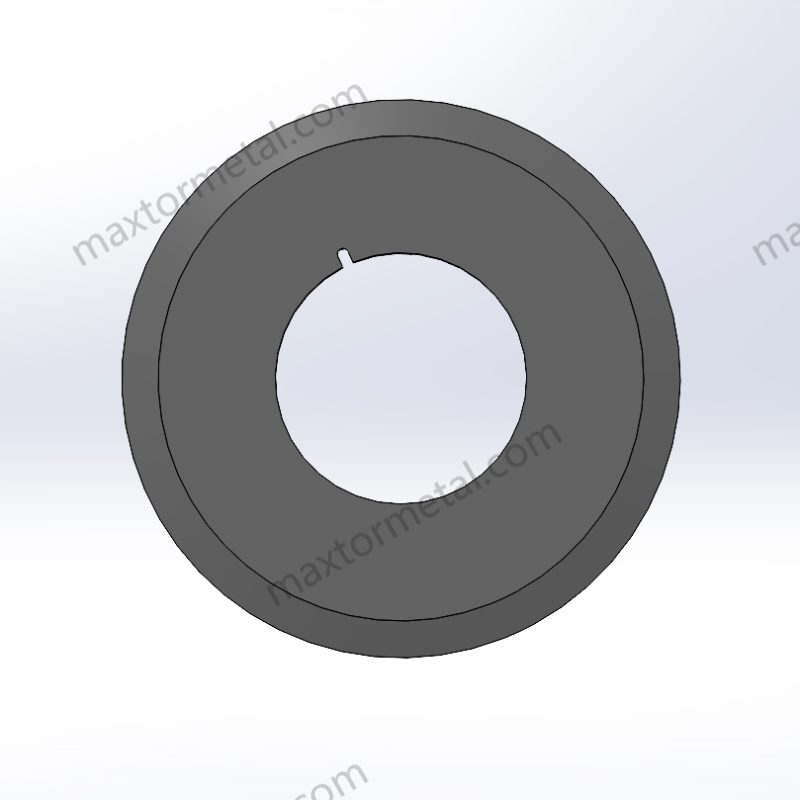
Kreismesser sind unverzichtbare Werkzeuge in vielen industriellen Anwendungen, von Verpackung und Papierindustrie Zu Metallbearbeitung und Kunststoffherstellung. Diese Klingen sind für saubere, präzise Schnitte in einer Vielzahl von Materialien konzipiert und verbessern so die Produktionseffizienz und -qualität.
Nanjing Metal, Mit über 18 Jahren Erfahrung in der Herstellung von Industrieklingen ist HUBER stolz darauf, zu den führenden Innovationen im Bereich der Kreismesser zu gehören. Unsere fortschrittlichen Fertigungsprozesse und unser Engagement für maßgeschneiderte Lösungen verhelfen Unternehmen weltweit zu überragender Schneidleistung.
Dieser Artikel untersucht die Entwicklung und Innovationen bei Kreismessern und beleuchtet wichtige Materialien, Beschichtungstechnologien und Designfortschritte. Er zeigt außerdem, wie diese Innovationen die Schneideffizienz deutlich steigern, die Wartungskosten senken und die Gesamtproduktivität in industriellen Umgebungen verbessern können.
1. Die Geschichte und Entwicklung von Kreismessern
Die Entwicklung runder Schneidemesser spiegelt die umfassenden Fortschritte in der Materialwissenschaft und Fertigungstechnologie wider.
Historische Entwicklung:
- Frühe Werkzeuge: In der Antike wurden die ersten Schneidwerkzeuge aus Stein und Knochen gefertigt. Obwohl diese Materialien rudimentär waren, markierten sie den Beginn menschlicher Innovationen im Bereich der Schneidetechnik.
- Industrielle RevolutionDie Industrielle Revolution brachte bedeutende Durchbrüche in der Schneidtechnologie. Die Einführung von Stahl als Klingenmaterial verbesserte deren Festigkeit und Haltbarkeit erheblich. Stahl ermöglichte es den Herstellern, schärfere und präzisere Messer herzustellen, die den steigenden Anforderungen der industriellen Produktion gerecht wurden.
Moderne Fortschritte:
- Kohlenstoffstahl: Die Einführung von Kohlenstoffstahl markierte einen bedeutenden Meilenstein in der Entwicklung von Schneidmessern. Dieses Material erhöhte die Lebensdauer der Klinge und die Schnittpräzision, insbesondere bei härteren Materialien.
- Wolframkarbid: Eine der bedeutendsten Innovationen ist heute die Verwendung von Wolframkarbid bei der Herstellung von Schneidmessern. Die bemerkenswerte Härte und Verschleißfestigkeit von Wolframkarbid machen es zum idealen Material zum Schneiden zäher, abrasiver Materialien. Es verlängert die Lebensdauer der Klingen und reduziert Ausfallzeiten.
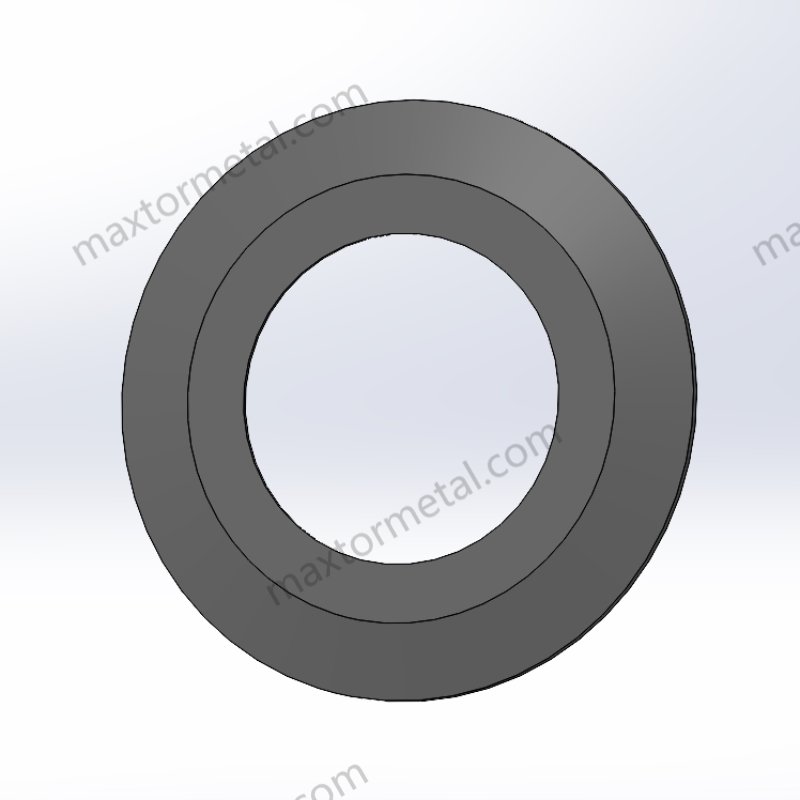
2. Derzeit beliebte Klingenmaterialien
Heutige Industrie-Schneidemesser werden aus verschiedenen Materialien gefertigt, die jeweils aufgrund ihrer Leistungsfähigkeit unter bestimmten Bedingungen ausgewählt werden. Zu den gängigsten Materialien gehören:
Material | Eigenschaften | Typische Anwendungen |
Kohlenstoffstahl | Hohe Festigkeit, Haltbarkeit und hervorragende Schnitthaltigkeit | Papierschneiden, Leichtmetalle und Kunststoffe |
Schnellarbeitsstahl (HSS) | Überlegene Verschleißfestigkeit, Hitzebeständigkeit und Zähigkeit | Schneiden von Metallen und harten Materialien bei hohen Geschwindigkeiten |
Wolframkarbid | Außergewöhnlich hart, ausgezeichnete Verschleißfestigkeit | Schneiden abrasiver Materialien wie Verbundwerkstoffe |
Hochleistungskeramik | Hohe Präzision und hohe Geschwindigkeit | Mikroschneiden, Elektronik und Feinmetalle |
- Kohlenstoffstahl: Schneidmesser aus Kohlenstoffstahl werden traditionell in vielen industriellen Anwendungen eingesetzt und sind für ihre Erschwinglichkeit und ausreichende Schneidleistung in weniger anspruchsvollen Umgebungen bekannt.
- Schnellarbeitsstahl (HSS): HSS bietet eine hervorragende Verschleiß- und Hitzebeständigkeit und ist daher ideal für Hochgeschwindigkeitsschneidanwendungen. Die Fähigkeit, die Schärfe über lange Zeiträume beizubehalten, verbessert die Produktivität.
- WolframkarbidSchneidmesser aus Wolframkarbid werden bevorzugt in Branchen eingesetzt, in denen hohe Verschleißfestigkeit entscheidend ist. Die Fähigkeit von Hartmetall, abrasive Materialien zu verarbeiten, ohne die Lebensdauer der Klinge zu beeinträchtigen, ist eine bedeutende Innovation in der Schneidtechnologie.
- Hochleistungskeramik: Dank ihrer außergewöhnlichen Härte und Hitzebeständigkeit werden Hochleistungskeramiken für Präzisionsschneidarbeiten eingesetzt. Diese Materialien kommen häufig in Anwendungen zum Einsatz, die Hochgeschwindigkeitsschnitte bei minimaler Wärmeausdehnung erfordern.
3. Beschichtungen und Behandlungstechnologien für Schneidmesser
Moderne Beschichtungs- und Behandlungstechnologien tragen maßgeblich zur Verbesserung der Haltbarkeit, Leistung und Wirtschaftlichkeit von Kreismessern bei. Diese Innovationen reduzieren den Verschleiß deutlich, verbessern die Schneidleistung und verlängern die Gesamtlebensdauer der Klingen. Dank technologischer Fortschritte bei Materialien und Verarbeitungstechniken können Hersteller heute Klingen herstellen, die sich durch außergewöhnliche Langlebigkeit, Präzision und Schneidleistung auszeichnen.
In der folgenden Tabelle sind die gängigsten Beschichtungs- und Behandlungstechnologien zusammengefasst und ihre Vorteile und spezifischen Einsatzmöglichkeiten hervorgehoben.
Beschichtung/Technologie | Vorteile | Verwendung |
Titannitrid (TiN) | Erhöht die Härte, verringert die Reibung und verbessert die Verschleißfestigkeit | Papierschneiden, Folienschneiden, Leichtmetalle, Kunststoffe |
Diamantähnlicher Kohlenstoff (DLC) | Außergewöhnliche Härte, geringe Reibung, hohe Korrosionsbeständigkeit, selbstschmierende Eigenschaften | Hochpräzisionsschneiden, Luft- und Raumfahrt, medizinische Geräte |
Wärmebehandlung | Verbessert Zähigkeit, Härte und Verschleißfestigkeit | Allzweck-Schneidemesser für leichte und mittelschwere Anwendungen |
Kryogene Behandlung | Verändert die Mikrostruktur und verbessert die Haltbarkeit unter Hochbelastungsbedingungen | Anwendungen mit hohem Verschleiß und hoher Beanspruchung, Schneiden von zähen Materialien |
Titannitrid (TiN)-Beschichtung
Die Titannitrid-Beschichtung (TiN) ist eine der am häufigsten verwendeten Oberflächenbehandlungen für Industrieklingen. Diese Beschichtung ist bekannt für ihre bemerkenswerte Härte sowie Verschleiß- und Korrosionsbeständigkeit. Durch die Bildung einer dünnen, aber extrem zähen Schicht auf der Klingenoberfläche schützt TiN die Klinge nicht nur vor vorzeitigem Verschleiß, sondern reduziert auch die Reibung beim Schneiden. Dadurch bleiben die Klingen länger scharf und benötigen weniger Wartung.
- Hauptvorteile:
- Härte: TiN-Beschichtungen erhöhen die Oberflächenhärte von Schneidmessern um bis zu 2.000 HV (Vickershärte) und machen sie so äußerst widerstandsfähig gegen Verschleiß durch abrasive Materialien.
- Reduzierte Reibung: Dank seines niedrigen Reibungskoeffizienten (0,4) ermöglicht TiN den Klingen ein sanfteres Gleiten durch das Material, wodurch die Wärmeentwicklung beim Schneiden verringert und somit die Schnittqualität verbessert wird.
- Verlängerte Klingenlebensdauer: Studien haben gezeigt, dass TiN-beschichtete Klingen bis zu 3–5 Mal länger halten als unbeschichtete Klingen, was sie ideal für Hochgeschwindigkeitsschneidanwendungen macht.
- Typische Anwendungen:
- TiN-Beschichtungen werden vor allem in der Papier-, Folien- und Verpackungsindustrie eingesetzt, wo Schnittpräzision und Haltbarkeit entscheidend sind. In diesen Branchen, in denen lange Produktionsläufe üblich sind, reduzieren TiN-beschichtete Klingen Betriebsausfallzeiten und steigern die Effizienz.
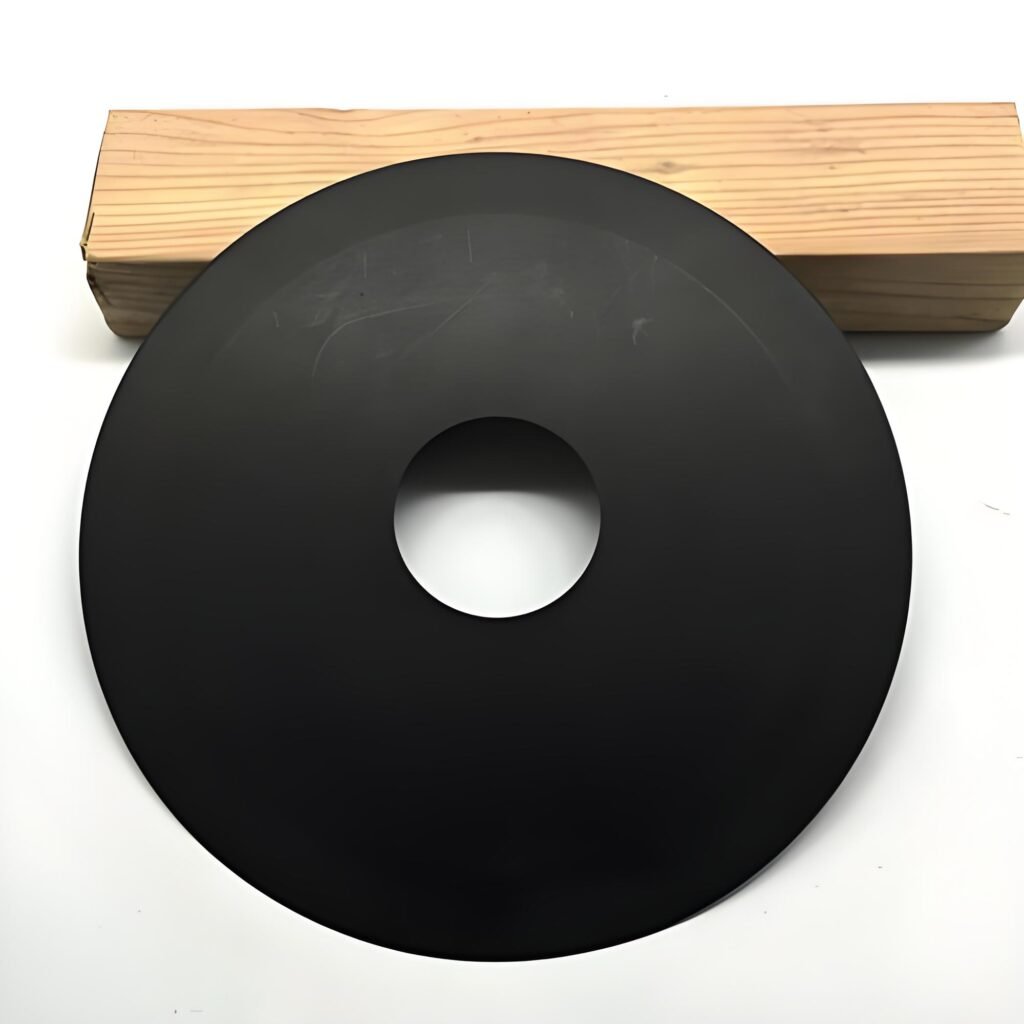
Diamantähnliche Kohlenstoffbeschichtung (DLC)
Diamantähnliche Kohlenstoffbeschichtungen (DLC) bieten außergewöhnliche Härte, Verschleißfestigkeit und geringe Reibung. Diese Technologie hat insbesondere in hochpräzisen Branchen wie der Medizintechnik und der Luft- und Raumfahrt, wo Schneidwerkzeuge über lange Zeit ultrascharfe Kanten behalten müssen, bahnbrechende Fortschritte erzielt. DLC-Beschichtungen imitieren die Eigenschaften natürlicher Diamanten und bieten eine Oberfläche, die nicht nur unglaublich hart, sondern auch korrosionsbeständig und selbstschmierend ist.
- Hauptvorteile:
- Härte: DLC-Beschichtungen gehören zu den härtesten verfügbaren Materialien. Mit Härtewerten von über 3.000 HV übertreffen sie die von TiN-Beschichtungen. Dadurch eignen sie sich ideal für Präzisionsschneidanwendungen mit schwer zerspanbaren Materialien.
- Reibungsreduzierung: DLC-Beschichtungen verringern die Reibung zwischen Schneide und Material deutlich und sorgen so für sanfteres Schneiden und minimale Wärmeentwicklung. Dadurch wird der Verschleiß sowohl der Schneide als auch des zu schneidenden Materials reduziert.
- Korrosionsbeständigkeit: DLC-Beschichtungen sind äußerst korrosionsbeständig und eignen sich daher zum Schneiden in rauen Umgebungen, beispielsweise in der Lebensmittel- und Pharmaindustrie, wo Sauberkeit und Klingenlebensdauer von größter Bedeutung sind.
- Typische Anwendungen:
- DLC-Beschichtungen werden häufig bei der Herstellung von Klingen für hochpräzise Schneidaufgaben eingesetzt, beispielsweise für medizinische Geräte, Automobilteile und Komponenten für die Luft- und Raumfahrt. Darüber hinaus kommen sie in der Verpackungsindustrie zum Einsatz, wo Sauberkeit und Schnittpräzision entscheidend sind.
Wärmebehandlung und kryogene Behandlung
Sowohl Wärmebehandlung als auch Kryobehandlung verbessern die Zähigkeit, Härte und Haltbarkeit von Schneidmessern. Diese Verfahren werden typischerweise bei Klingen aus Kohlenstoffstahl und Werkzeugstahl angewendet, die häufig für Hochleistungsschneidanwendungen eingesetzt werden.
- Wärmebehandlung: Bei der Wärmebehandlung wird die Klinge auf eine hohe Temperatur erhitzt und anschließend schnell abgekühlt, um die gewünschte Mikrostruktur zu erreichen. Dieser Prozess erhöht die Härte und Zähigkeit des Materials und macht die Klinge widerstandsfähiger gegen hohe Belastungen beim Schneiden. Durch die Wärmebehandlung kann die Klingenhärte auf ca. 60–65 HRC (Rockwell-Härte) erhöht werden, was sie ideal für Allzweck-Schneidemesser macht.
- Kryogene Behandlung: Die kryogene Behandlung ist ein Wärmenachbehandlungsverfahren, bei dem die Klinge auf extrem niedrige Temperaturen (−196 °C bzw. −321 °F) abgekühlt wird, um ihre Mikrostruktur zu verändern. Diese Behandlung verbessert die Verschleißfestigkeit und Haltbarkeit der Klinge, insbesondere unter hoher Belastung. Die kryogene Behandlung kann die Lebensdauer der Klinge im Vergleich zu unbehandelten Klingen um bis zu 30 % verlängern und ist daher eine ausgezeichnete Wahl für Anwendungen, die eine längere Klingenlebensdauer erfordern.
- Typische Anwendungen:
- Wärmebehandelte Klingen werden häufig für allgemeine Schneidarbeiten eingesetzt, unter anderem in der Papier-, Kunststoff- und Leichtmetallindustrie. Die kryogene Behandlung hingegen wird häufig bei Klingen angewendet, die in Umgebungen mit hohem Verschleiß eingesetzt werden, beispielsweise in der Stahlindustrie, wo die Klingen abrasiven Materialien und harten Schneidbedingungen ausgesetzt sind.
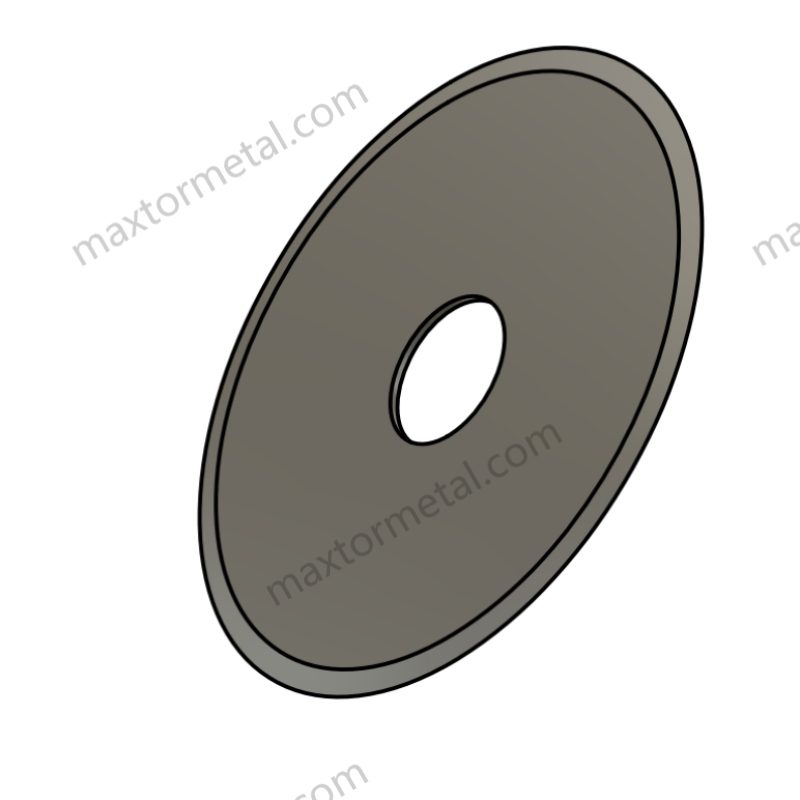
4. Optimierung des Klingenkantendesigns
Das Design der Klingenkante spielt eine entscheidende Rolle für die Gesamtleistung von Schneidmessern. Durch die Optimierung von Kantenform, -winkeln und -geometrie können Hersteller die Schneidleistung deutlich steigern, Materialverschwendung reduzieren und die Lebensdauer der Klinge verlängern. Fortschritte in der Präzisionsfertigung, wie CNC (Computer Numerical Control) und 3D-Druck, ermöglichen es Herstellern, hochpräzise, kundenspezifische Klinge Designs für spezifische Industrieanwendungen.
Kantenformen und Winkel
Die Kantengeometrie eines Kreismessers ist entscheidend für die Interaktion der Klinge mit dem zu schneidenden Material. Durch die Feinabstimmung von Kantenformen und -winkeln können Hersteller Klingen für ein breites Spektrum an Schneidanwendungen anpassen.
- Scharfe Winkel: Ein schärferer Kantenwinkel wird häufig zum Schneiden dünner, empfindlicher Materialien wie Papier, Folie oder Film verwendet. Diese Materialien erfordern eine präzise, scharfe Klinge, um saubere Schnitte ohne Ausreißen zu gewährleisten.
- Robuste Kanten: Für härtere Materialien wie Metalle oder Verbundwerkstoffe ist eine robustere Schneidenkonstruktion erforderlich. Ein etwas stumpferer Winkel ermöglicht es der Klinge, mehr Kraft auf das Material auszuüben und so ein effektives Schneiden ohne übermäßigen Verschleiß zu gewährleisten.
- Mikrogeometrieoptimierung: Spezielle Mikrogeometrien, wie z. B. geschliffene oder spiralförmige Kanten, können die Schneidleistung verbessern und die Lebensdauer der Klinge erhöhen. Diese Mikrogeometrien reduzieren die Belastung der Klinge während des Schneidvorgangs und sorgen so für einen effizienteren Schneidvorgang.
Präzisionsfertigungstechnologien
Der Einsatz von Präzisionsfertigungstechnologien wie CNC-Bearbeitung und 3D-Druck hat die Herstellung von Schneidmessern revolutioniert. Diese Technologien ermöglichen es Herstellern, Klingen mit hochpräzisen Kantengeometrien und komplexen Designs herzustellen, die auf die individuellen Anforderungen verschiedener Branchen zugeschnitten sind.
- CNC (Computergestützte numerische Steuerung)CNC-Technologie ermöglicht die Herstellung von Klingen mit außergewöhnlicher Kantenpräzision. CNC-Maschinen erreichen Toleranzen von bis zu 0,001 mm und ermöglichen so die Herstellung hochspezialisierter Schneidkanten. Dies ist besonders nützlich in Branchen, in denen Klingenpräzision entscheidend ist, wie beispielsweise in der Elektronik- und Automobilherstellung.
- 3D-Druck: Mit dem Aufkommen der additiven Fertigung entwickelt sich der 3D-Druck zu einer innovativen Methode für die Herstellung kundenspezifischer Schneidmesser. Diese Technologie ermöglicht die schnelle Prototypenentwicklung und Produktion komplexer Geometrien, die mit herkömmlichen Fertigungsmethoden bisher nur schwer realisierbar waren.
- AnpassungModerne Fertigungsmethoden, darunter der Einsatz fortschrittlicher Materialien wie Wolframkarbid und Keramik, ermöglichen eine individuelle Gestaltung der Klingenkanten. Maßgeschneiderte Designs stellen sicher, dass die Messer den spezifischen Schneidanforderungen verschiedener Materialien und Branchen gerecht werden, was die Effizienz steigert und Ausfallzeiten reduziert.
Diese Innovationen bei Beschichtungen, Behandlungen und Kantendesigns haben zu deutlichen Leistungs- und Haltbarkeitsverbesserungen von Kreismessern geführt. Durch die Wahl der richtigen Kombination aus Materialien, Beschichtungen und präzisionsgefertigten Klingendesigns können Hersteller ihre Schneideffizienz deutlich steigern, Betriebskosten senken und die Nachhaltigkeit ihrer Prozesse verbessern.
5. Die Bedeutung von Individualisierung und Präzisionstechnik
Im heutigen wettbewerbsintensiven Industrieumfeld stehen Unternehmen oft vor einzigartigen Schneidherausforderungen, die maßgeschneiderte Lösungen erfordern. Die individuelle Anpassung an spezifische Anforderungen gewinnt zunehmend an Bedeutung.
- Branchenspezifische LösungenOb Papier, Kunststoff oder Metall – jedes Material hat seine eigenen Schneideigenschaften. Nanjing Metal bietet maßgeschneiderte Schneidmesser, die den unterschiedlichen Anforderungen verschiedener Branchen gerecht werden, die Effizienz steigern und den Materialabfall minimieren.
- FeinmechanikBei Nanjing Metal setzen wir modernste Präzisionstechnik ein, um sicherzustellen, dass unsere Messer den strengsten Qualitätsstandards entsprechen. Diese Liebe zum Detail hilft unseren Kunden, höchste Schneidleistung zu erzielen und gleichzeitig Ausfallzeiten und Wartungskosten zu reduzieren.
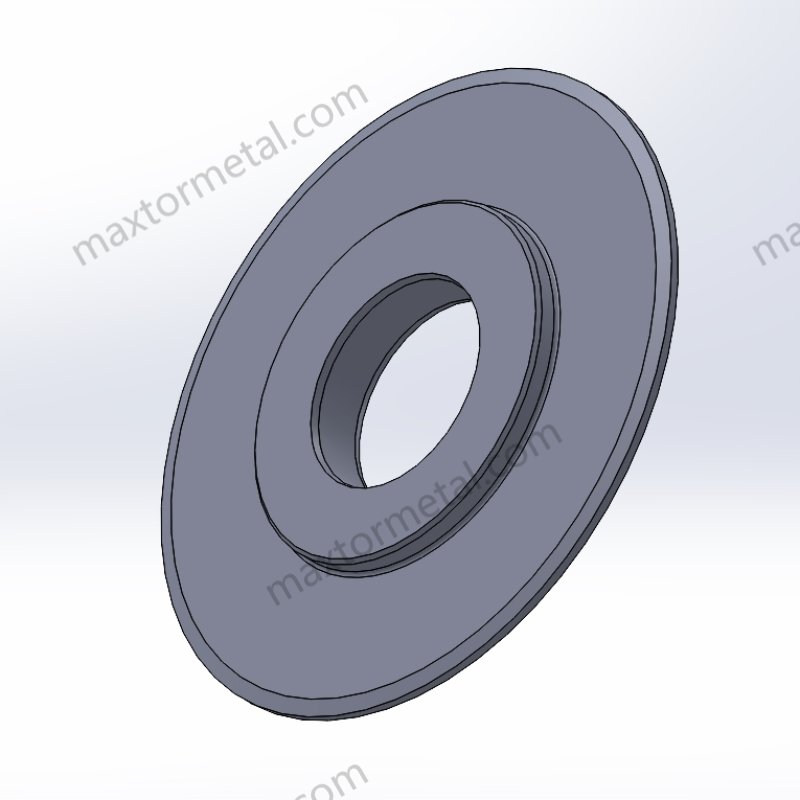
6. Nachhaltigkeit und Kreislaufwirtschaft
Nachhaltigkeit ist in allen Branchen ein wachsendes Anliegen, und der Markt für Schneidmesser bildet da keine Ausnahme. Hersteller suchen zunehmend nach Möglichkeiten, Abfall zu minimieren, die Produktlebensdauer zu verlängern und die Umweltbelastung ihrer Betriebsabläufe zu reduzieren.
- Verwendung recycelbarer MaterialienDurch die Integration recycelbarer Materialien in den Produktionsprozess können Hersteller dazu beitragen, die Umweltbelastung durch Schneidmesser zu reduzieren. Dies entspricht den Prinzipien der Kreislaufwirtschaft, in der Produkte wiederverwendet, repariert und recycelt statt entsorgt werden.
- Verlängerte KlingenlebensdauerInnovationen bei Materialien und Beschichtungen haben die Lebensdauer von Kreismessern deutlich verlängert. Länger haltbare Klingen reduzieren die Austauschhäufigkeit, minimieren den Abfall und verbessern die Nachhaltigkeit des Schneidprozesses.
- Grüne Produktion: Bei Nanjing Metal setzen wir auf umweltfreundliche Herstellungsverfahren und optimieren unsere Prozesse, um den Energieverbrauch und den ökologischen Fußabdruck zu reduzieren.
7. Zukünftige Trends und technologischer Ausblick
Die Zukunft von Kreisschneidemessern steht vor tiefgreifenden Veränderungen, die durch Fortschritte in der Materialwissenschaft, der digitalen Fertigung und der Automatisierung vorangetrieben werden. Diese Innovationen werden die Effizienz, Präzision und Nachhaltigkeit industrieller Schneidvorgänge deutlich steigern und Herstellern neue Möglichkeiten eröffnen, die Produktqualität zu verbessern und die Betriebskosten zu senken. Lassen Sie uns diese sich entwickelnden Trends und ihre möglichen Auswirkungen genauer betrachten.
Neue Materialien und Rotorblätter der nächsten Generation
Die Suche nach immer langlebigeren und leistungsfähigeren Materialien ist ein wichtiger Treiber für die Entwicklung von Schneidmessern. Aktuelle Materialien wie Kohlenstoffstahl, Wolframkarbid und Keramik bieten bereits beeindruckende Leistungsmerkmale, doch die laufende Forschung eröffnet neue Möglichkeiten in der Materialwissenschaft.
1. Verbundwerkstoffe für Schneidklingen:
- Metal-Matrix-Verbundwerkstoffe (MMCs):
- Hochleistungspolymere
2. Graphen und Nanobeschichtungen:
- Graphenbeschichtungen
- Nanostrukturierte Beschichtungen
Diese neuen Materialien dürften die Produktion von Längsschneidemessern revolutionieren, indem sie langlebigere Hochleistungswerkzeuge ermöglichen, die Ausfallzeiten und Wartungskosten reduzieren und gleichzeitig die Schneideffizienz verbessern.
Der Aufstieg der Automatisierung und intelligenten Fertigung in der Schneidmesserproduktion
Automatisierung und intelligente Fertigung verändern die Herstellung und Nutzung von Schneidmessern. Durch den Einsatz fortschrittlicher Sensoren, maschinellem Lernen und Echtzeit-Datenerfassung wird die nächste Fertigungsgeneration Produktion und Nutzung auf ein beispielloses Niveau optimieren.
1. Echtzeit-Datenanalyse für optimierte Leistung:
2.Automatisierung der Blatteinstellung
3. Automatisierung in der Rotorblattherstellung
Durch diese Fortschritte profitieren Hersteller von hochoptimierten, kosteneffizienten Schneidvorgängen, die ein Höchstmaß an Leistung gewährleisten und das Fehlerrisiko im Zusammenhang mit manuellen Anpassungen verringern.
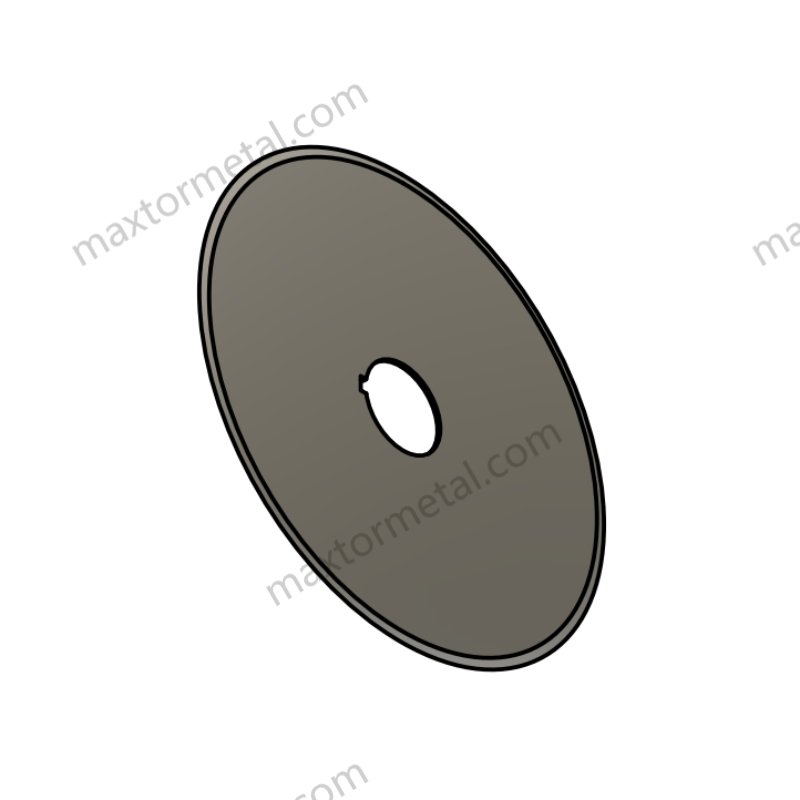
Individualisierung im großen Maßstab: 3D-Druck und additive Fertigung
3D-Druck, auch additive Fertigung genannt, wird die Entwicklung und Herstellung von Schneidemessern grundlegend verändern. Im Gegensatz zu herkömmlichen subtraktiven Fertigungsverfahren, bei denen Material aus einem größeren Block herausgeschnitten wird, werden die Klingen beim 3D-Druck Schicht für Schicht aufgebaut, was neue Möglichkeiten zur individuellen Gestaltung bietet.
- Verbesserte Anpassung
- Massenanpassung
- Schnelles Prototyping und Iteration:
Marktverschiebungen und Anforderungen an fortschrittliche Schneidmesser
Mit der Weiterentwicklung der Branchen verändert sich auch die Nachfrage nach Rundmessern. Kunden suchen zunehmend nach Klingen mit längerer Lebensdauer, höherer Präzision und besserer Effizienz, getrieben von umfassenden Nachhaltigkeitszielen und der Notwendigkeit, die Betriebskosten zu senken.
Die Zukunft der Kreisschneidemesser wird durch die Kombination modernster Materialien, fortschrittlicher Fertigungstechnologien und verbesserter Anpassungsmöglichkeiten geprägt sein. Diese Trends werden die Effizienz steigern, Kosten senken und die Leistung in zahlreichen Branchen verbessern und so die Entwicklung der Schneidtechnologie vorantreiben.
8. Fazit
Kreismesser spielen in vielen Branchen eine zentrale Rolle und tragen zu mehr Effizienz und Präzision in Schneidprozessen bei. Durch kontinuierliche Innovation und Weiterentwicklung bei Materialien, Beschichtungen, Kantendesign und Anpassung wurden diese Messer weiterentwickelt, um den sich ständig ändernden Anforderungen der modernen Fertigung gerecht zu werden.
Bei Nanjing MetalWir haben uns der Bereitstellung hochwertiger, maßgeschneiderter Schneidmesser verschrieben, die die Industriestandards nicht nur erfüllen, sondern übertreffen. Mit unserer Erfahrung und unserem technischen Know-how unterstützen wir Unternehmen dabei, ihre Schneideffizienz zu steigern und ihre Produktivität zu steigern.
Wir ermutigen Sie Entdecken Sie unsere Produkte und Dienstleistungen, die Ihnen dabei helfen sollen, bei Ihren industriellen Anwendungen eine überragende Leistung zu erzielen.
Verweise
- „Werkstoffe für industrielle Schneidwerkzeuge“ – Journal of Materials Science, 2021
- „Die Rolle von Beschichtungen für die Werkzeugleistung“ – Advanced Coatings Review, 2022
3 Antworten
Hallo
Ich bin auf der Suche nach Schneidklingen zum Schneiden von Papierkernen.
Die maximale Dicke beträgt etwa 10 mm
Können Sie mir eine Art Schneidklinge mit Spezifikation und Preis empfehlen?
Hallo Reginal, ich melde mich bald.
Ja, ihre Produkte sind ziemlich gut und der Service ist schnell.