Banyak industri bergantung pada Pisau industri untuk pemotongan presisi. Namun, produsen sering menghadapi tantangan seperti kualitas pemotongan yang tidak konsisten, keausan bilah yang cepat, dan penggantian yang sering. Salah satu faktor penting namun sering diabaikan adalah konsentrisitas bilah industri.
Konsentrisitas yang buruk dapat menyebabkan pemotongan tidak stabil, peningkatan limbah, dan biaya perawatan yang lebih tinggi. Sebaliknya, konsentrisitas yang tinggi memastikan kinerja pemotongan yang optimal, masa pakai bilah yang lebih lama, dan peningkatan efisiensi operasional.
Pada Nanjing Metal, kami telah menghabiskan 18 tahun menyempurnakan proses produksi bilah industri kami. Dengan berfokus pada konsentrisitas tinggi, kami membantu industri mencapai pemotongan presisi, penghematan biaya, dan peningkatan keselamatan. Artikel ini akan membahas pentingnya konsentrisitas, cara memastikannya, dan dampaknya terhadap kinerja, efisiensi, dan keselamatan.
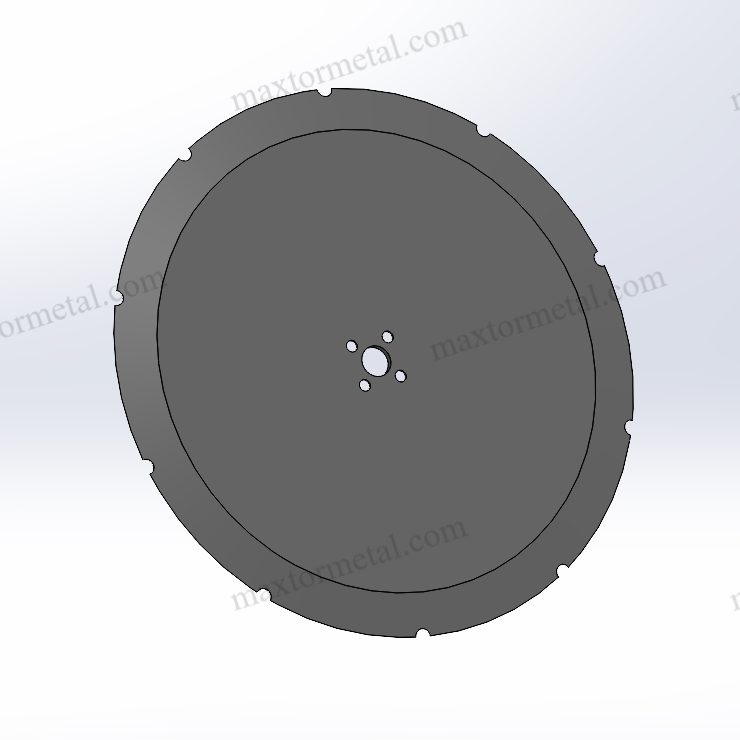
1. Apa itu Konsentrisitas dan Mengapa Itu Penting?
Menentukan Konsentrisitas pada Bilah Industri
Konsentrisitas adalah tingkat keselarasan pusat putaran bilah dengan ujung pemotongnya. Dalam istilah yang lebih sederhana, bilah industri dengan konsentrisitas tinggi mempertahankan jarak yang seragam antara ujung dan pusat putarannya selama gerakannya, memastikan pemotongan yang halus dan presisi.
Secara matematis, konsentrisitas sering direpresentasikan oleh total runout yang ditunjukkan (TIR), diukur dalam satuan mikron (µm). Nilai TIR yang lebih rendah menunjukkan konsentrisitas yang lebih baik, yang penting untuk mencapai presisi dalam aplikasi pemotongan kecepatan tinggi.
Standar dan Persyaratan Industri
Untuk menjaga konsistensi, banyak industri mengikuti standar khusus untuk memastikan bilah dengan konsentrisitas tinggi:
- Standar ISO 9001 – Mengamanatkan sistem manajemen mutu, termasuk kontrol manufaktur presisi.
- Standar ISO 2768-1 – Menentukan toleransi umum untuk peralatan pemesinan dan pemotongan.
- Nomor seri 3967 – Digunakan untuk toleransi geometri pada komponen presisi tinggi.
- ASTM A681 – Menentukan persyaratan material untuk baja kecepatan tinggi dan baja perkakas yang digunakan dalam bilah industri.
Menurut studi tahun 2023 oleh Industrial Cutting Technology Journal, lebih dari 70% produsen yang mengadopsi metode produksi bilah bersertifikat ISO melaporkan peningkatan rata-rata 30% dalam presisi pemotongan dan pengurangan 25% dalam biaya perawatan.
Konsentrisitas Rendah vs. Konsentrisitas Tinggi: Perbandingan Teknis
Faktor | Bilah Konsentrisitas Rendah | Bilah Konsentrisitas Tinggi |
Total Runout yang Ditunjukkan (TIR) | >50 µm | <10 µm |
Deviasi Pemotongan | ±0,5mm atau lebih | ±0,05mm atau kurang |
Tingkat Getaran | Tinggi, menyebabkan pemotongan tidak stabil | Minimal, memastikan presisi |
Pola Pemakaian | Tidak merata, menyebabkan kegagalan dini | Bahkan, memperpanjang umur |
Konsumsi Energi | Lebih tinggi karena peningkatan gesekan | Lebih rendah, meningkatkan efisiensi |
Dampak Kritis Konsentrisitas
- Akurasi Pemotongan – Konsentrisitas tinggi memungkinkan toleransi dalam ±0,01 mm, penting untuk industri seperti percetakan, tekstil, dan pengolahan makanan.
- Umur Pisau – Distribusi keausan yang merata meningkatkan masa pakai bilah hingga 50%, sehingga mengurangi biaya penggantian.
- Efisiensi Operasional – Mesin 25-40% beroperasi lebih efisien, mengurangi waktu henti akibat kesalahan penyelarasan.
- Keamanan – Pisau yang seimbang akan mengurangi risiko kegagalan mendadak atau tergelincirnya material, sehingga melindungi mesin dan operator.
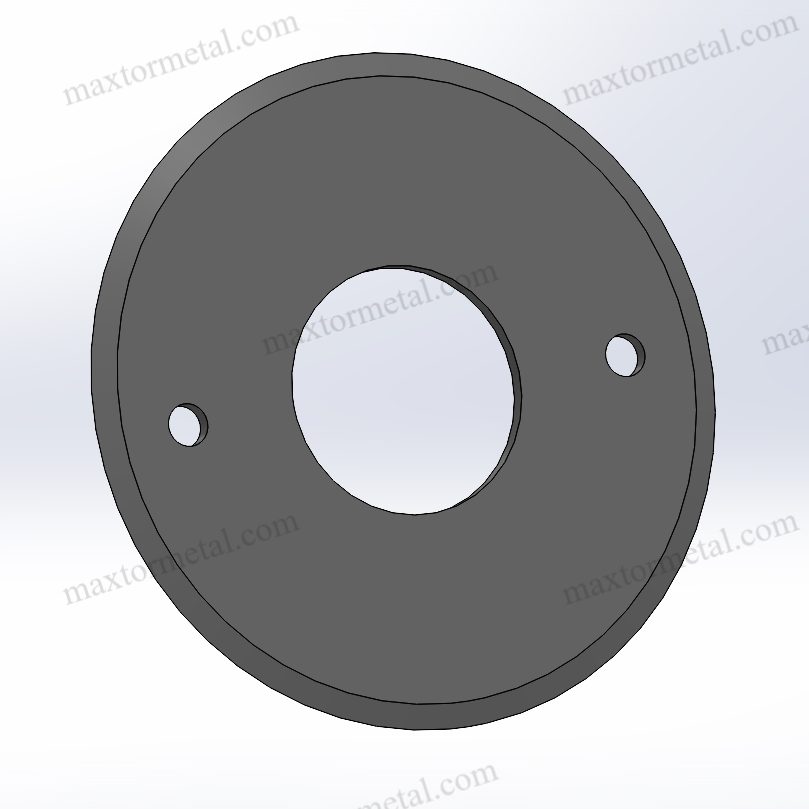
2. Cara Memastikan Bilah Berkonsentrisitas Tinggi
Proses Manufaktur yang Menjamin Konsentrisitas Tinggi
Pisau industri dengan konsentrisitas tinggi diproduksi menggunakan teknik rekayasa presisi canggih, termasuk:
1. Pemesinan Presisi CNC
- Memastikan pembuangan material yang seragam, mengurangi asimetri dalam struktur bilah.
- Mempertahankan toleransi seketat ±0,005 mm, penting untuk aplikasi yang memerlukan presisi tinggi.
2. Sistem Pengukuran Laser
- Menggunakan sensor laser non-kontak untuk mendeteksi penyimpangan tingkat mikron.
- Meningkatkan konsentrisitas dengan memastikan distribusi berat yang merata di sepanjang bilah.
3. Penggilingan dan Pelapisan Permukaan
- Meningkatkan kerataan dan keseragaman tepi, mengurangi goyangan bilah.
- Mencapai kekasaran permukaan Ra < 0,1µm, meminimalkan gesekan.
4. Penyeimbangan dan Pengujian
- Penyeimbangan dinamis berkecepatan tinggi menghilangkan ketidakseimbangan mikro sebelum pengiriman akhir.
- Menggunakan indikator dial dan mikrometer untuk mengukur konsentrisitas hingga akurasi ±2µm.
Cara Memilih Produsen Pisau yang Andal
Tidak semua produsen menjamin pisau dengan konsentrisitas tinggi. Berikut lima pertanyaan kunci yang perlu ditanyakan saat memilih pemasok:
- Apakah mereka menawarkan laporan toleransi presisi?
- Produsen yang dapat diandalkan harus menyediakan Chasil uji onsentrisitas pada setiap batch.
- Sertifikasi apa yang mereka pegang?
- Kepatuhan terhadap ISO 9001, ISO 2768, dan ASTM A681 menunjukkan kualitas.
- Apa proses pengendalian mutu mereka?
- Inspeksi optik otomatis dan pengujian laser merupakan tanda proses berkualitas tinggi.
- Bisakah mereka menyediakan solusi yang disesuaikan?
- Spesifikasi bilah khusus memastikan kesesuaian yang sempurna untuk aplikasi Anda.
- Industri apa yang mereka layani?
- Produsen yang berpengalaman dalam industri otomotif, kedirgantaraan, dan pengemasan biasanya mematuhi toleransi yang lebih ketat.
Manufaktur Presisi Nanjing Metal
Pada Nanjing Metal, kami menggunakan:
- Mesin penggilingan CNC 5-sumbu untuk konsentrisitas akurasi mikron.
- Pengujian laser runout untuk mencapai TIR < 10µm.
- Penyeimbangan berkecepatan tinggi untuk menghilangkan risiko getaran.
Dengan mempertahankan standar tinggi tersebut, pelanggan kami melaporkan:
✅ Peningkatan efisiensi pemotongan 30%
✅ Pengurangan frekuensi penggantian bilah 50%
✅ 20% menurunkan biaya operasional
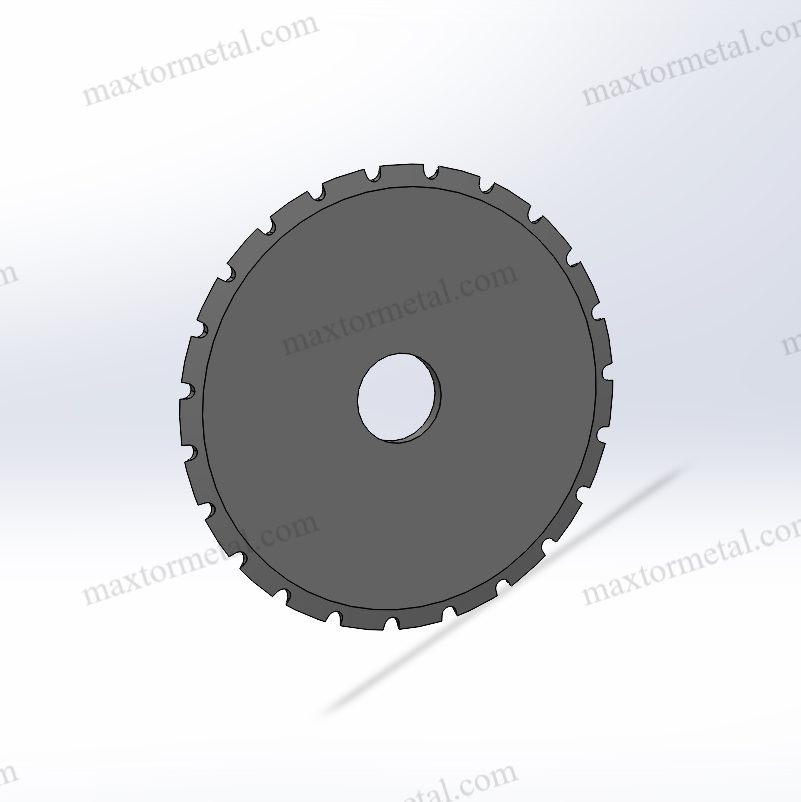
3. Bagaimana Konsentrisitas Mempengaruhi Akurasi Pemotongan
Dampak Dunia Nyata dari Konsentrisitas yang Buruk
Sebuah studi tahun 2022 oleh Precision Manufacturing Institute menemukan bahwa bilah dengan konsentrisitas rendah meningkatkan limbah material sebesar 12-15% dalam aplikasi pemotongan berkecepatan tinggi.
Studi Kasus: Dampak Konsentrisitas yang Buruk dalam Industri Pengemasan
- Seorang produsen karton bergelombang melaporkan adanya pemborosan material 10% akibat pemotongan yang tidak selaras.
- Setelah beralih ke konsentrisitas tinggi pisau putar, persentase limbahnya turun hingga 3%, sehingga menghemat $150.000 bahan baku setiap tahunnya.
Ilmu di Balik Akurasi Pemotongan
Tingkat Konsentrisitas Bilah | Deviasi Pemotongan yang Diharapkan | Tingkat Limbah Material |
Rendah (TIR > 50µm) | ±0,5mm atau lebih | 10-15% |
Sedang (TIR 20-50µm) | ±0,2 mm | 5-8% |
Tinggi (TIR < 10µm) | ±0,05mm atau kurang | <3% |
Bagaimana Konsentrisitas Tinggi Memastikan Akurasi
- Meminimalkan Getaran Bilah
- Pisau dengan konsentrisitas rendah menyebabkan getaran yang Smenggeser jalur pemotongan secara tidak terduga.
- Konsentrisitas tinggi mengurangi getaran lebih dari 80%, memastikan garis potong yang konsisten.
- Meningkatkan Stabilitas Kontak Material
- Pisau yang tidak sejajar menyebabkan distribusi tekanan tidak teratur, sehingga menghasilkan potongan yang tidak merata.
- Konsentrisitas tinggi memastikan penerapan gaya yang merata, menghasilkan tepian yang halus.
- Menghilangkan Kebutuhan Pemrosesan Sekunder
- Konsentrisitas yang buruk menyebabkan potongan bergerigi, sehingga memerlukan pemangkasan atau penyelesaian tambahan.
- Konsentrisitas tinggi mengurangi waktu pengerjaan ulang hingga 40%, meningkatkan produktivitas.
Contoh: Pisau Konsentrisitas Tinggi dalam Pembuatan Tekstil
Perusahaan tekstil yang menggunakan pisau pemotong dengan konsentrisitas rendah mengalami pemborosan kain sebesar 5% karena tepinya yang berjumbai. Setelah meningkatkan ke pisau pemotong dengan konsentrisitas tinggi yang digiling secara presisi, tingkat cacatnya turun menjadi 1%, sehingga menghemat biaya material ribuan dolar setiap tahunnya.
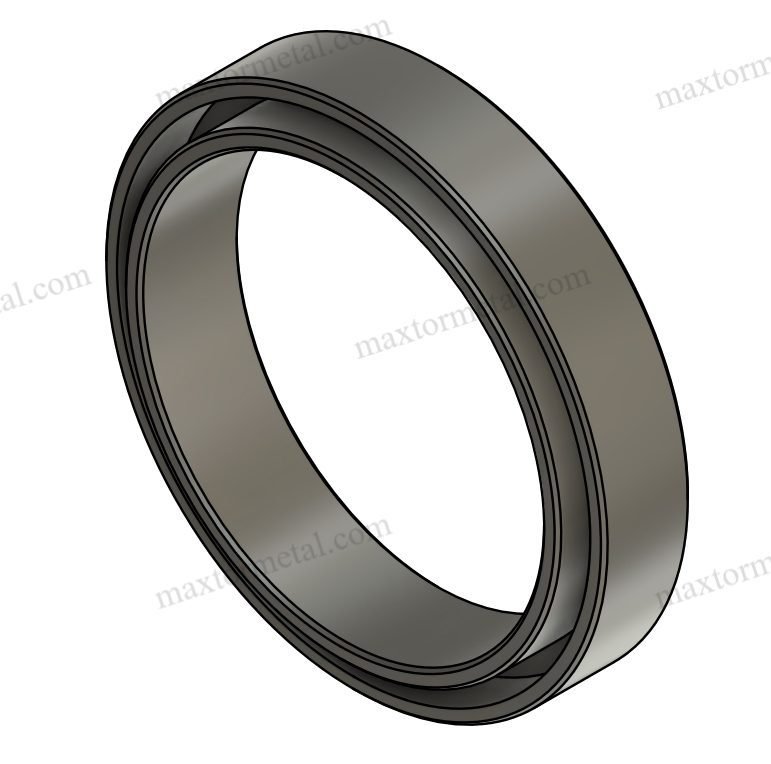
4. Bagaimana Konsentrisitas Mempengaruhi Umur Bilah
Mengapa Umur Bilah Itu Penting
Dalam aplikasi industri, penggantian bilah merupakan faktor biaya yang signifikan. Waktu henti akibat bilah yang aus berdampak langsung pada produktivitas, sementara penggantian yang sering meningkatkan biaya operasional. Studi menunjukkan bahwa keausan bilah menyumbang hingga 30% dari total biaya alat pemotong dalam industri seperti fabrikasi logam, pemrosesan kertas, dan produksi makanan.
Keausan Tidak Merata vs. Keausan Seragam: Peran Konsentrisitas
Pisau dengan konsentrisitas yang buruk mengalami:
✅ Titik-titik tegangan lokal, menyebabkan keausan dini di area tertentu.
✅ Masalah panas berlebih, mempercepat degradasi ujung tajam.
✅ Defleksi bilah, mengurangi presisi dan meningkatkan tingkat pemusnahan.
Sebuah studi tahun 2022 oleh Precision Tooling Institute menemukan bahwa bilah dengan konsentrisitas rendah menunjukkan tingkat keausan 60% lebih tinggi di zona tertentu dibandingkan dengan bilah dengan konsentrisitas tinggi, sehingga memerlukan penggantian dua kali lebih banyak.
Sebaliknya, bilah dengan konsentrisitas tinggi mengalami:
✔ Distribusi gaya pemotongan yang merata, mengurangi keausan yang tidak merata.
✔ Resistensi gesekan lebih rendah, sehingga meningkatkan kinerja pemotongan.
✔ Masa pakai lebih panjang, sehingga frekuensi penggantian berkurang.
Dampak Material terhadap Umur Bilah
Umur pakai bilah juga dipengaruhi oleh pilihan material. Tabel berikut menunjukkan umur pakai tipikal untuk berbagai material dalam kondisi konsentrisitas tinggi dan rendah.
Bahan Pisau | Umur Rata-rata (Pisau dengan Konsentrisitas Rendah) | Umur Rata-rata (Pisau dengan Konsentrisitas Tinggi) | Peningkatan % |
Baja Kecepatan Tinggi (HSS) | 6 bulan | 12 bulan | +50% |
Karbida Wolfram | 12 bulan | 24 bulan | +50% |
Pisau berlapis keramik | 18 bulan | 36 bulan | +50% |
Penghematan Biaya dari Bilah Konsentrisitas Tinggi
Beralih ke bilah dengan konsentrisitas tinggi dapat memangkas biaya penggantian hingga 50%. Pertimbangkan skenario berikut:
Jenis Pisau | Frekuensi Penggantian Tahunan | Biaya Blade Tahunan ($) | Biaya Downtime ($) | Jumlah Biaya ($) |
Pisau Standar | 2 kali | 10,000 | 5,000 | 15,000 |
Bilah Konsentrisitas Tinggi | 1 kali | 5,000 | 2,000 | 7,000 |
✅ Total penghematan: $8.000 per tahun per mesin
Pabrik produksi berskala besar yang menggunakan 50 mesin dapat menghemat $400.000 per tahun hanya dengan meningkatkan pisau menjadi berkonsentrisitas tinggi.
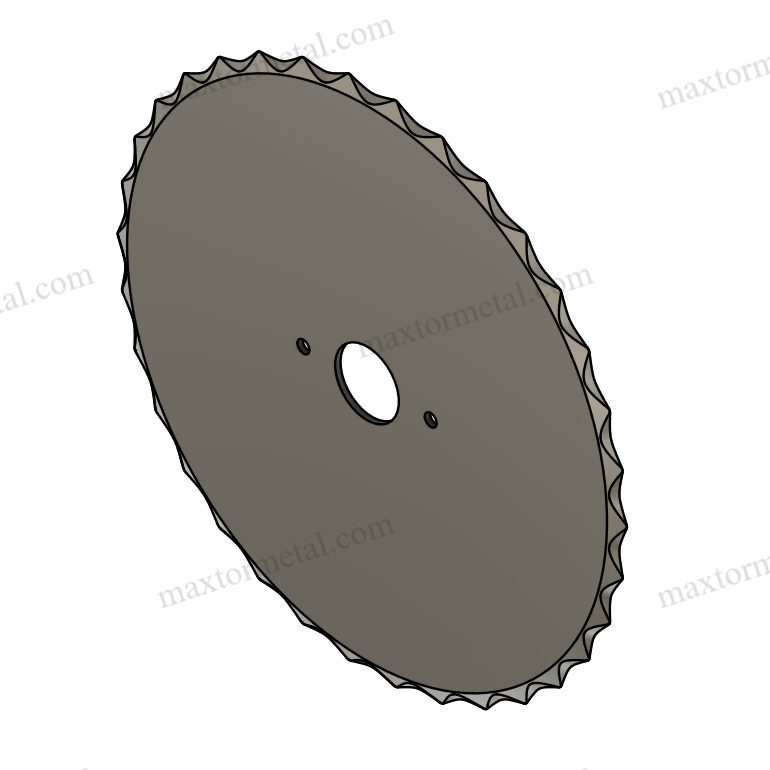
5. Bagaimana Konsentrisitas Meningkatkan Efisiensi Operasional
Efisiensi bilah secara langsung memengaruhi kinerja mesin, produktivitas, dan biaya produksi. Konsentrisitas yang buruk mengakibatkan peningkatan gesekan, keausan yang tidak merata, dan pergantian bilah yang lebih sering—yang semuanya mengurangi waktu aktif mesin.
Mengurangi Waktu Henti dan Perawatan
Mesin yang beroperasi dengan bilah konsentrisitas rendah memerlukan:
🚨 Kalibrasi ulang secara berkala untuk menyesuaikan ketidakselarasan.
Konsumsi energi lebih tinggi akibat pemotongan yang tidak efisien.
Penggantian komponen lebih sering karena meningkatnya getaran.
Sebaliknya, bilah dengan konsentrisitas tinggi:
✔ Mengurangi waktu kalibrasi ulang mesin sebesar 30%, meningkatkan waktu aktif.
✔ Menurunkan beban motor dan penggunaan energi sebesar 15%, memangkas biaya daya.
✔ Memperpanjang umur komponen mesin dengan 40%, mengurangi perawatan.
Studi Kasus: Peningkatan Efisiensi Industri Percetakan
Sebuah perusahaan percetakan komersial yang memproduksi jutaan lembar kertas per minggu menghadapi keausan bilah yang berlebihan, sehingga memerlukan penggantian setiap dua minggu. Setelah beralih ke bilah dengan konsentrisitas tinggi:
📌 Pergantian mata pisau dikurangi menjadi enam minggu sekali.
📌 Waktu henti mesin berkurang 35%.
📌 Biaya operasional keseluruhan turun sebesar 20%.
Menurut Laporan Pemotongan Industri 2023, bilah konsentrisitas tinggi meningkatkan produktivitas sebesar 10-20%, tergantung pada industrinya

6. Konsentrisitas dan Keamanan
Bagaimana Konsentrisitas Rendah Mempengaruhi Keselamatan
Pisau dengan konsentrisitas rendah menimbulkan getaran dan ketidakstabilan yang signifikan, yang dapat menyebabkan:
🔺 Kerusakan atau patahnya bilah, yang menyebabkan serpihan beterbangan berbahaya.
Pergerakan material yang tidak dapat diprediksi, meningkatkan risiko operator.
🔺 Kesalahan penyelarasan mesin, yang mengakibatkan penghentian darurat dan perbaikan.
Laporan tahun 2021 dari Administrasi Keselamatan dan Kesehatan Kerja (OSHA) menyatakan bahwa 38% cedera terkait alat pemotong disebabkan oleh penyelarasan bilah yang tidak tepat atau kegagalan akibat konsentrisitas yang buruk.
Stabilitas Mesin: Mengurangi Risiko Getaran
Kualitas Penyelarasan Blade | Dampak Getaran (mm/s²) | Tingkat Keausan Komponen Mesin | Risiko Kegagalan Mekanik |
Konsentrisitas Rendah | 12,5 mm/dtk² | Tinggi | Tinggi |
Konsentrisitas Sedang | 7,8 mm/dtk² | Sedang | Sedang |
Konsentrisitas Tinggi | 2,3 mm/dtk² | Rendah | Rendah |
📌 Mesin yang menggunakan bilah dengan konsentrisitas tinggi mengalami getaran 80% lebih sedikit, sehingga meningkatkan masa pakai bilah dan stabilitas mekanis.
Mencegah Kerusakan Pisau dan Kecelakaan di Tempat Kerja
Salah satu risiko paling parah dari bilah dengan konsentrisitas rendah adalah patahnya bilah saat dioperasikan dengan kecepatan tinggi. Hal ini dapat mengakibatkan:
🚨 Pisau terlepas secara tiba-tiba, melukai pekerja.
🚨 Tendangan balik material, merusak peralatan.
🚨 Penghentian mesin yang tidak direncanakan, mengganggu produksi.
Sebuah studi tahun 2020 di Jurnal Keselamatan Industri menemukan bahwa bilah dengan konsentrisitas tinggi mengurangi insiden kerusakan hingga 67%, mencegah pelanggaran keselamatan yang mahal dan cedera pekerja.
Studi Kasus: Peningkatan Keamanan Industri Pengolahan Makanan
Fasilitas pengolahan daging melaporkan beberapa insiden di mana bilah pisau patah karena konsentrisitas yang buruk, yang menyebabkan:
❌ Cedera yang memerlukan perawatan medis.
Risiko kontaminasi produk.
❌ Denda regulasi melebihi $50.000.
Setelah beralih ke bilah dengan konsentrisitas tinggi, mereka mengalami:
✅ Tidak ada kerusakan bilah dalam 12 bulan.
✅ Penurunan waktu henti mesin sebesar 50%.
✅ Peningkatan kepatuhan terhadap peraturan keamanan pangan.
Mengapa Memilih Nanjing Metal?
Empat Manfaat Utama dari Bilah Konsentrisitas Tinggi
- Pemotongan Presisi – Memastikan akurasi dan mengurangi pemborosan material.
- Masa Pakai Pisau Lebih Lama – Keausan yang seragam meningkatkan daya tahan.
- Efisiensi Lebih Tinggi – Mengurangi waktu henti mesin dan meningkatkan produktivitas.
- Peningkatan Keamanan – Meminimalkan risiko kerusakan dan cedera operator.
Mengapa Nanjing Metal?
- 18+ tahun keahlian dalam pembuatan bilah industri.
- Kontrol kualitas yang ketat, memenuhi standar ISO.
- Pemesinan CNC presisi, memastikan konsentrisitas yang unggul.
- Solusi bilah khusus, dirancang untuk aplikasi tertentu.
✅ Mencari pisau industri berpresisi tinggi? Hubungi Kami Sekarang untuk konsultasi gratis dan dapatkan pisau terbaik untuk industri Anda!
Referensi & Sumber Data
- Precision Tooling Institute (2022) – Analisis Tingkat Keausan Bilah Industri.
- Laporan Pemotongan Industri 2023 – Peningkatan Efisiensi dari Pisau Berkonsentrisitas Tinggi.
- Laporan Keselamatan Industri OSHA (2021) – Cedera di Tempat Kerja Terkait dengan Kegagalan Bilah.
- Jurnal Keselamatan Industri (2020) – Mengurangi Kerusakan Bilah Melalui Manufaktur Presisi.
- Jurnal Teknologi Pemotongan Industri (2023) – Dampak Konsentrisitas Bilah pada Pemotongan Presisi.
- Precision Manufacturing Institute (2022) – Studi Kasus tentang Akurasi Pemotongan & Limbah Material.
- ISO 9001 & DIN 3967 – Standar Internasional untuk Alat Pemotong Presisi.