सारांश
अपने जीवन काल को बढ़ाना डिस्क स्लिटिंग ब्लेड औद्योगिक संचालन में दक्षता बनाए रखने और लागत कम करने के लिए यह महत्वपूर्ण है। यह लेख ब्लेड के स्थायित्व को प्रभावित करने वाले कारकों की पड़ताल करता है, विशेषज्ञ रखरखाव युक्तियाँ प्रदान करता है, और ब्लेड के प्रदर्शन को अनुकूलित करने के लिए कार्रवाई योग्य रणनीतियाँ प्रदान करता है। जानें कि कैसे उचित देखभाल उत्पादकता में सुधार कर सकती है और पैसे बचा सकती है।
परिचय
डिस्क स्लिटिंग ब्लेड कागज़ और प्लास्टिक काटने से लेकर धातु काटने तक, कई औद्योगिक कार्यों में ये आवश्यक उपकरण हैं। हालाँकि, अनुचित रखरखाव या उपयोग से इनका जीवनकाल बहुत कम हो सकता है, जिससे लागत बढ़ जाती है और उत्पादकता कम हो जाती है। सिद्ध रखरखाव प्रथाओं को लागू करके और काम के लिए सही ब्लेड चुनकर, आप उनके जीवन को काफी हद तक बढ़ा सकते हैं। यह मार्गदर्शिका आपको समय और पैसे बचाते हुए अपने डिस्क स्लिटिंग ब्लेड से अधिकतम लाभ उठाने में मदद करने के लिए कार्रवाई योग्य जानकारी प्रदान करेगी।
ब्लेड की लंबी उम्र के महत्व को कम करके नहीं आंका जा सकता। जब ब्लेड की उचित देखभाल की जाती है, तो वे न केवल बेहतर प्रदर्शन करते हैं बल्कि परिचालन में रुकावटों को भी कम करते हैं। इस लेख में, हम व्यापक रखरखाव रणनीतियों का पता लगाएंगे, उन्नत तकनीकों में तल्लीन होंगे, और वास्तविक दुनिया के उदाहरणों को उजागर करेंगे जो उचित ब्लेड देखभाल के प्रभाव को प्रदर्शित करते हैं।
1. डिस्क स्लिटिंग ब्लेड को समझना
डिस्क स्लिटिंग ब्लेड क्या हैं?
डिस्क स्लिटिंग ब्लेड, जिन्हें रोटरी स्लिटर ब्लेड या सर्कुलर स्लिटिंग ब्लेड के रूप में भी जाना जाता है, सटीक उपकरण हैं जिनका उपयोग सामग्री को छोटे स्ट्रिप्स या सेक्शन में काटने के लिए किया जाता है। पैकेजिंग, धातु प्रसंस्करण और मुद्रण जैसे उद्योग स्वच्छ और कुशल कटौती के लिए इन ब्लेड पर बहुत अधिक निर्भर करते हैं।
प्रमुख विनिर्देशों में शामिल हैं:
- सामग्री: ब्लेड आमतौर पर टूल स्टील, कार्बाइड या स्टेनलेस स्टील से बने होते हैं, जो अनुप्रयोग पर निर्भर करता है।
- डिज़ाइन: विशिष्ट सामग्रियों और काटने की आवश्यकताओं के अनुरूप मोटाई, व्यास और किनारे की तीक्ष्णता में भिन्नता होती है।
डिस्क स्लिटिंग ब्लेड तैयार उत्पादों की गुणवत्ता बनाए रखने में महत्वपूर्ण भूमिका निभाते हैं। चाहे कठोर धातुओं या नाजुक प्लास्टिक फिल्मों को काटना हो, इन ब्लेड को काम के हिसाब से बनाया जाना चाहिए ताकि लगातार प्रदर्शन सुनिश्चित हो सके।
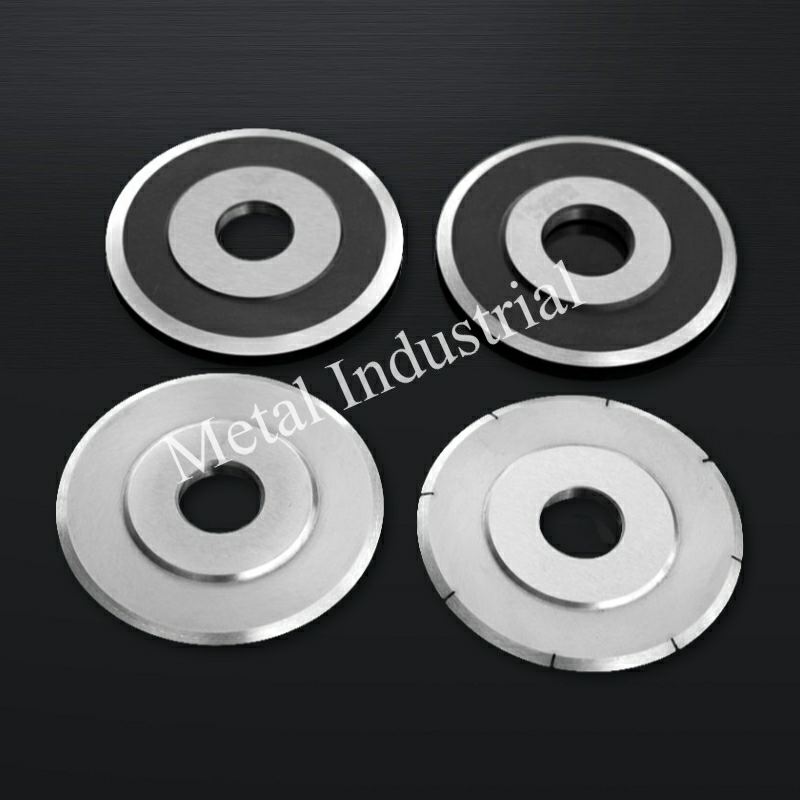
ब्लेड क्यों घिस जाते हैं?
ब्लेड के घिसने में कई कारक योगदान करते हैं:
- सामग्री कठोरता: कठोर पदार्थों को काटने से ब्लेड शीघ्र ही भोथरा हो सकता है।
- अनुचित संरेखण: गलत संरेखित ब्लेड असमान घिसाव पैदा करते हैं।
- अपर्याप्त रखरखाव: गंदगी, मलबा और जंग घिसाव को तेज करते हैं।
- अत्यधिक परिचालन गति: उच्च गति से गर्मी उत्पन्न होती है, जिससे ब्लेड की कठोरता और प्रदर्शन कम हो जाता है।
- ऑपरेटर त्रुटि: संचालन या भंडारण के दौरान गलत तरीके से संभालने से समय से पहले क्षति हो सकती है।
इन कारकों को समझना ब्लेड के जीवन को बढ़ाने की दिशा में पहला कदम है। इन चुनौतियों का सक्रिय रूप से समाधान करके, आप ब्लेड की दक्षता बनाए रख सकते हैं और डाउनटाइम को कम कर सकते हैं।
2. ब्लेड के घिसने और फटने की लागत
उत्पादकता और लाभप्रदता पर प्रभाव
घिसे हुए ब्लेड के कारण निम्नलिखित समस्याएं हो सकती हैं:
- डाउनटाइम: बार-बार ब्लेड बदलने से उत्पादन कार्यक्रम बाधित होता है।
- असंगत गुणवत्ता: कुंद ब्लेड असमान कटौती का कारण बनते हैं, जिसके परिणामस्वरूप उत्पाद अस्वीकृत हो जाता है और ग्राहक असंतुष्ट हो जाते हैं।
- उच्च लागत: नियमित ब्लेड प्रतिस्थापन से परिचालन व्यय में वृद्धि होती है, साथ ही प्रतिस्थापन के लिए शीघ्र शिपिंग या उत्पादन समय की हानि जैसी छिपी हुई लागतें भी होती हैं।
उदाहरण के लिए, निम्नलिखित डेटा पर विचार करें:
मीट्रिक | घिसे हुए ब्लेड | अनुरक्षित ब्लेड |
औसत डाउनटाइम (घंटे) | 12 | 4 |
मासिक प्रतिस्थापन लागत | $2,000 | $800 |
उत्पाद अस्वीकृति दर | 15% | 2% |
ये संख्याएँ खराब ब्लेड रखरखाव के महत्वपूर्ण वित्तीय प्रभाव को दर्शाती हैं। निवारक उपायों में निवेश करने से समय के साथ काफी बचत हो सकती है।
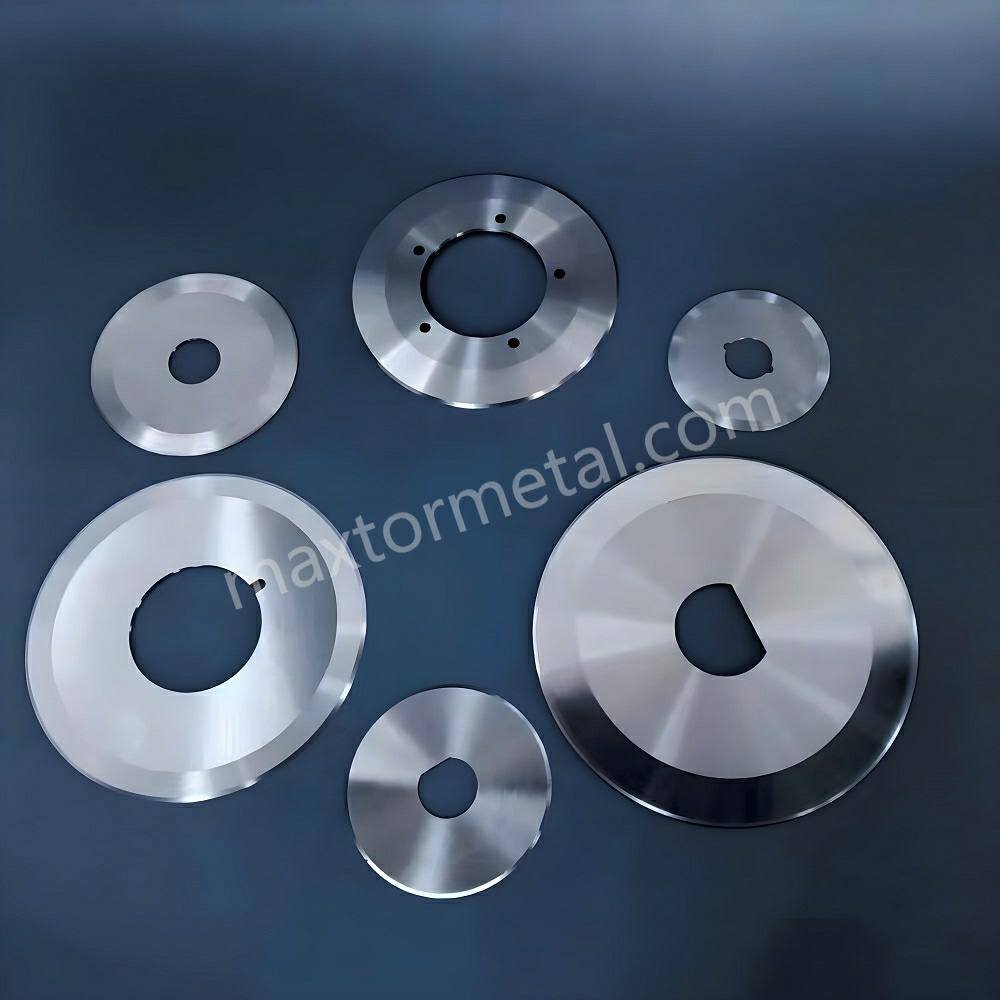
पर्यावरण संबंधी विचार
त्यागे गए ब्लेड इसमें योगदान करते हैं औद्योगिक कूड़ाउचित देखभाल के माध्यम से उनके जीवनकाल को बढ़ाने से अपशिष्ट कम होता है और स्थिरता लक्ष्यों के साथ संरेखित होता है। यह एक पर्यावरण के प्रति जागरूक कंपनी के रूप में आपकी ब्रांड प्रतिष्ठा को भी बढ़ा सकता है, जो आज के बाजार में एक महत्वपूर्ण कारक है।
जो कंपनियां ब्लेड की दीर्घायु संबंधी प्रथाओं को लागू करती हैं, वे न केवल पैसा बचाती हैं, बल्कि अपने पर्यावरणीय पदचिह्न को न्यूनतम करते हुए, हरित भविष्य में भी योगदान देती हैं।
3. जीवनकाल बढ़ाने के लिए सर्वोत्तम अभ्यास डिस्क स्लिटिंग ब्लेड
नियमित रखरखाव
ब्लेड की तीक्ष्णता बनाए रखने और नुकसान को रोकने के लिए नियमित रखरखाव बहुत ज़रूरी है। यहाँ कुछ ज़रूरी कदम दिए गए हैं:
- सफाई: प्रत्येक उपयोग के बाद किसी गैर-संक्षारक विलायक से मलबे और अवशेषों को हटाएँ। यह जमाव को रोकता है जो ब्लेड को सुस्त कर सकता है।
- निरीक्षण: खरोंच, चिप्स या असमान घिसाव के लिए प्रतिदिन जाँच करें। छोटी-मोटी समस्याओं को समय रहते पहचान लेने से बाद में बड़ी समस्याओं से बचा जा सकता है।
- स्नेहन: घर्षण और जंग को कम करने के लिए उपयुक्त स्नेहक का उपयोग करें, जिससे सुचारू संचालन सुनिश्चित हो सके।
- दस्तावेज़ीकरण: पैटर्न की पहचान करने और समय पर देखभाल निर्धारित करने के लिए ब्लेड के उपयोग और रखरखाव का लॉग बनाए रखें।
उचित भंडारण और हैंडलिंग
भंडारण की स्थिति ब्लेड के स्थायित्व को महत्वपूर्ण रूप से प्रभावित कर सकती है। इन सुझावों का पालन करें:
- शुष्क वातावरण: जंग और क्षरण को रोकने के लिए ब्लेड को नमी रहित स्थान पर रखें।
- सुरक्षात्मक मामले: भंडारण या परिवहन के दौरान आकस्मिक क्षति से बचने के लिए ब्लेड कवर या केस का उपयोग करें।
- संगठित भंडारण: पुनः प्राप्ति के दौरान खरोंचों से बचने के लिए ब्लेडों को व्यवस्थित रूप से व्यवस्थित करें, आदर्शतः समर्पित भंडारण रैक में।
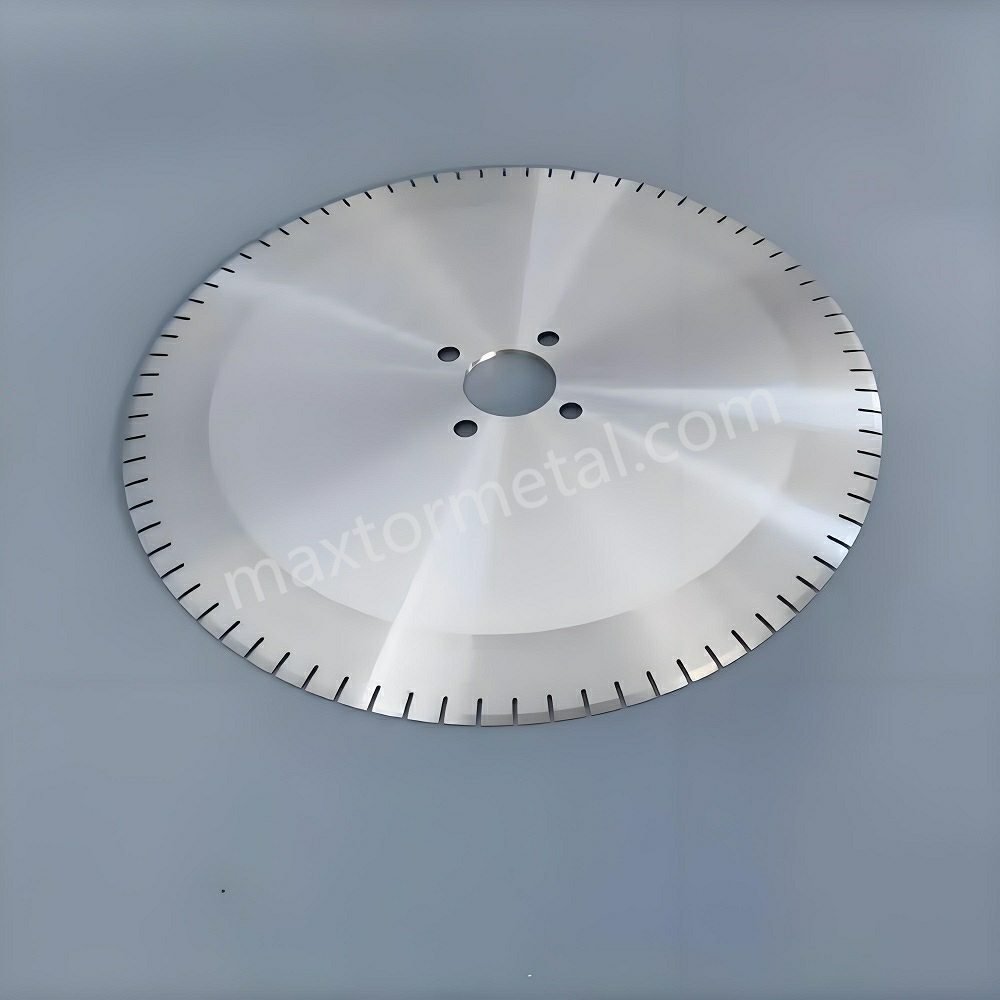
सामग्री संगतता
किसी खास सामग्री के लिए गलत ब्लेड का इस्तेमाल करने से वह जल्दी घिस सकता है। सुनिश्चित करें कि:
- ब्लेड को सामग्री की कठोरता और मोटाई के अनुसार डिज़ाइन किया जाता है।
- इस कार्य के लिए उचित किनारा प्रोफाइल (जैसे, दाँतेदार बनाम चिकना) का उपयोग किया जाता है।
- इष्टतम प्रदर्शन के लिए निर्माताओं के दिशानिर्देशों का पालन किया जाता है।
कार्य के लिए सही ब्लेड का चयन करने से उपकरण पर अनावश्यक दबाव को रोका जा सकता है, तथा इसकी दीर्घायु बढ़ाई जा सकती है।
4. ब्लेड का जीवन बढ़ाने की उन्नत तकनीक
परिचालन स्थितियों का अनुकूलन
कटिंग पैरामीटर को समायोजित करने से टूट-फूट को कम किया जा सकता है। यहाँ बताया गया है कि कैसे:
- रफ़्तार: गर्मी के निर्माण को कम करने और ब्लेड को कमजोर होने से बचाने के लिए ब्लेड की गति को सामग्री के प्रकार के साथ मिलाएं।
- दबाव: ब्लेड के विरूपण या दरार को रोकने के लिए अत्यधिक दबाव से बचें।
- संरेखण: सुनिश्चित करें कि ब्लेड पूरी तरह से संरेखित हों, ताकि असमान कट से स्थानीय स्तर पर घिसाव न हो।
ऑपरेटरों को इष्टतम सेटिंग्स को पहचानने के लिए प्रशिक्षण प्राप्त करना चाहिए, क्योंकि मामूली समायोजन ब्लेड के स्थायित्व पर महत्वपूर्ण प्रभाव डाल सकते हैं।
पैनापन और पुनः सतहीकरण
नियमित रूप से धार लगाने से ब्लेड की धार फिर से तेज हो जाती है और उपयोगिता बढ़ जाती है। पेशेवर रीसर्फेसिंग सेवाएँ निम्न कर सकती हैं:
- सूक्ष्म क्षति को दूर करें.
- एज प्रोफाइल को नई जैसी स्थिति में पुनः स्थापित करें।
- काटने की दक्षता में सुधार, कटौती के लिए आवश्यक बल को कम करना।
सामग्री की कठोरता और उपयोग की आवृत्ति के आधार पर, हर 500-1,000 कट के बाद ब्लेड को तेज़ करें। अधिक उपयोग को रोकने के लिए तेज़ करने के अंतराल का रिकॉर्ड रखें।
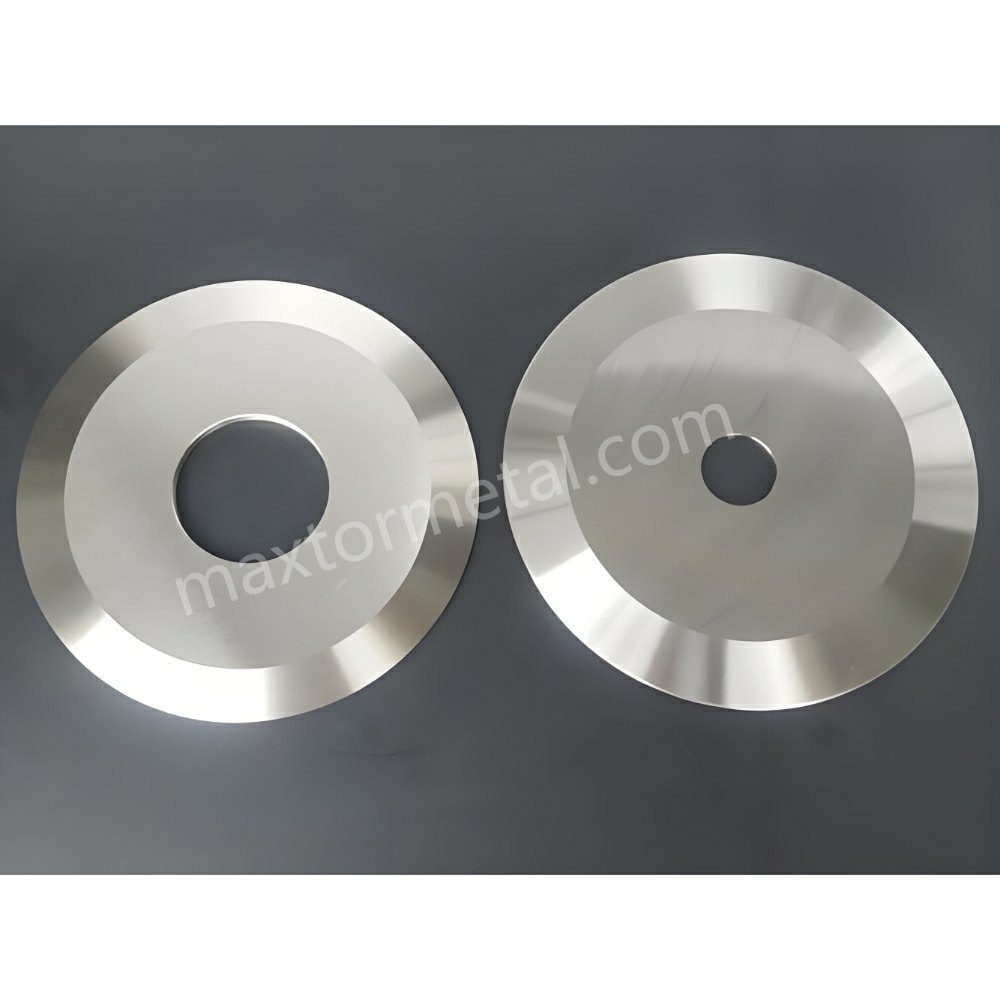
5. उच्च गुणवत्ता वाले ब्लेड का चयन
ब्लेड की गुणवत्ता क्यों मायने रखती है
उच्च गुणवत्ता वाले ब्लेड लंबे समय तक चलते हैं और बेहतर प्रदर्शन करते हैं। मुख्य विशेषताओं में शामिल हैं:
- सामग्री की संरचना: उच्च श्रेणी के स्टील या कार्बाइड से बने ब्लेड घिसाव का प्रतिरोध करते हैं तथा लम्बे समय तक तीखे बने रहते हैं।
- सूक्ष्मता अभियांत्रिकी: एकसमान किनारें लगातार कट सुनिश्चित करते हैं, जिससे ब्लेड पर तनाव कम होता है।
- कोटिंग्स: टाइटेनियम नाइट्राइड जैसे सुरक्षात्मक कोटिंग्स स्थायित्व को बढ़ाते हैं और घर्षण को कम करते हैं।
उच्च गुणवत्ता वाले ब्लेड में निवेश करने से विश्वसनीयता सुनिश्चित होती है और दीर्घकालिक लागत कम होती है।
विश्वसनीय निर्माता बनाम सामान्य विकल्प
सामान्य ब्लेड लागत-प्रभावी लग सकते हैं, लेकिन अक्सर:
- जल्दी खराब हो जाते हैं, जिससे बार-बार बदलने की जरूरत पड़ती है।
- असंगत प्रदर्शन, जिससे उत्पाद की गुणवत्ता खतरे में पड़ जाती है।
- निर्माता समर्थन या वारंटी का अभाव।
ब्लेड का चयन प्रतिष्ठित निर्माता गुणवत्ता, स्थिरता और समस्या निवारण के लिए समर्थन का आश्वासन प्रदान करता है।
6. वास्तविक दुनिया के उदाहरण और केस स्टडीज़
ब्लेड की बेहतर दीर्घायु की सफलता की कहानियाँ
- केस स्टडी 1: कंपनी ए ने नियमित रखरखाव लागू किया और ब्लेड बदलने की आवृत्ति को 40% तक कम कर दिया, जिससे सालाना $15,000 की बचत हुई।
- केस स्टडी 2: कंपनी बी ने उच्च गुणवत्ता वाले स्लिटर ब्लेड अपनाए, जिससे अस्वीकृति दर में 13% की कमी आई तथा ग्राहक संतुष्टि में वृद्धि हुई।
ये उदाहरण इस बात पर प्रकाश डालते हैं कि कैसे साधारण परिवर्तन से महत्वपूर्ण लागत बचत और दक्षता में वृद्धि हो सकती है।
सीख सीखी
- नियमित ब्लेड निरीक्षण महंगी विफलताओं को रोकता है।
- ब्लेड की देखभाल पर कर्मचारियों को प्रशिक्षण देने से परिचालन परिणामों में सुधार होता है।
- विश्वसनीय निर्माताओं के साथ साझेदारी करने से गुणवत्तापूर्ण उत्पादों और विशेषज्ञ सलाह तक पहुंच सुनिश्चित होती है।
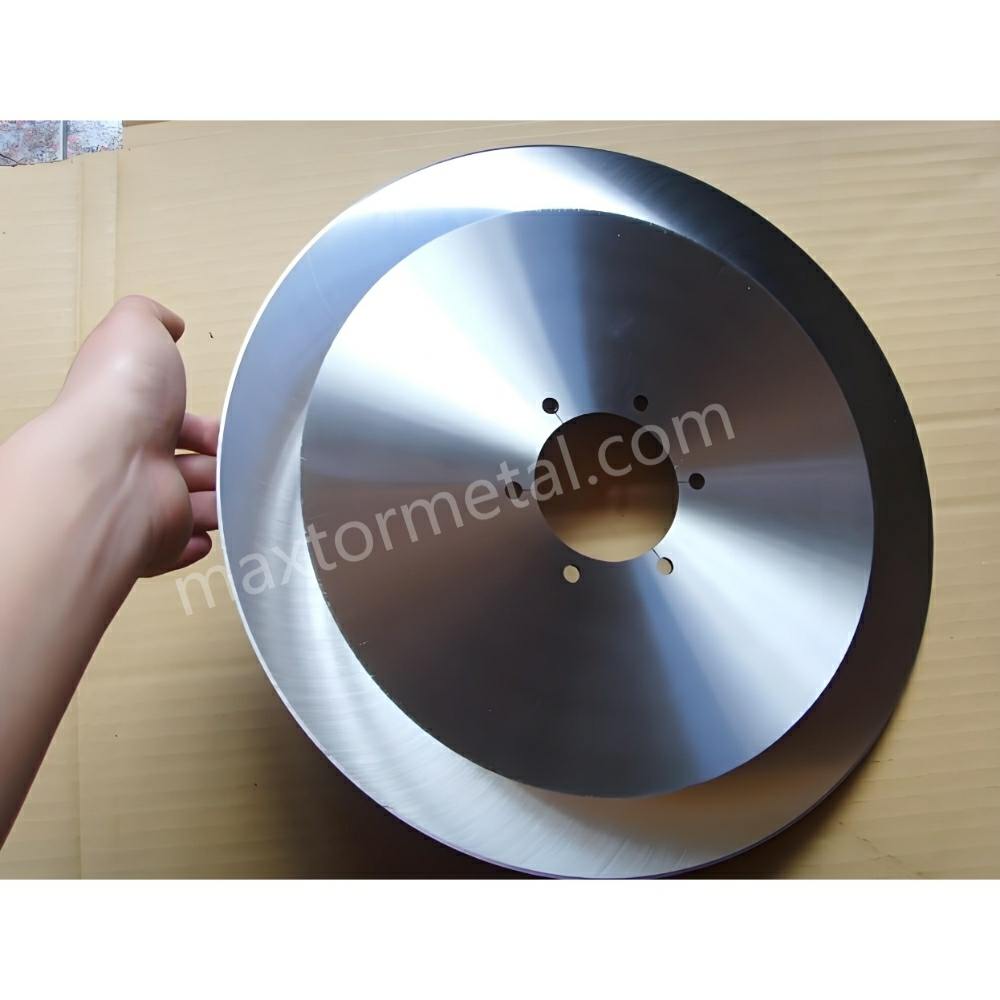
7. अक्सर पूछे जाने वाले प्रश्न (एफएक्यू)
मुझे अपने डिस्क स्लिटिंग ब्लेड को कितनी बार तेज करना चाहिए?
हर 500-1,000 कट या जब प्रदर्शन में गिरावट आए, तब ब्लेड को तेज़ करें। उपयोग और तेज़ करने के शेड्यूल का रिकॉर्ड रखने से लगातार प्रदर्शन सुनिश्चित करने में मदद मिलती है।
भंडारण का सबसे अच्छा तरीका क्या है? गोलाकार स्लिटिंग ब्लेड?
उन्हें सुरक्षात्मक कवर के साथ सूखी, व्यवस्थित स्थितियों में स्टोर करें। लंबे समय तक भंडारण के लिए, जंग और क्षरण को रोकने के लिए जलवायु-नियंत्रित वातावरण पर विचार करें।
क्या मैं क्षतिग्रस्त ब्लेडों की मरम्मत कर सकता हूँ या उन्हें बदल देना चाहिए?
मामूली क्षति को पुनः सतह बनाने के माध्यम से ठीक किया जा सकता है; गंभीर रूप से खराब हो चुके ब्लेड को बदलें। ब्लेड की उपयोगिता का आकलन करने के लिए मरम्मत सेवाओं के लिए किसी पेशेवर से परामर्श लें।
वे कौन से संकेत हैं जिनसे पता चलता है कि ब्लेड को बदलने की जरूरत है?
- धार लगाने के बावजूद बार-बार फीकापन आना।
- दिखाई देने वाली चिप्स या दरारें.
- असंगत कटौती.
- परिचालन के दौरान कंपन या शोर में वृद्धि, जो असंतुलन या संरचनात्मक क्षति का संकेत हो सकता है।
मैं अपनी सामग्री के लिए सही ब्लेड की पहचान कैसे कर सकता हूँ?
प्रत्येक सामग्री को विशिष्ट ब्लेड गुणों की आवश्यकता होती है। सामग्री काटने गाइड या निर्माताओं से संपर्क करें ताकि वे आपकी आवश्यकताओं के अनुसार ब्लेड की कठोरता, किनारे की रूपरेखा और मोटाई का मिलान कर सकें।
डिस्क स्लिटिंग ब्लेड का सामान्य जीवनकाल कितना होता है?
जीवनकाल सामग्री, उपयोग और रखरखाव के आधार पर अलग-अलग होता है, लेकिन आम तौर पर निरंतर औद्योगिक अनुप्रयोगों में यह कई सप्ताह से लेकर महीनों तक होता है।
क्या ब्लेड की अनुचित स्थापना से प्रदर्शन प्रभावित हो सकता है?
हां, गलत तरीके से इंस्टॉलेशन करने से गलत संरेखण और असमान घिसाव होता है, जिससे प्रदर्शन और दीर्घायु दोनों कम हो जाते हैं। इंस्टॉलेशन के लिए हमेशा निर्माता के दिशा-निर्देशों का पालन करें या किसी पेशेवर से सलाह लें।
क्या विशिष्ट अनुप्रयोगों के लिए विशेष कोटिंग्स उपलब्ध हैं?
हां, टाइटेनियम नाइट्राइड या हीरा-जैसे कार्बन जैसे कोटिंग्स घर्षण को कम कर सकते हैं, कठोरता बढ़ा सकते हैं, और धातु या उच्च घर्षण सामग्री जैसे विशेष अनुप्रयोगों के लिए काटने के प्रदर्शन में सुधार कर सकते हैं।
8. निष्कर्ष
अपने जीवन काल को बढ़ाना डिस्क स्लिटिंग ब्लेड नियमित रखरखाव, उचित उपयोग और गुणवत्ता वाले उत्पादों में निवेश के माध्यम से इसे प्राप्त किया जा सकता है। इस गाइड में बताई गई रणनीतियों का पालन करके, आप उत्पादकता में सुधार कर सकते हैं, लागत कम कर सकते हैं और उत्पाद की गुणवत्ता बढ़ा सकते हैं।
अपनी कटिंग प्रक्रियाओं को अनुकूलित करने के लिए तैयार हैं? उच्च प्रदर्शन वाले औद्योगिक ब्लेड की हमारी रेंज का पता लगाएं या हमारे विशेषज्ञों से संपर्क करें अनुकूलित समाधान के लिए।