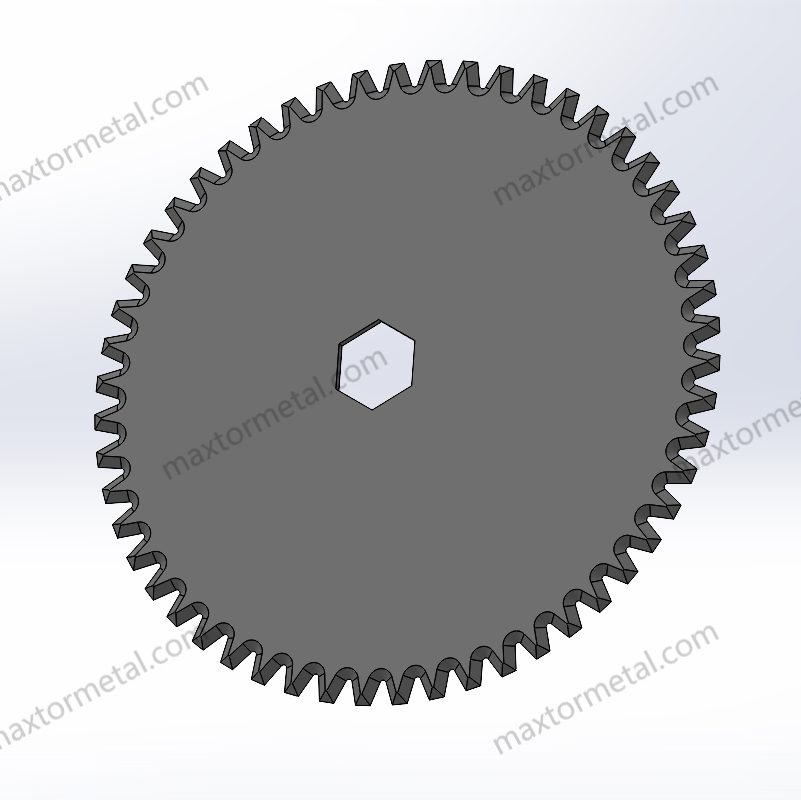
When you choose the right pisau lingkaran for your job, you make your work smoother and your results better. The correct circular knives help you get uniform cuts every time. This means your products look the same and you waste less material. Many industries use circular knives for tasks like slitting, trimming, or perforating. You should think about what you need to cut, how much you need to produce, and how to keep your team safe. Custom circular knives from Maxtor Metal can match your exact cutting needs, giving you longer-lasting blades and higher quality with every cut.
Poin-poin Utama
- Pick a circular knife that fits what you cut. This helps you get clean cuts and makes the blade last longer. Choose the right blade material, edge, and thickness for your needs. Think about how much you need to cut. Use safety features and handle the knife the right way. This keeps you safe and helps you work better. Custom blades can help with special jobs. They can make your cuts better and waste less material. Do not make mistakes like using the wrong blade. Do not forget about safety or pick the wrong size. This will help you save time and money.
Identify Your Cutting Application
To pick the right circular knives, you must know what you are cutting. Every material and job is different. You need to match the blade to your material and how thick it is. Think about how exact you want your cuts. This helps you get good results and keep your work at a high level.
Jenis Material
Circular knives can cut many kinds of materials. Each material acts differently when you cut it. This changes what kind of blade you need.
Kertas dan Karton
People use circular knives to cut paper and cardboard. If your blade is dull, the paper can rip or fray. A sharp edge gives you a smooth, clean cut. In fast factories, keeping the blade sharp is important. This helps you waste less and makes your products look the same.
Films and Foils
Films and foils are thin and bend easily. They can stretch or wrinkle when you cut them. You need a very sharp blade for these. This stops the material from getting messed up. Being exact is important, especially for packaging or electronics.
Tekstil dan Kain
Textiles and fabrics can come apart or bunch up. Special blades with teeth help stop this. For crush cut jobs, you might need a blade with a special tooth shape. This helps you cut all kinds of fabric well. You get a nice finish and good quality.
Rubber and Plastics
Rubber and plastics are strong and sometimes stretchy. You need a tough blade that does not wear out fast. The right blade shape helps you cut these without losing sharpness. Some plastics need a crush cut so they do not melt or stick.
Metal
Cutting metals is hard and needs a strong blade. You need circular knives made from tough materials like tungsten carbide or high-speed steel. These blades stay sharp and cut well, even in tough jobs.
Food Products
Food cutting needs blades that are safe and clean. You do not want to crush or dirty the food. Stainless steel circular knives are easy to clean and work well. For bread or meat, sharp blades help you cut cleanly without hurting the food.
Tip: Always pick a blade material that matches your product. This keeps your cuts good and your blade lasting longer.
Here is a table that shows different materials and their cutting problems:
Bahan | Common Use in Circular Knives | Unique Cutting Challenges and Properties |
---|---|---|
Baja Karbon Tinggi | Pisau industri | Strong, good edge retention; can chip if dropped |
1075/1095 Spring Steel | Disposable/thin blades | Durable, hard, precise cuts, affordable |
Besi tahan karat | Moisture-exposed environments | Rust resistant, needs careful sharpening |
Keramik | Medical, electronics, films | Extremely hard, corrosion resistant, brittle |
Solid Carbide | Precision industrial uses | Very hard, minimal binding, long edge life |
52100 Steel | Industrial, low moisture | High wear resistance, good edge retention |
M-2 High-Speed Steel | Heat/abrasion environments | High abrasion and heat resistance |
D-2 Tool Steel | Durable, corrosion resistant | Strong edge retention, heat resistant |
CPM 10V | High-impact cutting tools | High wear resistance, versatile |
8670 Carbon Alloy | Thicker blades | Hard, tough, high wear resistance |
Thickness and Density
How thick and dense your material is matters a lot. You need to pick the right blade thickness and type for the best cut.
Thin Materials
Thin things like films and foils need very sharp blades. Thin blades (about 0.4 mm) cut fast and waste less. But you may need to fix them more often. The right blade gives you clean cuts and less mess.
Medium-Thickness Materials
Paper and textiles are in the middle. You need a blade that is sharp but also lasts long. A medium blade works well here. It gives you good speed and lasts longer.
Thick or Dense Materials
Rubber, plastics, and metals are thick and hard. You need a strong blade that does not wear out fast. Thicker blades last longer and cut tough stuff better. But they might cut slower and waste more. The harder the material, the stronger your blade should be.
Here is a table to show how blade thickness changes your cutting:
Ketebalan Bilah | Kecepatan memotong | Waktu senggang | Sampah Material |
---|---|---|---|
Thin (~0.4 mm) | Cepat | Lebih tinggi | Rendah |
Sedang | Balanced | Sedang | Sedang |
Thick (1.0 mm+) | Lebih lambat | Lebih rendah | Lebih tinggi |
Catatan: Always match your blade thickness and type to your material. This keeps your machines safe and your cuts looking good.
Kebutuhan Presisi
How exact you need your cuts is very important. This changes what circular knives, blade material, and edge you pick.
Pemotongan Presisi Tinggi
Some jobs, like electronics or medical tools, need very exact cuts. You need blades made from tungsten carbide or ceramic. These blades stay sharp and cut very well. Special ways of making blades, like water jet or laser, help make blades that fit your needs.
Standard Cutting
For most jobs, you do not need super exact cuts. Regular circular knives made from high carbon steel or stainless steel work fine. These blades are fast, last long, and cut well.
Specialty Finishes
Some jobs need a special look or almost no rough edges. You might need a custom blade shape or a coating like Titanium Nitride. These coatings can make your blade last up to 40% longer. Special tooth shapes, like high-low or scalloped, help you get the cut you want.
Taking care of your blades keeps them sharp and your cuts exact. This means less time fixing things and better quality every time.
Being exact with circular knives is important for clean cuts and good work. The right blade material, tooth shape, and coating all help you get the precision you need.
Key Features of Circle Knives
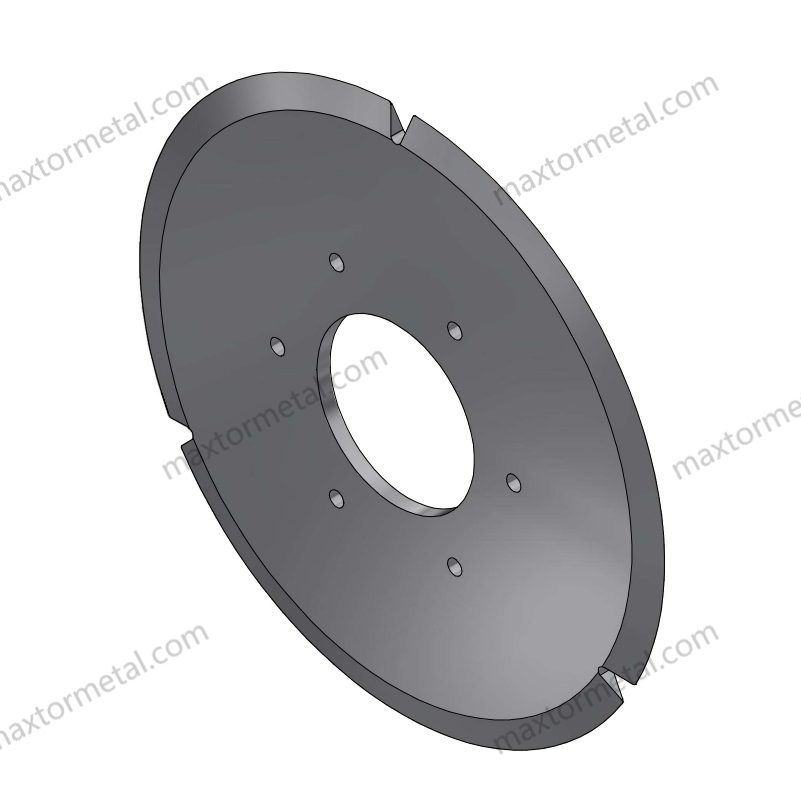
When you pick circular knives, you should check some main features. These features help you do your cutting jobs well. The right blade, edge type, size, and safety design all matter for how your industrial knife works.
Bahan Pisau
The blade material changes how long it lasts and how sharp it stays. It also affects how well it cuts different things. You should match the blade materials to your job for the best cutting edge quality and durability.
Baja Perkakas D2
D2 tool steel is very hard and does not wear out fast. You can use it to cut tough things. It stays sharp for a long time. This blade is good for slitting and trimming in busy places.
SKD-11 Alloy Steel
SKD-11 alloy steel is both hard and tough. This blade does not wear out or break easily. It is good for cutting strong plastics and other hard jobs. Many people use this material for circular knives.
Baja Kecepatan Tinggi (HSS)
High-speed steel (HSS) can handle heat and does not wear out fast. You can use it for fast, non-stop cutting. This blade is great for jobs that need exact cuts and high cutting edge quality. HSS blades cost more but last longer in hard jobs.
Karbida Wolfram
Tungsten carbide blades are very hard and last a long time. You can use them for very tough or rough materials. These blades keep their shape and sharpness after many uses. They work best for strong, non-stop jobs.
Besi tahan karat
Stainless steel blades do not rust and are easy to clean. You should use them for food, medical, or wet places. They give you safe, clean cuts and meet hygiene rules.
Pros and Cons of Each Material
You can look at the table below to compare blade materials. This helps you pick the right one for your circular knives.
Bahan Pisau | Keuntungan | Kekurangan | Aplikasi Umum |
---|---|---|---|
Baja Perkakas D2 | High hardness, good wear resistance, long-lasting sharpness | Can be brittle under heavy impact | Slitting, trimming, tough materials |
SKD-11 Alloy Steel | Balanced hardness and toughness, good wear and impact resistance | Lebih mahal dari baja karbon | Medium to high-strength plastics, general use |
Baja Kecepatan Tinggi (HSS) | High hardness, excellent wear and heat resistance, precise cuts | Higher cost, can be brittle under heavy impact | High-speed, precise cutting |
Karbida Wolfram | Extreme hardness, excellent wear resistance, long lifespan | Expensive, brittle, not for high-impact tasks | Abrasive, tough materials, continuous use |
Besi tahan karat | Rust-resistant, easy to clean, safe for food and medical use | Needs careful sharpening, not as hard as tool steels | Food, medical, wet environments |
Tip: Maxtor Metal has special coatings like TiN, CrN, and DLC. These coatings help your blade last longer, lower friction, and make the cutting edge quality better.
Edge Types
The edge type changes how your blade cuts. You need to pick the right edge for your material and job. This helps you get clean cuts and keeps your circular knives working well.
Bevel Tunggal
A single bevel blade has one side angled. It gives you exact trimming and slicing. This edge is good for soft things and jobs that need accuracy.
Double Bevel
A double bevel blade has both sides angled. It gives you sharpness and lasts longer. This edge is good for harder things and most cutting jobs.
Sharp Edge
A sharp edge blade gives you smooth, clean cuts. You should use it for paper, films, and food. It helps you avoid fraying or crushing.
Blunt Edge
A blunt edge blade is not as sharp but is stronger. You can use it for tough jobs where you need strength more than a fine cut.
Tooth Configuration (Serrated, Wavy, etc.)
Some blades have teeth or waves on the edge. Serrated or wavy blades help you cut tough or stretchy things. They lower machine stress and give you better control. You can pick different tooth shapes, like V, scalloped, or hi/lo V, to fit your needs.
Best Uses for Each Edge Type
Here is a table to help you choose the right edge for your circular knives:
Jenis Tepi | Characteristics & Configurations | Impact on Cutting Performance & Suitable Materials |
---|---|---|
Bevel Tunggal | One side angled, sharp or blunt | Precise trimming and slicing; good for soft materials |
Double Bevel | Both sides angled, sharp or blunt | Balanced sharpness and durability; good for tough materials |
Sharp Edge | Fine, smooth edge | Clean cuts for paper, films, food |
Blunt Edge | Less sharp, more durable | Heavy-duty jobs, less risk of chipping |
Serrated/Wavy | Teeth or waves, various shapes | Cuts tough/stretchy materials, reduces machine stress, better control |
Catatan: The right edge type helps you balance sharpness, durability, and precision. Always match the edge to your material and job.
Diameter and Size
The radius and size of your circular knives change how they cut. You need to pick the right diameter for your machine and material.
Standard Diameters
Most circular knives come in standard diameters. You should match the blade size to your machine for safe and good use. A blade with the right radius gives you better control and less shaking.
Custom Sizes
Sometimes, you need a custom size for special jobs. Maxtor Metal can make blades with any radius or thickness you want. Custom sizes help you get the best results for unique materials or machines.
Expansion Slots
Some blades have expansion slots. These slots help the blade handle heat and stop warping. You get more stable cuts and longer blade life.
Impact of Size on Performance
The size of your blade changes how it works. Here are some key points: A small radius blade gives you more control but may not cut thick things well. A large radius blade can cut bigger or thicker things but needs more power. Thin blades cut faster and with more accuracy but wear out quicker. Thick blades last longer and handle tough jobs but may cut slower.
Faktor | Keterangan | Dampak |
---|---|---|
Sampah Material | Thicker blades remove more material | Less efficient use of expensive or limited materials |
Pemotongan Presisi | Thinner blades provide cleaner, more precise cuts | Ideal for high-precision applications |
Kecepatan memotong | Thin blades cut faster due to less resistance | Important for high-volume jobs |
Tool Compatibility | Blade size and thickness must match machine power and design | Prevents tool damage and ensures safe operation |
Power Consumption | Thicker blades need more energy | Can affect tool lifespan and increase costs |
Always pick the smallest radius that fits your machine. This gives you more stability and better cutting edge quality.
Safety and Ergonomics
Safety and comfort are important when you use circular knives. Good design helps you avoid injuries and work longer without pain.
Fitur keamanan
Look for blades with safety caps, auto-retraction, or rounded tips. These features protect your hands when you use or store them. Auto-retractable blades pull back when not in use, so you are less likely to get cut.
Ergonomic Handle Designs
Ergonomic handles, like J-hook shapes, help your wrist and protect your fingers. Rubber grips and handles for both hands make the blade easier to hold and use. You can work longer and safer with less tiredness.
Protective Coatings
Coatings like TiN, CrN, and DLC help your blade last longer. They lower friction, stop rust, and keep the cutting edge quality high. Maxtor Metal offers these coatings for better durability and efficiency.
Maintenance and Handling Tips
Keep your blades clean and sharp. Store them safely with blade covers or clips. Change old blades quickly to keep your cuts clean and your team safe.
Using circular knives with good safety and ergonomic features helps you avoid injuries and work more comfortably. Always follow safe handling and storage practices.
Industry Applications for Circle Knife
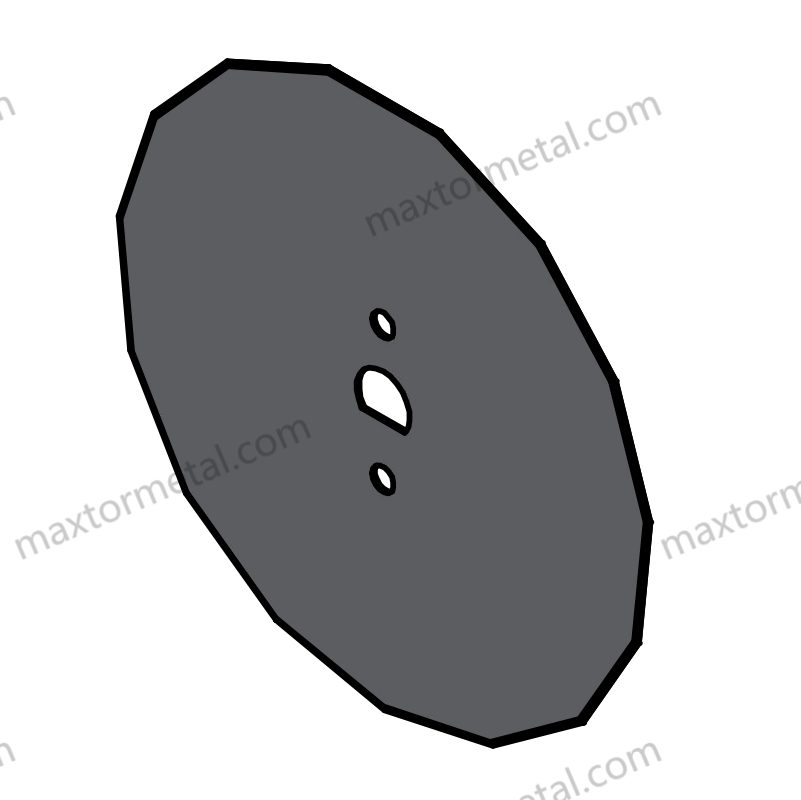
Paper & Packaging
Skenario Aplikasi Umum
Circular knives are used a lot in paper and packaging. They help cut paper rolls into smaller pieces. You can trim cardboard edges and make holes in packaging. These knives also cut films, foils, and laminates for machines. Bottom slitter knives help you get smooth, steady cuts.
Industry/Application Area | Deskripsi Aplikasi |
---|---|
Paper and Printing Industry | Circular knives cut paper rolls into thin strips for printing. Bottom slitter knives keep the paper steady for clean cuts. |
Industri Pengemasan | Circular knives cut films, foils, and laminates for packaging. They make rolls the right size for machines. You need to be exact for good packaging. |
Blade Requirements
Blades must be very sharp so paper does not tear. Strong edges help with lots of cutting. Fine teeth give smooth cuts, especially for thin films. For packaging, blades should stay sharp and cut with care.
Tip: Pick blades with special coatings so they last longer and need less fixing.
Textiles & Leather
Skenario Aplikasi Umum
Circular knives cut fabric, nonwovens, and leather sheets. They trim edges, cut rolls, and make holes in textiles. In fashion and furniture, people use them by hand or with machines.
Blade Requirements
Blades need to be extra sharp and have two angled sides. This stops fabric from fraying or stretching. Ceramic blades work well for fabric because they stay sharp. For leather, strong steel like SK2 or D-2 is best. Always wear safety gear and make sure blades fit your machine.
Catatan: Pisau khusus shapes and hardness help you match your job.
Pengolahan Makanan
Skenario Aplikasi Umum
Circular knives slice bread, cut meat and cheese, and cut food packaging. They help you get even pieces and make food look nice.
Blade Requirements
Blades should be stainless steel so they do not rust. Clean cuts stop food from getting crushed. You must clean and sanitize blades after each use. Store blades in cool, dry places with covers to keep them safe and clean.
Always follow food safety rules from the FDA and USDA to keep food safe.
Rubber & Plastics
Skenario Aplikasi Umum
Circular knives cut rubber sheets, plastic films, and trim plastic parts. They help you work with tough, thick materials in busy places.
Blade Requirements
Blades must be strong and sharp, made from D-2 tool steel or powdered metal. These materials help blades last and stay sharp. Check and fix blades often to keep them working well. Custom blades and special edges help with different rubber or plastic jobs.
- High-carbon steel and M-2 high-speed steel are good for many uses.
- Powdered metal blades work in hot or cold places.
- Sharpen blades often to keep them cutting well.
Metal & Foil
Skenario Aplikasi Umum
Circular knives cut thin metal sheets, trim aluminum or copper foils, and punch holes in metal tapes. They help you make neat, careful cuts.
Blade Requirements
Blades should be hard and tough, like high-speed steel (M-2), D-2 tool steel, or CPM 10V. These materials handle heat and last longer. Serrated or angled edges help you cut and punch holes cleanly. Pick the right edge shape so blades do not get dull too fast.
Daur Ulang
Skenario Aplikasi Umum
Circular knives shred paper, plastics, and metals. They also cut mixed materials for recycling and work in rough places.
Blade Requirements
Blades must be very tough and not break easily. Serrated or toothed edges help shred things fast. Easy cleaning is important because blades wear out quickly in recycling. Special coatings help blades last longer and work better.
Industri Medis
Skenario Aplikasi Umum
Circular knives cut medical tapes, dressings, and surgical drapes. They also cut nonwovens for medical use. These knives help you make careful, clean cuts for sensitive products.
Blade Requirements
Blades must be very sharp and clean, made from rust-proof materials. Fine edges help cut soft materials without damage. Always use blades that meet medical safety rules and are easy to clean.
Kebersihan
Skenario Aplikasi Umum
Circular knives cut diapers, wipes, and hygiene films. They also cut nonwovens for hygiene products.
Blade Requirements
Blades need to be sharp and clean to avoid hurting products. Stainless steel or food-safe materials help meet hygiene rules. Special coatings and custom shapes help with different hygiene jobs.
Label/Tape Manufacturing
Skenario Aplikasi Umum
Circular knives cut sticky tapes, label rolls, and punch holes in liners. They help you make neat, clean cuts for labels and tapes.
Blade Requirements
Blades should have non-stick coatings so glue does not build up. Sharp edges help you cut cleanly and accurately. You can change the number of teeth for different tapes. Special coatings help blades last longer when used a lot.
Remember: Using the right blade for your job helps you get the best results and keeps your work running well.
Choosing the Right Circle Knife Profile
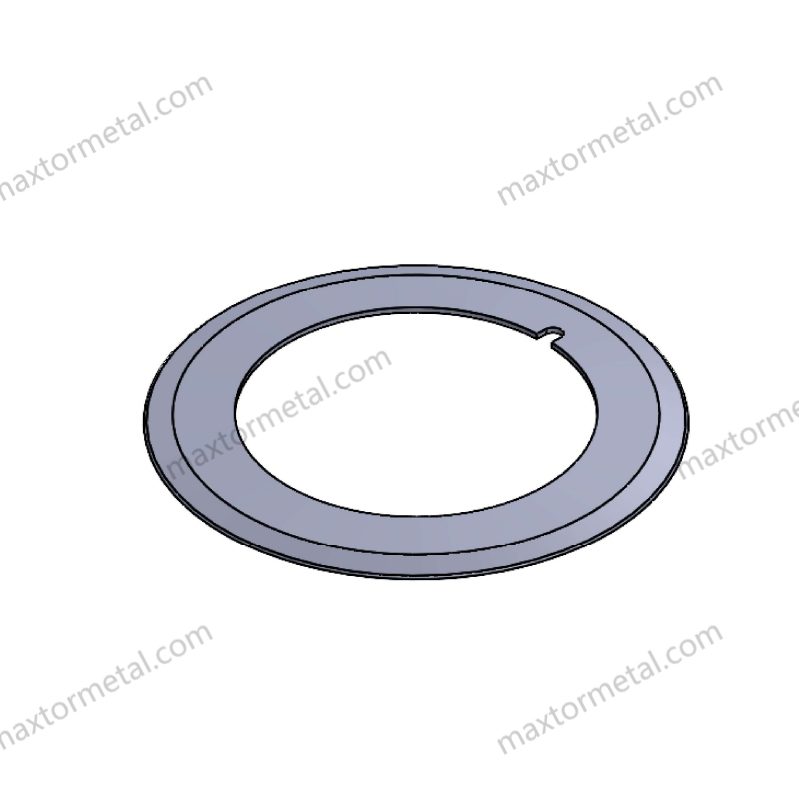
When you pick the right knife profile, your cutting gets better. The knife profile has three main parts: radius, bevel angle, and tooth shape. Each part changes how your circular knives work. You need to match the profile to your material, how fast you work, and the finish you want.
Profile Selection
Common Knife Profiles Overview
There are a few common knife profiles used in factories. Each one has special features and is best for certain jobs. The table below shows the most popular profiles and where they are used.
Knife Profile | Description & Features | Typical Application Scenarios & Industries |
---|---|---|
Straight Knives | Versatile, durable, beveled edges. Made from high carbon, stainless steel, carbide, ceramic, and specialty steels. | Used for cutting fabrics, corrugated products, paper, leather, steel, and food. |
Pisau Melingkar | Also called slitter knives. Made with high-quality materials and customizable designs. | Used for slitting, scoring, and trimming in plastics, glass, and rough fiber work. |
Pisau Potong | Guillotine or swing-style blades with various tooth profiles. | Common in packaging, food processing, fiberglass, foam, seafood, and leather industries. |
Tray Knives | Precision cutting with customizable tooth configurations. | Used in film roll cutting, container manufacturing, plastic cutting, packaging, and foil/film handling. |
Fiberglass Knives | Designed for hard, brittle fiberglass. Made from high carbon steel, stainless steel, and carbide with coatings. | Used in aerospace, automotive, boat building, and bathroom accessories. |
Tip: Always look at the knife profile before starting a new job. The right profile helps you save time and get better results.
Application Scenarios for Each Profile
- Straight knives are good for cutting textiles, paper, and leather. They make clean, straight cuts.
- Circular knives are best for slitting, scoring, or trimming things like plastic films or glass. The round shape and right radius help you cut fast and smooth.
- Cutoff knives are great for packaging and food jobs. They work well for chopping and slicing.
- Tray knives are used in packaging and converting. They cut films and foils with care.
- Fiberglass knives are made for tough, brittle stuff. They cut without breaking the material.
Pros and Cons Comparison Table
You should think about the good and bad points of each knife profile. The table below helps you compare them.
Knife Profile | Kelebihan | Kontra |
---|---|---|
Straight Knives | High precision, easy to sharpen, versatile | Not ideal for curved or round cuts |
Pisau Melingkar | Fast, continuous cuts, less material waste, customizable radius | Needs correct setup, may require special machines |
Pisau Potong | Good for quick, straight cuts, handles thick materials | Limited to certain shapes, may need frequent sharpening |
Tray Knives | Excellent for films and foils, customizable tooth profiles | Not suitable for thick or hard materials |
Fiberglass Knives | Cuts hard, brittle materials cleanly, reduces splintering | May wear faster on other materials |
Note: Picking the right knife profile for your job helps you waste less and avoid stopping your work.
Bevel and Tooth Options
Bevel Angle Selection
The bevel angle is the slant on the blade’s edge. This angle changes how sharp and strong your circular knives are. A small bevel angle (10°-20°) makes the blade very sharp. You use this for soft materials and jobs that need careful cuts. A bigger bevel angle (22°-30°) makes the blade stronger. This is better for hard materials and fast work.
When you pick the bevel angle, think about what you are cutting and how fast you need to go. Sharper angles cut cleaner but need more care. Wider angles last longer and let you work faster.
Tooth Configuration Types
Tooth configuration is the shape and pattern of the teeth on the blade. There are a few main types:
- Serrated teeth: Good for cutting tough or stretchy things. They grab and slice at the same time.
- Wavy teeth: Help you cut soft or sticky things. The wave shape keeps the material moving and stops sticking.
- V-shaped teeth: Give a strong bite for thick or hard things.
- Scalloped teeth: Make smooth cuts in soft or gentle items.
The right tooth shape helps you get the finish you want and keeps your work moving.
Real-World Application Cases
Many factories have done better by picking the right knife profile and tooth shape. For example, a box factory used micro-tooth blades and cut downtime from 14 hours to under 5 hours. They also saved 28% on costs. A packaging company used high-concentricity blades and lowered waste from 10% to 3%. In meat processing, custom blades stopped blade breaks and cut machine downtime in half.
Picking the right knife profile and tooth shape can save you money and time.
Cutting Effect Comparison Table
The table below shows how bevel angle and tooth shape change your cutting results.
Fitur | Sharper Bevel (10°-20°) | Wider Bevel (22°-30°) | Serrated Teeth | Wavy Teeth |
---|---|---|---|---|
Cut Quality | Very fine, precise cuts | Strong, durable cuts | Grips tough/stretchy material | Smooth cuts, less sticking |
Kecepatan Produksi | Slower, needs more care | Faster, less downtime | Good for high volume | Good for sticky materials |
Pemeliharaan | Perlu sering diasah | Less frequent sharpening | Easy to clean | Easy to clean |
Terbaik Untuk | Delicate, thin materials | Thick, hard materials | Rubber, plastics, textiles | Food, soft plastics, films |
Remember: The right bevel angle and tooth shape help you balance cut quality, speed, and blade life.
Tips for Matching Profile to Production Volume and Environment
- For big jobs, use a wider bevel angle and strong teeth. This helps your circular knives last longer.
- For careful or exact work, pick a sharper bevel and fine teeth. This gives you clean, exact cuts.
- Always match the blade’s radius to your machine and material. The right radius gives you better control and less waste.
- In hot or rough places, use blades with special coatings. This helps your circular knives last longer.
When you focus on picking the right knife profile, your cuts get better, faster, and safer. You also make your work easier and more efficient.
Customization and Maxtor Metal Solutions
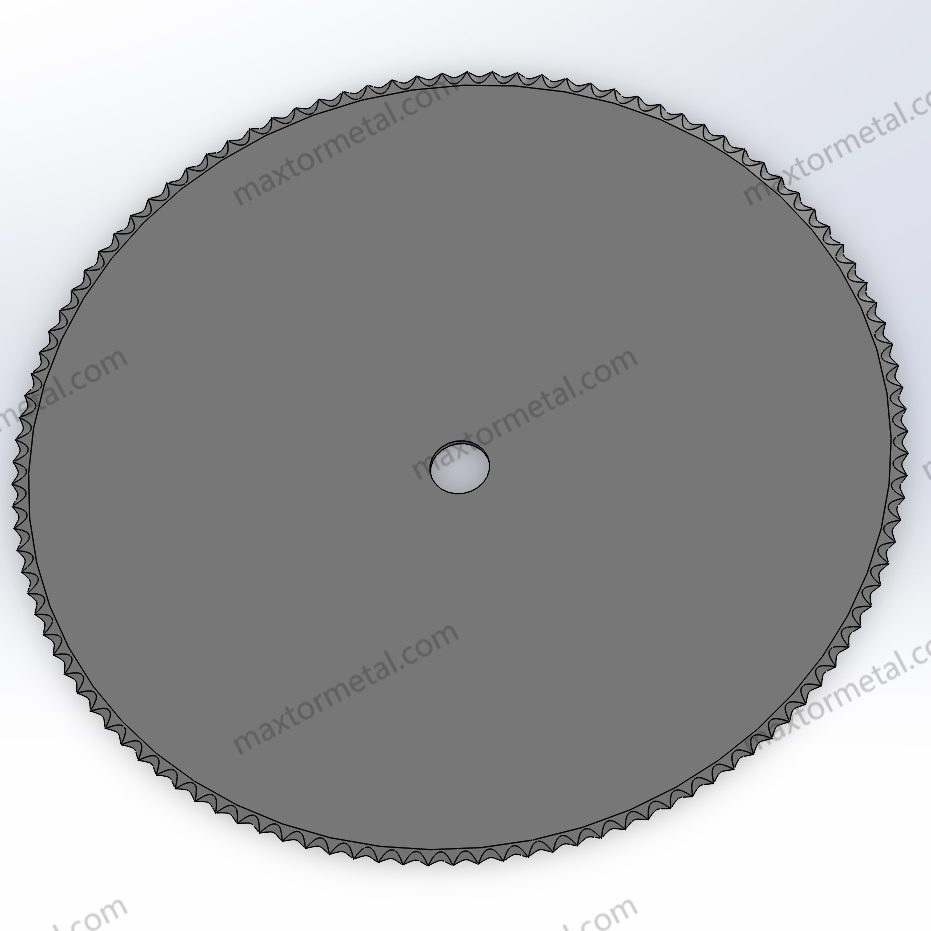
When to Customize
Sometimes, you need a custom circle knife for special jobs. Custom blades help you get the best results for hard or unique tasks. Here are some reasons to pick a custom blade:
- You cut things that need a specific edge, like thin films or strong metals.
- You want your blades to work better and last longer.
- Your job needs a certain tooth shape or edge angle for neat cuts.
- You want to waste less and stop your machines less often.
- You want to use new materials or coatings for better cutting.
- Your machine needs a blade with a certain size or shape.
- You need to replace an old blade and want it to match exactly.
Custom blades help you trim, slit, slice, perforate, or score many materials. You can also use custom designs to fix problems with new or tricky products.
OEM and Custom Blades
Maxtor Metal gives you lots of choices for custom and OEM blades. You can send them your drawings, sketches, or samples. Their team will help you design or improve your blade for better results. Here is what Maxtor Metal offers:
- Custom design and engineering with advanced CAD/CAM tools.
- Expert advice on picking the right material and coating for your job.
- Accurate blade shapes made with modern machines.
- Prototyping and testing to make sure your blade works before making more.
- Flexible production for both small and big orders.
- Full quality checks at every step, from start to finish.
- Real-time updates on your order, so you always know what’s happening.
- Help for importers, distributors, and users with easy ordering.
Maxtor Metal also has special coatings like TiN, CrN, and DLC. These coatings help your blade last longer and cut better. You can trust their careful quality checks and customer support to get blades that fit your needs.
Kesalahan Umum yang Harus Dihindari

When you pick a circular knife, you should watch out for common mistakes. These mistakes can make your cuts bad or even cause accidents. Many people mess up by picking the wrong material, not thinking about safety, or choosing the wrong knife size or edge. Knowing about these mistakes helps you work better and safer.
Ketidakcocokan Material
Using the Wrong Blade Material
Some people think any blade will work for their job. But using the wrong blade material can cause big trouble. If your blade is too soft for metal, it will wear out fast. If it is too hard for soft things, it can break or hurt your machine. Always use a blade that matches what you are cutting.
Consequences of Material Mismatch
Aspek | Consequences of Wrong Blade Material or Ignoring Safety Features |
---|---|
Using Wrong Blade Material | Can break the blade, ruin your work, and cause accidents. |
Improper Installation or Alignment | Makes cuts uneven, wears out blades, and can be unsafe. |
Ignoring Safety Features | Raises the chance of getting hurt or having blade problems. |
Loose Bolts or Poor Securing | Makes the blade shake, cut badly, and wear out faster. |
Lack of Proper Protective Equipment | Makes it easier to get hurt by sharp blades or flying pieces. |
Not Following Manufacturer Instructions | Can break the blade, make it work badly, and be unsafe. |
If you use the wrong blade, your cuts may look rough or break. You might even have an accident. You will need to fix or replace tools more often.
How to Avoid Material Mismatch
- Check what you need to cut before picking a blade.
- Read the guide that comes with each blade.
- Ask someone who knows if you are not sure.
- Try cutting a small piece first to see if it works.
Tip: Always use the right blade material for your job. This helps your tools last longer and work better.
Ignoring Safety
Lack of Proper Safety Features
Some people skip safety parts to save time or money. This is risky. Without guards or safety switches, you can get hurt. Blade guards and other safety tools help keep you safe and make your work better.
Unsafe Handling Practices
Bad habits can cause accidents. Forcing the blade, pushing too hard, or not wearing gloves can hurt you. Not checking for loose bolts or broken parts is also dangerous.
Tips for Ensuring Safety
- Always use blade guards and safety switches.
- Wear gloves and eye protection when you use blades.
- Make sure all bolts and parts are tight before you start.
- Let the blade do the work—do not push too hard.
- Clean and check your blade often for damage or wear.
Note: Following safety rules and using the right gear keeps you and your team safe every day.
Wrong Size or Edge
Selecting Incorrect Knife Size
If your knife is too big or too small for your machine, it can wobble or cut badly. The wrong size can also break your machine or cause accidents. Always check the size and thickness before putting in a new knife.
Choosing the Wrong Edge Type
The edge type is important for every job. If you use a blunt edge on thin film, it might tear. If you use a sharp edge on tough rubber, the blade can wear out fast. Picking the wrong edge means bad cuts and more time fixing things.
How to Select the Right Size and Edge
- Measure your machine’s needs before buying a knife.
- Match the edge type to your material and the finish you want.
- Use the maker’s chart or ask for help if you are not sure.
- Try different edges on samples to see what works best.
Quick Tip: The right size and edge help you get clean cuts, waste less, and stay safe.
Most Frequent Mistakes to Watch For:
- Using the wrong blade for your material
- Not matching blade size and tooth shape to your job
- Forgetting to clean and sharpen your blade
- Forcing the blade instead of letting it cut
- Skipping safety checks and not using guards
If you avoid these mistakes, your cuts will look better, your tools will last longer, and you will be safer at work.
Quick Selection Checklist
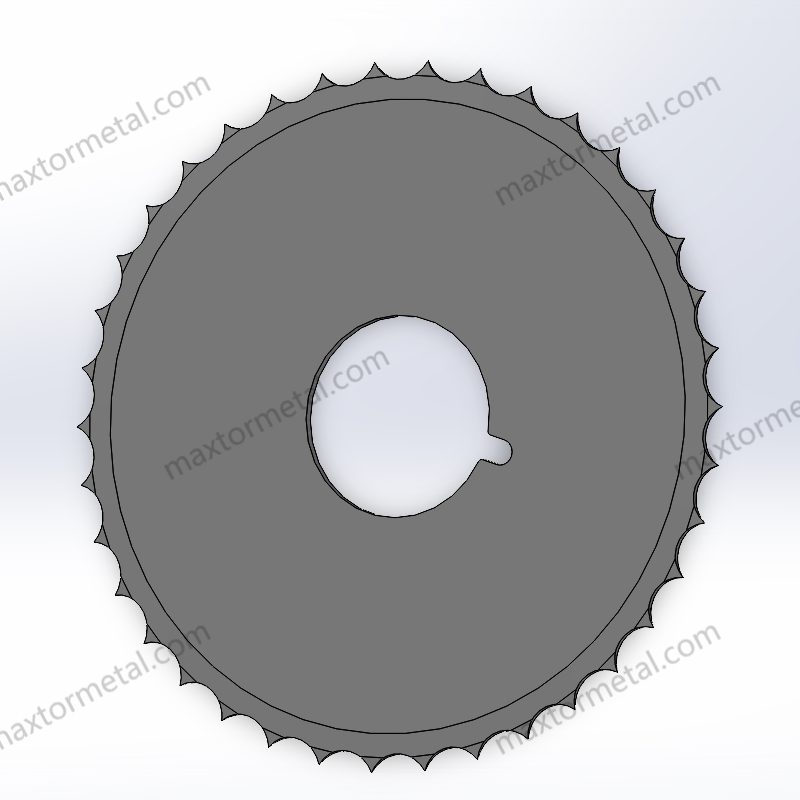
Before you choose your next circle knife, use this checklist to make sure you get the best fit for your job:
- Pick the right blade material. Think about what you need most—hardness, durability, corrosion resistance, or wear resistance. For example, high-carbon steel works well for tough jobs, while stainless steel is best for food or wet environments.
- Select the correct edge and tooth shape. Decide if you need a square edge, single bevel, double bevel, or a special tooth pattern. The right edge helps you get clean cuts and keeps your blade sharp longer.
- Match the blade to your material and cutting method. Check if you need to cut, trim, slit, slice, perforate, score, crease, or split. Each task works best with a certain blade type.
- Think about custom options. Sometimes, a standard blade will not fit your needs. Custom designs let you choose the size, shape, and coating that work best for your job.
- Talk to an expert. If you feel unsure, ask an engineer or blade specialist. They can help you pick the best material and design for your work.
- Check your industry needs. Different industries need different blades. Food, plastics, rubber, textiles, metals, paper, and packaging all have special requirements.
Tip: Always review this checklist before you order. Careful selection saves you time, money, and trouble down the line. The right circle knife makes your work easier and your results better.
To pick the best circular knife, follow these steps: First, figure out your cutting job, like slitting or trimming. Next, choose a blade material that fits what you need. Then, pick the right edge and tooth shape for your material. If you are not sure, ask experts for help or custom ideas. You can also get custom designs for a perfect fit and better quality.
Maxtor Metal can help you with expert advice and guides. Using the right knife makes your work better and gives you real results. For example, you can cut more things in less time. You will waste less material and use less energy. Your production speed can go up by 40%. You will have fewer rejected pieces and lower maintenance costs. The quality of your cuts will be more even. Your machines will last longer, too.
Improvement Category | Measurable Outcome |
---|---|
Hasil produksi | +20% |
Scrap Material | -25% |
Konsumsi Energi | -15% |
Kecepatan Produksi | +40% |
Rejected Materials | -50% |
Biaya Pemeliharaan | Lebih rendah |
Quality Consistency | Ditingkatkan |
Machine Lifespan | Extended |

Use the checklist and get help from experts to get the best results every time you cut.
Tanya Jawab Umum
What is the best way to keep my circle knife sharp?
You should clean your blade after each use. Store it in a dry place. Use a sharpening stone or tool made for your blade type. Replace the blade if it gets dull or damaged.
How do I know which blade material to choose?
Look at what you need to cut. For food, pick stainless steel. For tough jobs, use D2 or tungsten carbide. If you feel unsure, ask an expert or check the product guide.
Can I use one circle knife for different materials?
You should not use one blade for everything. Each material needs a special blade. Using the wrong blade can damage your work or the knife. Always match the blade to your job.
Why do some blades have teeth or waves?
Teeth or waves help you cut tough or stretchy things. They grip the material and make cutting easier. For soft or sticky items, wavy blades work best. For hard or thick items, use blades with strong teeth.
What safety steps should I follow when using circle knives?
Always wear gloves and eye protection. Check that the blade fits your machine. Use blade guards if you have them. Never force the blade. Keep your hands away from the cutting edge.
Lihat Juga
Top 10 Tips to Make Your Circular Razor BlaDes Last Longer
Cara Memilih Pisau Pemotong Bundar yang Tepat untuk Kinerja yang Tahan Lama
Cara Menjaga Pisau Bundar Anda Tetap Tajam dan Tahan Lama
Cara Memilih Bilah Bundar yang Tepat untuk Aplikasi Anda: Panduan Lengkap
5 Masalah Keausan Umum pada Pisau Gunting Bundar dan Solusi Perbaikan Ahli