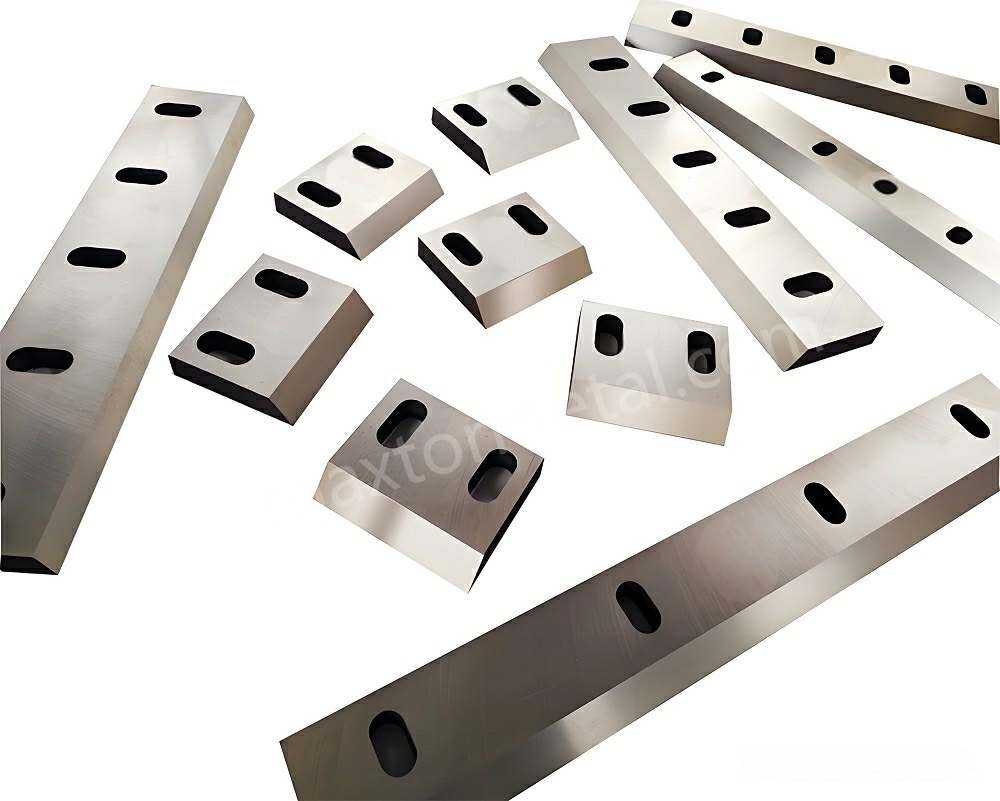
Bilah granulator durability is crucial for efficient plastic recycling. In a busy granulator, the granulator blade endures constant impact and heavy use daily. Using a weak blade leads to increased downtime, more frequent repairs, and higher costs. A plastic granulator requires a blade that can handle tough tasks without needing frequent replacement. Many facilities now opt for a pisau khusus tailored to their specific needs.
Poin-poin Utama
- Strong granulator blades made from good materials last longer and cut plastic better. D2 steel, HSS, and carbide tips are good choices.
- You should check and take care of the blades often. This means cleaning, sharpening, and using the right oil. Doing this keeps blades sharp and stops the machine from breaking down.
- Pick the right blade type and design for your plastic. This helps the machine cut better and saves energy.
- Blades that stay sharp lower repair costs and help recycle more. They also help machines work well.
- If you work with skilled manufacturers like Nanjing Metal, you get custom blades. These blades fit your recycling needs and help your machine work better.
Blade Durability
Key Factors
Komposisi Bahan
Blade durability starts with what the blade is made of. Manufacturers pick strong materials like high-carbon tool steels. These steels are tough and do not wear out fast. They have chromium and vanadium, which help stop rust and wear. Granulator blades need to handle lots of hits and rough plastic. The right steel keeps the blade sharp and stops it from rusting.
Kekerasan (HRC)
How hard a blade is matters a lot for how long it lasts. The Rockwell hardness test, using the C scale (HRC), checks this. Most granulator blades are between HRC 56 and 60. Harder blades resist wear better but can break more easily. Heat treatment helps get the best mix of hard and tough. This keeps the blade from bending and helps it stay sharp when working hard.
Retensi Tepi
Edge retention means how long a blade stays sharp. Blades that keep their edge can cut up to 30% more plastic before sharpening. Both the material and hardness affect edge retention. A blade that stays sharp longer means less stopping and more work done.
Resistance to Chipping/Wear
A good granulator blade should not chip or wear out fast. This is important in tough recycling jobs. Blades treated with heat chip up to 25% less. Good materials and careful making help blades handle shocks and stress. This stops them from breaking too soon.
Material Impact
Baja Perkakas D2
D2 tool steel is often used for granulator blades. It has HRC 58-60. Its wear resistance is 8 out of 10, and toughness is 6 out of 10. This steel is hard and strong, so it works well for most recycling jobs.
Baja Kecepatan Tinggi (HSS)
High-speed steel (HSS) is known for lasting a long time. Its wear resistance and edge retention are 9 out of 10. HSS blades last longer and work well with rough plastics. They are great for places that need strong blades and less fixing.
Pisau Berujung Karbida
Carbide-tipped blades are very hard, with HRC over 70. Their wear resistance is 10 out of 10. These blades are best for cutting rough or lots of plastic. They do not wear out or rust easily, so they are good for hard recycling work.
Granulator Blade Longevity
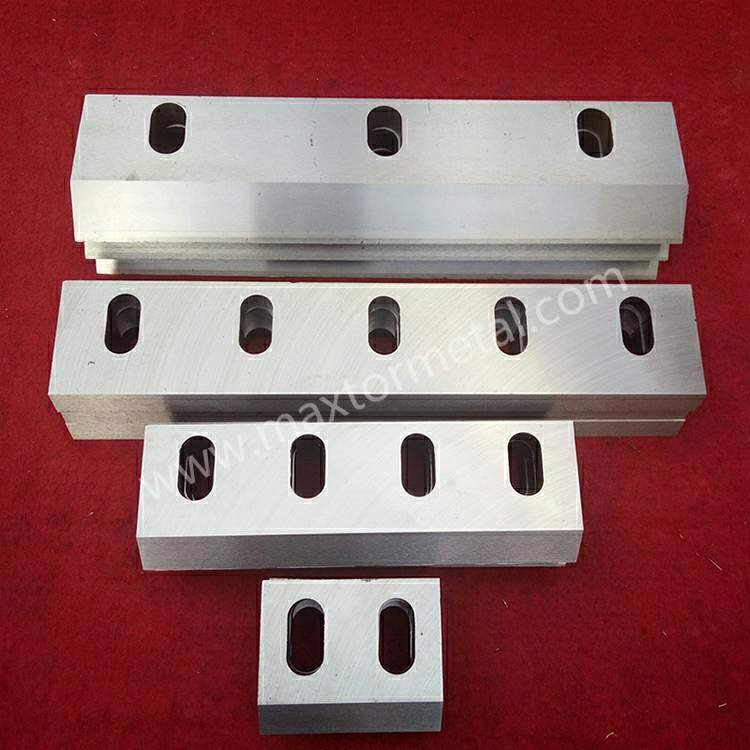
How long a granulator blade lasts affects recycling work. Operators need to spot early wear and do regular maintenance. This helps blades work well for a long time. Knowing these things lets facilities recycle more plastic with fewer stops and lower costs.
Wear Signs
Visual Indicators of Wear
Operators should look for chips, cracks, or rounded edges on blades. If the blade looks discolored or worn unevenly, it may be too hot or not lined up right. These signs show when a blade cannot cut well anymore.
Decreased Cutting Performance
If less plastic gets cut or the pieces are not even, the blade might be dull. More jams or cuts that do not finish mean the blade is having trouble. Watching for these problems helps keep the granulator working well.
Increased Power Consumption
When a blade is not sharp, the machine uses more power. If energy use goes up, the blade may be dull or broken. Checking power use can warn you when to fix or change the blade.
Unusual Noise or Vibration
Strange sounds or shaking can mean the blade is worn out or not balanced. Operators should listen for these changes. Fixing these problems fast stops more damage to the granulator.
Tips Perawatan
Regular Inspection Schedule
Having a set time to check blades helps them last longer. Facilities should look at and test blades every 2–4 minggu. Hour meters help track use and plan for checks. Keeping extra blades ready means less waiting when changing them.
Aspek | Recommendation / Benchmark |
---|---|
Frekuensi Perawatan | Check and clean blades every 2–4 weeks. Lubricate often. |
Blade Replacement (Light Use) | Change blades every 6–12 months if cutting soft plastics or used part-time. |
Blade Replacement (Heavy Use) | Change blades every 3–6 months. For tough plastics, change every 2 months. |
Blade Gap Adjustment | Keep blade gap between 0.2 and 0.3 mm for good cuts and less wear. |
Factors Affecting Lifespan | Blade life depends on plastic type, machine settings, blade quality, how you feed plastic, and dirt levels. |
Monitoring Metrics | Use sensors to watch for shaking, cutting speed, and power use. This helps know when to fix or change blades. |
Tips to Extend Lifespan | Load plastic the right way, sort out dirt, use good blades, and do regular checks. |
Proper Cleaning Techniques
Clean the machine and important parts every day to stop buildup. Take out debris after each use to stop rust and keep things running well. Do not use strong chemicals that could hurt the blade.
Sharpening and Replacement Guidelines
Sharpen blades as the maker says. If sharpening does not help or you see cracks, change the blade right away. Check and turn screens often to stop clogs and keep plastic moving. Use a checklist to make sure nothing is missed.
Lubrication and Alignment
Lubricate moving parts often to lower friction and wear. Use the right oil on bearings and gears for smooth work. Make sure blades are lined up to stop uneven wear and help them last longer. Keep the blade gap at 0.2 to 0.3 mm for best cutting.
Plastic Granulator Blades: Durability and Performance
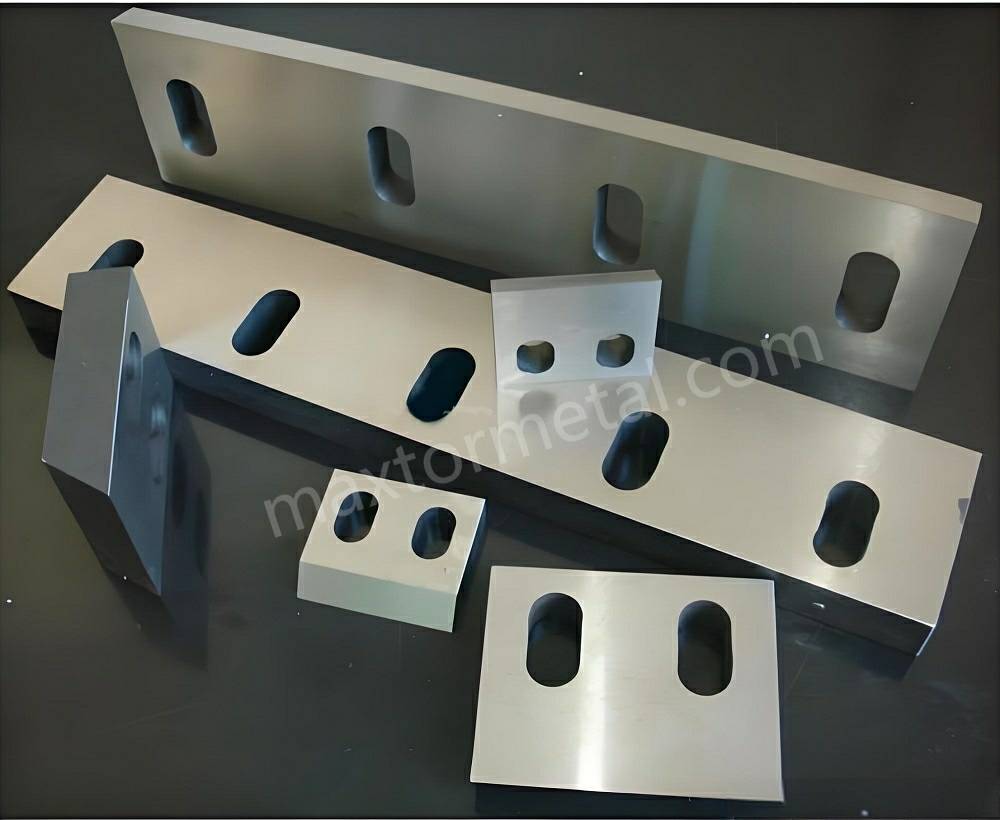
Top Materials
Baja Perkakas D2
D2 tool steel is a common choice for plastic granulator blades. It is both hard and tough. D2 blades have a hardness of HRC 58-60. They resist wear and are not too expensive. Many recycling centers use D2 blades. These blades can take many hits and stay sharp for a long time.
Baja Kecepatan Tinggi (HSS)
High-speed steel blades keep their edge longer than most. They are good at resisting wear. HSS blades cut well, even with rough plastics. Their hardness helps them last longer. Using HSS blades means less downtime and more plastic processed. Operators pick HSS for long life and steady work.
Carbide-Tipped Granulator Blade
Carbide-tipped blades are very hard, often above HRC 70. They have tungsten carbide inserts. This makes them last tiga kali lebih panjang than regular steel blades. These blades are best for places that recycle a lot of plastic. They are great when you need strong wear resistance and fast cutting.
Material Selection at Nanjing Metal Industrial
Nanjing Metal makes many types of plastic granulator blades. They offer D2, HSS, SKD-11, and carbide-tipped blades. The company uses special heat treatment and checks quality carefully. This makes sure each blade is strong and works well. Their team can design blades for special recycling jobs.
Granulator Blade Designs
Rotor Blades
Rotor blades are put on a spinning shaft. They do most of the cutting. These blades are used for many kinds of plastic. Their shape can be changed for different jobs.
Stator Blades
Stator blades do not move. They work with rotor blades to cut plastic. This setup gives steady and exact cuts. Stator blades help keep plastic pieces the same size.
Claw Blades
Claw blades have a special shape for tough jobs. They cut thick or hard plastic easily. Operators use claw blades for hard recycling work.
Specialty Designs
Specialty blades have custom shapes like hook or V-type. These are made for special recycling needs. New ways of making blades, like CNC grinding, make cuts smoother and reduce shaking. Studies show better blade designs can help recover more plastic and use less energy.
Tip: Picking the right blade shape and good materials helps blades cut better, need less fixing, and recycle more plastic.
Want better plastic granulator blades? Talk to a sales engineer at Kontak.
Ketajaman dan Retensi Tepi
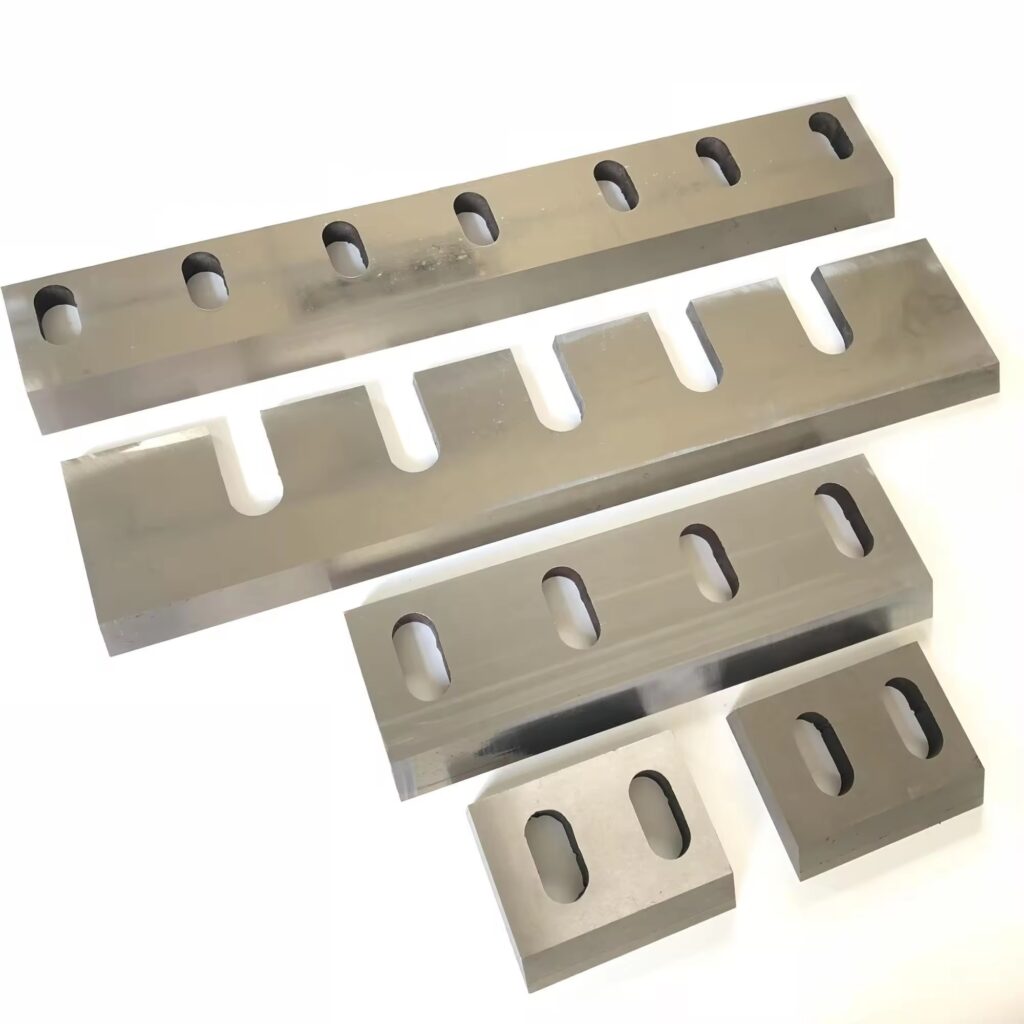
Sharpness and edge retention are very important in plastic recycling. A sharp blade makes clean cuts and keeps granule size even. When blades stay sharp, operators see fewer jams and smoother work. Blades that keep their sharpness waste less material and help machines work better.
Performance Impact
Efficiency and Energy Consumption
Sharp blades cut with less friction. Machines with sharp blades use less energy and work faster. Dull blades make more resistance, so machines use more power and slow down. Keeping blades sharp lowers energy bills and helps machines cut better.
Maintenance Frequency and Downtime
Blades that hold their edge need sharpening or changing less often. This means machines stop less and production keeps going. Using sharp blades lets workers spend less time fixing and more time recycling. Operators can plan when to do maintenance and avoid surprise stops.
Case Study: Improved Output in a Recycling Plant
A recycling plant changed from regular steel blades to high-speed steel blades. They saw 20% more plastic processed and 15% less energy used. Blade changes happened half as often. This boost came from better sharpness and edge retention, so the plant could recycle more with fewer stops.
Material Choices
D2 Tool Steel: Edge Retention and Cost-Effectiveness
D2 tool steel gives good edge retention and is not too costly. Its vanadium carbides help blades stay sharp and tough. Many places pick D2 because it works well for normal recycling jobs.
High-Speed Steel (HSS): Superior Longevity
High-speed steel blades stay sharp and last a long time. Their vanadium-alloyed structure helps them work longer. HSS blades are good for busy or rough recycling jobs, with fewer blade changes and steady cutting.
Carbide-Tipped Blades: Maximum Hardness, Lower Shock Resistance
Carbide-tipped blades are the hardest and keep their edge best. Multilayer coatings like TiN or TiAlN make blades last longer and look better. These coatings also keep blades cooler, which helps them last and saves money. Plants that recycle tough plastics often use carbide-tipped blades because they last the longest.
The Role of Heat Treatment in Edge Retention
Heat treatment makes blade materials stronger. This process helps blades stay sharp and last longer. For example, cryogenic treatment of D2 steel can make blades resist wear up to 30% more. Heat treatment helps every blade cut well and last longer.
Choosing the Right Granulator Blade
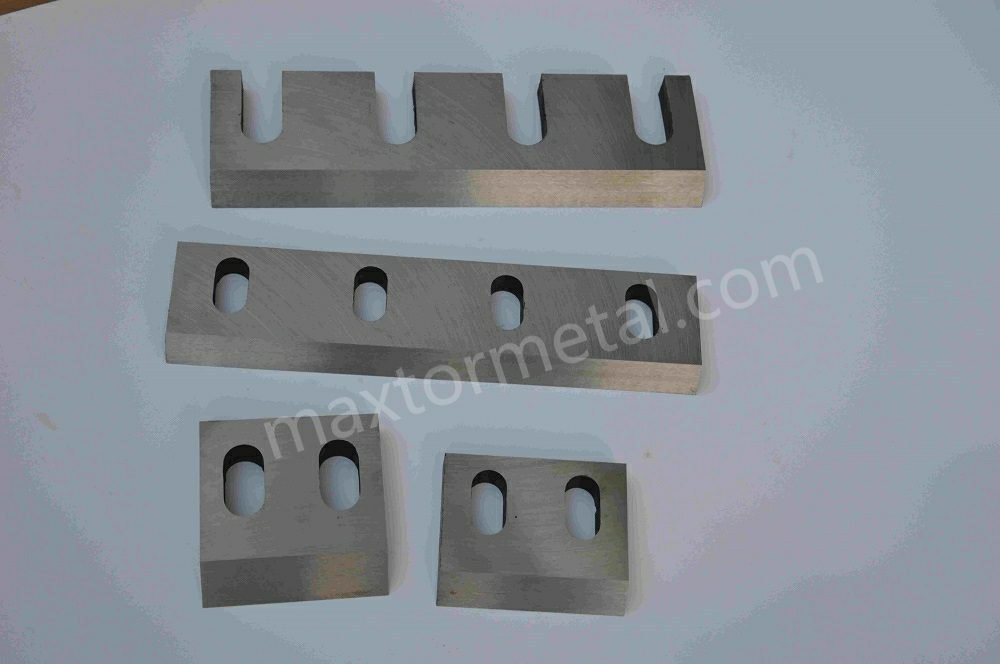
Application Match
Picking the right plastic crusher blades means knowing your recycling job. Operators need to think about what kind of plastic they are cutting. They should also know how much plastic they want to process and what size pieces they need. Every job, like blow molding or extrusion, needs a special blade shape and material. For example, if you recycle PET bottles, you might need blades with tungsten carbide tips. These tips help the blades last longer. Custom blades can be made to match the hardness and amount of plastic. This makes cutting better and helps stop the machine from stopping too much.
Data Category | Details / Examples |
---|---|
Bahan yang Diproses | Plastics, metals, food waste |
Blade Design Features | Blade angles, thickness (6mm-10mm), materials (tungsten carbide, high-speed steel, alloy steel) |
Throughput Requirements | 600 lb/hr intermittent, 2400 lb/hr instantaneous rate |
Granule Size Desired | 4 mm to 25 mm, common sizes 8-10 mm |
Feeding Methods | Manual, conveyor, pull rolls, robots, air-conveyance system |
Metrik Kinerja | Energy use, blade wear resistance, efficiency gains (e.g., 22% efficiency gain with carbide blades) |
Opsi Kustomisasi | Custom blades for specific materials and needs |
Custom plastic crusher blades help recycling centers get better results. For example, a German plant saved 40% on waste storage and handled materials 60% better after using custom blades. These blades lasted half again as long as old ones. This shows why picking the right blade for the job matters.
Cost vs. Value
When picking plastic crusher blades, buyers should think about price and value. Good blades stay sharp longer. This helps cut better and saves energy. Strong blades are easier to take care of. They are faster to change and cause less machine stopping. Over time, buying good blades means fewer repairs and lower costs.
- Good plastic crusher blades lower total costs by saving energy, needing less fixing, and stopping less.
- Help from suppliers, like warranties and quick parts, helps machines last longer and saves money.
- Plants that buy good granulator systems often get their money back fast, sometimes in less than a month.
A granulator blade that lasts a long time is made from strong materials. It also needs to be very hard and keep its edge sharp. When operators use better blades, they get better plastic pieces. They also have less machine stopping and pay less for repairs. Strong blades stay sharp longer, so the machine works better and lasts longer. New technology, like tungsten steel plating, helps blades last over 2,000 hours. This also means you do not have to fix them as often.
Tanya Jawab Umum
How often should operators replace the granulator blades?
Operators need to check blades every 2–4 weeks. If the machine works hard or cuts tough plastics, change blades every 2–3 months. Checking often helps stop surprise breakdowns and keeps recycling running well.
What are the signs of a dull or damaged blade?
A dull blade can make cuts uneven and cause loud noises. The machine might use more power. Operators may see more jams or plastic pieces that look different. These signs mean it is time to sharpen or change the blade.
Can custom blades improve recycling performance?
Custom blades fit special materials and machines. They help move more plastic and need less fixing. Many places get better results with blades made for their own recycling jobs.
Who is a trusted plastic crusher blade manufacturer for custom solutions?
Nanjing Metal is a trusted maker with 20 years of experience. They make custom blades for factories and are known for good quality and new ideas.
Lihat Juga
Temukan Pisau Peletizer Sempurna untuk Kebutuhan Pemrosesan Plastik Anda
Bilah Peletizer Dibandingkan: Temukan yang Tepat dengan Mudah
Apa Itu Bilah Peletizer dan Bagaimana Cara Kerjanya di Industri?
Cara Memilih Pisau Peletizer yang Tepat untuk Industri Anda
Panduan Lengkap Memilih Pisau Peletizer Terbaik untuk Mesin Anda