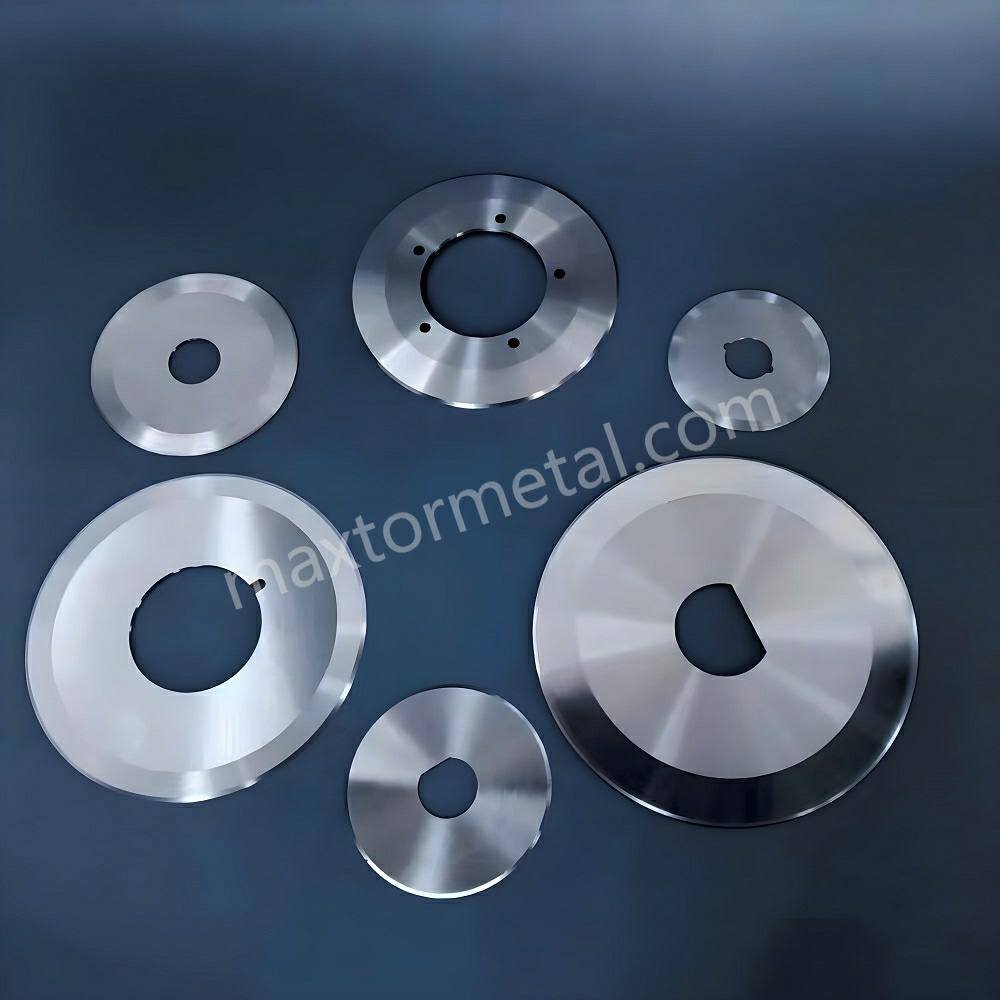
गोलाकार ब्लेड आधुनिक विनिर्माण और प्रसंस्करण उद्योगों की आधारशिला हैं। उनकी बहुमुखी प्रतिभा और सटीकता उन्हें अनुप्रयोगों की एक विस्तृत श्रृंखला में अपरिहार्य बनाती है। चाहे आप कपड़ा, भोजन या धातु काट रहे हों, सही गोलाकार ब्लेड चुनना दक्षता, गुणवत्ता और लागत-प्रभावशीलता सुनिश्चित करता है। यह मार्गदर्शिका आपकी विशिष्ट आवश्यकताओं के लिए एक सूचित निर्णय लेने के लिए गोलाकार ब्लेड के बारे में आपको जो कुछ भी जानना चाहिए, उस पर गहराई से चर्चा करती है।
1. गोलाकार ब्लेड का परिचय
गोलाकार ब्लेड उच्च परिशुद्धता और अनुकूलनशीलता के लिए डिज़ाइन किए गए रोटरी कटिंग उपकरण हैं। इनका उपयोग खाद्य प्रसंस्करण, कपड़ा निर्माण, प्लास्टिक और धातु निर्माण जैसे उद्योगों में किया जाता है। विभिन्न सामग्रियों और कार्यों को संभालने की उनकी क्षमता उन्हें औद्योगिक और वाणिज्यिक सेटिंग्स में सबसे अधिक मांग वाले उपकरणों में से एक बनाती है।
गोलाकार ब्लेड एक डिस्क के आकार का कटिंग टूल है जो स्लाइसिंग, ट्रिमिंग, छेद करने और स्कोरिंग जैसे कार्य कर सकता है। ये ब्लेड विभिन्न सामग्रियों और किनारे के प्रकारों में आते हैं, जिनमें से प्रत्येक विशिष्ट अनुप्रयोगों के लिए अनुकूलित होता है। उनकी सटीकता और स्थिरता उन्हें पारंपरिक कटिंग टूल से अलग करती है।
सीधे चाकू या बैंड आरी की तुलना में, गोलाकार ब्लेड प्रदान करते हैं:
- लाभ: निरंतर संचालन, उच्च गति और बेहतर सटीकता।
- सीमाएँ: जटिल आकृतियों के लिए विशिष्ट सेटअप की आवश्यकता हो सकती है तथा ये रैखिक या दोहरावदार कटों के लिए अधिक उपयुक्त होते हैं।
2. गोलाकार ब्लेड चुनने में मुख्य कारक
2.1 ब्लेड सामग्री का चयन
एक गोलाकार ब्लेड की सामग्री उसके प्रदर्शन और दीर्घायु में महत्वपूर्ण भूमिका निभाती है। सही सामग्री का चयन, काटे जाने वाली सामग्री, परिचालन स्थितियों और लागत संबंधी विचारों जैसे कारकों पर निर्भर करता है। नीचे सामान्य ब्लेड सामग्रियों की गहन तुलना दी गई है:
सामग्री | कठोरता (एचआरसी) | प्रतिरोध पहन | जंग प्रतिरोध | तापीय स्थिरता | अनुप्रयोग |
उच्च कार्बन स्टील | 55–62 | मध्यम | कम | मध्यम | सामान्य प्रयोजन कटिंग, लागत प्रभावी समाधान। |
स्प्रिंग स्टील | 45–55 | उच्च | कम | मध्यम | आघात प्रतिरोध, लचीला काटने वातावरण। |
स्टेनलेस स्टील | 50–58 | मध्यम | उच्च | मध्यम | खाद्य-ग्रेड अनुप्रयोग, उच्च आर्द्रता की स्थिति। |
डी2 टूल स्टील | 58–62 | उच्च | मध्यम | उच्च | परिशुद्ध कटाई, घिसाव-गहन कार्य। |
एम2 एचएसएस | 60–65 | बहुत ऊँचा | मध्यम | बहुत ऊँचा | उच्च गति संचालन, गर्मी गहन वातावरण। |
टंगस्टन कार्बाइड | 75–80 | अत्यंत ऊंचा | उच्च | बहुत ऊँचा | भारी-भरकम कटिंग, विस्तारित जीवनकाल। |
चीनी मिट्टी | 85+ | उच्च | बहुत ऊँचा | कम | अधातु अनुप्रयोगों में अति परिशुद्धता की आवश्यकता होती है। |
डेटा-संचालित अंतर्दृष्टि:
- प्रतिरोध पहनअध्ययनों से पता चलता है कि टंगस्टन कार्बाइड ब्लेड में उच्च कार्बन स्टील की तुलना में 10 गुना अधिक प्रतिरोध होता है, जो उन्हें उच्च उत्पादन वातावरण के लिए आदर्श बनाता है।
- जंग प्रतिरोधस्टेनलेस स्टील ब्लेड खारे वातावरण में 0.01 मिमी/वर्ष से कम की संक्षारण दर प्रदर्शित करते हैं, जिससे वे खाद्य प्रसंस्करण में अपरिहार्य हो जाते हैं।
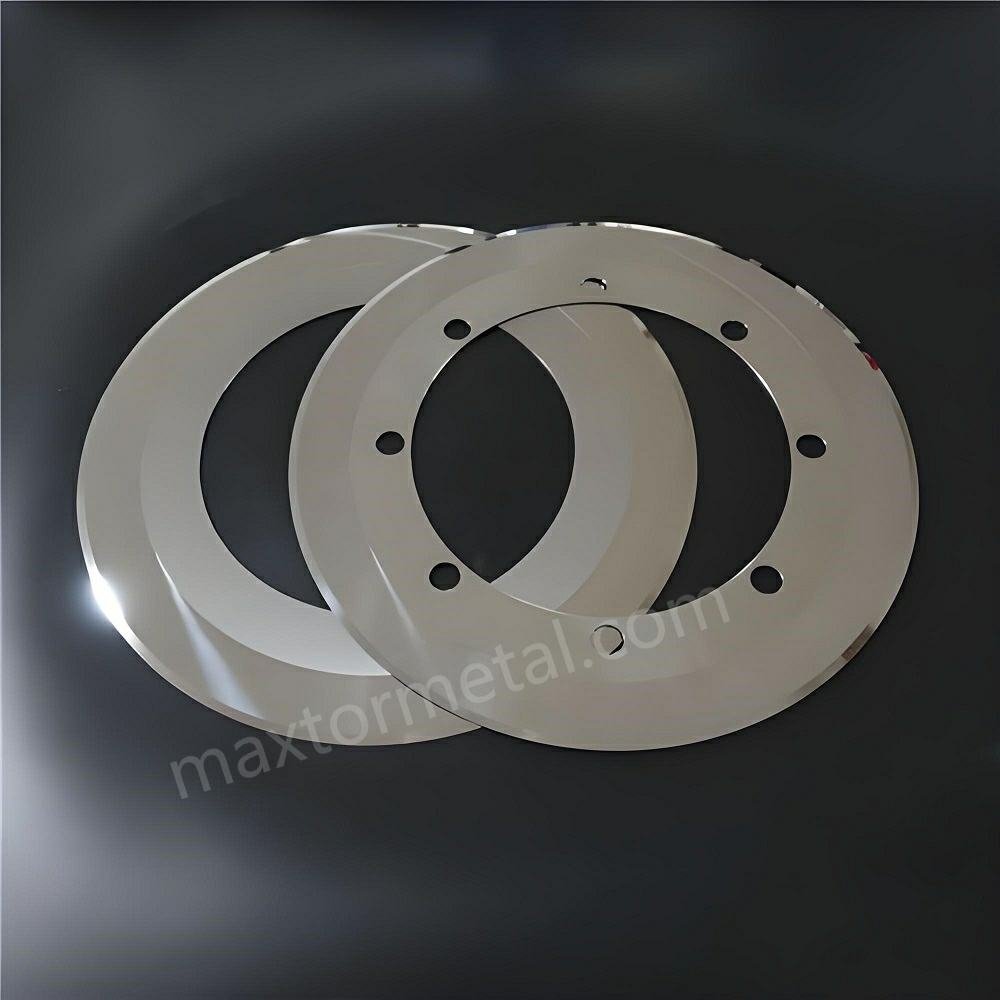
2.2 ब्लेड एज प्रकार का चयन
एक गोलाकार ब्लेड का किनारा प्रकार इसकी काटने की सटीकता और विशिष्ट कार्यों के लिए उपयुक्तता निर्धारित करता है। नीचे विस्तृत स्पष्टीकरण और उदाहरण दिए गए हैं:
सादे किनारे:
- सिंगल बेवल (तीखा): ब्रेड या कपड़े जैसी नरम सामग्री को काटने के लिए आदर्श। यह एक साफ, निर्बाध कट प्रदान करता है।
- सिंगल बेवल (ब्लंट): ऐसे अनुप्रयोगों के लिए डिज़ाइन किया गया है जहां स्थायित्व को तीक्ष्णता से अधिक प्राथमिकता दी जाती है, जैसे रबर काटना।
- डबल बेवल (तीव्र): दोहरे पक्ष की परिशुद्धता के लिए सर्वोत्तम, कांच के रेशों जैसी भंगुर सामग्रियों को काटने में उपयोग किया जाता है।
- डबल बेवल (कुंद): चमड़े जैसी सघन सामग्रियों में बार-बार कटौती की आवश्यकता वाले अनुप्रयोगों के लिए इष्टतम।
दांतेदार किनारे:
दाँत का प्रकार | विशेषताएँ | सर्वोत्तम अनुप्रयोग |
मानक वी | संतुलित डिजाइन, सामान्य प्रयोजन | प्लास्टिक, कार्डबोर्ड |
वैरी-गहराई V | बहुमुखी कट के लिए अलग-अलग दाँत की गहराई | मिश्रित सामग्री, लेमिनेट |
हाय/लो वी | सटीक कटाई के लिए बेहतर पकड़ | पतली धातुएं, पर्णिकाएं |
स्कैलप्ड | नरम सामग्री के लिए कोमल दांत | फोम, ब्रेड, मुलायम वस्त्र |
पेग स्टाइल | छिद्रण के लिए दांतों के बीच व्यापक दूरी | कागज, पैकेजिंग सामग्री |
तिरछा दांत | बेवल कट के लिए कोणीय दांत | लकड़ी, सघन सामग्री |
डबल-डबल शार्प | जटिल विवरणों के लिए अत्यंत तीक्ष्ण | उच्च परिशुद्धता स्लिटिंग |
तकनीकी तुलना:
- काटने की गतिअध्ययनों से पता चलता है कि सादे किनारों की तुलना में स्कैलोप्ड किनारे नरम सामग्रियों में 30% अधिक तीव्र काटने की गति प्राप्त करते हैं।
- दाँत प्रोफाइल: खूंटी-शैली के किनारों को ± 0.02 मिमी तक की सहनशीलता वाले छिद्रों के लिए पसंद किया जाता है।
3. उद्योग द्वारा परिपत्र ब्लेड अनुप्रयोग
3.1 खाद्य प्रसंस्करण
गोलाकार ब्लेड स्वचालित खाद्य प्रसंस्करण लाइनों की आधारशिला हैं। उनकी भूमिका सटीक स्लाइसिंग, डाइसिंग और भाग निर्धारण तक फैली हुई है। मुख्य विचारणीय बातें निम्नलिखित हैं:
- सामग्री: स्टेनलेस स्टील को इसके संक्षारण प्रतिरोध और स्वच्छता अनुपालन के कारण पसंद किया जाता है।
- किनारे का प्रकार: एकल बेवल तीखे किनारे न्यूनतम सामग्री विरूपण के साथ साफ कटौती सुनिश्चित करते हैं।
3.2 प्लास्टिक और रबर
गोलाकार ब्लेड सिंथेटिक सामग्रियों के लिए लगातार कटिंग प्रदान करते हैं, जिससे गर्मी या दबाव के कारण होने वाली विकृति से बचा जा सकता है। उच्च गति वाले स्टील (M2) को अक्सर उच्च घर्षण कटिंग के दौरान इसकी तापीय स्थिरता के लिए चुना जाता है।
3.3 वस्त्र एवं चमड़ा
गोलाकार ब्लेड कपड़ों और चमड़े को बिना घिसे या खिंचे काट देते हैं। सिरेमिक ब्लेड, अपने अत्यंत तीखे किनारों के साथ, जटिल डिजाइनों के लिए आदर्श हैं।
अंतर्दृष्टि: एक अग्रणी फैशन ब्रांड ने डबल-बेवल सिरेमिक ब्लेड के साथ चमड़े की कटाई में बेहतर परिशुद्धता की रिपोर्ट दी है, जिससे सिलाई प्रक्रिया तेज हो गई है।
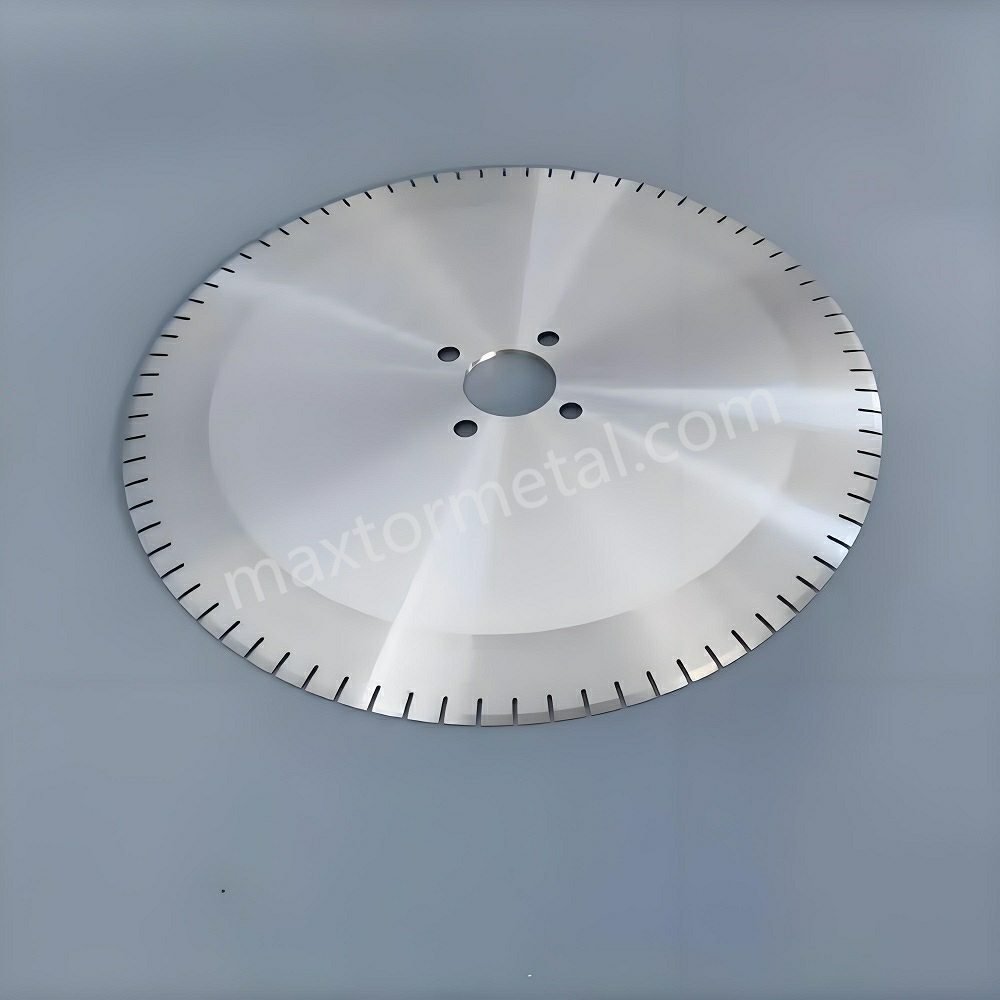
3.4 फोम उद्योग
फोम काटने के लिए कम से कम खिंचाव वाले ब्लेड की आवश्यकता होती है ताकि वे फटने से बच सकें। स्कैलप्ड किनारे विशेष रूप से प्रभावी होते हैं।
प्रयोगशाला परीक्षणों से पता चला कि स्कैलोप्ड ब्लेड मानक किनारों की तुलना में टूटने की दर को 25% तक कम कर देते हैं।
3.5पन्नी, चादरें, और Metals
धातु निर्माण में गोलाकार ब्लेड अपरिहार्य हैं क्योंकि वे गड़गड़ाहट और सामग्री की बर्बादी को कम करते हुए उच्च परिशुद्धता कटौती करने की क्षमता रखते हैं। उनके अनुप्रयोग ऑटोमोटिव विनिर्माण, एयरोस्पेस और पैकेजिंग जैसे उद्योगों में फैले हुए हैं।
टंगस्टन कार्बाइड युक्त ब्लेड को उनकी असाधारण कठोरता (एचआरसी 75-80) के कारण एल्युमीनियम, तांबा और स्टेनलेस स्टील जैसी धातुओं को काटने के लिए पसंद किया जाता है।
उच्च गति वाले स्टील (एम2) ब्लेड गर्मी प्रतिरोध और लंबे काटने के चक्र की आवश्यकता वाले कार्यों के लिए उपयुक्त हैं।
डबल-बेवल तीखे किनारे गड़गड़ाहट रहित कट और साफ फिनिश सुनिश्चित करते हैं, जो धातु पन्नी जैसे उत्पादों के लिए महत्वपूर्ण है।
पतली धातु की चादरों पर पकड़ और कट की स्थिरता में सुधार के लिए अक्सर तिरछे दाँतों वाले विन्यास का उपयोग किया जाता है
3.6 कागज और नालीदार कार्डबोर्ड
कागज़ और पैकेजिंग उद्योग में, गोलाकार ब्लेड सामग्री की बर्बादी को कम करते हुए तेज, सटीक कट प्राप्त करने के लिए महत्वपूर्ण हैं। इन ब्लेड का इस्तेमाल वाणिज्यिक पैकेजिंग से लेकर बुकबाइंडिंग तक के अनुप्रयोगों में स्लिटिंग, ट्रिमिंग और छिद्रण के लिए व्यापक रूप से किया जाता है।
स्टेनलेस स्टील ब्लेड उच्च आर्द्रता वाले वातावरण में संक्षारण और घिसाव के प्रति अपने प्रतिरोध के कारण आदर्श हैं।
टंगस्टन कार्बाइड विकल्प को उनके टिकाऊपन के कारण उच्च मात्रा में उत्पादन के लिए पसंद किया जाता है।
विभिन्न गहराई वाले वी-दांतेदार किनारे मोटे नालीदार कार्डबोर्ड में सुसंगत कट सुनिश्चित करते हैं।
स्कैलोप्ड किनारों का उपयोग नरम कागज उत्पादों जैसे टिशू और हल्के पैकेजिंग के लिए किया जाता है।
3.7 लकड़ी का काम
आरा मिलों और लकड़ी के काम में इस्तेमाल होने वाले गोलाकार ब्लेड साफ और सटीक कट के लिए अनुमति देते हैं। उदाहरण: तख्तों या प्लाईवुड की प्रोसेसिंग।
उच्च कार्बन स्टील अपनी लागत प्रभावशीलता और तेज करने में आसानी के कारण सामान्य प्रयोजन की लकड़ी काटने के लिए आम है।
टंगस्टन कार्बाइड युक्त ब्लेड को सागौन या इंजीनियर्ड लकड़ी जैसी कठोर या घर्षणकारी लकड़ी को काटने के लिए पसंद किया जाता है।
तिरछे दाँत वाले किनारे लकड़ियों को तख्तों में काटने के लिए आदर्श होते हैं।
डबल-बेवल तीखे किनारे, कैबिनेटरी या फर्नीचर बनाने जैसे बढ़िया लकड़ी के काम के लिए साफ कट प्रदान करते हैं।
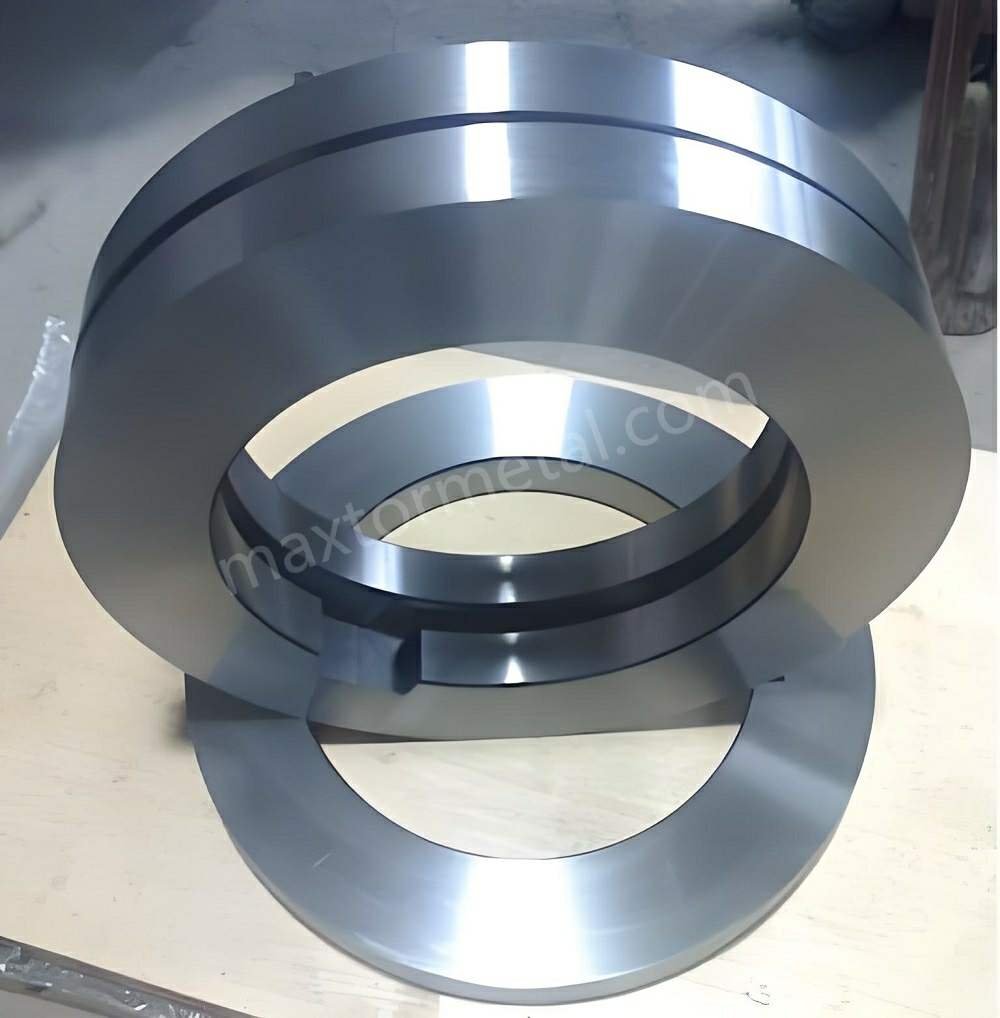
3.8 फाइबरग्लास
फाइबरग्लास को काटना इसकी भंगुर प्रकृति और घर्षण गुणों के कारण एक चुनौतीपूर्ण कार्य है। विशेष सामग्री और किनारे के डिज़ाइन वाले गोलाकार ब्लेड इस अनुप्रयोग में स्थायित्व और सटीकता प्रदान करते हैं।
कार्बाइड-टिप वाले ब्लेड, घिसाव और तापीय तनाव के प्रति अपने प्रतिरोध के कारण फाइबरग्लास के लिए उद्योग मानक हैं।
सिरेमिक ब्लेड का उपयोग अति-सटीक अनुप्रयोगों के लिए भी किया जाता है, हालांकि उनके टूटने की संभावना अधिक होती है।
प्रबलित बेवेल के साथ सादे किनारे उखड़ने और विघटन को न्यूनतम करते हैं।
पेग-शैली या विभिन्न गहराई वाले वी-दांत किनारे काटने की गति को नियंत्रित करने और सतह पर दरार को कम करने में मदद करते हैं।
4. काटने के प्रकार और ब्लेड विन्यास
4.1 काटना
सामग्री की कठोरता, घनत्व और मोटाई के आधार पर काटने का कार्य व्यापक रूप से भिन्न होता है। इष्टतम परिणाम प्राप्त करने के लिए:
- सामग्री कठोरता: रॉकवेल कठोरता (HRC) वाले ब्लेड का उपयोग करें जो काटे जाने वाली सामग्री की कठोरता से मेल खाता हो या उससे थोड़ा अधिक हो। उदाहरण के लिए, स्टेनलेस स्टील जैसी धातुओं को काटने के लिए 58 से अधिक HRC वाले D2 टूल स्टील या टंगस्टन कार्बाइड ब्लेड की आवश्यकता होती है।
- द्रव्य का गाढ़ापन: मोटे पदार्थों के लिए मजबूत ब्लेड की आवश्यकता होती है, जिनका कोर मजबूत हो, ताकि दबाव के कारण ब्लेड के झुकने या विकृत होने से बचा जा सके।
- काटने की गति: स्वचालित प्रणालियों जैसे उच्च गति संचालन में, M2 उच्च गति वाले स्टील से लाभ मिलता है क्योंकि यह गर्मी प्रतिरोधी है। अध्ययनों से पता चलता है कि ये ब्लेड 50 मीटर प्रति सेकंड से अधिक गति पर भी काटने की दक्षता बनाए रखते हैं।
4.2 ट्रिमिंग
उच्च गुणवत्ता वाली फिनिश प्राप्त करने के लिए सटीक ट्रिमिंग आवश्यक है:
- ब्लेड ज्यामिति: डबल-बेवल वाले तीखे ब्लेड न्यूनतम छिल के साथ सामग्री को हटाने में उत्कृष्ट होते हैं।
- किनारा सहनशीलता: कपड़ा निर्माण या खाद्य पैकेजिंग जैसे उद्योगों में एक समान किनारा सुनिश्चित करने के लिए ± 0.01 मिमी की सहनशीलता बनाए रखें।
- उद्योग अंतर्दृष्टि: फाइबरग्लास निर्माताओं ने पाया कि सिरेमिक ब्लेड ने मानक स्टील की तुलना में किनारों के टूटने को 35% तक कम कर दिया, जिससे थर्मल इन्सुलेशन पैनल जैसे अनुप्रयोगों में उत्पाद की गुणवत्ता में वृद्धि हुई।
4.3 स्लिटिंग और स्लाइसिंग
उच्च-मात्रा वाले स्लिटिंग और स्लाइसिंग कार्यों के लिए स्थायित्व और तीक्ष्णता की आवश्यकता होती है:
- उच्च कार्यभार: कागज और पन्नी उत्पादन में निरंतर उपयोग के तहत टंगस्टन कार्बाइड युक्त ब्लेड उच्च गति वाले स्टील की तुलना में 10 गुना अधिक समय तक चलते हैं।
- ब्लेड विन्यास: सटीक गैपिंग के साथ समायोज्य स्लिटर सेटअप सटीकता में सुधार करते हैं और सामग्री की बर्बादी को 15% तक कम करते हैं।
4.4 छिद्रण और स्कोरिंग
सटीक छिद्रण और स्कोर विशेष ब्लेड प्रोफाइल पर निर्भर करते हैं:
- दाँत का डिज़ाइन: पेग-स्टाइल या विभिन्न गहराई वाले वी-टूथ ब्लेड, बिना फाड़े नियंत्रित प्रवेश प्रदान करते हैं, जो कागज पैकेजिंग और चिकित्सा सामग्री के लिए आवश्यक है।
- गहराई नियंत्रण: सीएनसी-नियंत्रित स्कोरिंग प्रणालियों से सुसज्जित उन्नत मशीनें कड़े उद्योग मानकों को पूरा करते हुए प्रवेश गहराई को ±0.005 मिमी के भीतर समायोजित कर सकती हैं।
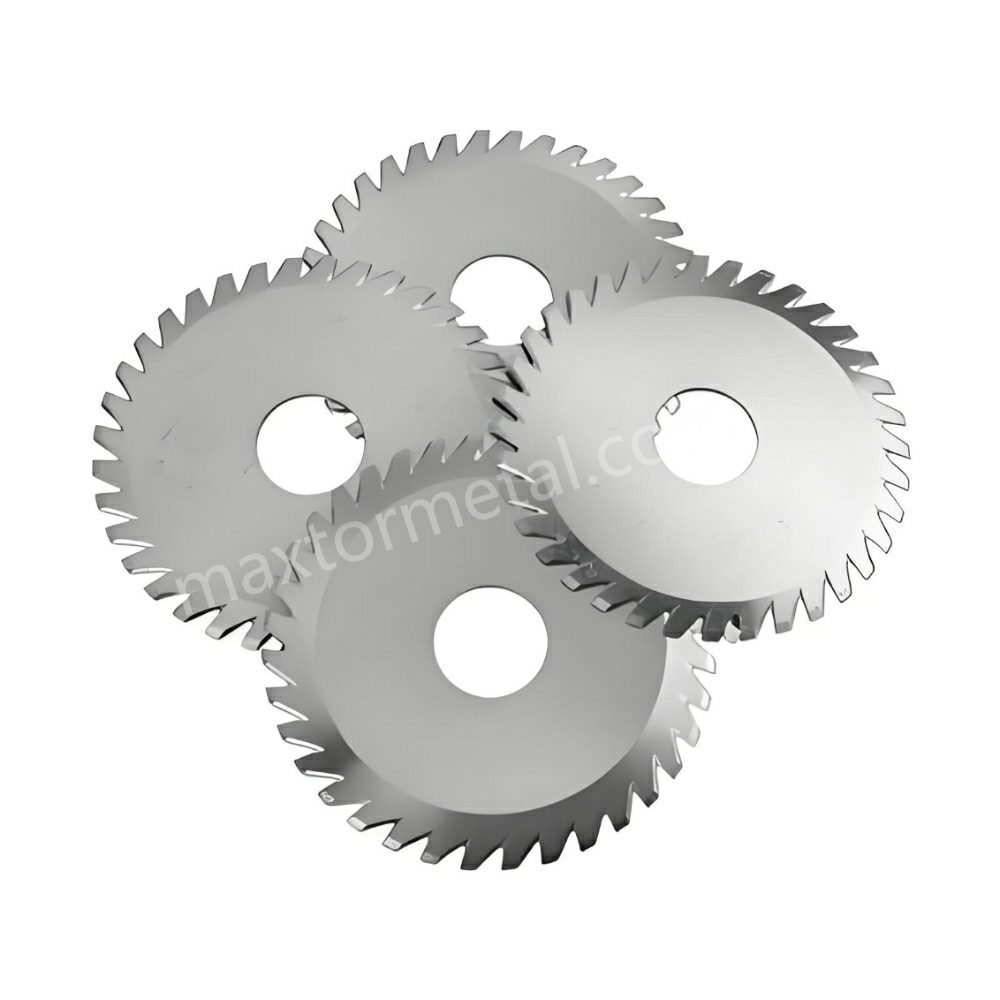
5. रखरखाव और देखभाल
5.1 दीर्घायु के लिए व्यावहारिक सुझाव
- भंडारण: ब्लेड को तापमान-नियंत्रित, कम आर्द्रता वाले वातावरण में रखें। अत्यधिक नमी जंग को बढ़ाती है, खासकर उच्च-कार्बन स्टील ब्लेड में।
- स्नेहन: परिचालन के दौरान घर्षण और घिसाव को कम करने के लिए औद्योगिक-ग्रेड स्नेहक का उपयोग करें।
- सफाई: अम्लीय या अपघर्षक क्लीनर का इस्तेमाल न करें। इसके बजाय, स्टेनलेस या सिरेमिक ब्लेड की अखंडता बनाए रखने के लिए पीएच-न्यूट्रल डिटर्जेंट का इस्तेमाल करें।
डेटा अंतर्दृष्टि:
नियमित सफाई और स्नेहन से ब्लेड की सेवा अवधि 40% तक बढ़ जाती है, जैसा कि 2022 में किए गए एक औद्योगिक टूलींग अध्ययन में बताया गया है।
5.2 घिसावट को पहचानना और उसका समाधान करना
पहनने के प्रारंभिक लक्षणों में शामिल हैं:
- दृश्य संकेतक: काटने वाले किनारे पर चिप्स या खरोंच।
- प्रदर्शन में गिरावट: ऑपरेशन के दौरान असमान कटौती या अत्यधिक प्रतिरोध।
- गर्मी से क्षति: घर्षण से उत्पन्न गर्मी के लंबे समय तक संपर्क में रहने के कारण रंग उड़ जाना या मुड़ जाना।
तकनीकी दृष्टिकोण:
ब्लेड की अखंडता का मूल्यांकन करने के लिए डिजिटल एज शार्पनेस टेस्टर का उपयोग करें। 15% से अधिक शार्पनेस हानि पुनः शार्पनिंग या प्रतिस्थापन की आवश्यकता को इंगित करती है।
5.3 सामान्य गलतियों से बचना
- अनुचित सफाई: स्टील वूल या कठोर अपघर्षकों से बचें जो सतह की फिनिश को नष्ट कर सकते हैं।
- गलत स्थापना: ब्लेडों का गलत संरेखण घिसाव की दर को बढ़ाता है और कट की गुणवत्ता को प्रभावित करता है। हमेशा निर्माता के टॉर्क विनिर्देशों का पालन करें।
5.4 अनुशंसित उपकरण
- शार्पनिंग सिस्टम: हीरा पीसने वाले पहियों वाली स्वचालित प्रणालियां ±0.001 मिमी की सहनशीलता प्राप्त करती हैं, जो किनारे की स्थिरता बनाए रखने के लिए आवश्यक है।
- ब्लेड सफाई इकाइयाँ: अल्ट्रासोनिक क्लीनर ब्लेड को नुकसान पहुंचाए बिना अवशेषों को प्रभावी ढंग से हटा देते हैं।
6. अक्सर पूछे जाने वाले प्रश्न
6.1 यह कैसे सुनिश्चित करें कि ब्लेड मेरे अनुप्रयोग के लिए उपयुक्त है?
निम्नलिखित मापदंडों का मिलान करें:
- सामग्री संगतता: उदाहरण के लिए, स्वच्छता नियमों को पूरा करने के लिए खाद्य-ग्रेड अनुप्रयोगों में स्टेनलेस स्टील का उपयोग करें।
- किनारे का प्रकार: स्कैलप्ड किनारे फोम जैसी नरम सामग्री के लिए सर्वोत्तम होते हैं, जबकि दांतेदार किनारे लकड़ी या मिश्रित सामग्री जैसी सघन सामग्री के लिए उपयुक्त होते हैं।
डेटा-संचालित सलाह:
2023 का एक अध्ययन कटिंग टूल इंस्टीट्यूट पाया गया कि 65% अनुप्रयोग विसंगतियाँ अनुचित सामग्री-किनारे संयोजनों के कारण थीं।
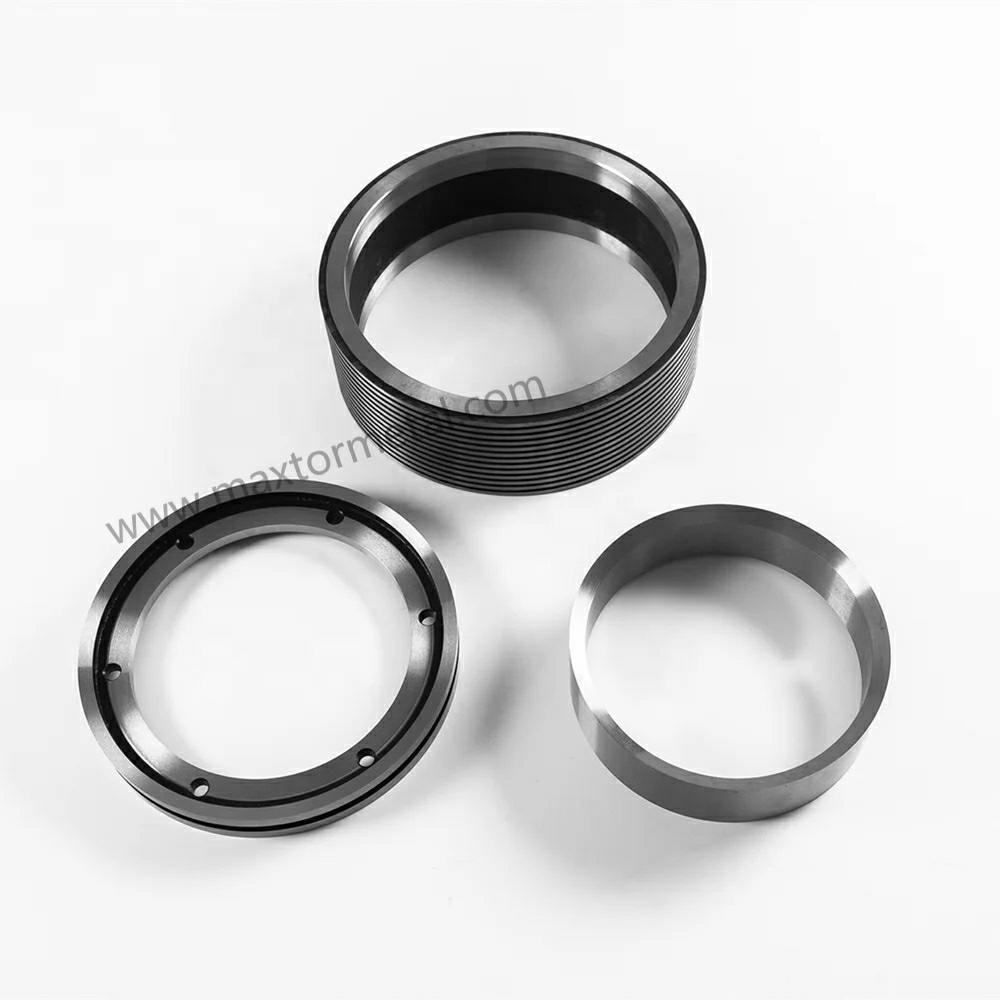
6.2 लागत बनाम लाभ विश्लेषण
टंगस्टन कार्बाइड या सिरेमिक जैसी प्रीमियम सामग्रियों में निवेश करने से:
- लंबी उम्र: टंगस्टन कार्बाइड ब्लेड उच्च कार्बन स्टील की तुलना में 3-5 गुना अधिक समय तक चलते हैं, जिससे प्रतिस्थापन की आवश्यकता कम हो जाती है।
- कम डाउनटाइम: उन्नत स्थायित्व ब्लेड परिवर्तन के लिए मशीन के रुकने को न्यूनतम करता है।
6.3 ग्राहक प्रश्न
क्यू: नरम सामग्री की सटीक कटाई के लिए कौन सा ब्लेड सबसे अच्छा है?
ए: स्कैलप्ड स्टेनलेस स्टील ब्लेड अपनी तीक्ष्णता और फटने के प्रतिरोध के कारण आदर्श है।
क्यू: ब्लेड को कितनी बार तेज किया जाना चाहिए?
ए: सामग्री और उपयोग के आधार पर, ब्लेड को आमतौर पर हर 100-200 घंटे के संचालन के बाद तेज करने की आवश्यकता होती है।
7. सर्कुलर ब्लेड खरीदने के सर्वोत्तम तरीके
7.1 विश्वसनीय आपूर्तिकर्ता का चयन
निम्नलिखित चेकलिस्ट के आधार पर आपूर्तिकर्ताओं का मूल्यांकन करें:
- प्रमाणपत्र: आईएसओ 9001 या समान गुणवत्ता मानक।
- अनुकूलन विकल्प: आपकी विशिष्टताओं के अनुरूप ब्लेड बनाने की क्षमता।
- सहायता सेवाएँ: बिक्री के बाद तेज करना, रखरखाव और तकनीकी सहायता।
डेटा अंतर्दृष्टि:
सर्वेक्षणों से पता चलता है कि औद्योगिक खरीदार ब्लेड विक्रेताओं का चयन करते समय आपूर्तिकर्ता प्रमाणन को प्राथमिकता देते हैं।
7.2 के लाभ कस्टम ब्लेड
कस्टम ब्लेड की पेशकश:
- परिशुद्धता फिट: अद्वितीय परिचालन आवश्यकताओं को पूरा करने के लिए डिज़ाइन किया गया, जिससे सेटअप समय कम हो जाता है।
- लागत बचत: यद्यपि प्रारंभिक लागत अधिक हो सकती है, लेकिन कस्टम ब्लेड अकुशलता और अपव्यय को न्यूनतम कर देते हैं।
7.3 थोक खरीद के लाभ
- मात्रा छूट: अधिकांश आपूर्तिकर्ता 100 इकाइयों से अधिक के ऑर्डर पर छूट प्रदान करते हैं।
- दीर्घकालिक समझौते: नियमित ब्लेड डिलीवरी के लिए अनुबंध स्थापित करने से खरीद का समय कम हो जाता है और मूल्य निर्धारण स्थिर हो जाता है।
उदाहरण: एक वैश्विक कपड़ा निर्माता ने एक विश्वसनीय ब्लेड आपूर्तिकर्ता के साथ बहु-वर्षीय समझौते पर हस्ताक्षर करके प्रतिवर्ष 15% की बचत की।
8. नानजिंग Metal का व्यावसायिक समर्थन
पर नानजिंग Metal, हम विविध उद्योगों के लिए उच्च-प्रदर्शन वाले गोलाकार ब्लेडों के डिज़ाइन और निर्माण में विशेषज्ञ हैं। हमारी सेवाओं में शामिल हैं:
- आपकी आवश्यकताओं को समझने के लिए निःशुल्क परामर्श।
- आपके अनुप्रयोगों के अनुरूप कस्टम ब्लेड समाधान।
- आकर्षक प्रथम-ऑर्डर छूट.
हमसे संपर्क करें आज ही अपने परिचालन को अत्याधुनिक परिपत्र ब्लेड समाधानों के साथ उन्नत करने के लिए संपर्क करें!
3 प्रतिक्रियाएं