まとめ
カスタム プレスブレーキ用金型 は、精密金属曲げ加工向けのカスタマイズされたソリューションを提供し、製造における効率と生産性を高めます。カスタマイズされたプレス ブレーキ ツールの利点、プロセス、実用的な用途、およびそれによってビジネス パフォーマンスがどのように向上するかをご覧ください。
はじめに: プレスブレーキ工具の精度の必要性
常に進化する製造業の世界では、精度と効率性が競争力維持の鍵となります。 プレスブレーキ用金型 板金を正確に成形・曲げる上で重要な役割を果たします。 高品質な生産を保証するしかし、標準ツールでは、さまざまな業界の特定の要求を満たすことができないことがよくあります。そこで、カスタム プレス ブレーキ ツールが登場し、課題を克服してパフォーマンスを最適化するカスタマイズされたソリューションを提供します。
この記事では、カスタム プレス ブレーキ ツールの利点、プロセス、実際のアプリケーションについて説明します。これらのツールによって金属加工がどのように変革され、コストが削減され、全体的な生産性が向上するかを説明します。
プレスブレーキツールとは何ですか?
プレスブレーキ用金型 プレスブレーキマシンで金属板を正確な形状に成形するパンチとダイが含まれます。パンチは金属に圧力をかけ、ダイは金属を支えて目的の角度や形状に成形します。
なぜこれが重要なのか?
これらのツールにはさまざまなデザインがあり、複数の曲げ角度、材料の厚さ、およびプロファイルに対応できます。たとえば、V ダイ、鋭角ダイ、オフセット ダイはそれぞれ特定のタスクを処理できます。実際、業界レポートによると、金属加工プロジェクトの 80% 以上が、品質と一貫性の基準を満たすためにプレス ブレーキ ツールに依存しています。
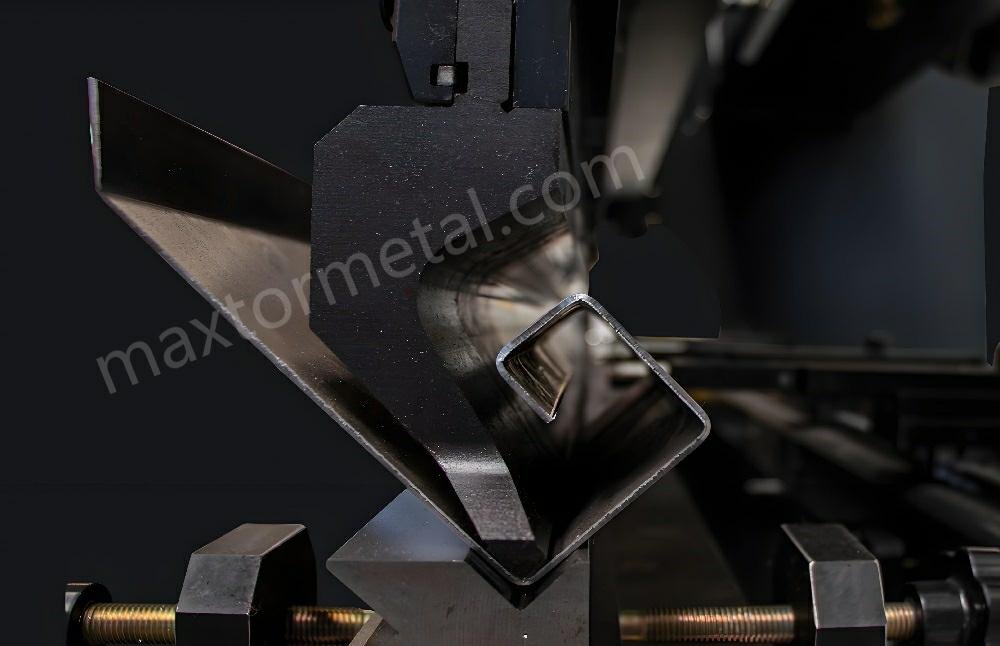
プレスブレーキ工具におけるカスタマイズの重要性
既製のソリューションでは複雑な設計ニーズに対応できない場合は、カスタム ツールが不可欠です。一般的なアプリケーションに対応する標準ツールとは異なり、カスタム ツールはプロジェクトの要件を正確に満たすように作成されます。
効率の向上
たとえば、ある製造会社は、非標準角度に対応するように設計されたカスタム プレス ブレーキ ツールに切り替えることで、セットアップ時間を 20% 節約しました。セットアップが高速化し、調整が少なくなるため、生産ラインをより効率的に稼働できます。
廃棄物の削減
プロジェクトの正確な仕様に合わせてツールをカスタマイズすることで、企業は廃棄材料とエラーを大幅に削減できます。これにより、リソースが節約され、最終製品が設計基準を満たすことが保証されます。
カスタムの恩恵を受ける業界 プレスブレーキ用金型
カスタムプレスブレーキツールは、いくつかの業界のプロセスに革命をもたらしました。
航空宇宙
- 航空機部品には、並外れた精度と軽量な材料が必要です。カスタムパンチにより、高強度アルミニウムパネルの正確な曲げが保証されます。
自動車
- シャーシ部品などの大量生産部品の再現性に対するニーズにより、カスタマイズされた金型の需要が高まっています。2023 年の業界レポートによると、カスタマイズされたツールにより、自動車部門の生産性が 30% 向上しました。

建設
- インフラストラクチャ プロジェクトでは厚い鋼鉄の梁やブラケットが使用されることが多く、カスタム ダイスを使用すると、より高いトン数の要件を効果的に処理できます。
エレクトロニクス
- 電子機器業界では、小型化された設計により、変形のない詳細な部品を作成するために精密なツールに依存しています。
カスタムプレスブレーキツールの仕組み
カスタム プレス ブレーキ ツールの作成には、共同作業による複数のステップのプロセスが含まれます。
- ニーズ分析: エンジニアは、プロジェクトの材料の種類、曲げ角度、および体積要件を評価します。
- デザイン: CAD ソフトウェアを使用して、パンチとダイの詳細なモデルが作成されます。これにより、すべての寸法と角度が最適化されます。
- 製造: CNC 加工により、極めて高精度のツールが製造されます。一部の施設では、±0.001 インチという厳しい許容誤差を実現しています。
- テスト: ツールは実際の生産ラインで厳密なテストを受け、効率と品質を最大限に高めるために調整が行われます。
このプロセスにより、ツールは既存の設備と特定の生産ニーズの両方と高い互換性を持つことが保証されます。
カスタムプレスブレーキツールの主な利点
1. 精密工学
カスタム ツールにより位置ずれがなくなり、大量生産でも完璧な曲げが保証されます。その結果、不良品が大幅に削減され、調査によると、不良率は最大 25% 低下することが示されています。
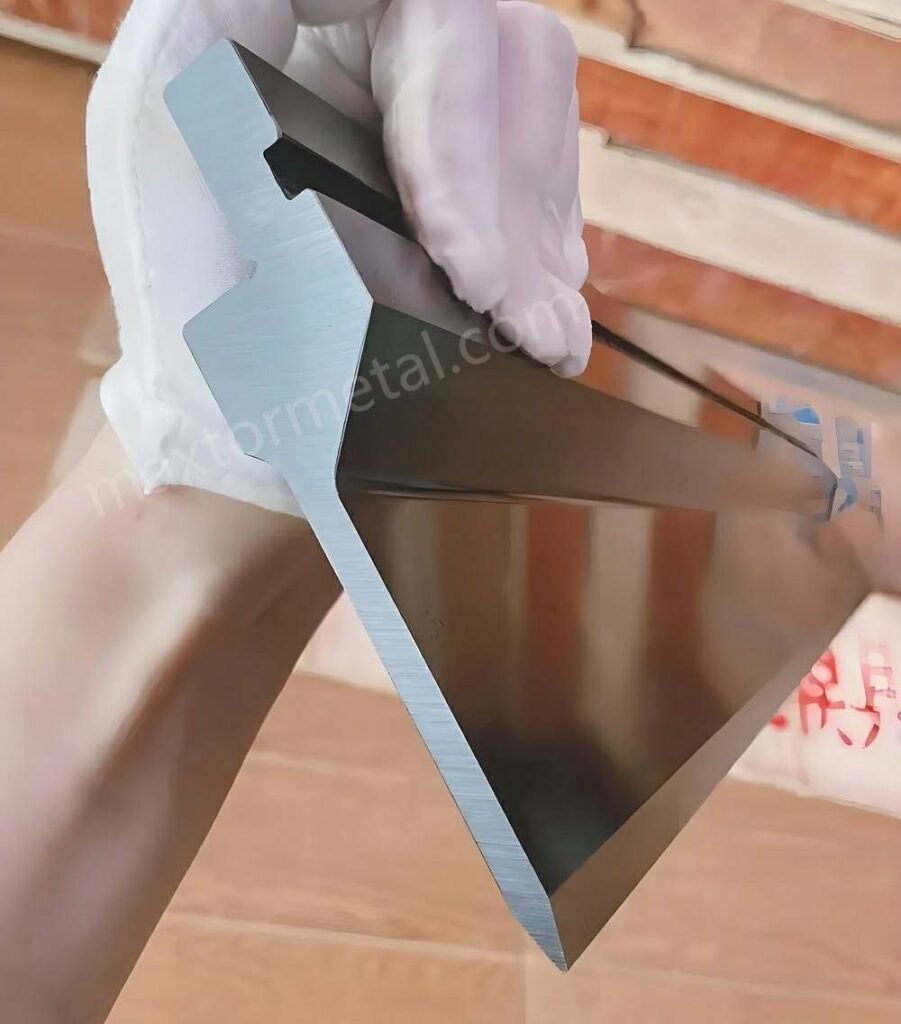
2. 処理時間の短縮
カスタマイズされた設計により、機械のセットアップと調整にかかる時間が短縮されます。サイクルが高速化することで、1 日に生産される完成品の数が増えます。
3. コスト最適化
カスタムツールには初期コストが高くなりますが、無駄を最小限に抑え、ダウンタイムを減らし、ツールの寿命を延ばすことでその効果が得られます。
4. 耐久性の向上
多くのカスタム ツールでは、摩耗に耐え、寿命を延ばすために硬化鋼やその他の高性能材料が使用されています。
ツールのカスタマイズにおける一般的な課題
プレスブレーキツールのカスタマイズには利点があるものの、次のような課題が生じる可能性があります。
- 初期コストが高い: カスタム ソリューションは初期費用が高くなります。ただし、ROI 分析により、時間の経過とともに費用が正当化されることがよくあります。
- リードタイム: カスタム ツールの設計と製造には数週間かかる場合があり、プロジェクトのタイムラインに影響を及ぼします。
これらの課題を克服するには、迅速な対応と価値重視のソリューションを保証する経験豊富なプロバイダーと協力する必要があります。
カスタムツールに使用される材料
適切な材料を選択することが、カスタム ツールの成功の鍵となります。人気のあるオプションは次のとおりです。
- 硬化鋼: 高張力アプリケーションに比類のない耐久性を提供します。
- 合金鋼: 強靭性と柔軟性のバランスが取れており、多目的用途に最適です。
- 炭化物: 非常に硬く、耐摩耗性に優れており、精密作業に最適です。
統計によると、硬化鋼で作られた工具は、柔らかい金属で作られた工具よりも長持ちし、長期的に見てより優れた価値を提供します。
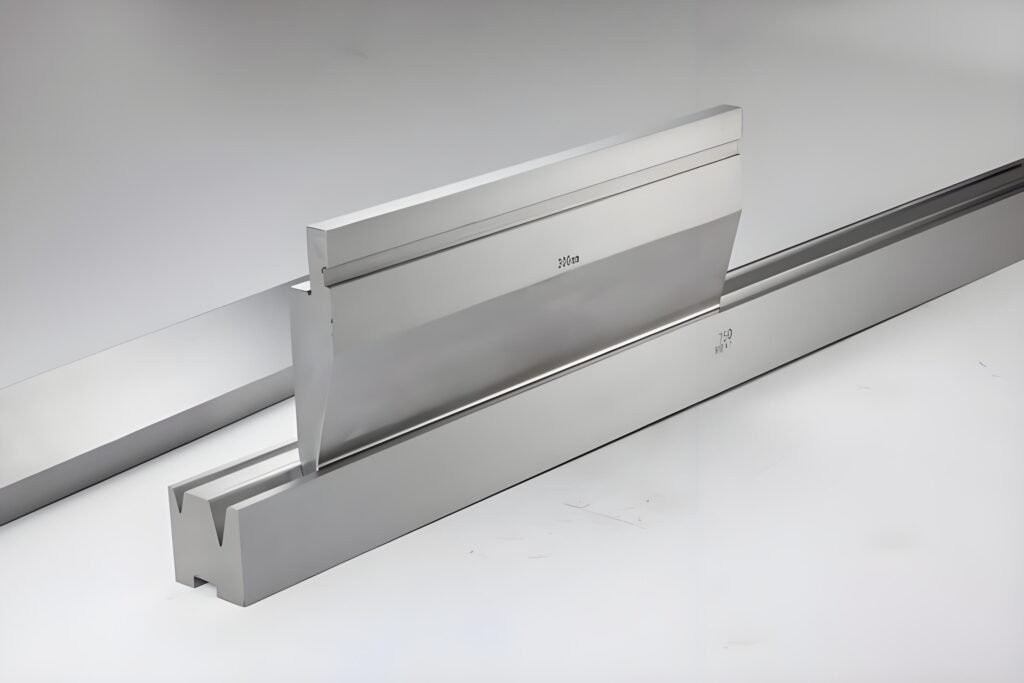
カスタムツールにおける先進技術の役割
先進技術がイノベーションを推進 カスタムプレスブレーキツール。 例えば:
- CNC加工: マイクロレベルの精度を実現し、一貫したパフォーマンスを備えたツールを生産します。
- 3Dプリント: プロトタイピングを高速化し、設計検証を迅速化します。
- シミュレーションソフトウェア: 曲げ操作をモデル化して潜在的な欠陥を予測し、設計を改良します。
これらの革新により、リードタイムが短縮され、最終製品の品質が向上し、メーカーに競争上の優位性がもたらされます。
業務にカスタムツールが必要な兆候
カスタム ツールの必要性を認識することが重要です。次の指標を確認してください。
- 製造中にエラーが頻繁に発生します。
- セットアップ時間が長くなったため、期限に間に合いませんでした。
- 製品の不一致に関する顧客からの苦情。
- 標準的なツールでは対応できないユニークなデザイン。
カスタムプレスブレーキツールを使用してこれらの問題に対処すると、結果が大幅に改善されます。
適切なカスタムツールプロバイダーの選択
プロバイダーを選択するときは、次の要素を考慮してください。
- 経験: あなたの業界で実績のある成功企業を探しましょう。
- テクノロジー: 最新の CNC 機械と設計ソフトウェアを使用していることを確認します。
- サポート: メンテナンスアドバイスなどのアフターサービスは、長期的な成功に不可欠です。
ケーススタディとレビューは、プロバイダーの信頼性と専門知識に関する貴重な洞察を提供します。
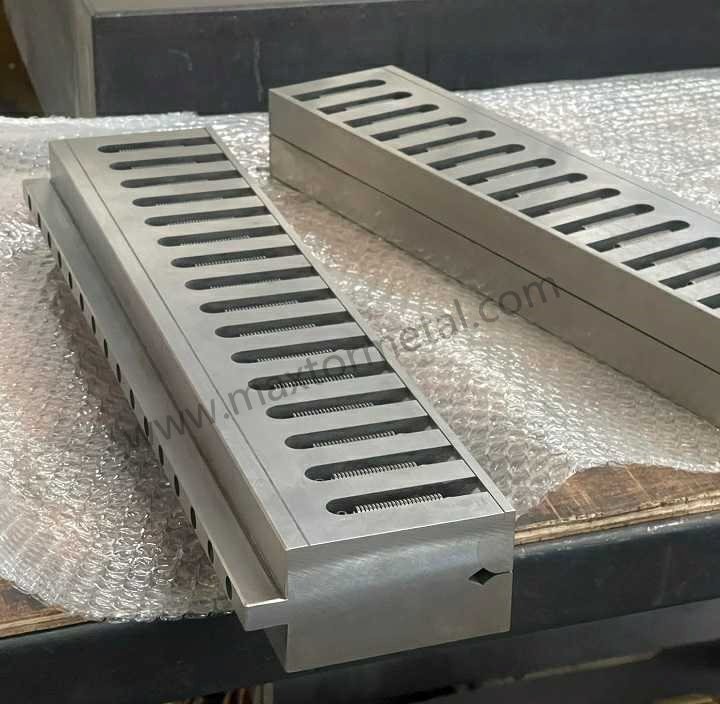
カスタムの実際の応用 プレスブレーキ用金型
ケーススタディ: 自動車の効率
ある自動車メーカーは、カスタムプレスブレーキ金型を採用した後、製造不良を 15% 削減しました。これは、1 年間で $50,000 を超える節約につながりました。
ケーススタディ: 建設の精度
ある鉄鋼製造会社は、橋梁プロジェクト用の特殊なブラケットを必要としていました。カスタム ツールを使用することで、厳しい期限を守り、検査中に 100% の成功率を達成できました。
カスタムプレスブレーキツールと標準プレスブレーキツールの比較
特徴 | カスタムツール | 標準ツール |
精度 | ユニークなデザインにぴったりフィット | 汎用 |
料金 | 初期投資額が高く、ROIも向上 | 初期費用は低いが耐久性は低い |
リードタイム | 時間はかかるが待つ価値はある | すぐに入手可能 |
耐久性 | 寿命の延長 | 短期使用 |
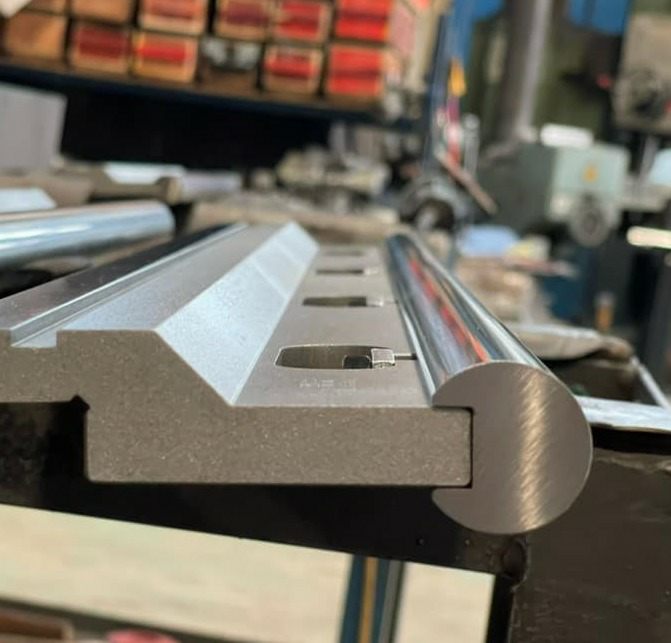
カスタムプレスブレーキツールのメンテナンスのヒント
適切な手入れにより工具の寿命が延びます:
- 定期的に清掃する: ゴミの蓄積を防ぎます。
- 頻繁に点検してください: 摩耗の兆候を早期に発見してください。
- 潤滑剤: 可動部品の摩擦を軽減します。
- 適切に保管してください: 腐食を防ぐために、乾燥した管理された環境を使用してください。
これらの手順に従うメーカーは、多くの場合、30% のツール寿命の向上を実感しています。
結論: カスタム プレス ブレーキ ツールを選択する理由
カスタム プレス ブレーキ ツールにより、メーカーは金属加工において精度、効率、柔軟性を実現できます。特定の課題に対処することで、これらのツールは標準ソリューションに比べて比類のない利点を提供します。コストの削減、品質の向上、独自の設計要件への対応など、どのような目的であっても、カスタム ツールがその答えです。
カスタム プレス ブレーキ ツールの可能性を解き放つ準備はできていますか? 今すぐお問い合わせください に もっと詳しく知る!