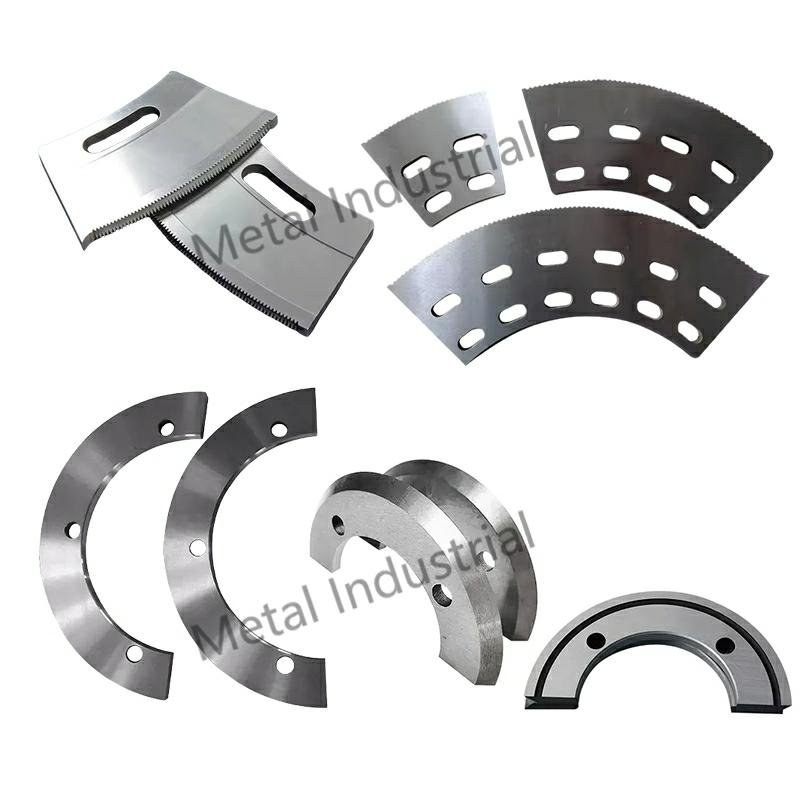
वैश्विक मांग कस्टम यांत्रिक ब्लेड हाल के वर्षों में इसमें उछाल आया है, जो विभिन्न उद्योगों में अनुकूलित समाधानों की आवश्यकता से प्रेरित है। हालिया रिपोर्ट, कस्टम ब्लेड का बाजार 2023 से 2030 तक 7.2% की चक्रवृद्धि वार्षिक वृद्धि दर (CAGR) से बढ़ने की उम्मीद है, जो उच्च परिशुद्धता वाले कटिंग टूल्स पर बढ़ती निर्भरता को दर्शाता है।
कस्टम ब्लेड महत्वपूर्ण उद्योग चुनौतियों का समाधान करते हैं, जैसे कि डाउनटाइम को 30% तक कम करना और कटिंग दक्षता को अनुकूलित करना। वे उन परिचालनों के लिए आवश्यक हैं जहाँ मानक ब्लेड कम पड़ते हैं, विनिर्माण, पुनर्चक्रण, खाद्य प्रसंस्करण और अन्य जैसे उद्योगों के लिए अद्वितीय समाधान प्रदान करते हैं।
यह लेख कस्टम मैकेनिकल ब्लेड के बेजोड़ फायदों की खोज करता है, सही ब्लेड चुनने के लिए एक व्यापक गाइड प्रदान करता है, और उनकी निर्माण प्रक्रिया में गहराई से जाता है। अंत में, आप पाएंगे कि कैसे ये ब्लेड आपके संचालन में क्रांति ला सकते हैं और लागत को काफी कम कर सकते हैं।
आइये सबसे पहले कस्टम मैकेनिकल ब्लेड के लाभों पर नजर डालें।
1. कस्टम मैकेनिकल ब्लेड के लाभ
1.1 परिचालन दक्षता में वृद्धि
कस्टम मैकेनिकल ब्लेड को कटिंग प्रदर्शन को अधिकतम करने, तेज़ उत्पादन चक्र प्राप्त करने और डाउनटाइम को कम करने के लिए इंजीनियर किया जाता है। अध्ययनों से पता चलता है कि कस्टम ब्लेड कटिंग गति को 40%-50% तक बढ़ा सकते हैं, उत्पादन दक्षता में उल्लेखनीय वृद्धि हुई।
कस्टम और मानक ब्लेड के बीच तुलनात्मक विश्लेषण इस लाभ को प्रदर्शित करता है:
ब्लेड का प्रकार | काटने की गति (इकाई/घंटा) | डाउनटाइम (घंटे/माह) | दक्षता लाभ |
मानक ब्लेड | 100 | 15 | आधारभूत |
कस्टम ब्लेड | 140 | 5 | +40% |
यह सुधार प्रति इकाई समग्र लागत को कम करता है और संसाधन उपयोग को अनुकूलित करता है, विशेष रूप से धातु निर्माण और कागज निर्माण जैसे उद्योगों में।
1.2 विशिष्ट आवश्यकताओं के अनुरूप
कस्टम ब्लेड को सामग्री के आसंजन, असमान कट या ब्लेड के तेजी से घिसने जैसी विशिष्ट चुनौतियों का समाधान करने के लिए सटीक रूप से तैयार किया जाता है। उदाहरण के लिए, रीसाइक्लिंग उद्योग में क्लाइंट उच्च घर्षण सामग्री को संभालने के लिए डिज़ाइन किए गए कस्टम दाँतेदार ब्लेड पर स्विच करने पर ब्लेड प्रतिस्थापन में 35% की कमी की रिपोर्ट करते हैं।
वास्तविक दुनिया के अनुप्रयोग:
- खाद्य प्रसंस्करणकस्टम हाइजीनिक ब्लेड खाद्य सुरक्षा के लिए FDA मानकों का अनुपालन करते हुए परिशुद्धता बनाए रखते हैं।
- Metalवर्किंगएंटी-वेयर कोटिंग वाले ब्लेड उच्च तनाव वाले वातावरण में 50% तक अधिक समय तक चलते हैं।
1.3 बेहतरीन कटिंग परिशुद्धता और गुणवत्ता
कस्टम मैकेनिकल ब्लेड सटीक, दोहराए जाने योग्य कट सुनिश्चित करते हैं, जो सीधे उत्पाद की गुणवत्ता में सुधार करते हैं। कपड़ा और पैकेजिंग जैसे उद्योगों में, जहाँ 0.01 मिमी से कम की सहनशीलता महत्वपूर्ण है, सटीक ब्लेड 20%-25% तक अपशिष्ट को कम करते हैं।
इसके अतिरिक्त, उच्च सटीकता वाले ब्लेड उत्पाद के आयाम और सतह की फिनिश को एक समान बनाए रखने में योगदान देते हैं, जिससे ग्राहक संतुष्टि और ब्रांड प्रतिष्ठा बढ़ती है।
1.4 लचीले डिज़ाइन विकल्प
कस्टम ब्लेड बहुमुखी विन्यास प्रदान करते हैं, जिनमें शामिल हैं:
- ज्यामितिसीधा, दाँतेदार, नोकदार या घुमावदार।
- एज शैलियाँएकल-बेवेल्ड, डबल-बेवेल्ड, या खोखली जमीन।
- सामग्रीकठोर इस्पात, टंगस्टन कार्बाइड, और अधिक।
यह अनुकूलनशीलता उद्योगों में व्यवसायों को उनकी प्रक्रियाओं के लिए पूरी तरह से अनुकूल समाधान खोजने में सक्षम बनाती है। उदाहरण के लिए, सीएनसी-ग्राउंड ब्लेड उच्च गति वाले विनिर्माण में बेहतर प्रदर्शन देते हैं, जटिल डिजाइनों को आसानी से समायोजित करते हैं।
1.5 लागत प्रभावशीलता
कस्टम ब्लेड में पहले से ज़्यादा निवेश करना पड़ता है, लेकिन लंबे समय में इससे काफ़ी बचत होती है। इसका कारण यह है:
कारक | कस्टम ब्लेड | मानक ब्लेड | लागत क्षमता |
सहनशीलता | उच्च (2 गुना अधिक समय तक रहता है) | मध्यम | +30% बचत |
प्रतिस्थापन आवृत्ति | 1-2 बार/वर्ष | 4-5 बार/वर्ष | +40% बचत |
रखरखाव लागत | न्यूनतम | उच्च (अक्सर डाउनटाइम) | +20% बचत |
कस्टम ब्लेड का उपयोग करने वाली कम्पनियां कम रखरखाव, लम्बी ब्लेड लाइफ और कम डाउनटाइम के कारण पहले वर्ष के भीतर 200% का औसत ROI रिपोर्ट करती हैं।
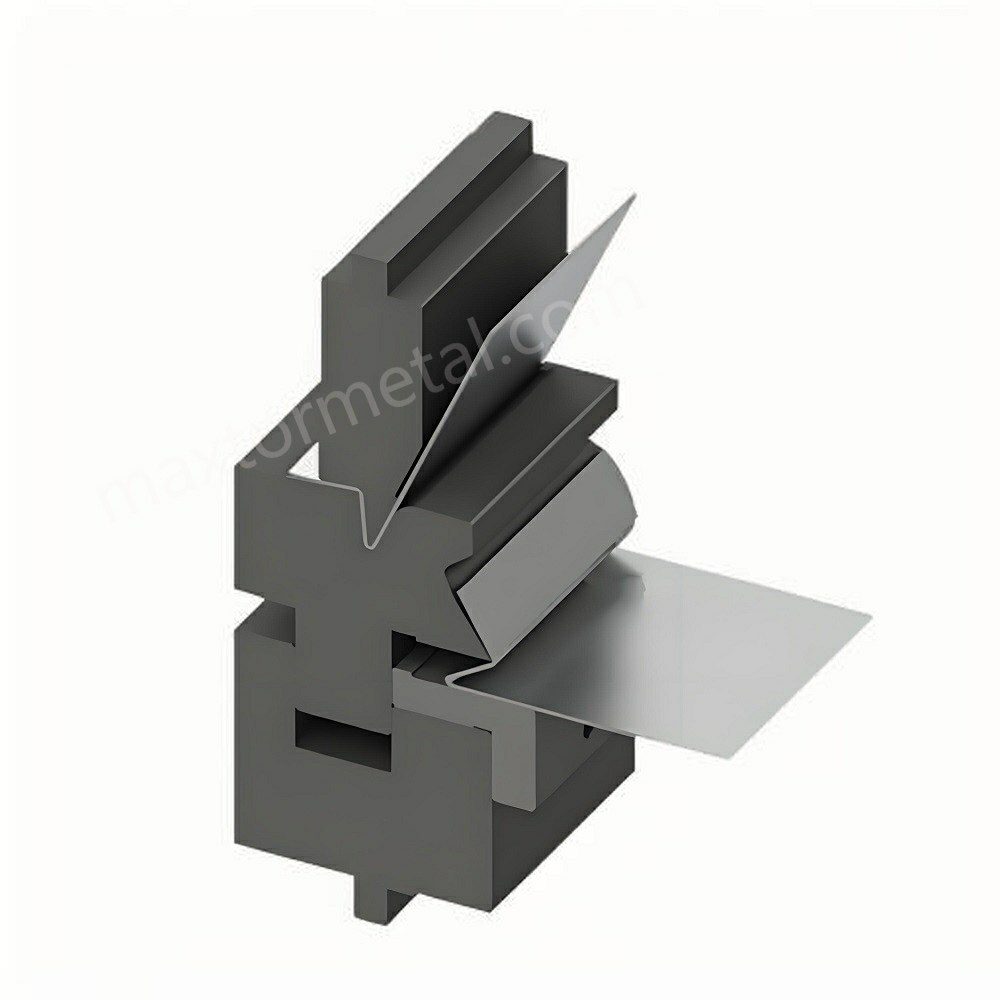
2. सही विकल्प कैसे चुनें कस्टम मैकेनिकल ब्लेड
2.1 सामग्री चयन
सामग्री सीधे ब्लेड की दीर्घायु और काटने के प्रदर्शन को प्रभावित करती है। मुख्य बातों में कठोरता, संक्षारण प्रतिरोध और धार प्रतिधारण शामिल हैं।
सामग्री | कठोरता (एचआरसी) | जंग प्रतिरोध | अनुशंसित अनुप्रयोग |
उच्च कार्बन इस्पात | 55-62 | कम | Metalवर्किंग, वुडवर्किंग |
स्टेनलेस स्टील | 48-56 | उच्च | खाद्य प्रसंस्करण, रासायनिक उद्योग |
टंगस्टन कार्बाइड | 70-80 | मध्यम | घर्षण सामग्री, उच्च परिशुद्धता कार्य |
2.2 ब्लेड डिज़ाइन पैरामीटर
ब्लेड का प्रदर्शन निम्नलिखित मापदंडों से प्रभावित होता है:
- किनारा कोणपरिशुद्धता कार्यों के लिए तीक्ष्ण कोण (~15°); भारी-भरकम अनुप्रयोगों में स्थायित्व के लिए बड़े कोण (~30°)।
- मोटाईबारीक कट के लिए पतले ब्लेड; उच्च प्रभाव वाले कार्यों के लिए मोटे ब्लेड।
3.3 उद्योग अनुप्रयोग और आवश्यकताएं
- Metalवर्किंग: घिसाव प्रतिरोधी कोटिंग के साथ उच्च शक्ति वाले ब्लेड की आवश्यकता होती है।
- पुनर्चक्रणमिश्रित सामग्रियों को संभालने के लिए दाँतेदार या नोकदार ब्लेड।
- खाद्य प्रसंस्करणसुरक्षा और गुणवत्ता सुनिश्चित करने के लिए जंग प्रतिरोधी, स्वच्छ ब्लेड।
2.4 आपूर्तिकर्ता प्रतिष्ठा और अनुभव
अनुभवी आपूर्तिकर्ता के साथ साझेदारी करने से आपको उच्च गुणवत्ता वाले ब्लेड और विश्वसनीय सेवा प्राप्त होती है। सिद्ध विशेषज्ञता और सकारात्मक ग्राहक समीक्षा वाली कंपनियों की तलाश करें।
2.5 मूल्य निर्धारण और डिलीवरी समय
जबकि मूल्य निर्धारण महत्वपूर्ण है, गुणवत्ता से समझौता किए बिना समय सीमा के भीतर डिलीवरी करने की आपूर्तिकर्ता की क्षमता पर विचार करना महत्वपूर्ण है। औसतन, 70% क्लाइंट आपूर्तिकर्ता चुनते समय लागत से ज़्यादा गुणवत्ता को प्राथमिकता देते हैं।
3. नानजिंग Metal इंडस्ट्रियल के बारे में
3.1 विशेषज्ञता और तकनीकी शक्ति
साथ 19 वर्ष का अनुभव मैकेनिकल ब्लेड डिजाइन और विनिर्माण में, नानजिंग Metal औद्योगिक क्षेत्र में अग्रणी है। हमारी इंजीनियरिंग टीम में शामिल हैं 9 कुशल डिजाइनर सीएडी और सॉलिडवर्क्स जैसे उन्नत उपकरणों में निपुणता, सटीक और नवीन डिजाइन सुनिश्चित करना।
3.2 हमारी कस्टम ब्लेड सेवाओं की अनूठी विशेषताएं
3.2.1 अत्यधिक व्यक्तिगत डिज़ाइन
हम ग्राहकों की सटीक आवश्यकताओं के अनुरूप ब्लेड उपलब्ध कराने के लिए उनके साथ मिलकर काम करते हैं।
3.2.2 उन्नत विनिर्माण प्रक्रियाएँ
हमारी उत्पादन सुविधाएं सटीकता और गुणवत्ता की गारंटी के लिए लेजर कटिंग, सीएनसी मशीनिंग और सीएनसी ग्राइंडिंग का उपयोग करती हैं।
3.2.3 कठोर गुणवत्ता नियंत्रण
प्रत्येक ब्लेड कठोर निरीक्षणों से गुजरता है, जिसमें कच्चे माल का परीक्षण, प्रक्रिया के दौरान जांच और अंतिम उत्पाद का परीक्षण शामिल है, जिससे अद्वितीय विश्वसनीयता सुनिश्चित होती है।
क्या आप जानना चाहते हैं कि कस्टम ब्लेड कैसे बनाए जाते हैं? आइये विनिर्माण प्रक्रिया के बारे में जानें।
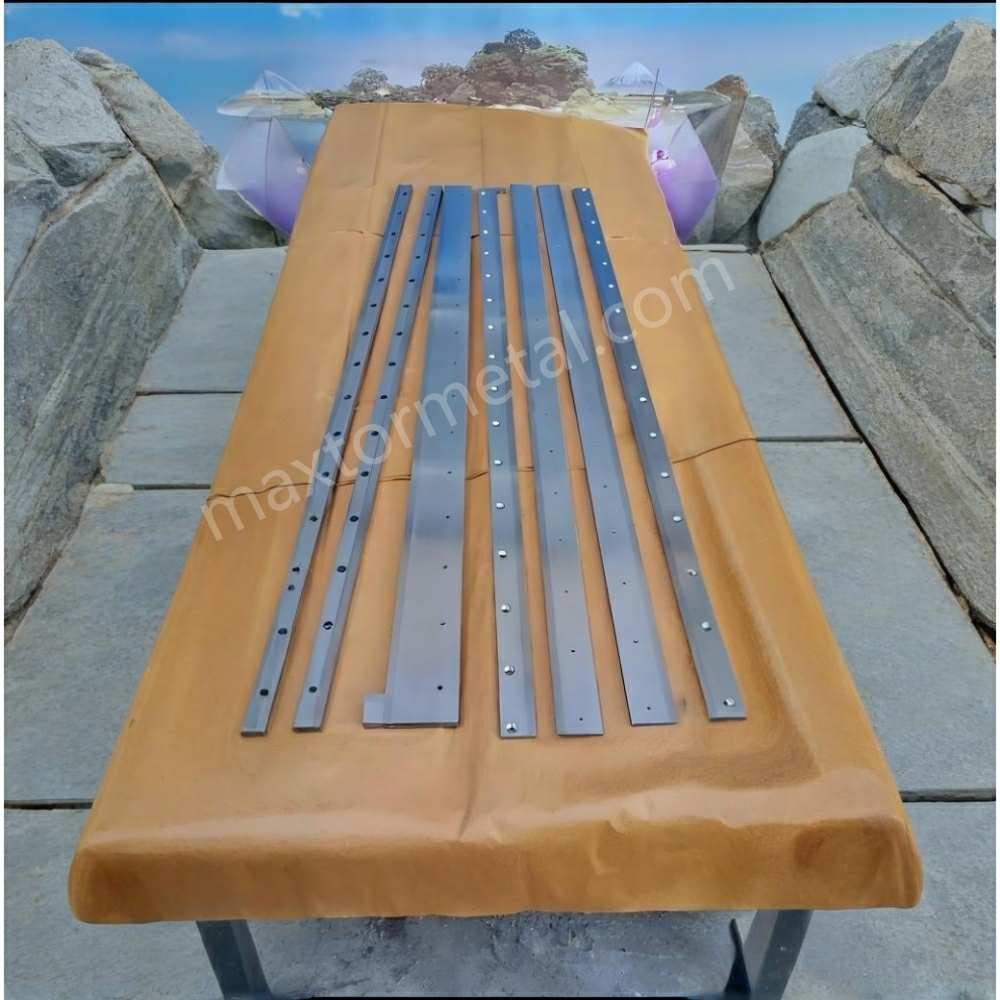
4. कस्टम मैकेनिकल ब्लेड के लिए विनिर्माण प्रक्रिया
4.1 डिज़ाइन चरण
उच्च गुणवत्ता वाले कस्टम मैकेनिकल ब्लेड की नींव उसके डिज़ाइन में निहित है। नानजिंग Metal इंडस्ट्रियल में, हमारे इंजीनियर डिज़ाइन बनाने और अनुकूलित करने के लिए ऑटोकैड, सॉलिडवर्क्स और ANSYS जैसे अत्याधुनिक सॉफ़्टवेयर का लाभ उठाते हैं। इस प्रक्रिया में शामिल हैं:
- परिमित तत्व विश्लेषण (FEA): यह सुनिश्चित करने के लिए कि ब्लेड चरम स्थितियों का सामना कर सकता है, तनाव और तापीय वितरण का अनुकरण करने के लिए उपयोग किया जाता है।
- परिशुद्ध प्रोटोटाइपिंगअंतिम उत्पाद को देखने और विनिर्माण से पहले संभावित समस्याओं का समाधान करने के लिए 3D मॉडल तैयार किए जाते हैं।
मुख्य डेटा:
- प्राप्त सहनशीलता: ब्लेड आयाम के लिए ±0.005 मिमी.
- डिजाइन संशोधन: ग्राहक आमतौर पर उत्पादन में जाने से पहले 2-3 डिजाइन पुनरावृत्तियों की समीक्षा और अनुमोदन करते हैं।
केस स्टडीएक खाद्य प्रसंस्करण ग्राहक ने FEA के माध्यम से अनुकूलित ब्लेड डिजाइन में परिवर्तन के बाद उत्पाद अपशिष्ट को 25% तक कम कर दिया, जिससे विभिन्न भारों के तहत एक समान स्लाइसिंग प्रदर्शन सुनिश्चित हुआ।
4.2 सामग्री का चयन और तैयारी
ब्लेड के प्रदर्शन और दीर्घायु के लिए सामग्री का चयन महत्वपूर्ण है। प्रत्येक सामग्री का चयन निम्न के आधार पर किया जाता है:
- कठोरता: एचआरसी में मापा जाता है (रॉकवेल कठोरता पैमाना).
- एज रिटेंशन: यह निर्धारित करता है कि ब्लेड कितनी देर तक तेज रहेगा।
- जंग प्रतिरोधखाद्य प्रसंस्करण और रासायनिक विनिर्माण जैसे उद्योगों के लिए महत्वपूर्ण।
सामग्री | कठोरता (एचआरसी) | एज रिटेंशन | जंग प्रतिरोध | विशिष्ट अनुप्रयोग |
उच्च कार्बन इस्पात | 55-62 | मध्यम | कम | Metalकार्य, सामान्य विनिर्माण |
स्टेनलेस स्टील | 48-56 | उच्च | उच्च | खाद्य प्रसंस्करण, स्वच्छता-महत्वपूर्ण कार्य |
टंगस्टन कार्बाइड | 70-80 | बहुत ऊँचा | मध्यम | पुनर्चक्रण, घर्षण सामग्री काटना |
सिरेमिक ब्लेड | 90+ | असाधारण | बहुत ऊँचा | परिशुद्धता कार्य, प्रयोगशाला वातावरण |
उत्पादन से पहले कच्चे माल का परीक्षण किया जाता है:
- रासायनिक संरचनास्पेक्ट्रोस्कोपी के माध्यम से सत्यापित.
- सूक्ष्म संरचनात्मक अखंडता: धातु विज्ञान का उपयोग करके जांच की गई।
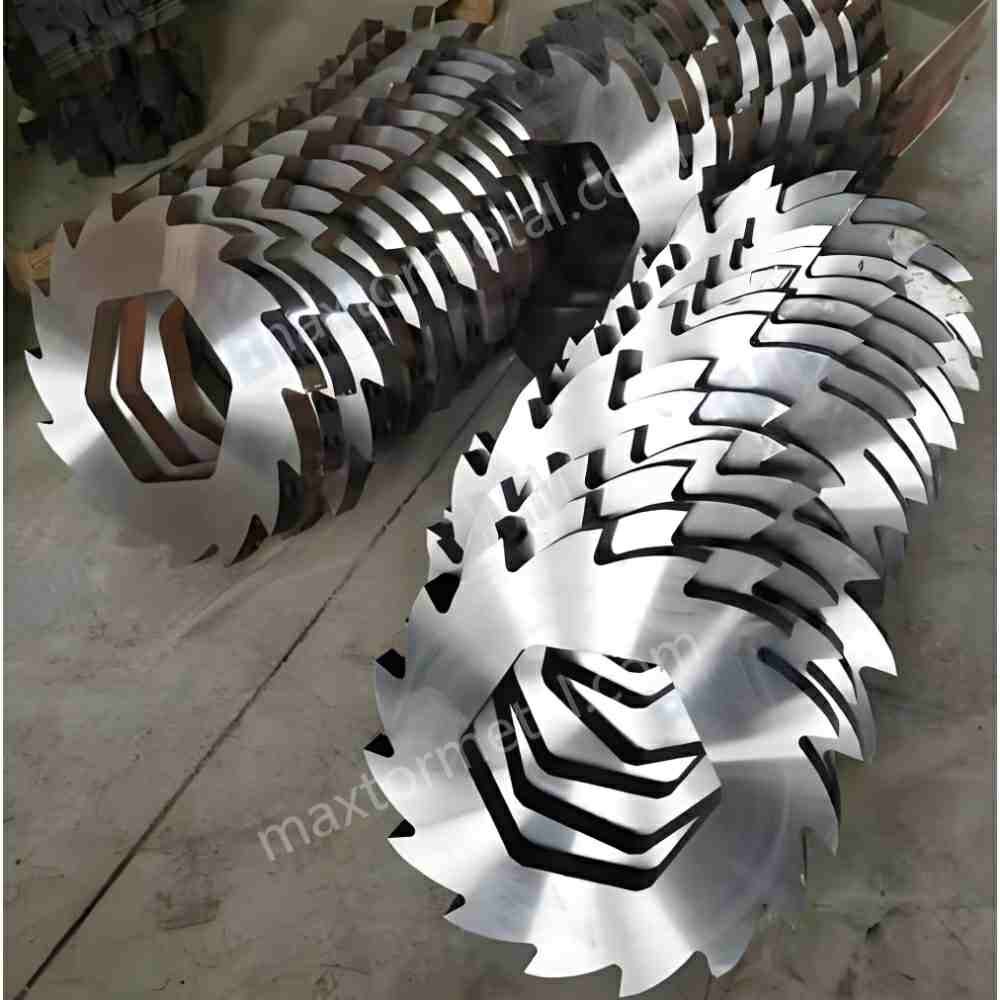
4.3 उन्नत प्रसंस्करण तकनीक
हमारी अत्याधुनिक सुविधाएं उन्नत विनिर्माण प्रक्रियाओं के संयोजन का उपयोग करती हैं, जिनमें शामिल हैं:
- लेजर कटिंग:
- शुद्धता: के भीतर कटौती हासिल करता है ±0.01 मिमी शुद्धता।
- बहुमुखी प्रतिभा: जटिल ज्यामिति और पतली सामग्रियों को संभालता है।
- क्षमता: तक की प्रक्रियाएँ 10 गुना तेज पारंपरिक तरीकों की तुलना में.
- सीएनसी मशीनिंग:
- अनुकूलन क्षमता: निरंतर सटीकता के साथ जटिल ब्लेड प्रोफाइल का उत्पादन करता है।
- सहनशीलता: एकसमान कटौती के माध्यम से ब्लेड की संरचनात्मक अखंडता को बढ़ाता है।
- सीएनसी पीस:
- तीखेपन: सतह खत्म के साथ रेजर-तेज किनारों को प्राप्त करता है रा < 0.1 µm.
- वर्दी: यह सुनिश्चित करता है कि सभी बैचों में किनारे के कोण एक समान रहें।
- सतही उपचार:
- कोटिंग्सटाइटेनियम नाइट्राइड (TiN) जैसे विकल्प पहनने के प्रतिरोध को बढ़ाते हैं 300%.
- उष्मा उपचार: ब्लेड की मजबूती और धार बनाए रखने की क्षमता में सुधार करता है।
प्रदर्शन मीट्रिक्स (उन्नत प्रसंस्करण से पहले और बाद में):
मीट्रिक | मानक ब्लेड | कस्टम ब्लेड (Metal) | सुधार (%) |
काटने की गति | 100 यूनिट/घंटा | 140 यूनिट/घंटा | +40% |
ब्लेड का जीवनकाल | 1,000 चक्र | 2,000 चक्र | +100% |
रखरखाव डाउनटाइम | 10 घंटे/माह | 5 घंटे/माह | -50% |
4.4 गुणवत्ता आश्वासन और परीक्षण
प्रत्येक ब्लेड कठोर 5-चरणीय गुणवत्ता आश्वासन प्रक्रिया से गुजरता है:
- कच्चे माल का परीक्षण: उद्योग मानकों (जैसे, आईएसओ 9001) के अनुपालन को सुनिश्चित करता है।
- आयामी निरीक्षण: समन्वय मापक मशीनों (सीएमएम) का उपयोग करके ब्लेड के आयामों को सत्यापित करता है।
- प्रदर्शन परीक्षण: दक्षता और किनारे के स्थायित्व को मापने के लिए काटने की स्थितियों का अनुकरण करता है।
- सतह अखंडता विश्लेषणअल्ट्रासोनिक परीक्षण के माध्यम से सूक्ष्म दरारें या अनियमितताओं का पता लगाता है।
- अंतिम सत्यापनग्राहक अनुमोदन के लिए वास्तविक दुनिया अनुप्रयोग परीक्षण आयोजित करता है।
परीक्षण मेट्रिक्स:
- कठोरता: विकर्स या रॉकवेल परीक्षण मशीनों के माध्यम से सत्यापित।
- एज शार्पनेस: लेजर एज प्रोफाइलर्स के साथ मापा जाता है, जिससे एज एंगल कम से कम हो जाता है 0.5°.
- घिसाव प्रतिरोध: घर्षण परीक्षणों के माध्यम से अनुकरण, 1,000+ चक्रों की नकल।
4.5 वितरण और ग्राहक सत्यापन
पूर्ण पैमाने पर उत्पादन से पहले, प्रोटोटाइप को क्लाइंट परीक्षण के लिए भेजा जाता है। फीडबैक यह सुनिश्चित करता है कि अंतिम बैच प्रदर्शन अपेक्षाओं से बेहतर हो।
डिलीवरी मेट्रिक्स:
- औसत लीड समय: 2-4 सप्ताह, जटिलता पर निर्भर करता है।
- समय पर डिलीवरी दर: 2023 के लिए हमारे आंतरिक मेट्रिक्स के अनुसार 98.7%।
ग्राहक सफलताएक पैकेजिंग कंपनी ने हमारे ब्लेडों को उनकी स्वचालित मशीनरी के साथ उपयोग के लिए मान्य करने के बाद उत्पादकता में 30% की वृद्धि की सूचना दी।
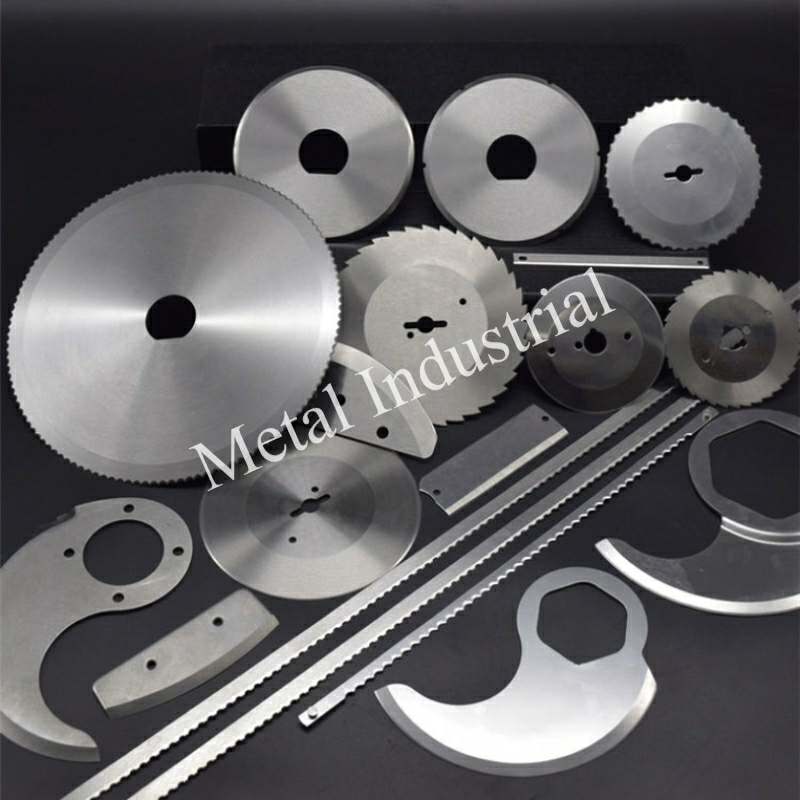
5. अक्सर पूछे जाने वाले प्रश्न (एफएक्यू)
5.1 कस्टम ब्लेड के लिए न्यूनतम ऑर्डर मात्रा क्या है?
न्यूनतम आदेश मात्रा है 10 टुकड़े, लेकिन हम प्रोटोटाइप के लिए लचीलापन प्रदान करते हैं, जिसमें एक विशिष्ट प्रोटोटाइप बैच शामिल होता है 2-3 इकाइयाँ.
5.2 डिलीवरी में कितना समय लगता है?
मानक उत्पादन में लगता है 2-4 सप्ताह, तत्काल परियोजनाओं के लिए त्वरित विकल्प उपलब्ध हैं।
5.3 क्या आप अनुकूलन प्रक्रिया के दौरान एकाधिक डिज़ाइन विकल्प प्रदान करते हैं?
हां, ग्राहकों को प्राप्त होता है 2-3 डिज़ाइन पुनरावृत्तियाँ अनुमोदन के लिए। प्रत्येक पुनरावृत्ति में इष्टतम प्रदर्शन सुनिश्चित करने के लिए क्लाइंट फीडबैक परिणाम शामिल किए जाते हैं।
5.4 क्या आप ब्लेड के रखरखाव के लिए मार्गदर्शन प्रदान करते हैं?
बिल्कुल। हम प्रदान करते हैं:
- व्यापक मैनुअल: सफाई, धार लगाना और भंडारण को कवर करना।
- प्रशिक्षण सत्र: ब्लेड के जीवनकाल को अधिकतम करने के लिए इन-हाउस रखरखाव टीमों के लिए।
5.5 आपकी बिक्री के बाद सेवा नीति क्या है?
हम प्रस्ताव रखते हैं:
- एक साल की वारंटी: विनिर्माण दोषों को कवर करता है।
- आजीवन समर्थन: इसमें परामर्श और समस्या निवारण सेवाएं शामिल हैं।
कस्टम मैकेनिकल ब्लेड का मूल्य
कस्टम मैकेनिकल ब्लेड अद्वितीय परिशुद्धता, दक्षता और लागत बचत प्रदान करते हैं, जिससे वे अपने परिचालन को बढ़ाने के उद्देश्य वाले व्यवसायों के लिए अपरिहार्य बन जाते हैं।
एक विश्वसनीय भागीदार के रूप में, नानजिंग Metal इंडस्ट्रीएल दशकों की विशेषज्ञता और अत्याधुनिक प्रौद्योगिकी द्वारा समर्थित वन-स्टॉप कस्टम ब्लेड समाधान प्रदान करता है।
क्या आप अपने परिचालन में परिवर्तन के लिए तैयार हैं? आज ही हमसे संपर्क करें निःशुल्क परामर्श के लिए या अपनी आवश्यकताओं के लिए सही कस्टम मैकेनिकल ब्लेड का चयन करने के लिए हमारी व्यापक मार्गदर्शिका डाउनलोड करें
4 प्रतिक्रियाएं
ऐसा लगता है जैसे आपने मेरे मन की बात पढ़ ली है! ऐसा लगता है कि आप इस बारे में बहुत कुछ जानते हैं, जैसे आपने इस पर किताब लिखी हो या कुछ और। मुझे लगता है कि आप संदेश को थोड़ा और स्पष्ट करने के लिए कुछ तस्वीरें लगा सकते हैं, लेकिन इसके बजाय, यह एक शानदार ब्लॉग है। एक शानदार किताब। मैं निश्चित रूप से वापस आऊँगा।
कस्टम मैकेनिकल ब्लेडों ने हमारी उत्पादन क्षमता और काटने की परिशुद्धता में उल्लेखनीय सुधार किया, जबकि रखरखाव लागत में भी कमी आई।
यह बहुत दिलचस्प है, आप एक बहुत ही कुशल ब्लॉगर हैं। मैं आपकी फ़ीड में शामिल हो गया हूँ और आपके और भी बेहतरीन पोस्ट की तलाश में बैठा हूँ। साथ ही, मैंने आपकी वेबसाइट को अपने सोशल नेटवर्क में शेयर किया है!
धन्यवाद! अगर आपको कस्टमाइज्ड इंडस्ट्रियल ब्लेड की भी जरूरत है तो बेझिझक मुझसे संपर्क करें।