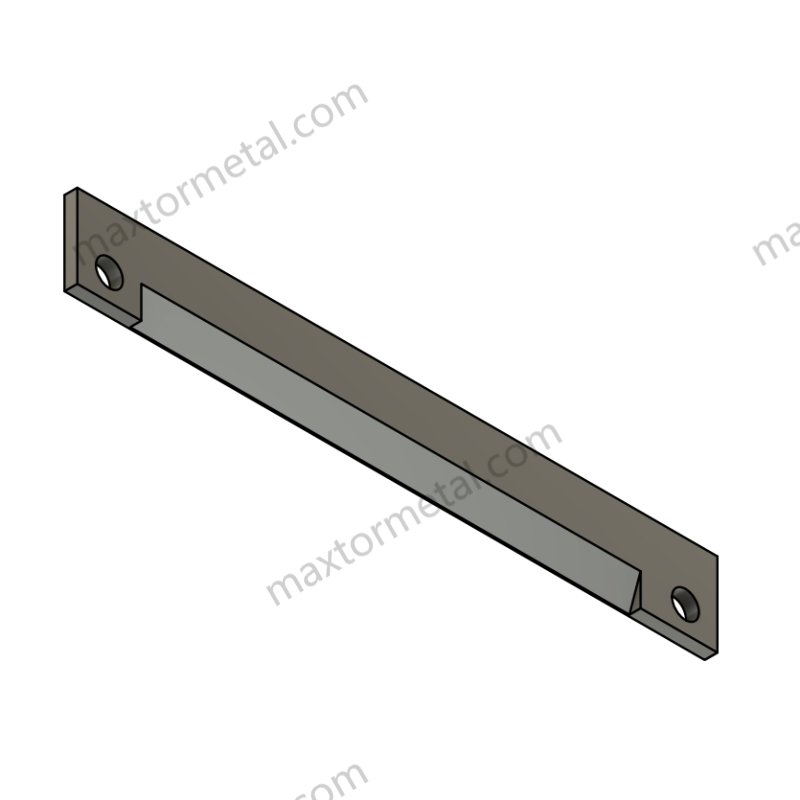
في عالم تصنيع السكاكين الصناعية، كل تفصيل مهم. من بين العمليات العديدة التي تحدد جودة النصل، المعالجة الحرارية تُعتبر هذه الخطوة بالغة الأهمية. فهذه العملية التحويلية لا تُحدد أداء سكاكين الآلات فحسب، بل تُحدد أيضًا متانتها وصلابتها ومقاومتها للتآكل.
على سبيل المثال، أظهرت الدراسات أن المعالجة الحرارية المناسبة يمكن أن تُحسّن صلابة النصل بأكثر من 40%، مع إطالة عمره الافتراضي بمقدار 50% أو أكثر. تُبرز هذه النتائج أن المعالجة الحرارية ليست مجرد إجراء تقني، بل هي حجر الأساس في تصنيع شفرات استثنائية. في هذه المقالة، سنستكشف عملية المعالجة الحرارية لسكاكين الآلات بالتفصيل، مُسلّطين الضوء على أهميتها، وأساليبها، وتحدياتها، وابتكاراتها.
ما هي المعالجة الحرارية؟
المعالجة الحرارية عملية هندسية دقيقة لتسخين وتبريد المعادن في ظروف مُتحكم بها لتعديل خصائصها الفيزيائية والميكانيكية مع الحفاظ على شكلها الخارجي. تُعد هذه الخطوة التحويلية أساسية في تصنيع السكاكين الصناعية، إذ تُصمم بنية الشفرة لتلبية متطلبات الأداء المحددة.
كيف تعمل المعالجة الحرارية
تكمن فعالية المعالجة الحرارية في قدرتها على التحكم بالبنية الدقيقة للمعدن، والتي بدورها تتحكم في خصائصه العامة. ومن خلال تغيير ترتيب الذرات داخل المادة، يمكن للمصنعين تحقيق النتائج التالية:
- زيادة الصلابة:
- تُنتج المعالجة الحرارية سطحًا خارجيًا أكثر صلابة، مما يُمكّن شفرات الماكينة من الحفاظ على حدتها لفترة أطول. على سبيل المثال، تُشير الأبحاث إلى أن التبريد يزيد من صلابتها بما يصل إلى 50% مقارنةً بالفولاذ غير المعالج، مما يُحسّن كفاءة القطع بشكل كبير.
- وهذا مفيد بشكل خاص للشفرات المستخدمة في التطبيقات ذات التأثير العالي، مثل التقطيع أو التقطيع بالمقصلة.
- هشاشة منخفضة:
- تُعوّض عملياتٌ مثل التصلب الهشاشة الناتجة عن التصليد. والنتيجة مزيجٌ أكثر توازناً بين الصلابة والمرونة، مما يسمح للشفرة بتحمّل الضغوط الديناميكية دون تكسّر.
- ليونة محسنة:
- بفضل تحسين بنية الحبيبات عبر دورات تسخين مُتحكم بها، تصبح الشفرة أكثر مرونة. تضمن هذه الخاصية انحناء الشفرة قليلاً تحت الضغط بدلاً من الانكسار، وهو أمر بالغ الأهمية للسلامة والمتانة.
- إزالة الشوائب:
- أثناء عملية التلدين، يتم تقليل الشوائب غير المرغوب فيها والضغوط الداخلية، مما يؤدي إلى إنشاء هيكل موحد وموثوق به يعمل بشكل يمكن التنبؤ به تحت الحمل.
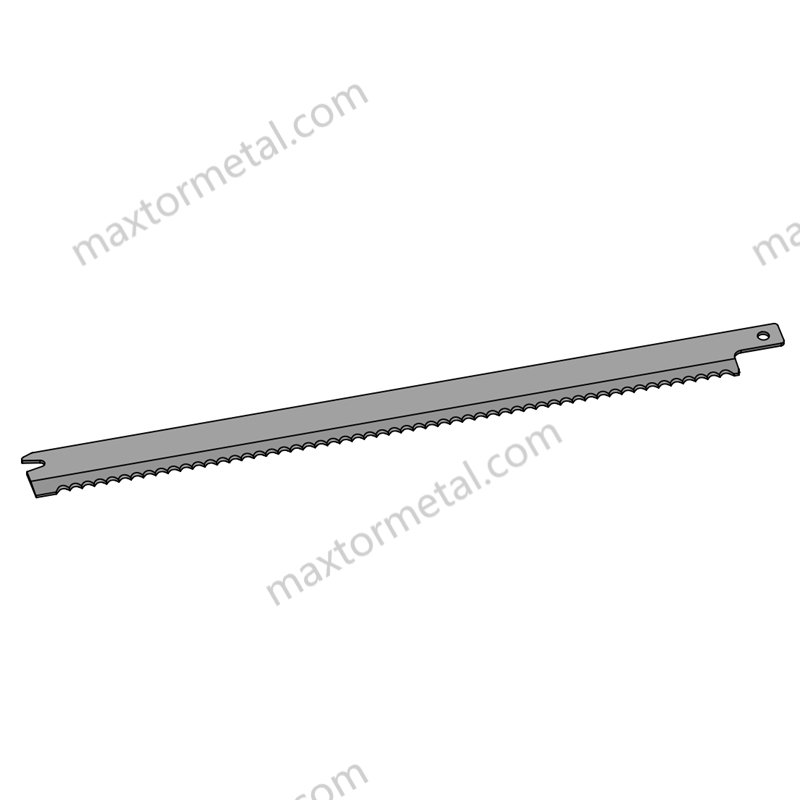
العلم وراء ذلك
تتكون معادن Metal من حبيبات مجهرية، وتتأثر خصائصها بشكل كبير بحجم هذه الحبيبات وشكلها واتجاهها. تُعدّل تقنيات المعالجة الحرارية، مثل التصليد أو التلدين، هذه الخصائص. على سبيل المثال، أثناء عملية التبريد، يتحول هيكل المعدن من الأوستينيت إلى المارتنسيت، مما يُنتج مادة أكثر صلابة ومقاومة للتآكل.
من خلال التحكم الدقيق في عوامل مثل تمن خلال التحكم في درجة الحرارة ومعدل التبريد ووقت الاحتفاظ، يضمن المصنعون أن المنتج النهائي يوفر موثوقية استثنائية، حتى في ظل الظروف الصناعية الأكثر صعوبة.
لماذا تعتبر المعالجة الحرارية ضرورية لأداء الشفرة
تعمل السكاكين الصناعية في بيئات قاسية، حيث تتعرض لدوران عالي السرعة، وتلامس للمواد الكاشطة، وتتعرض للحرارة لفترات طويلة. المعالجة الحرارية لا تُجهّز هذه الشفرات لتحمل هذه التحديات فحسب، بل تُحسّن أيضًا من أدائها وعمرها الافتراضي.
التأثير على خصائص شفرة المفتاح
- صلابة:
- قدرة الشفرة على قطع المواد الصلبة كالبلاستيك والمعادن والمنسوجات تتناسب طرديًا مع صلابتها. اختبارات ما بعد المعالجة (مثل اختبار صلابة روكويل) أظهرت الدراسات أن شفرات الفولاذ عالي السرعة (HSS) المقواة بشكل صحيح تحقق تصنيف صلابة يتراوح بين 62-67 HRC، وهو تحسن كبير مقارنة بالفولاذ غير المعالج.
- تضمن هذه الصلابة بقاء حافة الشفرة حادة لفترات طويلة، مما يقلل من تكرار الصيانة.
- صلابة:
- تضمن المتانة قدرة الشفرة على امتصاص الصدمات دون تشقق أو تشقق. على سبيل المثال، تُظهر شفرات الفولاذ الكربوني، عند تلطيفها بعد التصلب، زيادة في مقاومة الصدمات بنسبة 25-30%، مما يجعلها مناسبة لتطبيقات مثل تقطيع الخشب أو قص المعادن.
- ارتداء المقاومة:
- تزيد المعالجة الحرارية من قدرة السطح على مقاومة التآكل، حتى في ظل الظروف الكاشطة. تشير الدراسات إلى أن شفرات 30% المُقسّاة تحافظ على حدّتها لفترات أطول مقارنةً بنظيراتها غير المُقسّاة، مما يُقلّل بشكل كبير من وقت التوقف عن العمل.
فوائد خاصة بالمواد
- الفولاذ عالي السرعة (HSS):
- يكتسب مقاومة استثنائية للتآكل والتشوه بعد التصلب والتخمير، مما يجعله مثاليًا لتطبيقات القطع عالية السرعة.
- الفولاذ الكربوني:
- يظهر صلابة أفضل بعد التلدين، مما يجعله مناسبًا للمهام المتعددة حيث تكون الأولوية للمتانة على الصلابة.
- الفولاذ المقاوم للصدأ:
- من خلال معالجات متخصصة مثل التجميد بالتبريد العميق، يحقق الفولاذ المقاوم للصدأ بنية مارتنسيتية دقيقة، مما يعزز مقاومة التآكل مع الحفاظ على القوة.
من خلال تصميم عملية المعالجة الحرارية لتناسب السبائك المحددة والتطبيق المقصود، يمكن للمصنعين إنتاج سكاكين صناعية ذات خصائص أداء مثالية لكل حالة استخدام.
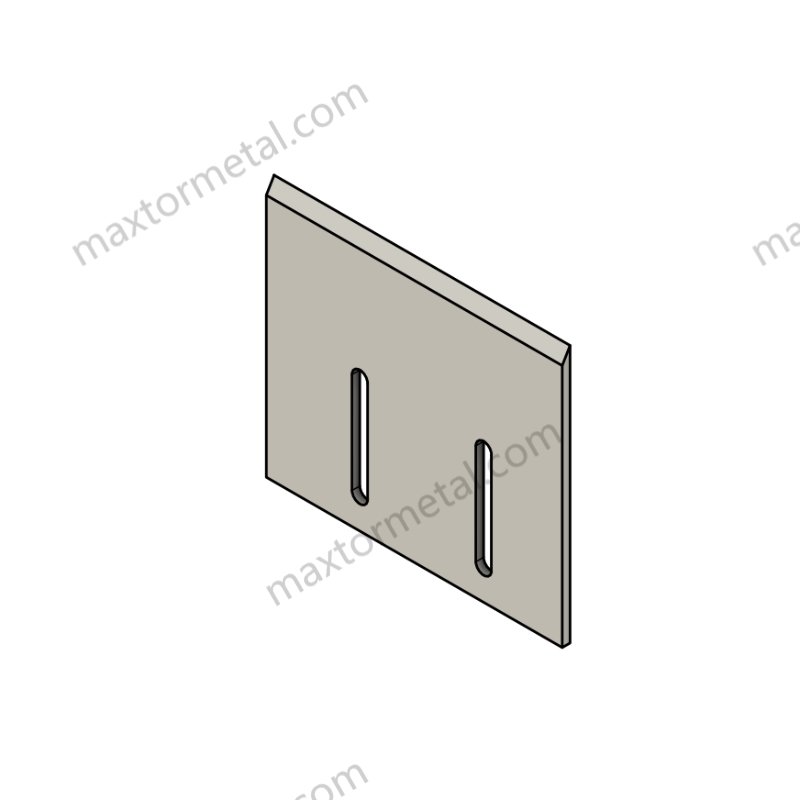
أنواع طرق المعالجة الحرارية
يعتمد تصنيع السكاكين الصناعي على طرق معالجة حرارية متنوعة، صُممت كل منها لتحقيق تحسينات ميكانيكية وبنيوية محددة في الشفرات. نستعرض أدناه أكثر العمليات استخدامًا، وآلياتها التفصيلية، ومزاياها، وتحدياتها، وتطبيقاتها الصناعية.
1. التصلب
عملية:
تبدأ عملية التصلب بتسخين الشفرة إلى حوالي 950 درجة مئوية (1750 درجة فهرنهايت)، حيث يتحول التركيب الدقيق للفولاذ إلى أوستينيت، وهي مرحلة تسمح للكربون بالذوبان بالتساوي. يلي ذلك تبريد سريع، عادةً باستخدام الزيت أو الهواء، لتثبيت التغييرات المطلوبة.
الآلية:
أثناء عملية التصلب، تُحاصر ذرات الكربون في بنية شبكية مشوهة، مما يؤدي إلى تكوين المارتنسيت، وهو أصلب بنية في الفولاذ. تُعدّ درجة الحرارة ومدة التسخين عاملين أساسيين لتحقيق الصلابة المطلوبة دون التعرض للكسر.
فوائد:
- مقاومة التآكل المحسنة:تتمتع سطح الشفرة المقوى بمقاومة كبيرة للتآكل، مما يجعلها مناسبة لقطع المواد الصلبة والكاشطة.
- الاحتفاظ بالحافة:يعمل التصلب على تحسين عمر الحواف الحادة، مما يقلل الحاجة إلى إعادة شحذها بشكل متكرر.
التطبيقات:
- شفرات المقصلة:تستخدم في الصناعات مثل صناعة الورق والتغليف والمنسوجات.
- سكاكين القص:لقطع المعادن أو المواد القوية الأخرى التي تتطلب الحدة والمتانة.
مثال:
في التجارب الصناعية، حققت شفرات الفولاذ عالي السرعة المقوى (HSS) تصنيف HRC (صلابة روكويل C) 65-68، مما أدى إلى مضاعفة عمرها الافتراضي تقريبًا مقارنة بنظيراتها غير المعالجة.
2. الإخماد
عملية:
تتضمن عملية التبريد التبريد السريع للشفرات بعد مرحلة التصلب لتصلب البنية المارتنسيتية. تشمل وسائط التبريد ما يلي:
- زيت: شائع في الفولاذ الكربوني والفولاذ السبائكي؛ يوفر تبريدًا متحكمًا به لمنع التشقق.
- ماء:تستخدم للمعادن التي تتطلب تبريدًا سريعًا ولكنها تزيد من خطر الانحناء.
- هواء:للحصول على شفرات دقيقة تتطلب الحد الأدنى من التشويه.
الآلية:
يُثبّت الإخماد البنية الصلبة بمنع إعادة تشكيل المراحل اللينة مثل البيرلايت أو الفريت. ومع ذلك، يُدخل إجهادات داخلية قد تحتاج إلى تخفيف من خلال المعالجة الحرارية.
التحديات:
- خطر التشقق:يؤدي التبريد السريع إلى خلق ضغوط حرارية غير متساوية.
- تشويه:قد تتشوه الشفرات الأكبر حجمًا أو الأرق بسبب التبريد غير المتساوي.
تدابير الرقابة:
- تساعد عملية المعادلة الحرارية المسبقة على تقليل خطر الصدمة الحرارية.
- تتنبأ الأدوات الحديثة، مثل برامج محاكاة الإخماد، بالعيوب المحتملة وتعمل على تخفيفها.
التطبيقات:
يعتبر التبريد ضروريًا للأدوات التي تتطلب أقصى قدر من الصلابة، مثل مفرمة الخشب، شفرات الحبيبات، و آلات التقطيع الصناعية.
مثال:
أدى التبريد إلى زيادة صلابة شفرات الفولاذ المستخدمة في الأدوات D2 إلى نطاق يتراوح بين 58-62 HRC، مما أدى إلى زيادة مقاومتها للتآكل والصدمات الشديدة.
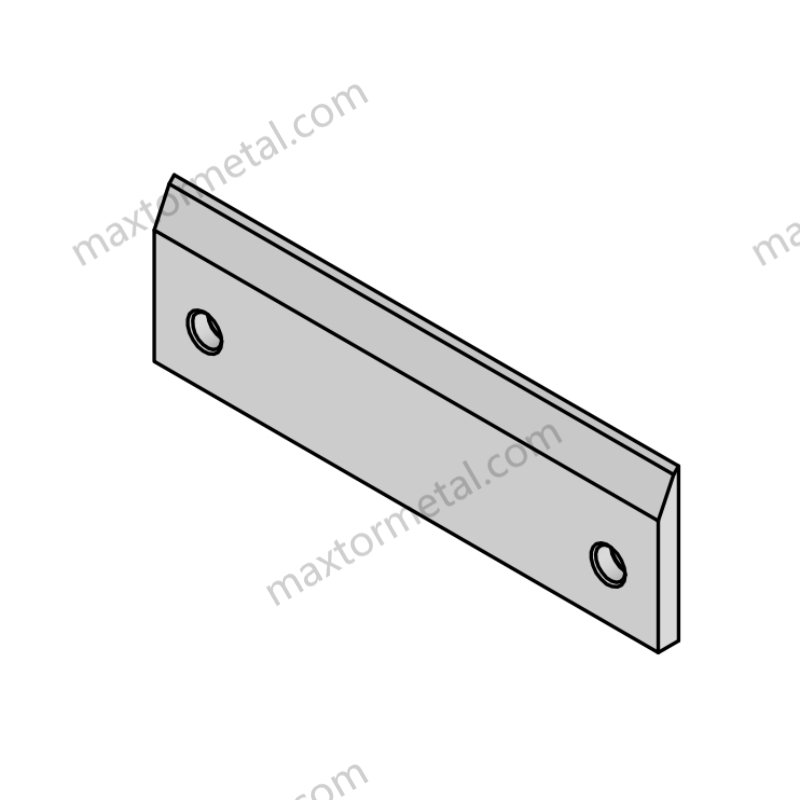
3. التلدين (التطبيع)
عملية:
تتضمن عملية التصلب، المعروفة أيضًا بالتلدين، إعادة تسخين الشفرة إلى درجة حرارة معتدلة (300-1100 درجة فهرنهايت أو 150-600 درجة مئوية) بعد التبريد. تعتمد درجة الحرارة الدقيقة على التوازن المطلوب بين الصلابة والمتانة. قد تتضمن هذه المرحلة دورات متعددة (1-3) للحصول على أفضل النتائج، خاصةً في الفولاذ عالي السبائك.
الآلية:
أثناء عملية التطبيع، تُخفَّف الضغوط الداخلية الناتجة عن الإخماد. ينتقل هيكل المعدن إلى حالة أكثر استقرارًا، مع تعديلات مُتحكَّم فيها لصلابته ومرونته ومرونته.
فوائد:
- هشاشة منخفضة:يضمن عدم تشقق الشفرات عند التعرض لصدمات مفاجئة أو أحمال ثقيلة.
- تحسين المرونة:يساعد الشفرات على تحمل قوى الانحناء دون أن تنكسر.
التطبيقات:
تُستخدم الشفرات المقسّاة على نطاق واسع في الصناعات التي تتطلب مزيجًا من المتانة والاحتفاظ بالحافة، مثل:
- سكاكين التقطيع:لقطع المواد الرقيقة مثل الفيلم أو الرقائق.
- شفرات دائرية:تستخدم في معالجة الأغذية أو المواد خفيفة الوزن.
دراسة الحالة:
أظهرت دراسة أجريت على شفرات الفولاذ الكربوني المقسّى 1095 زيادة في مقاومة الصدمات بواسطة 30%، مما يجعلها مثالية لقطع الأخشاب الصلبة وغيرها من المواد الكثيفة.
مقارنة الأساليب
طريقة | صلابة | صلابة | ارتداء المقاومة | التطبيقات |
التصلب | عالي | واسطة | عالي | سكاكين المقصلة والمقصات |
التبريد | عالي | منخفض (مُسبق الغضب) | عالي | آلات التقطيع والحبيبات |
هدأ | واسطة | عالي | واسطة | آلات التقطيع, معالجة الغذاء |
تكمل كل عملية الأخرى، حيث تعمل التصلب والتبريد على تحديد الصلابة المطلوبة، بينما توفر عملية التلطيف الصلابة اللازمة للمتانة الصناعية.
مشاكل المعالجة الحرارية الشائعة وحلولها
المعالجة الحرارية هي عملية حساسة للغاية يتطلب ذلك تحكمًا دقيقًا في درجة الحرارة والتوقيت والظروف البيئية. حتى الانحرافات الطفيفة قد تؤدي إلى عيوب تؤثر على أداء الشفرة ومتانتها وموثوقيتها. فيما يلي عرض مفصل للمشاكل الشائعة وأسبابها وحلولها العملية.
مشكلة | سبب | حل | البيانات الداعمة |
التصلب الزائد | التسخين المفرط أو التبريد السريع للغاية، مما يؤدي إلى تكوين بنية مارتنسيتية صلبة وهشة للغاية. | اضبط إعدادات درجة الحرارة على النطاقات المناسبة (مثلًا: الفولاذ عالي السرعة: ١٧٥٠-٢٢٠٠ درجة فهرنهايت، الفولاذ الكربوني: ١٣٠٠-١٦٥٠ درجة فهرنهايت). حسّن معدلات التبريد باستخدام أدوات المحاكاة. | تشير الدراسات إلى أن خفض درجة حرارة التصلب بمقدار 5% فقط يقلل من الهشاشة دون التضحية بالصلابة. |
تكسير | تراكم الإجهاد أثناء الإطفاء، غالبًا بسبب التبريد السريع أو التركيب غير المتساوي للمواد. | التسخين المسبق التدريجي قبل الإطفاء (حوالي ٣٠٠ درجة فهرنهايت) لتقليل الصدمة الحرارية. استخدم وسائل تبريد مُتحكم بها، مثل الزيت، بدلاً من الماء. | تسلط تقارير الصناعة الضوء على أن التحول من التبريد بالماء إلى التبريد بالزيت يقلل من حدوث التشققات بمقدار 30-40%. |
صلابة غير متساوية | درجة حرارة الفرن أو معدلات التبريد غير متناسقة. | ضمان توزيع الحرارة بشكل متساوي من خلال أفران متعددة المناطق متطورة مع تنظيم حراري دقيق. | يؤدي استخدام الأفران المعايرة مع فروق درجة الحرارة أقل من ±10 درجة فهرنهايت إلى تحسين توحيد الصلابة بحلول عام 20%. |
التشويه | التبريد غير المتماثل، أو أقسام الشفرات الرقيقة، أو المحاذاة غير السليمة أثناء العلاج. | استخدم أدوات التثبيت أو الدعامات أثناء التبريد للحفاظ على محاذاة الهيكل. اختر طرق تبريد أبطأ وأكثر انتظامًا. | أظهرت دراسة حالة أجريت على شفرات المقصلة أن تنفيذ أدوات المحاذاة أدى إلى تقليل الانحناء بمقدار 50%. |
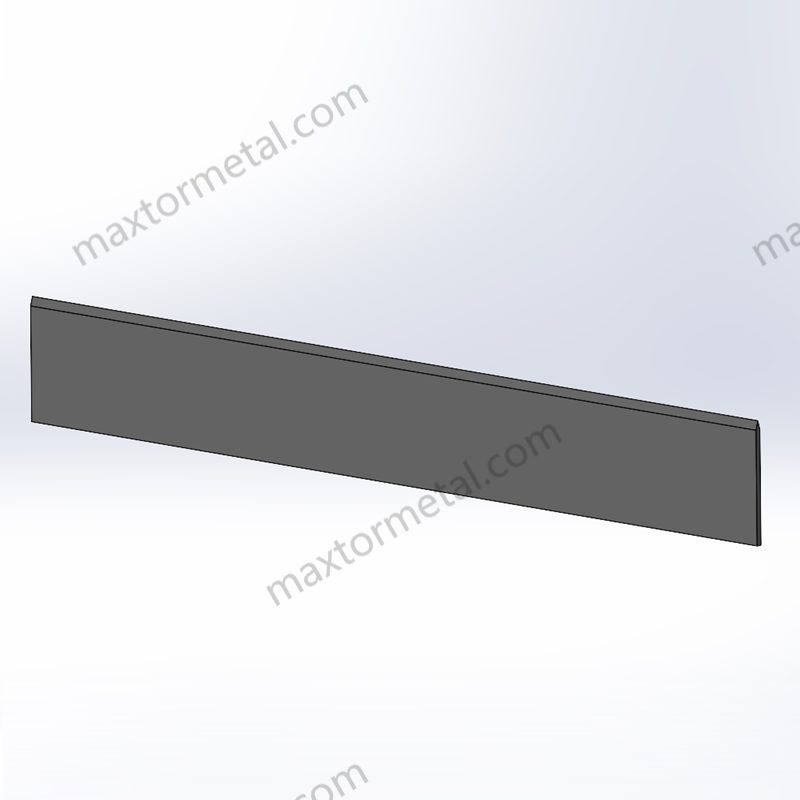
أفضل الممارسات الإضافية لمراقبة الجودة
- استخدم أجهزة اختبار صلابة روكويل لقياس صلابة الشفرات المعالجة. تُعدّ معايير الاختبار، مثل HRC 60-65 لشفرات الفولاذ عالي السرعة، معايير صناعية لأداء قطع فائق.
- استخدم أدوات التحليل البنيوي الدقيق مثل المجاهر الإلكترونية الماسحة (SEM) لفحص بنية الحبوب وتحديد المخالفات المحتملة.
رؤية الصناعة:
وفقًا لمسح أجرته عام 2023 معهد المعالجة Metalأكثر من 75% من عيوب سكاكين الآلات المعالجة حرارياً ناجمة عن عدم كفاية التحكم في العملية. الاستثمار في أنظمة المراقبة الآنية والنمذجة التنبؤية يمكن أن يقلل هذه المشاكل بشكل كبير.
درجات الحرارة والأوقات المثالية للمعالجة الحرارية للسكاكين الصناعية
تعتمد كفاءة المعالجة الحرارية بشكل كبير على التحكم الدقيق في درجة الحرارة والتوقيت، بما يتناسب مع نوع المادة وتطبيق الشفرة. فيما يلي جدول شامل يلخص المعايير المثلى بناءً على أبحاث واختبارات صناعية مكثفة:
مادة | درجة الحرارة المثالية (°ف) | المدة الموصى بها | ملاحظات نقدية |
حديدعالى السرعه | 1750–2200 | 1-2 ساعة (التصلب)؛ التلطيف: حوالي ساعتين عند 1000 درجة فهرنهايت | يؤدي التعرض لفترات طويلة لدرجات حرارة تزيد عن 2200 درجة فهرنهايت إلى خشونة الحبوب وتقليل احتفاظ الحافة. |
الفولاذ الكربوني | 1300–1650 | 30-60 دقيقة (دورة التلدين)؛ التبريد: سريع | يمكن أن يؤدي ارتفاع درجة الحرارة إلى أكثر من 1650 درجة فهرنهايت إلى إزالة الكربون، مما يؤدي إلى إضعاف الحافة القاطعة. |
الفولاذ المقاوم للصدأ | 1800–2000 | 2-4 ساعات (معالجة المحلول)؛ التهدئة: ساعتان عند 400-600 درجة فهرنهايت | يؤدي استخدام أفران التفريغ إلى تقليل الأكسدة وضمان سطح شفرة نظيف وناعم. |
فولاذ الأدوات (D2، A2) | 1850–1950 | ساعتان (التصلب)؛ التلطيف: 2-3 دورات عند درجة حرارة ~500 درجة فهرنهايت | تعمل عملية التبريد متعدد الدورات على تحسين مقاومة الصدمات، وهو أمر ضروري لقطع المواد الكاشطة مثل المعدن. |
تأثيرات درجة الحرارة والتوقيت غير الصحيحين
- انخفاض درجة الحرارة:
- يؤدي إلى تحول غير كامل إلى الأوستينيت، مما يؤدي إلى انخفاض الصلابة.
- دراسة الحالة: أدى انخفاض درجة حرارة شفرات الفولاذ D2 بمقدار 50 درجة فهرنهايت فقط إلى انخفاض كفاءة القطع بنسبة 15% في تطبيق قص المعادن.
- ارتفاع درجة الحرارة:
- يسبب خشونة الحبوب، مما يقلل من صلابتها واحتفاظها بالحافة.
- تظهر أبحاث الصناعة أن الإفراط في التعرض لدرجات الحرارة المرتفعة يزيد من قابلية حدوث شقوق التعب الحراري بنسبة 25%.
- مدة غير كافية:
- يمنع الانتشار الكامل للكربون أو عناصر السبائك.
- مثال: أدت دورات التبريد المختصرة لشفرات HSS إلى صلابة غير متسقة عبر الشفرة، مما أدى إلى زيادة معدلات التآكل بنسبة 20%.
- مدة مفرطة:
- يؤدي إلى استهلاك طاقة غير ضروري وقد يؤدي إلى تدهور جودة السطح بسبب الأكسدة أو الترسب.
- تقنيات متقدمة مثل جو الغاز الخاملس (على سبيل المثال، النيتروجين أو الأرجون) يتم استخدامها الآن لمقاومة هذه التأثيرات.
رؤى قائمة على البيانات حول تحسين المعالجة الحرارية
أحدثت التطورات الحديثة في المحاكاة والمراقبة الآنية ثورةً في عملية المعالجة الحرارية. على سبيل المثال:
- تحليل العناصر المحدودة (FEA):نمذجة انتقال الحرارة وتوزيع الإجهاد، والتنبؤ بالعيوب المحتملة قبل المعالجة. باستخدام تحليل العناصر المحدودة، خفّضت الشركات معدلات الرفض بمقدار 30% لأدوات القطع عالية الدقة.
- التصوير الحراري بالأشعة تحت الحمراء:يتتبع اتساق درجة الحرارة أثناء المعالجة الحرارية، مع انحرافات أقل من ±5 درجة فهرنهايت لضمان خصائص متسقة.
دعم البحوث:
- دراسة نشرت في مجلة تكنولوجيا معالجة المواد (2021) أبرز أن الأفران متعددة المناطق ذات التحكم الحراري الدقيق حققت اتساق 98% في الصلابة عبر دفعات كبيرة من سكاكين HSS.
- ال المجلة الدولية للمعالجة الحرارية (2022) وجد أن دمج المعالجة الحرارية الفراغية يقلل من العيوب المرتبطة بالأكسدة في سكاكين الفولاذ المقاوم للصدأ بواسطة 80%، مما يزيد من موثوقية المنتج.
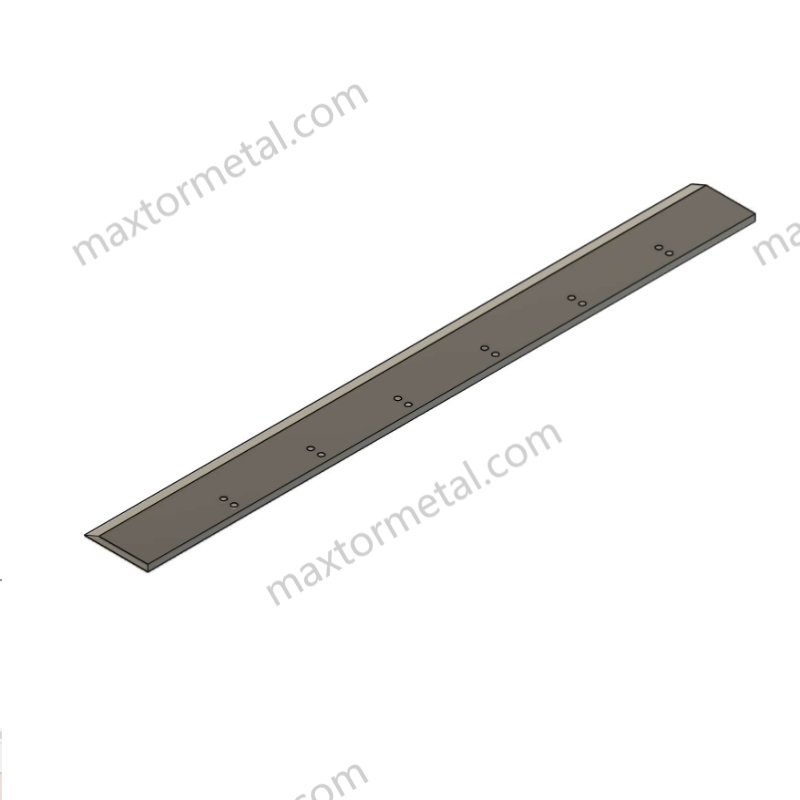
ضمان الجودة المعزز بعد المعالجة الحرارية
تخضع الشفرات المعالجة حرارياً لمراقبة جودة صارمة لضمان استيفائها لمعايير الأداء. تشمل أفضل ممارسات الصناعة ما يلي:
- اختبار الصلابة:
- تتحقق أدوات مثل أجهزة اختبار فيكرز وروكويل من صلابة سطح الشفرات المعالجة. على سبيل المثال، يجب أن تتراوح صلابة شفرة HSS عالية الجودة بين 62 و65 درجة مئوية، مما يضمن قوة قطع مثالية.
- التحليل البنيوي الدقيق:
- تكتشف الطرق المتقدمة مثل حيود الإلكترونات الخلفية (EBSD) تجانس بنية الحبوب، والذي يرتبط ارتباطًا مباشرًا بأداء الشفرة.
- اختبارات سلامة الحافة:
- يتم إخضاع الشفرات لمهام قطع محاكاة لقياس احتفاظ الحافة في ظل ظروف العالم الحقيقي.
ابتكارات المعالجة الحرارية والاتجاهات المستقبلية
مع تزايد الطلب الصناعي على دقة ومتانة واستدامة أعلى، تُحدث تقنيات المعالجة الحرارية المبتكرة نقلة نوعية في عمليات التصنيع. تُعزز هذه التطورات كفاءة ودقة واستدامة إنتاج السكاكين الآلية بيئيًا. وتُعد طريقتان متطورتان - المعالجة الحرارية بالتفريغ والتسخين الحثي عالي التردد - بارزتين بشكل خاص لتأثيرهما التحويلي على الصناعة.
1. المعالجة الحرارية بالفراغ
ملخص:
تتضمن المعالجة الحرارية الفراغية معالجة الشفرات في حجرة تفريغ محكمة الغلق، حيث يُفرّغ الهواء والغازات التفاعلية لخلق بيئة خاملة. تمنع هذه الطريقة الأكسدة، والترسّب، وإزالة الكربون (فقدان الكربون من سطح الشفرة)، وهي مشاكل شائعة في المعالجة الحرارية التقليدية.
الميزات الرئيسية:
- منع الأكسدة:من خلال إزالة الأكسجين، تضمن المعالجة الحرارية الفراغية سطح شفرة نظيف وناعم، مما يقلل من متطلبات التلميع بعد المعالجة.
- التحكم الدقيق في درجة الحرارة:تسمح أفران التفريغ المتقدمة بتوحيد درجة الحرارة داخل ±2 درجة فهرنهايت، مما يضمن نتائج متسقة عبر الدفعات.
- تخفيف إزالة الكربون:يحافظ على محتوى الكربون في الشفرة، ويحافظ على الخصائص المهمة مثل الصلابة ومقاومة التآكل.
فوائد:
- تحسين جودة السطح:تتمتع الشفرات المعالجة في أفران التفريغ بسطح أنظف بدون تغير في اللون أو تراكم القشور.
- سلامة المواد الأعلى:يحافظ غياب عملية إزالة الكربون على ثبات حافة الشفرة، مما يجعلها مثالية للأدوات الدقيقة مثل سكاكين التقطيع والشفرات الجراحية.
- كفاءة الطاقة:تستخدم العديد من أفران التفريغ تدفئة متعددة المناطق والعزل الأمثل، مما يقلل من استهلاك الطاقة بما يصل إلى 25% مقارنة بالطرق التقليدية.
التطبيقات:
- شفرات عالية الدقة:تستفيد المشارط الجراحية وسكاكين التقطيع الصناعية وأدوات القطع عالية السرعة من هذه الطريقة النظيفة والدقيقة.
- الفولاذ عالي السبائك:تعتبر السبائك مثل HSS والفولاذ المقاوم للصدأ مناسبة بشكل خاص للمعالجة بالتفريغ بسبب حساسيتها للأكسدة.
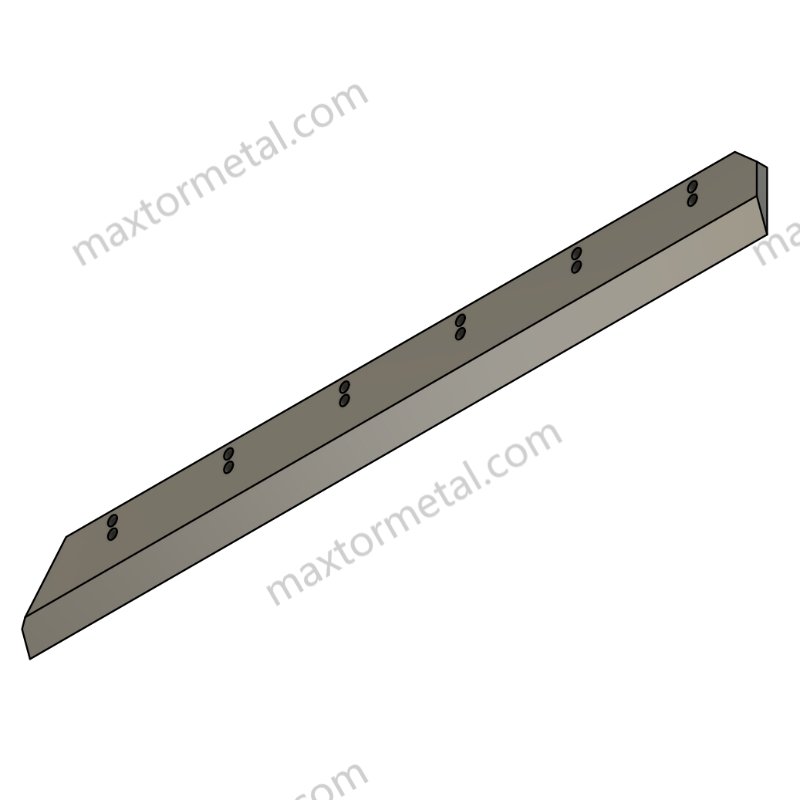
2. التدفئة بالحث عالي التردد
ملخص:
التسخين الحثي عالي التردد هو طريقة تسخين موضعية وسريعة، تستخدم مجالات كهرومغناطيسية لتسخين مناطق محددة من الشفرة. تتميز هذه التقنية بكفاءة عالية ومثالية للتطبيقات التي تتطلب تصلبًا انتقائيًا.
الميزات الرئيسية:
- التسخين السريع:يمكن لأنظمة التسخين الحثي تسخين سطح الشفرة إلى 2000 درجة فهرنهايت (1093 درجة مئوية) خلال ثواني.
- تطبيق محلي:يسمح بالتصلب الانتقائي لمناطق محددة (على سبيل المثال، حواف الشفرة) مع ترك القلب أكثر ليونة نسبيًا من أجل الصلابة.
- عملية عدم الاتصال:يتم التسخين دون اتصال جسدي، مما يزيل مخاطر التلوث.
فوائد:
- كفاءة الوقت:تعمل تقنية التسخين الحثي على تقليل أوقات دورة المعالجة الحرارية بما يصل إلى 80%- تحسين معدل الإنتاج.
- توفير الطاقة:تعمل التدفئة المركزة على تقليل إجمالي استهلاك الطاقة بما يصل إلى 30% مقارنة بالطرق المعتمدة على الفرن.
- تحسين الأداء:يخلق حافة صلبة ذات قلب قوي، مما يؤدي إلى أداء قطع متفوق ومقاومة للصدمات.
التطبيقات:
- شفرات القص:تضمن عملية التسخين الحثي حواف حادة ومتينة مع الحفاظ على المتانة الهيكلية.
- سكاكين المحبب:تتطلب هذه الأدوات حافة صلبة للتعامل مع المواد الكاشطة ونواة مرنة لامتصاص الصدمات.
الاستدامة في تقنيات المعالجة الحرارية
تتماشى كلٌّ من المعالجة الحرارية بالتفريغ والتسخين الحثي مع الطلب المتزايد على ممارسات التصنيع المستدامة. وتشمل الفوائد البيئية الرئيسية ما يلي:
- انخفاض استهلاك الطاقة:تعمل أنظمة التفريغ والحث الحديثة على تقليل استخدام الطاقة عن طريق 20–30%، مما يؤدي إلى خفض تكاليف التشغيل والبصمة الكربونية.
- انخفاض الانبعاثات:من خلال القضاء على الحاجة إلى النيران المكشوف والغازات الخطرة، تساهم هذه الأساليب في توفير بيئات إنتاج أنظف.
- كفاءة المواد:تعمل العمليات الدقيقة على تقليل هدر المواد، مما يضمن استخدامًا أكثر كفاءة للسبائك عالية الجودة.
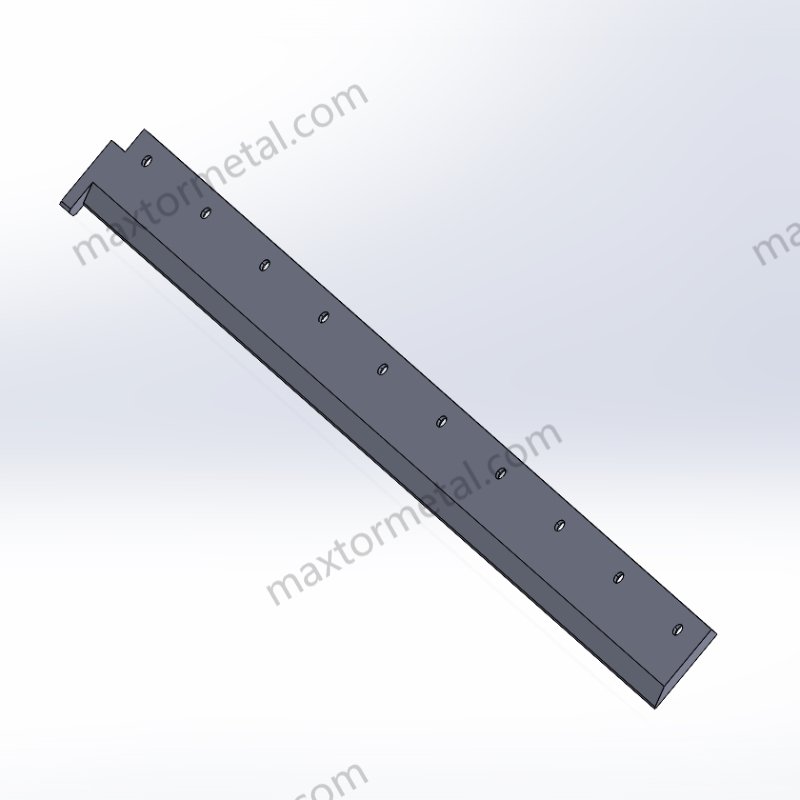
الاستدامة في تقنيات المعالجة الحرارية
تتماشى كلٌّ من المعالجة الحرارية بالتفريغ والتسخين الحثي مع الطلب المتزايد على ممارسات التصنيع المستدامة. وتشمل الفوائد البيئية الرئيسية ما يلي:
- انخفاض استهلاك الطاقة:تعمل أنظمة التفريغ والحث الحديثة على تقليل استخدام الطاقة عن طريق 20–30%، مما يؤدي إلى خفض تكاليف التشغيل والبصمة الكربونية.
- انخفاض الانبعاثات:من خلال القضاء على الحاجة إلى النيران المكشوف والغازات الخطرة، تساهم هذه الأساليب في توفير بيئات إنتاج أنظف.
- كفاءة المواد:تعمل العمليات الدقيقة على تقليل هدر المواد، مما يضمن استخدامًا أكثر كفاءة للسبائك عالية الجودة.
من خلال تبني تقنيات متقدمة، مثل المعالجة الحرارية الفراغية والتسخين الحثي عالي التردد، يمكن للمصنعين تحقيق أداء فائق للشفرات، وزيادة كفاءة الإنتاج، وعمليات مستدامة. هذه الابتكارات لا تلبي المتطلبات الصارمة للصناعات الحديثة فحسب، بل تضع المصنعين أيضًا في صدارة السوق التنافسية.
خاتمة
المعالجة الحرارية هي أساس تصنيع السكاكين الصناعية، فهي تُحسّن أداء الشفرات وطول عمرها وموثوقيتها. بإتقان فن وعلم هذه العملية، يُصبح المصنّعون مثل نانجينغ Metal ضمان أن شفراتهم تلبي أعلى معايير الصناعة.
مع 18 عامًا من الخبرة وفريق تصميم ماهر وتقنيات تصنيع متقدمة، تتخصص شركة Nanjing Metal في سكاكين آلية مخصصة نتميز في مختلف التطبيقات الصناعية. سواءً كنت بحاجة إلى شفرات مقصلة دقيقة أو سكاكين قص متعددة الاستخدامات، فلدينا الأدوات والمعرفة اللازمة لتلبية احتياجاتك.
اتصل بنا اليوم للحصول على حلول مخصصة وعروض أسعار مجانية لاكتشاف كيف يمكن لخبرتنا أن ترفع مستوى عملياتك.
استجابة واحدة