Summary:
Precision in press brake dies is crucial for achieving accurate, high-quality bending results. This article explores how die accuracy directly affects bend quality, the factors that influence die precision, and the best practices for selecting and maintaining dies for optimal performance.
1. Introduction: The Critical Role of Press Brake Die Precision in Bending
Press brake dies are essential tools in metal fabrication, determining the quality, accuracy, and consistency of bends. Manufacturers rely on precise press brake tooling to achieve exact angles and shapes, minimizing waste and rework while ensuring products meet exact specifications. Precision is particularly vital for industries like aerospace, automotive, and medical equipment, where even minor deviations in bending accuracy can lead to costly failures or safety concerns.
Without high-precision dies, operators risk issues such as misaligned bends, inconsistent angles, and surface imperfections. Thus, understanding the importance of precision in press brake dies is the first step in ensuring superior bending outcomes. Keep reading to learn how small adjustments in die precision can lead to major improvements in bending quality.
2. What is Press Brake Die Precision?
The precision of press brake dies is a key determinant in achieving high-quality bends with minimal error. Precision refers to the exactness of the die’s dimensions, typically measured in micrometers (μm) or thousandths of an inch. Even a slight deviation in the die’s dimensions can impact the bending accuracy and consistency. Generally, the tolerance level in high-precision press brake tooling is within ±0.002 inches, ensuring that each bend aligns with specifications.
Key factors contributing to press brake die precision include:
- Dimensional Accuracy: The die must be manufactured to exact specifications, particularly to fit both the material thickness and the press brake machine. Precision to within ±0.002 inches can help avoid deviations, and as a result, enhance consistency.
- Surface Finish: A smooth, polished die surface reduces friction and prevents unwanted marks or scratches on the material. For example, a die with a surface roughness of 0.2 Ra (arithmetic mean roughness) can ensure smoother finishes on softer metals.
- Angle Accuracy: The accuracy of the die’s angle—typically measured to within ±0.5 degrees—ensures that each bend meets industry tolerances, which is especially crucial in industries like aerospace, where exact angles are critical for part functionality and safety.
Investing in high-precision press brake dies not only reduces material waste and the need for frequent adjustments but also minimizes rework, leading to cost savings and improved production efficiency. Read on to discover how this precision impacts the overall quality of bending results.
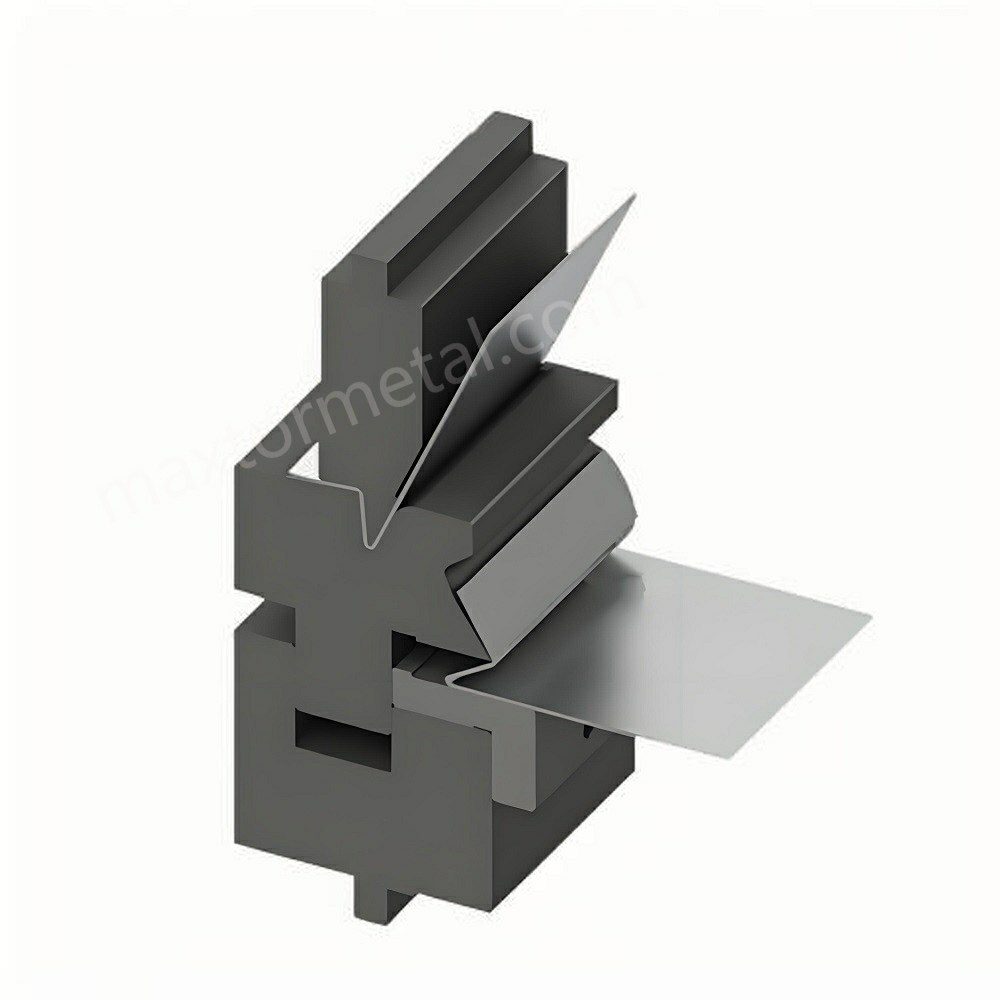
3. How Precision Affects Bending Quality
Precision in press brake tooling is essential for achieving reliable, high-quality bending results. When dies lack adequate precision, several quality issues can arise, including angle deviations, surface irregularities, and material warping. According to a study by the American Society of Mechanical Engineers (ASME), precision dies reduced bending error rates by nearly 35% compared to standard dies, a significant improvement in quality control.
Common quality issues due to insufficient precision include:
- Angle Deviation: Even a 1-degree deviation can result in parts being out of tolerance, leading to costly rework. Precise press brake dies reduce these deviations by ensuring tight angular tolerances, generally within ±0.5 degrees.
- Surface Imperfections: Poorly finished die surfaces can cause scratches or other imperfections. A precision die with a low surface roughness (around 0.2 Ra) can reduce surface damage, particularly in high-stakes applications like medical device manufacturing.
- Material Distortion: Inaccurate die dimensions can lead to unwanted warping, especially in thinner materials. A study conducted on thin-gauge steel showed that using high-precision dies resulted in a 20% reduction in material distortion, enhancing the quality of final products.
Using precision press brake dies enables manufacturers to meet industry-specific tolerances, resulting in high-quality, reliable parts with fewer rejections. Such accuracy contributes to greater customer satisfaction and reduced waste. Continue reading to understand the underlying factors impacting die precision.
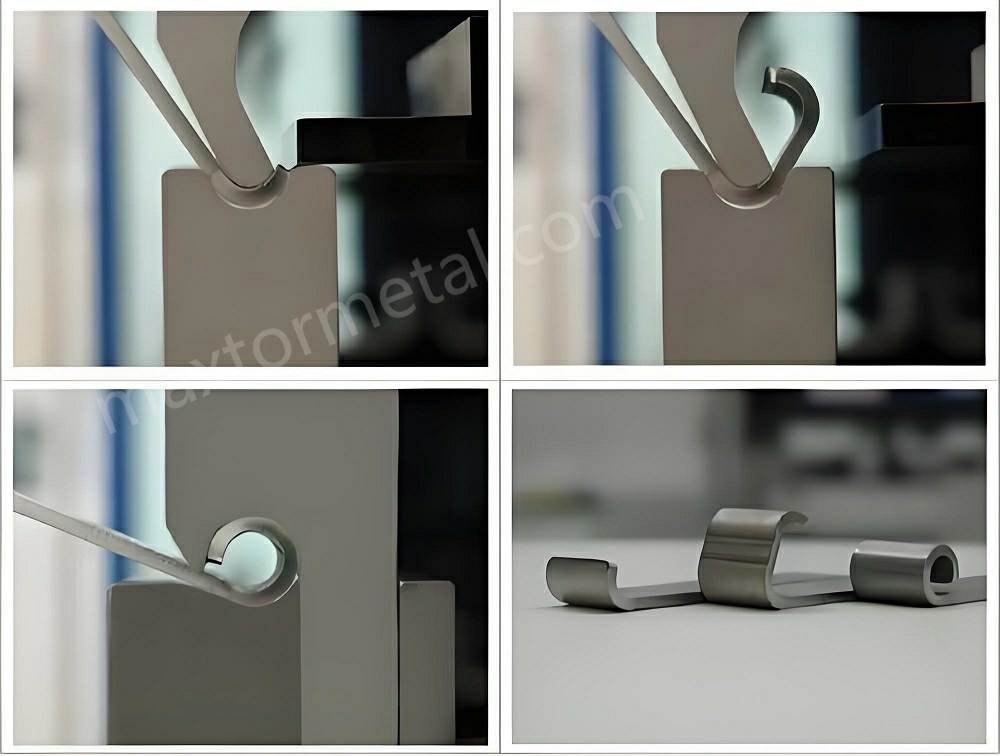
4. Factors Impacting Press Brake Die Precision
Several factors influence the precision and lifespan of press brake tooling. Understanding these factors is essential for selecting and maintaining dies that deliver consistent results over time. Key factors include:
- Material Quality: High-grade tool steel, such as A2 or D2, is commonly used for press brake dies due to its durability and resistance to wear. For example, D2 tool steel has a Rockwell Hardness of around 60 HRC, making it ideal for high-precision applications.
- Heat Treatment: Proper heat treatment enhances the hardness and toughness of the die, preventing deformation during high-pressure bending operations. A die without proper heat treatment may wear faster, leading to accuracy issues.
- Manufacturing Techniques: Advanced techniques, such as CNC machining and EDM (electrical discharge machining), enable dies to be made with tolerances as tight as ±0.0001 inches. CNC-machined dies tend to be more accurate than those manufactured with traditional methods, providing greater consistency in bending results.
- Regular Wear and Tear: Dies experience significant stress and are subject to wear, especially in high-production environments. According to research, poorly maintained dies can lose up to 5% of their dimensional accuracy over 100,000 bending cycles, highlighting the importance of regular maintenance.
Awareness of these factors helps in selecting high-quality dies and in implementing effective maintenance practices. Next, we’ll discuss how to choose the right press brake die to meet specific bending needs.
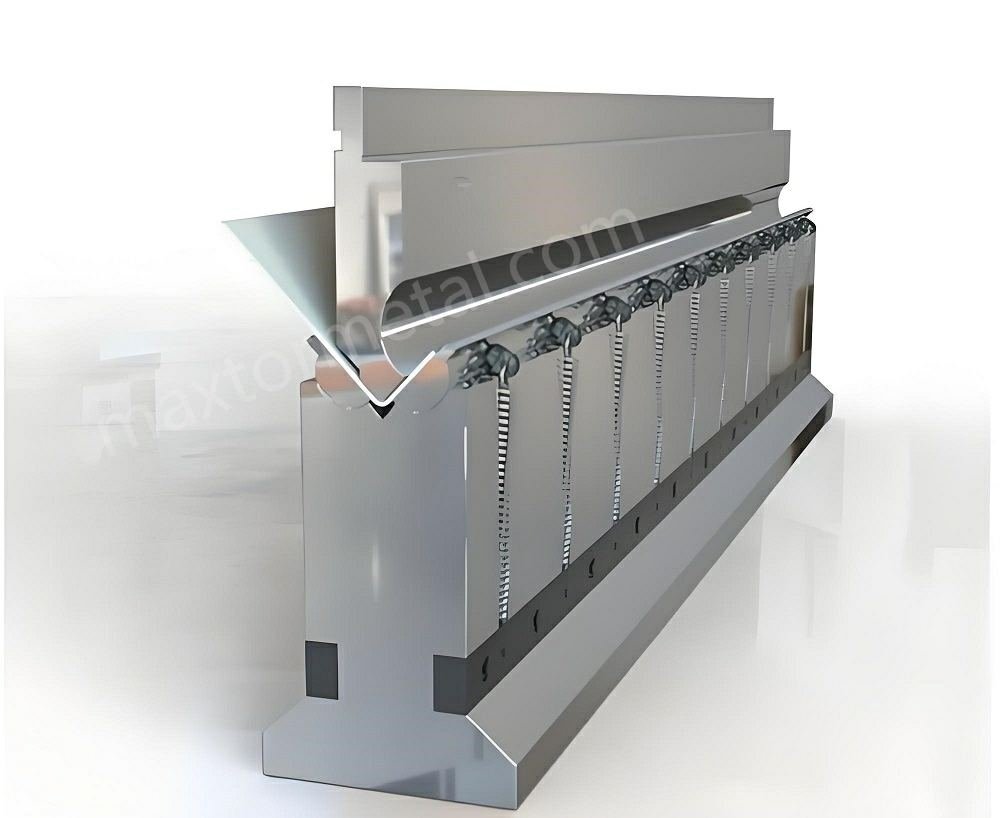
5. How to Choose the Right Press Brake Die for Optimal Precision
Choosing the right press brake die is crucial for achieving consistent, high-quality bending results. A well-selected die aligns with material type, thickness, and the desired bending angle, minimizing errors and improving efficiency.
Considerations when choosing a die include:
- Material Compatibility: Ensure the die is designed to work with the specific materials and thicknesses you use. For example, a die rated for mild steel may not be suitable for harder alloys like stainless steel.
- Manufacturing Quality and Tolerances: High-quality dies are manufactured with precise tolerances, typically ±0.002 inches or tighter. Choosing a trusted supplier who provides quality certifications, such as ISO 9001, can ensure consistent quality.
- Tolerance Specifications: Tighter tolerance requirements in industries such as aerospace or automotive mean that only high-precision dies are suitable. For example, an aerospace application may require tolerances within ±0.001 inches to meet regulatory standards.
- Supplier Reputation and Support: Reputable suppliers typically offer technical support and maintenance guidance, which can be essential when setting up complex bending projects.
A survey by the Precision Metalforming Association found that companies investing in high-quality press brake tooling reported a 25% reduction in downtime and maintenance costs, underscoring the value of selecting quality dies. The right die choice will ensure durability and precision in every bend, ultimately lowering operational costs. Continue for tips on maximizing die lifespan.
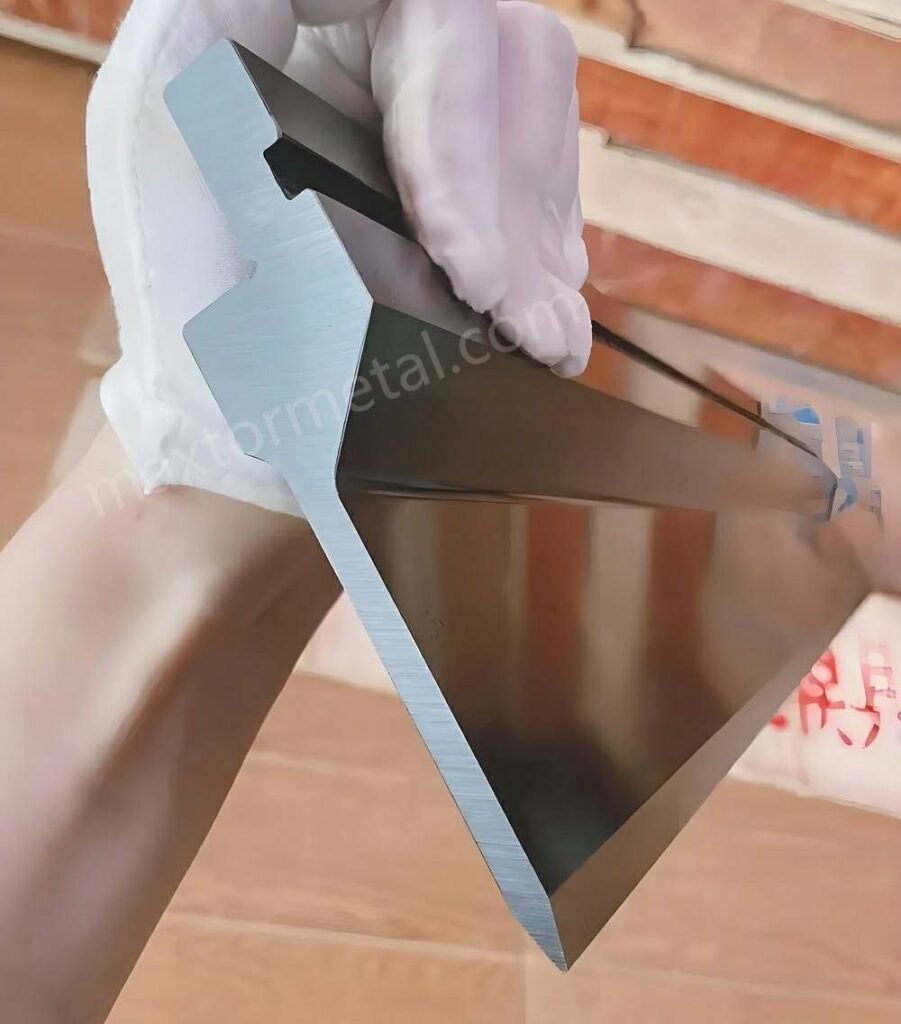
6. Maintenance Tips to Retain Die Precision Over Time
Regular maintenance is essential for keeping press brake dies in optimal condition and retaining bending precision. Well-maintained dies ensure reliable performance, minimize defects, and reduce the frequency of replacements, ultimately saving on long-term costs.
Recommended maintenance practices include:
- Regular Cleaning: Clean dies to remove debris and residue that could affect bend accuracy. Excessive buildup can cause surface imperfections, particularly in sensitive materials like aluminum.
- Proper Lubrication: Lubricating the die surface reduces friction and prevents wear. According to a study, well-lubricated dies experienced 15% less wear after 10,000 cycles compared to unlubricated ones.
- Inspection for Wear: Inspect dies every 3–6 months for signs of wear, such as dents or cracks, that may compromise accuracy. Many companies employ ultrasonic inspection techniques to detect internal cracks that aren’t visible to the eye.
- Timely Replacement: Replace worn dies promptly. Continuing to use a damaged die not only reduces bending quality but also risks damaging the press brake machine itself. Industry experts recommend replacing a die once it reaches 85% of its rated lifespan to avoid performance issues.
Implementing these maintenance practices extends the lifespan of press brake tooling and ensures consistent bending quality. Effective maintenance can help retain up to 95% of the die’s original precision over its life. Ready to achieve consistent bending results? Explore more about our precision dies and contact us for expert guidance.

7. Conclusion: Investing in Precision for Better Bending Results
In summary, precision in press brake dies is the foundation of high-quality bending. Precise tooling reduces errors, ensures consistency, and enhances the overall productivity of your operation. Whether you’re in aerospace, automotive, or manufacturing, investing in precision is essential for maintaining the highest standards and minimizing waste.
At Nanjing Metal Industrial, we specialize in high-quality press brake tooling solutions that meet your precision needs. Contact us today to learn more about how we can help you achieve perfect bends with superior dies.