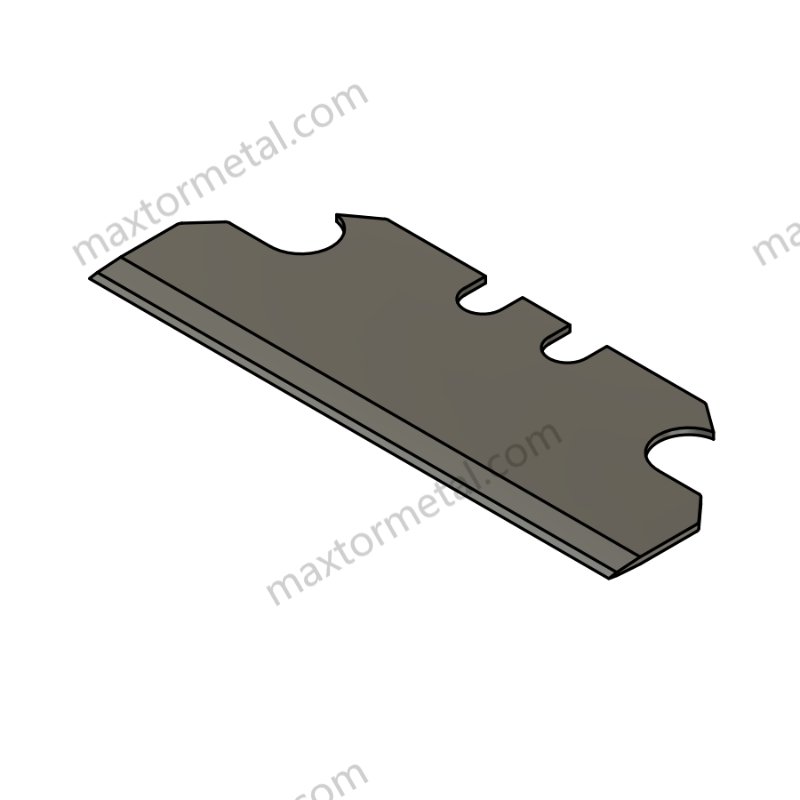
Im Bereich der modernen Fertigung haben sich Laserschneidtechniken als revolutionäre Kraft herausgestellt und neu definiert, wie Maschinenklingen und Messer hergestellt werden. Präzision, Effizienz und Vielseitigkeit sind heute Grundvoraussetzungen für die industrielle Produktion von Rotorblättern, und die Laserschneidtechnologie erfüllt diese Anforderungen nahtlos. Dieser Artikel untersucht die tiefgreifenden Auswirkungen des Laserschneidens bei der Rotorblattherstellung und wie es die Produktqualität steigert und gleichzeitig die Produktionsprozesse optimiert.
Vorteile der Laserschneidtechnologie
1. Hohe Präzision und Effizienz
Laserschneiden erreicht eine beispiellose Präzision, die es Herstellern ermöglicht, strenge Toleranzen einzuhalten. Durch Fokussierung eines hochintensiven Laserstrahls werden Materialien mit minimaler Fehlerquote geschnitten, was eine gleichbleibende Qualität über alle Chargen hinweg gewährleistet. Industriestudien zeigen beispielsweise, dass Laserschneiden eine Präzision von bis zu ±0,005 Zoll erreichen kann und damit herkömmliche Methoden bei weitem übertrifft. Darüber hinaus verkürzt es die Verarbeitungszeit erheblich und steigert die Betriebseffizienz.
2. Flexibilität
Beim Laserschneiden können verschiedene Materialien bearbeitet werden, darunter Metalle wie Edelstahl und Legierungen sowie Nichtmetalle wie Kunststoffe. Die Fähigkeit, komplizierte Designs zu verarbeiten, ermöglicht es Herstellern, Klingen und Messer mit komplexen Geometrien für unterschiedliche Anwendungen herzustellen.
3. Kosteneffizienz
Obwohl die anfänglichen Investitionen in Laserschneidmaschinen beträchtlich sein können, überwiegen die langfristigen Vorteile die Kosten. Durch die Reduzierung des Abfalls, die Minimierung des Bedarfs an zusätzlicher Verarbeitung und die Erhöhung des Durchsatzes erreichen Hersteller im Laufe der Zeit eine bessere Kosteneffizienz.
Vergleich des Laserschneidens mit herkömmlichen Methoden
Um die Überlegenheit des Laserschneidens bei der Herstellung von Maschinenklingen hervorzuheben, vergleichen wir seine Leistung mit herkömmlichen Schneidmethoden wie mechanischem Schneiden und Wasserstrahlschneiden und gehen dabei tiefer auf jeden Aspekt ein:
Aspekt | Laserschneiden | Mechanisches Schneiden | Wasserstrahlschneiden |
Präzision | ±0,005 Zoll | ±0,02 Zoll | ±0,01 Zoll |
Materialvielfalt | Behandelt Metalle, Legierungen, Nichtmetalle | Vorwiegend Metalle | Metals, Nichtmetalle, Verbundwerkstoffe |
Geschwindigkeit | Schneidet 30-40% schneller | Mäßig, muss fertiggestellt werden | Langsamer bei dicken Materialien |
Wärmeeinflusszone (WEZ) | Minimal | Hoch | Keiner |
Wartungsanforderungen | Mäßig | Hoch (Werkzeugverschleiß) | Hoch |
Umweltauswirkungen | Minimal | Mäßig | Hoch (erhebliche Wasserverschwendung) |
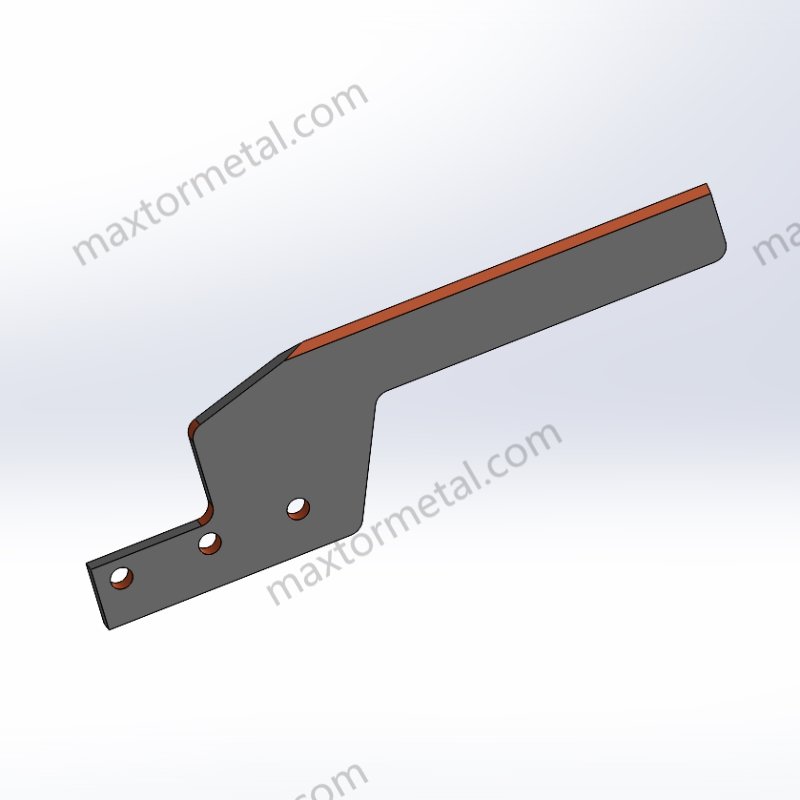
Technischer Hinweis:
- Präzision: Beim Laserschneiden werden fokussierte Strahlen verwendet, die das Material mit minimaler Schnittbreite (Schnittbreite) schmelzen oder verdampfen, wodurch hochkomplexe Muster möglich werden. Faserlaser können beispielsweise eine Schnittbreite von nur 0,1 mm erreichen.
- Materialvielfalt: Im Gegensatz zu herkömmlichen Methoden, die durch die Klingenhärte oder die Abrasivität des Wasserstrahls eingeschränkt sind, bearbeitet das Laserschneiden Materialien von 1 mm dünnen Blechen bis hin zu 25 mm dicken Metallen. Studien bestätigen seine Anpassungsfähigkeit in allen Branchen, von der Luft- und Raumfahrt bis hin zu Werkzeugen zur Lebensmittelverarbeitung.
- Umweltauswirkungen: Laser erfordern keine Verbrauchsmaterialien (z. B. Schneidöle oder Schleifmittel), was zu einem saubereren und nachhaltigeren Schneidprozess führt.
Arten von Laserschneidmaschinen
Laserschneidsysteme werden je nach Lasermedium in drei Hauptkategorien eingeteilt. Nachfolgend finden Sie eine ausführlichere Übersicht über ihre technischen Möglichkeiten und idealen Anwendungen:
Lasertyp | Primäres Medium | Anwendungen | Vorteile |
CO₂-Laser | Gas (CO₂, N₂, He) | Nichtmetalle, dünne Metalle, Holz, Kunststoffe | Erzeugt glatte Kanten, kostengünstig beim Schneiden großer Stückzahlen von Nichtmetallen |
Faserlaser | Massiv (Lichtwellenleiter) | Edelstahl, Aluminium, Messing, Kupfer | Hohe Energieeffizienz, ideal für reflektierende Metalle, schneidet schneller bei minimalem Wartungsaufwand |
Nd:YAG Laser | Fest (Kristallstab) | Präzisionsgravur, Feinschneiden von Metallen | Hervorragend geeignet für Mikrobearbeitungsaufgaben, geeignet zum Schneiden dünner Metalle und komplexer Designs |
Excimer-Laser | Gas und UV-Licht | Mikroschneiden von Polymeren, Keramik | Berührungsloses Schneiden, ideal für empfindliche Anwendungen, die eine Genauigkeit im Mikrometerbereich erfordern |
Technische Einblicke:
- Mit₂ Laser dominieren bei Anwendungen, die glatte, polierte Schnitte erfordern, und erreichen Oberflächen mit Rauheitswerten von nur Ra 3,2 μm.
- Faserlaser, angetrieben von Dioden, bietet der 50% im Vergleich zu CO₂-Lasern höhere Schnittgeschwindigkeiten für dünne Metalle und reflektierende Materialien.
Schritte im Klingenlaserschneidprozess
Für die Herstellung präziser Klingen ist es entscheidend, den gesamten Laserschneidprozess zu verstehen. Jeder Schritt gewährleistet Konsistenz, Qualität und Kundenzufriedenheit.
- Entwurfsphase
- Beginnt mit der CAD-Modellierung und stellt sicher, dass das Design Fertigungstoleranzen und materialspezifische Einschränkungen berücksichtigt.
- Mithilfe einer Lasersimulationssoftware wird die Verschachtelung (Anordnung der Teile auf dem Blech) optimiert, wodurch der Materialabfall um bis zu 20 % reduziert wird.
- Laserschneiden
- Ein fokussierter Laserstrahl, oft unterstützt durch Gase wie Sauerstoff oder Stickstoff, schneidet durch Materialien. Die Gasunterstützung kühlt den Schnitt und entfernt geschmolzenes Material für saubere Kanten.
- Moderne Systeme wie CNC-gesteuerte Faserlaser erreichen Schneidgeschwindigkeiten von bis zu 100 m/min bei dünnen Blechen.
- Qualitätskontrolle
- Automatisierte Werkzeuge wie Koordinatenmessgeräte (KMG) und Laserscanner stellen sicher, dass die endgültigen Abmessungen den Kundenspezifikationen mit einer Toleranz von ±0,01 mm entsprechen.
- Durch die Probenvalidierung wird sichergestellt, dass die Kanten glatt und die Materialintegrität gegeben sind und keine thermischen Verformungen auftreten.
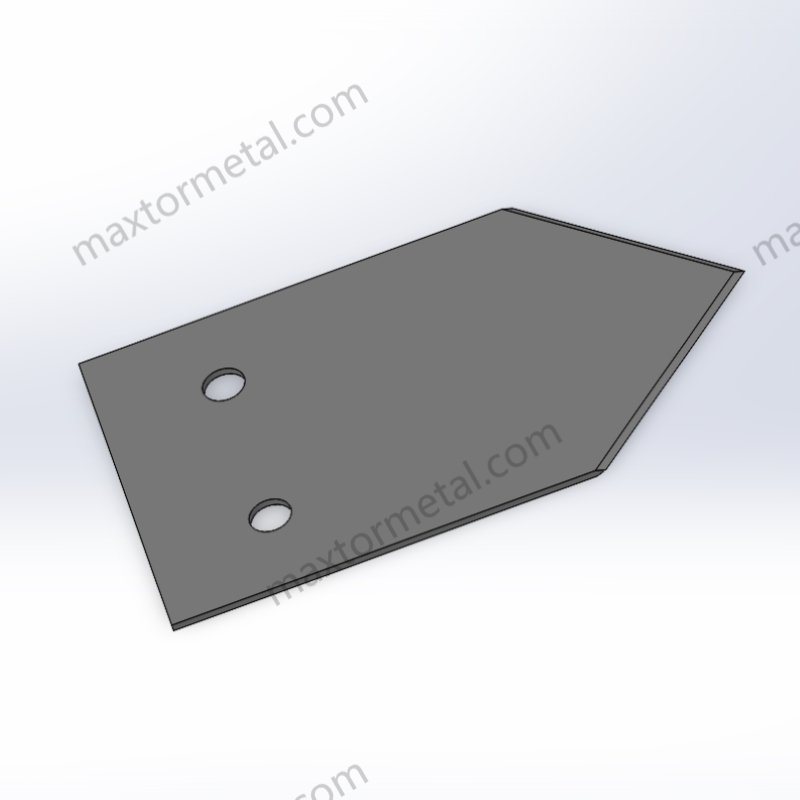
Anwendungen in verschiedenen Materialien
Die Anpassungsfähigkeit der Laserschneidtechnologie macht sie zu einem Eckpfeiler bei der Verarbeitung einer Vielzahl von Materialien. Hier ist eine ausführliche Analyse:
1. Metal Schneiden
Laserschneidsysteme sind weithin für ihre Effizienz bei der Bearbeitung von Metallmaterialien bekannt, einem entscheidenden Aspekt bei der industriellen Klingenherstellung.
- Edelstahl: Ideal für hochpräzise Klingen. Kann mit Faserlasern bis zu einer Dicke von 15 mm geschnitten werden, ohne dass die Kanten glatt werden. Die hohe Reflektivität von Edelstahl lässt sich mit Faserlasern mit einstellbaren Wellenlängen effektiv bewältigen.
- Werkzeugstahl: Wird häufig für Maschinenklingen verwendet und profitiert von der Fähigkeit des Laserschneidens, die Wärmeeinflusszone (WEZ) zu minimieren, die normalerweise weniger als 0,1 mm beträgt. Dadurch wird sichergestellt, dass die Härte und Festigkeit des Stahls erhalten bleiben.
- Leistungsstatistiken: Studien von Laser Focus World zeigen, dass das Laserschneiden die Nachbearbeitungszeit im Vergleich zu herkömmlichen Methoden um bis zu 501 TP4T reduziert.
Technischer Hinweis: Bei Metallen wie Kohlenstoffstahl wird häufig sauerstoffunterstütztes Schneiden eingesetzt. Der Sauerstoff reagiert mit dem Material und erzeugt einen exothermen Effekt, der die Schnittgeschwindigkeit erhöht, insbesondere bei dickeren Materialien.
2. Nicht-Metal-Schneiden
Nichtmetallische Materialien, darunter Kunststoffe, Verbundwerkstoffe und Keramik, erfordern Präzision und Feingefühl, die nur durch Laserschneiden erreicht werden können.
- Kunststoffe: Materialien wie Acryl und Polycarbonat können mit CO₂-Lasern geschnitten werden, wodurch polierte Kanten ohne Risse oder thermische Verformung erzielt werden.
- Verbundwerkstoffe: Diese Materialien stellen aufgrund ihrer mehrschichtigen Struktur eine Herausforderung dar. Das Laserschneiden gewährleistet saubere Kanten ohne Delamination, was bei mechanischen Methoden oft ein Problem darstellt.
- Einblicke in die Leistung: Laut einem Branchenbericht der Plastics Innovation Research Group aus dem Jahr 2023 erreicht das Laserschneiden bei Nichtmetallen im Vergleich zu Routersystemen 20-30% schnellere Produktionszeiten.
Umwelteinblick: Das Laserschneiden von Nichtmetallen ist umweltfreundlich, da es auf den Einsatz von Wasser oder chemischen Kühlmitteln verzichtet, die bei herkömmlichen Methoden häufig zum Einsatz kommen.
3. Herausforderungen und Lösungen
Bestimmte Materialien, insbesondere reflektierende Metalle wie Aluminium und Kupfer, stellen beim Laserschneiden besondere Herausforderungen dar.
- Reflektierende Metals:
- Herausforderung: Eine hohe Reflektivität kann den Laserstrahl streuen, was die Effizienz verringert und möglicherweise zu Geräteschäden führt.
- Lösung: Moderne Faserlaser verfügen über Antireflexoptiken und Wellenlängenoptimierung und sorgen so für stabile und effiziente Schnitte. Durch zusätzliche Strahlabsorber werden reflexionsbedingte Verluste zusätzlich gemindert.
- Materialstärke:
- Herausforderung: Das Schneiden von Materialien mit einer Dicke von über 20 mm erfordert eine höhere Laserleistung und führt häufig zu einer größeren Wärmeeinflusszone.
- Lösung: Mehrdurchgangs-Schneidstrategien und Hybridlasersysteme (Kombination von CO₂- und Faserlasern) bewältigen dicke Materialien effektiv und halten dabei die Qualität aufrecht.
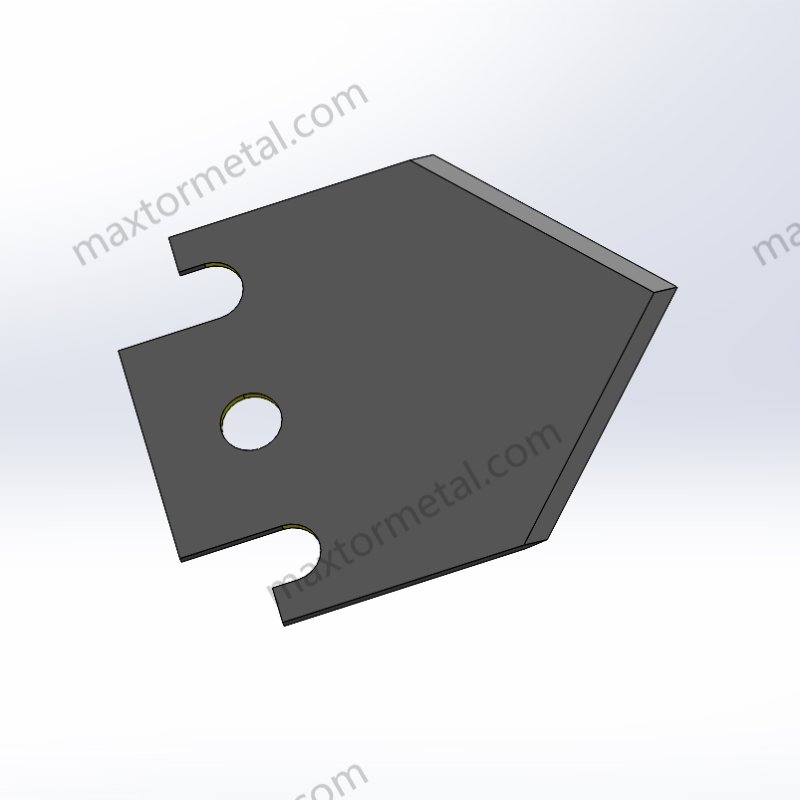
Materialauswahl für die Rotorblattherstellung
Die Auswahl der richtigen Materialien ist von entscheidender Bedeutung für die Leistung und Herstellbarkeit von Maschinenblättern.
1. Gemeinsame Materialien
Material | Eigenschaften | Anwendungen |
Edelstahl | Korrosionsbeständig, langlebig, hohe Zugfestigkeit | Lebensmittelverarbeitung, Industrieklingen |
Kohlenstoffstahl | Hohe Härte, hervorragende Schnitthaltigkeit | Industrielle Schneidwerkzeuge, Scheren |
Hochgeschwindigkeitsstahl | Hitzebeständig, behält die Schneide auch bei hohen Temperaturen | Präzisionsschneidwerkzeuge |
Brancheneinblick: Laut Angaben der World Steel Association entfallen 40 % der industriellen Klingenproduktion auf rostfreien Stahl, was auf seine Korrosionsbeständigkeit und Kompatibilität mit Laserschneidtechniken zurückzuführen ist.
2. Einfluss des Lasers auf Materialeigenschaften
Das Laserschneiden beeinflusst direkt die mechanischen und Oberflächeneigenschaften von Rotorblattmaterialien:
- Wärmeeinflusszone (WEZ):
Die WEZ ist ein kritischer Parameter bei der Materialverarbeitung. Beim Laserschneiden beträgt die WEZ normalerweise weniger als 0,1 mm, wodurch die Mikrostruktur des Materials erhalten bleibt. Dies ist eine erhebliche Verbesserung gegenüber dem mechanischen Schneiden, bei dem die WEZ bis zu 1 mm betragen kann. - Oberflächenrauheit:
Durch Laserschneiden entstehen glatte Oberflächen mit Rauheitswerten bis zu Ra 3,2 μm, wodurch der Bedarf an zusätzlichen Endbearbeitungsprozessen minimiert wird. - Kantenqualität:
Lasergeschnittene Kanten sind gratfrei und gewährleisten präzise Passungen bei Montageprozessen. Im Gegensatz dazu sind beim mechanischen Schneiden häufig sekundäre Entgratungsprozesse erforderlich.
Forschungshighlight: Eine Studie veröffentlicht im Zeitschrift für fortschrittliche Fertigungsprozesse (2023) stellten fest, dass Klingen, die durch Laserschneiden hergestellt wurden, eine 25% höhere Haltbarkeit und 15% längere Schnitthaltigkeit aufwiesen als Klingen, die mit herkömmlichen Methoden hergestellt wurden.
Wartung und Pflege von lasergeschnittenen Klingen
Die ordnungsgemäße Wartung lasergeschnittener Klingen gewährleistet Spitzenleistung, Langlebigkeit und Sicherheit. Vernachlässigung der Wartung kann zu suboptimaler Schneidleistung, erhöhtem Verschleiß und potenziellen Sicherheitsrisiken führen. Im Folgenden gehen wir näher auf diese Aspekte ein.
1. Verlängerung der Klingenlebensdauer
- Reinigungsprotokolle:
Durch regelmäßiges Reinigen werden Rückstände wie Klebstoffe, Rost oder Schmutz entfernt, die sich auf der Oberfläche der Klinge ansammeln. Bei Industrieklingen ist die Ultraschallreinigung äußerst effektiv, um komplizierte Kanten und Muster zu erreichen. - Schmierverfahren:
Hochwertige Schmierstoffe, die speziell für Schneidwerkzeuge entwickelt wurden, reduzieren Reibung und Betriebsbelastung. So verlängern synthetische Schmierstoffe die Lebensdauer von Klingen im Vergleich zu herkömmlichen Ölen um bis zu 30 %. Dies geht aus einer Studie der Zeitschrift für Schneidwerkzeugtechnik (2023). - Lagerbedingungen:
Um Korrosion zu vermeiden, sollten Klingen in einer klimatisierten, feuchtigkeitsfreien Umgebung gelagert werden. Vakuumversiegelte Verpackungen oder Korrosionsschutzpapier können Metalloberflächen bei längerer Lagerzeit zusätzlich schützen.
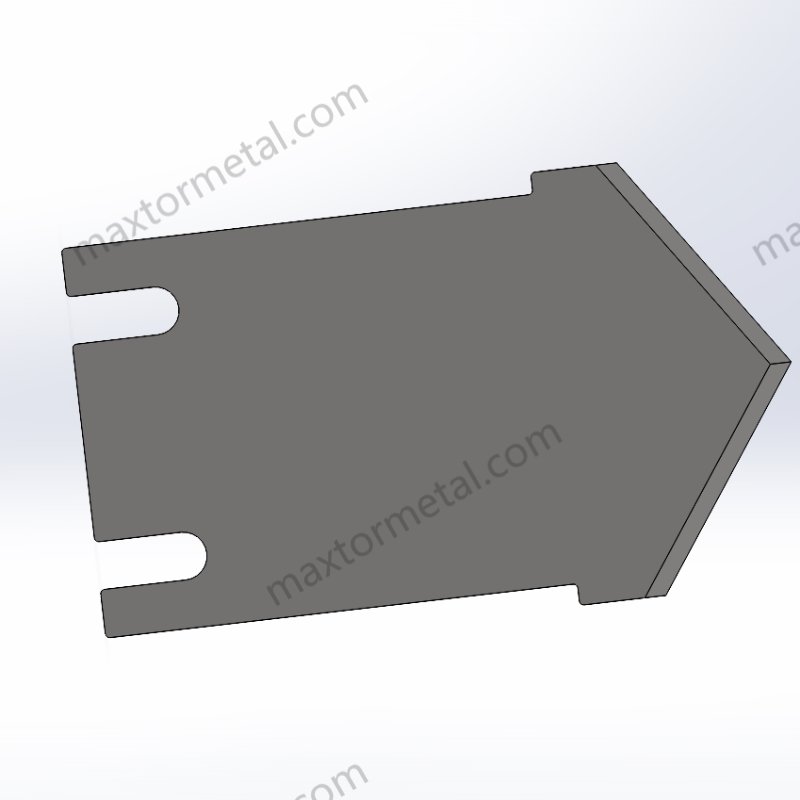
2. Erweiterte Wartungspraktiken
- Edge-Monitoring mit Technologie:
Mit Tools wie digitale Profilometer ermöglicht es Herstellern, die Schärfe der Schneide zu überwachen und Mikroschäden zu erkennen, die mit bloßem Auge nicht zu erkennen sind. Diese Geräte können Verschleißmuster beurteilen und vorhersagen, wann ein Nachschärfen erforderlich ist. - Regelmäßiges Schärfen:
Bei lasergeschnittenen Klingen sollte das Nachschärfen mit CNC-Schleifmaschinen durchgeführt werden, um gleichmäßige Fasenwinkel und Schneidkantengeometrie zu gewährleisten. Studien zeigen, dass präzises Nachschärfen die Betriebseffizienz um 20-25% erhöht. - Thermische Inspektion:
Beim Laserschneiden können geringe thermische Spannungen entstehen. Die Klingen sollten regelmäßig mithilfe von Infrarotkameras oder Wärmebildgeräten auf hitzebedingte Verformungen untersucht werden.
3. Tipps zur täglichen Wartung
Wartungsaufgabe | Frequenz | Hauptvorteile |
Reinigen der Klingenoberfläche | Nach jedem Gebrauch | Verhindert Korrosion und Rückstandsbildung |
Visuelle Schadensprüfung | Täglich | Erkennt frühzeitig Risse, Absplitterungen oder abgenutzte Kanten |
Kantennachschärfung | Wöchentlich oder nach Bedarf | Behält die Schneideffizienz und -präzision bei |
Richtige Lagerung | Laufend | Reduziert die Belastung durch Feuchtigkeit und Schadstoffe |
Branchentrends und Zukunft
Die Laserschneidtechnologie entwickelt sich rasant weiter und treibt Innovationen in der Herstellung von Maschinenklingen voran. Im Folgenden sind einige wichtige Trends aufgeführt, die die Zukunft der Branche prägen:
1. Fortschritte in der Lasertechnologie
- Ultrakurzpulslaser:
Diese Laser arbeiten im Femtosekundenbereich (10⁻¹⁵ Sekunden) und ermöglichen hochpräzises Schneiden ohne wärmebeeinflusste Zonen. Dies ist besonders vorteilhaft für dünne oder empfindliche Materialien wie Mikroklingen für medizinische Anwendungen.
Brancheneinblick: Forschung von Zeitschrift für Photonik (2023) gibt an, dass ultraschnelle Laser Präzisionsverbesserungen von bis zu 40% erreichen, insbesondere beim Schneiden spröder Materialien wie Keramik.
- Grüne Laser:
Grüne Laser bieten eine verbesserte Strahlabsorption, da ihre Wellenlängen für das Schneiden reflektierender Metalle wie Kupfer und Gold optimiert sind. Ab 2024 berichten Hersteller, die grüne Laser verwenden, von einer höheren Effizienz bei der Bearbeitung reflektierender Materialien.
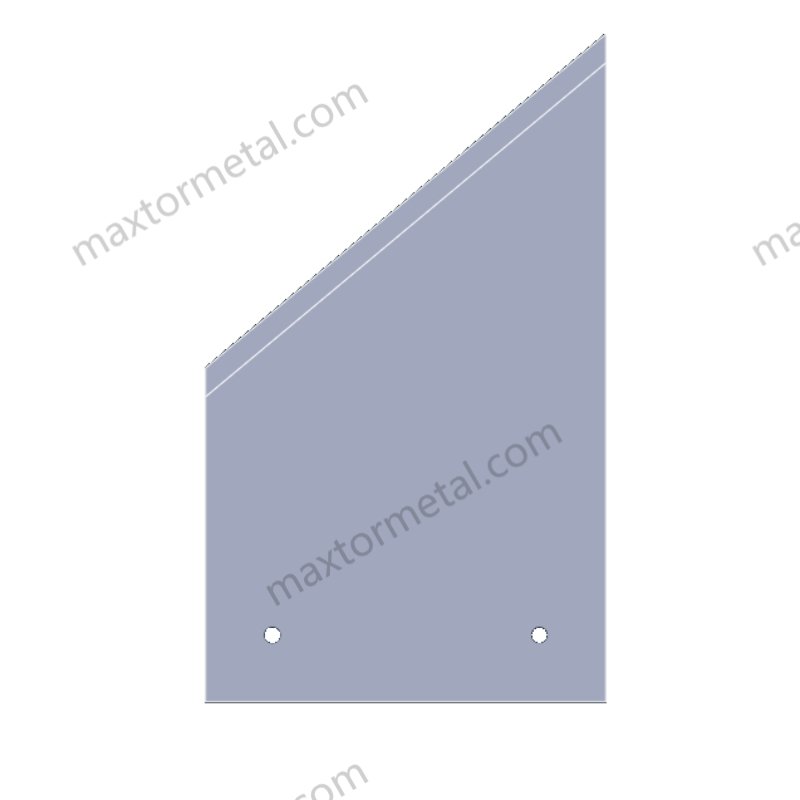
2. Automatisierung und intelligente Fertigung
- KI-Integration:
Künstliche Intelligenz wird eingesetzt, um Schneidewege zu optimieren, Materialverschwendung zu reduzieren und die Maschinenverfügbarkeit zu verbessern. KI-gestützte Systeme können Schneidedaten in Echtzeit analysieren, um Einstellungen dynamisch anzupassen und so Fehler um bis zu 50 % zu reduzieren. - Predictive Maintenance per IoT:
In Schneidemaschinen integrierte IoT-Sensoren überwachen kritische Komponenten wie Linsen und Düsen. Prädiktive Algorithmen analysieren diese Daten, um Wartungsarbeiten zu planen, bevor Fehler auftreten. So werden Ausfallzeiten um bis zu 40%. - Robotik und Automatisierung:
Zur Automatisierung der Rotorblattherstellung gehören Roboter-Handlingsysteme für die Materialzufuhr zu Laserschneidern und die Sortierung nach dem Schnitt. Diese Innovationen rationalisieren die Prozesse und ermöglichen eine Produktion rund um die Uhr mit minimalem menschlichen Eingriff.
3. Nachhaltigkeit beim Laserschneiden
- Energieeffizienz:
Moderne Faserlaser verbrauchen 30% weniger Energie als herkömmliche CO₂-Laser und tragen so zu umweltfreundlicheren Herstellungsprozessen bei. - Weniger Abfall:
Fortschrittliche Verschachtelungsalgorithmen reduzieren Materialverschwendung, indem sie das Layout der Klingendesigns auf Blechen optimieren. Durch Verschachtelung können bis zu 15% Rohmaterial pro Charge eingespart werden, wie aus einem Bericht von 2023 hervorgeht Fertigungsüberprüfung.
4. Neue Trends in der Rotorblattherstellung
- Hybrid-Schneidsysteme:
Durch die Kombination von CO₂- und Faserlasern bieten Hybridsysteme mehr Flexibilität beim Schneiden unterschiedlicher Materialien in einer einzigen Maschine. - Mikrofertigungsanwendungen:
Im Zuge der branchenübergreifenden Miniaturisierung werden Laserschneidsysteme für die Mikrobearbeitung maßgeschneidert, mit denen Klingen mit Details ab 10 Mikrometern hergestellt werden können.
Schlussfolgerung
Laserschneiden ist zu einem Eckpfeiler in der Herstellung von Maschinenklingen geworden und bietet unübertroffene Präzision, Effizienz und Vielseitigkeit. Nanjing Metal, Wir nutzen modernste Lasertechnologie und 18 Jahre Erfahrung, um qualitativ hochwertige, maßgeschneiderte Klingen. Werden Sie unser Partner und erleben Sie die nächste Stufe der Präzision in der Klingenherstellung. Kontaktieren Sie uns noch heute für eine kostenlose Beratung und entdecken Sie unsere maßgeschneiderten Lösungen.
Verweise
- Laser-Institut von Amerika – Jahresbericht zur Laserschneidtechnologie, 2023
- Einblicke von McKinsey in die Fertigung – „Smart Manufacturing Trends“, 2023
- Zeitschrift für fortgeschrittene Fertigung – „Laserschneiden in der Industrie: Präzision und Effizienz“, 2022
- Zeitschrift für Materialwissenschaft – „Einfluss wärmebeeinflusster Zonen auf Schneidprozesse“, 2023
- Zeitschrift für Schneidwerkzeugtechnik– „Maximierung der Werkzeuglebensdauer durch fortschrittliche Wartungspraktiken“, 2023
- Zeitschrift für Photonik – „Femtosekundenlaser: Präzisionsfertigung neu definiert“, 2023
- Fertigungsüberprüfung – „Nachhaltigkeit bei Laserschneidprozessen“, 2023
- Zeitschrift für fortgeschrittene Fertigung – „KI und IoT in der vorausschauenden Wartung für Lasersysteme“, 2023
- Weltstahlverband – „Materialtrends bei industriellen Schneidanwendungen“, 2023