Summary
Precision in Roll Shear Blades plays a critical role in achieving high-quality results in metal coil slitting. This article explores how precise blade manufacturing and maintenance improve slitting efficiency, reduce waste, and enhance overall production quality. Learn how choosing the right blades and suppliers can transform your slitting line’s performance.
1. Introduction: The Importance of Precision in Metal Coil Slitting
In industries where precision is paramount, metal coil slitting lines are indispensable. These systems cut wide coils of metal into narrower strips, catering to diverse applications such as automotive, construction, and electronics. However, the outcome of these processes hinges on a key component: the Roll Shear Blade.
High-quality slitting requires blades with exceptional precision. Without it, companies face problems like uneven cuts, increased material waste, and frequent machine downtime. This article answers a critical question: How does blade precision affect your slitting results and production efficiency?
By understanding the impact of blade precision, businesses can unlock higher productivity, better material utilization, and superior product quality. Let’s dive deeper.
2. Understanding the Roll Shear Blade: Structure and Function
What Is a Roll Shear Blade?
A Roll Shear Blade is a pivotal tool in metal coil slitting lines, designed to precisely cut wide coils of metal into narrower, uniform strips. These blades work in pairs—an upper blade rotates against a lower blade—to achieve clean cuts without distorting the metal. The process relies on the interplay of sharpness, alignment, and material strength to meet strict industrial standards.
The precision of a Roll Shear Blade determines not only the quality of the cuts but also the efficiency of the entire production line. Misalignment or inferior materials can lead to operational inefficiencies, costing companies time and money.
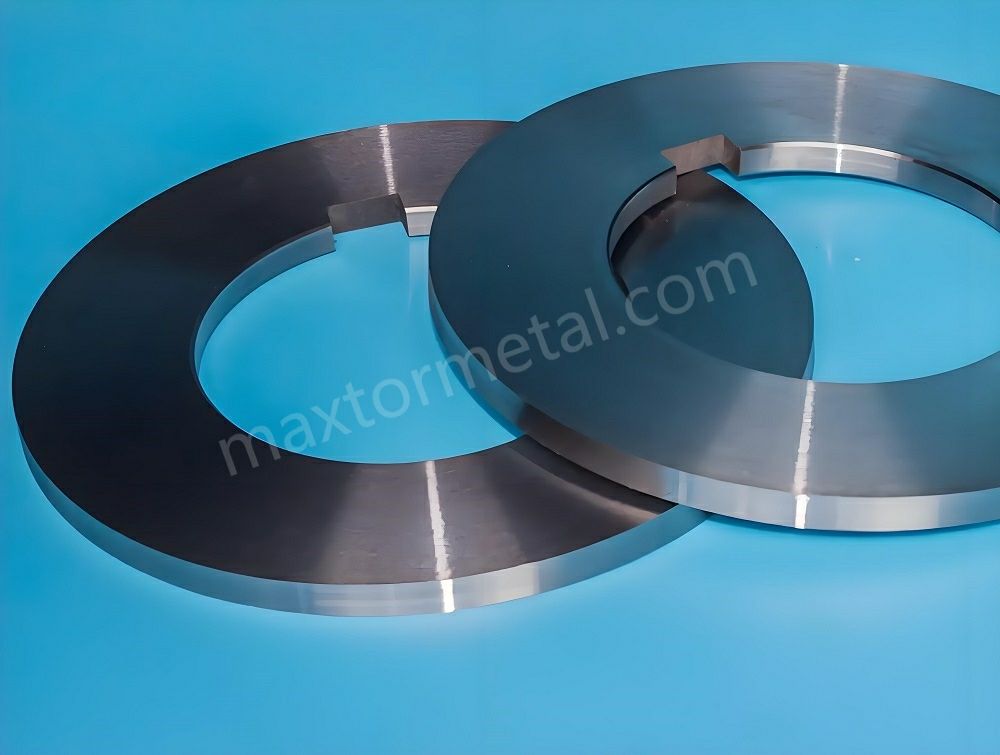
Blade Materials and Construction
The material of a blade significantly influences its performance and lifespan. Common materials include:
- High-Speed Steel (HSS): Known for exceptional sharpness retention and toughness, HSS blades are widely used in standard slitting operations.
- Carbide Blades: Offering superior wear resistance, carbide is ideal for high-volume or heavy-duty slitting. These blades can last up to 2-3 times longer than HSS in certain applications.
Blade construction also involves advanced processes like CNC machining and surface grinding to achieve tolerances as tight as ±0.001 mm, ensuring that every blade meets exacting specifications.
Key Factors Influencing Blade Performance
- Sharpness: Dull blades can damage the material and reduce efficiency. Regular sharpening maintains cutting quality.
- Hardness: Measured on the Rockwell scale, the hardness of a blade impacts its durability and ability to withstand heat during high-speed cutting.
- Alignment: Proper alignment of the upper and lower blades minimizes vibration and ensures precise cuts, reducing wear on both the blade and machinery.
By understanding these factors, businesses can better appreciate the importance of investing in high-quality blades.
3. The Impact of Blade Precision on Slitting Results
Why Precision Matters
Precision is the cornerstone of effective metal slitting. A blade with precise tolerances ensures consistent cuts, which directly impacts the usability of the final product. Conversely, even a small deviation can result in:
- Burr Formation: Uneven cuts leave burrs, which require additional processing and increase costs.
- Material Deformation: Misaligned blades can bend or warp the metal, rendering it unusable for further applications.
- Increased Downtime: Substandard blades wear out quickly, leading to frequent stoppages for replacements or repairs.
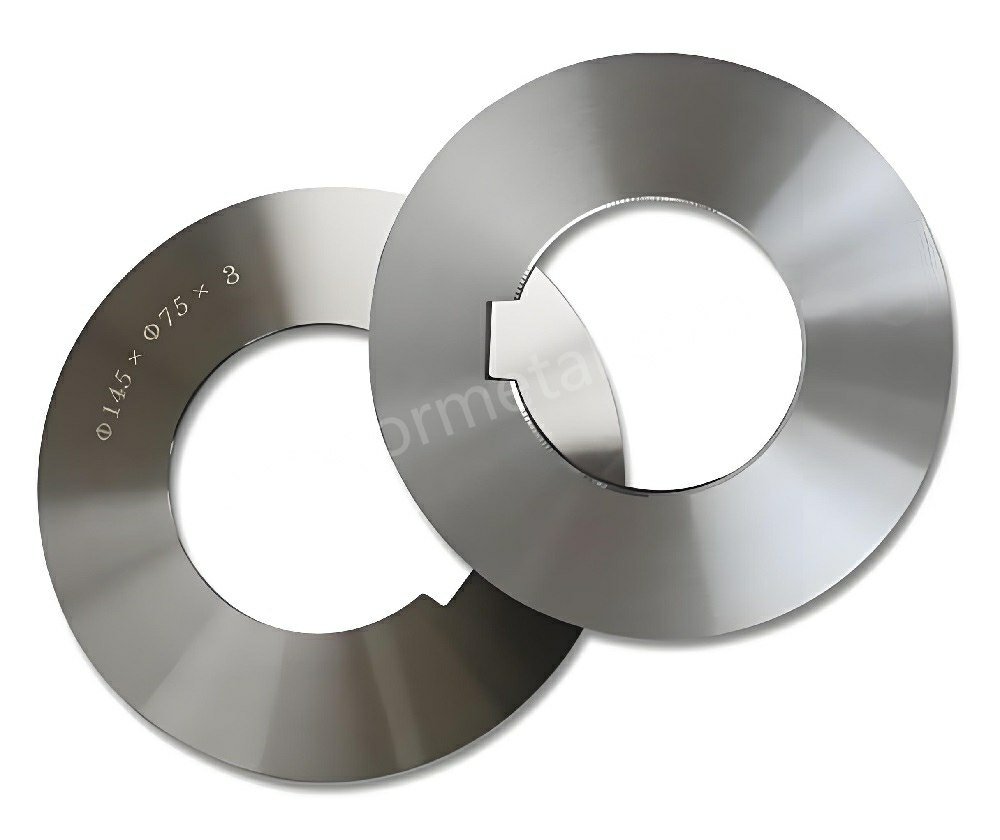
Real-World Data on Precision Benefits
A study conducted in a metal processing facility revealed the following improvements after switching to precision-engineered blades:
- Throughput increased by 20%, attributed to reduced downtimes.
- Scrap material reduced by 25%, saving thousands of dollars annually.
- Operators reported a 15% reduction in energy consumption, as precise cuts required less effort from the machines.
These metrics underscore the tangible benefits of investing in high-precision blades.
Challenges in Achieving Precision
- Blade Clearance: The gap between the upper and lower blades must be meticulously set based on the metal thickness. A variance of just 0.01 mm can compromise the cut.
- Blade Wear: Regular inspection and sharpening are critical to maintaining blade precision.
- Overheating: High-speed operations generate heat, which can alter blade dimensions and reduce sharpness. Using proper lubrication can mitigate this issue.
Precision blades offer more than just cleaner cuts—they enable smoother operations and significant cost savings.
4. Precision vs. Production Efficiency: A Delicate Balance
Cost vs. Benefits of Precision
The initial cost of high-precision blades may seem steep, but their long-term advantages make them a worthwhile investment. Consider this:
- Fewer Replacements: High-quality blades can last twice as long as standard blades, reducing replacement costs.
- Improved Efficiency: A precise blade cuts faster and cleaner, allowing for higher production speeds without compromising quality.
- Waste Reduction: With fewer defective cuts, waste can decrease by up to 30%, according to industry reports.
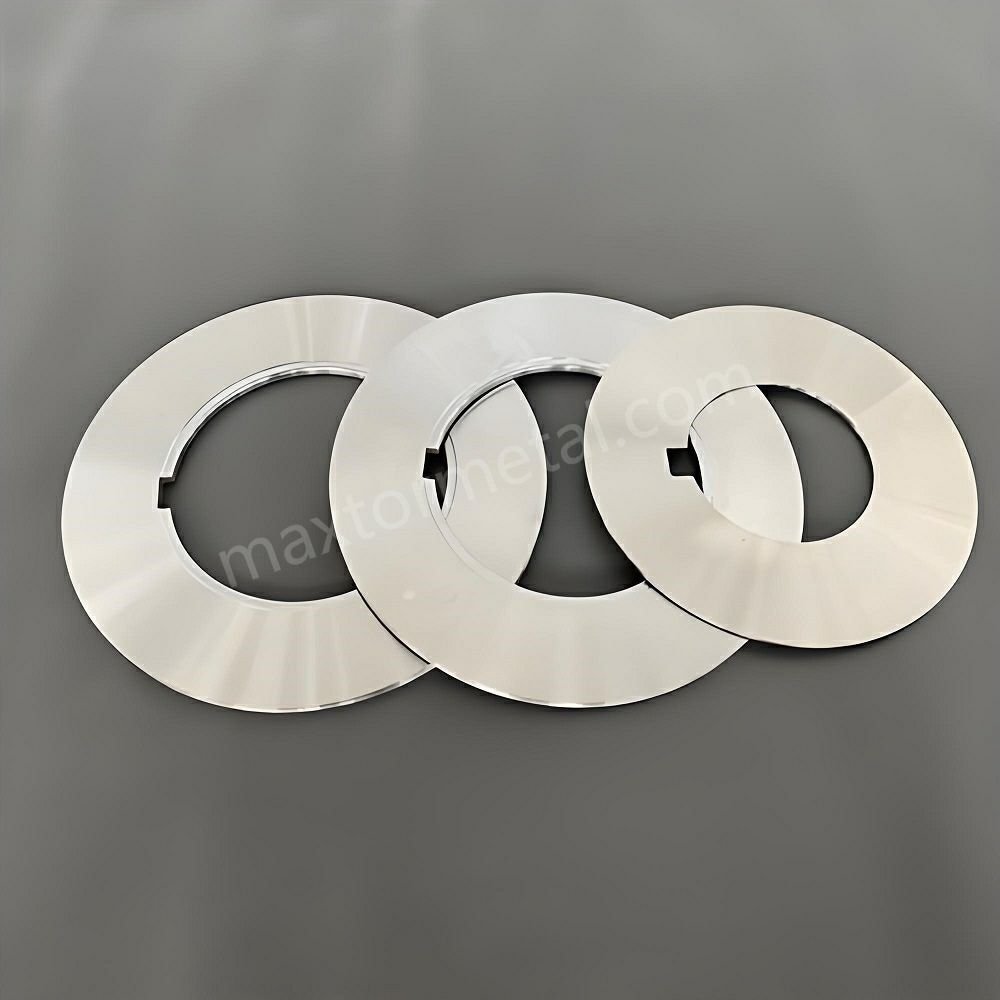
Case Study: Balancing Speed and Precision
A manufacturer of automotive components faced frequent quality issues due to misaligned slitting blades. After upgrading to precision Roll Shear Blades, they reported:
- A 40% improvement in production speed.
- A 50% reduction in rejected materials.
This demonstrates that precision blades enable manufacturers to achieve both speed and quality.
Economic and Operational Benefits
- Lower Maintenance Costs: High-grade blades are less prone to chipping or cracking, saving on maintenance expenses.
- Consistent Quality: Precision cuts meet industry standards, reducing the need for rework.
- Enhanced Machine Lifespan: Properly aligned blades minimize wear and tear on the slitting line’s components.
By striking the right balance, companies can optimize both production speed and cut quality.
5. Key Factors That Ensure Roll Shear Blade Precision
1. Material Selection
Material selection is the foundation of blade precision. High-speed steel and carbide are preferred for their durability and resistance to heat and wear. For instance, carbide blades can withstand cutting speeds of up to 2,000 meters per minute, making them ideal for demanding applications.
2. Advanced Manufacturing Techniques
- CNC Machining: Guarantees consistent blade dimensions within tolerances as tight as ±0.005 mm.
- Surface Grinding: Achieves ultra-sharp edges necessary for clean cuts, with edge quality often measured in microns.
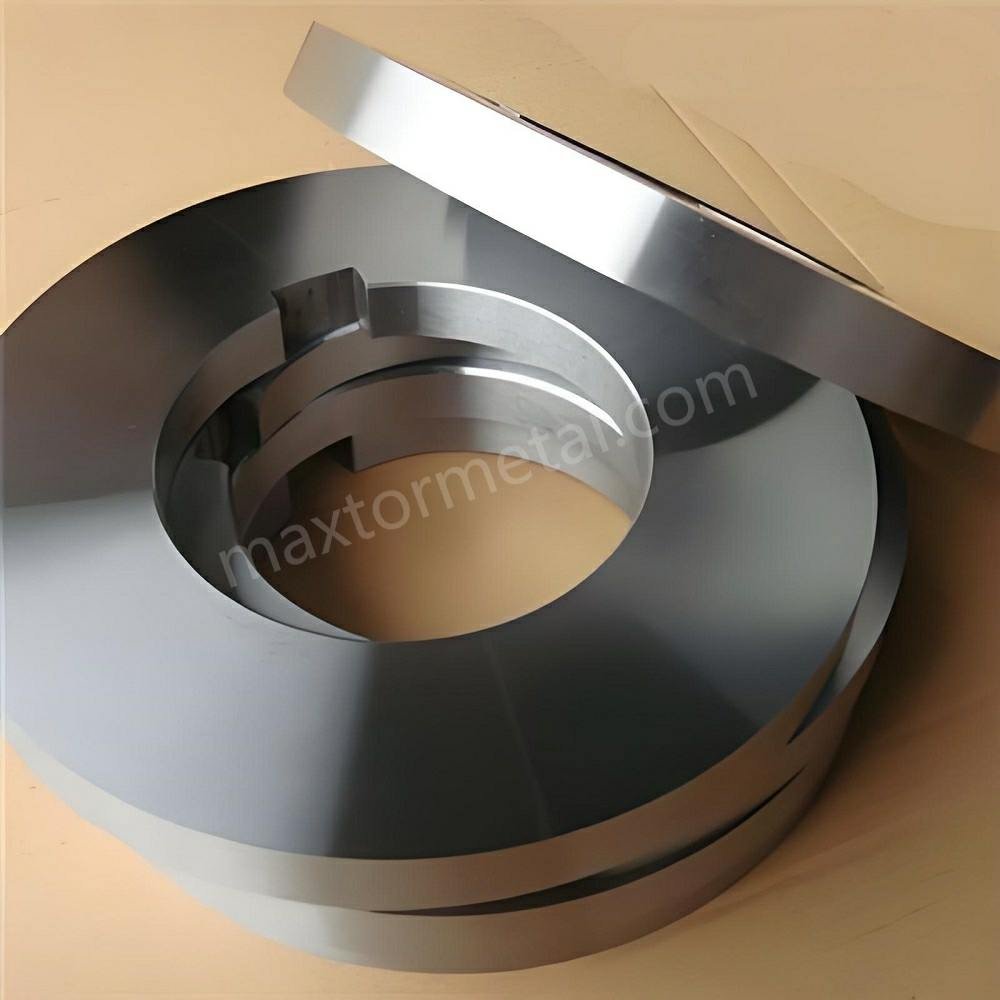
3. Rigorous Quality Control
Manufacturers employ multiple testing procedures to ensure every blade meets industry standards:
- Hardness Tests: Ensures durability under high-stress conditions.
- Dimensional Inspections: Confirms blade thickness and diameter for consistent performance.
4. Blade Maintenance Practices
To maintain precision, blades require regular care. Recommended practices include:
- Resharpening: Performed after every 200-300 hours of operation, depending on material type.
- Alignment Checks: Misaligned blades can cause uneven cuts and accelerate wear.
- Proper Storage: Storing blades in controlled environments prevents rust and deformation.
Impact of Maintenance on Performance
A survey of metal processors showed that companies adhering to strict maintenance schedules experienced a 25% reduction in downtime, highlighting the importance of proper blade care.
6. Choosing the Right Roll Shear Blade Supplier
Key Qualities to Look For
- Expertise in Precision Manufacturing: A reliable supplier should have years of experience and a portfolio of satisfied clients.
- Customization Options: Blades tailored to your specific slitting requirements ensure optimal performance.
- After-Sales Support: Services such as maintenance training and spare part availability add value.
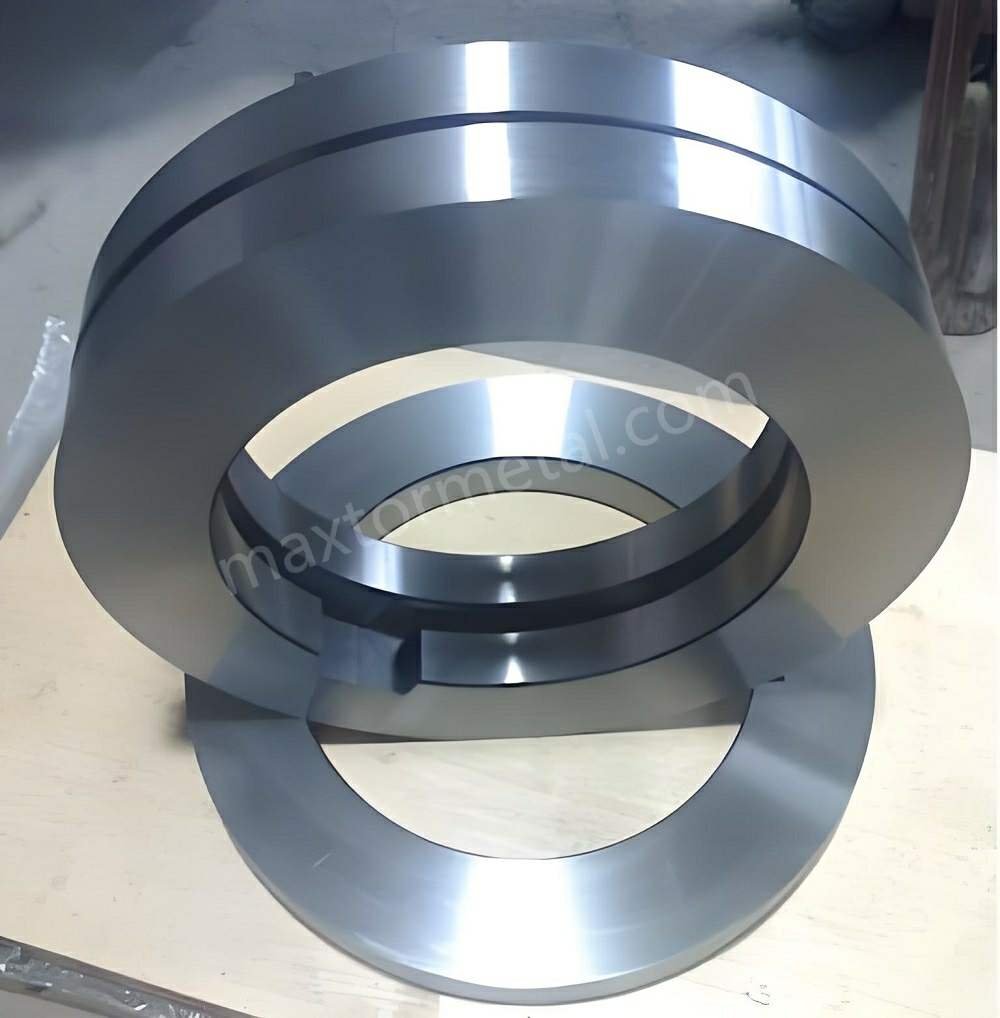
Data-Driven Decision Making
When selecting a supplier, ask for performance data or case studies. For instance, a top-tier supplier should be able to demonstrate how their blades achieve tolerances within ±0.001 mm or reduce downtime by a measurable percentage.
The Cost of Choosing Poorly
Subpar suppliers may offer lower prices but often compromise on quality. This can lead to:
- Frequent blade failures, increasing downtime.
- Higher material waste due to inconsistent cuts.
- Additional costs for rework and replacement.
Investing in a trusted supplier ensures long-term benefits and operational efficiency.
7. Conclusion: Invest in Precision for Long-Term Success
In the competitive world of metal coil processing, precision is non-negotiable. High-quality Roll Shear Blades enhance slitting line efficiency, reduce waste, and deliver consistent product quality.
By investing in precision-engineered blades, you unlock long-term savings and a competitive edge. Don’t let subpar blades hold back your production potential.
Ready to elevate your slitting line’s performance? Contact us today to explore our premium Roll Shear Blade solutions.
2 Responses