Industrielle Schneidvorgänge erfordern Präzision, Effizienz und Langlebigkeit. Ob in der Papier-, Kunststoff-, Metall- oder Textilindustrie, Schlitzklingen und Messer spielen eine entscheidende Rolle für glatte und präzise Schnitte. Ein Schlüsselfaktor, der die Leistung einer Klinge maßgeblich beeinflusst, ist der Kantenradius der Schneidklinge.
Viele Hersteller übersehen die Bedeutung dieses scheinbar kleinen Details, doch es wirkt sich direkt auf Haltbarkeit, Schneidleistung, Sicherheit und die allgemeine Produktionsqualität aus. Dieser Artikel untersucht die Bedeutung des Kantenradius bei Industriemessern, seinen Einfluss auf die Schneidleistung und die Auswahl des richtigen Radius für Ihre Anwendung.
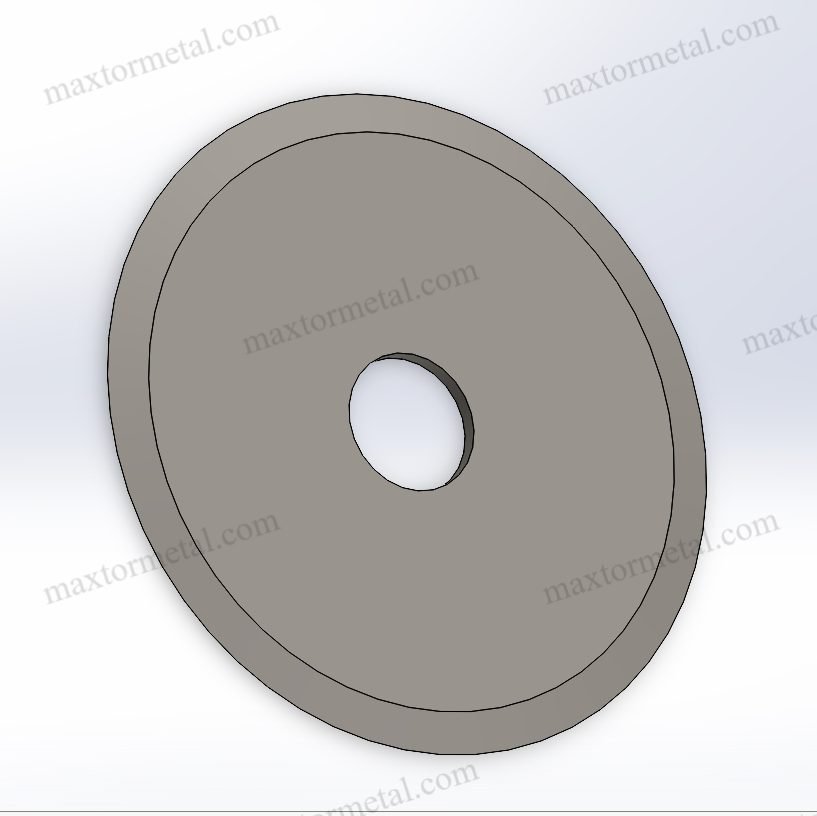
1. Was ist der Kantenradius?
1.1 Definition und Bedeutung
Beim industriellen Schneiden bezeichnet der Kantenradius die Krümmung oder Rundung an der äußersten Spitze eines Schlitzklinge oder Messer. Er wird als Radius der abgerundeten Kante gemessen, an der die beiden Klingenoberflächen aufeinandertreffen. Obwohl eine Kante mit bloßem Auge scharf erscheinen mag, zeigt eine mikroskopische Untersuchung, dass selbst die schärfsten Klingen eine gewisse Krümmung aufweisen.
Dieses kleine, aber entscheidende Detail wirkt sich erheblich auf Schneidleistung, Haltbarkeit, Energieeffizienz und Sicherheit aus. Ein optimierter Kantenradius reduziert die Spannungskonzentration, minimiert das Absplittern der Klinge und verlängert deren Lebensdauer.
📌 Wichtige technische Erkenntnisse:
Der Kantenradius wird üblicherweise in Mikrometern (µm) gemessen, wobei die Werte je nach Anwendung zwischen 5µm und 50µm liegen.
- Kleiner Kantenradius (<10µm): Ideal für ultrapräzise Schnitte, nutzt sich jedoch schnell ab.
- Mittlerer Kantenradius (10–30µm): Am besten für eine ausgewogene Leistung zwischen Schärfe und Haltbarkeit.
- Großer Kantenradius (>30µm): Haltbarer, erfordert aber möglicherweise eine höhere Schneidkraft.
1.2 Klingenkantenform: Scharf vs. Abgerundet
Mikroskopische Unterschiede und ihre Auswirkungen
Unter einem Hochleistungsmikroskop eine scharfkantige Klingee hat eine spitze Struktur, während eine Klinge mit Kantenradius einen leicht gebogenen Übergang an der Spitze hat.
Kantentyp | Mikroskopische Struktur | Schnitteigenschaften | Haltbarkeit | Ideale Anwendungen |
Scharfe Kante | Feine Spitze mit fast keiner Krümmung | Geringe Schnittkraft, präzise Anschnitte | Verschleißt schnell, neigt zum Absplittern | Dünne Kunststofffolien, Textilien, Weichfolien |
Abgerundete Kante (mit Kantenradius) | Gebogene Spitze mit gleichmäßiger Kraftverteilung | Weniger Schnittwiderstand, sanfteres Schneiden | Längere Lebensdauer, geringere Absplitterungsgefahr | Schneiden von Karton, Papier, Gummi und Metall |
📌 Branchenfallstudie:
Eine Studie aus dem Jahr 2019 über industrielle Schneidklingen ergab Folgendes:
- Klingen mit einem Kantenradius von 15–20 µm blieben beim Hochgeschwindigkeits-Papierschneiden 30% länger scharf als Klingen mit einem Radius von 5 µm.
- Eine Klinge mit einem Radius von 30 µm reduzierte die Mikroabsplitterung bei Metallschneidevorgängen durch 40% und verringerte so die Klingenwechselhäufigkeit.
1.3 Wie sich der Kantenradius auf verschiedene Klingenmaterialien auswirkt
Verschiedene Klingenmaterialien wirken sich aufgrund ihrer Härte und Verschleißfestigkeit unterschiedlich auf den Kantenradius aus:
Klingenmaterial | Kantenradiuseignung | Beste Anwendungen |
Schnellarbeitsstahl (HSS) | 10–30µm | Papier, Kunststofffolien, Weichmetalle |
Wolframkarbid | 20–50µm | Dicker Gummi, abrasive Materialien, Metallschlitzen |
Keramikklingen | 5–20 µm | Hochpräzise Schnitte, elektronische Filme |
Die Wahl des richtigen Kantenradius in Kombination mit Klingenmaterial sorgt für optimale Schneidleistung und längere Lebensdauer.
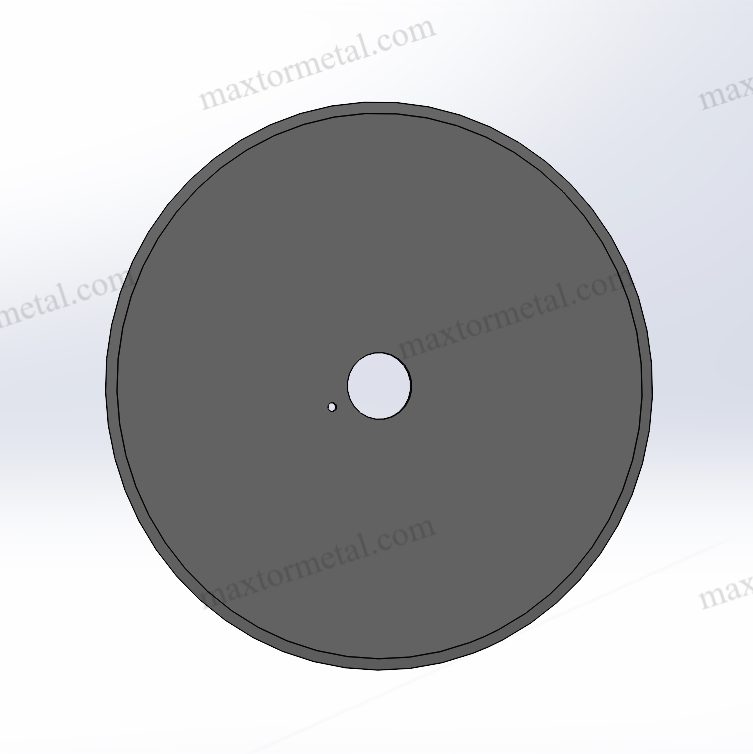
2. Warum der Kantenradius wichtig ist
2.1 Erhöht die Haltbarkeit
Eine scharfkantige Klinge weist an ihrer Spitze eine hohe Spannungskonzentration auf, wodurch sie anfällig für Absplitterungen und schnellen Verschleiß ist. Eine Klinge mit leicht abgerundetem Kantenradius verteilt die Schnittkraft gleichmäßiger und verhindert so einen vorzeitigen Ausfall.
Technische Einblicke in die Spannungsverteilung von Rotorblättern
Simulationen mit der Finite-Elemente-Analyse (FEA) zeigen, dass:
- Ein Kantenradius von 5 µm führt zu einer doppelt so hohen Spannungskonzentration an der Schnittstelle wie ein Kantenradius von 20 µm.
- Ein Kantenradius von 30 µm reduziert Mikrobrüche in Hartmetallklingen um 35% und führt so zu einer längeren Klingenlebensdauer.
📌 Anwendung in der realen Welt:
Beim Schneiden von Wellpappe ist der Wechsel von einer scharfen Klinge (5µm Radius) zu einer Klinge mit mikroabgerundeter Kante (Radius 15 µm) erhöhte Klingenlebensdauer um 25%, wodurch Umrüstungen und Betriebskosten reduziert wurden.
2.2 Verbessert die Schnittqualität
Der richtige Kantenradius sorgt für sauberere, gleichmäßigere Schnitte, indem er Risse und Materialverformungen minimiert. Eine zu scharfe Klinge kann sich schnell abnutzen, was zu ungleichmäßigen Schnitten führt.
Einfluss des Kantenradius auf verschiedene Materialien
Materialtyp | Idealer Kantenradius | Auswirkungen auf die Schnittqualität |
Dünne Kunststofffolie | 5–10 µm | Reduziert Risse und verbessert die Glätte |
Papier & Karton | 10–20µm | Reduziert Papierstaub und verbessert die Schnittkonsistenz |
Dicke Gummiplatten | 20–30µm | Minimiert Verformungen und erhöht die Präzision |
Blech | 30–50µm | Verhindert übermäßigen Verschleiß und sorgt für Langlebigkeit |
📌 Branchenbeispiel:
Ein Hersteller flexibler Verpackungen berichtete, dass durch die Erhöhung des Klingenkantenradius von 10 µm auf 20 µm die Zahl fehlerhafter Schnitte um 15% reduziert wurde, was zu weniger Materialabfall und einer höheren Ausbeute führte.
2.3 Verbessert die Schneideffizienz
Die Schneideffizienz hängt von Widerstand, Wärmeentwicklung und Klingenlebensdauer ab. Ein optimierter Kantenradius kann den Schneidwiderstand reduzieren und so zu höheren Bearbeitungsgeschwindigkeiten und geringerem Energieverbrauch führen.
Reduzierung des Schnittwiderstands durch Kantenradius
Eine Studie über Schlitzklingen in Schnellarbeitsstahlanwendungen ergab Folgendes:
- Eine Klinge mit einem Kantenradius von 15 µm erfordert 10% weniger Schneidkraft als eine scharfe Klinge mit 5 µm.
- Eine Klinge mit einem Kantenradius von 30 µm bei Metallschneideanwendungen reduzierte die Reibung und verbesserte die Geschwindigkeit um 18%.
Wie sich der Kantenradius auf den Energieverbrauch auswirkt
Bei schnellem Klingenverschleiß erhöht sich der Schnittwiderstand, was den Motorbedarf automatisierter Schneidemaschinen erhöht. Durch die Optimierung des Kantenradius konnten Unternehmen Folgendes reduzieren:
✔ Maschinenstromverbrauch um bis zu 12%
✔ Klingenersatz durch 20–30%
✔ Ausfallzeit für Wartungsarbeiten durch 15%
📌 Effizienzsteigerungen beim Kunststoffschneiden:
Eine Verpackungsfabrik, die Schlitzmesser mit einem Kantenradius von 25 µm verwendet, konnte aufgrund des verringerten Materialwiderstands eine Steigerung der Liniengeschwindigkeit um 30% verzeichnen.
2.4 Verbessert die Sicherheit
Eine scharfe Klinge ohne Kantenradius kann zu unerwarteten Absplitterungen führen und so das Risiko von Klingenbrüchen und Arbeitsunfällen erhöhen. Die Optimierung des Kantenradius verbessert die Handhabungssicherheit und reduziert die Risiken bei der Wartung.
Wichtige Sicherheitsvorteile eines abgerundeten Kantenradius
✔ Weniger Absplittern der Klinge: Reduziert das Risiko, dass scharfe Fragmente abbrechen.
✔ Einfachere Handhabung der Klinge: Minimiert das Risiko versehentlicher Schnitte während der Installation.
✔ Geringere Ermüdung des Bedieners: Reduziert den erforderlichen übermäßigen Kraftaufwand beim Schneiden.
📌 Verbesserung der Wartungssicherheit:
Eine Papierverarbeitungsanlage ist auf Klingen mit einem mikrogerundeten Kantenradius von 20 µm umgestiegen. Dadurch wurden die Fälle von Klingenbrüchen um 50% reduziert und die Arbeitsumgebung der Maschinenbediener sicherer.
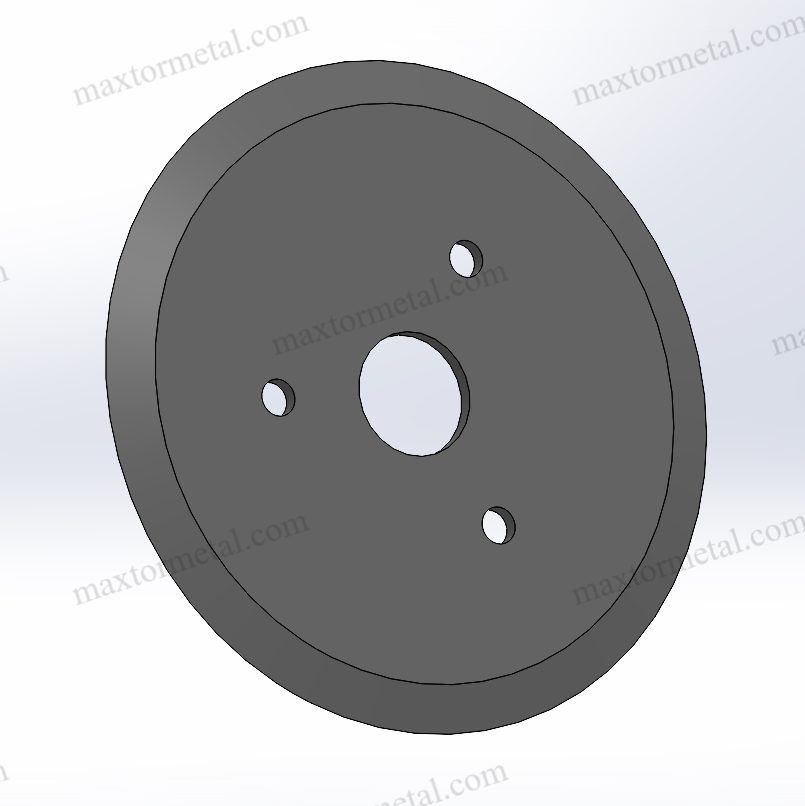
3. So wählen Sie den richtigen Kantenradius
Die Wahl des richtigen Kantenradius ist entscheidend für optimale Leistung, Haltbarkeit und Effizienz der Klinge. Die richtige Wahl hängt von verschiedenen Faktoren ab, wie z. B. Materialart, Schnittgeschwindigkeit, erforderliche Präzision und Klingenzusammensetzung. Nachfolgend finden Sie eine detaillierte Anleitung zur Bestimmung des optimalen Kantenradius für Ihre spezifische Anwendung.
3.1 Materialart und Dicke
Das zu schneidende Material spielt eine wichtige Rolle bei der Bestimmung des geeigneten Kantenradius. Verschiedene Materialien reagieren unterschiedlich auf die Sägeblattgeometrie. Die Wahl des richtigen Radius kann Risse, Staubentwicklung und vorzeitigen Sägeblattverschleiß minimieren.
Materialtyp | Materialeigenschaften | Empfohlener Kantenradius | Grund |
Dünne Kunststofffolien | Weich, dehnbar | 5–10µm (scharf) | Verhindert Dehnungen und sorgt für saubere Schnitte |
Papier & Karton | Faserig, geschichtet | 10–20µm (mittel) | Reduziert Staub und verbessert die Kantenglätte |
Dicke Gummiplatten | Dicht, elastisch | 20–30µm (mittelgroß) | Verhindert das Festkleben der Klinge und verringert die Reibung |
Folie & Aluminium | Dünn, formbar | 5–15µm (scharf-mittel) | Verhindert Kantenaufrollung und Materialverformung |
Blech | Hart, starr | 30–50µm (groß) | Verbessert die Haltbarkeit und verhindert das Absplittern der Klinge |
📌 Branchenbeispiel:
In der Verpackungsindustrie konnte durch den Wechsel von einer scharfkantigen Klinge (5 µm) zu einer Klinge mit einem Kantenradius von 15 µm beim Schneiden von Kunststofffolien die Reißrate um 20% gesenkt und die Produktionsgeschwindigkeit erhöht werden.
3.2 Schneidanwendung
Jeder Schneidvorgang erfordert ein ausgewogenes Verhältnis zwischen Schärfe und Haltbarkeit. Anwendungen mit hohen Geschwindigkeiten oder schweren Materialien profitieren von einer abgerundeten Kante, während Präzisionsschnitte einen feineren Kantenradius erfordern.
✔ Hochgeschwindigkeitsschneiden (z. B. Papier, Etiketten, Folie) → Ein moderater Kantenradius (10–20 µm) verhindert vorzeitigen Verschleiß und erhält gleichzeitig die Schärfe.
✔ Präzisionsschneiden (z. B. Elektronik, medizinische Materialien) → Ein feiner Kantenradius von 5–10 µm sorgt für saubere Schnitte ohne Grate.
✔ Schweres Schneiden (z. B. Gummi, dicker Kunststoff, Metallfolie) → Ein größerer Kantenradius von 20–50 µm verlängert die Lebensdauer der Klinge und reduziert Absplitterungen.
📌 Fallstudie:
Ein Metallverarbeitungsbetrieb stellte fest, dass sich die Lebensdauer der Klingen bei gleichbleibender Schnittpräzision verdoppelte, wenn der Kantenradius seiner Schneidklingen aus Wolframkarbid von 15 µm auf 35 µm vergrößert wurde.
3.3 Klingenmaterial und Beschichtungen
Das Klingenmaterial beeinflusst die Wahl des Kantenradius hinsichtlich Verschleißfestigkeit, Festigkeit und Wirtschaftlichkeit. Bestimmte Beschichtungen können zudem die Leistung verbessern und die Reibung verringern.
Klingenmaterial vs. Eignung des Kantenradius
Klingenmaterial | Härte (HRC) | Empfohlener Kantenradius | Beste Anwendungen |
Schnellarbeitsstahl (HSS) | 60–64 HRC | 10–30µm | Papier, dünne Kunststoffe, allgemeines Schneiden |
Wolframkarbid | 85–90 HRC | 20–50µm | Metal Schlitzen, dicker Gummi, Schleifmittel |
Keramikklingen | 90+ HRC | 5–15 µm | Hochpräzise Anwendungen (Medizin, Elektronik) |
Beschichtungen und ihre Vorteile:
✔ Titannitrid (TiN): Erhöht die Härte, verringert die Reibung und verlängert die Lebensdauer der Klinge.
✔ Diamantähnlicher Kohlenstoff (DLC): Bietet extrem niedrige Reibung und extreme Verschleißfestigkeit für Metall- und Hochgeschwindigkeitsschneiden.
✔Chromnitrid (CrN): Reduziert die Wärmeentwicklung bei Hochgeschwindigkeits-Schneideanwendungen.
📌 Effizienzeinblick:
Ein Hersteller von Verpackungsfolien konnte durch den Einsatz von DLC-beschichteten Klingen mit einem Kantenradius von 10 µm seinen Energieverbrauch um 12% senken und die Schneidpräzision verbessern.
3.4 Herstellerempfehlungen und Anpassungen
Die Wahl des richtigen Kantenradius erfordert oft eine fachkundige Beratung. Industrielle Hersteller wie Nanjing Metal Angebot maßgeschneiderte Lösungen, wodurch sichergestellt wird, dass jede Klinge für eine optimale Schneidleistung ausgelegt ist.
✔ Die individuelle Kantenprofilierung sorgt für das richtige Gleichgewicht zwischen Schärfe und Haltbarkeit.
✔ Fortschrittliche CNC-Schleiftechniken sorgen für gleichbleibende Kantenradiusgenauigkeit.
✔ Die Beratung durch Experten hilft, das beste Material, die beste Beschichtung und die beste Kantengeometrie für bestimmte Anwendungen zu bestimmen.
🔗 Kontakt Nanjing Metal für eine kostenlose Beratung zur Klingenauswahl!
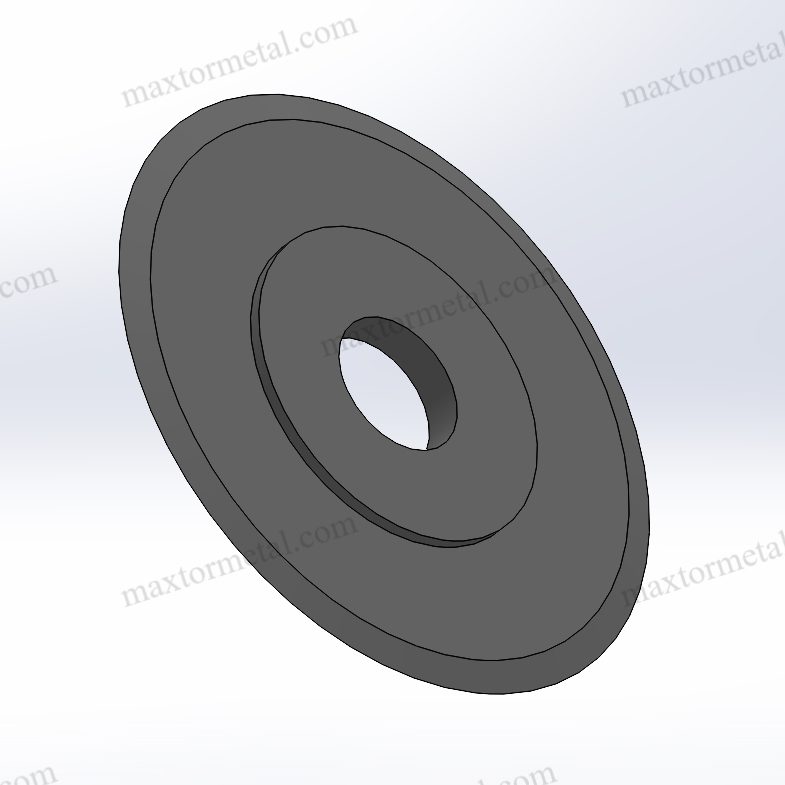
4. Best Practices der Branche
4.1 Fallstudien: Kantenradiusoptimierung in verschiedenen Branchen
Papier- und Druckindustrie
- Unternehmen, die Klingen mit einem Kantenradius von 15–20 µm verwenden, berichteten von einer Reduzierung der Klingenwechsel um 20% innerhalb von sechs Monaten.
- Die Staubentwicklung wurde um 18% verringert, wodurch die Effizienz der Druckerwalze verbessert wurde.
Kunststoff- und flexible Verpackungen
- Der Wechsel von scharfen Klingen (5 µm) zu leicht abgerundeten Klingen (10–15 µm) verbesserte die Schnittglätte und reduzierte fehlerhafte Verpackungen um 12%.
- Aufgrund der geringeren Reibung wurden Energieeinsparungen von 8% verzeichnet.
Metal Schneidindustrie
- Ein Kantenradius von 35 µm bei Klingen aus Wolframkarbid verlängert die Lebensdauer um 35% und reduziert so Wartungskosten und Ausfallzeiten.
- Die Zahl der Chipping-Vorfälle ging um 40% zurück, was zu einem sichereren Betrieb führte.
📌 Optimierungsergebnis:
Ein Papierhersteller wechselte zu präzisionsgeschliffenen Sägeblättern mit einem Kantenradius von 20 µm und sägte:
✔ Klingenlebensdauer um 25% verlängert
✔ Staubbelastung reduziert durch 18%
✔ Schnittqualitätsverbesserung durch 15%
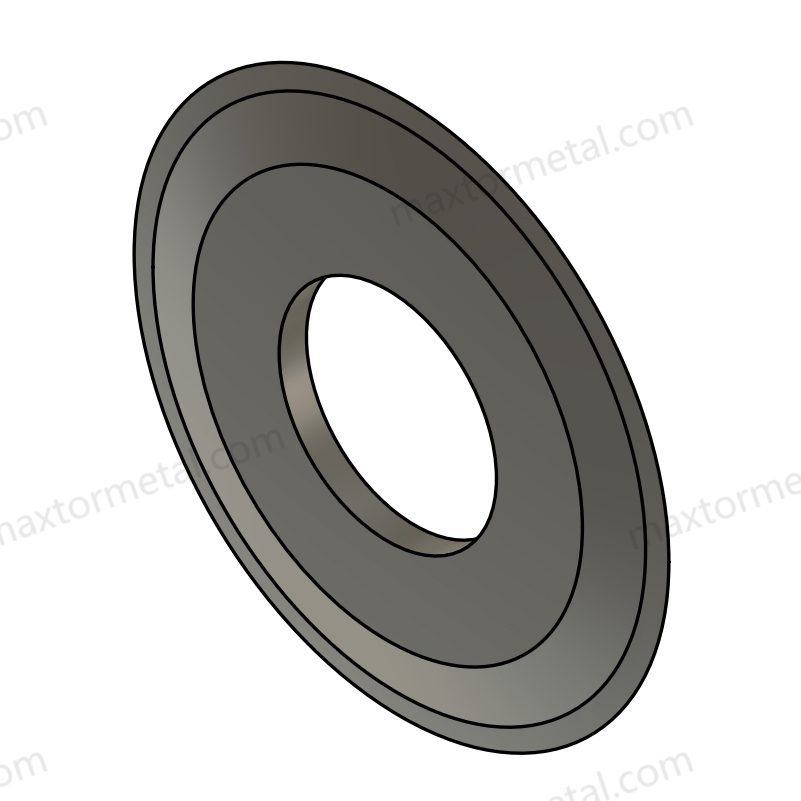
4.2 Optimierung der Rotorblatt- und Geräteintegration
Eine gut konstruierte Klinge ist nur ein Teil eines kompletten Schneidsystems. Um die Leistung zu maximieren, müssen die Parameter der Schneidemaschine mit den Klingenspezifikationen übereinstimmen.
Schlüsselfaktoren bei der Blade-Integration
✔ Stabilität des Klingenhalters: Sorgt für eine gleichmäßige Druckverteilung und verhindert eine Durchbiegung der Klinge.
✔ Spannungskontrolle: Durch die richtige Bahnspannung werden Materialverschiebungen und Kantenfehler verringert.
✔ Schnittwinkeleinstellungen: Durch die Feineinstellung des Klingeneintrittswinkels wird übermäßiger Verschleiß vermieden.
Maschineneinstellung | Auswirkungen auf die Leistung der Klinge |
Falsche Spannungseinstellungen | Verursacht vorzeitiges Abstumpfen der Klinge und ungleichmäßige Schnitte |
Hochgeschwindigkeitsschneiden ohne Kantenradiuseinstellung | Erhöht die Reibung und die Wärmeentwicklung |
Optimierte Schneidgeschwindigkeit + korrekter Kantenradius | Reduziert den Verschleiß, verbessert die Schnittqualität |
📌 Best Practice der Branche:
Eine Wellpappenverpackungsfabrik optimierte ihre Klingenhalter, ihr Spannungssystem und ihren Kantenradius (von 10 µm auf 20 µm) und erreichte dadurch:
✔ 40% längere Klingenlebensdauer
✔ 15% schnellere Schneidgeschwindigkeiten
✔ Geringere Betriebskosten durch reduzierte Ausfallzeiten
Der Kantenradius der Schneidklinge ist ein entscheidender Faktor für deren Haltbarkeit, Schnittqualität, Effizienz und Sicherheit. Ein gut gewählter Kantenradius verlängert die Lebensdauer der Klinge, verbessert die Präzision und senkt die Betriebskosten.
Für eine optimale Leistung ist die Auswahl des richtigen Kantenradius basierend auf Materialtyp, Anwendungsgeschwindigkeit und Klingenzusammensetzung von entscheidender Bedeutung. Nanjing Metal, mit über 18 Jahren Erfahrung in der industriellen Messerherstellung, bietet maßgeschneiderte Lösungen um Unternehmen bei der Optimierung ihrer Schneidprozesse zu unterstützen.
🔗 Kontaktieren Sie uns noch heute um Expertenempfehlungen und leistungsstarke industrielle Schlitzklingen auf Ihre Bedürfnisse zugeschnitten.