Industrial blade tolerance plays a crucial role in determining the efficiency, durability, and cost-effectiveness of manufacturing processes. Choosing the wrong tolerance can lead to poor cutting performance, excessive machine wear, and increased operational costs. Studies suggest that improper blade tolerances can result in up to 30% higher maintenance costs due to misalignment and increased wear rates.
Bei Nanjing Metal, we have 18 years of experience designing and manufacturing precision industrial blades. Our expertise allows us to offer custom industrial blades that balance blade tolerance standards with cost efficiency. In this article, we will explore the fundamentals of industrial blade tolerance, its impact on performance and manufacturing, and how to select the optimal tolerance for different applications.
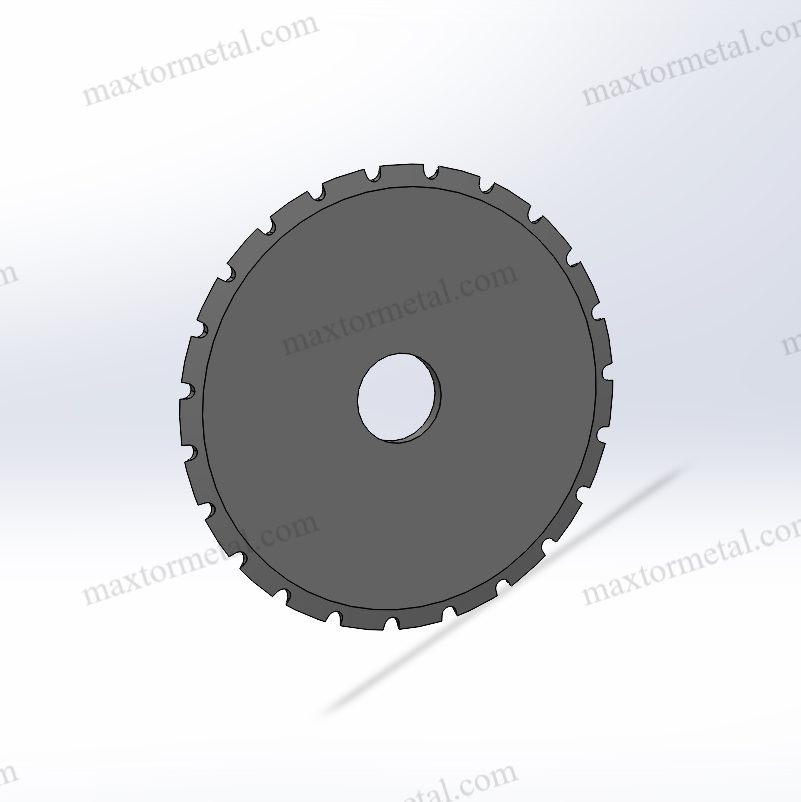
1. What Is Industrial Blade Tolerance?
Definition of Blade Tolerance
Industrial blade tolerance refers to the acceptable range of variation in blade dimensions, including thickness, length, width, and edge sharpness. These tolerances ensure that machinery blade specifications meet operational requirements without compromising performance.
The Role of Tolerance in Blade Performance
A well-defined blade manufacturing tolerance ensures that:
- Blades fit precisely into cutting machines, preventing misalignment and reducing vibration.
- The cutting process remains consistent, reducing the risk of material defects.
- Production downtime is minimized due to fewer adjustments and replacements.
Common Blade Tolerance Ranges
Different industries require different levels of precision. Below is a general guideline for blade tolerance standards:
Klingentyp | Thickness Tolerance (mm) | Length Tolerance (mm) | Edge Tolerance (mm) |
Standard Industrial | ±0.05 | ±0.10 | ±0.02 |
Präzisionsschneiden | ±0.02 | ±0.05 | ±0.01 |
Medical/Aerospace | ±0.01 | ±0.03 | ±0.005 |
Choosing the appropriate tolerance is critical to balancing blade performance und production efficiency.
2. Why Choosing the Right Blade Tolerance Matters
The Impact of Tight vs. Loose Tolerances
Many manufacturers assume that tighter blade tolerance always leads to better performance. While high precision is critical in some applications, overly strict tolerances can increase manufacturing costs without delivering substantial benefits. On the other hand, loose tolerances can lead to performance inconsistencies and machine blade misalignment. Striking the right balance is key.
Tighter Tolerances: When Do They Help?
Tighter tolerances (e.g., ±0.01mm) are crucial when:
- Blades must interact with other precision components (e.g., surgical scalpels, and aerospace knives).
- High-speed cutting processes demand consistency, such as in high-precision metal stamping.
- The material being cut is highly sensitive (e.g., ultra-thin films or delicate composites).
However, achieving ultra-tight tolerances requires advanced CNC grinding, laser measurement, and additional quality control steps, all of which increase costs.
Looser Tolerances: When Are They Acceptable?
A looser blade tolerance (e.g., ±0.05mm or ±0.10mm) is acceptable when:
- The cutting process does not demand extreme precision (e.g., woodworking, bulk food slicing).
- Machines allow for slight variations without affecting performance.
- The material properties are less affected by tolerance variations (e.g., cardboard, rubber, plastics).
By opting for an appropriate tolerance instead of an unnecessarily strict one, businesses can reduce manufacturing costs by up to 20-30% while maintaining effective cutting performance.
Case Study: Food Processing Blades
A food packaging company initially specified ±0.01mm tolerance for their slicing blades, assuming it would improve cutting accuracy. However, the reality was:
- Production costs increased by 30%, as tighter tolerances required advanced precision machining.
- Lead times doubled due to additional quality control and calibration processes.
- Minimal performance improvement, as a ±0.02mm tolerance, provided the same slicing consistency.
After reassessing their requirements, they relaxed the tolerance to ±0.02mm, achieving:
✅ 20% cost savings on blade production
✅ Faster manufacturing times, reducing lead times by 40%
✅ No noticeable drop in performance
This demonstrates how overly tight tolerances can be an unnecessary financial burden.
Equipment Compatibility and Blade Performance
The interaction between blade tolerances and machine blade specifications is crucial:
- If tolerances are too loose, blades may misalign, leading to poor cuts and increased wear on machines.
- If tolerances are too tight, production delays and higher costs may occur due to excessive precision requirements.
- Finding an optimal blade manufacturing tolerance ensures machine compatibility and cost-efficient operation.
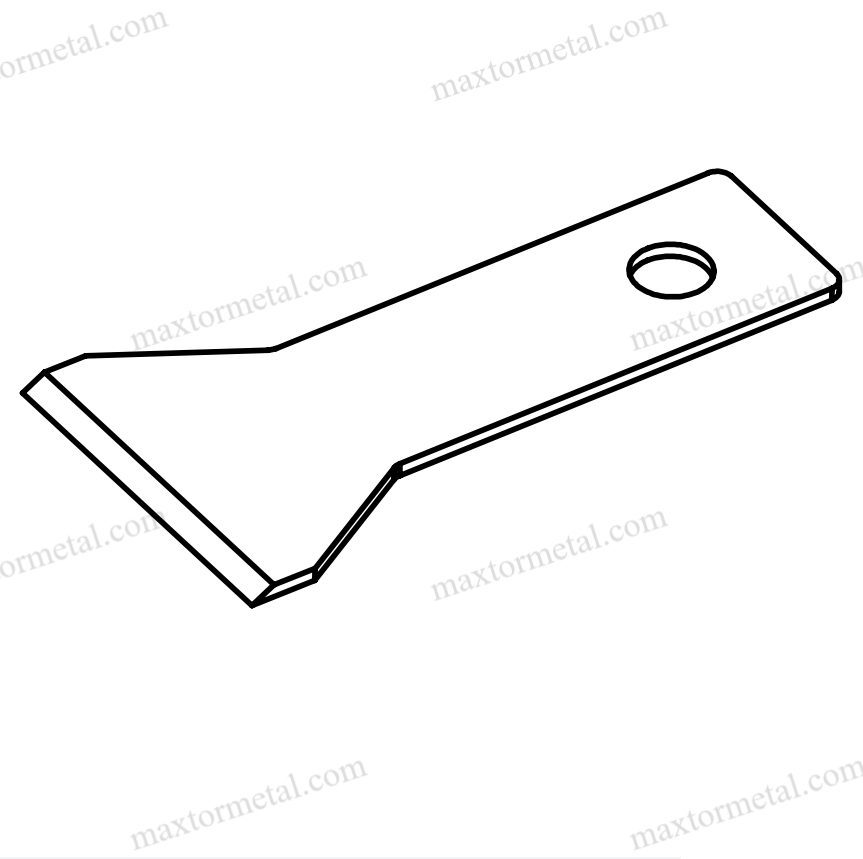
3. How Blade Tolerance Relates to Manufacturing Processes
The Importance of Matching Tolerance with Manufacturing Precision
Selecting the right blade tolerance requires an understanding of the entire manufacturing ecosystem. Even the most precise industrial knife cannot compensate for inaccuracies in other machine components.
For example, if a machine has a positional accuracy of ±0.05mm, using a blade with a ±0.01mm tolerance provides no additional benefit—it merely increases production costs.
Machine Precision | Recommended Blade Tolerance | Grund |
±0.10mm | ±0.05mm | No need for extreme precision |
±0.05mm | ±0.02mm | Balances performance & cost |
±0.02mm | ±0.01mm | Required for precision work |
Key takeaway: Blade tolerance should align with the precision of the entire system, not just the blade itself.
Impact of Blade Tolerance on Production Efficiency
Blade tolerance directly affects manufacturing efficiency and cost-effectiveness:
- Tighter tolerances require advanced machining, such as CNC grinding, EDM cutting, or laser measuring, increasing costs.
- Looser tolerances allow for faster production, reducing manufacturing lead times by up to 50%.
- Over-specifying blade tolerance leads to material waste, increasing overall expenses.
Example: Cost Analysis of Blade Tolerances
Tolerance Level | Manufacturing Cost Increase | Lead Time Increase | Materialabfall |
±0.10mm | Base cost | Standard | Minimal |
±0.05mm | +10% cost | +15% time | Mäßig |
±0.01mm | +40% cost | +50% time | Hoch |
As shown above, tightening tolerances beyond what is necessary leads to higher costs without significant functional improvements.
The Trade-off Between Precision and Cost
To avoid unnecessary expenses, manufacturers should:
- Assess machine accuracy before defining blade tolerance.
- Prioritize functionality over extreme precision unless required for specialized applications.
- Consult with blade manufacturers to determine the best balance of cost and performance.
4. Evaluating Application-Specific Tolerance Requirements
Industry-Specific Blade Tolerance Standards
The appropriate industrial blade tolerance varies by industry. Below are typical tolerance requirements:
Industrie | Recommended Tolerance | Warum es wichtig ist |
Medizinische Industrie | ±0.01mm | Ensures surgical precision & safety |
Luft- und Raumfahrt | ±0.02mm | Maintains structural integrity |
Verpackung | ±0.05mm | Allows high-speed processing |
Holzbearbeitung | ±0.10mm | Provides flexibility for material variations |
When to Use Tighter Tolerances
✅ High-precision applications where even slight deviations cause defects:
- Medical scalpels & surgical knives (where precision affects patient safety).
- Aerospace cutting tools (where structural integrity is critical).
- Microelectronics & semiconductor cutting blades (where minute misalignments impact production yields).
When Standard Tolerances Are Sufficient
✅ General manufacturing applications where small variations do not impact performance:
- Verpackungsklingen (±0.05mm is typically sufficient for clean cuts).
- Food slicing knives (where ±0.02mm can maintain efficiency without extra cost).
- Wood-cutting blades (±0.10mm is often acceptable since wood has natural irregularities).
How to Determine the Right Tolerance for Your Application
To select the optimal blade tolerance, consider:
- Material properties (soft materials like plastic tolerate looser tolerances).
- Cutting speed requirements (high-speed cutting may require tighter tolerances).
- Machine precision (if the machine’s accuracy is low, ultra-precise blades won’t improve performance).
- Cost-benefit analysis (is the added precision worth the expense?).
Practical Example: Packaging Industry
A packaging company originally used ±0.02mm tolerances for their cutting blades, assuming it would improve edge precision. However, testing showed that ±0.05mm produced the same results while:
- Reducing blade costs by 25%
- Lowering production waste by 15%
- Decreasing lead times by 35%
This example highlights why evaluating application needs before setting tolerance levels is crucial.
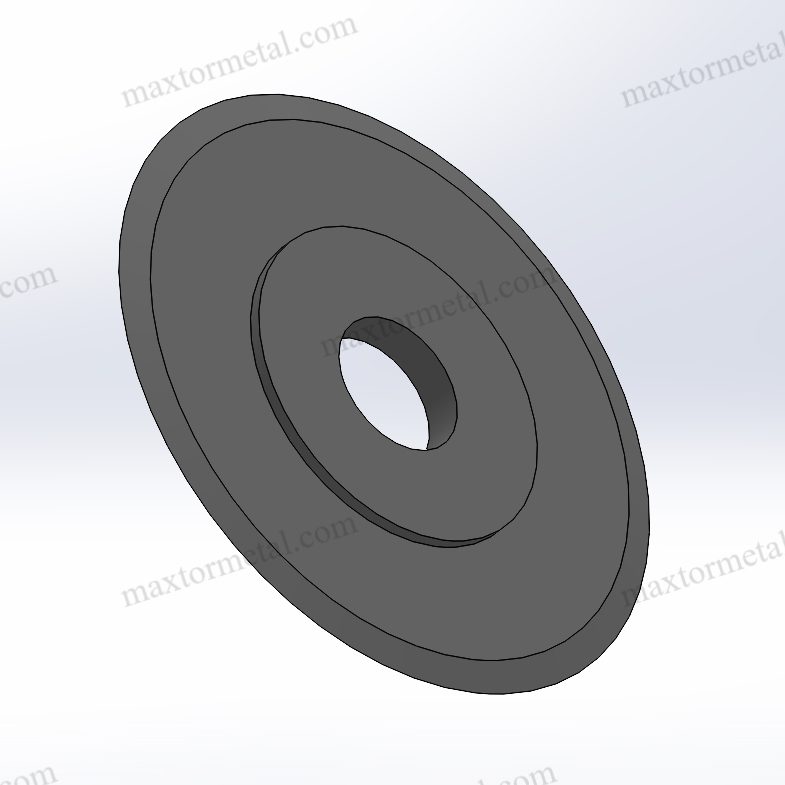
5. The Cost Implications of Overly Tight Tolerances
Choosing an unnecessarily tight industrial blade tolerance can lead to higher manufacturing costs, increased material waste, and longer production lead times. While many manufacturers assume that tighter tolerances always yield better performance, the reality is that diminishing returns often set in. Understanding these cost factors can help businesses optimize their machinery blade specifications for better efficiency and profitability.
Higher Manufacturing Costs Due to Over-Specification
The cost of producing precision industrial blades increases exponentially as tolerances become stricter. This is because tighter tolerances require:
- High-Precision Equipment
- Advanced CNC grinding, EDM (Electrical Discharge Machining), and laser cutting are needed to achieve sub-micron accuracy.
- These machines operate at slower speeds to maintain accuracy, reducing overall productivity.
- Extended Quality Control Processes
- Every batch of industrial knives must undergo more rigorous inspections, including:
- Laser scanning for dimensional accuracy
- Surface roughness measurements
- Edge sharpness consistency checks
- This increases labor costs and slows down delivery times.
- Every batch of industrial knives must undergo more rigorous inspections, including:
- Specialized Manufacturing Environments
- Temperature and humidity-controlled facilities are needed for ultra-tight tolerances (e.g., ±0.005mm).
- Even minor environmental variations can impact the final product, requiring additional process adjustments.
Example: Cost Increase for Tighter Tolerances
Tolerance Level | Manufacturing Cost Increase | Production Speed Reduction |
±0.10mm | Baseline cost | Standard speed |
±0.05mm | +15% cost | -10% speed |
±0.02mm | +40% cost | -25% speed |
±0.01mm | +75% cost | -50% speed |
From the table, we see that moving from a ±0.10mm tolerance to a ±0.01mm tolerance can increase costs by up to 75% while halving production speed. Manufacturers should carefully evaluate whether such precision is truly necessary.
Material Waste and Its Financial Impact
Tighter tolerances result in higher rejection rates. Even small deviations can cause entire batches to be discarded, increasing raw material costs and waste disposal fees.
- A ±0.01mm tolerance may require 5-10% of blades to be scrapped due to slight imperfections.
- A ±0.05mm tolerance can reduce scrap rates to below 2%, leading to significant cost savings.
Case Study: Aerospace Blade Manufacturing
An aerospace parts manufacturer initially required ±0.005mm tolerance for turbine cutting blades. However, after analyzing performance data, they found that ±0.02mm offered the same functionality. This adjustment:
✅ Reduced material waste by 35%
✅ Saved $500,000 annually in rejected blades
✅ Shortened production cycles by 20%
The Diminishing Returns of Ultra-Tight Tolerances
Beyond a certain point, tightening tolerances does not improve performance. For example:
- A ±0.02mm tolerance often performs just as well as a ±0.01mm tolerance in industrial cutting applications.
- Over-tightening tolerances does not extend blade lifespan unless machine components are also equally precise.
- Tolerances below ±0.01mm are often only necessary for specialized applications, such as semiconductor cutting or medical scalpels.
Instead of over-specifying tolerance, manufacturers can focus on blade coatings, material selection, and edge geometry to achieve superior cutting performance.
Extended Lead Times and Supply Chain Delays
- Strict tolerances require additional machining time, slowing down overall production.
- Tighter tolerances mean fewer suppliers can meet the requirements, increasing procurement risks.
- More frequent recalibrations and rework cause unexpected delays and production bottlenecks.
For high-volume industries such as food processing, packaging, and metal stamping, unnecessarily tight tolerances can double production times and delay order fulfillment.
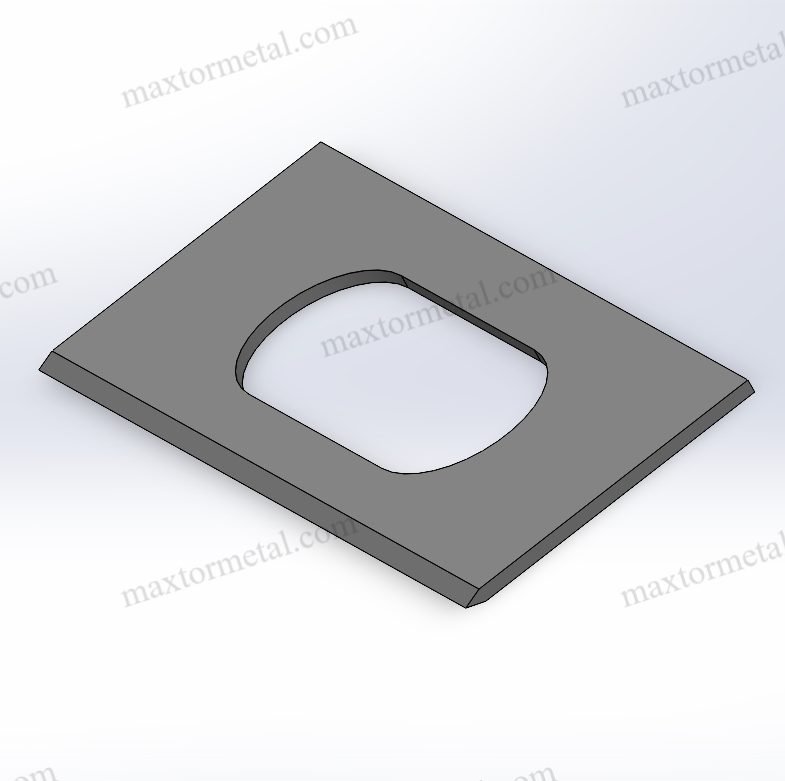
6. How Expert Consultation Can Help Optimize Blade Tolerance
At Nanjing Metal, we:
- Assess customer requirements to determine optimal blade tolerance standards.
- Provide custom industrial blades designed for specific cutting applications.
- Offer alternative solutions, such as blade coatings und material upgrades, to enhance performance without increasing tolerance requirements.
7. The Benefits of Choosing the Right Blade Tolerance
Optimizing industrial blade tolerance provides multiple long-term advantages:
1. Lower Production Costs
- Avoid unnecessary precision expenses.
- Reduce raw material waste by minimizing rejected blades.
- Simplify quality control and inspection processes.
2. Faster Lead Times
- Simpler machining processes reduce production delays.
- Less stringent quality control speeds up blade delivery.
- Broader supplier availability ensures reliable sourcing.
3. Consistent Blade Performance
- Balanced tolerances help maintain machine compatibility and cutting stability.
- Avoids excessive friction and premature blade wear.
- Supports reliable production cycles in high-speed environments.
4. Sustainable Manufacturing Practices
- Reduces material waste by selecting realistic tolerance limits.
- Lowers energy consumption by reducing excessive grinding and polishing.
- Supports lean manufacturing principles by eliminating unnecessary precision steps.
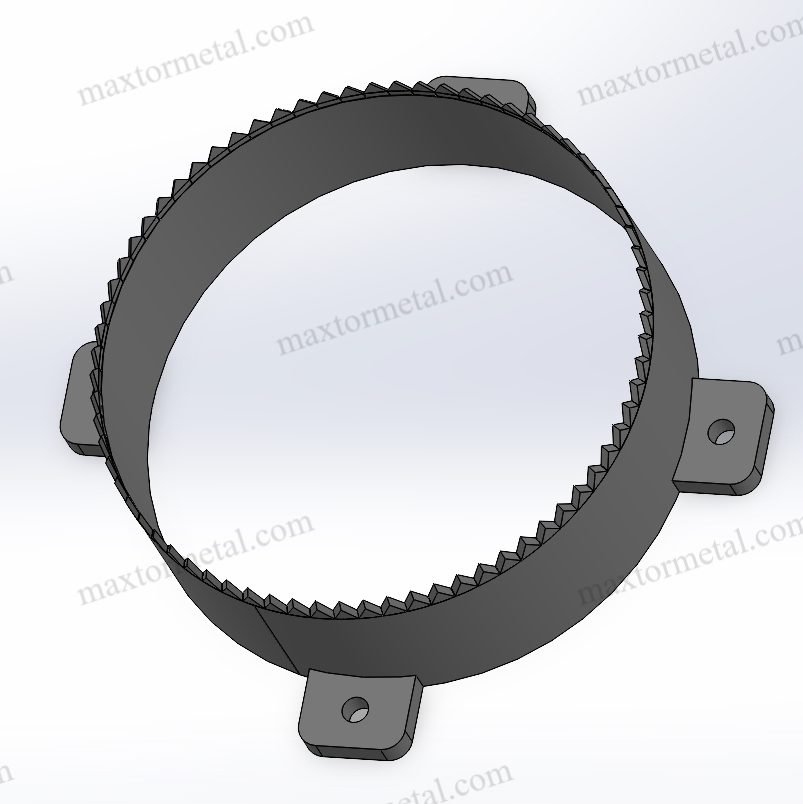
Choosing the right industrial blade tolerance is not just about precision—it’s about balancing cost, efficiency, and performance. Overly tight tolerances increase expenses without necessarily improving blade functionality.
Bei Nanjing Metal, we help clients analyze their needs, optimize tolerances, and find cost-effective solutions. Our team can assist with custom industrial blades, material upgrades, and manufacturing consultations.
📩 Kontaktieren Sie uns noch heute to optimize your blade tolerance standards and improve your production efficiency!
Verweise
- Manufacturing cost data sourced from The International Journal of Advanced Manufacturing Technology (2023).
- Performance impact of tolerances from The American Society of Mechanical Engineers (ASME) Reports.
- Industry-specific tolerance standards from ISO 2768 and ANSI B4.1.