching to carbide blades. A wind turbine maker worked 30% faster and wasted 20% less material. These stories show how carbided knives help factories work better and make better things.
Custom Industrial Knives Manufacturer: Nanjing Metal
If you need special blades, नानजिंग Metal is a trusted maker. They have 20 years of experience making strong, custom steel knives for many jobs. Their skilled team makes sure every blade fits what each customer needs, like in paper, plastics, food, and recycling. People in the industry know Nanjing Metal for making tough, sharp, and accurate machine knives.
Carbiding is very important for today’s factories. Reports say carbide blades are used most, with over 63% of the market. These blades last longer, cut better, and save money. Steel knives with carbide work better than other types in hard jobs. They help factories work faster and stop machines from breaking down as much.
Experts say companies should look at how strong carbide steel knives are. They should also learn about new rules and new tools to do better work. If you want a trusted knife maker, Nanjing Metal has made custom steel knives for 20 years.
Want to use better steel knives in your factory? Talk to a Nanjing Metal sales engineer यहाँ.
सामान्य प्रश्न
What makes carbided blades better than regular steel blades?
Carbided blades have a tough layer on top of the steel. This layer helps the blade stay sharp for a longer time. It also protects the blade from getting worn out. Factories use these blades for hard jobs because they last much longer than regular steel blades.
How does carbiding affect the maintenance of industrial steel blades?
Carbiding means you do not have to sharpen blades as often. The hard surface keeps the edge sharp through more uses. Workers spend less time fixing blades. This helps factories save money and keeps machines working.
Can carbiding be applied to all types of steel blades?
Most steel blades in factories can get a carbide coating. The process works best on high carbon steel and alloy steel. Makers pick the right steel for the job and the coating method.
Why do industries choose custom steel blades from a professional manufacturer?
Industries need blades that fit their machines and materials. A custom steel blade maker like Nanjing Metal has 20 years of experience. Their team makes strong and reliable blades for many jobs. They are known as a trusted manufacturer.
यह भी देखें
छिद्रण ब्लेड और उनके व्यावहारिक अनुप्रयोगों को समझना
How To Select The Ideal Pelletizer Knife For Machines
औद्योगिक ब्लेड प्रदर्शन को बढ़ाना: ब्लेड कोटिंग्स, अनुप्रयोगों और लाभों के लिए एक व्यापक गाइड
वाटर रिंग पेलेटाइजिंग चाकू: फायदे और नुकसान सरल शब्दों में समझाए गए
क्या आपका ग्रेनुलेटर ब्लेड वास्तविक रीसाइक्लिंग कार्य के लिए पर्याप्त टिकाऊ है?