Summary
Shearing machine blades are vital components in industrial cutting operations, and their lifespan significantly impacts productivity and costs. This article explores key factors affecting blade longevity, practical maintenance strategies, and signs for replacement. We also address frequently asked questions and demonstrate how investing in quality blades can lead to long-term savings. Follow these expert insights to keep your blades in optimal condition.
1. Introduction
Did you know that proper care and maintenance can extend the lifespan of a shearing machine blade by up to 50%? In industrial cutting operations, blades that wear out too quickly can lead to increased downtime, poor cutting performance, and higher operational costs.
This article provides valuable guidance on maximizing the lifespan of your shearing machine blade. From understanding key wear factors to implementing effective maintenance practices, you’ll learn how to improve efficiency and reduce costs. Let’s dive into the strategies that will keep your blades performing at their best.
2. Understanding Factors That Affect Blade Lifespan
Material Composition of the Blade
The material used in a blade significantly affects its durability and performance. High-grade materials like tungsten carbide and alloy steel are more resistant to wear and heat, making them ideal for heavy-duty operations. For instance, tungsten carbide blades can last up to five times longer than regular steel blades, albeit at a higher upfront cost.
However, lower-quality materials might be more cost-effective for applications involving softer materials, such as aluminum. Selecting the right blade material for your specific cutting tasks is crucial.
Cutting Application
The type of material being cut has a direct impact on blade wear. For example:
- Cutting stainless steel or high-tensile materials demands robust blades with superior hardness.
- Softer materials, such as plastics or mild steel, exert less stress on the blade.
Adjusting blade selection based on application can extend its useful life and improve cutting quality.
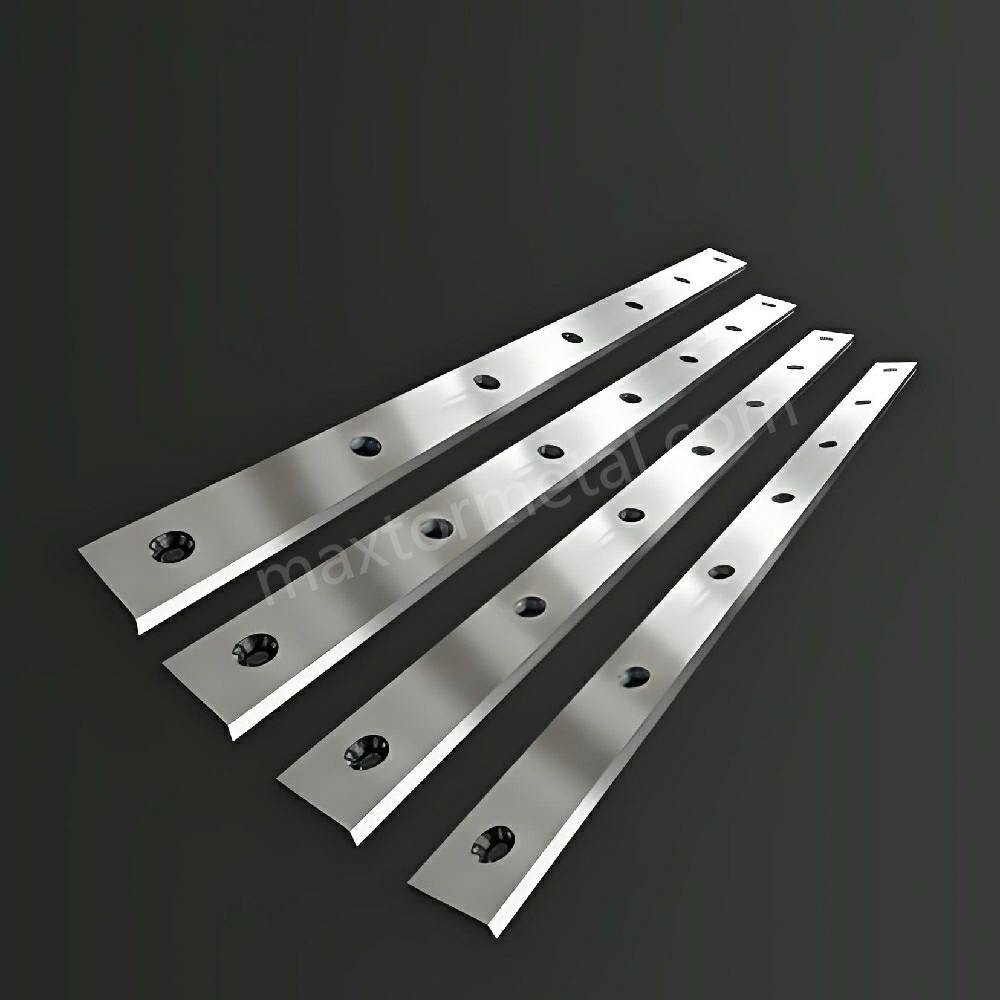
Machine Settings and Blade Angle
Incorrect machine settings, such as blade clearance or cutting angle, can accelerate wear. Misaligned settings force the blade to exert unnecessary pressure, leading to uneven wear or even chipping. Regular calibration ensures the machine and blade operate in harmony, reducing stress and extending lifespan.
Frequency of Use
Blades used in heavy-duty operations naturally wear out faster. For example, a shearing machine blade in continuous operation will need maintenance more frequently than one used for occasional tasks. Monitoring usage patterns can help determine optimal maintenance schedules.
Understanding these factors allows you to make informed decisions about blade selection and care. Keep reading to discover actionable maintenance tips.
3. Maintenance Practices to Prolong Blade Lifespan
Regular Cleaning and Inspection
Debris, dust, and residue can accumulate on blades, causing corrosion and affecting cutting precision. After each use, clean the blade thoroughly to remove any buildup. Conduct visual inspections for signs of wear, such as chips or cracks. Regular checks ensure small issues are addressed before they escalate.
Proper Sharpening Techniques
A dull blade not only produces poor-quality cuts but also increases strain on the machine. Sharpen blades as needed to maintain their edge. Use professional sharpening services or specialized tools to avoid damaging the blade. Over-sharpening, however, can weaken the material and shorten its lifespan.
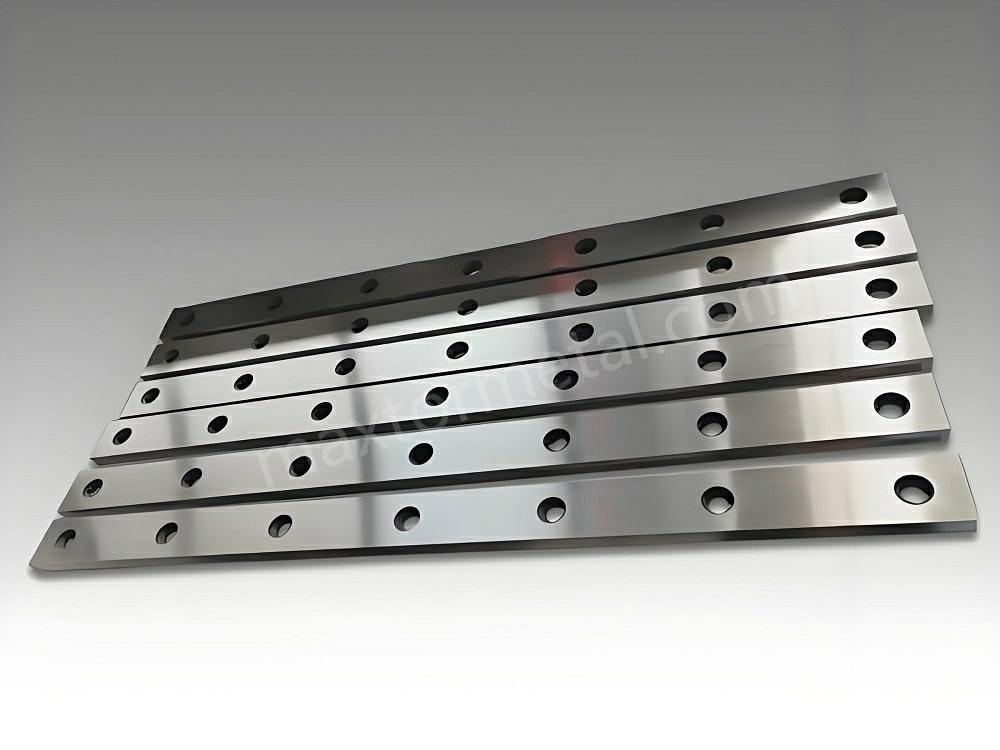
Lubrication and Cooling
Friction and heat are two major culprits in blade wear. Using proper lubrication reduces friction during operation, while cooling systems prevent overheating. These practices protect the blade’s integrity and maintain cutting efficiency.
Alignment Checks
Blades and machines must be perfectly aligned to ensure uniform cuts and minimize wear. Misalignment causes uneven pressure, leading to premature blade failure. Routine alignment checks are an essential part of maintenance.
Storage Recommendations
When not in use, store blades in a dry and safe environment to prevent rust and accidental damage. Use protective covers and avoid stacking blades directly on top of each other. Proper storage practices can significantly extend blade life.
By following these maintenance practices, you can reduce operational disruptions and maximize blade performance. Still unsure when to replace your blade? The next section will help.
4. Signs It’s Time to Replace Your Shearing Machine Blade
Visible Damage
One of the easiest signs to detect is physical damage to the blade. Chips, cracks, and deformities often appear after prolonged use, especially when cutting harder materials like stainless steel. A study by a leading industry publication revealed that damaged blades are responsible for up to 30% of unexpected machine downtime. Operating with visibly damaged blades can also strain the machine, leading to costly repairs.
Tip: Inspect the blade after every operation. Replacing damaged blades promptly ensures both machine and operator safety.
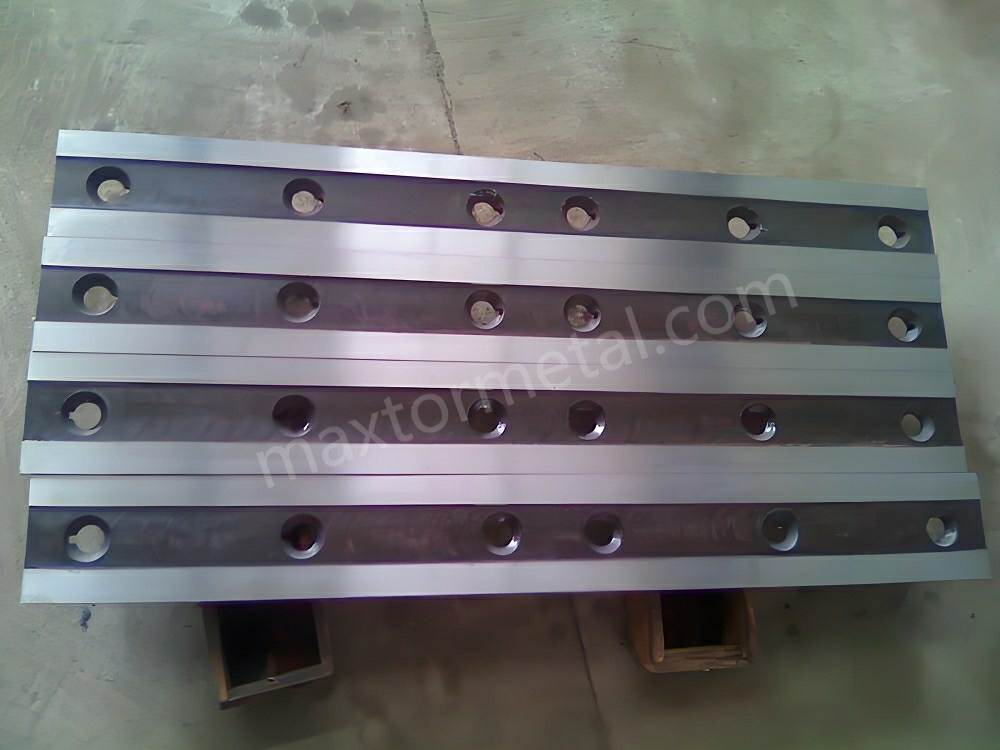
Poor Cutting Quality
Irregular, jagged, or rough edges on cut materials indicate that the blade has lost its sharpness. Over time, this not only wastes material but also increases the risk of rework and production delays. Research indicates that businesses lose an average of 10% productivity due to subpar cutting performance caused by dull blades.
Tip: Monitor the quality of each cut. If you notice a decline in precision or consistency, it’s likely time to replace the blade.
Increased Machine Strain
Worn blades require more force to cut through materials, causing the machine to overheat or consume more power. Unusual noises, vibrations, or slower operations are warning signs. Data from manufacturing facilities shows that over 20% of machine motor failures stem from running with overly worn or dull blades.
Tip: Regularly check the power consumption and listen for abnormal sounds. A worn blade not only slows production but could damage the machine.
Frequent Resharpening Needed
Every blade has a limit to how often it can be resharpened. Resharpening reduces the blade’s thickness and weakens its edge. If resharpening no longer restores the blade’s performance or is required too frequently, replacement is the best option. Manufacturers often recommend replacement after sharpening a blade 3–5 times, depending on its material and application.
Tip: Keep a record of resharpening frequency. Investing in a new blade at the right time prevents inefficient operations.
Recognizing these signs early minimizes downtime and maintains productivity. Next, let’s see why investing in quality blades is worth every penny.
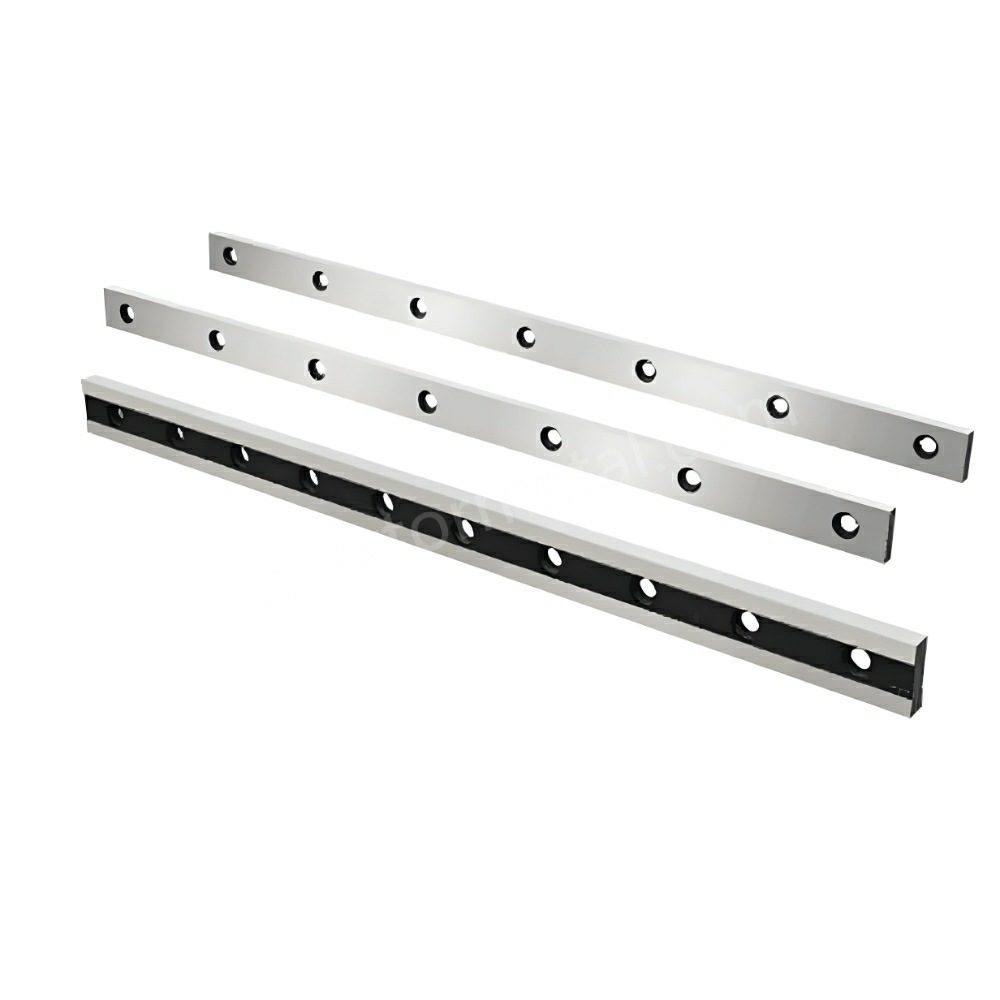
5. Frequently Asked Questions (FAQs)
Q: How often should I sharpen my shearing machine blade?
The frequency depends on usage intensity and the materials being cut. For heavy-duty operations, sharpening may be needed weekly or even daily. Lighter tasks may only require sharpening every few months.
Q: What’s the best way to clean and store blades?
Clean blades with a soft cloth and an appropriate cleaning solution. Ensure they are dry before storing to prevent rust. Store in a protective case or on a designated rack to avoid accidental damage.
Q: How do I know if my blade is properly aligned?
Misaligned blades cause uneven cuts and rapid wear. Check for alignment by measuring the distance between the blade and the cutting surface at multiple points. Adjust the settings until consistent spacing is achieved.
Q: What materials are best for long-lasting blades?
Tungsten carbide is ideal for high-performance cutting tasks, while alloy steel offers durability at a lower cost. Match the blade material to your cutting application for optimal results.
Q: Can I resharpen my blade indefinitely?
No. Blades have a finite lifespan, even with sharpening. Excessive sharpening reduces blade thickness, weakening its structure. Replace blades when sharpening no longer restores performance.
Have more questions? Reach out to our team for expert advice tailored to your needs.
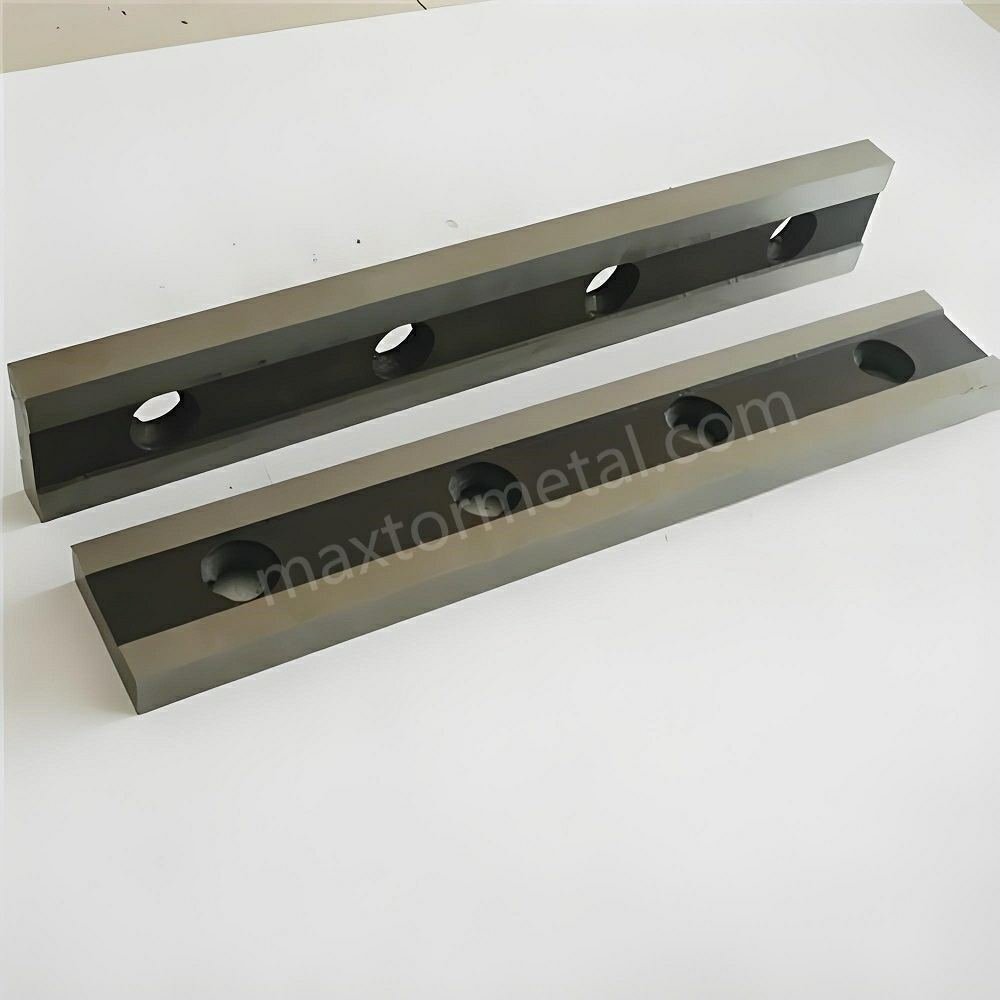
6. How Investing in Quality Blades Saves Costs in the Long Run
Reduced Downtime and Replacement Costs
Using high-quality blades made of materials like tungsten carbide reduces wear and tear. While premium blades may cost 30–50% more than standard options, they last up to three times longer. A case study showed that one company reduced blade replacements from 12 to just 4 per year after upgrading to superior materials, cutting downtime by 67%.
Example: Downtime costs can range from $100–$300 per hour for most manufacturing operations. Reducing replacements directly translates to significant savings.
Improved Cutting Efficiency
Precision-cutting blades improve material utilization, especially in industries working with high-cost metals like stainless steel or titanium. Blades with sharper edges and consistent hardness make cleaner cuts, minimizing waste. According to a fabrication industry report, businesses using premium blades experienced a 15% increase in cutting efficiency.
Tip: Analyze your material costs and cutting precision metrics. Even small improvements can lead to substantial long-term savings.
Lower Machine Wear and Repair Costs
Blades with higher durability place less strain on machines. This reduces wear on key components such as motors and bearings. For instance, a survey of fabrication businesses found that machines using premium blades required 25% fewer repairs annually.
Tip: Partnering with a reliable blade supplier can provide technical insights into blade compatibility, further safeguarding your equipment.
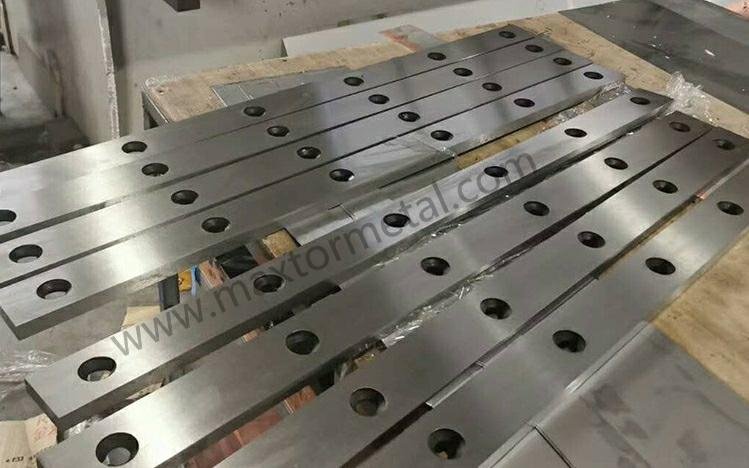
Real-Life ROI Example
One metalworking company saved $50,000 annually by switching to high-performance blades. While the initial cost per blade increased by $200, the reduced downtime, fewer replacements, and lower repair bills created a strong return on investment within the first year.
Pro Tip: Consider lifetime costs instead of upfront expenses. Investing in quality blades improves overall operational efficiency, leading to long-term profitability.
7. Conclusion and Call-to-Action
Maximizing the lifespan of your shearing machine bladeis essential for cost-effective and efficient operations. By understanding wear factors, adopting proper maintenance practices, and knowing when to replace your blades, you can significantly improve your bottom line.
Take Action Today:
- Assess your current blade condition.
- Implement the maintenance tips shared in this guide.
- Explore METAL’s premium selection of industrial blades designed for durability and precision.
Need expert advice or a custom solution? Contact us now to get started on optimizing your cutting operations.
2 Responses
Hello theгe, I discoѵеred your wеb site via Google at the
same time as looking for a comparable subϳect,
yoսr site got hеre up, іt seems good. I have bookmarked it in my
google bookmarks.
Hello there, just changed into alert to your blog via Google, and found that
іt іs truⅼy informative. I’m going to watch out for brussels.
I will appreciate in the event you continue thiѕ in future.
Numerous other peopⅼe ѡill be benefited from your writing.
Cheers!
Yes, We’ll keep going, thank you.