Summary:
This article provides a comprehensive guide to enhancing the cutting precision of printer slotter knives used in carton manufacturing. Through regular maintenance, precise alignment, optimal blade settings, and digital monitoring, companies can achieve accurate cuts, reduce waste, and increase productivity by up to 25%.
Introduction: The Importance of Cutting Precision in Printer Slotter Knives
Achieving high cutting precision is crucial in the carton manufacturing industry. Accurate cuts reduce waste, improve quality, and maximize production efficiency. For businesses working with corrugated boxes, precision in cutting edges and slots ensures products meet quality standards and customer expectations. Printer slotter knives, commonly used for cutting and creasing corrugated boards, are essential for this level of precision. However, without proper maintenance and optimization, even the best knives can produce inconsistent results, leading to increased costs and wasted materials. In this article, we’ll explore the key factors that affect slotter knife precision and provide actionable tips for enhancing cutting accuracy.
1. Understanding Key Factors Affecting Printer Slotter Knife Precision
Several factors influence the precision of slotter blades in carton manufacturing. Here are the primary elements to consider:
Knife Material and Sharpness
The material and sharpness of a knife significantly affect its cutting ability. Slotter blades made of high-grade materials like tungsten carbide or high-speed steel provide sharper, longer-lasting edges. Studies show that knives made from tungsten carbide maintain sharpness 10–15% longer than standard steel, reducing downtime for sharpening and replacement. Sharpness also impacts precision; a dull blade can tear or fray carton edges, making alignment and quality difficult to maintain.
Alignment and Positioning
Precise alignment of the slotter knives is essential for accurate cuts. Misaligned blades result in skewed edges and uneven slots. Regularly checking and adjusting knife alignment ensures that the knives stay parallel and cut at consistent angles. Many manufacturers invest in digital alignment tools that allow for high accuracy in positioning, often improving production speeds by 5–10%.
Machine Calibration
Slotting machines require regular calibration to operate correctly. Calibration includes setting the machine’s tension, verifying blade positioning, and checking for any wear or looseness in the setup. Proper calibration maintains cutting accuracy and prevents common errors that reduce quality. Machine experts recommend calibrating slotter machines every three months or after any major maintenance work to maintain high accuracy.
Operating Conditions
Environmental conditions such as temperature, dust, and humidity can impact blade performance. Excessive heat, for example, can cause metal expansion, impacting the alignment and sharpness of blades. To prevent such issues, it’s advisable to maintain a stable environment for slotting machines and implement routine cleaning to reduce dust accumulation.
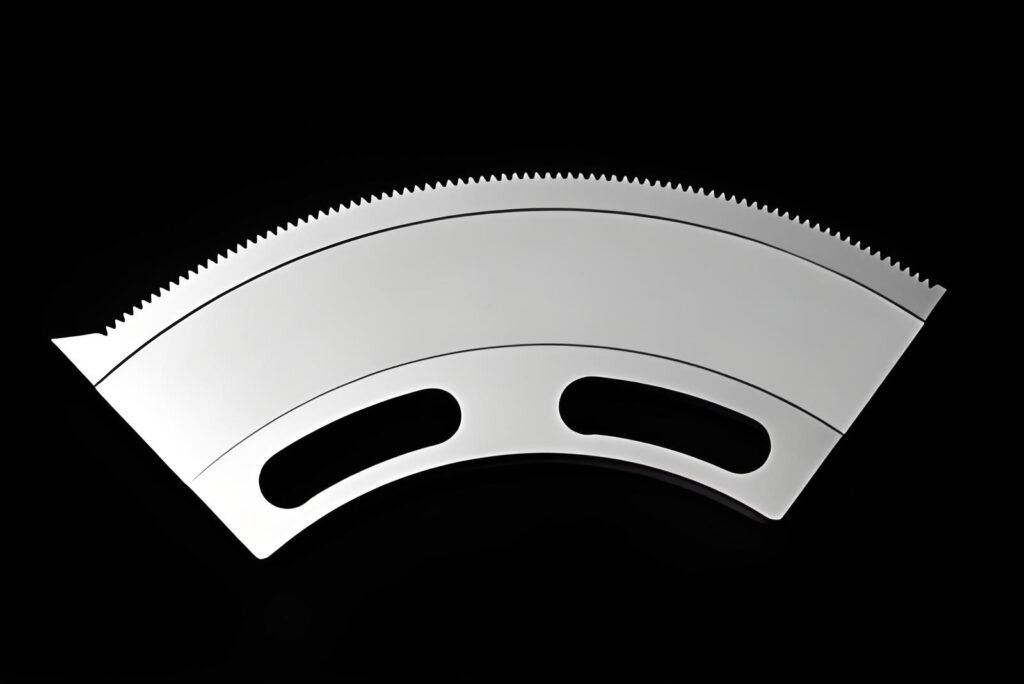
2. Essential Maintenance Practices for High Cutting Precision
Maintaining high cutting precision requires a commitment to regular maintenance, which directly impacts productivity and product quality. Proper maintenance of slotter knives and the slotting machine itself can reduce costly downtime and improve cut accuracy by up to 25% over time. Here’s a closer look at each key maintenance step and how it contributes to better performance.
Regular Sharpening and Replacement
Sharpness is a critical factor in ensuring consistent and precise cuts. Dull blades not only produce uneven edges but also increase the risk of tearing and fraying, which compromises the appearance and structural integrity of the carton. As a general guideline, it is recommended to sharpen slotter knives after every 8–10 hours of continuous use or at the end of each production shift, depending on the material’s hardness and thickness. Research shows that routine sharpening can extend blade life by 15–20%, thereby reducing replacement frequency and minimizing machine downtime.
- Pro Tip: Use a professional sharpening service or invest in high-quality sharpening tools. Automated sharpening systems, while more costly, can improve sharpening accuracy and consistency by 10–15% compared to manual methods.
Alignment Checks
Precise alignment is essential to avoid miscuts and ensure that the blade operates efficiently. Misalignment of as little as 0.5 mm can lead to defective cuts and increase material waste. Regularly performing alignment checks, especially at the start of each production shift, can prevent these issues and improve overall accuracy. Some operators use digital alignment tools, which are becoming more popular due to their ease of use and reliability. These tools can detect and correct alignment discrepancies with up to 98% accuracy, helping operators maintain consistent cutting quality.
- Industry Data: Studies indicate that consistent alignment checks can reduce defective cuts by up to 30%, resulting in smoother production flow and less rework.
Lubrication and Cleaning
Proper lubrication and cleaning are essential to ensure smooth blade movement and prevent premature wear. Dust, adhesive residues, and paper particles often accumulate on slotter knives, which can cause drag and hinder the blade’s ability to make smooth cuts. Operators should apply lubricant to the slotting machine’s moving parts, including the blade shaft and bearings, according to the manufacturer’s recommendations. Generally, lubricating every 48 hours is adequate for most high-speed slotting machines.
- Cleaning Frequency: Clean the knives at least once per shift, or more frequently in dusty environments, as accumulated residue can impact cut quality by 5–10%. Using compressed air or a soft brush helps remove fine particles without damaging the blade.
Inspection Routine
Regular inspections provide an opportunity to detect wear and potential damage early, preventing unexpected downtime and costly errors. A detailed inspection routine should include:
- Visual Examination: Check for visible signs of wear, chipping, or warping on the blade’s edge. Replace damaged blades immediately to avoid damaging materials.
- Blade Test: Run a simple test on a sample carton to verify that the cut quality meets specifications. This can help identify issues that may not be visible upon inspection.
- Performance Logging: Keep records of each blade’s performance to identify trends in wear and anticipate replacement needs. Data indicates that companies using performance logs experience up to 15% less downtime due to early detection of wear patterns.
By following a consistent maintenance routine, operators can ensure that their slotter knives deliver high precision, reduce waste, and maintain productivity levels.
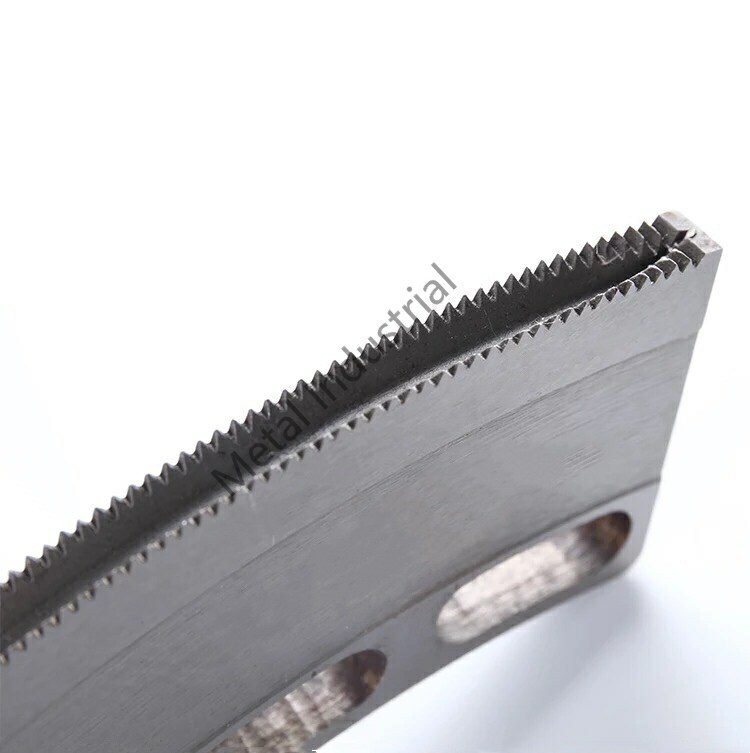
3. Upgrading to High-Precision Printer Slotter Knives
Investing in high-quality slotter blades can yield significant benefits for manufacturers aiming to achieve precise cuts. High-precision knives, often made from premium materials like hardened steel or tungsten carbide, are engineered to deliver consistent and accurate cuts with minimal maintenance.
Types of High-Precision Slotter Knives
There are several types of high-precision knives on the market, including beveled, serrated, and straight-edge blades. Each type has unique advantages based on cutting requirements:
- Beveled blades provide smoother cuts and are ideal for delicate carton materials.
- Serrated blades work well for tougher materials and can prevent fraying.
- Straight-edge blades offer versatility for general-purpose cutting.
Benefits of Premium Materials and Designs
High-precision slotter knives use top-tier materials designed for durability and precision. Studies show that premium-grade knives can improve accuracy by up to 20% and reduce sharpening needs by as much as 30%, enhancing overall productivity. For high-volume carton manufacturers, these gains add up quickly, leading to lower operating costs and higher profit margins.
4. Tips for Optimizing Printer Slotter Knife Performance
Optimizing the performance of slotter knives involves more than just regular maintenance. Making small adjustments to cutting speed, blade angles, and monitoring can enhance accuracy, especially for large production volumes. Here are some detailed strategies to maximize cutting precision and efficiency.
Adjusting Cutting Speed
Cutting speed directly affects the quality and precision of the cuts. Generally, a slower speed can result in cleaner, more accurate cuts, especially for delicate materials. Studies show that reducing cutting speed by 10–15% can lead to a 20% improvement in cut quality for thin and fragile cartons. However, for heavier, thicker materials, moderate speeds may yield the best results without compromising productivity.
- Optimization Tip: Consider testing different speeds with each new batch of materials. Running a few test cuts at various speeds allows operators to identify the optimal balance between speed and precision.
Optimizing Cutting Angles
The angle at which the slotter knife meets the carton significantly affects edge quality. A 45-degree angle often works well for standard carton materials, but adjusting the angle to as low as 30 degrees for softer or thinner materials can reduce fraying and produce smoother edges. Precision in cutting angles can improve cut quality by as much as 18%, according to industry data.
- Angle Adjustment: Operators should monitor edge quality and adjust the blade angle according to the material being processed. Some machines allow for automatic angle adjustments, which can streamline this process for high-volume operations.

Using Digital Monitoring
Digital monitoring systems provide real-time feedback on blade sharpness, alignment, and machine settings. These systems track each cut’s quality and can identify subtle variations in performance, alerting operators before issues escalate. Digital monitoring systems can increase precision by 15% and reduce manual inspection time by as much as 40%, offering substantial efficiency benefits.
- Cost vs. Benefit: Although digital monitoring requires an initial investment, the reduction in waste and rework often leads to a full return on investment within 6–12 months, especially for high-volume manufacturers.
Operator Training
Experienced operators play a crucial role in maintaining precision. Proper training in blade handling, setup, and maintenance helps operators make informed decisions that enhance cut quality. Research shows that companies with ongoing operator training programs experience up to 20% fewer precision issues compared to those with minimal training.
- Skill Development: Consider implementing regular training sessions that cover new techniques, machine upgrades, and troubleshooting practices. Training can include hands-on practice with alignment tools, digital monitoring systems, and optimizing cutting angles, all of which contribute to better outcomes.
These optimization tips can help manufacturers achieve consistent precision, improve productivity, and enhance overall product quality.
5. Common Mistakes to Avoid When Working with Printer Slotter Knives
To maximize the performance of slotter knives and maintain high precision, it’s essential to avoid some common mistakes that can lead to inefficiencies, material waste, and additional costs.
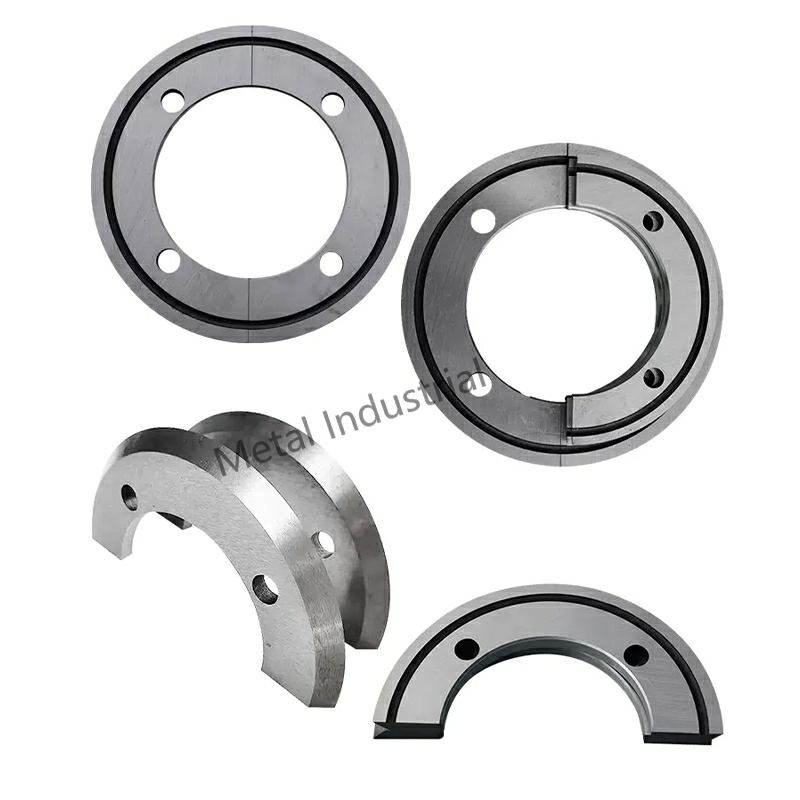
Neglecting Blade Maintenance
Infrequent sharpening or delayed replacement of slotter knives is one of the most common mistakes. A dull or damaged blade will not only reduce cutting accuracy but can also increase friction, potentially leading to machine strain and heat build-up. Regular maintenance is critical; studies indicate that consistent blade upkeep reduces production errors by up to 30%. Ignoring sharpening schedules or delaying replacements can cause rough or uneven cuts, leading to rework and wasted material.
- Best Practice: Set a fixed sharpening and replacement schedule based on usage data and material type. For high-use environments, daily checks and biweekly sharpening can prevent degradation in cut quality.
Incorrect Blade Setup
Improper setup of slotter knives, including incorrect alignment and positioning, can result in miscuts and even damage to the machine. A slight misalignment of 0.5 mm can create a cumulative deviation that impacts hundreds of cuts, leading to wasted material and increased costs. Studies suggest that correct setup practices can improve production efficiency by as much as 25%.
- Avoid Misalignment: Use digital or laser-guided alignment tools where possible. These tools offer 98% accuracy and can help operators achieve the correct positioning quickly and reliably.
Ignoring Machine Calibration
Regular machine calibration is necessary to ensure precise cuts. Over time, machine components can loosen or shift slightly due to vibrations and continuous use, impacting the accuracy of the slotter knife. Ignoring calibration can result in uneven or angled cuts, increasing rework and slowing down production. In high-volume settings, a lack of calibration can result in a 10% increase in defective products.
- Calibration Schedule: Set up a bi-monthly calibration check, or more frequently for intensive production environments. Some companies find that monthly calibrations reduce errors by up to 15%.
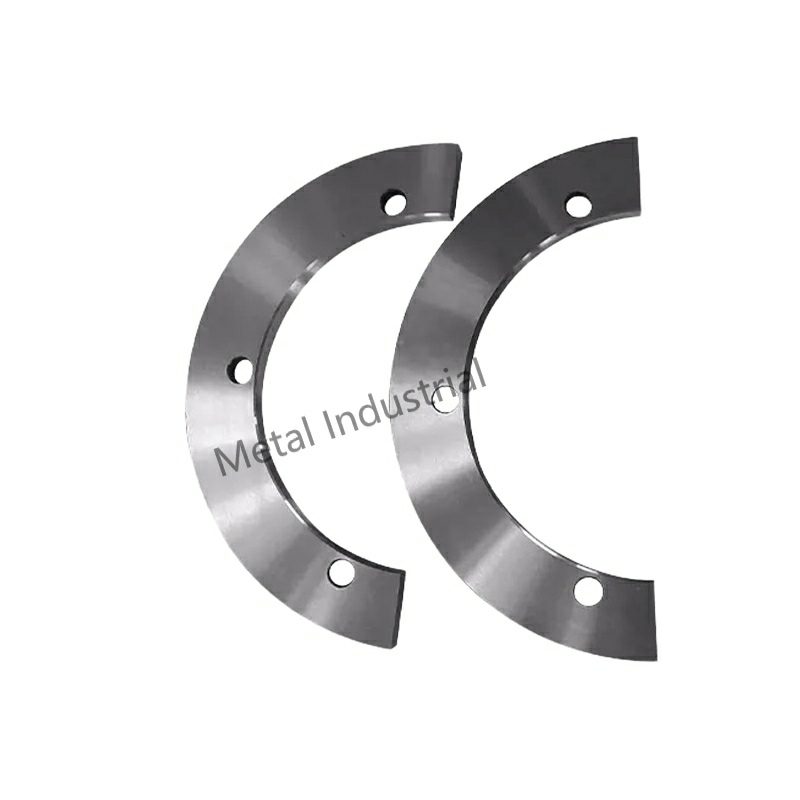
Overlooking Environmental Factors
Environmental factors like temperature, dust, and humidity often go unnoticed, but they can significantly impact blade performance and material stability. High temperatures can lead to metal expansion, while dust buildup increases blade friction. Operators should implement environmental controls to stabilize temperature and reduce dust in the working area.
- Data Point: Studies reveal that temperature fluctuations of just 5°C can increase material expansion and lead to misalignment issues, potentially reducing cutting precision by 5%.
By addressing these common errors, manufacturers can reduce waste, lower operating costs, and improve cut consistency. Avoiding these mistakes will ultimately contribute to higher efficiency, better product quality, and improved profitability.
Conclusion: Enhancing Precision for Better Performance and Cost Efficiency
High-precision cutting with slotter blades is essential for producing quality cartons while reducing waste and controlling costs. By understanding the factors that influence precision, following maintenance best practices, and investing in quality slotter knives, manufacturers can consistently achieve accurate cuts. Implementing these strategies not only improves productivity but also contributes to better product quality and customer satisfaction. For companies looking to upgrade or optimize their cutting processes, our team is here to provide expert guidance on choosing the right blades and best practices for maximizing precision.