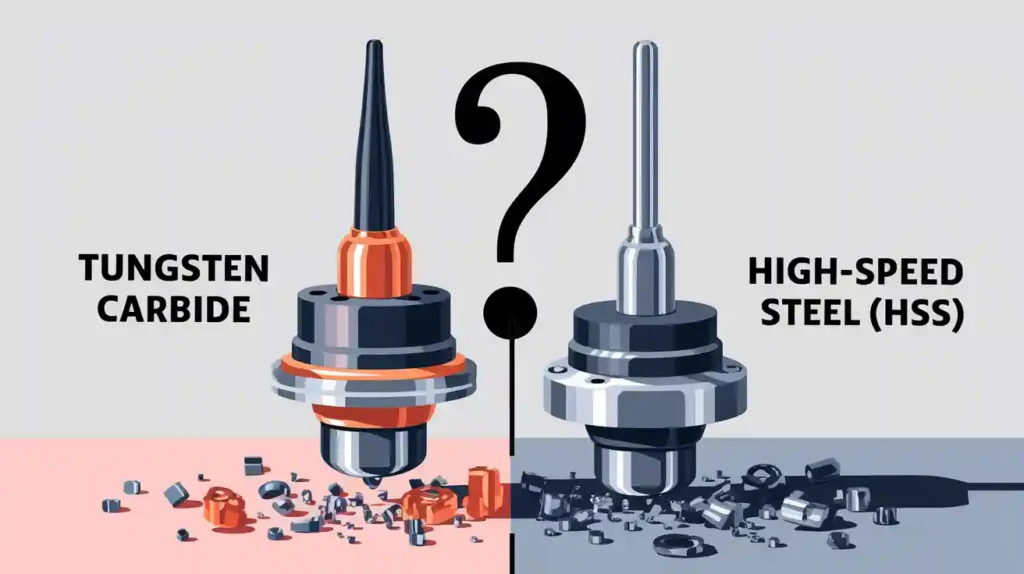
Choosing the best material for your industrial blade is crucial, and Karbida Wolfram stands out for its exceptional hardness and wear resistance. This makes it ideal for cutting tough or rough materials quickly and efficiently. Nanjing Metal specializes in providing high-quality Tungsten Carbide custom blades tailored to meet specific industrial needs. While high-speed steel (HSS) is versatile and suitable for applications requiring frequent tool changes, Tungsten Carbide remains the preferred choice for durability and performance. The table below highlights the global tungsten consumption in 2024:
Jenis Bahan | Percentage of Global Tungsten Consumption |
---|---|
Tungsten Carbide Products | 65% |
Steels / Super-Alloys (including HSS) | 14% |
Tungsten Metal Products | 12% |
Chemicals & Others | 9% |
As shown, the majority of tungsten is used in Tungsten Carbide products, underscoring its importance in industrial blades. The Asia-Pacific region leads this market, with a significant demand for pisau khusus solutions.
Poin-poin Utama
- Tungsten Carbide blades stay sharp for a long time. They cut hard materials faster than High-Speed Steel blades. This makes them good for tough jobs and big projects.
- High-Speed Steel blades are tougher and can handle impacts better. They are good for jobs with sudden shocks or when you change blades often.
- You should pick a blade based on what you cut. Think about how often you cut and your budget. Tungsten Carbide is best for hard, rough materials and when you use blades a lot. High-Speed Steel is better for softer materials and different kinds of jobs.
- Custom industrial blades can help you cut more accurately. They fit your machines better and lower downtime. This helps you save time and money.
- Nanjing Metal gives you high-quality custom blades. They offer expert help, advanced manufacturing, and good service for your cutting needs.
Perbedaan Utama
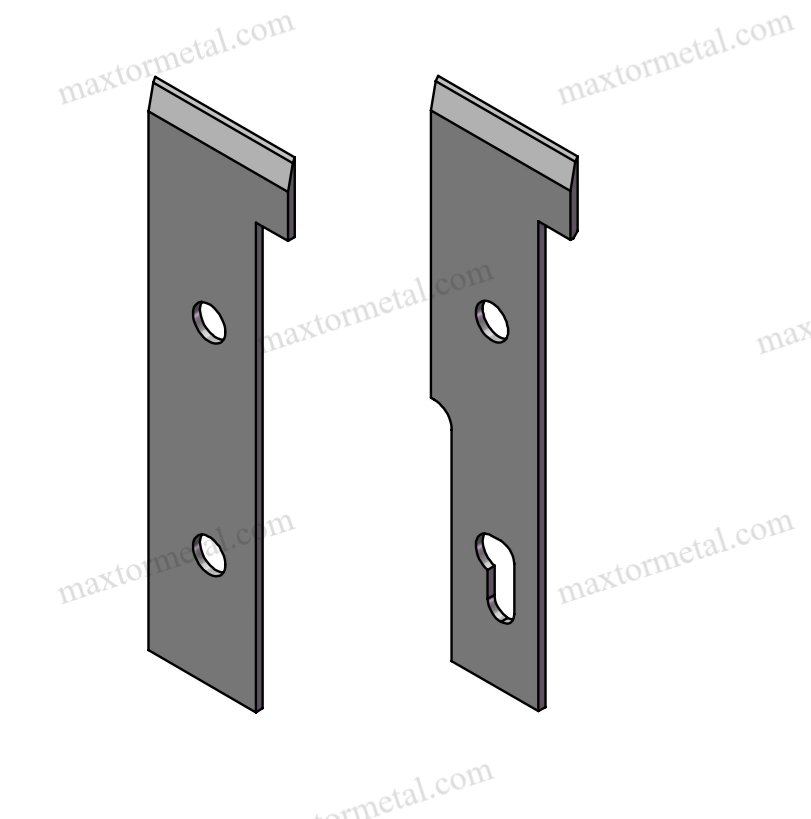
Tabel Perbandingan
Tungsten Carbide vs High-Speed Steel (HSS) – Key Properties
It is important to know how these materials work when cutting. The table below lists the main things that matter for people using industrial blades:
Milik | Baja Kecepatan Tinggi (HSS) | Karbida Wolfram |
---|---|---|
Hardness & Wear | High; stable up to ~500°C | Extremely high; stable up to 1000°C |
Kekerasan | High; less brittle | Lower; more brittle, can chip |
Stabilitas Termal | Good up to 500°C | Excellent up to 1000°C |
Cutting Speed & Tool Life | Suitable for moderate speeds; good durability | Handles much higher speeds; lasts much longer |
Cost & Manufacturing | More affordable; easier to make | More expensive; needs special equipment |
Aplikasi Umum | Drill bits, taps, general cutting tools | Industrial blades, wear plates, rock drilling |
Machinability | Easy to process | Hard to process; needs special tools |
Tip: If you want a blade that stays sharp for a long time and cuts tough stuff, choose Karbida Wolfram. If you need a blade that can take more hits and is easy to swap, HSS might be better.
Komposisi Bahan
Karbida Wolfram
Karbida Wolfram is made by mixing tungsten carbide powder with a metal binder, usually cobalt. The mix usually has 70% to 97% tungsten carbide and 3% to 30% cobalt. The high amount of tungsten carbide makes the blade very hard and helps it last longer. Cobalt holds the blade together and gives it some toughness so it does not break easily.
The size of the grains and the amount of cobalt change how the blade works. Smaller grains and less cobalt make the blade harder and help it last longer. More cobalt and bigger grains make the blade tougher and better at handling shocks. For industrial blades, fine grains are used to keep the edge sharp and stop chipping.
Baja Kecepatan Tinggi (HSS)
Baja Berkecepatan Tinggi is a type of steel with many elements mixed in. It has tungsten, molybdenum, chromium, vanadium, and carbon. The usual mix is 0.6% to 1.3% carbon, 4% to 18% tungsten, 1% to 5% molybdenum, 3% to 5% chromium, and 1% to 4% vanadium. These elements work together to make HSS tough, heat-resistant, and useful for many jobs.
HSS has a complex structure with tiny carbides and particles. These help the blade last longer and stay strong. Tungsten and molybdenum make it harder and help it handle heat. Chromium and vanadium add toughness and help it resist wear. This mix makes HSS a good pick for tools that need to handle hits and changing loads.
Catatan: Pick the material that fits your needs best. Choose the one with the most hardness and wear resistance, or the one with better toughness and impact resistance.
- Karbida Wolfram tools can last up to 10 times longer than HSS tools in tough jobs.
- HSS is better at handling impacts, so it works well for jobs with sudden shocks or changing loads.
- Karbida Wolfram costs more and is harder to make, but it works best in fast and tough jobs.
Tungsten Carbide in Industrial Blades
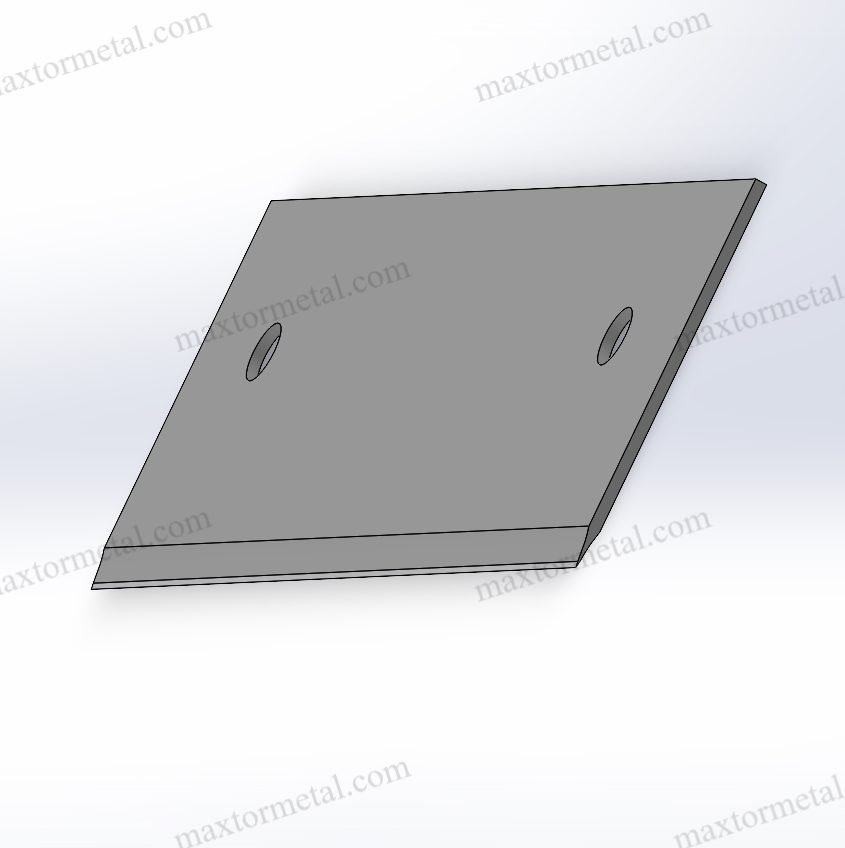
Kekerasan dan Ketahanan Aus
Comparative Hardness and Wear Resistance Data
When picking a blade for cutting, hardness is very important. Karbida Wolfram blades are much harder than high-speed steel blades. Their Vickers Hardness is between 1600 and 2200 HV. High-speed steel blades are only about 700 to 900 HV. This means Karbida Wolfram blades stay sharp longer. They work well even on tough or rough materials.
These blades keep their hardness at high heat, up to 1000°C. High-speed steel loses hardness above 500°C. So, Karbida Wolfram is better for jobs with lots of heat. The special mix of tungsten carbide and cobalt helps these blades work better. The sintering process also makes them strong. You can trust these blades for hard jobs and tough materials.
Tip: Harder blades last longer and need fewer changes. This saves you time and money.
Application Example – Paper Industry
In the paper industry, sharp blades are very important. Karbida Wolfram blades are used to cut and slit paper rolls. These blades stay sharp and keep their shape longer than high-speed steel blades. You will not need to change blades as often. This means your machines can run more and stop less. You get less downtime and more work done.
Studies show these blades give cleaner and more exact cuts. You will see better results and lower costs for repairs. Their sharpness and wear resistance make them the best choice for cutting paper and similar jobs.
Cutting Speed and Tool Life
Performance Comparison with HSS
You want blades that cut fast and last a long time. Karbida Wolfram blades can cut 4–7 times faster than high-speed steel blades. For example, they can cut alloy steel at about 160 meters per minute. High-speed steel blades work best at about 70 meters per minute.
Parameter | Pisau Baja Kecepatan Tinggi (HSS) | Bilah Tungsten Karbida |
---|---|---|
Kecepatan memotong | ~70 m/min (steel) | ~160 m/min (alloy steel) |
Umur Alat | Good, but shorter | 5–10x longer |
Tahan Panas | Hingga 500°C | Hingga 1000°C |
Karbida Wolfram blades also last much longer. They can last 5–10 times longer than high-speed steel blades. This means you will not need to change blades as much. You save time and money on labor. Even though these blades cost more at first, they save you money over time.
Catatan: Longer tool life and faster cutting mean your machines work better and you get more done.
Skenario Aplikasi Umum
Karbida Wolfram blades are used in many industries where high performance is needed. Here are some common uses:
- Cutting metal sheets, thick rubber, plastics, and composites
- Making car parts by cutting aluminum very precisely
- Trimming composite materials and alloys in airplanes
- Making medical tools that need to be very exact
- Slicing meat, vegetables, and cheese in food factories
These blades are best for places that make a lot of products all the time. You can count on them for high efficiency and little downtime. They stay sharp and resist wear, so they are great for cutting hard or rough materials. You will also see them in woodworking, metalworking, and paper cutting, where being tough and exact is important.
If you want a blade that stays sharp, cuts fast, and lasts long, Karbida Wolfram is the best choice for your cutting needs.
High-Speed Steel (HSS) in Industrial Blades
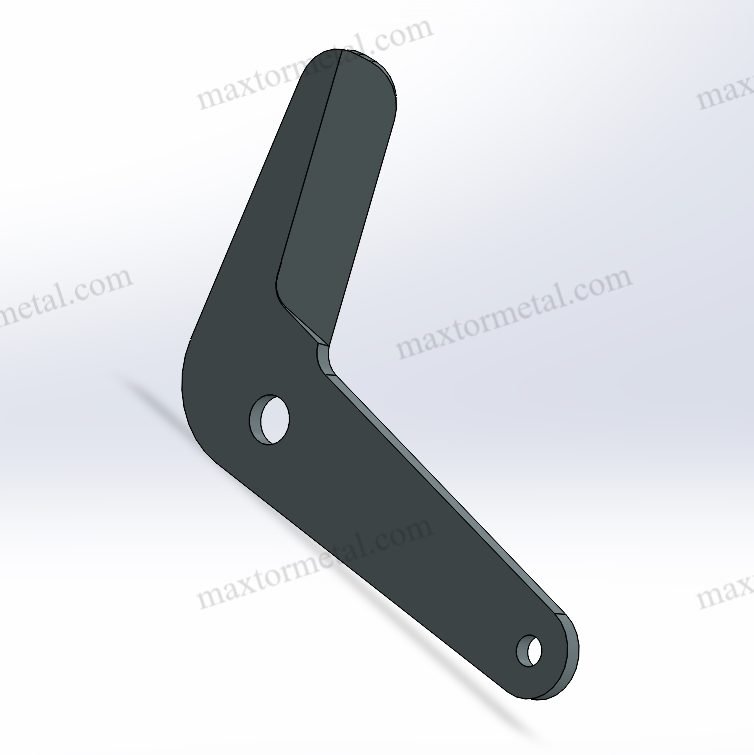
Toughness and Impact Resistance
High-Speed Steel is known for being tough and handling impacts well. HSS blades do not break easily when used. They can bend a bit if pushed hard, instead of snapping. This makes them good for jobs with sudden hits or shocks.
Application Examples in Metalworking and Woodworking
You often see HSS blades in metal and woodworking shops. In metalworking, HSS blades cut softer metals, drill, and shape parts. They are used to make holes in steel beams or trim metal sheets. In woodworking, HSS blades cut hardwood, softwood, and plywood. They are used in saws, planers, and routers. HSS blades also cut plastic and other soft materials easily.
Comparison with Tungsten Carbide
Aspek | Baja Kecepatan Tinggi (HSS) | Tungsten Carbide (WC/Co) |
---|---|---|
Common Failure Modes | Cracking under impact or stress | Cracking or catastrophic failure under sudden impact; abrasion, adhesive, and erosion corrosion wear |
Kekerasan | High toughness and ductility; better resistance to cracking | More brittle; prone to cracking due to hardness and brittleness |
Ketahanan Aus | Moderate wear resistance | Superior wear resistance and hardness |
Aplikasi yang Cocok | Dynamic environments with impacts | Steady, abrasive cutting conditions |
Failure Risk Mitigation | Selection of appropriate grade and design to enhance toughness | Selection of appropriate grade to balance hardness and toughness |
HSS blades resist cracking better than tungsten carbide blades. HSS can take more hits and still work. Tungsten carbide is harder but can break if dropped or hit too hard. If your job has sudden impacts or changing loads, HSS is safer and more reliable.
Tip: Pick HSS blades for jobs with lots of vibration or shock. They last longer in these tough situations.
Versatility and Cost
High-Speed Steel blades are flexible and work for many tasks. You can use them on different materials. HSS blades cost less, so they are a smart choice for many shops.
Material Compatibility and Performance
- HSS blades cut wood, metal, and plastic easily.
- You can use HSS for softer metals like aluminum and mild steel.
- HSS blades work well for plastics and composite materials.
- These blades handle rough milling and heavy cuts better than carbide because they are less brittle.
- HSS tools work well when setups are not stable or the workpiece moves.
- You can use HSS blades for small jobs and many different tasks.
Tungsten carbide blades are best for hard metals, abrasive materials, and big production runs. They keep their edge longer but do not handle shock as well as HSS.
Catatan: HSS blades are more forgiving if your machine setup is not perfect or if you switch between materials.
Market Price Range
HSS blades cost less than tungsten carbide blades. They are cheaper because they are easier to make and use less expensive materials. This makes HSS a good choice if you want to save money or need many blades.
Cost Comparison with Tungsten Carbide
Tungsten carbide blades cost more at first because of expensive materials and harder production. But they last longer and work better for tough jobs. If you run a big factory or cut hard stuff all day, carbide blades can save money over time by needing fewer changes.
For smaller shops or jobs that do not need extreme hardness, HSS blades cost less. You get good results for less money. HSS blades are easy to replace and sharpen, so you save on maintenance.
Summary Table: Cost-Effectiveness
Jenis Aplikasi | Best Choice | Mengapa? |
---|---|---|
High-volume, tough jobs | Karbida Wolfram | Longer life, less downtime |
Low-volume, varied work | Baja Kecepatan Tinggi (HSS) | Lower cost, easy to replace and sharpen |
Tip: If you want to save money on general cutting or need blades for many jobs, HSS is a smart pick. For heavy-duty, non-stop work, think about carbide for long-term savings.
Skenario Aplikasi
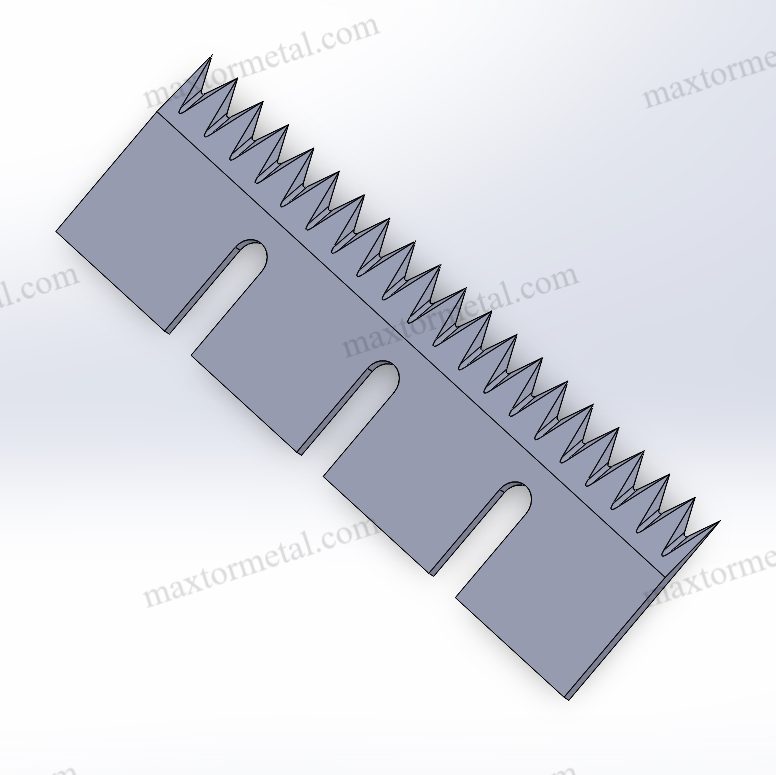
When to Use Tungsten Carbide
High-Volume, Continuous Production
Pick Tungsten Carbide blades if your factory runs all day. These blades are best for cutting lots of material without stopping. They stay sharp much longer than most other blades. You will not need to change them as often. This helps you get more work done. Special finishes and edge treatments make these blades even stronger. These upgrades help the blades last longer and stop them from chipping. This is important when machines run for a long time.
Cutting Hard or Abrasive Materials
Use Tungsten Carbide blades for cutting tough or gritty stuff. These blades can handle hard metals and rough materials very well. In farming, tools with this material last much longer than regular steel. Farmers use them for plowing and harvesting. They do not need to change blades as much and save money. Other industries also use these blades for rough jobs every day.
Applications Requiring Minimal Downtime
You want your machines to keep running without stopping. Tungsten Carbide blades help you do this. They last a long time, so you do not need to stop for blade changes. Special coatings make these blades even better at handling heat and wear. This keeps your machines working and helps you finish jobs on time.
Industries: Metalworking, Woodworking, Paper Processing, Plastics
Many industries use these blades for their hardest jobs. In metalworking, they cut thick sheets and hard metals easily. Woodworking shops use them for smooth cuts in hardwood. The paper industry uses them to trim and slit big rolls. Plastic factories use them to cut tough plastics. If you cut a lot or work with hard stuff, these blades are a good choice.
Tip: Want fewer blade changes and more work time? Try these blades for your hardest jobs.
When to Use HSS
Applications Requiring High Impact Resistance
Choose high-speed steel (HSS) blades for jobs with sudden hits. These blades bend instead of breaking, so they are safer. HSS works well if you hit knots in wood or tough spots in metal.
Frequent Tool Changes or Short Production Runs
If you change blades a lot or do short jobs, HSS is a smart pick. These blades are easy to sharpen and swap out. You can save money and work on many tasks. HSS blades are great for shops with lots of different jobs.
Budget-Conscious Operations
HSS blades cost less than carbide blades. You get good results without spending too much. If you want to save money and still get good cuts, HSS is a good choice. These blades are easy to keep sharp, which helps you stick to your budget.
Industries: General Metalworking, Woodworking, Maintenance Shops
You see HSS blades in many metal and wood shops. Maintenance teams use them for repairs and quick fixes. These blades work for drills, saws, and milling tools. They cut many materials and stay sharp under heat. Bi-metal blades, made with HSS and spring steel, last longer and cut straighter than plain steel blades. HSS blades do not chip or dull easily, even in tough jobs. Many people say they get cleaner cuts and less waste with HSS blades.
- HSS is best for jobs needing heat resistance and some toughness.
- You can use HSS for careful cutting, woodworking, and repairs.
- These blades give a good mix of strength and price, so many shops like them.
Note: If you want a blade that is strong, easy to sharpen, and not expensive, HSS is a good choice for many daily jobs.
Choosing the Right Material
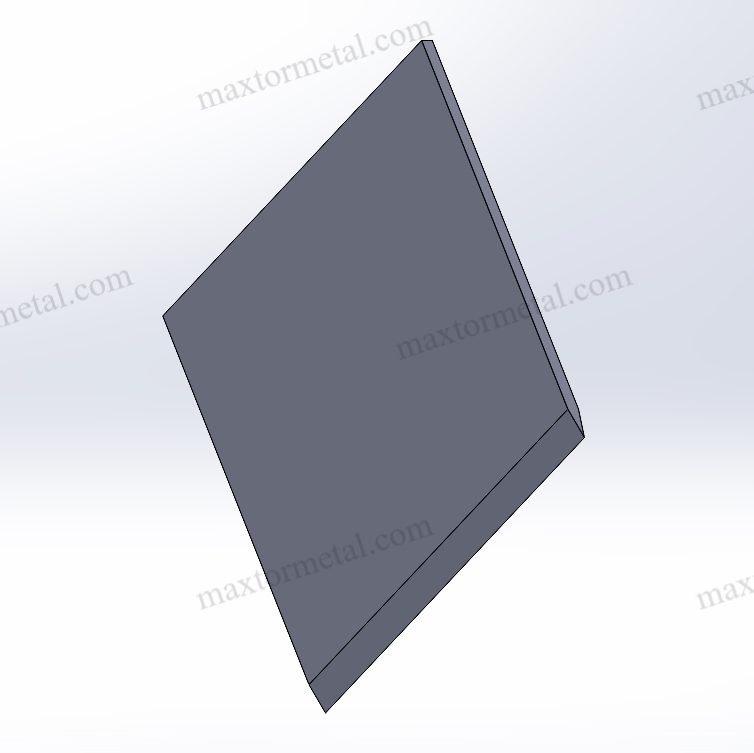
Bahan yang Akan Dipotong
Hardness and Abrasiveness of the Material
When you choose a blade, you need to look at what you want to cut. Some materials are very hard or rough. Others are softer and easier to cut. The right blade material helps you get the best results and saves you money.
- Hard materials, like hardened steel or ceramics, need a blade that can stay sharp and resist wear.
- Abrasive materials, such as fiberglass or composites, quickly dull regular blades.
- Softer materials, like mild steel, wood, or plastic, do not wear down blades as fast.
- If your workpiece has a rough surface or contains hard particles, you need a blade with high wear resistance.
You should also think about how fast you want to cut and if the job needs a tough blade or a hard one.
Suitability of Tungsten Carbide for Hard or Abrasive Materials
Tungsten Carbide blades work best for hard or abrasive materials. These blades have exceptional hardness and wear resistance. You can use them for high-speed cutting and for jobs where you need the blade to stay sharp for a long time. If you cut things like hardened steel, glass, or abrasive composites, this material gives you a clean cut and a long tool life. The fine grain size and binder content in the blade help balance hardness and toughness. This makes the blade strong enough for tough jobs but still able to keep a sharp edge.
Suitability of HSS for Softer or Less Abrasive Materials
High-speed steel (HSS) blades are a good choice for softer or less abrasive materials. These blades offer high toughness and shock resistance. You can use them for cutting wood, mild steel, or plastic. HSS blades handle interrupted cuts and sudden impacts better than harder blades. If your job involves frequent tool changes or you need a blade that can take a hit, HSS is a smart pick. You also save money because these blades cost less and are easy to sharpen.
Frekuensi Penggunaan
High-Volume, Continuous Use
If you run your machines all day and cut large amounts of material, you need a blade that lasts. Tungsten Carbide blades keep their edge much longer than steel blades. You do not need to stop your machines often to change blades. This saves you time and reduces downtime. These blades work well in factories where stopping the line costs money. You get more work done with fewer interruptions.
- Tungsten Carbide blades last longer under abrasive conditions.
- You reduce maintenance and replacement costs.
- You keep your production line running smoothly.
Intermittent or Low-Volume Use
If you only cut materials sometimes or in small batches, high-speed steel blades may suit you better. These blades handle impacts and shocks well. You can use them for jobs where you start and stop often. HSS blades cost less, so you do not spend much on tools you use less often. They are also easy to replace and sharpen, which helps you keep costs down.
- HSS blades absorb impacts better.
- You save money on tools for small or varied jobs.
- You can switch blades quickly for different tasks.
Anggaran
Initial Investment vs. Long-Term Cost
You need to think about both the price you pay at first and the money you spend over time. Tungsten Carbide blades cost more upfront. They last much longer, so you buy fewer blades and spend less on replacements. High-speed steel blades cost less to buy, but you need to replace them more often.
Faktor | Karbida Wolfram | Baja Kecepatan Tinggi (HSS) |
---|---|---|
Initial Material Cost | Tinggi | Rendah |
Umur Alat | Panjang | Pendek |
Proses Manufaktur | Complex | Simple |
Labor and Automation | Higher at first, but less over time | Lower overall |
Waste and Efficiency | Less waste, more efficient | More waste, less efficient |
Cost-Effectiveness in Different Scenarios
Tungsten Carbide blades give you the best value in high-volume, demanding jobs. You spend more at first, but you save money over time because you do not need to change blades as often. These blades also help you keep your machines running, which means you get more work done.
- You get lower long-term costs in busy factories.
- You reduce downtime and maintenance.
- You improve efficiency and save on labor.
High-speed steel blades work well if you want to save money now or if you do not use your blades all the time. You pay less at first, but you may spend more on replacements and downtime. These blades are a good choice for small shops or jobs that do not need extreme hardness.
Tip: Think about how often you use your blades and what you cut. The right choice helps you save money and get better results.
Custom Industrial Blades
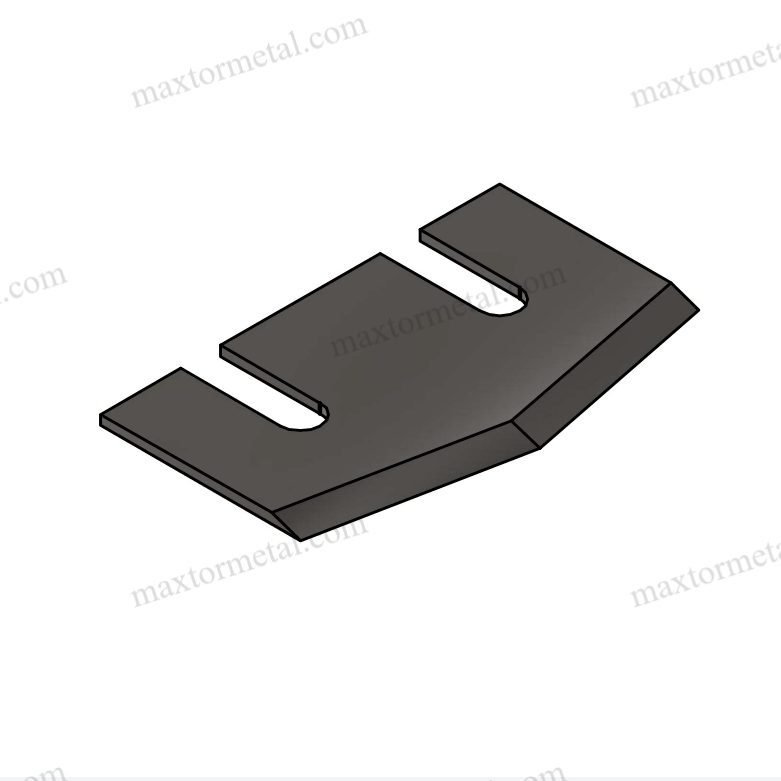
Mengapa Kustomisasi Itu Penting
Every cutting job is not the same. Sometimes, you need blades that fit your machines just right. Some jobs need blades for special materials. Custom industrial blades help you do these jobs better. Here are some reasons why custom blades are important:
- You get cuts that are exact, even with odd materials or sizes.
- Custom blades fit your needs and work better with your machines.
- The right blade design and material help it last longer and need fewer changes.
- Custom blades make your workplace safer and lower repair costs.
- You can pick the edge angle, thickness, and length to fit your job and stop delays.
- Special materials like SKD11, D2, and 6CrW2Si keep the blade hard and strong.
- Pisau Kustom help industries like aerospace, cars, electronics, and building by meeting tough cutting needs.
Custom blades save you time and money by stopping delays and making work faster. You also get safer work and better results with blades made for your job.
Layanan Nanjing Metal
Nanjing Metal is a trusted maker of custom industrial blades. They have 20 years of experience and are known for good quality and service. You get help from a skilled team that knows what you need.
- Nanjing Metal makes custom blades and helps with design changes to make them work better.
- They use advanced CNC machines and 3D printing for high quality and accuracy.
- You get strong quality checks at every step, from picking materials to the final check.
- Nanjing Metal offers both ODM and OEM services, making blades from your drawings or samples.
- They handle shipping and customs, so importing is easy for you.
- Many industries like food, packaging, recycling, metal cutting, plastics, rubber, textiles, and printing use these services.
- You get blades that help you work faster, save money, and support your green goals.
If you want to know more or talk about your needs, click Kontak to reach a sales engineer. Get the right blade for your special job today!
- Pick Tungsten Carbide if you cut a lot and need blades that last.
- HSS is better for jobs where blades must be tough or changed often.
- It is smart to choose the blade material that fits your job, budget, and what you are cutting.
- Custom blades can help you fix special problems and make work faster.
Tanya Jawab Umum
What is the main difference between Tungsten Carbide and HSS blades?
Tungsten Carbide blades stay sharp longer and cut harder materials. HSS blades handle impacts better and cost less. You should choose based on your cutting needs.
Can I use Tungsten Carbide blades for all materials?
You can use Tungsten Carbide blades for many tough jobs. They work best on hard or abrasive materials. For softer or less demanding tasks, HSS blades may be a better fit.
How do I know which blade material is right for my job?
Think about what you cut, how often you cut, and your budget. If you need long-lasting sharpness, pick Tungsten Carbide. If you want flexibility and lower cost, choose HSS.
Lihat Juga
Menguasai Seni Pisau Tungsten Carbide
Bagaimana cara memperpanjang masa pakai pisau melingkar baja tungsten secara efektif?
10 Besar Pemasok dan Produsen Bilah Pemotong Peletizer yang Perlu Anda Ketahui di Tahun 2025
10 Besar Produsen dan Pemasok Pisau Peletizer Cincin Udara Teratas di Tahun 2025
Cara Mengganti Bilah Pelat Die Peletizer dengan Aman dan Efisien
Temukan Pisau Peletizer Sempurna untuk Kebutuhan Pemrosesan Plastik Anda
Tanggapan 2