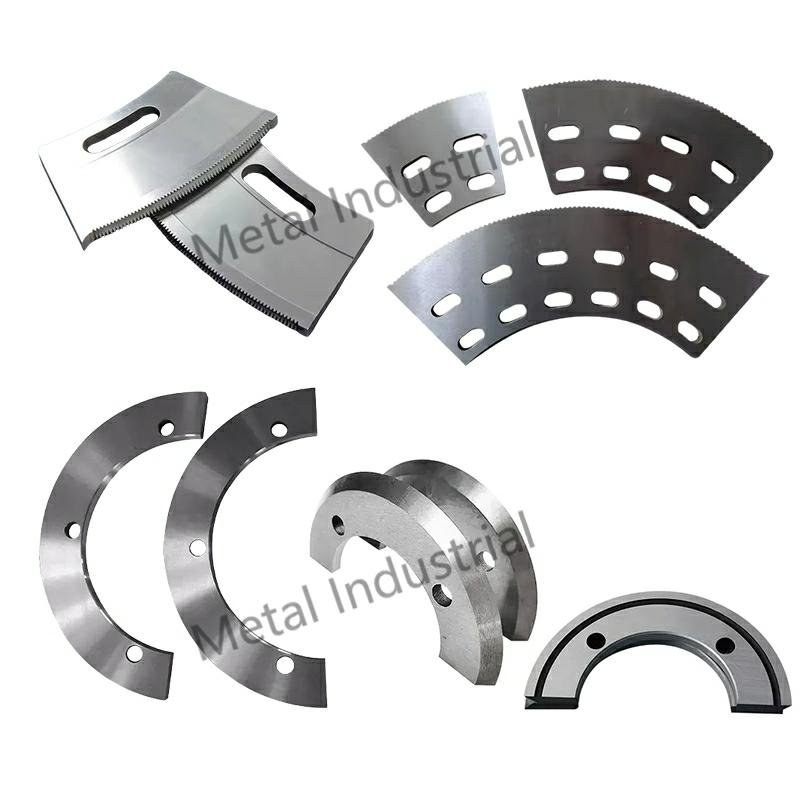
In today’s fast-paced industrial landscape, packaging operations are crucial to ensuring high product quality and customer satisfaction. However, companies in the packaging sector often face one significant issue: the frequent replacement of packing machine blades and knives. This issue not only increases operational costs but also leads to production downtime, decreased efficiency, and compromised product quality.
In this article, we will explore the importance of using long-lasting packing machine blades and knives, focusing on the numerous benefits they bring to manufacturing operations. We will also demonstrate how investing in durable blades can help businesses save money, improve performance, and reduce waste.
1. The Real Cost of Short-Lived Blades
When companies opt for low-cost, short-lasting packing machine blades and knives, they might initially save money. However, the true costs associated with these blades are often hidden in multiple areas of the production process. These hidden costs, when compounded over time, result in far greater losses than the savings achieved through cheaper, less durable blades.
1.1 Production Time Loss
One of the most immediate costs associated with एसhort-lived blades is the downtime incurred when blades need to be replaced. While it may seem like a simple task, the act of stopping production, replacing the blades, and restarting operations introduces significant delays.
In fact, research has shown that, on average, every blade change leads to 30-60 minutes of downtime. Over time, this downtime can accumulate into hundreds of hours per year. Let’s break it down further:
Blade Changes Per Month | Average Downtime (minutes) | Monthly Downtime (hours) | Annual Downtime (hours) |
10 | 30 | 5 | 60 |
20 | 30 | 10 | 120 |
30 | 45 | 22.5 | 270 |
As shown in the table, even at a moderate replacement rate of 20 changes per month, a company could experience a 120 hours of downtime annually. For high-demand industries like food packaging, this can result in a 15-20% loss in annual productivity due to downtime, directly impacting order fulfillment, customer satisfaction, and ultimately, revenue generation.
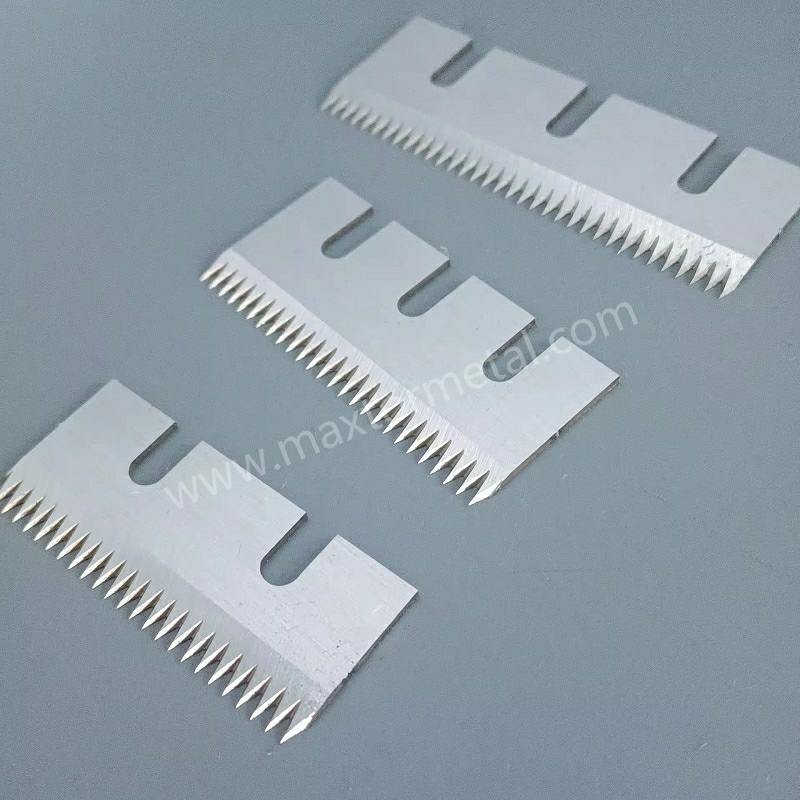
1.2 Labor Waste
Short-lived blades not only consume time on the production line but also waste valuable labor hours spent by technicians on routine maintenance. Consider that a maintenance technician typically spends 15-30 minutes per blade replacement. When blades need to be replaced frequently, technicians are tied up with this task, reducing their availability to perform higher-value work like equipment calibration or optimizing the packaging line.
Research indicates that maintenance personnel can spend up to 12-15% of their total work hours on blade-related tasks when low-quality blades are used. A 40% increase in labor costs is often the result, particularly in businesses with large production teams. Here’s a rough breakdown:
Blade Changes Per Month | Labor Time per Change (minutes) | Monthly Labor Time (hours) | Annual Labor Time (hours) |
10 | 30 | 5 | 60 |
20 | 30 | 10 | 120 |
30 | 45 | 22.5 | 270 |
For a company with 20 changes per month, this amounts to an additional 120 hours annually, which could instead be spent on improving production processes or quality control, rather than performing repetitive tasks like blade replacement.
Furthermore, there is an indirect cost in terms of lost productivity for higher-skilled staff, as they are required to allocate more time to blade replacements, rather than driving continuous improvements in the production process.
1.3 Decreased Quality
The impact of poor-quality blades on product quality is one of the most significant hidden costs. Dull or damaged packing machine blades often lead to inconsistent cuts, uneven seals, and poor packaging integrity. This not only affects the product’s shelf life but also results in substantial product waste and increased rework.
For instance, packaging machinery with low-quality knives can result in a 5-10% increase in defective products. The most common issues include:
- Inconsistent seals: A blunt blade may fail to create a clean seal, leading to products being inadequately sealed, which can compromise freshness or safety.
- Uneven cuts: A dull blade causes irregular cuts, which may lead to improperly sized packaging, increasing the need for rework and additional material costs.
- Packaging integrity issues: Faulty cuts can also compromise the entire packaging structure, resulting in damaged goods or products that cannot be sold.
The costs of these quality issues can be staggering. A report by the Manufacturing Quality Assurance Association (MQAA) found that for every 1% increase in defective products, companies typically experience a 4-6% increase in operational costs due to rework, waste, and customer returns.
In an industry like food packaging, quality issues related to blade performance can have an immediate effect on consumer trust, leading to negative reviews, loss of clients, and even regulatory scrutiny.
1.4 Unexpected Machine Wear
When packing machine knives become dull or are replaced too frequently, they exert additional strain on the machinery itself. Blunt blades require more force to make cuts, which increases friction within the machine. Over time, this extra friction causes a significant increase in wear and tear on the mechanical components, leading to a shorter lifespan of the equipment.
A study conducted by the International Packaging Equipment Association (IPEA) revealed that machinery subjected to additional friction due to dull blades experiences up to a 30% increase in maintenance costs. The reasons include:
- Increased motor strain: As the machine works harder to compensate for dull blades, motors and belts experience more stress, leading to more frequent failures and repairs.
- Overheating and excessive wear on bearings: Higher friction means bearings wear out faster, requiring more frequent replacement.
- Hydraulic or pneumatic failure: Excess friction can affect fluid systems in machines, leading to costly hydraulic repairs.
The long-term impact is even more pronounced. Over the course of 5 years, equipment running on dull blades may require 20-30% more maintenance than machines using high-performance, durable blades. In some cases, this can shorten the lifespan of machinery by up to 5 years, significantly increasing replacement costs and reducing the return on investment.

2. Nanjing Metal’s Solution: Long-Lasting Packing Machine Blades and Knives
At Nanjing Metal, we understand the challenges that come with low-quality, short-lived blades. With 18 years of experience in the industry, we provide durable, high-performance packing machine knives designed to reduce downtime and enhance production efficiency.
2.1 Premium Raw Materials
We use only the highest-grade steel and advanced coatings to manufacture our blades. Materials such as high-carbon steel or stainless steel are chosen for their superior strength and resistance to wear. Our advanced coatings also protect against corrosion, ensuring that the blades maintain their cutting edge longer.
2.2 Precision Manufacturing
Each blade is produced with precision to guarantee sharpness and accuracy in cutting. We use state-of-the-art machinery and rigorous quality control to ensure that every packing machine knife meets the strictest standards. Our precision manufacturing ensures that blades consistently deliver clean cuts, reducing production waste and downtime.
2.3 कस्टम समाधान
We recognize that each production line is unique. That’s why we offer customized solutions tailored to the specific needs of each client. Whether you need blades for a high-speed packaging line or blades that work with particular materials, we can design and manufacture blades to meet your exact requirements.
3. The Benefits of Investing in Long-Lasting Blades
Choosing high-quality, long-lasting packing machine blades and knives is more than just an upgrade—it’s a strategic investment that offers measurable benefits across various aspects of production. These benefits range from operational efficiency to cost savings and improved sustainability. Below, we delve deeper into how durable blades can transform your manufacturing process.
3.1 Maximized Operating Time
One of the most immediate and tangible benefits of long-lasting blades is the dramatic reduction in downtime. High-performance blades are engineered using premium materials and advanced coatings, enabling them to retain sharpness for longer periods even under heavy use.
Technical Insight:
Durable blades, such as those made from high-carbon tool steel or tungsten carbide, exhibit wear resistance that is 3-5 times greater than standard stainless steel blades. Additionally, blades treated with PVD (Physical Vapor Deposition) coatings, like titanium nitride, experience reduced friction and improved longevity.
सहायक डेटा:
- Downtime Reduction: Research by the International Packaging Association (IPA) found that manufacturers using high-quality blades experience a 40% decrease in blade replacements annually, reducing total downtime by 30-50%.
- Output Increase: Companies reported a 20% boost in overall output, thanks to fewer production interruptions caused by blade maintenance.
ब्लेड सामग्री | Average Lifespan (in operational hours) | Frequency of Replacement (per year) |
Standard Stainless Steel | 50-100 | 20-24 |
उच्च कार्बन इस्पात | 150-200 | 6-8 |
टंगस्टन कार्बाइड | 300-500 | 3-4 |
By reducing replacement frequency, businesses save not only time but also labor costs, ensuring a more seamless production process.
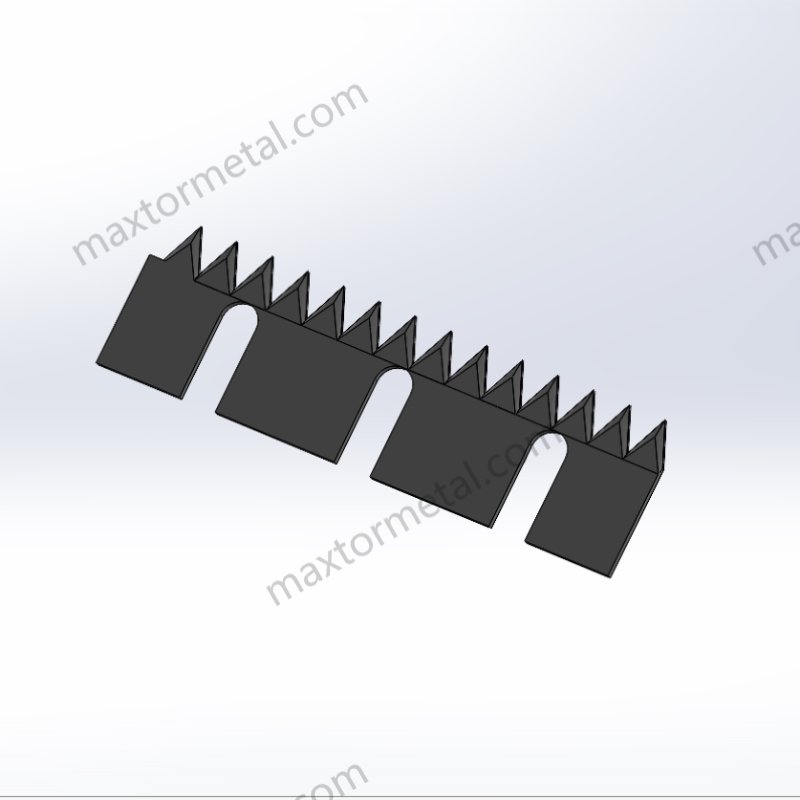
3.2 Improved Team Efficiency
Frequent blade changes disrupt workflows and divert skilled technicians from higher-value tasks. When operators spend less time managing routine maintenance, they can redirect their focus to optimizing production lines, improving quality control, and solving critical operational issues.
Technical Insight:
Durable blades are designed for quick installation and removal, often featuring modular mounting systems that minimize changeover time. Paired with advanced blade retention technologies, such as spring-loaded fixtures, they simplify the replacement process when needed.
सहायक डेटा:
- According to a study by the Manufacturing Productivity Council, companies using durable blades observed a 25% improvement in technician productivity, as blade-related maintenance tasks dropped significantly.
- The time saved by reducing blade changes allowed teams to dedicate 15-20% more hours to optimizing machinery settings, leading to greater efficiency and fewer production errors.
Key Observation: By reducing routine blade replacements, technicians can focus on machine optimization, ensuring smoother operations and better long-term results.
3.3 Protecting Product Quality
High-quality blades are precision-engineered to deliver consistent, clean cuts and seals, which are essential for maintaining product integrity. Dull or inconsistent blades, by contrast, can cause packaging defects such as uneven seals, improper cuts, or damaged materials.
Technical Insight:
Durable blades are manufactured to tight tolerances, often within ±0.01 mm, ensuring superior cutting accuracy. This precision minimizes the risk of material tearing or uneven seals, especially for high-speed production lines.
सहायक डेटा:
- A study conducted by PackTech Analytics revealed that manufacturers using precision blades experienced a 70% reduction in defective packaging compared to those using standard blades.
- Packaging defects caused by dull blades result in an average of 5-10% product waste, leading to higher costs for materials and rework. High-quality blades can virtually eliminate these issues, ensuring packaging consistency.
मुद्दा | Defect Rate with Standard Blades | Defect Rate with Precision Blades |
असमान कटौती | 12% | 2% |
Poor Seal Integrity | 8% | 1% |
Material Tearing | 10% | <1% |
Clean, precise cuts not only improve product presentation but also enhance shelf life, directly impacting customer satisfaction and brand loyalty.
3.4 Extending Equipment Lifespan
Low-quality blades cause additional strain on machinery due to the higher force required for cutting. Over time, this can lead to premature wear and tear on key components, increasing maintenance costs and reducing the overall lifespan of the equipment.
Technical Insight:
High-performance blades are designed with low-friction coatings, such as diamond-like carbon (DLC), that reduce the force required for cutting. This minimizes stress on motors, gears, and other moving parts. Additionally, blades with optimized edge geometry distribute force evenly, further reducing wear on machinery.
सहायक डेटा:
- Research by the Packaging Machinery Manufacturers Institute (PMMI) shows that equipment running on high-quality blades has a 20-30% longer operational lifespan, with significantly fewer breakdowns caused by blade-related stress.
- Companies using durable blades reported an 18% reduction in annual maintenance costs and a 25% decrease in unscheduled repairs over a 5-year period.
Cost Comparison:
Expense Category | Standard Blade Costs | Long-Lasting Blade Costs | Savings with Durable Blades |
Maintenance Costs (Annual) | $15,000 | $10,000 | $5,000 |
Equipment Repair Costs | $8,000 | $5,000 | $3,000 |
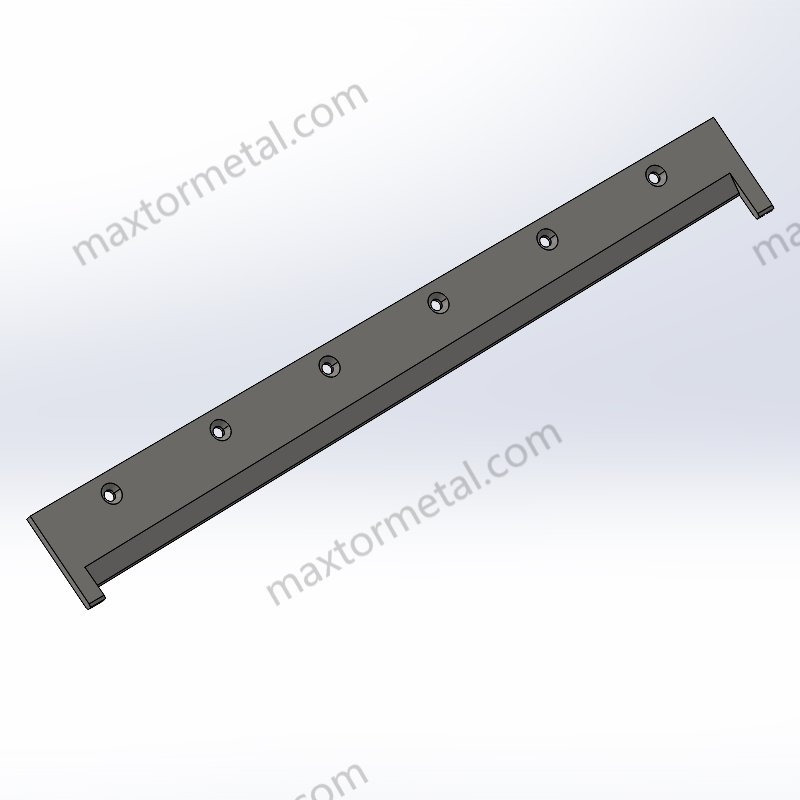
3.5 Enhancing Sustainability
In an era where sustainability is a growing concern, durable blades offer an eco-friendly alternative. Short-lived blades contribute to industrial waste, as they must be frequently replaced. Long-lasting blades reduce waste generation, aligning with sustainable production practices.
Technical Insight:
Advanced materials like tungsten carbide and PVD coatings not only extend blade life but also reduce the frequency of disposal. Additionally, many high-quality blades are recyclable, allowing manufacturers to implement circular economy principles.
सहायक डेटा:
- A report by Sustainable Packaging Association (SPA) found that companies using long-lasting blades reduced blade waste by 60-70% annually.
- The extended life of durable blades reduces raw material consumption, lowering the carbon footprint associated with blade production and disposal.
पर्यावरणीय प्रभाव:
मीट्रिक | मानक ब्लेड | Long-Lasting Blades | Reduction (%) |
Blade Waste (tons/year) | 1.5 | 0.5 | 66% |
CO2 Emissions (kg/year) | 10,000 | 4,000 | 60% |
By leveraging durable packing machine blades and knives, manufacturers not only gain operational and financial advantages but also contribute to a more sustainable future. These benefits, backed by technical innovations and proven industry data, make the choice clear: investing in high-performance blades is a smart, strategic move for any business.

4. Environmental Impact and Sustainability
In today’s world, sustainability is more important than ever. Packing machine blades and knives are often discarded after use, leading to industrial waste. However, by investing in high-quality, long-lasting blades, companies can reduce waste by extending the blades’ lifespan.
Additionally, at Nanjing Metal, we incorporate sustainable practices into the production process. Our blades are manufactured using eco-friendly coatings and materials, and we have minimized waste in our production facilities. By choosing our blades, companies not only improve their efficiency but also contribute to a greener, more sustainable future.
निष्कर्ष
In conclusion, long-lasting packing machine blades and knives offer a range of benefits, from reducing operational costs to improving product quality and team efficiency. By making the switch to high-performance blades, businesses can enhance their production processes, ensure customer satisfaction, and reduce machine downtime.
If you’re ready to optimize your packaging operation, we invite you to आज ही हमसे संपर्क करें. Our कस्टम ब्लेड समाधान are designed to meet your unique needs, ensuring maximum efficiency and durability. Reach out now for a consultation or a free quote.
Invest in long-lasting blades and unlock the full potential of your production line!