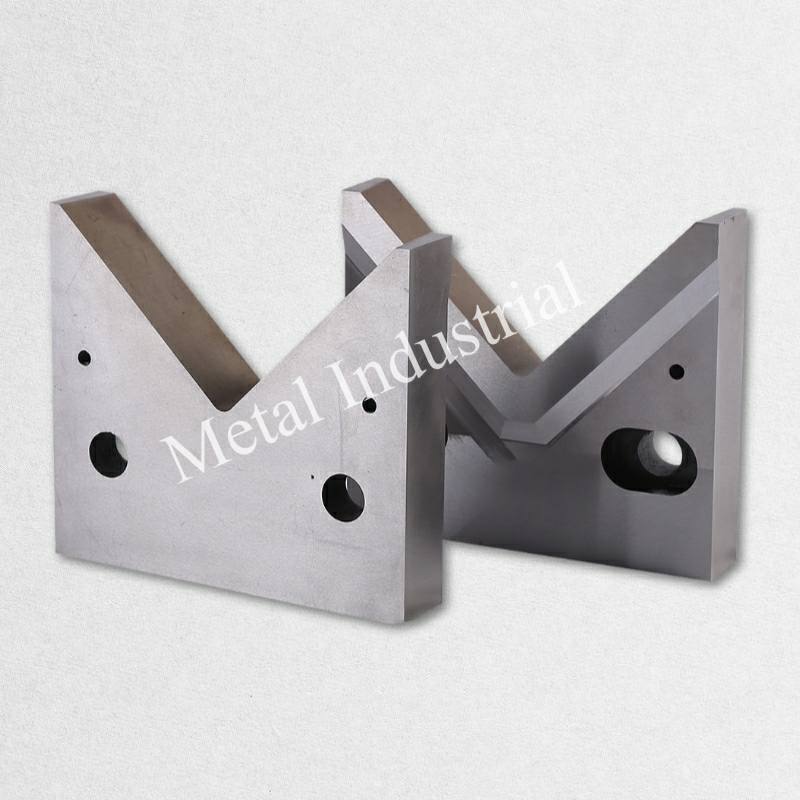
正しい選択 アイアンワーカーマシン交換ブレード can significantly improve your metalworking efficiency. It’s essential to select a カスタムブレード that perfectly fits your machine and specific job requirements, whether for cutting, punching, or shearing. Using the correct blade not only enhances cutting precision but also reduces downtime and keeps your team safe. Shop owners often report that the right blades help machines operate more smoothly and extend their lifespan. For the best results, be sure to review both technical specifications and customer feedback before making your selection.
重要なポイント
- Pick blades that match your machine and job. This helps you get accurate cuts. It also makes blades last longer. – Use blades made from strong materials like carbide or high-carbon steel. This means you will not need to replace them often. It also helps you save money. – Keep blades clean and lined up right. Sharpen them often to keep cuts good. This also stops damage to your machine. – Use the right blade for the metal and job. For example, use special blades for shearing, punching, or notching. This helps blades work better and last longer. – Buy from trusted suppliers like Nanjing Metal. They can make custom blades and give expert help. This makes your shop work better.
Ironworker Machine Replacement Blades: Selection Criteria
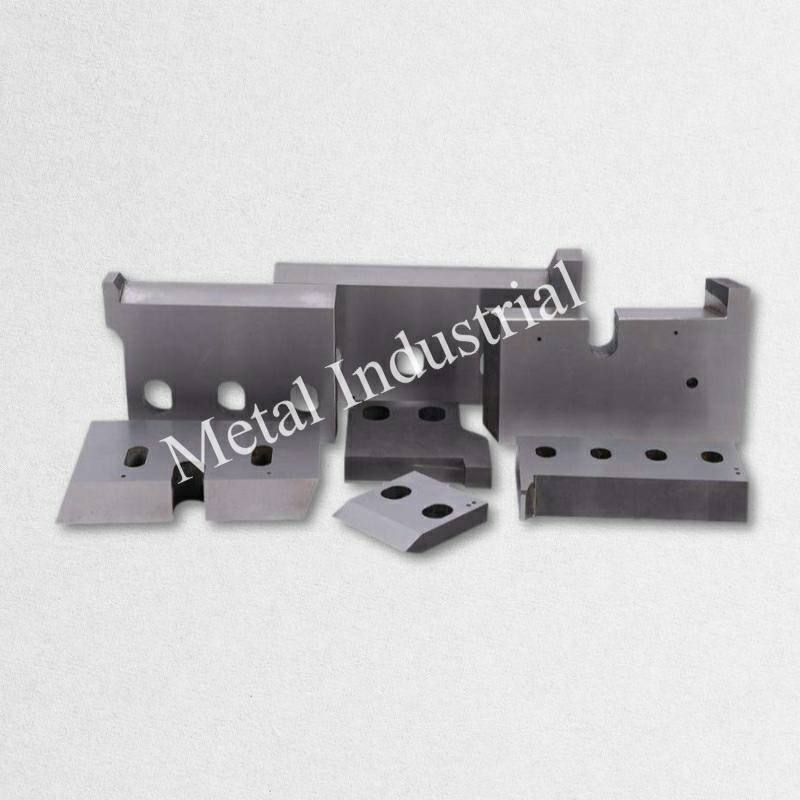
Performance Factors
When picking ironworker machine replacement blades, you should look at a few important things. These things help you get the best results and keep your machine working well.
- Durability: Blades with carbide tips last a long time. You do not have to replace them as often. High-carbon steel blades can be sharpened 3 to 5 times. Premium carbide blades can be sharpened 5 to 8 times.
- Precision: Good blades make smooth, clean cuts. They also keep cuts very exact. This is very important in car and airplane work. Even small mistakes can cause big problems.
- Rustproofing: Rust can make blades wear out faster. It also means you need to buy new blades more often. Blades with chromium or powder coatings do not rust easily. This helps them last longer.
- Cost-effectiveness: Blades that last longer save you money. You do not have to stop work as much to change them.
- Maintenance: Sharpening and regrinding blades keeps them cutting well. It also helps you waste less metal. Most companies say they save money and get better cuts when they take care of their blades.
You should also look at how fast the blade cuts, how long it lasts, and how good the finished metal looks. Watching these things helps you use your ironworker machine better.
Application Matching
It is important to use the right blade for your job. Shearing, notching, and punching all need different blades. If you use a shearing blade for punching, the cuts will not be good. The blade will also wear out faster. Studies show that the right blade can cut the force needed by half. It can also make the blade last over 25% longer. This means your cuts are cleaner, your blades last longer, and your shop works better.
Tip: Always check your machine’s rules and the metal you want to cut before picking a blade. This helps you get the best results and keeps your blades safe.
Industry rules are also important when picking blades. The table below shows the main things to think about:
Criteria | 説明 |
---|---|
Quality | Strong steel frame, exact punching, cutting, and bending; easy-to-use controls. |
Safety Compliance | Follows ANSI B 11-5 rules for safety guards and emergency stops. |
Capacity & Capabilities | Fits the power, size, and jobs you need to do. |
費用対効果 | Lets you use fewer machines, saving money and space. |
Maintenance & Operation | Needs little care, saves energy, and has good support from the maker. |
Technological Advancements | CNC controls and quick-change tools help you work faster and stop less. |
Top Ironworker Machine Blades by Application
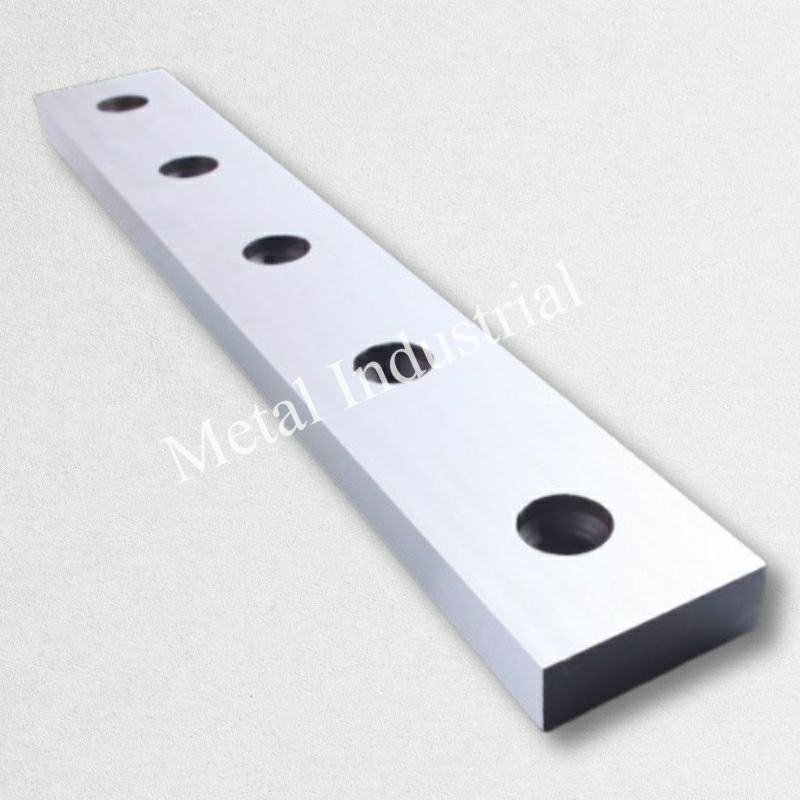
正しいものを選ぶ アイアンワーカーマシン交換ブレード helps your shop do better work. Each blade has a special job in metalworking. Some blades are for shearing, notching, punching, or cutting many things. Using the right blade for your job makes work faster. It also helps your machine last longer and gives you smooth cuts and holes.
せん断刃
Product Examples
- Metal Alligator Shear Blades
These blades are called crocodile shear blades too. They are used in alligator shears for tough metal cutting. You can cut scrap, bars, rods, and mixed metal waste with them. Makers use strong materials like 65Mn, Cr12MoV, SKD-11, and high-speed steel. This makes the blades last long and cut well.
Compatible with: Most hydraulic ironworker and recycling machines. - Edwards Shear Blades (AISI D2)
These blades are made for Edwards ironworker machines. They are tough and make clean, sharp cuts in mild and stainless steel.
Compatible with: Edwards ironworker machines. - Geka Shearing Blades (AISI D2)
These blades fit Geka ironworkers. They last a long time and make neat cuts with few burrs.
Compatible with: Geka ironworker machines.
User Feedback & Application Notes
When you use good shearing blades, you get many benefits:
- Cutting gets up to 15% faster.
- You change blades less, so downtime drops by 67%.
- Machine repairs go down by 25%.
- You save energy by keeping the blade gap right.
- You do less maintenance, which saves time and money.
- The right blade gap makes cuts better and tools last longer.
- Automation and sensors help set blade gaps, so mistakes are fewer.
- Shops that track blade wear can plan fixes and stop big problems.
Pick blade materials that match your metal’s hardness and toughness. Changing blade shape, like rake angle and edge, makes cutting easier and saves energy. Putting blades in the right way stops metal from bending and keeps cuts smooth. Sharpening and changing blades on time keeps your machine working its best.
Notching Blades
Product Examples
- Piranha Notcher Blades (AISI D2)
These blades fit Piranha ironworker machines. They stay sharp and last long for notching jobs.
Compatible with: Piranha ironworker machines. - Sunrise Notching Blades (AISI D2)
These blades are for Sunrise machines. They make clean notches and need little care.
Compatible with: Sunrise ironworker machines. - Edwards Notching Blades (AISI D2)
These blades go in Edwards ironworkers. They fit well and work well for notching.
Compatible with: Edwards ironworker machines.
User Feedback & Application Notes
People in metal shops say D2 steel notching blades do not chip or bend easily. Many workers say lining up blades right helps them last longer. Shops see more work done and fewer broken tools with good notching blades. One worker said their saw cut straight for a year without fixing it, even on many metals. Another user liked how strong and exact their notching blades were. Checking and changing blades often keeps your work good and stops delays.
Punching Blades
Product Examples
- American Punch Punch Dies (AISI S7)
These punch dies fit many ironworker brands. They are tough and last long, even when punching thick steel.
Compatible with: Most major ironworker machines. - Cleveland Punch & Die Punches (AISI S7)
These punches fit many machines and work well for lots of punching.
Compatible with: Various ironworker machines. - Geka Punching Tools (AISI S7)
These tools are for Geka ironworkers. They last long and make good holes every time.
Compatible with: Geka ironworker machines.
User Feedback & Application Notes
You can trust S7 steel punching blades for hard jobs. Users say tungsten carbide tips make blades last longer. You can sharpen them three to five times before changing. Watching cut quality and machine strain helps you spot worn blades early. Good blades mean less downtime and less machine wear. Some shops now change blades only four times a year instead of twelve. Lining up and caring for blades helps them last and work well. Many people save money and get better results with top punching blades, even if they cost more at first.
All-Purpose Blades
Product Examples
- Edwards Universal Blades (AISI D2)
These blades do many cutting and notching jobs. They fit Edwards and other big brands.
Compatible with: Edwards and other ironworker machines. - Sunrise Multi-Function Blades (AISI D2)
These blades are made for many uses. They work for shearing and notching.
Compatible with: Sunrise ironworker machines. - Scotchman General Purpose Blades (AISI D2)
These blades are used for many jobs. People like them because they work well and are easy to use.
Compatible with: Scotchman ironworker machines.
User Feedback & Application Notes
Shops that do many jobs pick all-purpose blades. People like how these blades work for many tasks and always cut well. Many say they get more done and stop less after using D2 blades. People like that the blades keep a sharp edge and are easy to put in. Checking and changing blades on time keeps your shop running and stops surprise problems.
Real Results with Ironworker Blades
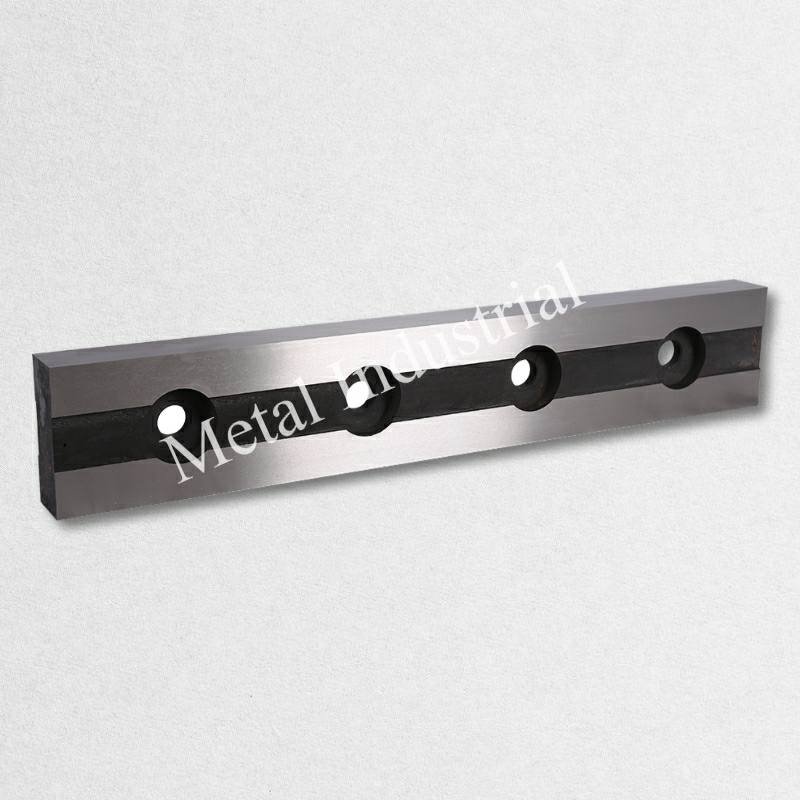
Shop Case Studies
Case Study 1: Increased Productivity in a Structural Steel Shop
A busy steel shop changed to better shearing and punching blades. Workers saw jobs finished faster and cuts looked smoother. The team worked 30% quicker than before. They had less downtime because blades stayed sharp. The manager said, “We finish jobs early now. Our machine works better. The team feels sure about every cut.” This story shows that picking the right blade helps you work faster and better.
Case Study 2: Reducing Downtime in a Recycling Facility
A recycling plant had to stop often to change blades. They started using new alligator shear blades for tough scrap. After this, downtime dropped by 67%. The blades cut mixed metal easily. Workers had fewer jams and did less fixing. The plant saved money on new blades. The supervisor said, “We process more metal each day. Our machines run longer without stopping. The new blades really helped us.”
Case Study 3: Precision Cutting for Custom Fabrication
A custom shop needed very exact cuts for tricky jobs. They picked top notching and punching blades for their machine. Workers made tight cuts and smooth edges every time. The shop sent out better products faster. One worker said, “Now we cut with precision every day. We trust our blades to give the quality our customers want.” The shop wasted less metal and worked more efficiently on all jobs.
Common Issues Solved
Metal shops often have problems like blades wearing out fast, blades not lining up, or using the wrong blade for the metal. The best ironworker machine blades fix these problems and help you get better results.
Problem 1: Rapid Blade Wear
Blades can wear out too quickly. This happens if you use too much pressure or the blade is not lined up right. Good blades with the right setup last longer. You can stop fast wear by using the right pressure and tension. Shops that switched to better blades saw:
- Blades lasted longer and needed fewer changes
- Lower costs for fixing machines
- Cuts stayed good and even
Too much pressure makes blades hot and wear out faster. If blades or holders are not lined up, they wear unevenly and break early. Setting up blades with the right pressure, alignment, and tension helps them last longer.
Problem 2: Misalignment and Poor Fit
If blades are not lined up, cuts look bad and blades break faster. You can use special tools to check if blades are straight. The table below shows what numbers to check for blade setup:
パフォーマンスメトリック | Value Range/Threshold | Why It Matters |
---|---|---|
Straightness | 0.4 – 0.6 μm | Keeps blade edge straight for accurate cuts |
Axis Misalignment | 6″ – 7″ per 200 mm | Measures misalignment that causes wear |
Perpendicularity | ~1 μm | Ensures blade sits at the correct angle |
Runout | ≤ 0.5 μm | Reduces vibration and uneven wear |
Overall Accuracy | ≤ 2 μm | Confirms proper setup for best performance |
You can stop misalignment by checking these numbers when you put in new blades. Shops that do this work better and their blades last longer.
Problem 3: Material Compatibility Challenges
Cutting different metals can be hard if you use the wrong blade. You need to match the blade to the metal you cut. For example, D2 steel blades are good for hard metals. High-speed steel works well for long jobs. Shops that use the right blade for each job see:
- Cleaner cuts with fewer rough edges
- Fewer broken tools
- More work done and less wasted metal
Picking the right blade and checking how much load it can take helps you avoid blade breaks. Making blades stronger and testing them also helps them last longer and work better.
You can see how good blades save money and help shops do better work. For example:
- Fixing turbine blades with lasers saved about $6,297 for each part, adding up to over $1.4 million a year.
- Electron beam work used 79% less material and cut costs from $17,430 to $9,810 for titanium parts.
- Engine blade tip repairs saved up to 81% in costs.
- New ways of making parts cut costs by 30% to 50% for airplane parts.
These examples show that picking the right ironworker machine blades saves money, helps you work faster, and makes your shop’s work better.
Ironworker Machine Replacement Blades Maintenance Tips
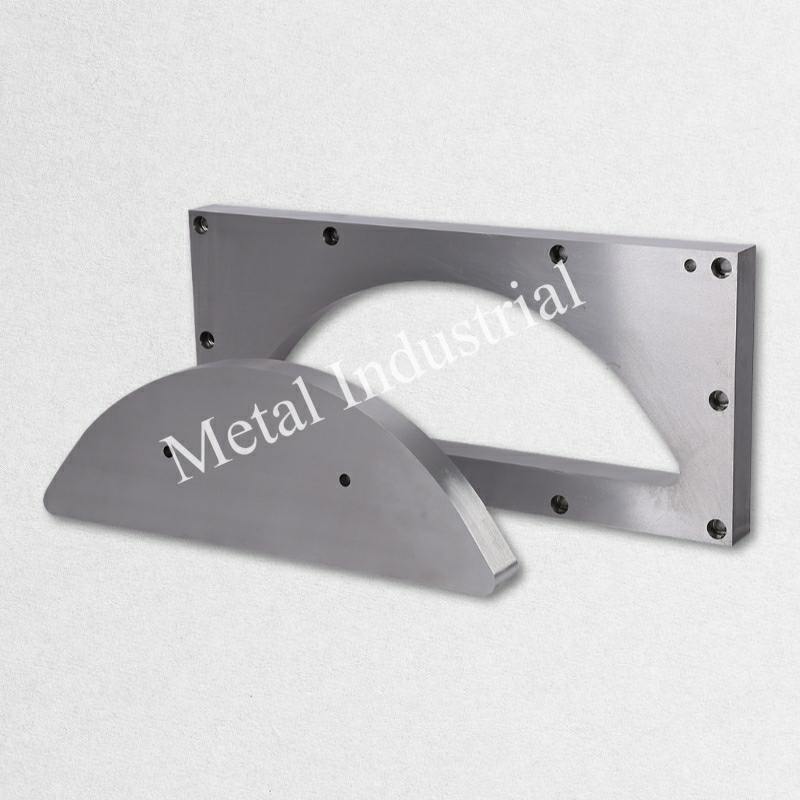
Maximizing Lifespan
Proper Alignment and Installation
Always check if the blade is lined up before you start. Lining up the blade right keeps cuts straight. It also stops the blade from getting too much stress. When you put in a new blade, use the correct tools. Follow the steps in your machine’s manual. This helps stop the blade from wearing out unevenly or breaking too soon. Keeping the blade lined up also keeps workers safe and makes cuts more accurate.
定期的な清掃と潤滑
Clean your blades after every 8 to 10 hours of work. Also clean them after cutting dirty metal. Use compressed air or a soft brush to get rid of dirt. Pick a cleaner that does not cause rust and is gentle. Dry the blade well so it does not rust. After cleaning, put oil on the blade or do this every 20 hours. Oil helps the blade move smoothly and stay cool. These steps help your blade last longer and keep your cuts neat.
Tip: Cleaning your blades often stops dirt from building up. This keeps your blade safe and your cuts looking good.
Material Handling Best Practices
Be careful when you move metal pieces. Do not drop heavy metal on the blade. Always feed metal into the machine at a steady speed. This keeps the pressure even and stops sudden shocks. Sudden shocks can crack or break the blade. Good handling keeps the blade and machine safe. It also helps everyone in the shop stay safe.
Scheduled Inspections and Preventive Maintenance
Make a plan to check your blades often. Look for signs like wear, cracks, or chips. Change or fix blades before they break. Checking blades early helps you avoid sudden problems. It also keeps your shop running without stops. Regular checks help keep everyone safe in the work area.
Replacement Signs
Dull or Chipped Cutting Edges
If the blade edge looks dull or chipped, change it. Dull blades make rough cuts and can hurt your machine.
Visible Cracks or Deformation
Check for cracks or bends in the blade. These mean the blade is weak and could break soon.
Decreased Cutting Quality or Increased Burrs
If your cuts look rough or have more burrs, the blade might be worn out. Change it to keep your work neat and exact.
Difficulty in Installation or Alignment
If it is hard to put in or line up the blade, it might be bent or damaged. A new blade will fit better and work safely.
Increased Machine Vibration or Noise
If the machine is louder or shakes more, the blade may be damaged inside. These sounds can mean cracks or other problems. Change the blade to keep your machine safe and working well.
Note: Watching for these signs helps you stop accidents and keeps your shop safe.
Picking the right ironworker machine replacement blades helps you get more work done and makes your cuts accurate. Shops use real numbers, like how fast blades wear out and how much force is needed to cut, to see which blades work best. You should always use the right blade for your job to get the best results. If you need a custom blade, Nanjing Metal is a trusted company with 20 years of experience and a good name in the business. If you want help from an expert, you can talk to their sales engineer.
よくある質問
What is the best way to choose the right ironworker machine replacement blades for my job?
Pick a blade that matches your job, like shearing, notching, or punching. Always look at your machine’s manual and check what metal you will cut. If you are not sure, ask a trusted maker for help.
How often should I replace ironworker blades?
Change blades if you see dull spots, cracks, or bad cuts. Most shops check their blades every week. Checking often helps you stop problems and keeps your machine working well.
Can I use one blade for different metals?
Some all-purpose blades can cut many metals. But you get better cuts if you use a blade made for each metal. The right blade makes cuts smoother and helps the blade last longer.
参照
高硬度のせん断ブレードを選ぶ理由 切断ニーズに合わせて精度と寿命を向上