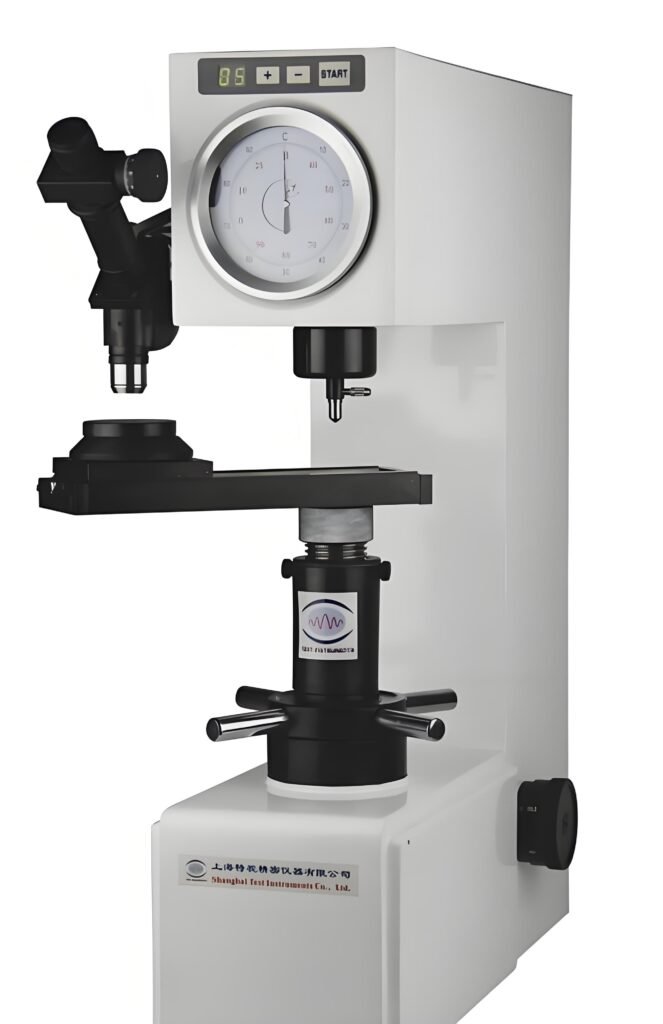
When selecting the right cutting solutions for industrial applications, businesses face a multitude of decisions. One of the most crucial factors to consider is the hardness and toughness of industrial blades. These two properties determine the blade’s performance, durability, and ability to withstand stress in various cutting environments. In this article, we will explore the relationship between hardness and toughness, their significance, and how they affect cutting solutions. We’ll also delve into the factors influencing these properties, the testing methods used to assess them, and provide practical examples to help guide your decision-making.
1. What is Blade Hardness?
độ cứng is a material’s ability to resist indentation, scratching, and abrasion. In industrial blades, hardness plays a critical role in determining how well the blade retains its sharpness and resists wear during prolonged use. Harder blades tend to maintain a sharp edge for longer, providing precise cuts and maximizing performance in demanding applications. However, there is often a trade-off: a blade that is extremely hard can be more brittle, making it more susceptible to cracking under stress.
Advantages and Disadvantages of High Hardness
High hardness comes with distinct advantages and drawbacks:
Thuận lợi:
- Hao mòn điện trở: Harder materials are more resistant to abrasion, meaning the blade will maintain its sharpness over a longer period.
- Cắt chính xác: Harder blades maintain fine, sharp edges, making them perfect for applications requiring high levels of precision.
Disadvantages:
- Độ giòn: While a hard blade will resist wear, it may be more prone to cracking under stress, especially if subjected to sudden force.
- Chipping: A hard blade may be more likely to chip, particularly when cutting through tough or irregular materials.
Common Hardness Testing Methods
To accurately assess the hardness of industrial blades, several testing methods are employed, including:
- Rockwell Hardness Test: This is the most common test used to measure the hardness of materials. It involves applying a diamond cone or steel ball to the material’s surface and measuring the depth of indentation. It’s widely used for blades made from materials like high-speed steel.
- Vickers Hardness Test: Ideal for testing harder materials or for microhardness measurements, this test uses a diamond pyramid indenter and is often used for carbide blades.
- Brinell Hardness Test: This test is frequently used on materials with coarse or uneven surfaces. A steel or carbide ball is pressed into the surface, and the diameter of the indentation is measured.
- Knoop Hardness Test: The Knoop test is most suitable for very thin or delicate materials. It uses an elongated diamond pyramid to measure microhardness in very small areas.
Blade Material Examples and Recommended Hardness Tests:
Vật liệu | Recommended Test | Hardness Range |
Thép tốc độ cao | Rockwell | 60-65HRC |
cacbua | Vickers or Knoop | 75-85 HRA |
Thép công cụ | Rockwell or Brinell | 50-62 HRC |
Want to learn more about how hardness can affect your cutting solutions? Continue reading below.
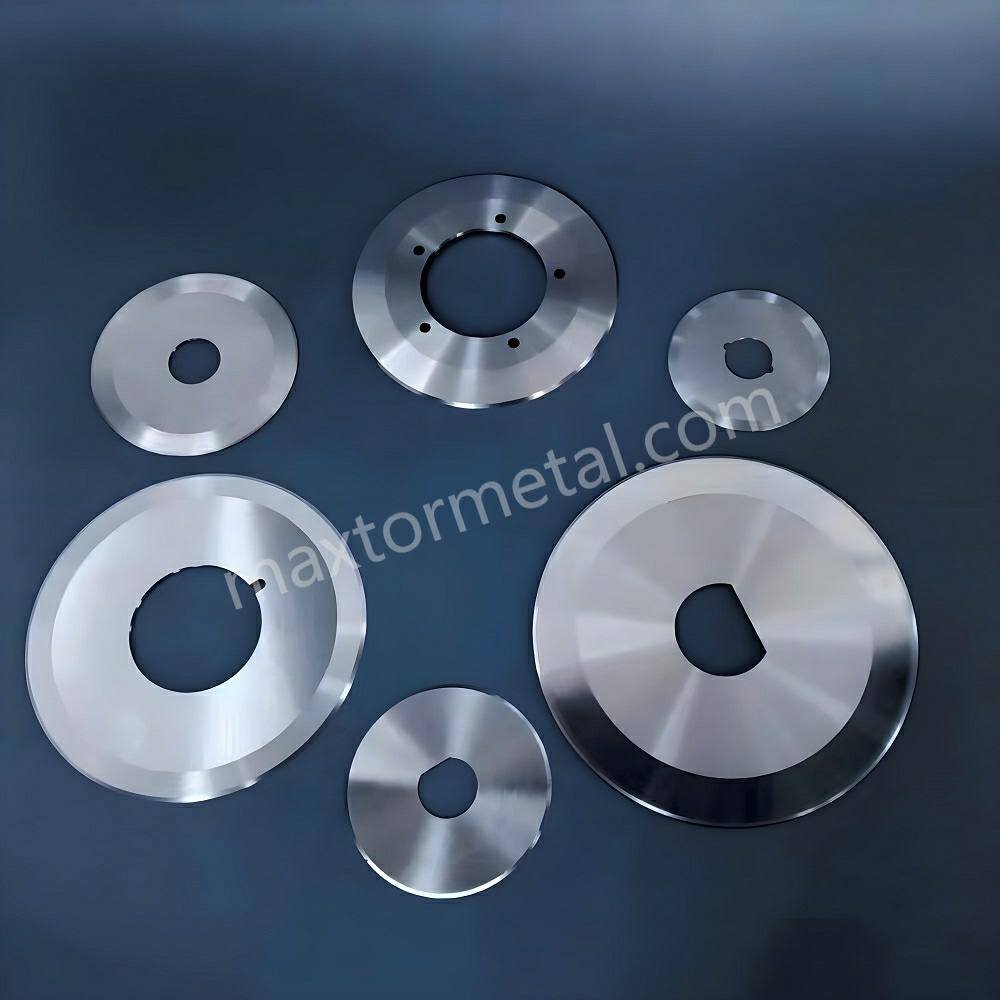
2. What is Blade Toughness?
While hardness is essential for wear resistance and precision, toughness is just as important for ensuring that blades can withstand stress and impact without breaking. Toughness refers to a material’s ability to absorb energy and endure high-stress situations. In industrial blades, toughness prevents breakage during sudden impacts or while cutting tough, dense materials.
Forms of Toughness in Industrial Blades
Toughness manifests primarily in two ways:
- Impact Resistance: This is the ability of the blade to withstand high-force impacts without cracking or breaking. Blades used in construction or heavy machinery need to endure shocks from hard materials without damage.
- Energy Absorption: The blade’s ability to absorb and dissipate energy while cutting or striking dense materials. This is essential for blades exposed to sudden, high-energy forces.
Importance of Toughness Across Industries
Toughness is especially vital in industries where blades are subjected to intense forces, including:
- Construction: Blades in this field often deal with high-impact forces, such as cutting through concrete, metal, or dense materials.
- Forestry: Blades need to withstand heavy impacts while cutting through wood, which can be dense and fibrous.
- Heavy Machinery: Blades used in industrial machines face continuous exposure to high-stress conditions, requiring both toughness and wear resistance.
Common Toughness Testing Methods
Two key testing methods are used to assess toughness:
- Tensile Testing: This test measures how much a material can stretch before it breaks, which is particularly useful for assessing the ductility of the material. Tensile testing is commonly used to assess blades made from materials like stainless steel or spring steel.
- Impact Testing (Charpy/Izod): These tests measure the energy a material can absorb during a high-velocity impact. It’s essential for assessing the toughness of blades exposed to sudden shocks or impacts.
Blade Material Examples and Recommended Toughness Tests:
Vật liệu | Recommended Test | Toughness Characteristics |
Spring Steel | Impact Test (Charpy) | Excellent impact resistance, ideal for tough cutting jobs |
Thép không gỉ | Tensile Test | Good toughness, well-balanced for both strength and flexibility |
Tempered Tool Steel | Both Tensile and Impact | Combines toughness with excellent wear resistance |
Spring steel, known for its high toughness, is well-suited for impact testing. On the other hand, stainless steel, with its balance between toughness and corrosion resistance, is best tested for tensile strength.
Curious about how toughness influences your cutting solutions? Let’s explore further.
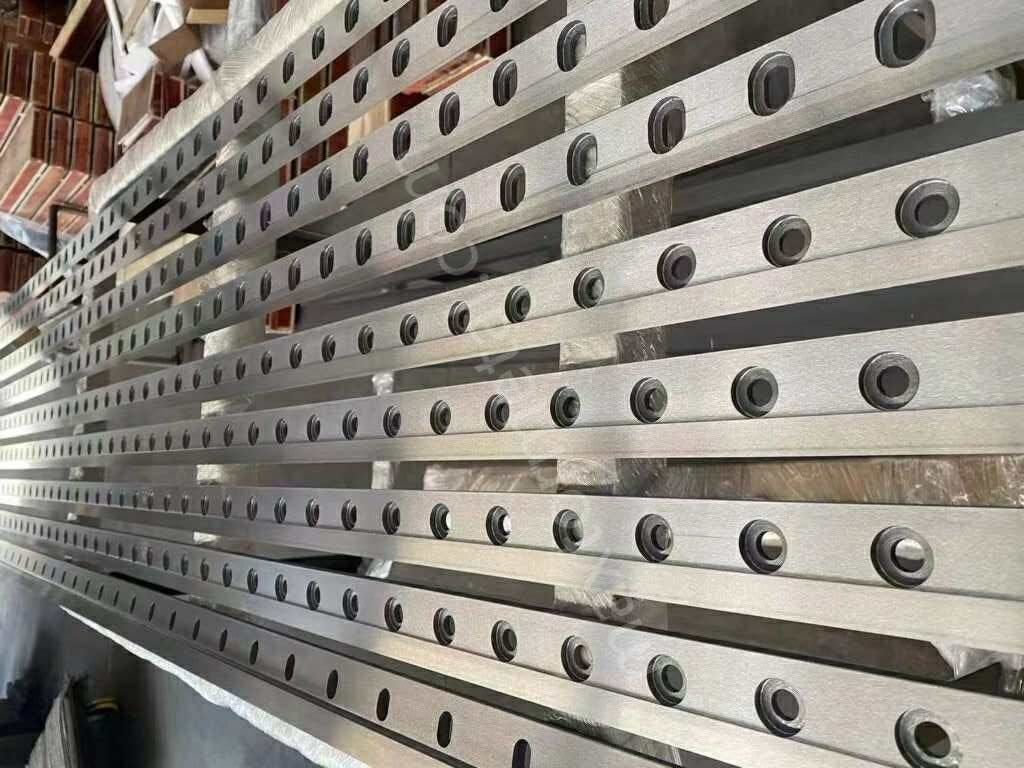
3. The Balance Between Hardness and Toughness
Striking the right balance between hardness and toughness is crucial to achieving optimal blade performance. While hardness enhances wear resistance and sharpness, too much hardness can make the blade brittle, leading to fractures under stress. On the other hand, while a tough blade can absorb impacts well, it might not hold a sharp edge as long as a harder blade.
Real-World Examples of Balanced Blade Performance
Different cutting applications require a careful balance of both properties:
- Precision Blades for Metal Cutting: These need to be both hard enough to resist wear and tough enough to endure impact. For example, thép tốc độ cao blades are often selected for metal cutting due to their excellent hardness and moderate toughness.
- Woodworking Blades: Blades in woodworking need to be especially tough to endure the impacts from cutting through dense or fibrous wood. These blades typically have a higher toughness rating but may not be as hard as those used for metal cutting.
Need help selecting the right combination of hardness and toughness for your cutting solutions? Contact our experts today for tailored recommendations.
4. Factors Influencing Blade Hardness and Toughness
Several factors influence how blades perform in terms of hardness and toughness. These include the material composition, heat treatment processes, and blade design.
4.1 Material Composition
The materials used in blade manufacturing determine both hardness and toughness. Blades made from high-carbon steel, for example, tend to be harder but less tough. On the other hand, materials like stainless steel offer a good balance between these properties.
4.2 Heat Treatment Processes
Heat treatments like quenching (rapid cooling), tempering (controlled heating), and annealing (gradual cooling) help adjust both hardness and toughness. Each process can enhance a blade’s performance in different ways.
4.3 Blade Design and Geometry
The thickness, edge geometry, and overall design of a blade also influence its performance. Blades with thicker profiles tend to be tougher but may not hold their sharpness as well. Conversely, thinner blades can achieve higher hardness but are more prone to breaking.
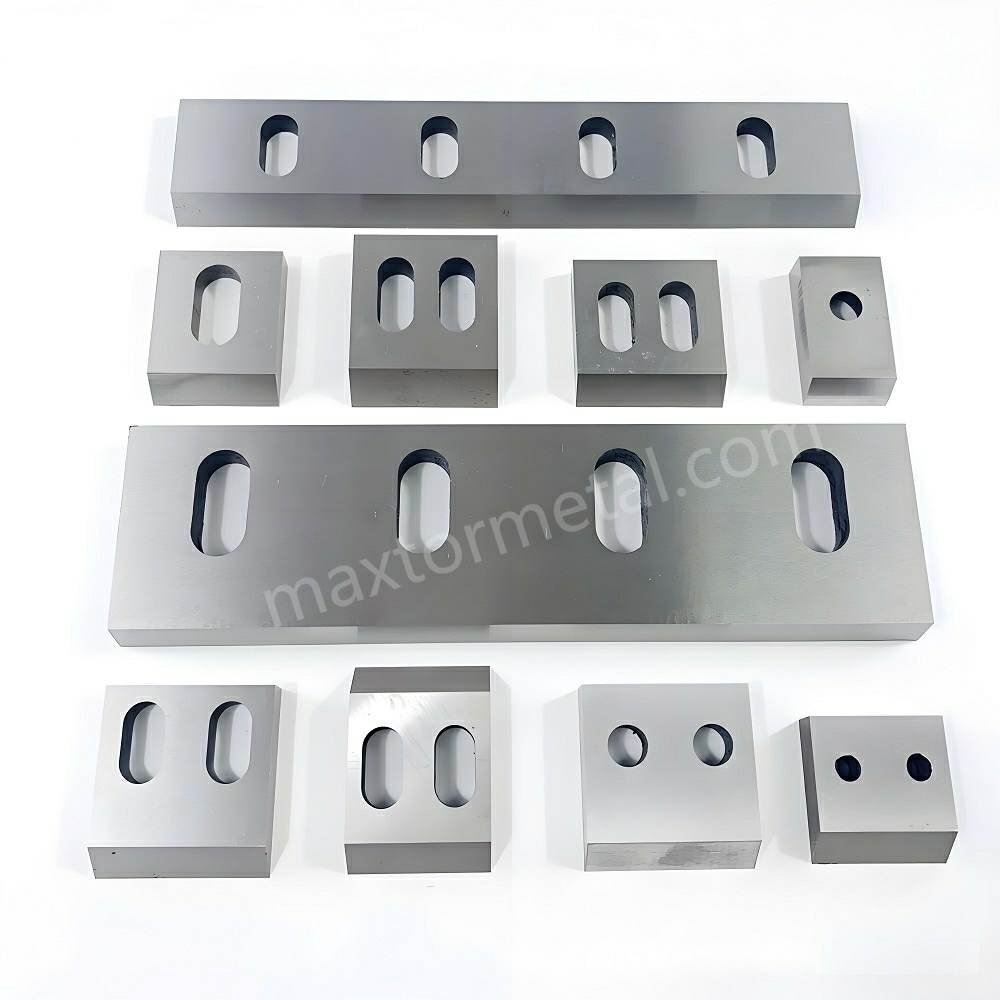
5. Selecting the Right Blade for Your Needs
Choosing the right blade for your application depends on understanding the specific requirements of your industry. Whether you need high wear resistance or superior toughness, it’s essential to assess both properties before making a decision.
5.1 Assessing Your Industry Requirements
Different industries have unique cutting needs, and understanding those requirements will guide you in selecting the right blade. For instance, blades used in food processing require a balance of sharpness and corrosion resistance, while blades in construction focus more on toughness.
5.2 Testing and Certification Standards
Certification ensures that your blades meet industry standards for both hardness and toughness. Always work with suppliers who offer blades that meet these certifications for reliable performance.
5.3 Working with Reliable Suppliers
Reliable suppliers can provide expert advice and tailored cutting solutions for your needs. By working with the right partner, you can ensure that your blades deliver consistent performance.
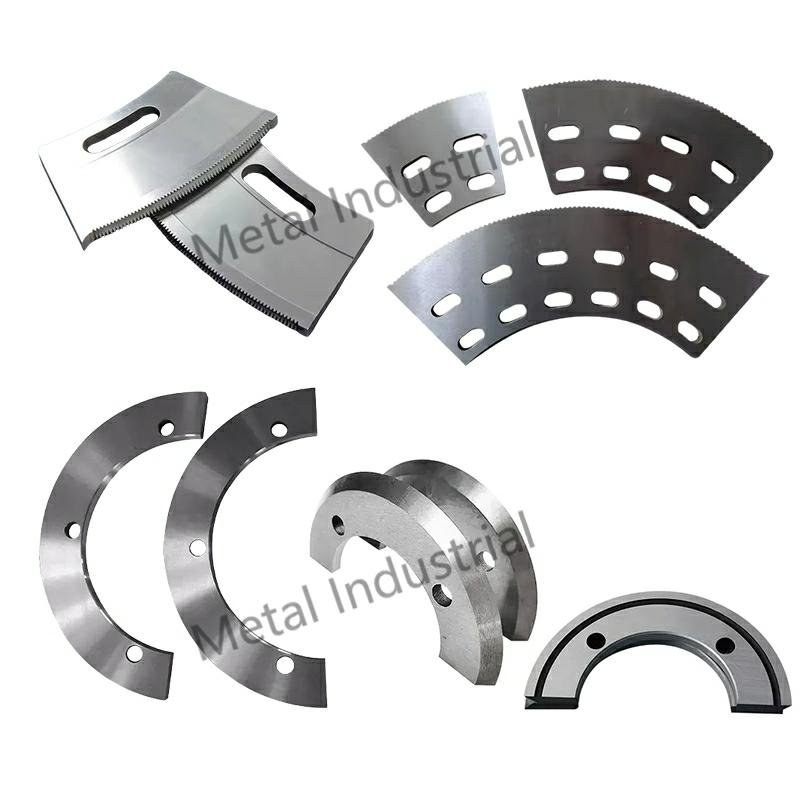
6. Solutions for Common Blade Performance Issues
Blades can face wear, chipping, or breakage over time. Here’s how you can address these issues:
- Premature Wear: Use harder materials and maintain sharpness through regular sharpening.
- Breakage or Chipping: Select tougher materials or adjust the blade design for more impact resistance.
7. Making Informed Decisions for Optimal Blade Performance
When choosing industrial blades for your cutting solutions, understanding the relationship between hardness Và toughness is vital. By considering the specific needs of your application—whether it’s precision cutting, high-impact resistance, or wear resistance—you can select the ideal blade material and design to optimize performance.
As hardness ensures a sharp edge that resists wear and maintains precision, toughness guarantees that the blade can handle impacts and continue cutting without fracturing. The right balance between these two properties will allow your blades to perform optimally, reducing downtime and ensuring longer-lasting results.
Want to learn more or find the perfect cutting solutions for your application? Liên hệ chúng tôi today for expert guidance and high-quality blades.