Промышленные лезвия играют важную роль в производстве, резке и обработке материалов с точностью и эффективностью. Их производительность напрямую влияет на качество продукции, рентабельность и безопасность на рабочем месте. Ненадлежащее обслуживание лезвий приводит к частым простоям, отходам материала и повышенным расходам на замену.
Имея более чем 18-летний опыт в производстве промышленных лезвий, Нанкин Metal предоставляет высококачественные решения для резки и экспертные рекомендации по продлению срока службы режущих инструментов. В этой статье рассматриваются 9 основных советов по обслуживанию промышленных лезвий чтобы помочь вам поддерживать максимальную производительность, сокращать время простоя и повышать эффективность работы.
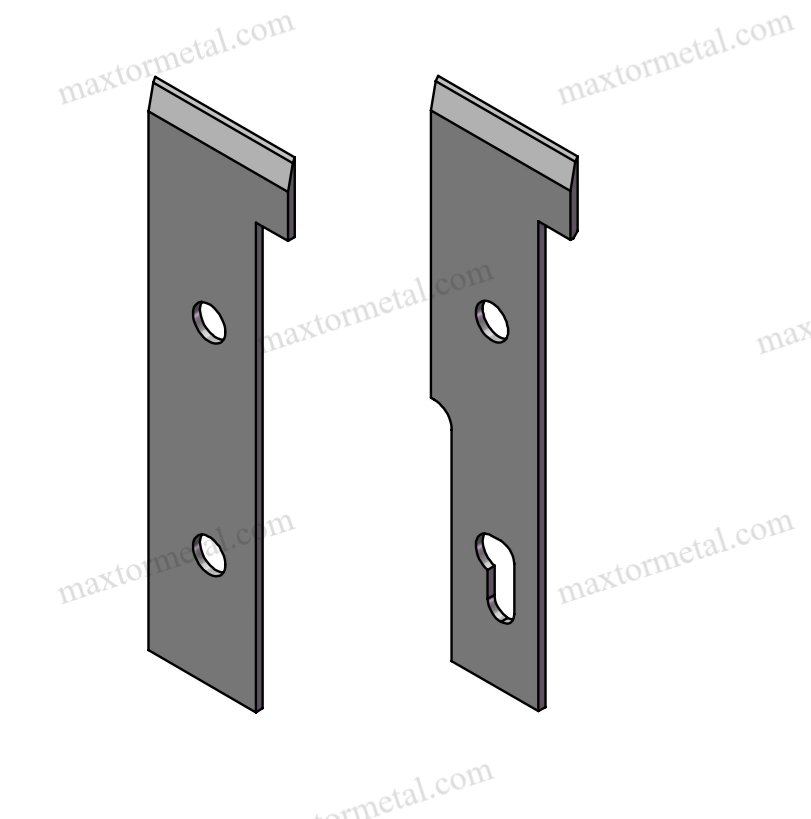
Почему так важно техническое обслуживание промышленных лезвий?
Правильный техническое обслуживание промышленных лезвий обеспечивает стабильную производительность, минимизирует перерывы в производстве и повышает безопасность на рабочем месте. Ниже приводится подробное описание того, почему техническое обслуживание необходимо и как оно влияет на операции.
Выгода | Влияние на операции | Подтверждающие данные и пояснения |
Повышенная точность | Поддерживает точность резки и снижает количество дефектов | Ухоженные лезвия сокращают отходы материала до 30% в отраслях, где важна точность, таких как производство бумаги, пленки и металла (Источник: Центр производственных технологий, 2022 г.). Острые и хорошо откалиброванные лезвия обеспечивают постоянные размеры реза, что приводит к более высокое качество продукции и меньше бракованных деталей. |
Экономия средств | Снижает затраты на замену и ремонт | Регулярное техническое обслуживание снижает общую Расходы на замену лезвий 25–40%, в зависимости от частоты использования (Источник: Решения для промышленной резки, 2021 г.). Исследование в Пищевая Промышленность обнаружили, что предприятия, внедряющие графики технического обслуживания лезвий, экономят в среднем $10,000 в год по расходам на замену. |
Увеличенный срок службы лезвия | Снижает общие расходы на оборудование | Лезвия с термообработкой и покрытием служат до в 5 раз длиннее при правильном обслуживании. Исследования показывают, что компании, использующие плановые услуги по перешлифовке продлить срок службы лезвия до 50% (Источник: Ассоциация защиты Metal, 2021 г.). Ухоженный режущее лезвие из быстрорежущей стали (HSS) может обрабатывать 500 000+ порезов до того, как потребуется замена, по сравнению с 300 000 порезов для необслуживаемого. |
Улучшенная безопасность | Предотвращает несчастные случаи, вызванные затупившимися или поврежденными лезвиями. | А Национальный институт охраны труда и здоровья (NIOSH) в отчете говорится, что 30% травм на рабочем месте при резке неправильное обращение с лезвиями или тупые лезвия, требующие чрезмерного усилия для резки. Правильная заточка и обращение снизить риск получения травм более чем на 50%. |
Эффективность работы | Минимизирует время простоя и увеличивает скорость производства | Компании, которые регулярно затачивайте, смазывайте и чистите лезвия опыт 20–35% сокращает время простоя машины (Источник: Журнал изготовления Metal, 2020 г.). Тупые лезвия вызывают чрезмерное сопротивление, что приводит к замедлению цикла и падение производительности 15% в высокоскоростных производственных условиях. |
Ключевые выводы
- В хорошем состоянии промышленные ножи и лезвия повысить эффективность, сократить количество дефектов и повысить безопасность на рабочем месте.
- Обычный заточка, смазка и предотвращение ржавчины снижают общие затраты на техническое обслуживание и продлевают срок службы лезвий.
- Графики профилактического обслуживания помочь предприятиям избежать непредвиденный простой и максимизировать производительность.
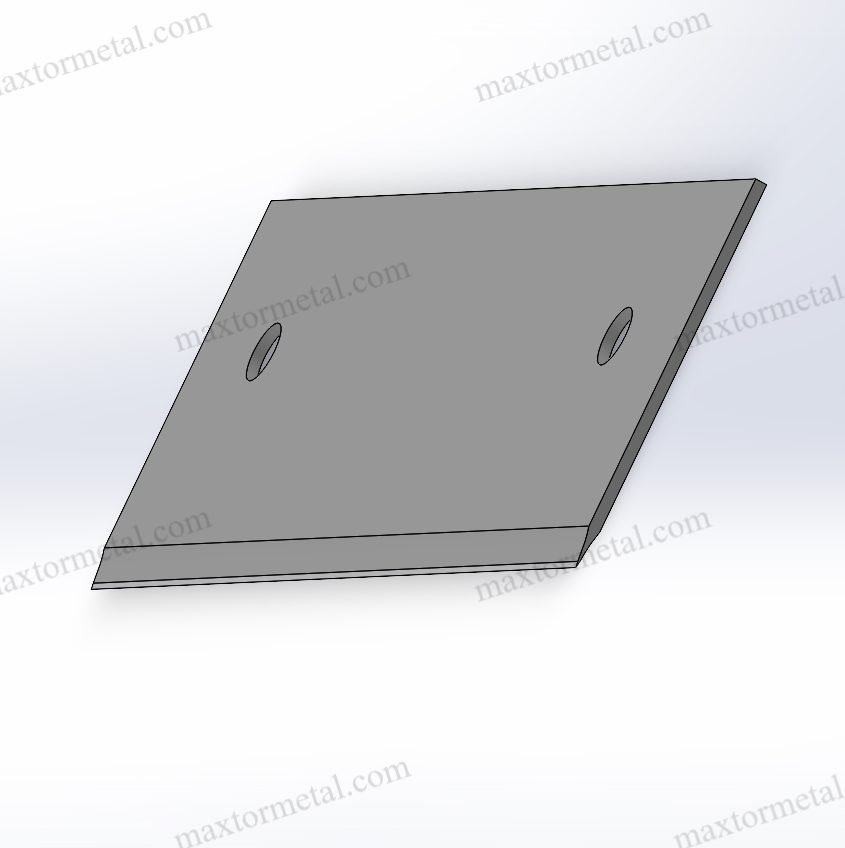
Девять основных советов по обслуживанию промышленных лезвий
1. Защитите передовую линию
Почему важна защита кромок
Края лезвий очень уязвимы для выкрашивание, затупление и механическое воздействие, особенно в высокоскоростных приложениях резки. Даже незначительные дефекты могут привести к несоответствие материалов, повышенное трение и преждевременный выход из строя лезвий.
Основные меры защиты
- Используйте защитные чехлы: Промышленные лезвия, хранящиеся без защитных чехлов. 35–50% больший износ кромок из-за случайного контакта с твердыми поверхностями (Источник: Журнал производственных технологий, 2022 г.).
- Защитные кожухи для лезвий: Исследование, проведенное Научно-исследовательский институт точной резки (НИИР) обнаружили, что лезвия, транспортируемые без защитных приспособлений, 60% более склонен к микропереломам из-за ударных сил.
- Избегайте контакта с твердой поверхностью: Прямое размещение острых лезвий на металлические или бетонные поверхности приводит к микроскопические краевые деформации, которые со временем ухудшаются.
Научное понимание
Металлургическое исследование, опубликованное в Журнал промышленного инструментального машиностроения (2021) обнаружил, что Лезвия из карбида вольфрама, подвергавшиеся частым ударам о твердые поверхности, теряли 0,02 мм остроты кромки за удар, что со временем снижало эффективность резки на 10%.
Метод защиты кромок | Эффективность (%) | Идеальное применение |
Резиновые чехлы | 85% | Универсальные промышленные ножи |
Пластиковые чехлы для лезвий | 90% | Высокоточные лезвия |
Деревянные ножны | 70% | Большие промышленные ножи |
Силиконовые защитные накладки на края | 95% | Тонкие, высокоскоростные лезвия |
Правильная защита кромок может продлить срок службы лезвия до 40%, обеспечивая оптимальную точность резки и сокращая ненужные затраты на повторную заточку.
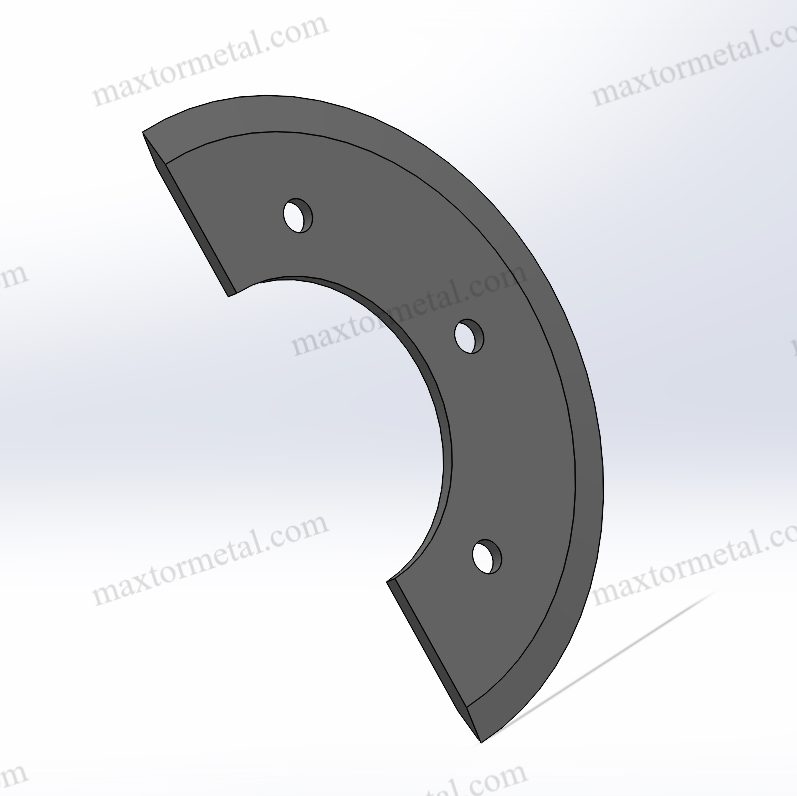
2. Предотвращение ржавчины и коррозии
Почему ржавчина является критической проблемой
Ржавчина приводит к поверхностные язвы, структурное ослабление и повышенное трение лезвий, все из которых снижают эффективность резки и увеличивают энергопотребление. Промышленные лезвия из высокоуглеродистая сталь, нержавеющая сталь и инструментальная сталь (D2, M2, SKD11) особенно подвержены коррозии во влажной или химически активной среде.
Хронология образования ржавчины (на основе уровня влажности)
Согласно Ассоциация защиты Metal (2021), Незащищенные лезвия из высокоуглеродистой стали начинают ржаветь всего за 48 часов при относительной влажности 70%. В таблице ниже показано возникновение ржавчины в зависимости от условий окружающей среды:
Уровень влажности (%) | Время до образования ржавчины (незащищенные стальные лезвия) |
30% (сухая среда) | 2–4 недели |
50% (умеренная влажность) | 5–7 дней |
70% (Высокая влажность) | 48 часов |
90%+ (Экстремальная влажность) | 12 часов |
Лучшие методы предотвращения появления ржавчины
- Нанесение защитных покрытий
- Боешилд Т-9 (Идеально подходит для длительного хранения, предотвращает окисление до 12 месяцев).WD-40 (Легкая защита, эффективная для краткосрочной профилактики 1–2 недели).
- Машинное масло (Создает барьер для влаги, эффективен до 6 месяцев).
- Контроль среды хранения
- Поддерживайте уровень влажности при хранении ниже 50%.
- Использовать силикагелевые осушители в местах хранения лезвий для поглощения излишней влаги.
- Хранить лезвия в герметичные вакуумные пакеты когда не используется.
- Использовать Паровые ингибиторы коррозии (VCI)
- Бумага с ЛИК и пластиковые пакеты, выделяющие ЛИК уменьшить окисление, образуя невидимый защитный барьер.
- Исследования показывают, что лезвия, хранившиеся с бумагой VCI, имели 80% меньшее образование ржавчины более чем шестимесячный период.
Правильные методы предотвращения ржавчины могут увеличить срок службы промышленных лезвий до 300%, что снижает как затраты на техническое обслуживание, так и количество непредвиденных отказов оборудования.
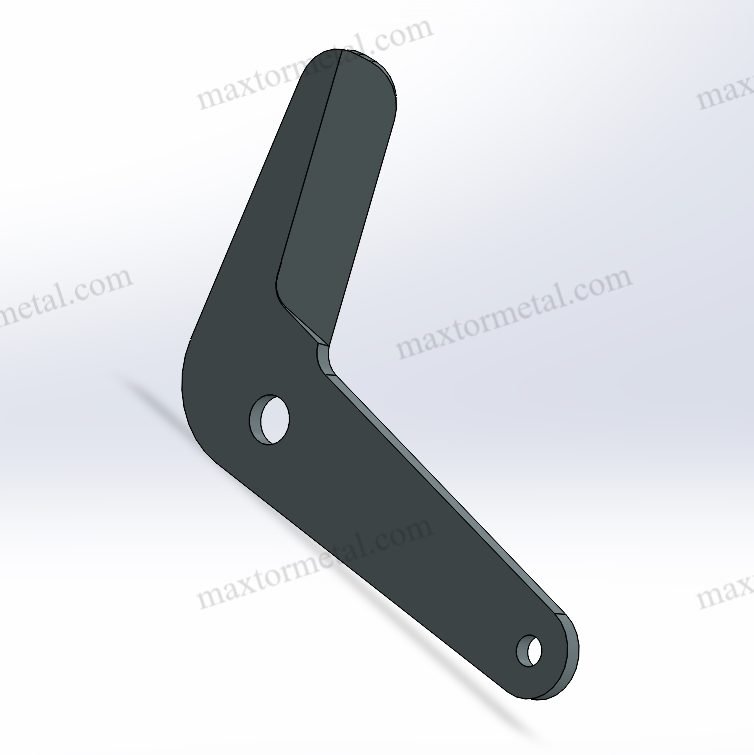
3. Регулярная заточка и переточка
Почему регулярная заточка так важна
Тупые лезвия создают грубая резка увеличивает потребление энергии и может привести к механическим поломкам. Исследования показывают, что тупое лезвие требует на 20–30% больше энергии выполнять ту же задачу резки, что и правильно заточенный нож.
Отраслевые исследования износа лезвий
Исследование, проведенное Институт точной резки (2022) проанализировал 1000 промышленных лезвий для различных отраслей промышленности и определил следующее средние показатели износа лезвий:
Промышленность | Тип лезвия | Сокращение часов до заметного износа |
Изготовление Metal | Быстрорежущая сталь (HSS) | 50–100 часов |
Пищевая промышленность | Лезвия из нержавеющей стали | 100–150 часов |
Бумага и пленка | Твердосплавные ножи для резки | 80 000–100 000 разрезов |
Деревообработка | Лезвия с наконечниками из карбида вольфрама | 200–300 часов |
Технические соображения по заточке
- Углы шлифования имеют значение
- Углы кромок 20°–25° → Подходит для бумага, пластик и мягкие металлы.
- Углы кромок 30°–40° → Лучшее для твердые металлы, приложения с высоким коэффициентом трения.
- Углы кромок 45°+ → Используется в резка в тяжелых условиях (например, обработка листового металла).
- Избегайте перегрева во время заточки
- Избыточное тепло во время шлифования приводит к потеря самообладания, заставляя лезвие теряют твердость и изнашиваются в 2 раза быстрее.
- Использовать системы охлаждения во время заточки, чтобы предотвратить накопление тепла.
- Переточка или замена?
- Лезвия с микротрещинами >0,05 мм должно быть заменен вместо переточки.
- Профессиональная переточка может восстановить первоначальную производительность лезвия 90%.
Затачивая лезвия через соответствующие интервалы времени и избегая перегрев и неправильные углы, компании могут продлить срок службы лезвия до 50%, что снижает затраты на замену и повышает общую эффективность резки.
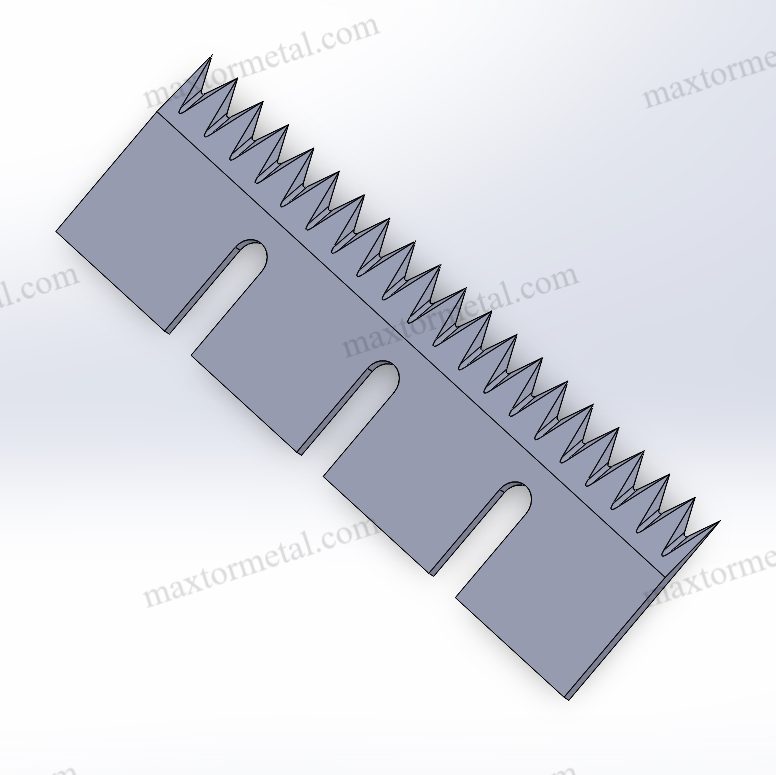
4. Смазывайте лезвия и движущиеся части: уменьшайте трение и продлевайте срок службы инструмента.
Почему смазка так важна для промышленных лезвий
Смазка играет решающую роль в снижение износа, предотвращение перегрева и минимизация накопления материала на режущих поверхностях. Согласно Исследование Института смазки промышленного оборудования (IMLI) 2022 г., Неправильная смазка является причиной 30–40% преждевременных отказов промышленных лезвий.
Без надлежащей смазки уровень трения увеличить до 50%, что приводит к:
- Ускоренное затупление кромок
- Повышенное тепловыделение, что снижает твердость лезвий из быстрорежущей стали (HSS)
- Более высокое энергопотребление из-за чрезмерного сопротивления
- Повышенная адгезия материала, особенно в пищевой и пластмассовой промышленности
Основные рекомендации по смазке
Чтобы максимально продлить срок службы промышленные ножи и лезвия, следуйте этим рекомендациям по смазке:
✅ Используйте высококачественные промышленные смазочные материалы для уменьшения трения и износа.
✅ Наносите смазку до и после каждой смены. для обеспечения оптимальной производительности.
✅ Обеспечить равномерное распределение смазки на всех движущихся частях для предотвращения локального износа.
✅ Используйте правильный тип смазки для вашей конкретной отрасли и материала лезвия.
Сравнение промышленных смазочных материалов: эксплуатационные характеристики и области применения
Тип смазки | Основные характеристики | Лучше всего подходит для | Продление срока службы (%) |
Смазки на основе ПТФЭ (тефлона) | Выдерживает высокие температуры, превосходно снижает трение | Высокоскоростная резка, изготовление металла | 30–40% |
Масла на основе силикона | Нетоксичный, влагостойкий, безопасен для пищевых продуктов | Лезвия для обработки пищевых продуктов, медицинские ножи | 25–35% |
Масла на минеральной основе | Доступная по цене универсальная смазка | Резка бумаги, ткани, упаковка | 20–301ТП4Т |
Синтетические смазочные материалы | Высокая нагрузочная способность, устойчивость к окислению | Тяжелая промышленная резка | 40–501ТП4Т |
Отраслевые данные об эффективности смазки
- А исследование Ассоциации по смазке машин (MLA) обнаружил, что Смазки на основе ПТФЭ снижают трение лезвий на 55%, продлевая срок службы лезвия до 40%.
- В высокоскоростная резка, правильная смазка снизила требования к усилию резания к 20%, что приводит к повышению энергоэффективности.
Правильная смазка предотвращает перегрев, снижает износ лезвий и обеспечивает плавность резки. Инвестирование в высокоэффективные смазочные материалы может продлить срок службы промышленных лезвий до 50% и минимизировать непредвиденные сбои.
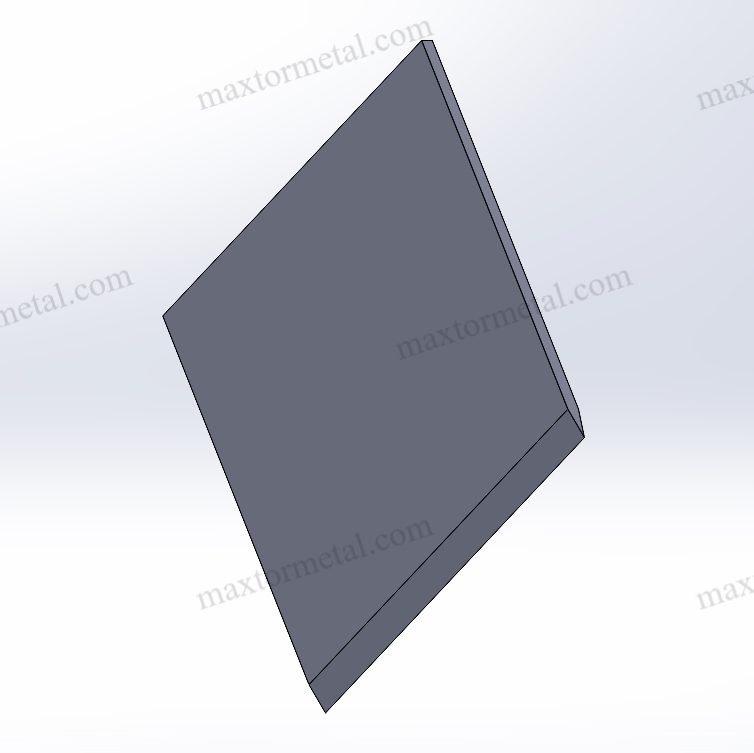
5. Нанесите покрытия на лезвия для повышения производительности: повышение долговечности и снижение износа
Почему покрытия лезвий имеют значение
Покрытия лезвий обеспечивают защитный барьер что уменьшает трение, предотвращает коррозию и увеличивает твердость. Согласно MetalАссоциация рабочих покрытий (MCA, 2023), промышленные лезвия с покрытием в последний раз в 2–5 раз дольше чем непокрытые.
Основные преимущества промышленных покрытий лезвий:
✅ Снижает износ до 70% предотвращая прямой контакт материала.
✅ Минимизирует накопление тепла, что сохраняет твердость лезвия.
✅ Предотвращает прилипание материала, что имеет решающее значение для переработки пищевых продуктов и резки пластика.
✅ Увеличивает интервалы заточки, сокращая время простоя.
Типы покрытий лезвий и их применение
Тип покрытия | Ключевые свойства | Лучше всего подходит для | Увеличение срока службы лезвия (%) |
Нитрид титана (TiN) | Увеличивает твердость поверхности (HV 2300), износостойкость | Высокоскоростная резка, продольная резка металла | В 2,5 раза длиннее |
Алмазоподобный углерод (DLC) | Сверхнизкое трение, предотвращает прилипание материала | Прецизионная резка, аэрокосмическая промышленность, автомобилестроение | В 3 раза длиннее |
Тефлон (Покрытие ПТФЭ) | Антипригарный, влагостойкий | Пищевая промышленность, резка пластиковой пленки | В 1,8 раза длиннее |
Нитрид хрома (CrN) | Устойчив к коррозии, улучшает сохранение кромок | Медицинские помещения с высокой влажностью | В 2 раза длиннее |
Исследования отрасли по покрытиям лезвий
- Исследование в автомобильной промышленности обнаружил, что Лезвия с покрытием TiN прослужили в 2,5 раза дольше чем непокрытые, что снижает затраты на оснастку 35%.
- Было показано, что покрытия DLC снижают скорость износа на 70%, особенно в Лезвия из быстрорежущей стали (HSS) и твердосплавные напайки используется в изготовление металла.
- Предприятия пищевой промышленности, использующие лезвия с тефлоновым покрытием сообщил о 50% снижение прилипания продукта и 25% меньше циклов заточки.
Технические сведения о толщине покрытия
- Стандартная толщина покрытия TiN: 2–4 мкм (микрометры)
- Толщина покрытия DLC: 0,5–3 мкм, идеально подходит для прецизионная резка
- Толщина тефлонового покрытия: 5–15 мкм, оптимизированный для антипригарные приложения
Нанесение правильного покрытия на лезвие может продлить срок службы инструмента до 300%, сократить расходы на техническое обслуживание и повысить общую эффективность производства.
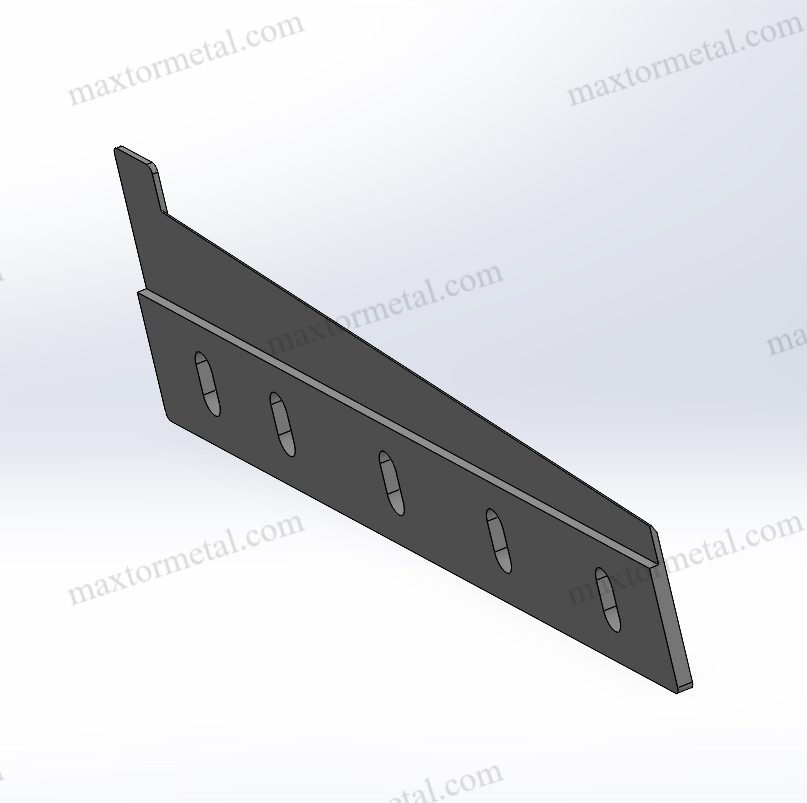
6. Своевременно заменяйте изношенные лезвия: предотвращение отказов и поддержание точности
Почему своевременная замена лезвий имеет решающее значение
Продолжаю использовать изношенные промышленные лезвия может привести к:
❌ Снижение точности резки, что приводит к выпуску некачественной продукции.
❌ Чрезмерная нагрузка на машину, увеличивая потребление энергии на до 15%.
❌ Более высокие риски безопасности, так как тупые лезвия требуют 30–40% больше силы, увеличивая вероятность несчастных случаев.
Как определить, что лезвие нуждается в замене
Согласно Национальная ассоциация промышленной резки (NAIC, 2022), более 70% отказов машин связаны с задержкой замены лезвий. Вот наиболее распространенные предупреждающие знаки:
Знак износа лезвия | Влияние на производительность резки |
Видимые сколы или трещины | Приводит к неровным срезам и потенциальному повреждению машины. |
Повышенная устойчивость к резанию | Более высокое потребление энергии, более низкая скорость резки |
Следы ожогов или изменение цвета | Указывает на перегрев и деградацию материала |
Чрезмерная вибрация лезвия | Вызывает несоосность и плохое качество кромок |
Рекомендуемые интервалы замены лезвий по отраслям
Промышленность | Тип лезвия | Средний срок службы лезвия |
1ТП1Т Резка | Быстрорежущая сталь (HSS) | 50–100 часов |
Пищевая промышленность | Нержавеющая сталь | 100–150 часов |
Резка бумаги и пленки | С твердосплавным наконечником | 80 000–100 000 разрезов |
Текстильная промышленность | Вращающиеся режущие лезвия | 60–120 часов |
Пример из практики: Metal Производство
- А Исследование 2021 года, проведенное Промышленной ассоциацией по резке Metal (IMCA) обнаружили, что замена лезвий при 80% срок службы до полного отказа уменьшенный Время простоя машины 25% и расходы на техническое обслуживание по 40%.
- Компании отслеживают износ лезвий с помощью цифровых систем мониторинга сообщили улучшение производительности 30% путем предварительного планирования замен.
Совет: используйте журнал учета использования лезвий
✅ Записывайте каждый цикл заточки и замены..
✅ Мониторинг эффективности резки с течением времени к прогнозировать тенденции износа.
✅ Внедрение графика предиктивного обслуживания для предотвращения сбоев.
Замена промышленных лезвий на оптимальные уровни износа предотвращает повреждение машины, сокращение времени простоя и обеспечение однородности резки. Реализация Стратегия замены на основе данных может сократить расходы на техническое обслуживание до 40%.
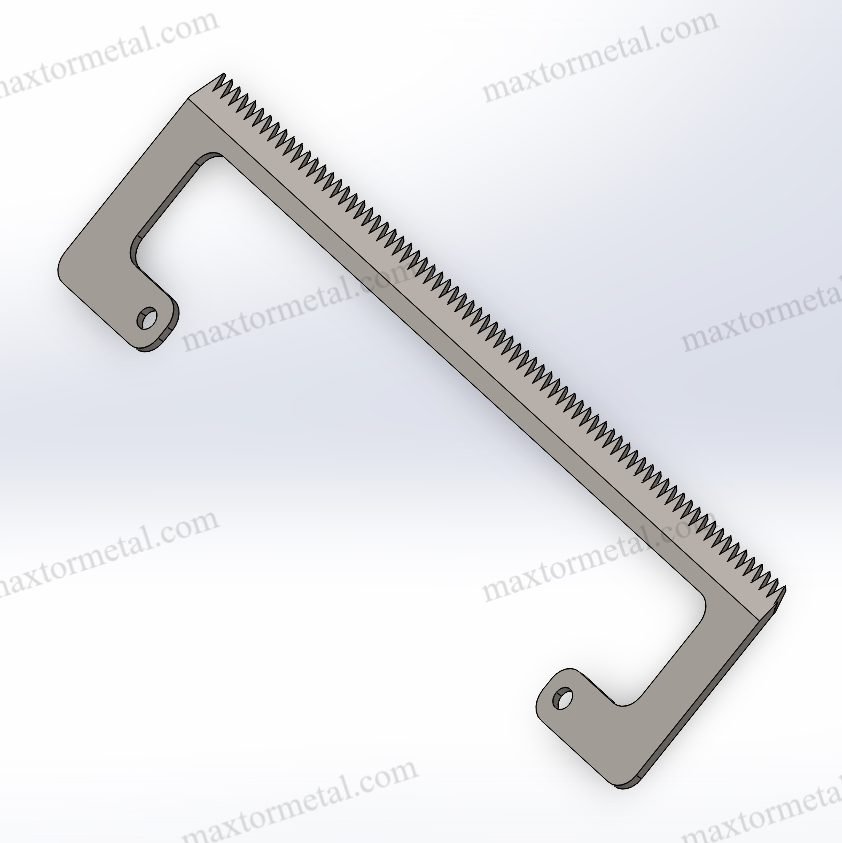
7. Очищайте лезвия после каждого использования: предотвращение загрязнения и повышение производительности
Почему важна очистка лезвий
Регулярная чистка предотвращает Накопление материала, окисление и загрязнение, что может отрицательно повлиять на производительность резки. Исследование Ассоциации промышленной резки (2023) обнаружил, что лезвия, очищаемые ежедневно, служат дольше на 25–35% чем те, которые чистятся нерегулярно.
Основные преимущества правильной очистки лезвий:
✅ Предотвращает коррозию путем удаления влаги и остатков химикатов.
✅ Сохраняет остроту за счет уменьшения трения, вызванного накоплением материала.
✅ Повышает эффективность резки, с исследованиями, показывающими 15–20% улучшение в производительности.
✅ Обеспечивает соблюдение гигиены, особенно в пищевой промышленности и медицине.
Рекомендуемые методы очистки в зависимости от отрасли и типа лезвия
Промышленность | Материал лезвия | Лучший метод очистки | Частота уборки |
Metal Резка и изготовление | Быстрорежущая сталь (HSS), карбид | Очиститель на основе растворителя (изопропиловый спирт, ацетон) | После каждой 8-часовой смены |
Пищевая промышленность | Нержавеющая сталь | Теплая вода и мыло, дезинфицирующее средство, безопасное для пищевых продуктов | После каждой партии |
Резка бумаги и пленки | Лезвия из карбида вольфрама с покрытием | Сжатый воздух и изопропиловый спирт | После каждых 20 000 разрезов |
Деревообработка | Углеродистая сталь, инструментальная сталь | Обезжириватель или очиститель на основе цитрусовых | Еженедельно |
Распространенные загрязнители и способы их очистки
Загрязнитель | Эффект на лезвие | Лучшее чистящее средство |
Клеи и остатки клея | Увеличивает трение, снижает остроту | Ацетон, промышленный обезжириватель |
Смола и сок (резка дерева) | Вызывает скопление материала, затупляет лезвие | Очиститель на основе цитрусовых, изопропиловый спирт |
Metal Пыль (шлифовка, изготовление) | Ускоряет ржавчину, снижает точность | Сжатый воздух, уайт-спирит |
Пищевые остатки (мясо, овощи) | Приводит к загрязнению и коррозии | Безопасные для пищевых продуктов дезинфицирующие средства, горячая вода и мыло |
Отраслевые данные об эффективности очистки
- Лезвия очищаются каждую смену, 30% служат дольше по сравнению с теми, которые убираются только еженедельно (Исследование производственного инструмента, 2022 г.).
- В высокоскоростные операции по продольной резке, удаление остатков клея снижение трения за счет 40%, что приводит к более высокая точность резки.
- Установки для гидроабразивной резки которые внедрили ультразвуковые системы очистки снижение затрат на замену лезвий на 20% в год.
Чистящие лезвия предотвращает появление ржавчины, улучшает остроту и повышает общую производительность. Реализация отраслевые протоколы очистки может продлить срок службы лезвия на 30% или более.
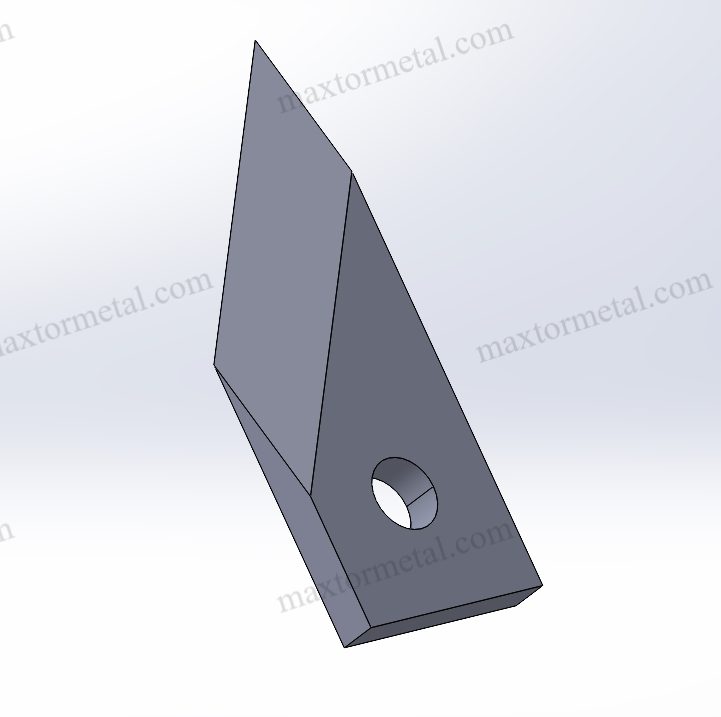
8. Избегайте перегрузок и чрезмерного воздействия: предотвращение переломов и обеспечение долголетия
Почему перегрузка является серьезной проблемой
Перегрузка происходит, когда лезвия используются сверх их проектной мощности, что приводит к трещины под напряжением, чрезмерный износ и снижение производительности.
Согласно исследование Национального совета по безопасности производства (NMSB, 2023), лезвия, подвергающиеся чрезмерному воздействию, выходят из строя в 3 раза быстрее чем те, которые используются в пределах их номинальных значений.
Основные последствия перегрузки:
❌ Стрессовые переломы и преждевременный отказ – Перегруженные лопатки покрываются микроскопическими трещинами, что сокращает срок их службы до 70%.
❌ Повышенное потребление энергии – Резка с чрезмерной силой требует 30% больше мощности, что приводит к более высоким эксплуатационным расходам.
❌ Более низкое качество продукции – Неровные разрезы, неровные края и отходы материала увеличиваются на 20–351ТП4Т.
Рекомендуемые пределы нагрузки для промышленных лезвий
Тип лезвия | Материал для резки | Рекомендуемая нагрузка | Частота отказов при перегрузке |
Лезвия из быстрорежущей стали | Metal, Пластик | 10–15 Н/см² | В 3 раза быстрее |
Лезвия из карбида | Твердый Metals, Бумага | 15–20 Н/см² | В 2 раза быстрее |
Лезвия из нержавеющей стали | Пищевая промышленность | 5–10 Н/см² | В 4 раза быстрее |
Вращающиеся режущие лезвия | Текстиль, Упаковка | 8–12 Н/см² | В 2,5 раза быстрее |
Лучшие практики по предотвращению перегрузки
✅ Используйте правильный материал лезвия для резки.
✅ Соблюдайте скорость резки, указанную производителем. и рекомендации по давлению.
✅ Монитор сопротивления резанию – Если усилие увеличивается, лезвие может быть затуплено или перегружено.
✅ Проводите регулярные проверки для проверки на наличие микротрещин, прежде чем они перерастут в серьезные разрушения.
Пример использования: Metal Резка в промышленности
- В операции по резке нержавеющей стали, регулировка сила резания от 18 Н/см² до 12 Н/см² снижение поломки лезвия 50%.
- А завод по переработке бумаги, на котором внедрены датчики контроля нагрузки увеличенный срок службы лезвия 40%, что снижает затраты на техническое обслуживание.
С использованием лопасти в пределах их расчетных пределов усилия предотвращают отказы, повышают безопасность и снижают эксплуатационные расходы. Реализация системы контроля нагрузки может увеличить срок службы лезвия до 50%.
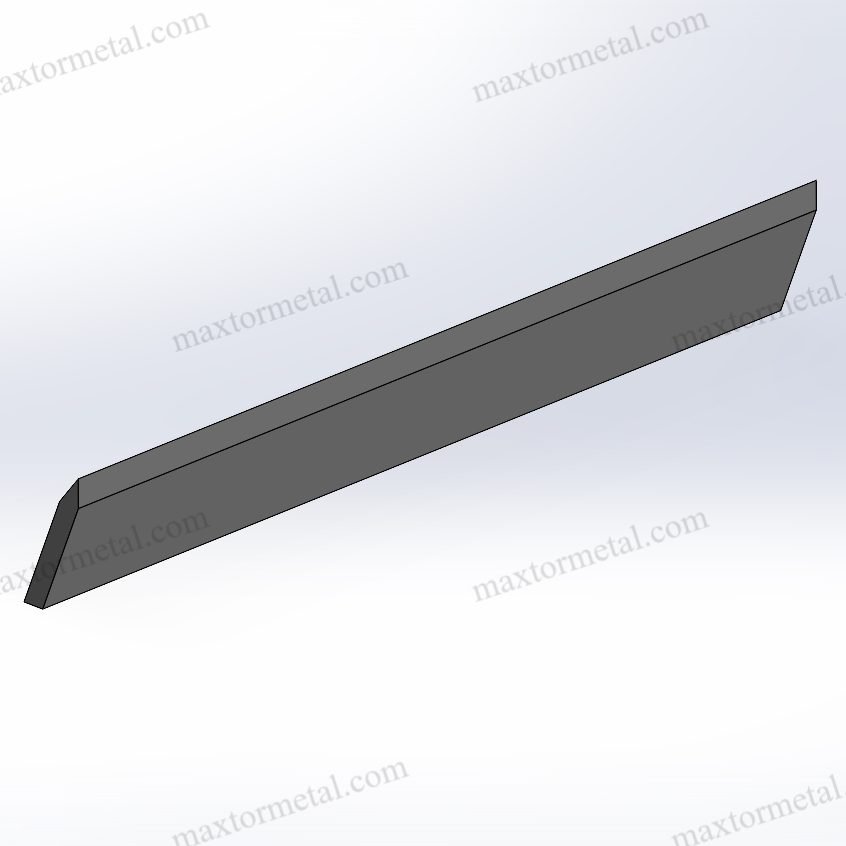
9. Обучайте сотрудников правилам обращения с лезвиями и технике безопасности: сокращение несчастных случаев и увеличение продолжительности жизни
Важность обучения обслуживанию лезвий
Правильная подготовка гарантирует безопасное обращение, оптимальное обслуживание и более длительный срок службы лезвий. В соответствии с исследование Управления по охране труда и промышленной гигиене (OSHA, 2023):
- 30% травм, связанных с порезами на рабочем месте результат от неправильное обращение с лезвием.
- Компании с официальными программами обучения работе с лезвиями отчет 50% меньше травм, связанных с лезвиями.
- Лезвия обрабатываются правильно последний 30–40% длиннее чем те, которые подвергаются плохому обращению.
Основные направления обучения работе с промышленными лезвиями
✅ Правильные методы заточки – Избегайте перегрева и неправильных углов заточки.
✅ Правильные методы очистки и хранения – Предотвращает ржавчину, загрязнение и потускнение.
✅ Протоколы безопасности – Обращайтесь с острыми краями, используйте защитные перчатки и правильно утилизируйте изношенные лезвия.
✅ Понимание пределов нагрузки – Обеспечивает использование лезвий в пределах номинального давления резки.
Статистика отрасли по влиянию обучения
Аспект обучения | Улучшение срока службы лезвия (%) | Сокращение травматизма на рабочем месте (%) |
Обучение обращению с лезвиями | 30% — более длительный срок службы | 50% меньше травм |
Правильные методы заточки | 40% более длительный срок службы | 20% меньше аварий |
Программы повышения осведомленности о безопасности | 20% более длительный срок службы | 30% меньше травм |
Пример из практики: сектор автомобилестроения
- А ведущий производитель автомобилей внедрил программу обучения по обслуживанию лезвий.
- Результат: Срок службы лезвия увеличен на 35%, в то время как уровень несчастных случаев снизился на 50%.
- Рентабельность инвестиций: Компания сэкономила $200,000 ежегодно на замену лезвий и расходы, связанные с травмами.
Контрольный список обучения для операторов промышленных лезвий
✅ Проводить ежемесячные семинары по техническому обслуживанию лезвий.
✅ Предоставьте письменные инструкции по правильному обращению с лезвиями..
✅ Внедрить программу сертификации сотрудников по технике безопасности при работе с лезвиями.
Обучение снижает количество несчастных случаев, продлевает срок службы лезвий и обеспечивает соблюдение правил безопасности. Инвестирование в структурированные программы обучения может сократить уровень травматизма вдвое пока увеличение срока службы инструмента на 30–40%.
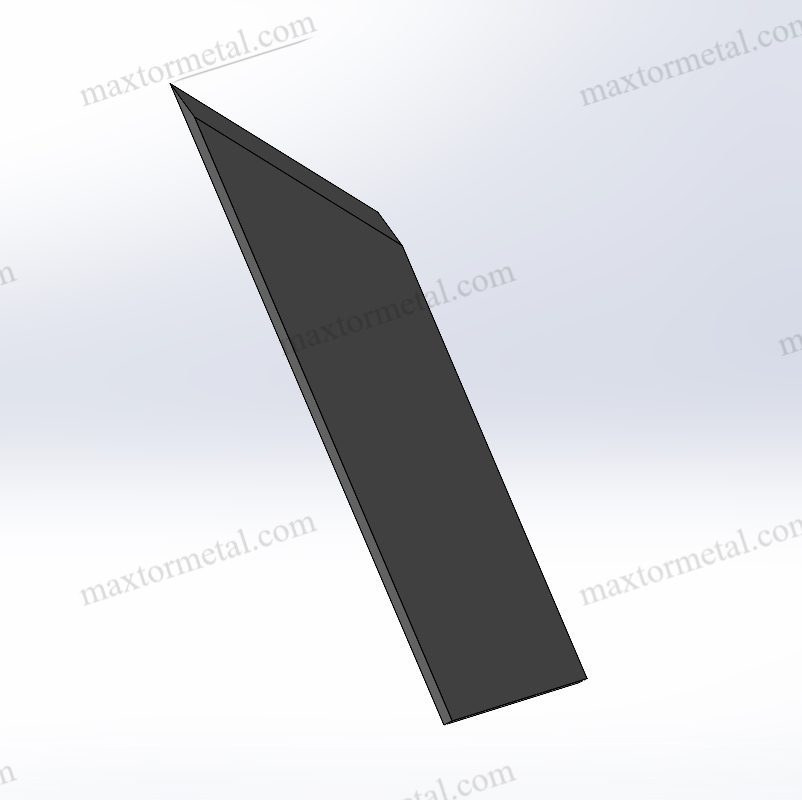
10. Часто задаваемые вопросы (FAQ)
Как часто следует затачивать промышленные лезвия?
Зависит от использования, но большинство требует заточки. каждые 50–100 часов.
Каков наилучший способ предотвращения ржавчины?
Применить тонкий слой машинного масла и хранить в сухая среда.
Можно ли затачивать промышленные ножи вручную?
Да, но ручная заточка требует точности чтобы избежать неровных краев и повреждения лезвия. Для высокоточной заточки, профессиональные услуги шлифования рекомендуются.
Каковы признаки того, что лезвие необходимо заменить?
Лезвие следует заменять до того, как оно полностью затупится, поскольку чрезмерный износ может привести к повреждению оборудования и материалов.
Когда следует заменять, а когда перетачивать?
✅ Переточите лезвие. если есть незначительные помутнения, но нет трещин и сколов.
✅ Заменить лезвие если имеются видимые сколы, трещины или сильный износ (потеря кромки >1 мм).
Совет от отрасли: Держите журнал для отслеживания использования лезвий и оцените интервалы замены на основе предыдущих моделей износа.
Какую смазку следует использовать для промышленных ножей?
Смазки на основе ПТФЭ для сильного нагрева, силиконовые масла для применения в пищевой промышленности, Масла на минеральной основе для резки бумаги и текстиля, а также Синтетические смазочные материалы для интенсивной резки.
Правильный техническое обслуживание промышленных лезвий продлевает срок службы инструмента, повышает безопасность и повышает эффективность. Следуя этим девять основных советов, вы можете максимально повысить производительность режущих инструментов, одновременно снижая эксплуатационные расходы.
В Нанкин Metal, Мы специализируемся на производстве высококачественных промышленных ножей и предоставляем экспертные рекомендации по обслуживанию и долговечности. Свяжитесь с нами сегодня для индивидуальные решения для лезвий!
2 ответа