Краткое содержание
Продольная резка лезвия являются незаменимыми инструментами в отраслях, где требуется точная резка, но износ может существенно повлиять на их производительность. В этом руководстве мы рассмотрим распространенные причины износа режущих лезвий, признаки, указывающие на необходимость ремонта, и лучшие практики обслуживания и восстановления этих важных инструментов. Понимание этих факторов может помочь предприятиям повысить производительность, сократить время простоя и снизить эксплуатационные расходы.
Введение
Продольные лезвия являются важнейшими компонентами в отраслях, где точная резка и разрезание материалов имеют важное значение. Эти лезвия, часто называемые режущими ножами или вращающимися режущими лезвиями, используются в различных производственных секторах, таких как обработка металла, производство бумаги, пластмасс и даже упаковка. Со временем эти лезвия изнашиваются, что может существенно повлиять на производительность и производительность. Способность определять причины этого износа, знать, когда следует ремонтировать или заменять лезвия, и правильно их обслуживать, может привести к значительной экономии средств и более плавной работе.
В этом подробном руководстве мы рассмотрим факторы, способствующие износу режущих лезвий, как ремонтировать поврежденные лезвия и лучшие методы обслуживания для продления срока их службы. Давайте углубимся.
Что такое Лезвия для резки и почему они важны
Продольные лезвия — это режущие инструменты, предназначенные для нарезки материалов на более мелкие, более управляемые куски. Эти лезвия бывают разных форм и размеров, обычно круглые или прямые, и созданы для удовлетворения особых требований к резке. Основная роль режущих лезвий — обеспечение плавных, чистых и точных разрезов, минимизация отходов и повышение общей эффективности производства.
Основные характеристики режущих лезвий
- Материал: Прорезные лезвия обычно изготавливаются из высококачественной стали или карбидных материалов, которые известны своей прочностью, износостойкостью и способностью выдерживать нагрузки непрерывной резки. Высокоуглеродистая сталь и карбид вольфрама являются распространенными материалами, используемыми для лезвий, которые режут прочные материалы.
- Дизайн: Продольные лезвия могут иметь различные формы. Круглые лезвия являются наиболее распространенными и используются в операциях ротационной продольной резки. Прямые лезвия часто используются для резки материалов по прямым линиям, обеспечивая больший контроль над резкой.
- Точность: Одной из важнейших характеристик режущих лезвий является их способность делать чистые разрезы с минимальным количеством заусенцев. Это снижает необходимость в дополнительных отделочных работах, которые могут быть трудоемкими и дорогостоящими.
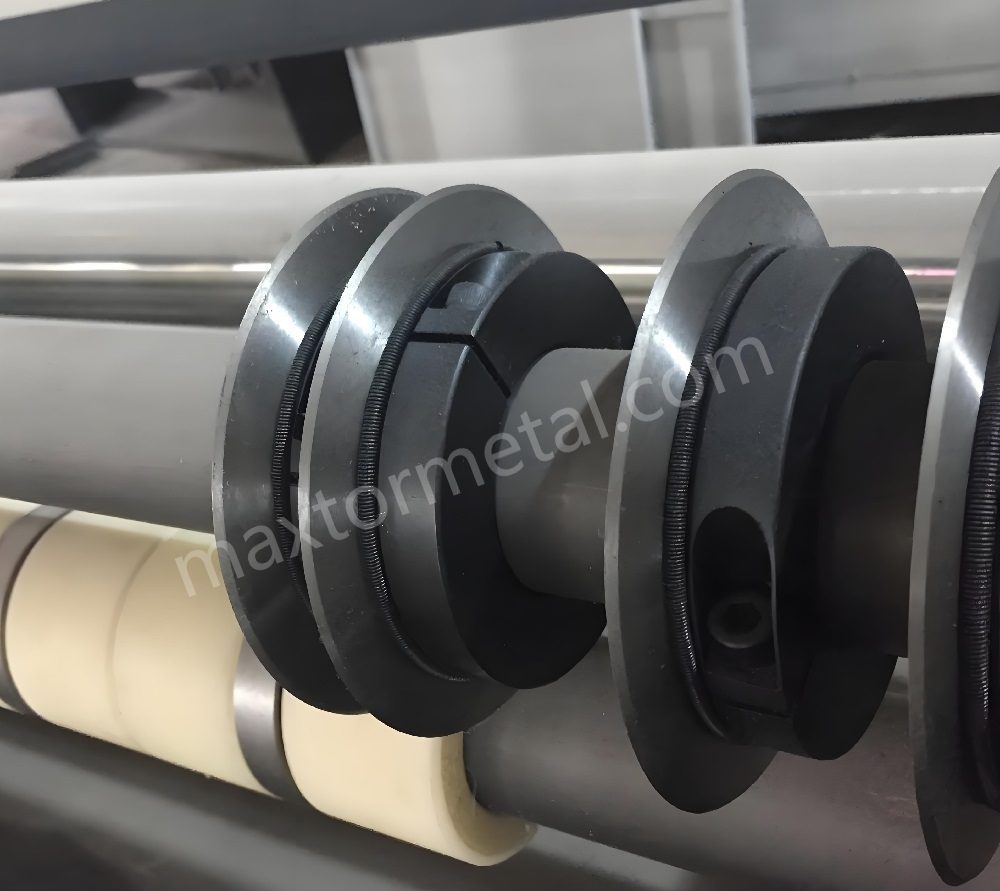
Почему они важны
Режущие лезвия напрямую влияют на эффективность производства и качество продукции. Вот как:
- Точная резка: Высококачественные режущие лезвия обеспечивают чистые разрезы, что значительно сокращает отходы материала. В таких отраслях, как производство бумаги и металла, минимизация отходов может привести к существенной экономии средств.
- Высокая эффективность: Острое и ухоженное лезвие может быстрее резать материалы, сокращая время производства и увеличивая общую производительность.
- Постоянная производительность: Постоянство производительности лезвий гарантирует, что качество конечного продукта остается высоким. Если лезвие начинает ухудшаться, это может привести к неровным разрезам, что может привести к дефектам продукта и недовольству клиентов.
Однако лезвия для резки не вечны. По мере износа лезвий они могут вызывать такие проблемы, как грубые разрезы, снижение скорости резки и увеличение простоев, что может привести к более высоким эксплуатационным расходам.
Распространенные причины Режущее лезвие Носить
Лезвия для резки со временем изнашиваются из-за нескольких факторов. Понимание основных причин износа лезвий является ключом к предотвращению ненужных повреждений и обеспечению эффективной работы лезвий в течение более длительного периода. Давайте рассмотрим основные факторы:
1. Механические проблемы
- Несоосность: Для оптимальной производительности режущие лезвия должны быть правильно выровнены в машине. Неправильное выравнивание может привести к неровным режущим кромкам, что приведет к более быстрому износу и снижению точности резки. Например, если лезвие не идеально выровнено с разрезаемым материалом, это может привести к неравномерному распределению давления, что ускорит износ и приведет к дефектам в конечном продукте.
- Чрезмерное давление: Если при резке применяется слишком большое усилие, лезвие может оказаться напряженным, что приведет к сколам и затуплению. Это часто является результатом перегрузки оборудования или неправильной регулировки давления резки.
- Неправильный зазор: Зазор между режущим лезвием и разрезаемым материалом должен быть точным. Если зазор слишком узкий или слишком широкий, это может вызвать чрезмерное трение, что приведет к повреждению и ускоренному износу лезвия.
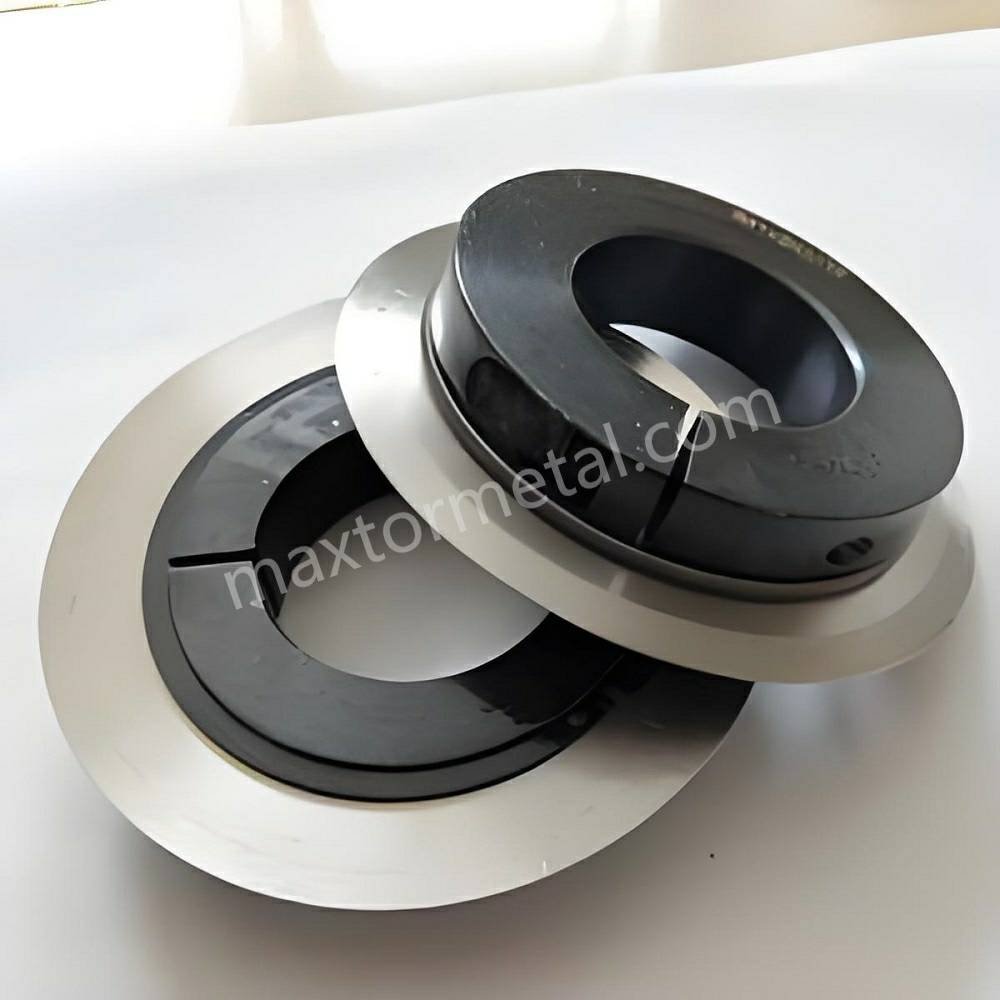
2. Материальные проблемы
- Абразивные материалы: Некоторые материалы, особенно с абразивными свойствами, изнашивают лезвия гораздо быстрее. Например, резка металлов с высокой твердостью или материалов с внедренным зерном может значительно сократить срок службы режущих лезвий. В таких случаях использование правильного материала лезвия, например, твердосплавных лезвий для твердых материалов, может смягчить чрезмерный износ.
- Несовместимость материалов: Не все режущие лезвия подходят для каждого типа материала. Использование лезвия, не предназначенного для определенного материала, может привести к более быстрому износу лезвия. Например, использование стандартного стального лезвия для резки высокоабразивных синтетических материалов приведет к сокращению срока службы.
3. Факторы окружающей среды
- Коррозия: Воздействие влаги, химикатов или других едких элементов может со временем ослабить режущие лезвия. Ржавчина или коррозия могут вызвать появление ямок на поверхности лезвия, что снижает его остроту и режущую способность. Эта проблема особенно распространена в средах с высокой влажностью или там, где разрезаемые материалы выделяют пыль или другие едкие частицы.
- Перегрев: Непрерывная работа без надлежащего охлаждения может привести к перегреву режущих лезвий. Возникающая в результате термическая усталость может привести к снижению твердости и производительности. Для предотвращения этого должны быть установлены надлежащие системы охлаждения, особенно при использовании лезвий в течение длительного времени.
Понимая эти общие причины, предприятия могут принять меры по предотвращению преждевременного износа и продлению срока службы своих режущих лезвий.
Признаки, указывающие на ваш Режущее лезвие Нужен ремонт
Знание того, когда режущее лезвие нуждается в ремонте, имеет решающее значение для предотвращения дальнейшего повреждения и поддержания эксплуатационной эффективности. Следующие признаки указывают на то, что пришло время осмотреть и, возможно, отремонтировать ваши лезвия:
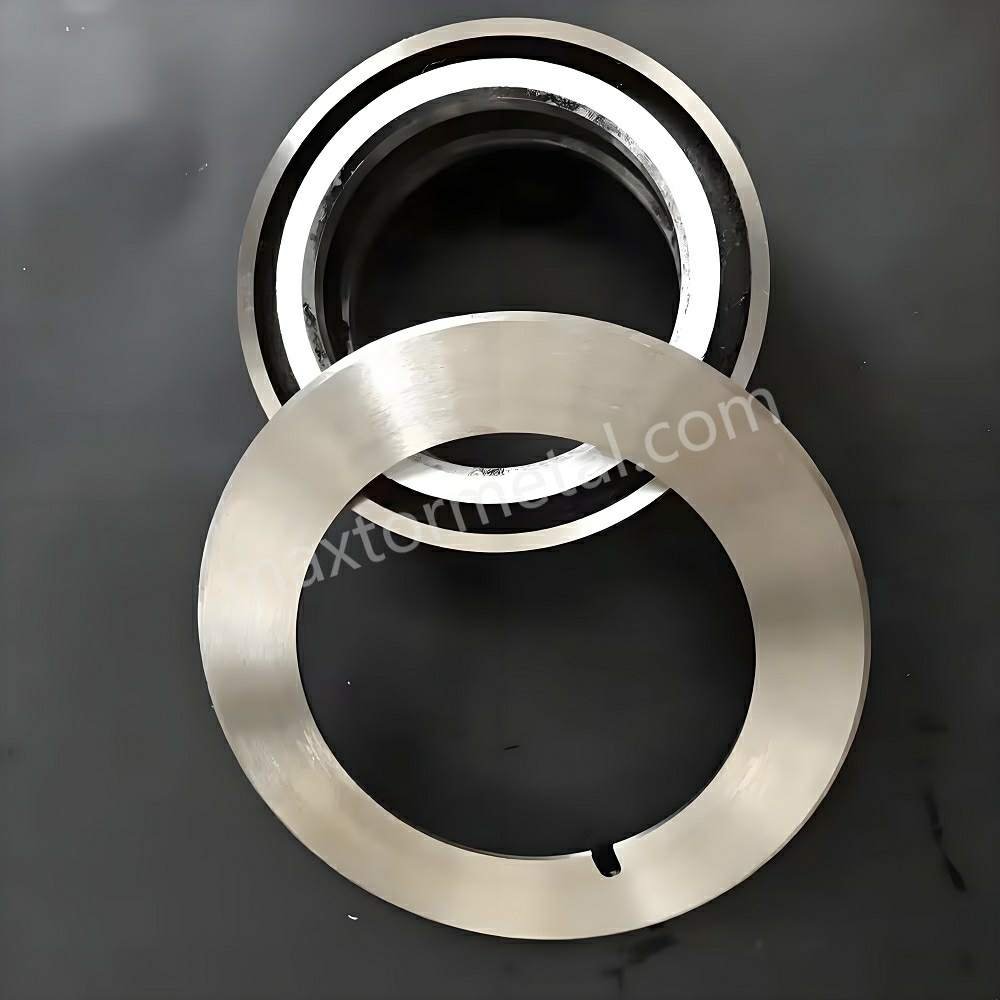
1. Проблемы с производительностью
- Снижение точности резки: Если режущее лезвие начало делать неровные или грубые разрезы, скорее всего, лезвие износилось. Это может привести к дефектам в конечном продукте и может потребовать больше времени на отделку, тем самым снижая общую производительность.
- Неровные края или заусенцы: Когда лезвие начинает изнашиваться, края часто становятся неровными, что приводит к появлению заусенцев на разрезаемом материале. Заусенцы могут увеличить потребность в постобработке и снизить общее качество конечного продукта.
2. Физический ущерб
- Видимые сколы и трещины: Если на поверхности лезвия заметны сколы или трещины, это признак того, что лезвие получило значительные повреждения. Эти дефекты могут ухудшить производительность и привести к более серьезным проблемам, если их не устранить.
- Тупые края: Со временем лезвия для резки теряют свою остроту. Если режущие кромки заметно затупились или имеют следы износа, пришло время заточки или замены.
3. Эксплуатационные проблемы
- Повышенная вибрация: Если вы заметили, что машина для продольной резки вибрирует больше обычного во время работы, это может быть вызвано изношенным или неровным режущим лезвием. Это может повлиять на качество резки и может указывать на то, что лезвие требует немедленного внимания.
- Необычные шумы: Необычные звуки, такие как скрежет или визг во время резки, могут быть признаком того, что лезвие не функционирует должным образом. Это может быть вызвано чрезмерным износом, несоосностью или загрязнением поверхности лезвия.
Раннее обнаружение этих признаков может предотвратить дорогостоящий ремонт и свести к минимуму простои, обеспечивая бесперебойную работу вашего предприятия.
Как эффективно ремонтировать и обслуживать режущие лезвия
Как только вы определили, что ваши режущие лезвия нуждаются в ремонте, крайне важно быстро решить проблемы, чтобы предотвратить дальнейшие повреждения и поддерживать оптимальную производительность. Ниже приведены основные шаги по ремонту и обслуживанию режущих лезвий:
Пошаговый процесс ремонта
- Осмотр и диагностика
Перед выполнением любого ремонта необходимо тщательно осмотреть лезвие на предмет износа, повреждения или несоосности. Ищите трещины, сколы или тупые края. На этом этапе важно определить, вызвана ли проблема неправильными методами эксплуатации, проблемами с материалами или факторами окружающей среды. - Методы заточки
Лезвия для резки часто тупятся из-за длительного использования. Чтобы восстановить их остроту, используйте заточные станки, которые затачивают лезвие под постоянным углом. Заточка гарантирует, что лезвие снова сможет делать чистые, точные разрезы. Обязательно используйте правильные методы заточки, чтобы сохранить геометрию лезвия, гарантируя, что оно не станет слишком тонким или неровным. - Замена поврежденных секций
В случае серьезного повреждения может потребоваться замена частей лезвия или даже всего лезвия. Например, если часть лезвия треснула и не подлежит ремонту, ее отрезание и замена восстановят функциональность.
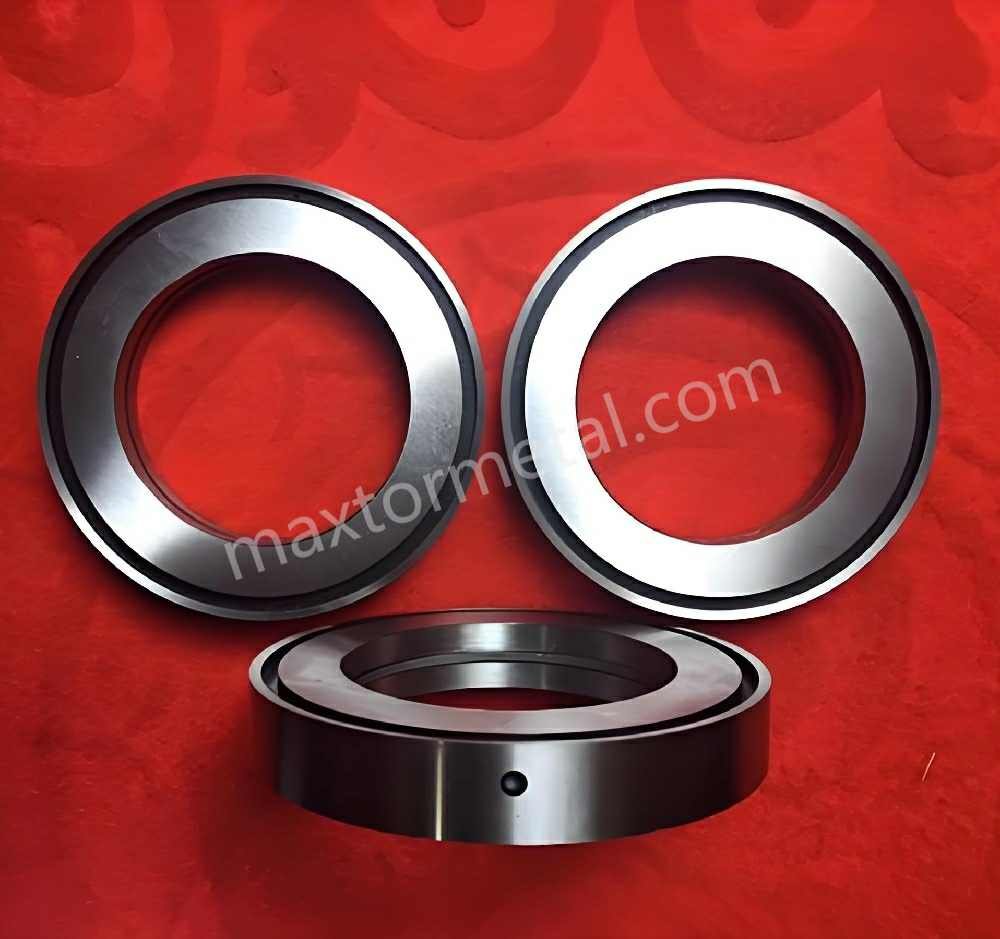
Советы по профилактическому обслуживанию
- Регулярные проверки
Внедрите регулярный график осмотров для контроля состояния лезвия. Раннее выявление износа может помочь сократить дорогостоящий ремонт и время простоя. - Правильная очистка и смазка
Очищайте лезвие после каждого использования, чтобы удалить мусор, пыль и загрязняющие вещества, которые могут ускорить износ. Наносите смазочные материалы, чтобы защитить лезвие от ржавчины и коррозии. - Обеспечьте правильное выравнивание
Регулярно проверяйте выравнивание режущего лезвия. Несоосность может привести к неравномерному износу, что снижает эффективность и долговечность лезвия.
Соблюдая эти правила обслуживания и ремонта, вы сможете поддерживать режущие лезвия в оптимальном состоянии в течение более длительного времени.
Когда следует рассмотреть замену лезвия вместо ремонта
В некоторых случаях замена режущего лезвия может быть более экономически выгодной, чем его ремонт. Вот когда следует рассмотреть замену:
Экономический анализ
- Стоимость ремонта по сравнению с заменой: Если стоимость ремонта лезвия превышает 50% стоимости нового, замена может быть более практичным вариантом.
- Серьёзный ущерб: Если лезвие получило значительные повреждения, которые невозможно эффективно отремонтировать, его замена может оказаться более экономичным решением в долгосрочной перспективе.
Соображения производительности
- Время простоя: Частые ремонты могут привести к длительному простою, что негативно сказывается на производительности. В таких случаях замена лезвия гарантирует, что операции могут быть возобновлены без задержки.
- Долгосрочная надежность: Новое лезвие для резки обеспечивает большую надежность и производительность по сравнению с отремонтированным. Если лезвие постоянно ломается, его замена устранит текущие проблемы и повысит общую эффективность.
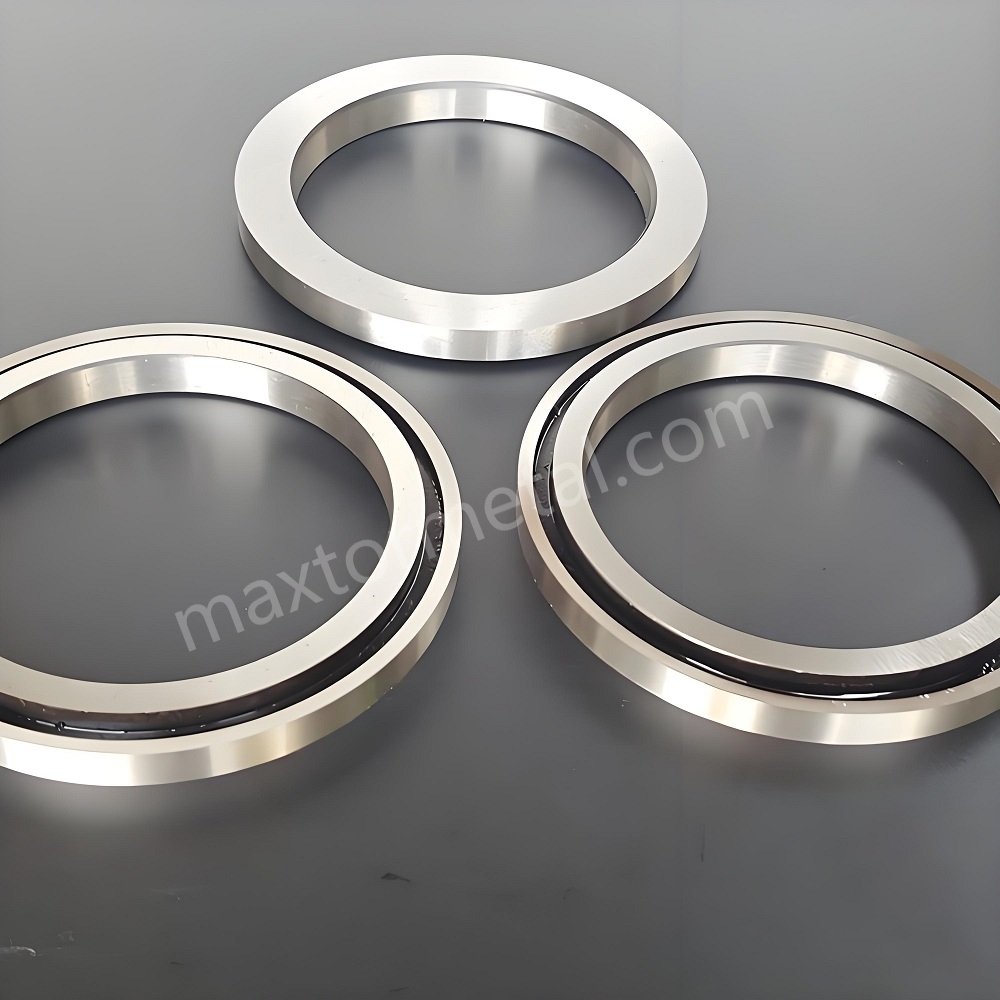
Как выбрать правильного поставщика услуг по ремонту режущих лезвий
Выбирая авторитетный и опытный поставщик услуг для ремонта лезвий для резки имеет важное значение для поддержания качества и долговечности ваших лезвий. При выборе поставщика учитывайте следующие факторы:
Ключевые факторы для оценки
- Опыт и экспертиза
Ищите поставщиков услуг с проверенной репутацией в ремонт режущего лезвия. Квалифицированный поставщик будет иметь необходимые инструменты и опыт для эффективного восстановления лезвий. - Время выполнения
Быстрое выполнение ремонта имеет решающее значение для избежания длительного простоя. Выберите поставщика услуг, который может быстро выполнить ремонт, чтобы ваши операции работали бесперебойно. - Настройка
Убедитесь, что поставщик предлагает индивидуальные решения, основанные на вашем конкретном типе лезвия и материале, который вы режете. Индивидуализация гарантирует, что ваши лезвия будут отремонтированы в соответствии с самыми высокими стандартами.
Заключение
Режущие лезвия незаменимы во многих отраслях, но для поддержания эффективности им требуется регулярное обслуживание и ремонт. Понимание причин износа, распознавание ранних признаков повреждения и соблюдение надлежащей процедуры ремонта и обслуживания может сэкономить вашему бизнесу значительное время и деньги. Независимо от того, выбираете ли вы ремонт или замену, принятие упреждающих мер по уходу за вашими режущими лезвиями обеспечит бесперебойную и эффективную работу.
Узнать больше
Для получения дополнительных советов по обслуживанию режущих лезвий и изучения решений по ремонту, Свяжитесь с нами сегодня. МЕТАЛЛ Команда экспертов готова оказать вам помощь в выборе лезвий для продольной резки.