Resumo:
Este artigo fornece um guia abrangente para melhorar a precisão de corte de facas de ranhura usadas na fabricação de caixas. Por meio de manutenção regular, alinhamento preciso, configurações ideais de lâmina e monitoramento digital, as empresas podem obter cortes precisos, reduzir desperdícios e aumentar a produtividade em até 25%.
Introdução: A importância da precisão de corte em facas de ranhuras de impressora
Alcançar alta precisão de corte é crucial na indústria de fabricação de caixas. Cortes precisos reduzem o desperdício, melhoram a qualidade e maximizam a eficiência da produção. Para empresas que trabalham com caixas de papelão ondulado, a precisão nas bordas de corte e ranhuras garante que os produtos atendam aos padrões de qualidade e às expectativas do cliente. Facas de ranhura para impressora, comumente usadas para cortar e vincar placas de papelão ondulado, são essenciais para esse nível de precisão. No entanto, sem manutenção e otimização adequadas, até mesmo as melhores facas podem produzir resultados inconsistentes, levando a custos maiores e desperdício de materiais. Neste artigo, exploraremos os principais fatores que afetam a precisão da faca de entalhe e forneceremos dicas práticas para melhorar a precisão do corte.
1. Compreendendo os principais fatores que afetam Faca para ranhurar impressora Precisão
Vários fatores influenciam a precisão das lâminas de ranhura na fabricação de caixas. Aqui estão os principais elementos a serem considerados:
Material e afiação da faca
O material e a nitidez de uma faca afetam significativamente sua capacidade de corte. Lâminas de ranhuras feitas de materiais de alta qualidade, como carboneto de tungstênio ou aço rápido, fornecem bordas mais afiadas e duradouras. Estudos mostram que facas feitas de carboneto de tungstênio mantêm a nitidez 10–15% mais do que o aço padrão, reduzindo o tempo de inatividade para afiação e substituição. A nitidez também afeta a precisão; uma lâmina cega pode rasgar ou desfiar as bordas da caixa, dificultando a manutenção do alinhamento e da qualidade.
Alinhamento e Posicionamento
O alinhamento preciso das facas de ranhura é essencial para cortes precisos. Lâminas desalinhadas resultam em bordas tortas e ranhuras irregulares. Verificar e ajustar regularmente o alinhamento das facas garante que elas permaneçam paralelas e cortem em ângulos consistentes. Muitos fabricantes investem em ferramentas de alinhamento digital que permitem alta precisão no posicionamento, geralmente melhorando as velocidades de produção em 5–10%.
Calibração de Máquina
As máquinas de entalhe exigem calibração regular para operar corretamente. A calibração inclui definir a tensão da máquina, verificar o posicionamento da lâmina e verificar se há desgaste ou folga na configuração. A calibração adequada mantém a precisão do corte e evita erros comuns que reduzem a qualidade. Os especialistas em máquinas recomendam calibrar as máquinas de entalhe a cada três meses ou após qualquer trabalho de manutenção importante para manter alta precisão.
Condições de operação
Condições ambientais como temperatura, poeira e umidade podem impactar o desempenho da lâmina. Calor excessivo, por exemplo, pode causar expansão do metal, impactando o alinhamento e a nitidez das lâminas. Para evitar tais problemas, é aconselhável manter um ambiente estável para máquinas de entalhe e implementar limpeza de rotina para reduzir o acúmulo de poeira.
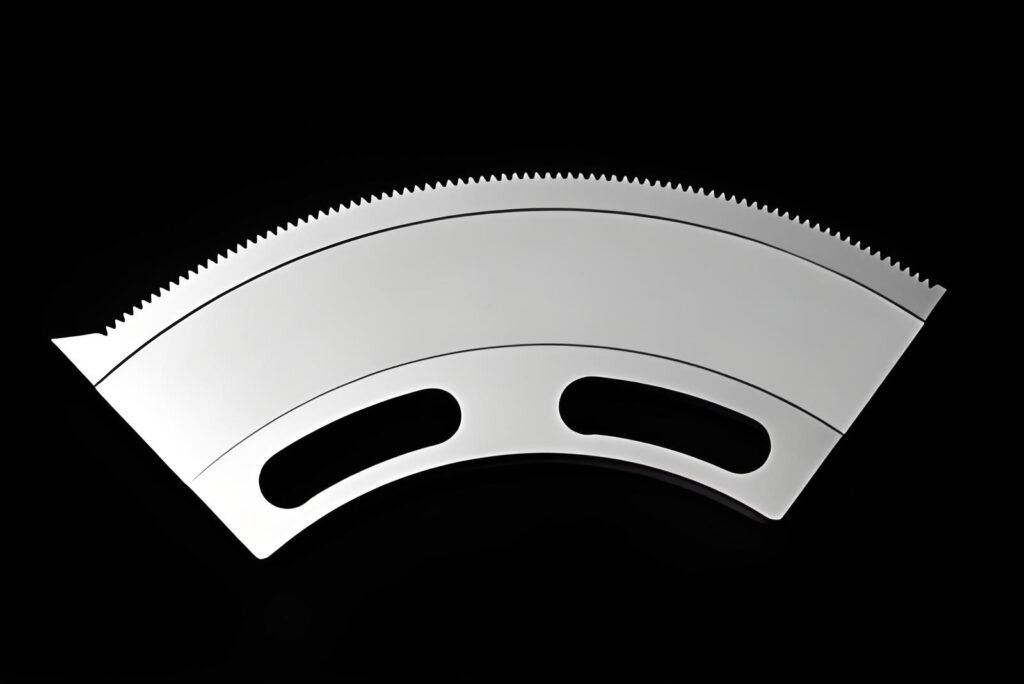
2. Práticas essenciais de manutenção para alta precisão de corte
Manter alta precisão de corte requer um comprometimento com a manutenção regular, o que impacta diretamente a produtividade e a qualidade do produto. A manutenção adequada das facas de entalhe e da própria máquina de entalhe pode reduzir o tempo de inatividade dispendioso e melhorar a precisão do corte em até 25% ao longo do tempo. Aqui está uma análise mais detalhada de cada etapa de manutenção essencial e como ela contribui para um melhor desempenho.
Afiação e substituição regulares
A afiação é um fator crítico para garantir cortes consistentes e precisos. Lâminas cegas não só produzem bordas irregulares, mas também aumentam o risco de rasgos e desfiamentos, o que compromete a aparência e a integridade estrutural da caixa. Como orientação geral, é recomendado afiar as facas de ranhura a cada 8–10 horas de uso contínuo ou no final de cada turno de produção, dependendo da dureza e espessura do material. Pesquisas mostram que a afiação de rotina pode estender a vida útil da lâmina em 15–20%, reduzindo assim a frequência de substituição e minimizando o tempo de inatividade da máquina.
- Dica profissional: Use um serviço profissional de afiação ou invista em ferramentas de afiação de alta qualidade. Os sistemas de afiação automatizados, embora mais caros, podem melhorar a precisão e a consistência da afiação em 10–15% em comparação aos métodos manuais.
Verificações de alinhamento
O alinhamento preciso é essencial para evitar cortes errados e garantir que a lâmina opere com eficiência. Um desalinhamento de apenas 0,5 mm pode levar a cortes defeituosos e aumentar o desperdício de material. A execução regular de verificações de alinhamento, especialmente no início de cada turno de produção, pode evitar esses problemas e melhorar a precisão geral. Alguns operadores usam ferramentas de alinhamento digitais, que estão se tornando mais populares devido à sua facilidade de uso e confiabilidade. Essas ferramentas podem detectar e corrigir discrepâncias de alinhamento com precisão de até 98%, ajudando os operadores a manter uma qualidade de corte consistente.
- Dados da indústria: Estudos indicam que verificações consistentes de alinhamento podem reduzir cortes defeituosos em até 30%, resultando em um fluxo de produção mais suave e menos retrabalho.
Lubrificação e Limpeza
Lubrificação e limpeza adequadas são essenciais para garantir um movimento suave da lâmina e evitar desgaste prematuro. Poeira, resíduos de adesivos e partículas de papel frequentemente se acumulam nas facas de entalhe, o que pode causar arrasto e prejudicar a capacidade da lâmina de fazer cortes suaves. Os operadores devem aplicar lubrificante nas peças móveis da máquina de entalhe, incluindo o eixo da lâmina e os rolamentos, de acordo com as recomendações do fabricante. Geralmente, lubrificar a cada 48 horas é adequado para a maioria das máquinas de entalhe de alta velocidade.
- Frequência de limpeza: Limpe as facas pelo menos uma vez por turno, ou com mais frequência em ambientes empoeirados, pois resíduos acumulados podem impactar a qualidade do corte em 5–10%. Usar ar comprimido ou uma escova macia ajuda a remover partículas finas sem danificar a lâmina.
Rotina de inspeção
Inspeções regulares fornecem uma oportunidade de detectar desgaste e danos potenciais precocemente, prevenindo tempo de inatividade inesperado e erros dispendiosos. Uma rotina de inspeção detalhada deve incluir:
- Exame visual: Verifique se há sinais visíveis de desgaste, lascas ou empenamentos na borda da lâmina. Substitua lâminas danificadas imediatamente para evitar danos aos materiais.
- Teste de lâmina: Execute um teste simples em uma caixa de amostra para verificar se a qualidade do corte atende às especificações. Isso pode ajudar a identificar problemas que podem não ser visíveis na inspeção.
- Registro de desempenho: Mantenha registros do desempenho de cada lâmina para identificar tendências de desgaste e antecipar necessidades de substituição. Dados indicam que empresas que usam registros de desempenho têm até 15% menos tempo de inatividade devido à detecção precoce de padrões de desgaste.
Ao seguir uma rotina de manutenção consistente, os operadores podem garantir que suas facas de entalhe ofereçam alta precisão, reduzam o desperdício e mantenham os níveis de produtividade.
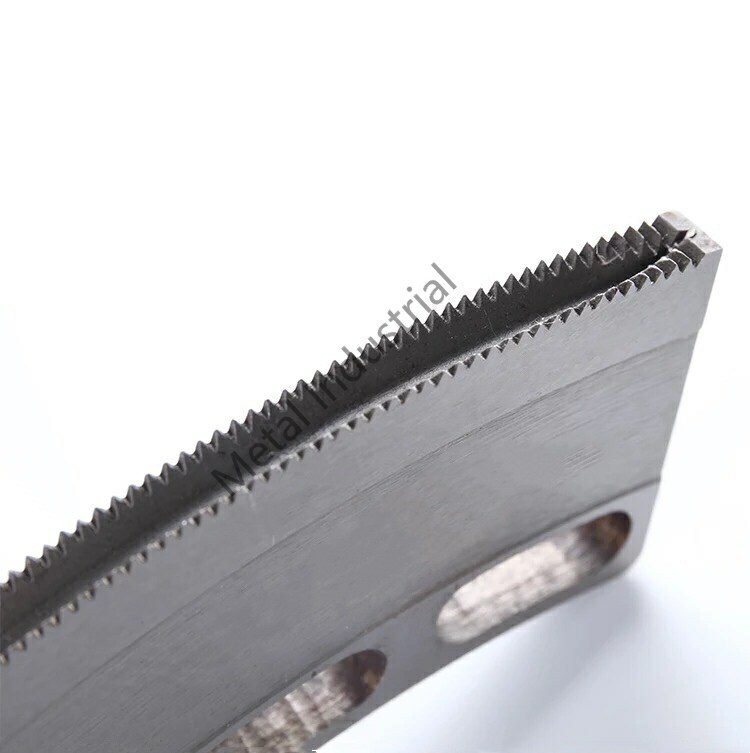
3. Atualizando para alta precisão Facas para impressoras Slotter
Investir em lâminas de ranhura de alta qualidade pode gerar benefícios significativos para fabricantes que buscam obter cortes precisos. Facas de alta precisão, geralmente feitas de materiais premium como aço temperado ou carboneto de tungstênio, são projetadas para fornecer cortes consistentes e precisos com manutenção mínima.
Tipos de facas de fenda de alta precisão
Existem vários tipos de facas de alta precisão no mercado, incluindo lâminas chanfradas, serrilhadas e de fio reto. Cada tipo tem vantagens únicas com base nos requisitos de corte:
- Lâminas chanfradas proporcionam cortes mais suaves e são ideais para materiais de papelão delicados.
- Lâminas serrilhadas funcionam bem para materiais mais resistentes e podem evitar desfiamento.
- Lâminas de corte reto oferecem versatilidade para cortes de uso geral.
Benefícios de materiais e designs premium
As facas de ranhura de alta precisão usam materiais de primeira linha projetados para durabilidade e precisão. Estudos mostram que facas de qualidade premium podem melhorar a precisão em até 20% e reduzir as necessidades de afiação em até 30%, aumentando a produtividade geral. Para fabricantes de caixas de papelão de alto volume, esses ganhos aumentam rapidamente, levando a custos operacionais mais baixos e margens de lucro mais altas.
4. Dicas para otimizar o desempenho da faca de ranhura da impressora
Otimizar o desempenho das facas de ranhura envolve mais do que apenas manutenção regular. Fazer pequenos ajustes na velocidade de corte, ângulos da lâmina e monitoramento pode aumentar a precisão, especialmente para grandes volumes de produção. Aqui estão algumas estratégias detalhadas para maximizar a precisão e a eficiência do corte.
Ajustando a velocidade de corte
A velocidade de corte afeta diretamente a qualidade e a precisão dos cortes. Geralmente, uma velocidade mais lenta pode resultar em cortes mais limpos e precisos, especialmente para materiais delicados. Estudos mostram que reduzir a velocidade de corte em 10–15% pode levar a uma melhoria de 20% na qualidade do corte para caixas finas e frágeis. No entanto, para materiais mais pesados e espessos, velocidades moderadas podem produzir os melhores resultados sem comprometer a produtividade.
- Dica de otimização: Considere testar velocidades diferentes com cada novo lote de materiais. Executar alguns cortes de teste em várias velocidades permite que os operadores identifiquem o equilíbrio ideal entre velocidade e precisão.
Otimizando ângulos de corte
O ângulo em que o faca de fenda atende à caixa afeta significativamente a qualidade da borda. Um ângulo de 45 graus geralmente funciona bem para materiais de caixa padrão, mas ajustar o ângulo para até 30 graus para materiais mais macios ou finos pode reduzir o desfiamento e produzir bordas mais suaves. A precisão nos ângulos de corte pode melhorar a qualidade do corte em até 18%, de acordo com dados do setor.
- Ajuste de ângulo: Os operadores devem monitorar a qualidade da borda e ajustar o ângulo da lâmina de acordo com o material que está sendo processado. Algumas máquinas permitem ajustes automáticos de ângulo, o que pode agilizar esse processo para operações de alto volume.

Usando Monitoramento Digital
Os sistemas de monitoramento digital fornecem feedback em tempo real sobre a nitidez da lâmina, alinhamento e configurações da máquina. Esses sistemas rastreiam a qualidade de cada corte e podem identificar variações sutis no desempenho, alertando os operadores antes que os problemas aumentem. Os sistemas de monitoramento digital podem aumentar a precisão em 15% e reduzir o tempo de inspeção manual em até 40%, oferecendo benefícios substanciais de eficiência.
- Custo vs. Benefício:Embora o monitoramento digital exija um investimento inicial, a redução de desperdício e retrabalho geralmente leva a um retorno total do investimento em 6 a 12 meses, especialmente para fabricantes de alto volume.
Treinamento do Operador
Operadores experientes desempenham um papel crucial na manutenção da precisão. O treinamento adequado em manuseio, configuração e manutenção da lâmina ajuda os operadores a tomar decisões informadas que melhoram a qualidade do corte. Pesquisas mostram que empresas com programas contínuos de treinamento de operadores apresentam até 20% menos problemas de precisão em comparação com aquelas com treinamento mínimo.
- Desenvolvimento de habilidades: Considere implementar sessões de treinamento regulares que abranjam novas técnicas, atualizações de máquinas e práticas de solução de problemas. O treinamento pode incluir prática com ferramentas de alinhamento, sistemas de monitoramento digital e otimização de ângulos de corte, tudo isso contribuindo para melhores resultados.
Essas dicas de otimização podem ajudar os fabricantes a obter precisão consistente, melhorar a produtividade e aprimorar a qualidade geral do produto.
5. Erros comuns a evitar ao trabalhar com facas de ranhura de impressora
Para maximizar o desempenho das facas de entalhe e manter alta precisão, é essencial evitar alguns erros comuns que podem levar a ineficiências, desperdício de material e custos adicionais.
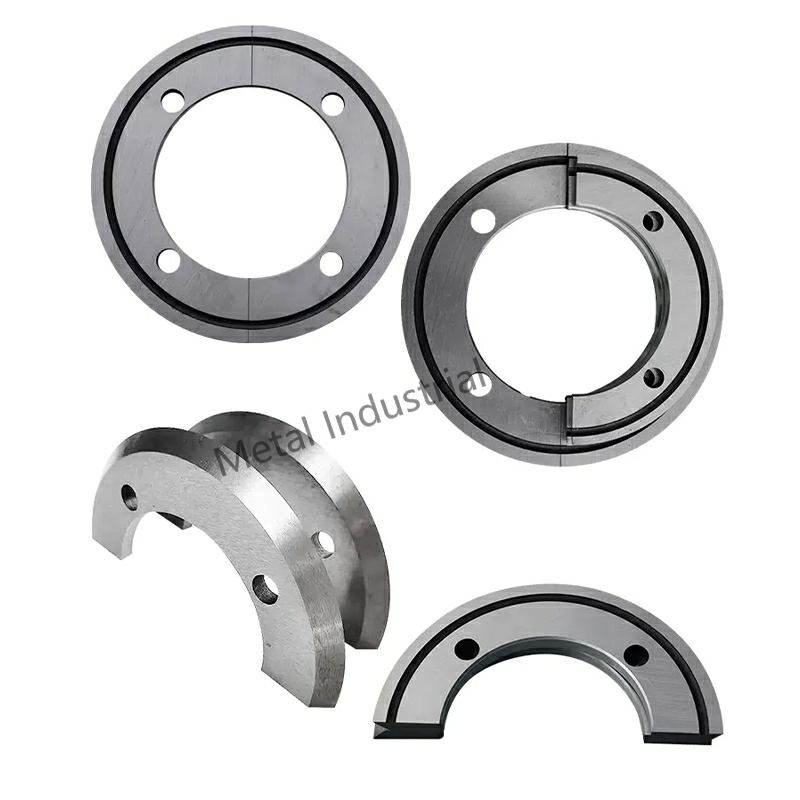
Negligenciar a manutenção da lâmina
Afiação pouco frequente ou substituição tardia de facas de ranhura é um dos erros mais comuns. Uma lâmina cega ou danificada não só reduzirá a precisão do corte, mas também pode aumentar o atrito, potencialmente levando à tensão da máquina e ao acúmulo de calor. A manutenção regular é crítica; estudos indicam que a manutenção consistente da lâmina reduz os erros de produção em até 30%. Ignorar cronogramas de afiação ou atrasar substituições pode causar cortes ásperos ou irregulares, levando a retrabalho e desperdício de material.
- Melhores práticas: Defina um cronograma fixo de afiação e substituição com base nos dados de uso e no tipo de material. Para ambientes de alto uso, verificações diárias e afiação quinzenal podem evitar degradação na qualidade do corte.
Configuração incorreta da lâmina
A configuração inadequada de facas de ranhura, incluindo alinhamento e posicionamento incorretos, pode resultar em cortes errados e até mesmo danos à máquina. Um leve desalinhamento de 0,5 mm pode criar um desvio cumulativo que afeta centenas de cortes, levando ao desperdício de material e aumento de custos. Estudos sugerem que práticas de configuração corretas podem melhorar a eficiência da produção em até 25%.
- Evite desalinhamento: Use ferramentas de alinhamento digitais ou guiadas a laser sempre que possível. Essas ferramentas oferecem precisão 98% e podem ajudar os operadores a atingir o posicionamento correto de forma rápida e confiável.
Ignorando a calibração da máquina
A calibração regular da máquina é necessária para garantir cortes precisos. Com o tempo, os componentes da máquina podem se soltar ou se deslocar levemente devido a vibrações e uso contínuo, impactando a precisão da faca de entalhe. Ignorar a calibração pode resultar em cortes irregulares ou angulados, aumentando o retrabalho e diminuindo a produção. Em configurações de alto volume, a falta de calibração pode resultar em um aumento de 10% em produtos defeituosos.
- Cronograma de calibração: Configure uma verificação de calibração bimestral, ou mais frequentemente para ambientes de produção intensiva. Algumas empresas descobrem que calibrações mensais reduzem erros em até 15%.
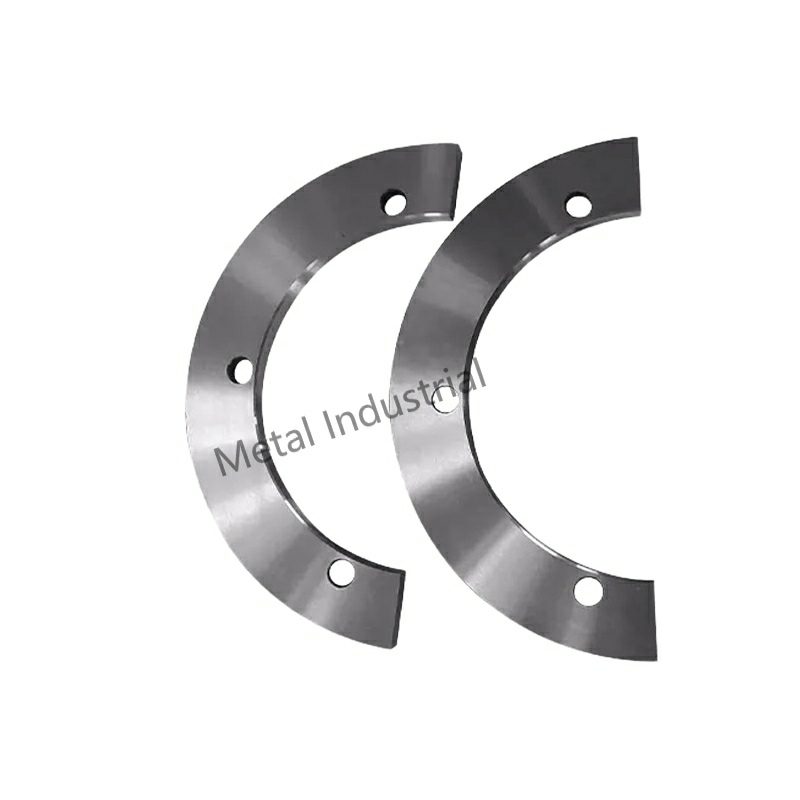
Negligenciando Fatores Ambientais
Fatores ambientais como temperatura, poeira e umidade muitas vezes passam despercebidos, mas podem impactar significativamente o desempenho da lâmina e a estabilidade do material. Altas temperaturas podem levar à expansão do metal, enquanto o acúmulo de poeira aumenta o atrito da lâmina. Os operadores devem implementar controles ambientais para estabilizar a temperatura e reduzir a poeira na área de trabalho.
- Ponto de dados: Estudos revelam que flutuações de temperatura de apenas 5 °C podem aumentar a expansão do material e levar a problemas de desalinhamento, reduzindo potencialmente a precisão de corte em 5%.
Ao abordar esses erros comuns, os fabricantes podem reduzir o desperdício, diminuir os custos operacionais e melhorar a consistência do corte. Evitar esses erros contribuirá, em última análise, para maior eficiência, melhor qualidade do produto e maior lucratividade.
Conclusão: Melhorando a precisão para melhor desempenho e eficiência de custos
O corte de alta precisão com lâminas de ranhura é essencial para produzir caixas de qualidade, reduzindo o desperdício e controlando os custos. Ao entender os fatores que influenciam a precisão, seguindo as melhores práticas de manutenção e investindo em facas de ranhura de qualidade, os fabricantes podem obter cortes precisos de forma consistente. A implementação dessas estratégias não apenas melhora a produtividade, mas também contribui para uma melhor qualidade do produto e satisfação do cliente. Para empresas que buscam atualizar ou otimizar seus processos de corte, nossa equipe está aqui para fornecer orientação especializada sobre como escolher as lâminas certas e as melhores práticas para maximizar a precisão.