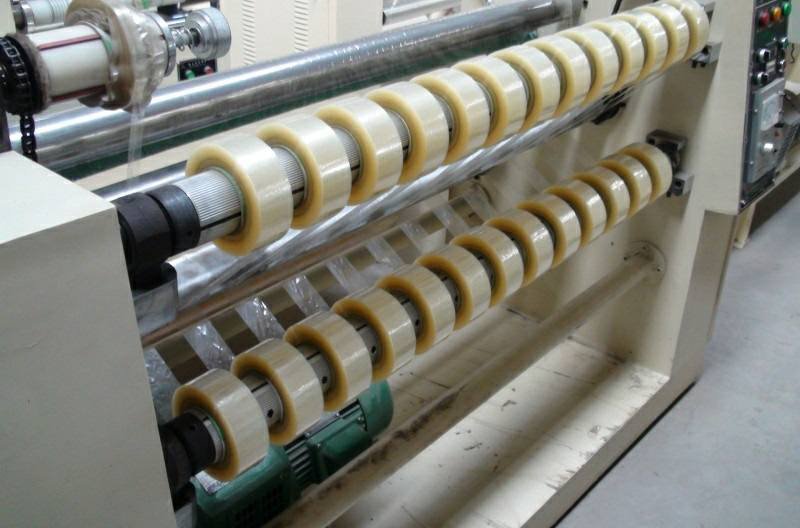
Das Schneiden von klebrigen Materialien wie Klebebändern, Schaumstoffen und Klebstoffen ist in vielen Branchen eine häufige Herausforderung. Diese Materialien können unglaublich schwierig zu handhaben sein, da sie dazu neigen, an Oberflächen zu haften, was zu erhöhtem Verschleiß der Schneidklingen führt. Dieses Problem beeinträchtigt nicht nur die Leistung der Klinge, sondern erhöht auch die Betriebskosten und Ausfallzeiten aufgrund des häufigen Klingenwechsels. In diesem Artikel untersuchen wir, warum das Schneiden von klebrigen Materialien Klingen beschädigt, und bieten effektive Schneidlösungen, um die Lebensdauer Ihrer Werkzeuge zu verlängern und gleichzeitig die Schneideffizienz zu verbessern.
Das Problem verstehen: Wie klebrige Materialien die Klingen beschädigen
Klebrige Materialien stellen beim Schneiden besondere Herausforderungen dar. Im Gegensatz zu Standardmaterialien erzeugen Klebstoffe und Leime zusätzliche Reibung und neigen dazu, an der Oberfläche der Klinge zu haften, was zu schnellerem Verschleiß führt. Aber was genau passiert beim Schneidvorgang? Lassen Sie es uns aufschlüsseln:
1. Physische Schäden an der Klinge
Beim Schneiden klebriger Materialien ist die Klinge starkem Druck und Reibung ausgesetzt. Wenn klebrige Substanzen mit der Schneide in Kontakt kommen, kann die Klinge schnell ihre Schärfe verlieren. Mit der Zeit führt diese Reibung zur physischen Abnutzung der Klingenkante, was zu Absplitterungen, Rissen oder sogar völliger Stumpfheit führen kann.
2. Haftung auf der Klingenoberfläche
Eines der häufigsten Probleme beim Schneiden klebriger Materialien sind Klebstoffrückstände auf der Klinge. Da das Klebstoffmaterial an der Oberfläche der Klinge haftet, beeinträchtigt es die Schneide und verringert die Fähigkeit, präzise Schnitte zu erzielen. Diese Ablagerungen müssen häufig gereinigt werden und können, wenn sie nicht beseitigt werden, sowohl die Schnittqualität als auch die Klingenleistung beeinträchtigen.
3. Reduzierte Schneideffizienz und Genauigkeit
Wenn Klingen abgenutzt sind oder sich mit Klebstoffrückständen verfangen, lässt ihre Schnittpräzision nach. Dies kann zu ungleichmäßigen Schnitten führen, die wiederum Probleme beim Endprodukt verursachen können, wie z. B. schlechte Verarbeitung oder Ausschuss. Der Verlust an Schnittpräzision erhöht die Ausfallzeiten, da die Bediener die Klinge entweder häufig reinigen oder vorzeitig austauschen müssen.
4. Erhöhte Betriebskosten
Häufiger Klingenwechsel und zusätzliche Wartungsarbeiten zum Entfernen klebriger Rückstände tragen zu höheren Betriebskosten bei. Diese wiederkehrenden Ausgaben können sich schnell summieren und die Rentabilität von Unternehmen beeinträchtigen, die regelmäßig klebrige Materialien schneiden.
Durch frühzeitiges Angehen dieser Probleme mit geeigneten Schneidlösungen können Hersteller den Verschleiß deutlich reduzieren, die Effizienz verbessern und ihre langfristigen Betriebskosten senken. Lesen Sie weiter, um herauszufinden, wie Sie Ihre Klingen schützen und Ihre Schneidprozesse optimieren können.
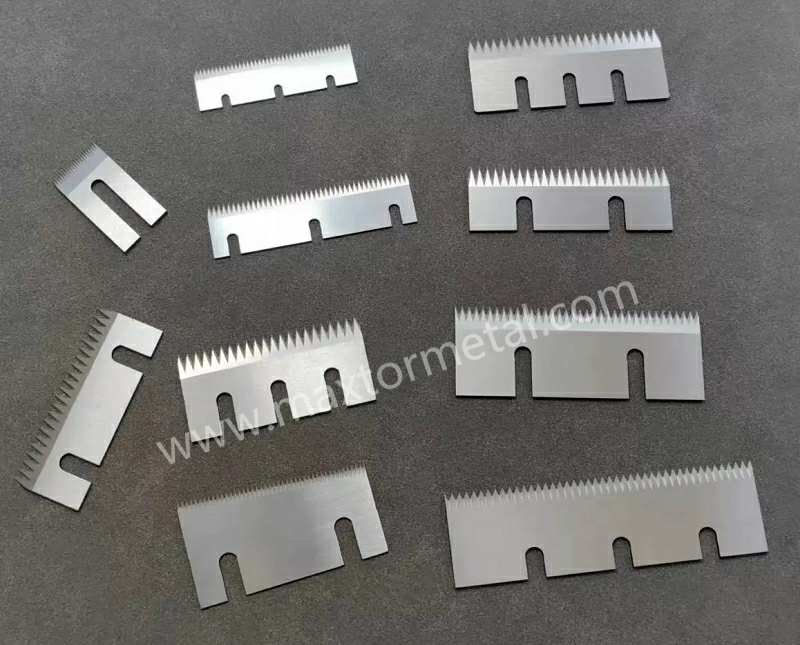
Effektive Schneidlösungen: So schützen Sie Ihre Klingen vor Beschädigungen
Es gibt verschiedene Schneidlösungen, die Ihre Klingen vor den schädlichen Auswirkungen des Schneidens klebriger Materialien schützen können. Lassen Sie uns diese Strategien genauer untersuchen:
1. Auswahl des richtigen Klingenmaterials und -designs
Beim Schneiden klebriger Substanzen ist die Auswahl des richtigen Klingenmaterials von entscheidender Bedeutung, da es direkten Einfluss auf die Haltbarkeit, Schnittpräzision und Verschleißfestigkeit der Klinge hat.
- Auswahl des Klingenmaterials
Beim Schneiden klebriger Materialien benötigen Sie ein Klingenmaterial, das der bei diesen Anwendungen üblichen hohen Reibung und Klebstoffablagerung standhält. Kohlenstoffstahl, Wolframkarbid und Keramik sind allesamt brauchbare Optionen, aber jede hat ihre eigenen Stärken und Schwächen.- Kohlenstoffstahl Klingen
Diese sind in der Regel weniger teuer und bieten eine gute Gesamtleistung für mittelschweres Schneiden. Kohlenstoffstahl ist für seine Zähigkeit und Verschleißfestigkeit bekannt. Beispielsweise kann er unter normalen Bedingungen bis zu 30% länger halten als Standardklingen aus Kohlenstoffstahl. Beim Schneiden besonders klebriger Materialien kann er jedoch aufgrund der höheren Reibung schneller stumpf werden. Wolframkarbidklingen
Wolframkarbid ist eines der härtesten Materialien, die in Schneidklingen verwendet werden, und seine Verschleißfestigkeit ist außergewöhnlich. Untersuchungen zeigen, dass Wolframkarbidklingen bis zu dreimal länger als Klingen aus Kohlenstoffstahl in Umgebungen mit klebrigen Materialien. Dies gilt insbesondere beim Schneiden von Substanzen wie Klebstoffen oder gummibasierten Materialien, die eine hohe Reibung erzeugen. Allerdings sind sie mit höheren Anschaffungskosten verbunden.
- Keramikklingen
Keramikklingen sind besonders hitze- und verschleißfest, im Vergleich zu Metallklingen jedoch spröder. Diese Klingen eignen sich für bestimmte Schneidarbeiten mit klebrigen Materialien, insbesondere wenn eine hohe Präzision erforderlich ist. Keramikklingen bleiben in der Regel länger scharf, neigen jedoch dazu, bei starken Stößen zu brechen.
- Kohlenstoffstahl Klingen
- Überlegungen zum Klingendesign
Das Design der Klinge spielt beim Schneidvorgang eine wichtige Rolle. Faktoren wie Zahngeometrie, Schneidkantenwinkel und Beschichtungen können die Effizienz der Klinge verbessern, insbesondere bei klebrigen Materialien. Zum Beispiel:- Gezackte Klingen: Sägeblätter mit Zacken oder Zähnen erzeugen eine Sägebewegung, die dazu beiträgt, die Kontaktfläche zwischen Sägeblatt und Material zu verringern. Dadurch wird die Gefahr einer Klebstoffansammlung an der Schneide minimiert.
- Glatte Klingen: Glattkantige Klingen, die oft mit speziellen Materialien beschichtet sind, können die Reibung zwischen der Klinge und klebrigen Oberflächen verringern und so verhindern, dass Klebstoff überhaupt erst haften bleibt. Dieses Design hilft auch beim sanfteren Schneiden von Materialien wie Gummi oder Schaumstoff, bei denen häufig Klebstoffe verwendet werden.
2. Optimale Schnittparameter: Geschwindigkeit, Druck und Winkel
Durch die richtigen Schneidparameter können Sie die Lebensdauer Ihrer Klingen verlängern und gleichzeitig die Schneideffizienz optimieren.
- Schnittgeschwindigkeit
Geschwindigkeit ist einer der einflussreichsten Faktoren beim Schneiden klebriger Materialien. Untersuchungen legen nahe, dass bei hoher Geschwindigkeit der Klingen die Wärmeentwicklung zunimmt, was dazu führen kann, dass die Klinge durch Überhitzung schneller stumpf wird. Umgekehrt erhöht zu langsames Schneiden die Reibung, was zu mehr Materialablagerungen führt. Studien zeigen, dass eine optimale Schnittgeschwindigkeit sein sollte 20-30% langsamer als die Geschwindigkeit zum Schneiden trockener, nicht klebender Materialien, abhängig von der Dicke und Art des Materials. - Schnittdruck
Bei zu hohem Druck kann die Klinge in das Material gedrückt werden, was zu erhöhter Reibung und schnellerem Klingenverschleiß führt. Dies ist besonders beim Schneiden klebriger Materialien nachteilig, da der zusätzliche Druck dazu führt, dass Klebstoff an der Klinge haften bleibt. Daten von Klingentestunternehmen zeigen, dass eine Reduzierung des Schneiddrucks um nur 10 % die Lebensdauer der Klinge in einigen Fällen um bis zu 15–20 % verlängern kann. - Schnittwinkel
Der Schnittwinkel beeinflusst, wie die Klinge mit dem Material interagiert. Ein spitzerer Winkel kann zu schnellerem Schneiden führen, erhöht aber auch den Verschleiß, insbesondere bei klebrigen Materialien. Ein Schnittwinkel von 45° wird häufig zum Schneiden klebriger Materialien empfohlen, da er die Schneidleistung mit minimaler Klingenbelastung in Einklang bringt.
3. Regelmäßige Wartung und Reinigung
Klingen, die zum Schneiden klebriger Materialien verwendet werden, erfordern mehr Wartung als Klingen, die für nicht klebende Materialien verwendet werden. Hier ist der Grund:
- Klingenreinigung
Nach dem Schneiden klebriger Materialien bleiben oft Rückstände an der Klinge haften. Dies kann ein erhebliches Problem darstellen, da die Ansammlung klebriger Substanzen die Effizienz der Klinge beeinträchtigen kann. Die Verwendung von Reinigungsmitteln, die speziell für Klebstoffrückstände entwickelt wurden, ist entscheidend. Zu den üblichen Reinigungsmitteln gehören Aceton und Isopropylalkohol, die Klebstoffe effektiv auflösen, ohne die Klinge zu beschädigen. Es ist wichtig, die Klinge sofort nach dem Gebrauch zu reinigen, um verhärtete Rückstände zu vermeiden, die später schwerer zu entfernen sind.- Dateneinblick: Das Reinigen der Klingen nach jedem Gebrauch kann die Lebensdauer der Klinge im Vergleich zu Klingen, die nicht regelmäßig gereinigt werden, um bis zu 50% verlängern, insbesondere beim Schneiden von Klebstoffen wie Leim oder Klebeband.
- Geplante Rotorblattinspektionen
Durch die Überprüfung der Klingen nach jedem Schaltvorgang oder Schneidzyklus können Sie Anzeichen von Verschleiß frühzeitig erkennen. Achten Sie auf:- Kanten stumpf machenHinweis: Wenn sich die Schneide merklich stumpf oder rau anfühlt, ist es Zeit zum Schärfen oder Austauschen.
- Rückstandsbildung: Wenn sich sichtbare Rückstände auf der Klinge befinden, kann dies zu ungleichmäßigen Schnitten und möglicherweise zu weiteren Schäden führen.
- Verschleißmuster: Ungleichmäßiger Verschleiß kann auf Probleme mit dem Schnittdruck oder der Schnittgeschwindigkeit hinweisen, die angepasst werden sollten.
Durch frühzeitiges Erkennen von Verschleiß können schwerwiegendere Schäden verhindert und so Ausfallzeiten sowie die Notwendigkeit häufigerer Klingenwechsel reduziert werden.
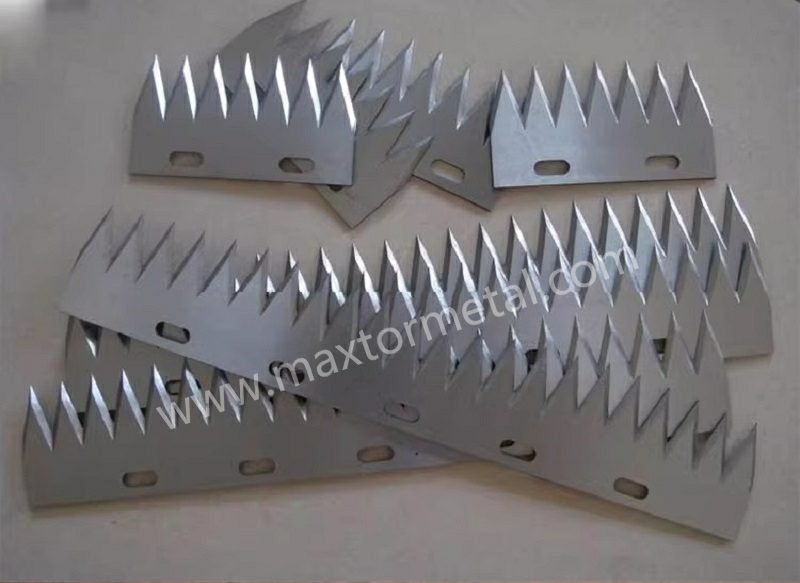
4. Fortschrittliche Klingenbeschichtungen: Schützen Sie Ihre Klingen mit Technologie
Das Schneiden klebriger Materialien stellt besondere Herausforderungen dar, insbesondere wenn es darum geht, Materialablagerungen und Klingenschäden zu verhindern. Eine der effektivsten Methoden zur Bewältigung dieser Herausforderungen ist die Verwendung moderner Klingenbeschichtungen. Lassen Sie uns untersuchen, wie diese Beschichtungen funktionieren, welche Vorteile sie bieten und welche verschiedenen Arten erhältlich sind.
4.1 Klingenbeschichtungen: Was sie bewirken
Klingenbeschichtungen dienen als Schutzschicht, die die Leistung und Lebensdauer der Klinge beim Schneiden klebriger Materialien verbessert. Sie erreichen dies, indem sie die Reibung verringern und Materialanhaftung verhindern. Beides ist entscheidend für die Aufrechterhaltung der Schneidleistung und Klingenschärfe.
Verbesserte Härte und Verschleißfestigkeit
Die Hauptfunktion von Klingenbeschichtungen besteht darin, die Oberflächenhärte der Klinge zu erhöhen. Eine härtere Oberfläche minimiert den Verschleiß, was besonders wichtig ist, wenn durch Materialien geschnitten wird, die übermäßige Reibung oder abrasiven Kontakt verursachen können. Die Beschichtung hilft der Klinge, der Ansammlung klebriger Rückstände zu widerstehen, die sonst ihre Schärfe beeinträchtigen können.
Vermeidung von Materialanhaftungen
Klebrige Materialien wie Klebstoffe, Bänder und Schaumstoffe bleiben bekanntermaßen an Schneidklingen haften. Diese Haftung kann die Schneidleistung erheblich verringern, was zu Klingenschäden oder häufigerem Reinigen führen kann. Beschichtungen wirken als Barriere und verhindern, dass diese Materialien direkt an der Klingenoberfläche haften bleiben. Dadurch wird die Wartungshäufigkeit verringert.
Hier ist eine visuelle Darstellung, wie Beschichtungen die Reibung verringern und die Schneidleistung verbessern:
Materialtyp | Ohne Beschichtung | Mit Beschichtung |
Reibung | Hoch | Niedrig |
Adhäsionsbildung | Bedeutsam | Minimal |
Verschleißrate | Hoch | Niedrig |
Schneideffizienz | Reduziert | Erweitert |
4.2 Vorteile von Klingenbeschichtungen
Beschichtete Klingen bieten eine Reihe von Vorteilen, die sich direkt auf die Wirtschaftlichkeit und Produktivität von Schneidvorgängen auswirken. Hier sind einige der wichtigsten Vorteile:
Verlängerte Klingenlebensdauer
Beschichtungen reduzieren den Verschleiß von Klingen erheblich und verlängern so ihre Lebensdauer. Dies ist besonders wichtig in Branchen, in denen häufig klebrige Materialien geschnitten werden. Studien haben beispielsweise gezeigt, dass beschichtete Klingen beim Schneiden von stark klebenden Materialien wie Bändern oder Klebstoffen zwei- bis dreimal länger halten als unbeschichtete Klingen.
Reduzierte Wartungskosten
Wenn eine Klinge beschichtet ist, muss sie weniger häufig gewartet werden. Ohne die Ansammlung klebriger Rückstände bleibt die Klinge länger sauber und die Notwendigkeit des Nachschärfens oder Ersetzens wird minimiert. Untersuchungen zeigen, dass Unternehmen ihre Wartungskosten durch den Einsatz beschichteter Klingen um bis zu 30 % bis 50 % senken können, insbesondere in Schneidumgebungen mit hohem Volumen.
Verbesserte Schnittgenauigkeit
Beschichtungen helfen auch, die Schärfe der Klinge zu erhalten und sorgen so für präzise Schnitte. Dies ist in Branchen wie der Verpackungs- oder Fertigungsindustrie, in denen hohe Präzision erforderlich ist, von entscheidender Bedeutung. Eine Klinge mit einer Schutzbeschichtung kann die Häufigkeit des Abstumpfens verringern, sodass der Schneidvorgang seine hohen Standards hinsichtlich Genauigkeit und Konsistenz beibehalten kann.
Verbesserte Schneidleistung
Klingenbeschichtungen verringern die Reibung zwischen Klinge und Material, was weniger Widerstand während des Schneidvorgangs bedeutet. Dies führt zu einem sanfteren Schneiden, einer geringeren Wärmeentwicklung und weniger Schäden an Klinge und Schneidmaterial. Dies wiederum kann das Risiko minderwertiger Schnitte verringern, wodurch die Gesamtleistung verbessert und Materialabfall reduziert wird.
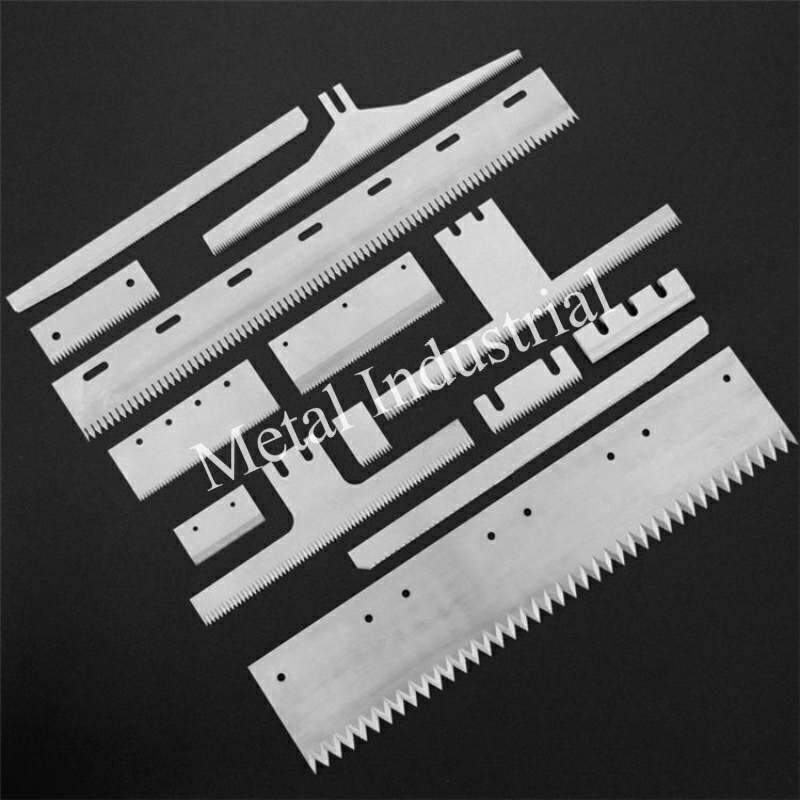
4.3 Arten von Klingenbeschichtungen und ihre Eigenschaften
Es sind verschiedene Beschichtungsarten erhältlich, jede mit spezifischen Eigenschaften, die für verschiedene Schneidaufgaben geeignet sind. Im Folgenden gehen wir näher auf die Beschichtungsarten ein, die üblicherweise zum Schneiden klebriger Materialien verwendet werden, und heben ihre Stärken und idealen Anwendungen hervor.
Nanobeschichtungen
- Merkmale: Nanobeschichtungen bestehen aus ultrafeinen Partikeln, die sich an die Klingenoberfläche binden und für hervorragende Härte und Verschleißfestigkeit sorgen. Diese Beschichtungen verbessern die Abrieb- und Korrosionsbeständigkeit der Klinge, die beim Schneiden klebriger Materialien häufig auftreten. Nanobeschichtungen verbessern auch die Leistung der Klinge in Umgebungen mit hohen Temperaturen, da sie Hitze besser standhalten als andere Beschichtungen.
- Vorteile: Die feinen Partikel in Nanobeschichtungen sorgen für eine glattere Klingenoberfläche, wodurch verhindert wird, dass klebrige Materialien an der Klinge haften bleiben. Die verbesserte Oberflächenhärte erhöht die Lebensdauer der Klinge und Nanobeschichtungen reduzieren die Häufigkeit der Klingenreinigung.
- Anwendungen: Nanobeschichtungen werden häufig in Branchen eingesetzt, in denen hohe Präzision und Haltbarkeit erforderlich sind, wie etwa in der Elektronik-, Automobil- und Medizinbranche. Sie sind besonders effektiv beim Schneiden hochviskoser Materialien wie Industrieklebstoffen, Schmelzklebern oder Materialien auf Gummibasis.
- Branchendaten: Laut einer Studie der Zeitschrift für FertigungsprozesseBei Tests mit klebrigen Materialien schnitten nanobeschichtete Klingen besser ab als unbeschichtete Klingen und zeigten bei über 100 Stunden Schneidebetrieb eine um bis zu 50 % geringere Abnutzung.
Harte Beschichtungen (TiN, TiC, TiAlN)
- Merkmale: Hartbeschichtungen wie Titannitrid (TiN), Titancarbonitrid (TiC) und Titanaluminiumnitrid (TiAlN) sind für ihre außergewöhnliche Härte bekannt, die den Verschleiß durch klebrige und abrasive Materialien verringert. Diese Beschichtungen bieten außerdem eine hervorragende Hitzebeständigkeit, die beim Schneiden von Materialien, die viel Reibung und Hitze erzeugen, von entscheidender Bedeutung ist.
- Vorteile: Diese Beschichtungen tragen dazu bei, den Reibungskoeffizienten zwischen der Klinge und dem zu schneidenden Material zu senken, wodurch verhindert wird, dass Klebstoffe an der Klingenoberfläche haften bleiben. Darüber hinaus halten sie hohen Schnittgeschwindigkeiten und Temperaturen stand und sind daher ideal für industrielle Anwendungen.
- Anwendungen: Hartbeschichtungen werden in vielen Branchen eingesetzt, darunter in der Metallverarbeitung, Verpackung und Automobilherstellung. Sie sind besonders wirksam in Umgebungen, in denen hohe Schneidkräfte angewendet werden, wie etwa beim Schneiden durch dicke, klebrige Klebstoffe oder Gummimischungen.
- Brancheneinblick: Titannitrid-Beschichtungen (TiN) reduzieren den Klingenverschleiß in Hochdruckschneidumgebungen nachweislich um bis zu 60 % im Vergleich zu unbeschichteten Klingen. Diese Beschichtungen verbessern auch die Schnittgeschwindigkeit, indem sie die Reibungskräfte auf der Klinge verringern.
Nitridbeschichtungen (TiN, AlN)
- Merkmale: Nitridbeschichtungen wie Titannitrid (TiN) und Aluminiumnitrid (AlN) bieten eine hervorragende Korrosionsbeständigkeit. Dies macht sie ideal zum Schneiden in Umgebungen mit hoher Luftfeuchtigkeit oder Kontakt mit Chemikalien. Nitridbeschichtungen sind besonders wirksam bei der Verhinderung von Rost und Korrosion, die die Leistung der Klinge mit der Zeit beeinträchtigen können.
- Vorteile: Nitridbeschichtungen schützen Klingen vor Korrosion durch klebrige Materialien, die Wasser oder Lösungsmittel enthalten können. Darüber hinaus beugt die Beschichtung Verschleiß vor, sodass die Klingen auch in korrosiven Umgebungen länger halten.
- Anwendungen: Diese Beschichtungen werden häufig in Branchen wie der Lebensmittelverarbeitung, der Pharmaindustrie und der Herstellung medizinischer Geräte verwendet, wo Feuchtigkeit und Kontakt mit Chemikalien häufig sind. Sie sind besonders wirksam bei Anwendungen, bei denen in nassen oder feuchten Umgebungen geschnitten werden muss.
- Beispiel: Bei der Lebensmittelverarbeitung, wo klebrige Substanzen wie Sirup und Soßen vorherrschen, hat sich gezeigt, dass TiN-Beschichtungen die Lebensdauer der Klinge im Vergleich zu unbeschichteten Klingen um bis zu 50% verlängern, wodurch die Ausfallzeiten erheblich reduziert und die Produktivität gesteigert werden.
Polymerbeschichtungen
- Merkmale: Polymerbeschichtungen wie PTFE (Teflon) und PVD (Physical Vapor Deposition) sind für ihre hervorragenden Antihafteigenschaften bekannt. Diese Beschichtungen verhindern, dass Klebstoffe und andere klebrige Materialien an der Klingenoberfläche haften bleiben, wodurch die Notwendigkeit häufiger Reinigung und Wartung verringert wird.
- Vorteile: Der Hauptvorteil von Polymerbeschichtungen ist ihre Fähigkeit, Materialanhaftungen zu widerstehen. Dies ist besonders nützlich für Branchen, die mit Materialien wie Bändern, Schäumen oder klebrigen Folien arbeiten, bei denen ständige Rückstandsbildung ein Problem darstellt. Polymerbeschichtungen können die Lebensdauer der Klinge verlängern und Ausfallzeiten reduzieren.
- Anwendungen: Polymerbeschichtungen werden in Branchen wie Verpackung, Textilien und Elektronik verwendet, in denen das Schneiden durch klebrige oder klebende Materialien üblich ist. Sie sind besonders nützlich zum Schneiden von Materialien wie Schaumstoffband, Klebeetiketten und Kunststofffolien.
- Effizienzdaten: Ein Bericht aus der Zeitschrift für Schneidwerkzeuge zeigt, dass PTFE-beschichtete Klingen beim Schneiden von Klebebändern und Schaumstoffen eine um 40 % verbesserte Schneidleistung im Vergleich zu unbehandelten Klingen aufweisen.
5 Optimierung automatisierter Schneideanlagen
Beim Arbeiten mit klebrigen Materialien ist die Optimierung automatisierter Schneidegeräte unerlässlich, um sowohl die Schnittpräzision als auch die Klingenlebensdauer aufrechtzuerhalten. Durch die Anpassung wichtiger Maschinenparameter und den Einsatz der richtigen Werkzeuge können Unternehmen ihre Schneidvorgänge deutlich verbessern.
- Automatisierte Schneidemaschinenkalibrierung
Durch regelmäßiges Kalibrieren der Schneidegeräte wird sichergestellt, dass die Schneidparameter – wie Geschwindigkeit, Druck und Winkel – auf optimalem Niveau gehalten werden. Automatisierte Systeme können so programmiert werden, dass sie sich an bestimmte Materialien anpassen und diese Parameter automatisch anpassen, um eine maximale Schneidleistung zu erzielen. Bei klebrigen Materialien ermöglichen viele automatisierte Systeme eine dynamische Geschwindigkeitsanpassung, die dazu beiträgt, übermäßige Reibung und Klebstoffansammlungen zu verhindern. - Schneidwerkzeugüberwachung und Sensoren
Moderne automatische Schneidemaschinen sind mit Sensoren ausgestattet, die den Zustand der Schneidklinge in Echtzeit überwachen können. Diese Sensoren können Anzeichen von Verschleiß, Überhitzung oder übermäßiger Reibung erkennen und die Schneidparameter entsprechend anpassen. Studien zeigen, dass die Integration intelligenter Sensoren in Schneidsysteme die Lebensdauer der Klinge um bis zu 25 % verlängern kann, da diese Sensoren Überbeanspruchung und Überhitzung verhindern können, bevor Schäden auftreten. - Automatisierte Rotorblatt-Wartungssysteme
Einige moderne Schneidsysteme sind mittlerweile mit Selbstreinigungsfunktionen ausgestattet, die Klebstoffrückstände zwischen den Schnitten automatisch von den Klingen entfernen. Dadurch wird verhindert, dass sich Ablagerungen auf die Schneidleistung auswirken, und manuelle Eingriffe sind weniger erforderlich. Dies führt zu höherer Produktivität und weniger Ausfallzeiten. - Datengetriebene Optimierung
Durch das Sammeln und Analysieren von Daten aus automatisierten Schneidsystemen können Unternehmen ihre Schneidprozesse optimieren, um sicherzustellen, dass die Klingen mit Höchstleistung arbeiten. Durch die Datenanalyse können Trends in Bezug auf Verschleißraten, Schneidleistung und optimale Parameter aufgedeckt werden, die zur Anpassung von Arbeitsabläufen und zur Vorhersage erforderlicher Wartungsarbeiten verwendet werden können.
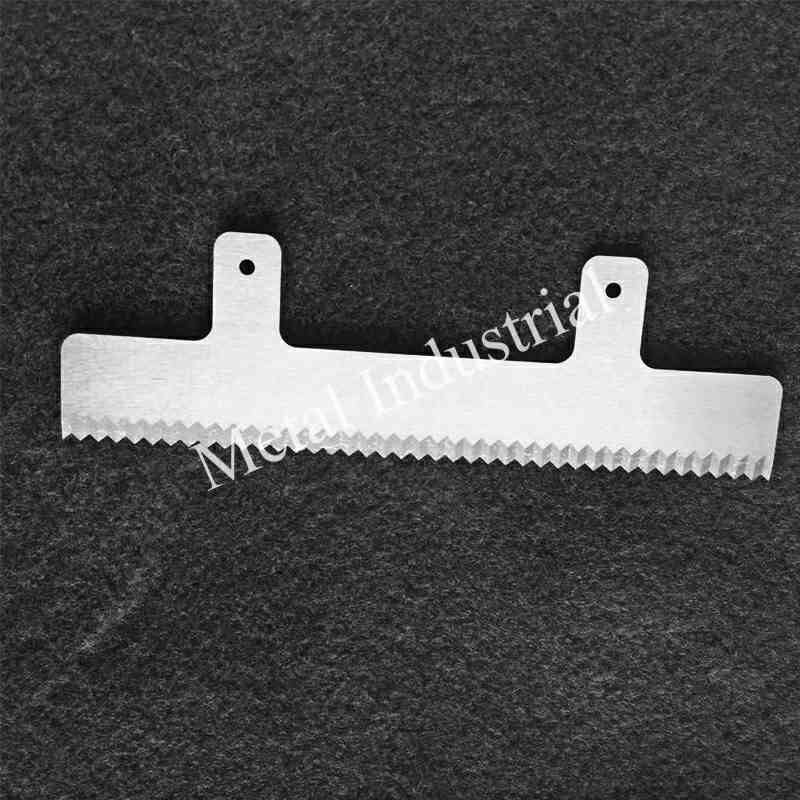
Den richtigen Rotorblattlieferanten auswählen: Qualität und Leistung sicherstellen
Auswählen der richtige Klingenlieferant ist der Schlüssel zum Erreichen optimaler Schneidlösungen. Ein zuverlässiger Lieferant kann Ihnen helfen, das richtige Klingenmaterial, die richtige Beschichtung und das richtige Design für Ihre spezifischen Schneidaufgaben auszuwählen.
1. Lieferantenkompetenz bewerten
Ein seriöser Klingenlieferant sollte die Anforderungen Ihrer Branche genau kennen und Ihnen maßgeschneiderte Empfehlungen geben können. Suchen Sie nach Lieferanten mit nachweislicher Erfolgsbilanz bei der Bereitstellung hochwertiger, langlebiger Klingen zum Schneiden klebriger Materialien.
2. Maßgeschneiderte Blade-Lösungen
Viele Anbieter bieten kundenspezifische Klingen speziell für Ihre Schneidanforderungen entwickelt. Ob Sie mit bestimmten Klebstoffen arbeiten oder eine spezielle Beschichtung benötigen, die Zusammenarbeit mit einem Lieferanten, der maßgeschneiderte Lösungen anbietet, kann zu besseren Ergebnissen und länger anhaltender Leistung führen.
3. Kundendienst und Garantie
Kundensupport ist wichtig, insbesondere bei der Behebung von Problemen im Zusammenhang mit Klingenverschleiß oder -leistung. Ein guter Lieferant sollte umfassende After-Sales-Services anbieten, einschließlich Garantieoptionen und Unterstützung bei der Fehlerbehebung.
Schlussfolgerung
Das Schneiden klebriger Materialien muss kein ständiger Kampf sein. Durch die Auswahl der richtigen Materialien, die Anpassung der Schneidparameter, die Wartung der Ausrüstung und die Verwendung moderner Beschichtungen können Sie Klingenschäden deutlich reduzieren und die Gesamtschneideleistung verbessern. Darüber hinaus trägt die Optimierung Ihrer automatisierten Schneidausrüstung dazu bei, dass Ihre Schneidlösungen so effektiv wie möglich sind. Diese Strategien sparen Ihnen nicht nur Geld, sondern steigern auch Ihre Produktivität.
Bereit, Ihre Schneidprozesse zu optimieren? Kontaktieren Sie uns um noch heute mehr über maßgeschneiderte Schneidlösungen zu erfahren, die Ihre Klingen schützen und Ihre Leistung steigern.