सारांश
प्रेस ब्रेक पंच और मर जाता है सटीक धातु निर्माण के लिए महत्वपूर्ण हैं, लेकिन घिसाव और क्षति प्रदर्शन को प्रभावित कर सकती है और लागत बढ़ा सकती है। यह मार्गदर्शिका सामान्य घिसाव के प्रकारों, उत्पादन पर उनके प्रभाव और प्रभावी मरम्मत और रखरखाव समाधानों की पड़ताल करती है। अपने टूलींग के जीवन को बढ़ाने और डाउनटाइम को कम करने के लिए व्यावहारिक रणनीतियाँ सीखें।
परिचय: रखरखाव का महत्व प्रेस ब्रेक टूलिंग
प्रेस ब्रेक पंच और डाई धातु निर्माण के आवश्यक घटक हैं, जो शीट मेटल में सटीक और सुसंगत मोड़ सुनिश्चित करते हैं। हालांकि, बार-बार उपयोग और अनुचित हैंडलिंग से घिसाव और टूट-फूट हो सकती है, जिससे उत्पादन की गुणवत्ता और दक्षता पर नकारात्मक प्रभाव पड़ सकता है। घिसाव के कारणों को समझना और अपने टूलींग की मरम्मत या रखरखाव करने का तरीका जानना समय और पैसे बचा सकता है, साथ ही परिचालन परिणामों में सुधार कर सकता है।
यह गाइड प्रेस ब्रेक टूलिंग द्वारा सामना किए जाने वाले आम घिसाव के मुद्दों, उनके प्रभावों और कार्रवाई योग्य मरम्मत रणनीतियों पर गहराई से चर्चा करता है। चाहे आप अपने औजारों के जीवन को बढ़ाना चाहते हों या उत्पादन को अनुकूलित करना चाहते हों, यह लेख आपकी ज़रूरतों के अनुरूप व्यावहारिक समाधान प्रदान करता है।
प्रेस ब्रेक पंच और डाइज़ में पहनने के सामान्य प्रकार
1. उपकरण के खराब होने के कारण
धातु निर्माण के दौरान उपकरण का घिसना अपरिहार्य है। हालाँकि, इसके कारणों को समझने से इसके प्रभाव को कम करने में मदद मिल सकती है:
- बार-बार तनाव: हर ऑपरेशन में घर्षण और दबाव शामिल होता है। समय के साथ, यह टूलिंग सामग्री को कमज़ोर कर देता है, ख़ास तौर पर उच्च-उत्पादन वाले वातावरण में। अध्ययनों से पता चलता है कि 24/7 ऑपरेशन में इस्तेमाल किए जाने वाले उपकरण रुक-रुक कर इस्तेमाल किए जाने वाले उपकरणों की तुलना में 30% तक तेज़ी से ख़राब होते हैं।
- सामग्री प्रबंधन त्रुटियाँऔजारों का गलत इस्तेमाल या शीट धातु की गलत स्थिति के कारण असमान दबाव बिंदु उत्पन्न हो सकते हैं, जिससे विरूपण या टूट-फूट हो सकती है।
- गलत टन भारअनुशंसित सीमा से ज़्यादा टन भार का उपयोग करने से घिसाव तेज़ हो जाता है। शोध से पता चलता है कि किसी उपकरण के अधिकतम टन भार को 20% से ज़्यादा करने से उसका जीवनकाल आधा हो सकता है।

2. पहनने के विशिष्ट प्रकार
विरूपण
विरूपण सुस्त या चपटे किनारों के रूप में दिखाई देता है, जो झुकने की सटीकता से समझौता करता है। यह समस्या तब उत्पन्न होती है जब उपकरण निरंतर उच्च दबाव का अनुभव करते हैं या स्टेनलेस स्टील जैसी कठोर सामग्रियों के साथ काम करते हैं। उदाहरण के लिए, अनुचित तरीके से संरेखित पंच केवल 100 चक्रों के बाद अपनी तीक्ष्णता का 10% खो सकते हैं।
खुर
अत्यधिक तनाव के अधीन औजारों में हेयरलाइन फ्रैक्चर बन सकते हैं। ये दरारें अक्सर छोटी शुरू होती हैं लेकिन समय के साथ बढ़ती जाती हैं, जिससे संभावित रूप से विनाशकारी विफलता हो सकती है। उच्च-तनाव झुकने वाले संचालन 40% द्वारा दरार की संभावना को बढ़ाते हैं, खासकर अगर टूलिंग सामग्री घटिया है।
जंग
जंग नमी, आर्द्रता या पर्यावरण में मौजूद कुछ रसायनों के संपर्क में आने से होती है। उदाहरण के लिए, नमी वाली जगहों पर रखे औजारों को अगर बिना उपचार के छोड़ दिया जाए तो वे एक साल के अंदर जंग लगने के कारण अपनी 15% तक की ताकत खो सकते हैं।
3. दृश्य संकेतक
जल्दी ही खराबी का पता लगाने से महत्वपूर्ण लागत बचाई जा सकती है:
- गोल किनारेऐसे मुक्कों की तलाश करें जो अब साफ मोड़ पैदा नहीं करते।
- दृश्यमान दरारेंहेयरलाइन फ्रैक्चर का पता लगाने के लिए उपकरणों का तेज रोशनी में निरीक्षण करें।
- सतह का रंग उड़नाजंग या धुंधले धब्बे अक्सर संक्षारण का संकेत देते हैं।
नियमित दृश्य निरीक्षण छोटी समस्याओं को बड़ी समस्या बनने से रोकने में मदद करता है।
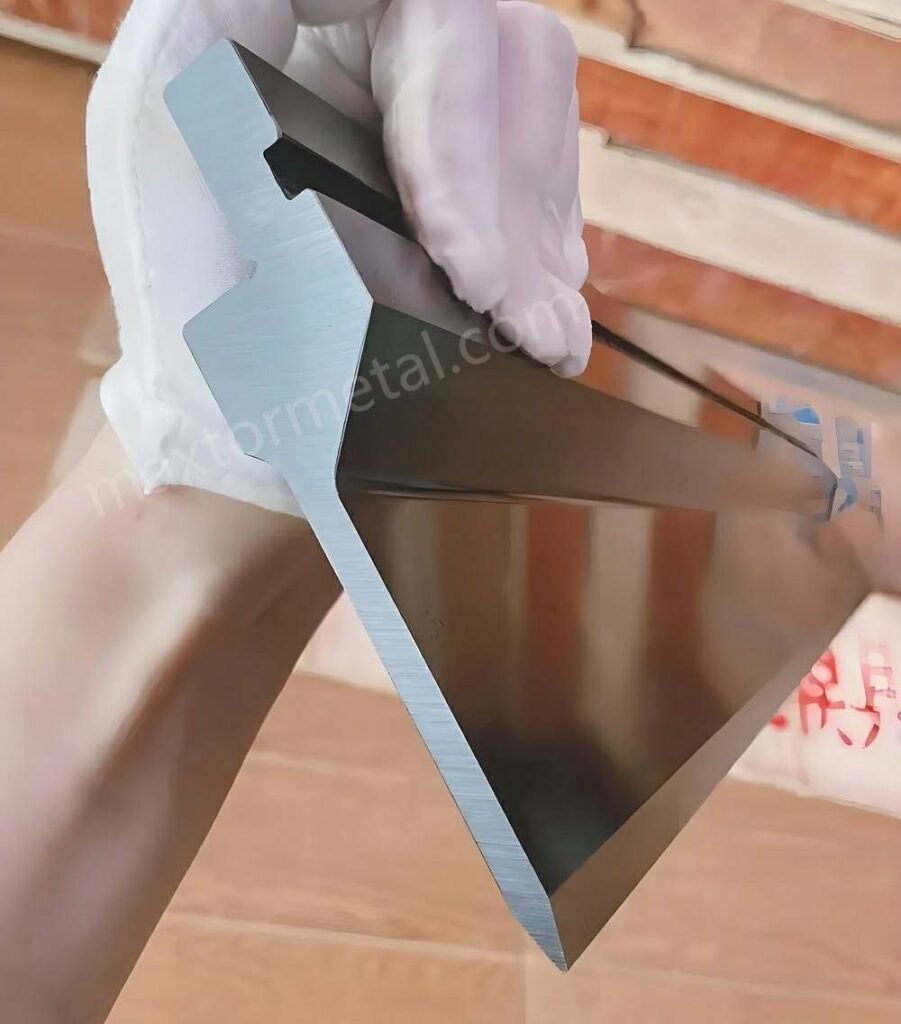
उत्पादन पर उपकरण के घिसाव का प्रभाव
1. गुणवत्ता संबंधी मुद्दे
घिसे हुए औजारों के कारण बेमेल या दोषपूर्ण मोड़ बनते हैं। उदाहरण के लिए, सुस्त पंच असमान कोण बना सकते हैं, जबकि फटी हुई डाई शीट मेटल पर निशान छोड़ सकती है। ऐसे दोषों के कारण अक्सर अस्वीकृत हिस्से बनते हैं, जिससे अपशिष्ट बढ़ता है और ऑर्डर में देरी होती है।
2. बढ़ी हुई लागत
परिचालन लागत में वृद्धि निम्नलिखित कारणों से होती है:
- बार-बार उपकरण बदलनाघिसे हुए औजारों को लगातार बदलने की जरूरत होती है, प्रत्येक सेट की कीमत हजारों डॉलर होती है।
- सामग्री अपशिष्टदोषपूर्ण उत्पाद महंगे कच्चे माल की बर्बादी करते हैं।
- स्र्कना: उपकरण विफलताएं उत्पादन को रोक सकती हैं। इंडस्ट्री वीक के एक अध्ययन के अनुसार, अनिर्धारित डाउनटाइम से निर्माताओं को औसतन नुकसान होता है $260,000 प्रति घंटा.
3. उपकरणों को होने वाले जोखिम
घिसे हुए या क्षतिग्रस्त उपकरणों का उपयोग करने से प्रेस ब्रेक पर ही तनाव बढ़ जाता है। उदाहरण के लिए, गलत तरीके से लगाए गए पंच और डाई मशीन के हाइड्रोलिक या यांत्रिक घटकों को नुकसान पहुंचा सकते हैं, जिससे महंगी मरम्मत या कम जीवनकाल हो सकता है।
उपकरण के खराब होने की समस्या का सक्रियतापूर्वक समाधान करके, कंपनियां इन क्रमिक समस्याओं से बच सकती हैं।
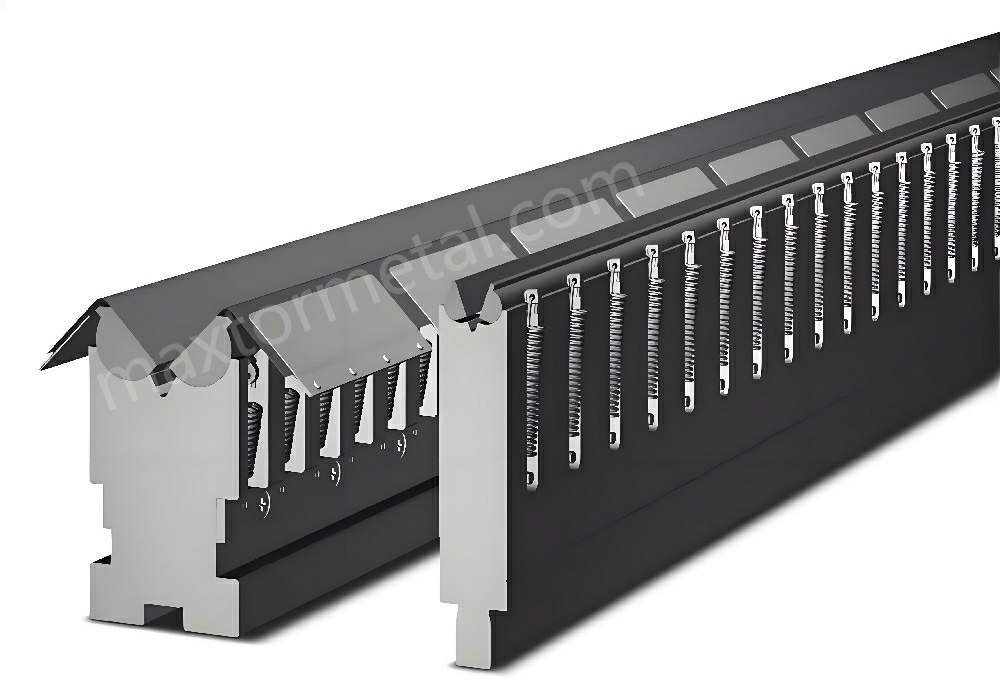
प्रभावी मरम्मत और रखरखाव समाधान
1. सामान्य मरम्मत विधियाँ
पीसना और पुनः तेज करना
पुनः तीक्ष्णता से धार की सटीकता बहाल होती है, झुकने की सटीकता में सुधार होता है। एक अच्छी तरह से तीक्ष्ण किया गया पंच कई चक्रों तक नए जैसा प्रदर्शन कर सकता है। अध्ययनों से पता चलता है कि पुनः तीक्ष्ण किए गए उपकरण प्राप्त कर सकते हैं 90% उनके मूल प्रदर्शन का, जिससे उनकी उपयोगिता बढ़ जाती है।
उष्मा उपचार
गर्मी उपचार घिसे हुए औजारों की सतह को फिर से सख्त करके उन्हें मजबूत बनाता है। यह विधि उन औजारों के लिए विशेष रूप से प्रभावी है जो बिना दरार के मध्यम घिसे हुए हैं।
वेल्डिंग मरम्मत
दरारों या फ्रैक्चर के लिए, वेल्डिंग एक विश्वसनीय समाधान है। दरारें भरने के बाद, तकनीशियन सुचारू संचालन सुनिश्चित करने के लिए सतह को पीसते और पॉलिश करते हैं।
2. रखरखाव युक्तियाँ
सक्रिय रखरखाव पहनने को काफी कम कर देता है:
- नियमित निरीक्षणसाप्ताहिक या प्रत्येक 50 चक्र के बाद दृश्य और स्पर्श जांच कराएं।
- उचित सफाई: मलबे को हटाने और जंग को रोकने के लिए औजारों को रोज़ाना साफ करें। अतिरिक्त सुरक्षा के लिए गैर-संक्षारक स्नेहक का उपयोग करें।
- संरेखण जाँचदबाव को समान रूप से वितरित करने के लिए प्रत्येक ऑपरेशन से पहले सुनिश्चित करें कि पंच और डाई पूरी तरह से संरेखित हैं।
3. कब बदलें या कब मरम्मत करें
कभी-कभी, उपकरणों को बदलना उनकी मरम्मत करने से ज़्यादा किफ़ायती होता है। उदाहरण के लिए, अगर पंच की सतह पर दरारें 30% से ज़्यादा हैं या विरूपण निर्माता की सहनशीलता से ज़्यादा है, तो प्रतिस्थापन से लगातार प्रदर्शन सुनिश्चित होता है।
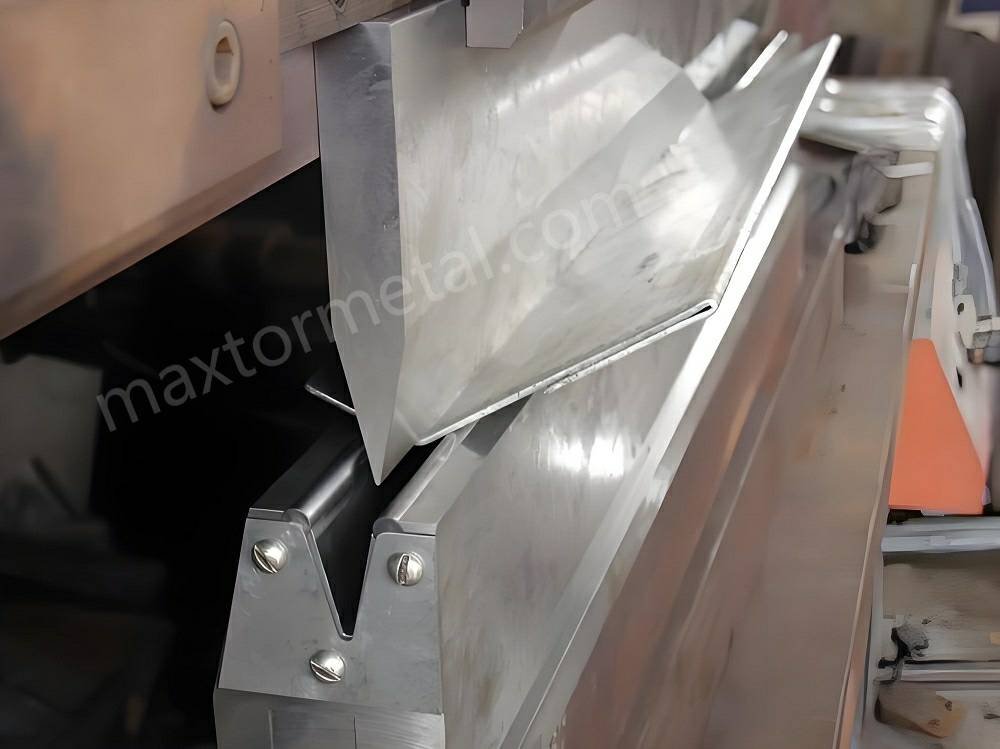
सही सेवा प्रदाता या प्रतिस्थापन उपकरण चुनना
1. विश्वसनीय प्रदाताओं के मुख्य गुण
ऐसे आपूर्तिकर्ताओं की तलाश करें जो निम्नलिखित पेशकश करते हों:
- उच्च परिशुद्धता मानकसख्त सहनशीलता के साथ निर्मित उपकरण लंबे समय तक चलते हैं और बेहतर प्रदर्शन करते हैं।
- अनुकूलन: अनुकूलित समाधान विशिष्ट झुकने की आवश्यकताओं को पूरा करते हैं।
- तकनीकी समर्थनसलाह और मरम्मत सेवाएं प्रदान करने वाले प्रदाता प्रारंभिक खरीद से परे मूल्य जोड़ते हैं।
2. विशेषज्ञ सहायता के लाभ
अनुभवी प्रदाता आपको सबसे अच्छे मरम्मत या प्रतिस्थापन विकल्पों की पहचान करने में मदद कर सकते हैं। वे दीर्घकालिक विश्वसनीयता सुनिश्चित करने के लिए वारंटी या रखरखाव योजनाएँ भी प्रदान कर सकते हैं।
3. आपूर्तिकर्ताओं का मूल्यांकन
आपूर्तिकर्ताओं का मूल्यांकन करते समय, निम्नलिखित बातों पर विचार करें:
- प्रमाणपत्रआईएसओ या समकक्ष प्रमाणपत्र की तलाश करें।
- ग्राहक समीक्षासकारात्मक प्रतिक्रिया विश्वसनीयता दर्शाती है।
- मामले का अध्ययनसिद्ध परिणाम आपूर्तिकर्ता की विशेषज्ञता को प्रदर्शित करते हैं।
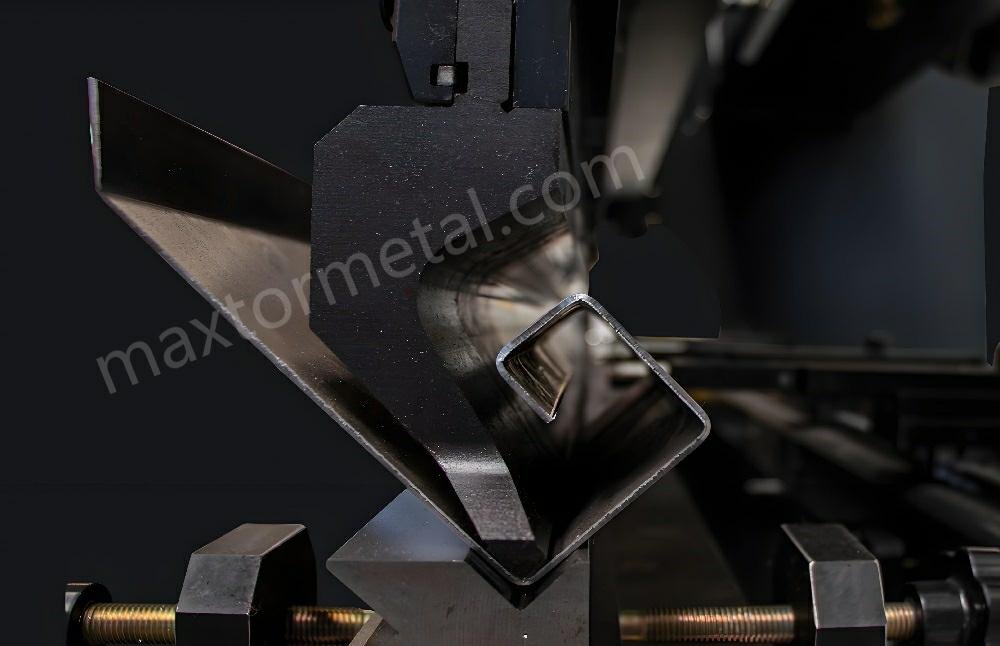
प्रभावी टूलींग प्रबंधन के लिए अतिरिक्त जानकारी
केस स्टडी: उपकरण का जीवनकाल बढ़ाने में सफलता
एक मध्यम आकार की शीट धातु निर्माण कंपनी ने अपने उत्पादों के लिए द्वि-साप्ताहिक शार्पनिंग और संरेखण जांच लागू की। प्रेस ब्रेक पंच और मर जाता हैछह महीने के भीतर, उन्होंने टूलिंग लागत में 25% की कमी की और उत्पादन दक्षता में 15% की वृद्धि की। इस सरल रणनीति ने डाउनटाइम को टाला और अनावश्यक प्रतिस्थापन को समाप्त किया।
FAQ
औजारों का कितनी बार निरीक्षण किया जाना चाहिए?
औजारों का निरीक्षण, उनकी उपयोग तीव्रता के आधार पर, कम से कम महीने में एक बार या प्रत्येक 50 उत्पादन चक्रों के बाद करें।
पंच और डाई के लिए कौन सी सामग्री सर्वोत्तम है?
हाई-कार्बन स्टील और टूल स्टील सबसे ज़्यादा टिकाऊ होते हैं। वे घिसाव, विरूपण और दरार के प्रति बेहतरीन प्रतिरोध प्रदान करते हैं।
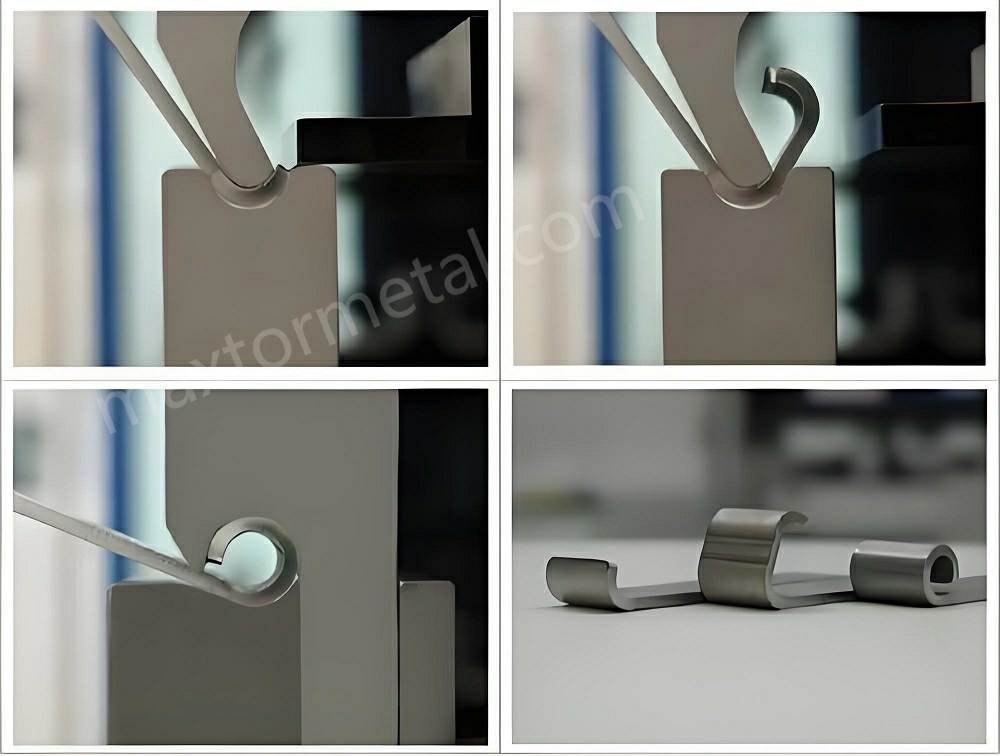
विज़ुअल गाइड: पहनने और मरम्मत के तरीके
एक इन्फोग्राफिक दृश्य रूप से निम्न का प्रतिनिधित्व कर सकता है:
- गोल किनारे → पीसना और तेज करना।
- दरारें → वेल्डिंग और पॉलिशिंग.
- जंग → सफाई और स्नेहन.
इन दृश्यों से टीमों के लिए पहनने संबंधी समस्याओं की पहचान करना और उनका कुशलतापूर्वक समाधान करना आसान हो जाता है।
निष्कर्ष: अपने अनुकूलन के लिए कार्रवाई करें प्रेस ब्रेक टूलिंग
प्रेस ब्रेक पंच और डाई सटीक धातु निर्माण की रीढ़ हैं। उन्हें ठीक से बनाए रखने से लगातार उत्पादन गुणवत्ता सुनिश्चित होती है, लागत कम होती है और डाउनटाइम से बचा जा सकता है। आम घिसाव पैटर्न को पहचानकर, समय पर मरम्मत करके और रखरखाव के सर्वोत्तम तरीकों का पालन करके, आप अपने टूलिंग के जीवनकाल को अधिकतम कर सकते हैं।
क्या आप अपने प्रेस ब्रेक टूलींग का जीवन बढ़ाने के लिए तैयार हैं? आज ही हमसे संपर्क करेंय विशेषज्ञ मरम्मत सेवाओं या उच्च गुणवत्ता वाले प्रतिस्थापन का पता लगाने के लिए। हमारी टीम आपकी उत्पादन प्रक्रिया को अनुकूलित करने और विश्वसनीय परिणाम प्राप्त करने में आपकी सहायता करने के लिए यहाँ है।
3 प्रतिक्रियाएं
इस वेबसाइट पर वास्तव में वह सारी जानकारी और तथ्य मौजूद हैं जिनकी मुझे इस विषय पर आवश्यकता थी और मैं नहीं जानता था कि किससे पूछूं।
इस वेबसाइट में वास्तव में वह सारी जानकारी और तथ्य हैं जिनकी मुझे आवश्यकता थी
विषय के बारे में मुझे कुछ समझ नहीं आया और मुझे नहीं पता था कि किससे पूछूं।