Summary:
Precision in slitting machine blades is essential for achieving superior cutting performance across industries. This article delves into the importance of blade accuracy, its impact on cutting results, and practical solutions for selecting, maintaining, and optimizing these crucial tools.
Introduction
In today’s fast-paced industrial environment, precision is more than a buzzword—it’s a necessity. Slitting machine blades, essential tools in manufacturing, significantly impacts the efficiency and quality of production processes. From clean cuts to reduced material waste, the precision of these blades dictates the success of various industries.
Achieving flawless cuts, however, isn’t without its challenges. Factors like blade material, sharpness, and maintenance practices play pivotal roles in ensuring consistency. This article explores how precision influences cutting performance and offers insights into optimizing these critical tools for maximum efficiency.
Understanding Slitting Machine Blades
Slitting machine blades, commonly referred to as slitting knives or precision cutting tools, are specialized components designed to cut or slit materials with accuracy. They are indispensable in industries where clean, consistent cuts are non-negotiable.
Industries that rely on these tools include:
- Automotive: Precision blades cut materials like steel sheets to exact dimensions for engine components and structural elements. For example, cutting tolerances in this sector often range within ±0.02 mm.
- Electronics: In the production of microchips or printed circuit boards (PCBs), blades need to handle delicate materials with tolerances as small as 0.01 mm.
- Packaging: These tools ensure that packaging materials like plastic films and cardboard maintain consistent dimensions, enabling seamless assembly lines.
High-speed operations in these industries demand tools that combine sharpness, durability, and precision.
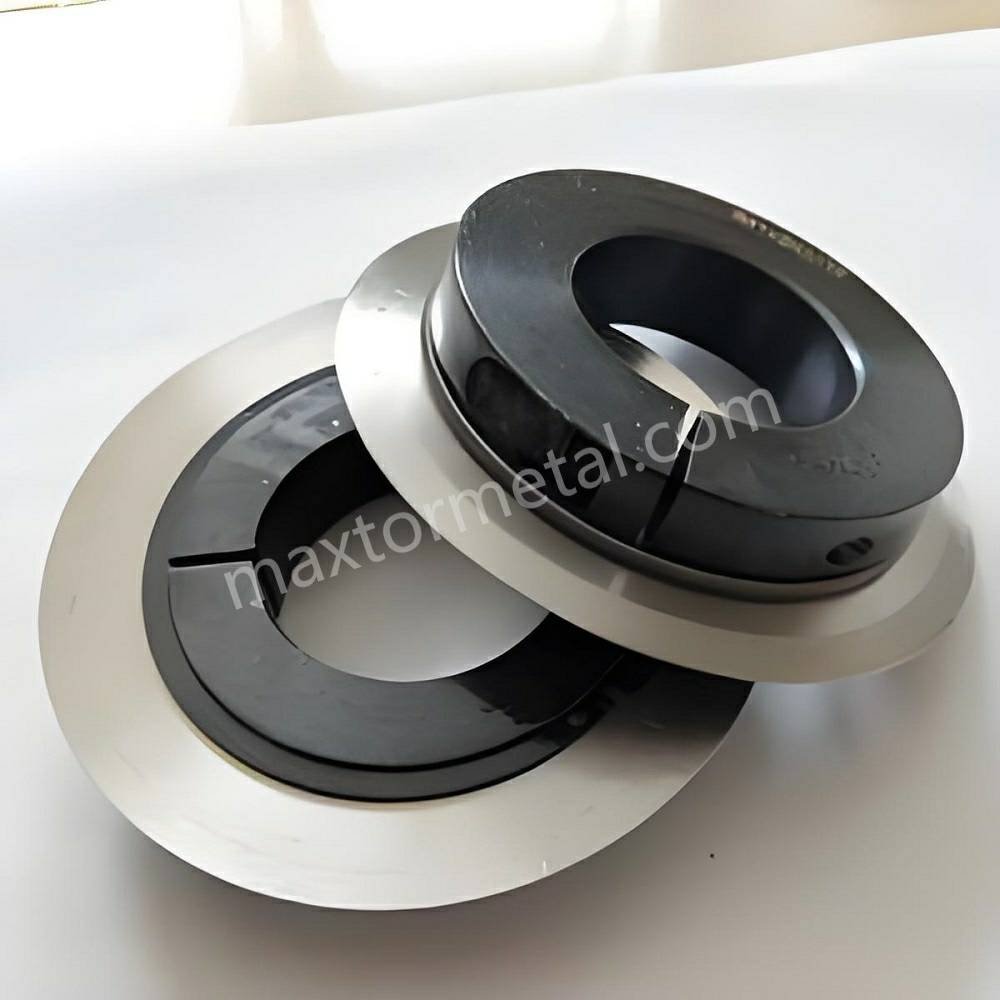
Precision in Slitting Blades: What It Means
Precision in slitting blades is about achieving consistent results with minimal variation. The concept includes three key factors:
- Dimensional Accuracy: Manufacturing with tolerances as tight as ±0.01 mm ensures that cuts are uniform. This is particularly important in electronics, where any deviation can lead to product failure.
- Sharpness: A razor-sharp blade reduces cutting force and ensures clean edges. Research shows that sharp blades improve operational efficiency by up to 25%.
- Material Quality: Durable materials like tungsten carbide allow for extended use without compromising precision.
Without these attributes, manufacturers face challenges like increased material waste and lower product quality.
The Science Behind Precision Cutting
Precision cutting is a balance of physics and engineering. Here’s how it works:
- Stress Distribution: Precision blades apply uniform pressure, minimizing the risk of cracking or deforming materials.
- Heat Management: High-quality blades reduce friction, limiting heat buildup that could warp materials or dull the blade.
- Material Interaction: Sharp blades make clean cuts, ensuring materials don’t bend, tear, or distort during the process.
In the electronics industry, where precise slits enable functional PCBs, even a minor error can result in product defects and expensive recalls.
How Blade Precision Impacts Cutting Results
The impact of precision on cutting performance cannot be overstated. Consider the following:
- Edge Quality: Precise blades eliminate burrs, producing smooth edges and reducing the need for costly secondary processing.
- Operational Speed: Sharp, accurate tools enable faster production cycles without compromising quality.
- Material Waste: Precision blades significantly reduce scrap rates, saving resources.
According to a study by Manufacturing Efficiency Journal, companies that upgraded to high-precision slitting tools saw a 20% reduction in material waste and a 15% improvement in production speed.
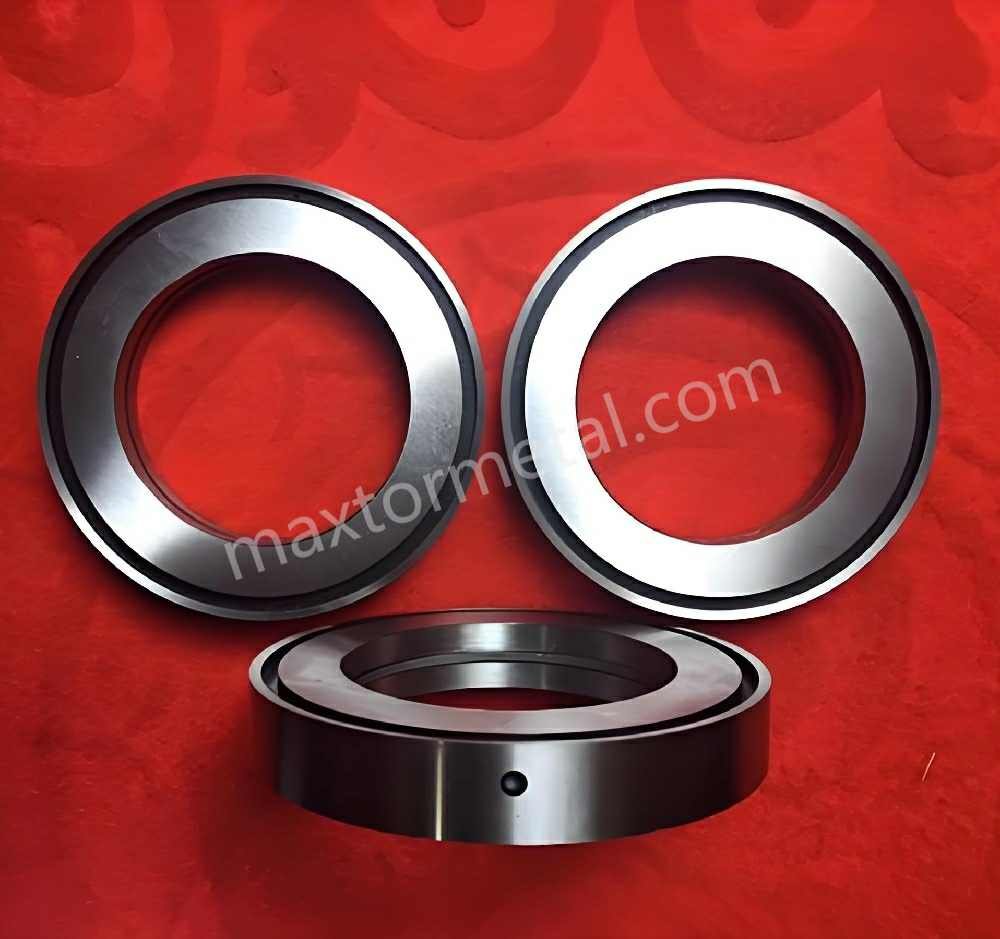
Real-World Applications: Industries that Demand Precision
Industries with strict quality standards rely heavily on slitting machine blades:
- Automotive: Cutting precision is vital for safety-critical parts like brake pads and engine components.
- Packaging: Clean cuts ensure that packaging lines run smoothly without jamming or misalignments.
- Electronics: High-precision tools prevent damage to sensitive components like wafers or flexible circuit boards.
Each industry has unique requirements, emphasizing the importance of selecting the right blade for the job.
Key Features of High-Precision Slitting Blades
Not all blades are created equal. High-precision blades stand out because they possess:
- Micro-Tolerances: These blades can cut with tolerances tighter than ±0.01 mm, ensuring uniformity in production.
- Specialized Coatings: Coatings like titanium nitride reduce wear and friction, extending the blade’s lifespan.
- Balanced Edges: Proper weight distribution prevents wobbling, maintaining consistent cuts.
Such features make these tools indispensable in high-volume manufacturing environments.
Factors Affecting Blade Precision
Several factors influence the precision of slitting machine blades:
- Manufacturing Processes: Advanced techniques like laser cutting and CNC machining ensure consistent sharpness and dimensions.
- Material Quality: High-grade alloys or tungsten carbide offer superior wear resistance and durability.
- Blade Design: Geometry, including edge angles and thickness, affects cutting efficiency and precision.
A report by Global Cutting Tools Insights notes that blades made with premium materials last up to 50% longer than standard counterparts.
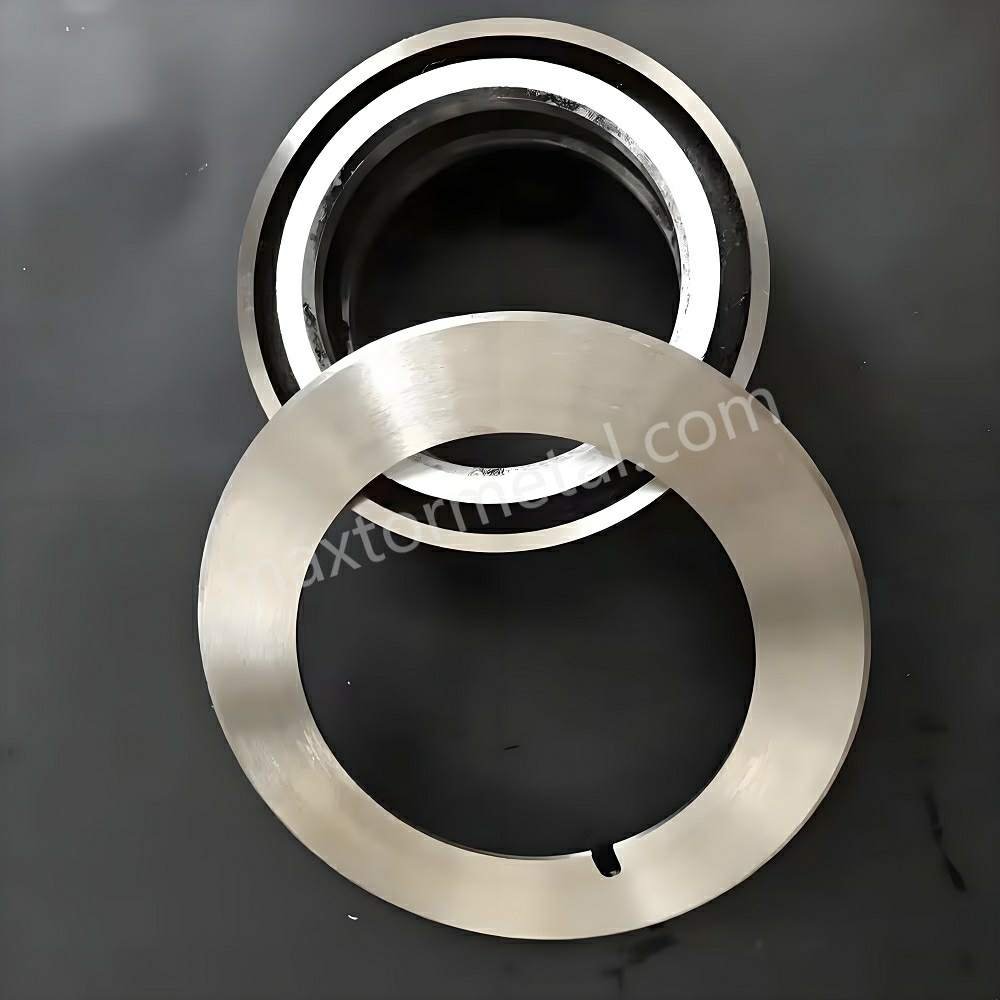
Why Blade Sharpness Matters
Blade sharpness is critical for achieving precision. Here’s why:
- Reduced Cutting Force: A sharp blade requires less effort, lowering strain on machinery and operators.
- Cleaner Cuts: Sharp tools produce smoother edges, reducing the need for post-processing.
- Extended Lifespan: Frequent sharpening keeps blades performing at peak levels, saving on replacements.
Manufacturers prioritizing sharpness report up to 30% fewer production interruptions.
The Role of Material Quality in Blade Precision
The material used in slitting machine blades directly impacts their durability and cutting ability. Common materials include:
- Tungsten Carbide: Known for its exceptional hardness and heat resistance, tungsten carbide is ideal for cutting metals and other tough materials.
- High-Speed Steel (HSS): More affordable than carbide, HSS is suitable for lower-intensity applications like cutting plastics.
For example, tungsten carbide blades typically last three times longer than HSS blades, providing a better return on investment despite their higher cost.
Common Cutting Challenges Solved by Precision Blades
Precision blades address many common manufacturing challenges:
- Burr Formation: Sharp edges eliminate unwanted burrs, producing smooth finishes.
- Uneven Cuts: High-precision blades ensure every cut matches exact specifications.
- Heat Damage: Friction-resistant coatings minimize heat buildup, protecting materials.
By solving these issues, precision tools improve efficiency and product quality.
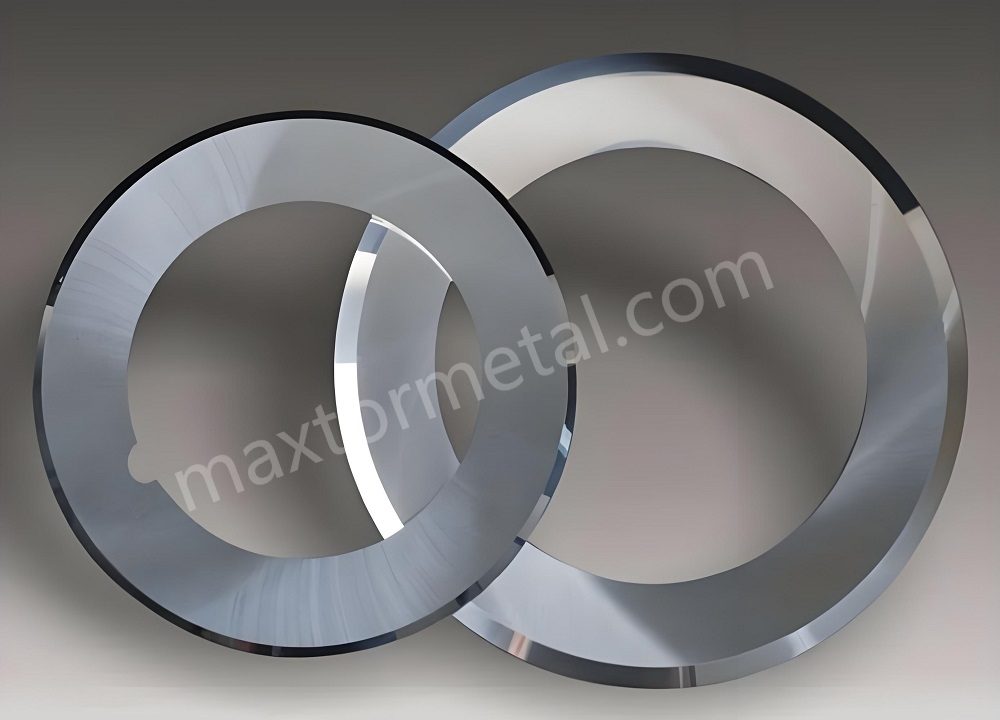
Economic Benefits of Using Precision Blades
Precision blades offer long-term financial benefits, including:
- Reduced Downtime: Durable, sharp tools require fewer replacements, minimizing interruptions.
- Lower Maintenance Costs: Quality materials reduce wear and tear on both blades and machinery.
- Material Savings: Precise cutting minimizes waste, optimizing resource use.
A 2023 survey by Cutting Edge Solutions found that companies using high-precision tools saved an average of $20,000 annually in material costs alone.
How to Choose the Right Slitting Machine Blade
Selecting the right blade involves careful consideration:
- Material Compatibility: Match the blade material to your application (e.g., carbide for metal, HSS for softer materials).
- Cutting Geometry: Choose edge angles based on the desired cut quality and speed.
- Coating Requirements: For high-speed operations, opt for blades with friction-resistant coatings.
Consulting an experienced supplier ensures you receive blades tailored to your specific needs.
Maintenance Practices to Preserve Blade Precision
Proper maintenance is essential for prolonging blade life and maintaining precision. Key practices include:
- Cleaning: Remove debris and residue after each use.
- Sharpening: Use professional tools to maintain a consistent edge.
- Storage: Store blades in a dry, secure location to prevent damage.
Regular maintenance can extend blade life by up to 40%, according to industry experts.
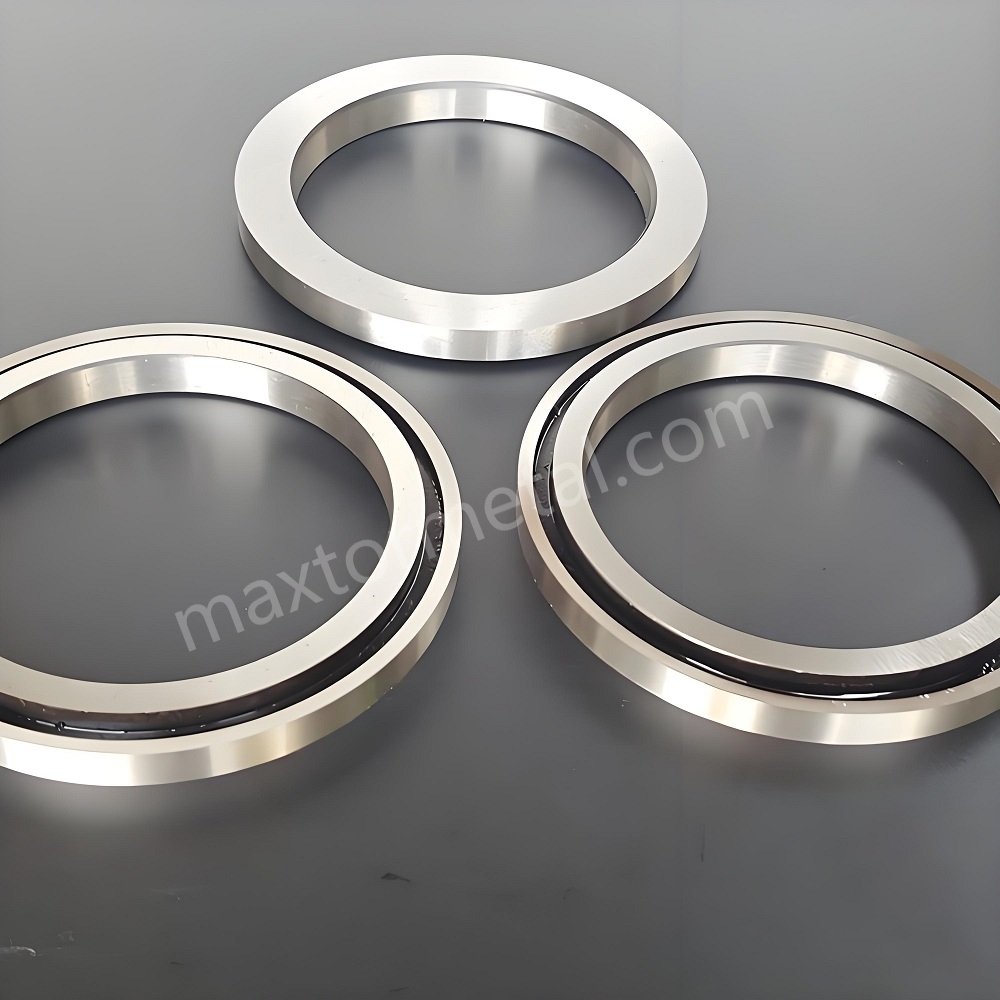
Innovations in Blade Manufacturing
Recent advancements in blade technology include:
- Laser-Cut Edges: Provide unmatched precision and sharpness.
- Cryogenic Treatments: Enhance blade hardness, reducing wear over time.
- Nanotech Coatings: Self-healing properties improve longevity and efficiency.
These innovations promise to revolutionize cutting performance across industries.
Future Trends in Slitting Machine Blades
Looking ahead, trends include:
- AI-Driven Adjustments: Automating blade alignment for consistent accuracy.
- Eco-Friendly Materials: Developing recyclable blades to reduce environmental impact.
- Hybrid Designs: Combining materials for optimal strength and flexibility.
Staying informed about these advancements ensures your business remains competitive.
FAQs
1. What industries benefit most from slitting machine blades?
Industries like automotive, electronics, and packaging depend on these tools for precision cutting.
2. How often should I replace slitting machine blades?
Replacement depends on usage and maintenance, but high-quality blades last significantly longer.
3. What’s the best material for slitting blades?
Tungsten carbide is ideal for heavy-duty tasks, while HSS is suitable for less demanding applications.
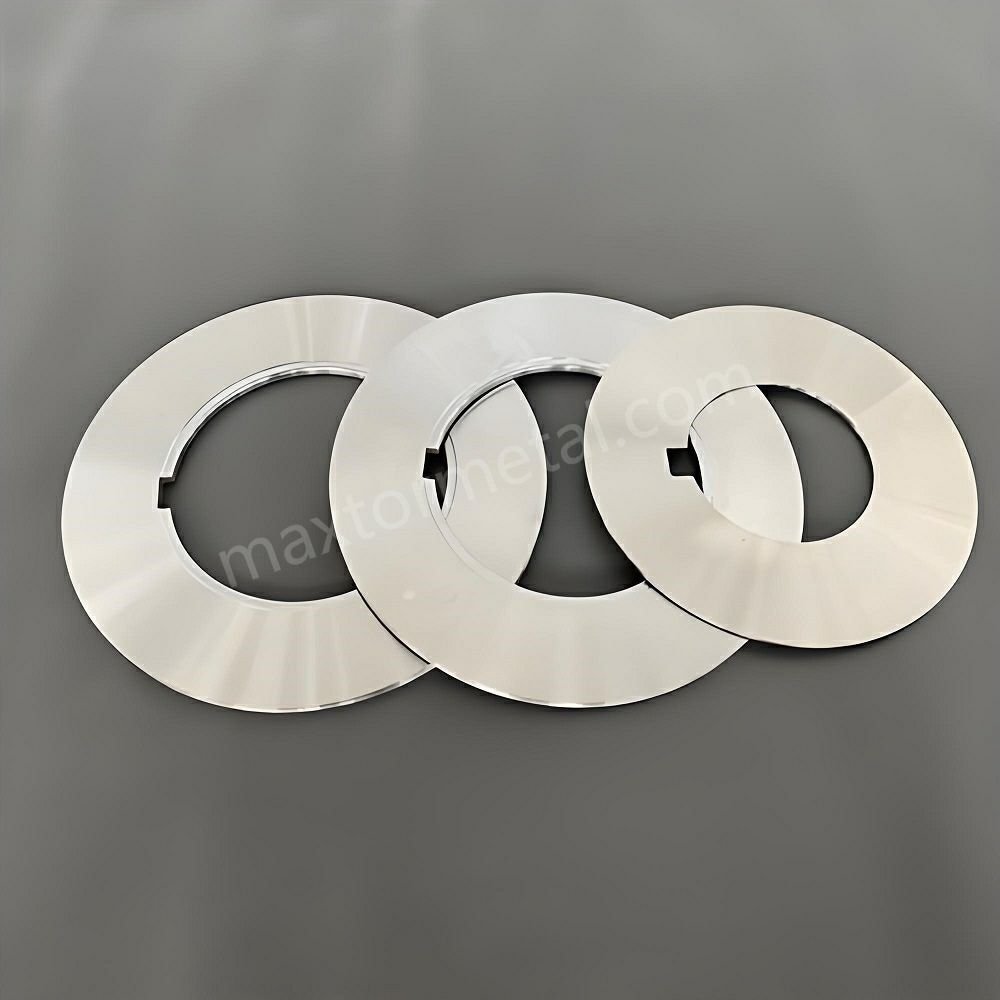
4. How can I maintain blade precision?
Regular cleaning, sharpening, and proper storage are essential for preserving blade performance.
5. Do precision blades reduce costs?
Yes, they minimize material waste, reduce downtime, and lower maintenance expenses.
Conclusion
Precision in slitting machine blades is a critical factor for achieving efficient, high-quality cutting. By understanding the importance of blade accuracy, investing in advanced tools, and implementing proper maintenance, businesses can optimize their operations and reduce costs.
Contact us todayto explore METAL’s precision cutting solutions and find the perfect blade for your needs!