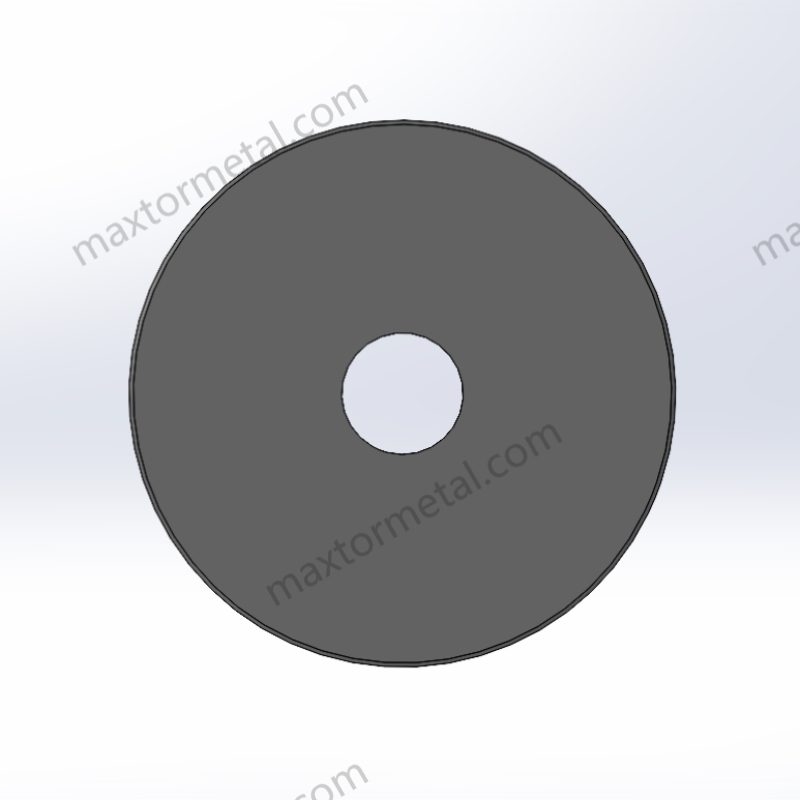
Da die Nachfrage nach Batterien aufgrund von Elektrofahrzeugen, erneuerbaren Energiespeichern und tragbarer Elektronik stark steigt, steht die Batterieindustrie zunehmend unter Druck, die Effizienz zu steigern und die Qualität aufrechtzuerhalten. Zu den entscheidenden Werkzeugen, die diesen Fortschritt ermöglichen, gehören Batterieschneideklingen. Diese präzisionsgefertigten Messer gewährleisten saubere, präzise und zuverlässige Schnitte in jeder Phase der Batterieproduktion.
Der globale Batteriemarkt wurde im Jahr 2022 auf 15 Billionen TP108 Milliarden geschätzt und soll bis 2030 voraussichtlich 15 Billionen TP310 Milliarden erreichen, was einer durchschnittlichen jährlichen Wachstumsrate (CAGR) von 15,81 Billionen TP4 zwischen 2023 und 2030 entspricht (Quelle: Industry Insights, 2023). Allein Elektrofahrzeuge dürften 60% dieser Nachfrage ausmachen, angetrieben durch globale Bemühungen zur Dekarbonisierung und staatliche Maßnahmen zur Förderung der Nutzung sauberer Energien.
Mit 18 Jahren Erfahrung, Nanjing Metal ist führend in der industriellen Rotorblattherstellung und liefert kundenspezifische Lösungen, die auf die besonderen Anforderungen der Batterieherstellung zugeschnitten sind.
Die zentrale Rolle von Schneidklingen bei der Batterieherstellung
Präzisionsschneiden für Schlüsselprozesse
Schneidklingen spielen eine entscheidende Rolle bei der Gewährleistung der Präzision in mehreren Phasen der Batterieproduktion, beispielsweise:
- Elektrodenschneiden: Saubere Schnitte wirken sich direkt auf die Effizienz elektrochemischer Reaktionen aus.
- Separator-Trimmen: Präzises Schneiden verhindert Materialschäden und erhält die Integrität des Separators.
- Schlitzen von Batterielaschen: Glatte Schnitte sorgen für nahtlose Verbindungen bei der Montage.
Jeder Schritt erfordert äußerst langlebige, scharfe Klingen, die enge Toleranzen einhalten können. Unterschiedliche Materialien wie Kupfer, Aluminium, Polyethylen und Polypropylen unterstreichen den Bedarf an maßgeschneiderten Lösungen zusätzlich.
Leistungsherausforderungen und -anforderungen
Die Batterieherstellung ist ein komplexer Prozess, der Schneidwerkzeuge erfordert, die:
- Behandeln Sie empfindliche Materialien, ohne Grate oder Risse zu verursachen.
- Behalten Sie die Schärfe über lange Produktionsläufe hinweg bei, um Ausfallzeiten zu minimieren.
- Halten Sie extremen Präzisionsanforderungen stand, oft im Mikrometerbereich.
Anwendungen von Schneidklingen in der Batterieproduktion
1. Elektrodenschneiden
Elektrodenmaterialien wie Kupfer- und Aluminiumfolien sind für die Batterieleistung von entscheidender Bedeutung, da sie beim Laden und Entladen den Strom effizient leiten. Diese Materialien sind typischerweise dünn (zwischen 0,1 und 0,3 mm), sodass präzises Schneiden für eine gleichmäßige Stromverteilung und optimale elektrochemische Leistung unerlässlich ist.
Wichtige Überlegungen:
- Klingenmaterialien:
- Hartmetall und Schnellarbeitsstahl (HSS) werden aufgrund ihrer hohen Härte und Verschleißfestigkeit häufig verwendet. Hartmetallklingen sind beispielsweise fünfmal härter als Stahl und gewährleisten so eine längere Werkzeugstandzeit auch bei der Massenproduktion.
- Schnellarbeitsstahl (HSS) Klingen sind kostengünstig und für die Bearbeitung weicherer Metalle geeignet. Sie werden häufig bei weniger anspruchsvollen Elektrodenschneidvorgängen verwendet.
- Beschichtungen:
- Titannitrid (TiN)und Titancarbonitrid (TiCN) Beschichtungen werden auf Klingen aufgetragen, um die Reibung zu verringern und die Verschleißfestigkeit zu erhöhen. Diese Beschichtungen erhöhen die Lebensdauer der Klinge um 30–40 % im Vergleich zu unbeschichteten Klingen. Insbesondere TiCN verhindert wirksam Materialanhaftung und sorgt dafür, dass Kupfer und Aluminium nicht an der Klinge haften bleiben, was zu saubereren Schnitten führt.
- Vorteile:
- Saubere Schnitte sind unerlässlich, um Abfall zu minimieren. So konnte beispielsweise ein Hersteller von Lithium-Ionen-Batterien durch den Einsatz hochwertiger Hartmetallklingen den Materialabfall bei der Elektrodenproduktion um 15% reduzieren, was zu erheblichen Kosteneinsparungen führte.
- Der Präzision der Schnitte sorgt für gleichmäßige Elektrodenschichten, was die Batterieleistung verbessert, indem interne Kurzschlüsse oder eine ungleichmäßige Stromverteilung verhindert werden.
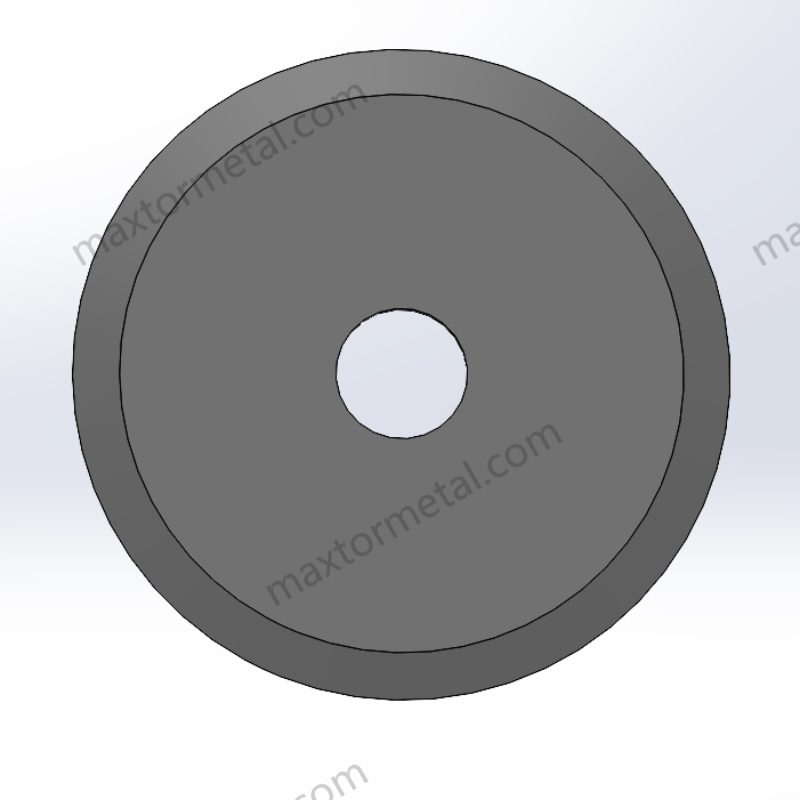
2. Trenner-Trimmen
Batterieseparatoren sind dünne, poröse Membranen, typischerweise aus Polypropylen (PP) oder Polyethylen (PE). Diese Materialien spielen eine wichtige Rolle bei der Vermeidung von Kurzschlüssen, indem sie Anode und Kathode physisch trennen. Der Separator darf keine Risse oder Unebenheiten aufweisen, da selbst kleinste Risse die Sicherheit und Leistung der Batterie beeinträchtigen können.
Wichtige Überlegungen:
- Klingendesign:
- Spezialkanten Verhindern Sie Schäden am Separatormaterial. Nanjing Metal-Klingen sind mit mikrofeinen Schneidkanten ausgestattet, die sicherstellen, dass selbst dünnste Separatoren (bis zu 20 Mikrometer) ohne Reißen oder Ausfransen geschnitten werden.
- Antistatische Beschichtungen werden zur Handhabung leichter und empfindlicher Materialien eingesetzt. Diese Beschichtungen sind besonders wichtig, um statische Entladungen zu verhindern, die das Separatormaterial beschädigen oder zu Verunreinigungen führen können.
- Vorteile:
- Durch das richtige Schneiden der Separatoren wird eine Ausbeute von 99% oder mehr in der Produktion sichergestellt und Fehler vermieden, die zu einer Schwellung der Batterie oder einem thermischen Durchgehen führen könnten.
- Da Separatoren direkt mit der Sicherheit und Leistung von Lithium-Ionen-Batterien verbunden sind, verbessert ein beschädigungsfreies Schneiden die Gesamtlebensdauer der Batterie. Die Lebensdauer eines gut geschnittenen Separators erhöht sich um 7-10%.
3. Batterielasche abschneiden
Batterielaschen, typischerweise aus Kupfer oder Aluminium, verbinden die internen Komponenten der Batterie mit dem externen Schaltkreis. Jeder Fehler beim Schneiden der Laschen kann zu einer schlechten Konnektivität führen, was sich letztendlich auf die Kapazität, Effizienz und Lebensdauer der Batterie auswirkt. Präzision beim Schneiden der Laschen ist daher von größter Bedeutung.
Wichtige Überlegungen:
- Blade-Funktionen:
- Benutzerdefinierte Abmessungen: Nanjing Metal-Sägeblätter sind auf bestimmte Laschengrößen zugeschnitten, oft mit einer Genauigkeit von bis zu 0,1 mm, wodurch eine präzise Ausrichtung und Passform gewährleistet wird.
- Kantengestaltung: Die Klingenkanten sind für saubere Schnitte optimiert, um Grate zu vermeiden, die die elektrische Leitfähigkeit der Batterie beeinträchtigen können.
- Ergebnisse:
- Eine hochpräzise Klinge kann Montagefehler um bis zu 20 % reduzieren. Sauber und gratfrei geschnittene Batterielaschen sorgen für eine bessere Haftung bei der Montage und erhöhen so die mechanische und elektrische Stabilität.
- Durch ordnungsgemäße Laschenschnitte wird außerdem die Lebensdauer der Batterie um 5-10% verbessert, da saubere elektrische Kontakte dazu beitragen, Leistungsverlust und -verschlechterung zu minimieren.
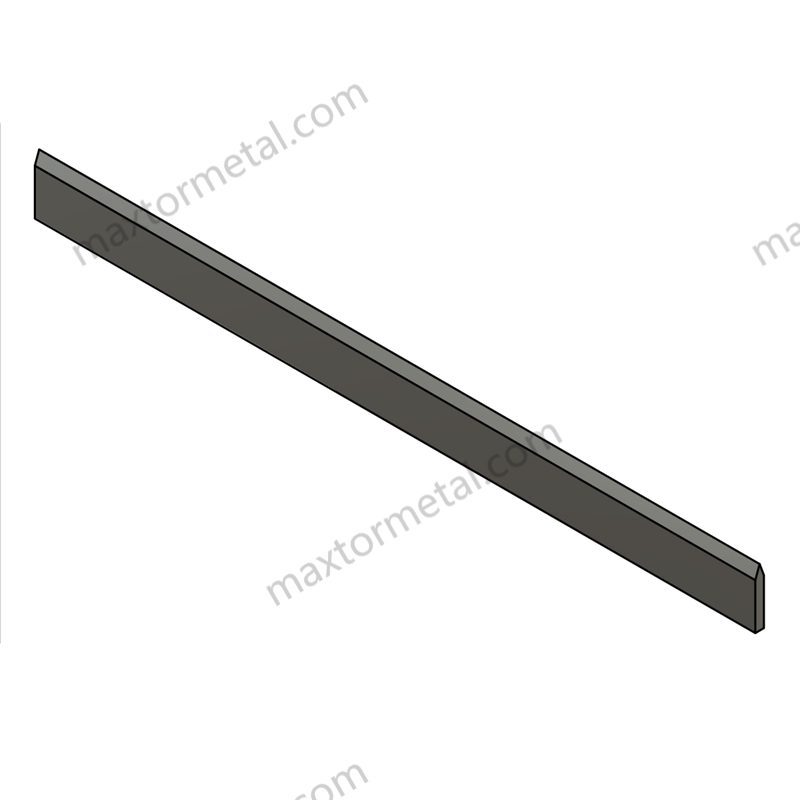
4. Endmontage und Verpackung
In der Endphase der Batterieproduktion werden Schneidklingen eingesetzt, um Gehäuse zuzuschneiden, überschüssiges Material zu entfernen und sicherzustellen, dass die Batteriekomponenten präzise in ihre Gehäuse passen. In dieser Phase müssen die Schneidklingen eine Vielzahl von Materialien, darunter Kunststoffe, Metalle und Verbundwerkstoffe, verarbeiten und dabei ein hohes Maß an Präzision gewährleisten.
Wichtige Überlegungen:
- Klingenmaterialien:
- Aufgrund seiner guten Haltbarkeit und Wirtschaftlichkeit wird Schnellarbeitsstahl zum allgemeinen Schneiden in Montage- und Verpackungsprozessen verwendet.
- Hartmetallklingen können zum Schneiden härterer Materialien oder bei hohen Produktionsmengen verwendet werden, da sie die Wartungskosten senken.
- Vorteile:
- Die Gewährleistung einer präzisen Verpackung und Montage ist entscheidend für die Batteriesicherheit und die Zuverlässigkeit des Endprodukts. Korrekte Gehäuseschnitte tragen dazu bei, die Anzahl der Nachproduktionsfehler zu reduzieren und so die Gesamtausbeute zu verbessern.
- Präzise Schnitte sorgen außerdem dafür, dass die Batterien fest in ihren Gehäusen sitzen und Schäden während des Transports und der Verwendung vermieden werden.
Auswahl des richtigen Klingenmaterials
Die Wahl des Klingenmaterials spielt eine entscheidende Rolle für die Qualität, Haltbarkeit und Wirtschaftlichkeit des Schneidprozesses. Nachfolgend finden Sie einen Vergleich gängiger Klingenmaterialien in der Batterieherstellung:
Material | Vorteile | Anwendungen |
Wolframkarbid | Außergewöhnliche Verschleißfestigkeit, hohe Härte, lange Lebensdauer | Elektrodenschneiden, Separatortrimmen |
Hochgeschwindigkeitsstahl | Vielseitig, kostengünstig, gute allgemeine Haltbarkeit | Universelles Schneiden, Laschenschneiden |
Keramik | Ultrascharfe Kanten, nicht magnetisch, korrosionsbeständig | Spezialschneiden, insbesondere für nichtmetallische Werkstoffe |
Beschichtungstechnologie:
- Titannitrid- (TiN) und Titancarbonitrid- (TiCN) Beschichtungen erhöhen die Lebensdauer der Klingen deutlich, reduzieren die Reibung und verhindern Materialanhaftungen. Untersuchungen haben gezeigt, dass diese Beschichtungen die Lebensdauer der Klingen um bis zu 40 % verlängern und die wartungsbedingten Ausfallzeiten um 30 % reduzieren können.
- TiCN ist besonders vorteilhaft für Hochgeschwindigkeitsschneidanwendungen und bietet überlegene Verschleißfestigkeit, selbst beim Schneiden schwer zu bearbeitender Materialien wie Aluminiumfolien.
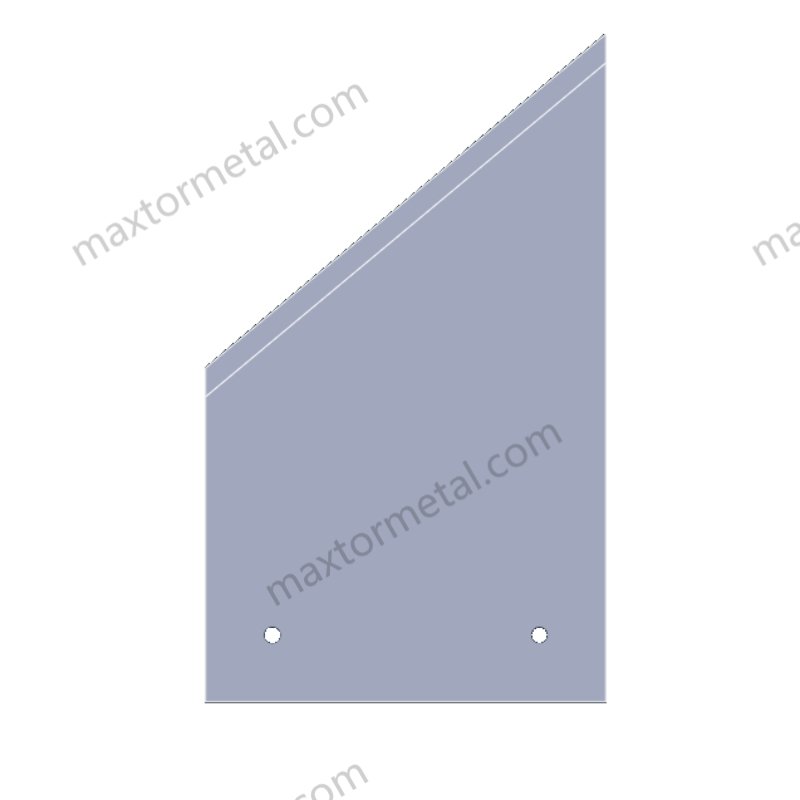
Vorteile von Kundenspezifische Klingen
In der Batterieherstellung gleicht keine Produktionslinie der anderen. Unterschiede bei Materialien, Maschinen und Produktionsvolumen erfordern maßgeschneiderte Schneidwerkzeuge, die den spezifischen Anforderungen gerecht werden. Während Standardklingen für manche Anwendungen ausreichen, bieten kundenspezifische Klingen Lösungen für komplexe, anspruchsvolle Szenarien und bieten verbesserte Präzision, Leistung und Kosteneffizienz.
Warum eine individuelle Anpassung wählen?
1. Entwickelt für einzigartige Materialeigenschaften und Abmessungen
Batteriekomponenten unterscheiden sich stark in Materialzusammensetzung und Dicke. Zum Beispiel:
- Elektroden: Kupfer- und Aluminiumfolien erfordern Klingen mit ultrascharfen Kanten, um ein Reißen der dünnen Folien (oft 0,1–0,3 mm dick) zu vermeiden.
- Trennzeichen: Membranen aus Polypropylen oder Polyethylen sind druckempfindlich und benötigen antistatische Beschichtungen, um Schäden zu vermeiden.
Eine maßgeschneiderte Klinge wird entwickelt, um diese materialspezifischen Anforderungen zu erfüllen. Dies gewährleistet:
- Konstante, gratfreie Schnitte, auch bei anspruchsvollen Materialien.
- Bessere Kompatibilität mit Produktionslinienmaschinen, wodurch Ausrichtungsprobleme reduziert werden.
2. Verbesserte Leistung in anspruchsvollen Umgebungen
Die Batterieherstellung erfordert oft Hochgeschwindigkeits- und Präzisionsprozesse. Standardklingen können schnell verschleißen oder enge Toleranzen nicht einhalten, was zu Produktionsengpässen führt. Maßgeschneiderte Klingen bieten:
- Haltbarkeit: Wolframkarbid- oder Keramikmaterialien sorgen für eine längere Lebensdauer.
- Präzision: Kundenspezifische Kantendesigns gewährleisten die Genauigkeit auch über längere Produktionsläufe hinweg.
3. Reduzierte Ausfallzeiten durch optimierte Haltbarkeit
Häufiger Klingenwechsel stört die Produktion und erhöht die Betriebskosten. Maßgeschneiderte Klingen sind für spezifische Schneidaufgaben optimiert und gewährleisten:
- Längere Intervalle zwischen den Austauschen.
- Weniger Maschineneinstellungen beim Klingenwechsel.
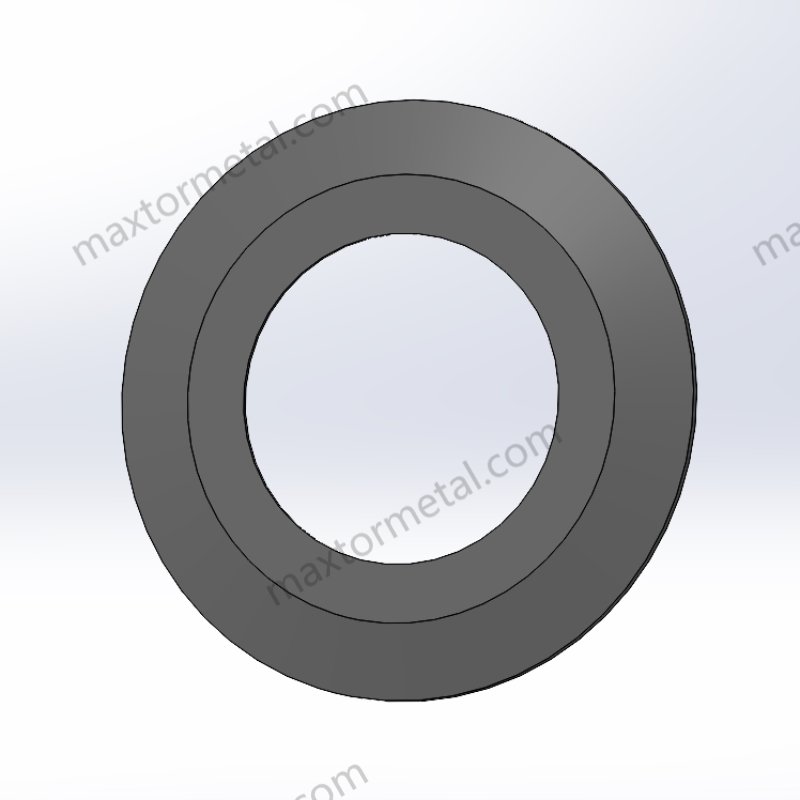
Wirtschaftliche Vorteile hochwertiger Schneidklingen
Die Investition in hochpräzise, langlebige Schneidklingen steigert nicht nur die Betriebseffizienz, sondern bietet auch messbare finanzielle Vorteile. Im Folgenden finden Sie wichtige Bereiche, in denen diese Klingen Kosteneinsparungen ermöglichen und die Produktionsergebnisse verbessern:
1. Erhöhte Produktivität
Hochwertige Sägeblätter bleiben länger scharf und präzise, ermöglichen höhere Schnittgeschwindigkeiten und kürzere Zykluszeiten. Beispielsweise ermöglichen Wolframkarbid-Sägeblätter mit TiCN-Beschichtung ununterbrochenes Schneiden mit 10.000 Schnitten pro Stunde und eignen sich daher ideal für Produktionslinien mit hohem Durchsatz.
Dateneinblick:
- Ein Batteriehersteller meldete eine Verkürzung der Zykluszeit um 20% nach der Umstellung auf präzisionsgefertigte Klingen, was zu einer zusätzlichen Produktion von 15.000 Einheiten pro Monat führte.
- Eine verbesserte Schnittgeschwindigkeit kann je nach Komplexität des Schneidprozesses zu einer Steigerung des Produktionsdurchsatzes um 15–25% beitragen.
2. Reduzierter Materialabfall
Präzisionsschneiden minimiert Grate, Schnittfehler und Materialverformungen, die bei minderwertigen Klingen häufig auftreten. Dies ist besonders wichtig beim Schneiden dünner Elektroden (0,1–0,3 mm dick) und Separatoren (bis zu 20 Mikrometer).
Branchenbeispiel:
Eine Lithium-Ionen-Batteriefabrik, die jährlich 500.000 Batterien produziert, reduzierte den Materialabfall von 51 TP4T auf 21 TP4T und sparte dadurch rund 1.500 km Separatormaterial ein. Bei durchschnittlichen Separatorkosten von 1 TP5T10 pro Meter entspricht dies einer jährlichen Einsparung von 1 TP5T150.000.
3. Geringere Wartungskosten
Langlebige Klingen müssen seltener ausgetauscht werden und minimieren Produktionsunterbrechungen durch Klingenwechsel oder Reparaturen. Beispielsweise haben Klingen aus Wolframkarbid eine bis zu dreimal längere Lebensdauer als herkömmliche Stahlklingen, was die Austauschhäufigkeit deutlich reduziert.
Dateneinblick:
- Ein Hersteller konnte durch den Einsatz maßgeschneiderter, langlebiger Rotorblätter seine Ausfallzeiten um 501 Tsd. Tonnen (von 20 auf 10 Stunden pro Monat) reduzieren. Dies führte zu einer jährlichen Produktivitätssteigerung von 180.000 Tsd. Tonnen, gemessen am Produktionswert der Produktionslinie.
4. Kapitalrendite (ROI)
Metrisch | Standardklingen | Hochwertige Klingen | Finanzielle Auswirkungen |
Klingenlebensdauer | 3 Monate | 9 Monate | Reduzierte Ersatzteilkosten |
Ausfallzeit (monatlich) | 20 Stunden | 10 Stunden | Produktionssteigerung: $80.000/Jahr |
Materialabfall | 5% insgesamt | 2% insgesamt | Einsparungen: $150.000/Jahr |
Wartungskosten (jährlich) | $30,000 | $15,000 | Einsparungen: $15.000/Jahr |
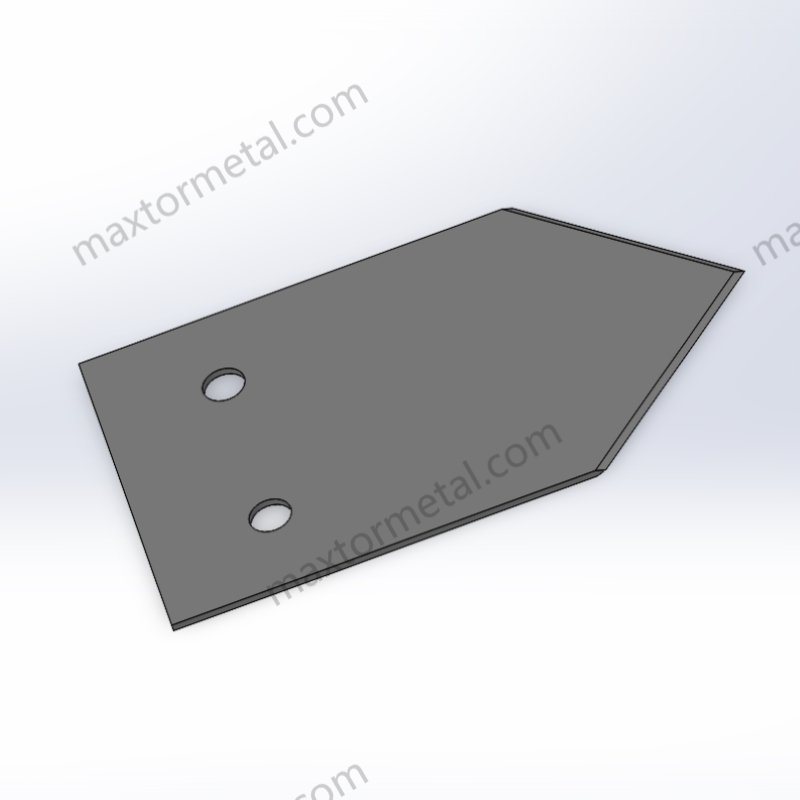
Zukünftige Trends und Herausforderungen
Die Batterieindustrie entwickelt sich rasant, angetrieben durch technologische Fortschritte und Marktanforderungen. Die Schneidklingentechnologie muss mit diesen neuen Herausforderungen Schritt halten.
1. Neue Herausforderungen
- Festkörperbatterien:
- Für Feststoffbatterien werden Schneidwerkzeuge benötigt, die Keramik- und Festelektrolytmaterialien verarbeiten können. Diese Materialien sind härter und spröder als herkömmliche Komponenten von Lithium-Ionen-Batterien.
- Klingen aus ultraharten Materialien wie Diamantkanten oder keramikbeschichteten Oberflächen sind unerlässlich.
- Batterie-Recycling:
- Da die Regierungen strengere Recyclingvorschriften erlassen, wird die Nachfrage nach Klingen, mit denen sich Altbatterien präzise zerlegen lassen, steigen.
- Diese Klingen müssen gemischte Materialien wie Metalle, Kunststoffe und Klebstoffe durchschneiden, ohne die Recyclingfähigkeit zu beeinträchtigen.
Datenpunkt: Der Markt für recycelte Batterien soll von 10,5 Milliarden TP5B im Jahr 2022 auf 127 Milliarden TP5B im Jahr 2030 wachsen, wobei Schneidtechnologien eine entscheidende Rolle bei der effizienten Materialrückgewinnung spielen (Quelle: Energy Storage Journal, 2023).
2. Innovationen bei Schneidklingen
- Intelligente Klingen:
- In Schneidklingen integrierte fortschrittliche Sensoren liefern Echtzeit-Feedback zu Klingenleistung, Verschleiß und Schneidbedingungen.
- Diese Daten ermöglichen eine vorausschauende Wartung, reduzieren ungeplante Ausfallzeiten um 20–30% und gewährleisten eine gleichbleibende Schnittqualität.
Beispiel: Ein Pilotprogramm mit der Integration von mit Sensoren ausgestatteten Klingen reduzierte die Ausfallzeit einer Separator-Schneidelinie um 25 Stunden pro Monat und sparte so jährlich schätzungsweise $100.000 Betriebskosten.
- Umweltfreundliche Materialien:
- Hersteller von Rotorblättern erforschen recycelbare und nachhaltige Materialien, um ihre Umwelt-, Sozial- und Governance-Ziele (ESG) zu erreichen.
- Beispielsweise kann die Verwendung biologisch abbaubarer Beschichtungen oder Materialien mit einem geringeren CO2-Fußabdruck das Nachhaltigkeitsprofil eines Unternehmens verbessern.
Ein typisches Beispiel: Ein europäischer Hersteller hat umweltfreundliche Hartmetallklingen eingeführt und konnte seine CO2-Emissionen während der Produktion um 10% reduzieren, wodurch er seine ESG-Konformität verbesserte.
Schlussfolgerung
Schneidklingen sind bei der Batterieherstellung unverzichtbar, da sie Präzision, Effizienz und Qualität gewährleisten. Nanjing Metal bringt unübertroffene Expertise mit und bietet maßgeschneiderte Lösungen auf Basis von 18 Jahren Erfahrung. Unser Engagement für Qualität und Innovation macht uns zu einem vertrauenswürdigen Partner der Branche.
Sind Sie bereit, Ihre Batterieproduktion zu optimieren? Kontaktieren Sie uns noch heute für individuelle Schneidklingenlösungen, die auf Ihre Bedürfnisse zugeschnitten sind.