Die Reifenindustrie ist hart umkämpft und stellt hohe Anforderungen an Präzision und Langlebigkeit. Der Schlüssel zur Aufrechterhaltung hoher Produktivität und zur Minimierung der Kosten liegt in der Verwendung der richtigen Werkzeuge, insbesondere der im gesamten Produktionsprozess eingesetzten Klingen und Messer. Hochleistungs-Industrieklingen für die Reifenherstellung sind von entscheidender Bedeutung für die Optimierung der Produktionseffizienz und die Senkung der Betriebskosten.
Bei Nanjing MetalWir wissen, wie wichtig hochwertige Klingen sind, die den hohen Anforderungen der Reifenproduktion standhalten. Mit einer langen Tradition von Innovation und Handwerkskunst bietet Nanjing Metal Reifenherstellern innovative Lösungen.
In diesem Leitfaden erfahren Sie, wie Sie die richtigen Klingen für die Reifenherstellung auswählen. Dabei liegt der Schwerpunkt auf Klingenmaterialien, Anwendungen und deren Wartung.
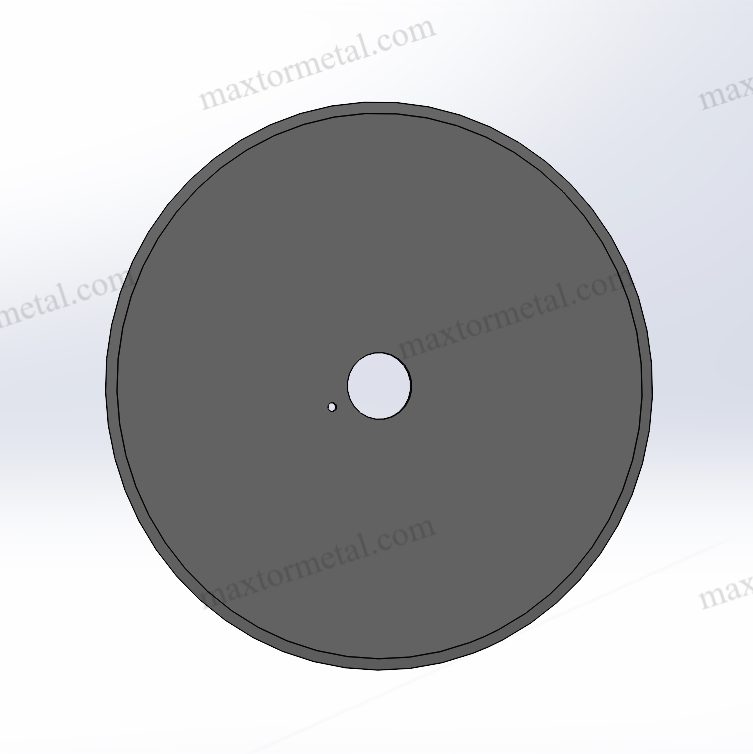
1. Leitfaden zur Auswahl von Klingen für die Reifenindustrie
Um die richtigen Klingen für die Reifenherstellung auszuwählen, müssen mehrere Schlüsselfaktoren verstanden werden:
- Materialtyp
- Haltbarkeit
- Anwendungsspezifische Anforderungen
1.1 Materialauswahl: Kohlenstoffstahl, Edelstahl und legierter Stahl
Je nach Aufgabe bieten unterschiedliche Materialien unterschiedliche Vorteile. Nachfolgend finden Sie einen Vergleich gängiger Klingenmaterialien in der Reifenherstellung:
Klingentyp | Vorteile | Einschränkungen | Typische Anwendungen |
Kohlenstoffstahl | Scharfe Schnitthaltigkeit, kostengünstig, hohe Härte | Anfällig für Rost, geringere Korrosionsbeständigkeit | Gummimischung, Weichgummischneiden |
Edelstahl | Korrosionsbeständig, präzise Schnitte, langlebig | Teurer als Kohlenstoffstahl | Trimmen, Veredeln, Hygieneanwendungen |
Legierter Stahl | Hohe Verschleißfestigkeit, lange Lebensdauer, hohe Belastbarkeit | Teuer, erfordert spezielle Handhabung | Schlitzen, Hochleistungsschneiden, verstärkter Gummi |
Wolframkarbid | Extrem langlebig, hervorragend für Präzision, behält die Schärfe länger | Hohe Anschaffungskosten, spröder als andere Stähle | Präzisionsschneiden, Reifenfinish |
Wichtigste Erkenntnis: Beim Schneiden von weichem Gummi ist Kohlenstoffstahl möglicherweise kostengünstiger, aber in Bezug auf Haltbarkeit und Langzeitleistung sind legierter Stahl und Edelstahl oft überlegen. Die Kenntnis Ihrer Produktionsanforderungen hilft bei der Materialauswahl.
1.2 Klingenanwendungen: Schneiden, Trimmen, Schlitzen und mehr
Die Reifenproduktion umfasst mehrere Schritte, für die unterschiedliche Klingentypen erforderlich sind. Lassen Sie uns die einzelnen Anwendungen genauer betrachten:
- Schneidklingen: Diese Klingen sind hauptsächlich für das Schneiden großer Gummiplatten konzipiert. Typischerweise werden hierfür Klingen aus Kohlenstoffstahl oder legiertem Stahl verwendet.
- Trimmklingen: Nachdem die Reifenform geformt ist, muss überschüssiges Gummi abgeschnitten werden. Klingen aus rostfreiem Stahl werden aufgrund ihrer Korrosionsbeständigkeit und sauberen Schneideigenschaften oft bevorzugt.
- Schlitzklingen: Diese werden zum Zuschneiden von Reifen auf ihre endgültige Breite verwendet. Sägeblätter aus legiertem Stahl sind hier aufgrund ihrer Langlebigkeit und Widerstandsfähigkeit gegen Schnitte mit hoher Belastung die beste Wahl.
Die Auswahl des Klingentyps für jede Anwendung gewährleistet hochwertige Ergebnisse und maximiert die Produktivität.
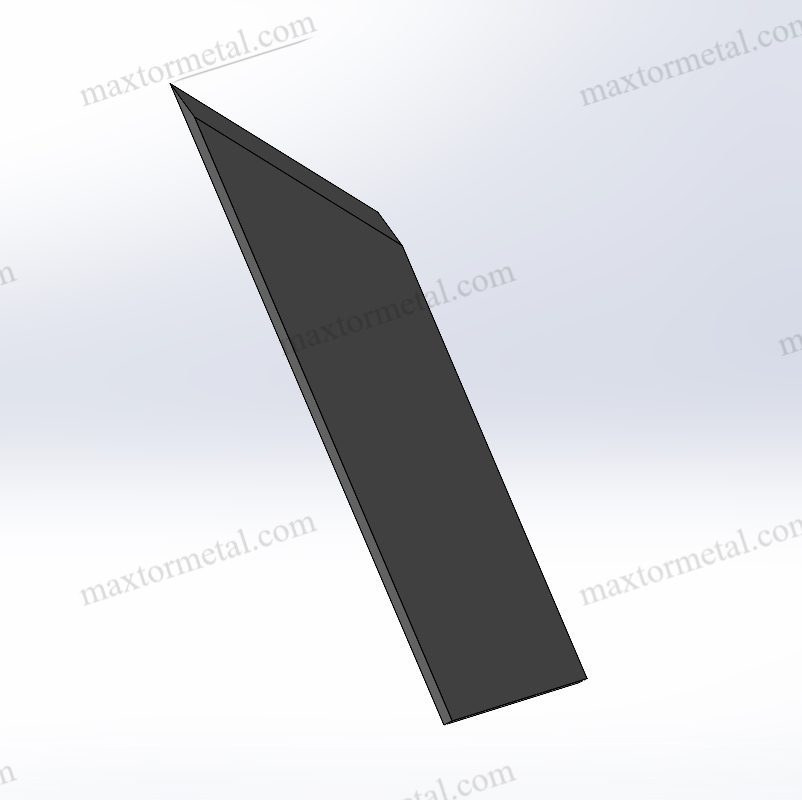
2. Industrielle Klingen in der Reifenherstellung
Industrielle Klingen spielen eine entscheidende Rolle für Präzision, Effizienz und die Reduzierung von Materialabfall im gesamten Reifenherstellungsprozess. Von der Gummimischung bis zur Endbearbeitung gewährleisten Klingen, dass jeder Schritt der Reifenproduktion strenge Qualitäts- und Haltbarkeitsstandards erfüllt. Hier finden Sie einen ausführlicheren und detaillierteren Überblick über die Funktionsweise verschiedener Klingen in den verschiedenen Phasen der Reifenherstellung.
2.1 Kautschukmischung: Schneidklingen
Anwendung: In dieser Phase der Gummimischung werden Rohstoffe wie Gummi, Ruß, Öle und andere Additive miteinander vermischt. Mit Schneidklingen wird Rohgummi vor dem Mischen in handliche Stücke geschnitten und zerkleinert. Dies ist ein entscheidender Schritt für gleichbleibende Materialeigenschaften und optimale Mischleistung.
- Klingentyp: Klingen aus Kohlenstoffstahl (oft bevorzugt)
- Hauptmerkmale: Klingen aus Kohlenstoffstahl sind scharf und schnitthaltig und ermöglichen so ein schnelles und effizientes Schneiden zäher Gummimischungen. Sie werden aufgrund ihrer Wirtschaftlichkeit insbesondere beim Schneiden weicher bis mittelharter Gummimischungen eingesetzt.
- Blade-LeistungDie Schneidleistung hängt auch von Faktoren wie der Klingengeometrie und der zu verarbeitenden Gummiart ab. Beispielsweise eignen sich Klingen mit spezifischen Kantenprofilen besser zum Schneiden unterschiedlich dicker Gummiplatten, was den Verschleiß der Klingen während des Betriebs verringern kann.
2.2 Reifenformung: Trimmklingen
Anwendung: Nach der Reifenformung muss überschüssiges Gummi vom Reifen abgeschnitten werden. Mit Schneidklingen werden überschüssiges Gummi entfernt und die exakte Reifenform sichergestellt.
- Klingentyp: Klingen aus rostfreiem Stahl (am häufigsten verwendet)
- Hauptmerkmale: Edelstahlklingen sind äußerst korrosionsbeständig und eignen sich daher ideal für hochpräzise Arbeiten wie das Zuschneiden von Formreifen. Diese Klingen können bei hohen Geschwindigkeiten arbeiten, ohne an Schärfe zu verlieren, und bieten saubere Schnitte und eine präzise Kantenbildung.
- Leistungsmetriken: Schneidklingen aus Edelstahl tragen außerdem dazu bei, Fehler nach dem Formen, wie z. B. ungleichmäßige Reifendicken, zu reduzieren. Durch die verbesserte Schneidpräzision tragen diese Klingen direkt zu weniger Materialabfall und einer besseren Reifenqualität bei.
2.3 Reifenschlitzen: Schlitzklingen
Anwendung: Schneidklingen sind entscheidend, um große Reifenrollen auf die endgültige Breite und Form zu bringen. Dieser Schritt ist notwendig, um Reifen mit präzisen Abmessungen und Eigenschaften herzustellen, die den spezifischen Leistungsanforderungen entsprechen.
- Klingentyp: Klingen aus legiertem Stahl (bevorzugt für Schneidearbeiten)
- Hauptmerkmale: Klingen aus legiertem Stahl bieten höchste Haltbarkeit und Hitzebeständigkeit. Ihre Robustheit gewährleistet, dass sie dem hohen Druck und der Kraft standhalten, die zum Schneiden von verstärktem Gummi und Stahlgürtelreifen erforderlich sind, ohne übermäßigen Verschleiß zu erleiden.
- Wichtige Überlegungen: Die Effektivität von Schlitzklingen hängt auch von der Geometrie der Klinge ab, beispielsweise vom Kantenwinkel und der Klingendicke. Durch die Optimierung dieser Faktoren können die Schlitzpräzision und die Schnittgeschwindigkeit weiter verbessert werden.
2.4 Reifenfinish: Präzisionsschneidklingen
Anwendung: Im letzten Schritt werden die Reifenkanten, insbesondere die Seitenwände, verfeinert, um ein gleichmäßiges, glattes Erscheinungsbild zu gewährleisten. Mit Präzisionsklingen werden diese Kanten beschnitten und überschüssiges Gummi entfernt, ohne die Reifenstruktur zu beschädigen.
- Klingentyp: Klingen aus Wolframkarbid (oder beschichtete Stahlklingen)
- Hauptmerkmale: Hartmetallklingen sind extrem hart und verschleißfest und eignen sich daher ideal für präzise Schnitte in der Endbearbeitung. Selbst bei häufigem Einsatz in Hochgeschwindigkeitsprozessen bleiben die Klingen lange scharf.
- Leistungsmetriken: Hartmetallklingen verbessern zudem die Kantenqualität, indem sie sicherstellen, dass keine Unregelmäßigkeiten oder unerwünschte Grate am Reifen zurückbleiben. Reifen mit glatten, gleichmäßigen Seitenwänden sehen optisch ansprechender aus und bieten eine bessere Leistung in Bezug auf Aerodynamik und Balance.
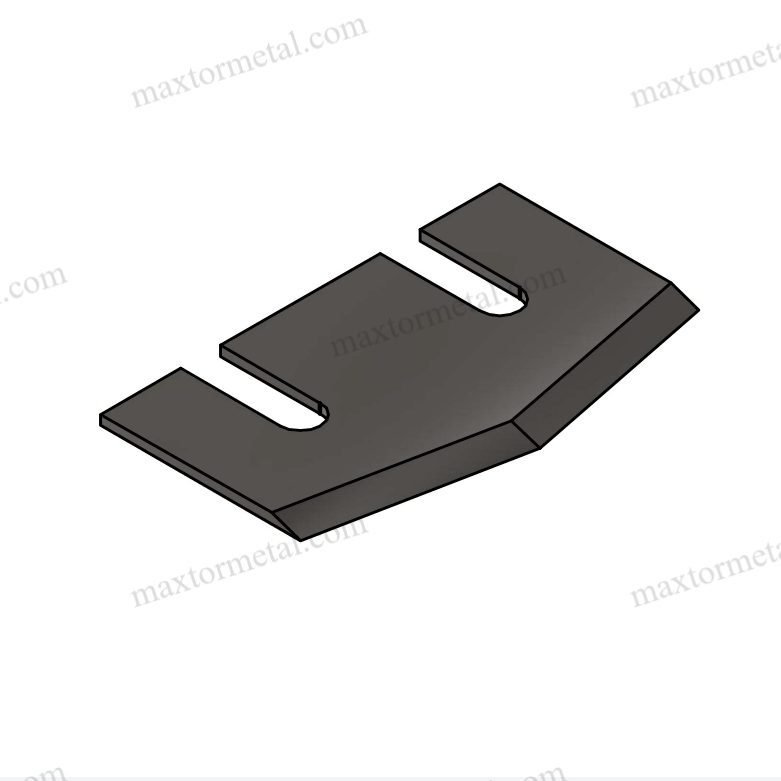
3. Hochleistungs-Industrieklingen: Vorteile
3.1 Höhere Produktionseffizienz
Hochleistungsklingen verbessern die Schnittgeschwindigkeit und -präzision, was sich direkt in einer höheren Produktionseffizienz niederschlägt. Der Effizienzgewinn resultiert nicht nur aus höheren Schnittgeschwindigkeiten, sondern auch aus reduzierten Ausfallzeiten durch Klingenwechsel. Eine Studie, die in Das Internationale Journal für Wirtschaftsingenieurwesen (2021) kam zu dem Schluss, dass Reifenhersteller, die Hochleistungsklingen verwenden, aufgrund geringerer Ausfallzeiten und weniger Klingenwechsel eine Steigerung der Produktionsraten um 20% verzeichnen konnten.
3.2 Längere Klingenlebensdauer
Hochwertige Industrieklingen halten auch längerem Gebrauch stand, ohne an Schärfe oder Integrität zu verlieren. Beispielsweise können Klingen aus legiertem Stahl, die für schwere Schneidarbeiten in der Reifenherstellung verwendet werden, bis zu 2,5-mal länger halten als ihre Pendants aus Kohlenstoffstahl. Die Internationale Kautschukstudiengruppe hat festgestellt, dass sich die Kosten für den Klingenaustausch im Laufe eines Jahres um 40% senken lassen, wenn man auf eine Klinge aus hochwertigem legiertem Stahl umsteigt.
3.3 Reduzierte Ausfallzeiten
Langlebige Klingen, die seltener ausgetauscht werden müssen, reduzieren ungeplante Ausfallzeiten. Hochleistungsklingen bleiben in der Regel länger scharf und liefern gleichmäßige Schneidergebnisse, sodass häufiges Nachjustieren seltener erforderlich ist.
- Branchendaten: Laut einem Bericht der Nationaler Verband der Gummihersteller (2022) verzeichneten Reifenhersteller, die langlebige Hochleistungsklingen verwendeten, 40% weniger ungeplante Ausfallzeiten als Hersteller mit Standardklingen. Die verbesserte Zuverlässigkeit der Hochleistungsklingen steigerte die Effizienz der Produktionslinie deutlich.
3.4 Kostensenkung
Hochleistungsklingen sind zwar mit höheren Anschaffungskosten verbunden, doch ihre längere Lebensdauer, die verbesserte Schneidleistung und der geringere Wartungsaufwand führen langfristig zu Einsparungen. Hersteller, die in hochwertige Klingen investieren, erzielen häufig eine Senkung der Gesamtkosten pro produzierter Einheit.
- Wirtschaftsdaten: Die Studie zur Herstellungskostenanalyse (2022) fanden heraus, dass Hersteller, die Hochleistungsklingen verwenden, dank der höheren Produktivität und des geringeren Bedarfs an Klingenwechseln jährlich bis zu 18% an Betriebskosten einsparen könnten.
Die Investition in hochwertige Klingen hilft Reifenherstellern nicht nur, eine gleichbleibende Produktion zu gewährleisten, sondern führt langfristig auch zu erheblichen Einsparungen. Klingen, die dauerhaft scharf bleiben, hohen Schnittbelastungen standhalten und nur minimalen Wartungsaufwand erfordern, sind entscheidend für eine nachhaltige Kosteneffizienz in der Reifenproduktion.
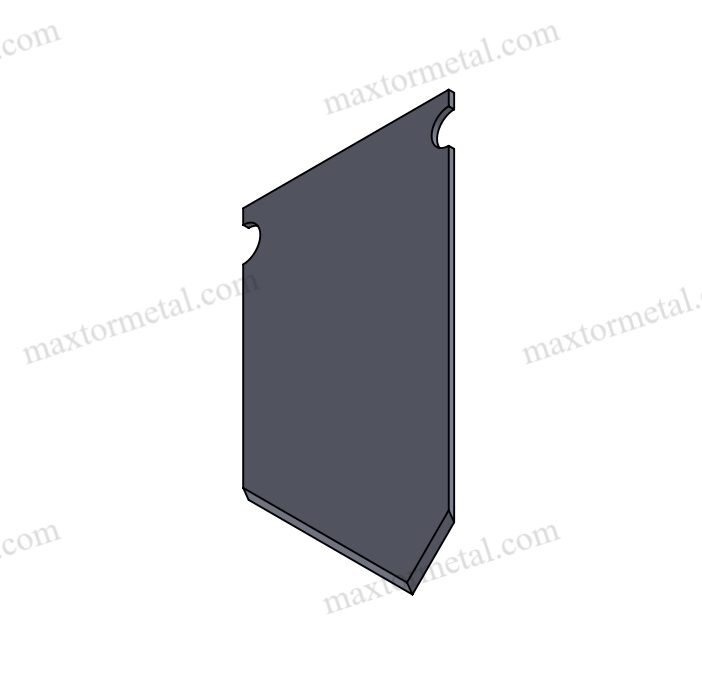
4. Kundenspezifische Blade-Lösungen für die Reifenherstellung
Reifenherstellung ist nicht immer gleich. Je nach Produktionsumgebung benötigen Sie möglicherweise maßgeschneiderte Klingen, die Ihren spezifischen Anforderungen entsprechen. Nanjing Metal bietet maßgeschneiderte Klingenlösungen, um sicherzustellen, dass Ihre Klingen genau auf Ihre Anforderungen abgestimmt sind.
Bei der kundenspezifischen Rotorblattfertigung arbeiten wir eng mit dem Kunden zusammen, um Rotorblätter zu entwickeln, die zur Produktionslinie, zum Materialtyp und zu den Produktionsmengen passen. Unser Expertenteam begleitet Sie durch jeden Prozessschritt, vom Entwurf bis zur Fertigung, und stellt sicher, dass Ihre Rotorblätter perfekt auf Ihre Bedürfnisse abgestimmt sind.
5. Wartung und Pflege der Klinge
Die ordnungsgemäße Wartung von Industrieklingen ist entscheidend für ihre Langlebigkeit, Effizienz und Leistung. Die richtige Pflege verlängert nicht nur die Lebensdauer der Klingen, sondern minimiert auch Produktionsausfallzeiten und verbessert die Gesamtkosteneffizienz des Herstellungsprozesses. Nachfolgend finden Sie detaillierte, datengestützte Vorgehensweisen zur Optimierung der Klingenwartung in der Reifenherstellung:
5.1 Regelmäßiges Schärfen
Das regelmäßige Schärfen von Klingen gewährleistet deren Effizienz und Effektivität. Mit der Zeit verschleißen Klingen durch Reibung und Stöße mit harten Materialien. Stumpfe Klingen führen zu höherem Energieverbrauch und weniger effizienter Schneidleistung, was sich letztendlich auf den gesamten Produktionszyklus auswirkt.
- Schärfungshäufigkeit: Die Häufigkeit des Schärfens hängt vom Klingenmaterial und der Art des Schneidens ab. Zum Beispiel: Klingen aus Kohlenstoffstahl Beim Gummischneiden müssen die Klingen möglicherweise alle 50–100 Betriebsstunden geschärft werden, während Hartmetallklingen, die härter und haltbarer sind, können mehrere hundert Stunden halten, bevor sie geschärft werden müssen.
- Schärfmethoden: Um die Kantengeometrie der Klinge zu erhalten, sollten Präzisionsschleifmaschinen verwendet werden. Falsches Schärfen kann zu ungleichmäßigen Kanten führen, die unsaubere Schnitte und damit Qualitätsmängel bei der Reifenherstellung verursachen können.
5.2 Sachgemäße Lagerung
Die Lagerbedingungen spielen eine entscheidende Rolle für die Qualität der Klingen. Unsachgemäße Lagerung von Klingen, insbesondere in Umgebungen mit schwankender Luftfeuchtigkeit oder extremen Temperaturen, kann zu Rost und Korrosion führen, insbesondere in Klingen aus KohlenstoffstahlUm diese Probleme zu vermeiden, müssen ordnungsgemäße Lagerungspraktiken befolgt werden.
- UmgebungsbedingungenLagern Sie die Klingen in einer sauberen, trockenen Umgebung bei stabilen Temperaturen zwischen 15 und 25 °C. Die Luftfeuchtigkeit sollte unter 50 °C liegen, um Oxidation und Rost zu vermeiden. Werden Klingen in Bereichen mit hoher Luftfeuchtigkeit gelagert, sollten sie regelmäßig überprüft und mit Schutzölen oder Rostschutzmitteln behandelt werden.
- Speichersysteme: Die Implementierung von Klingenaufbewahrungssystemen wie benutzerdefinierten Werkzeugständern oder Koffern mit korrosionsbeständigen Auskleidungen trägt dazu bei, die Integrität der Klingenkanten zu erhalten und das Risiko physischer Schäden während der Lagerung und Handhabung zu minimieren.
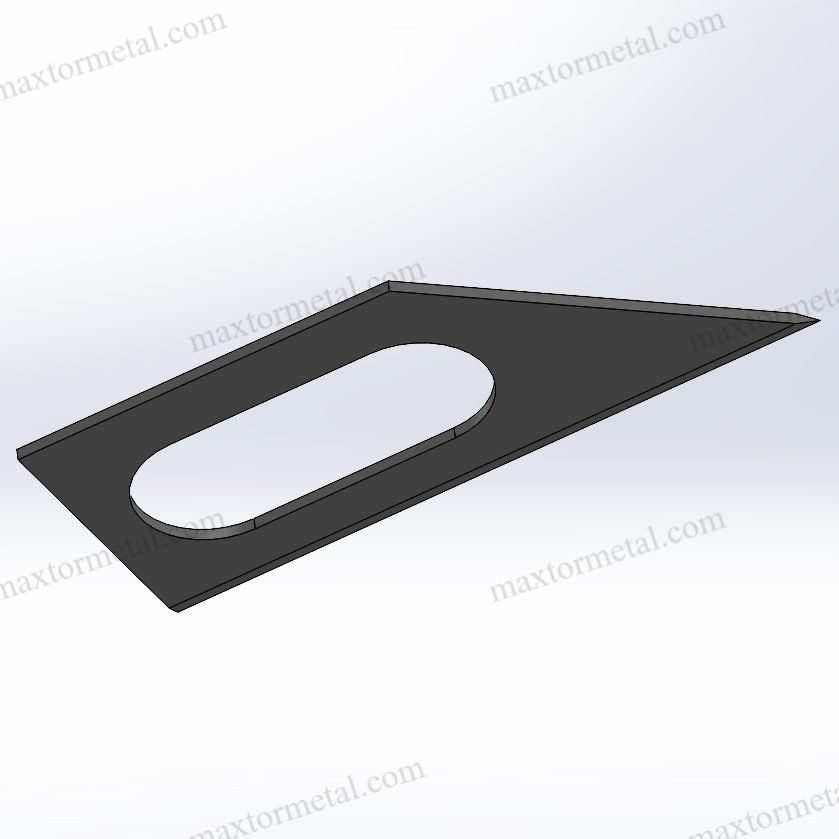
5.3 Routineinspektionen
Regelmäßige Inspektionen sind entscheidend, um frühzeitig Anzeichen von Verschleiß, Beschädigungen oder anderen Problemen zu erkennen, die die Leistung der Klinge beeinträchtigen können. Das rechtzeitige Erkennen von Problemen wie stumpfen Kanten, Absplitterungen, Rissen oder Verbiegungen kann plötzliche Ausfälle während der Produktion verhindern und die Sicherheit erhöhen.
- Inspektionshäufigkeit: Rotorblätter sollten mindestens einmal pro Schicht überprüft werden, insbesondere in Produktionsumgebungen mit hohem Produktionsvolumen. Bei Rotorblättern, die in kritischen Prozessen eingesetzt werden, können Inspektionen vor jedem Arbeitsgang erforderlich sein. Digitale Inspektionswerkzeuge oder Kameras können helfen, kleinere Fehler und Risse in der Rotorblattoberfläche zu erkennen, die mit bloßem Auge möglicherweise nicht sichtbar sind.
- Wichtige Indikatoren für Klingenverschleiß:
- Stumpfe Kanten: Führt zu ineffizientem Schneiden, höherem Energieverbrauch und inkonsistenter Produktqualität.
- Absplitterungen und Risse: Treten typischerweise durch Stöße oder Belastungen auf. Wenn sie nicht behoben werden, kann es zum Versagen der Klinge kommen.
- Biegen oder Verziehen: Kommt häufig bei Klingen vor, die hohen Temperaturen oder unsachgemäßer Handhabung ausgesetzt sind.
5.4 Behebung häufiger Blade-Fehler
Rotorblätter können verschiedene Ursachen haben, darunter unsachgemäße Wartung, minderwertige Materialien oder übermäßiger Verschleiß. Das frühzeitige Erkennen dieser Probleme und entsprechende Korrekturmaßnahmen können kostspielige Ausfallzeiten und eine suboptimale Produktion verhindern.
- Stumpfe KantenStumpfe Klingen erhöhen den Schneidwiderstand, was zu mehr Hitze und vorzeitigem Verschleiß führt. Regelmäßiges Schärfen sollte durchgeführt werden, bevor die Klingen zu stumpf werden, um effektiv zu arbeiten. Klingen aus legierter Stahl oder Wolframcarbid Normalerweise bleiben sie länger scharf, müssen aber geschärft werden, wenn sie abgenutzt sind.
- RisseRisse entstehen oft durch mechanische Belastung oder unsachgemäße Wärmebehandlung. Sobald Risse auftreten, muss die Klinge umgehend ausgetauscht werden, da eine gerissene Klinge während des Betriebs zerbrechen und zu Schäden oder Verletzungen führen kann.
- Biegen oder VerziehenVerzogene Klingen entstehen durch ungleichmäßige Erwärmung während der Herstellung oder übermäßige Betriebsbelastung. Das Verbiegen kann die Schnittpräzision der Klinge beeinträchtigen und zu ungleichmäßigen Schnitten führen. Regelmäßige Kontrollen können diesem Problem vorbeugen.
6. Blade-Innovation in der Reifenindustrie
Mit der Weiterentwicklung der Reifenindustrie entwickelt sich auch die Technologie der in der Produktion eingesetzten Klingen weiter. Diese Innovationen verbessern die Leistung der Klingen, steigern die Effizienz der Reifenproduktion und senken die Gesamtkosten. Hier sind einige der neuesten Trends und technologischen Fortschritte im Klingendesign:
6.1 Fortschrittliche Beschichtungen für eine längere Lebensdauer
Die Verwendung von fortschrittliche Beschichtungen wie Diamant, Keramik, Und Titannitrid (TiN) hat die Haltbarkeit von Industrieklingen dramatisch verbessert.
- DiamantbeschichtungenDiamantbeschichtungen verbessern die Härte und Verschleißfestigkeit der Klingen. Sie reduzieren die Reibung beim Schneiden, was zu schärferen Kanten und einer längeren Klingenlebensdauer führt. Diamantbeschichtete Klingen eignen sich ideal zum Schneiden stark abrasiver Materialien, wie z. B. Gummimischungen mit eingebetteten Stahldrähten.
- Keramikbeschichtungen: Keramikbeschichtete Klingen bieten eine hohe Hitze- und Korrosionsbeständigkeit. Diese Beschichtungen sorgen dafür, dass die Klingen auch unter extremen Bedingungen scharf bleiben, was die Effizienz verbessert und den Wartungsbedarf reduziert. Forschung in der Reifenindustrie (2021) has found that ceramic-coated blades in high-stress environments outperform traditional steel blades by 35% in terms of longevity and cutting precision.
- Titannitrid (TiN): TiN coatings offer enhanced resistance to wear and corrosion while also reducing friction. This results in smoother cuts and better overall blade performance, which is essential for high-volume tire manufacturing operations. TiN coatings are particularly beneficial for blades used in high-speed slitting and cutting tasks.
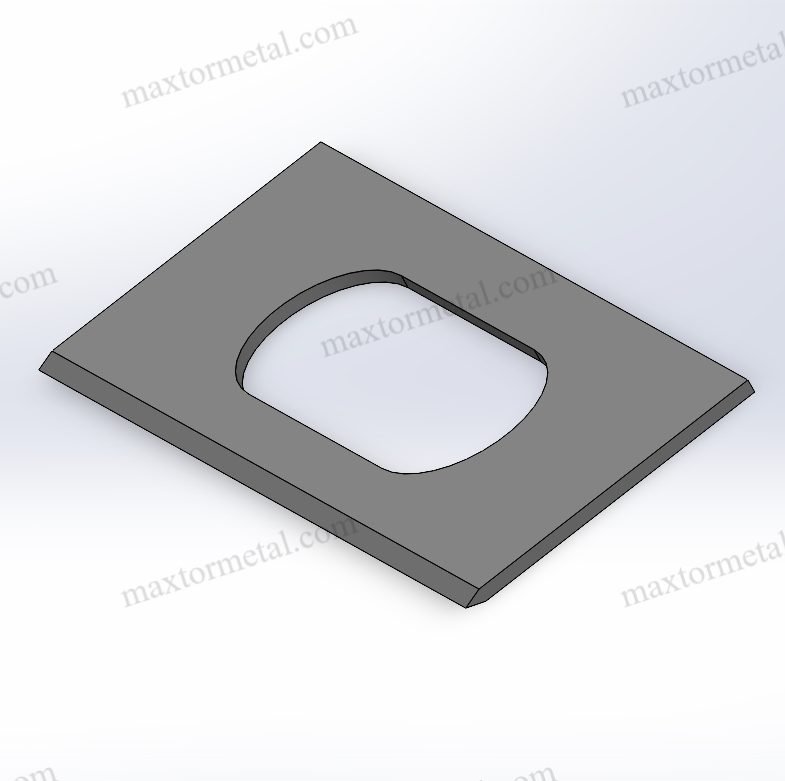
6.2 Heat Treatment for Blade Durability
Innovations in heat treatment techniques have enabled blades to maintain their sharpness and strength longer, even under intense operational conditions.
- New Heat Treatment Techniques: Advances in heat treatment processes such as vacuum heat treatment und induction hardening allow for more precise control over the hardness and toughness of blades. These treatments ensure that blades can withstand the extreme stresses they face during tire production, such as cutting through reinforced materials and high-tensile rubbers.
6.3 Custom Blade Geometry
Blade geometry—such as edge angles, thickness, and surface finish—can significantly affect the cutting efficiency and quality of the process.
- Edge Angle and Blade Geometry: Manufacturers are now designing blades with customized geometries tailored to specific production needs. For example, blades with sharper or more acute angles are ideal for fine cuts in tire finishing, while thicker edges are used for more robust cutting tasks in slitting or molding.
- Specialized Edge Coatings: Some blades feature specialized coatings to reduce wear and improve cutting precision at higher speeds. This includes cobalt-alloy coatings that can maintain cutting efficiency at elevated temperatures commonly found in the tire production process.
- Innovative Designs: Companies like Nanjing Metal are investing in the development of proprietary geometries that optimize cutting angles and reduce friction. According to a report by Tire Technology International (2022), custom-designed blades have led to a 10–15% increase in overall cutting efficiency, reducing operational costs and improving product quality.
These technological innovations in blade materials, coatings, heat treatment, and geometry have significantly improved the longevity and performance of blades used in tire manufacturing. Manufacturers that stay up-to-date with these advancements can benefit from reduced downtime, improved cutting precision, and lower maintenance costs.
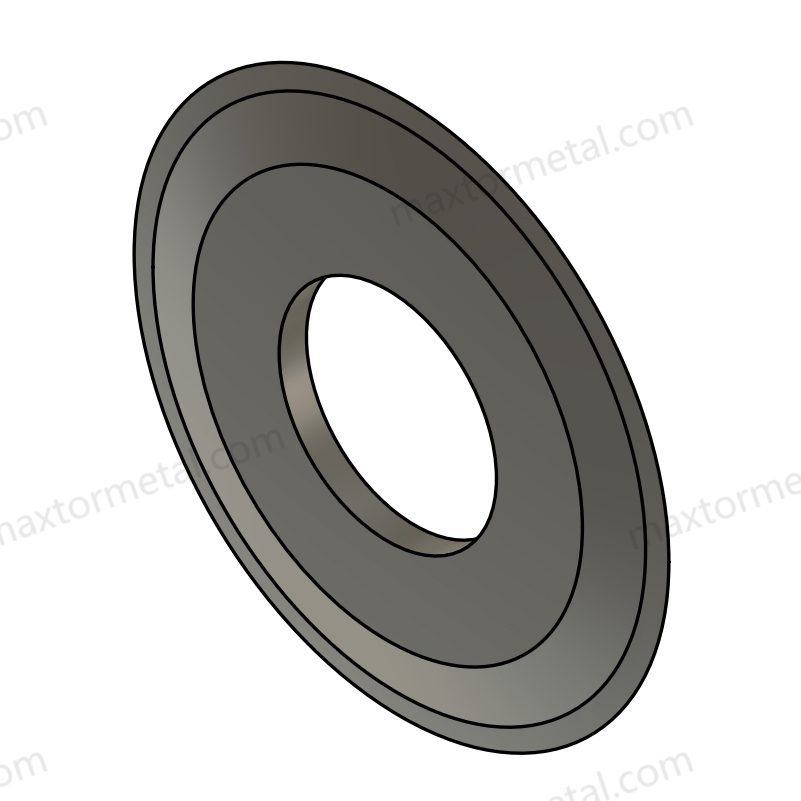
7. Vergleich verschiedener Klingentypen für die Reifenherstellung
Selecting the right blade type for specific tasks is crucial in optimizing the tire manufacturing process. Each blade type is designed with unique features that make them suitable for specific tasks. Below is a more detailed comparison of the most commonly used blades in tire production, with added insights into material properties and performance metrics.
Klingentyp | Funktion | Material | Recommended Use | Detailed Insights |
Kreissägeblätter | Continuous cutting of rubber sheets | Carbon steel, alloy steel, tungsten carbide | Ideal for bulk cutting | Circular blades are often chosen for their uniform cutting capability and precision in slicing large volumes of rubber sheets or tire components. The use of Wolframcarbid in these blades, known for its hardness and wear resistance, allows for extended lifespan, especially when cutting high-abrasion materials. |
Trimmklingen | Removing excess rubber after molding | Stainless steel, cobalt alloy | Clean cuts in tire shaping and trimming | Trimming blades must have a sharp edge and corrosion resistance, as they are exposed to high temperatures and humidity. Stainless steel blades are ideal for this purpose because they resist corrosion while maintaining a sharp edge. Cobalt-alloy trimming blades are more resilient to wear and tear when exposed to high temperatures during the final tire shaping process. |
Schlitzklingen | Cutting tires into widths and precise shapes | Alloy steel, high-speed steel | Slitting rubber to size | Slitting blades are designed for accuracy and precision when dividing tire sections into specified widths. Schnellarbeitsstahl (HSS) is preferred here due to its excellent heat resistance and ability to maintain sharpness under stress. Legierter Stahl, often used for slitting blades, provides a balance of toughness and cost-effectiveness. The cutting speed and resistance to heat buildup make alloy steel particularly suited for high-speed slitting applications. |
The choice of material significantly impacts the blade’s performance, wear resistance, and cutting quality. Tungsten carbide is ideal for high-abrasion tasks, while stainless steel excels in precision cutting and trimming. Alloy steel and high-speed steel offer a balanced combination of durability and performance for slitting operations.
8. Optimierung der Schneideffizienz
To maximize efficiency and minimize production costs, it is essential to understand the relationship between blade geometry und cutting performance. The design of the blade’s edge, angle, and surface properties can influence cutting speed, precision, and the quality of the final product. Let’s explore some key factors that play a critical role in blade efficiency:
8.1 Key Factors in Blade Geometry:
8.1 Blade Angle
The angle at which the blade meets the material during cutting—known as the Schnittwinkel—plays a crucial role in reducing cutting resistance. A sharper cutting angle (smaller blade angle) can reduce friction and make cutting easier, leading to faster production times. However, there is a tradeoff: sharper angles can cause blades to wear faster, as the cutting edge becomes more vulnerable to impact and heat buildup.
- Optimal Blade Angles for Tire Manufacturing:
- Kreissägeblätter: Typically use an angle between 20° and 30°, which allows for a balance between cutting speed and blade durability. This ensures smooth, continuous cuts of rubber sheets without excessive wear.
- Trimming blades: A sharper angle of around 15° to 20° is often used for cleaner cuts, especially during the final tire shaping process where precision is paramount.
- Slitting blades: Usually have a slightly larger cutting angle (30° to 45°) to withstand the increased stress from cutting through thicker, tougher rubber materials.
8.2 Edge Design
The design of the blade edge—whether smooth, serrated, or honed—can significantly impact cutting precision, friction levels, and heat generation. A smooth edge tends to reduce friction, leading to lower heat generation and longer blade life. On the other hand, a serrated edge is better suited for cutting through more fibrous or abrasive materials.
- Smooth Edges: Provide clean, precise cuts with minimal wear. This is particularly important for trimming blades that require sharpness and accuracy throughout the production process.
- Serrated Edges: Often used in applications where the material being cut is tougher, like steel-belted rubber. Serrated edges provide better grip and cutting efficiency, especially for Schlitzklingen used for tougher tire segments.
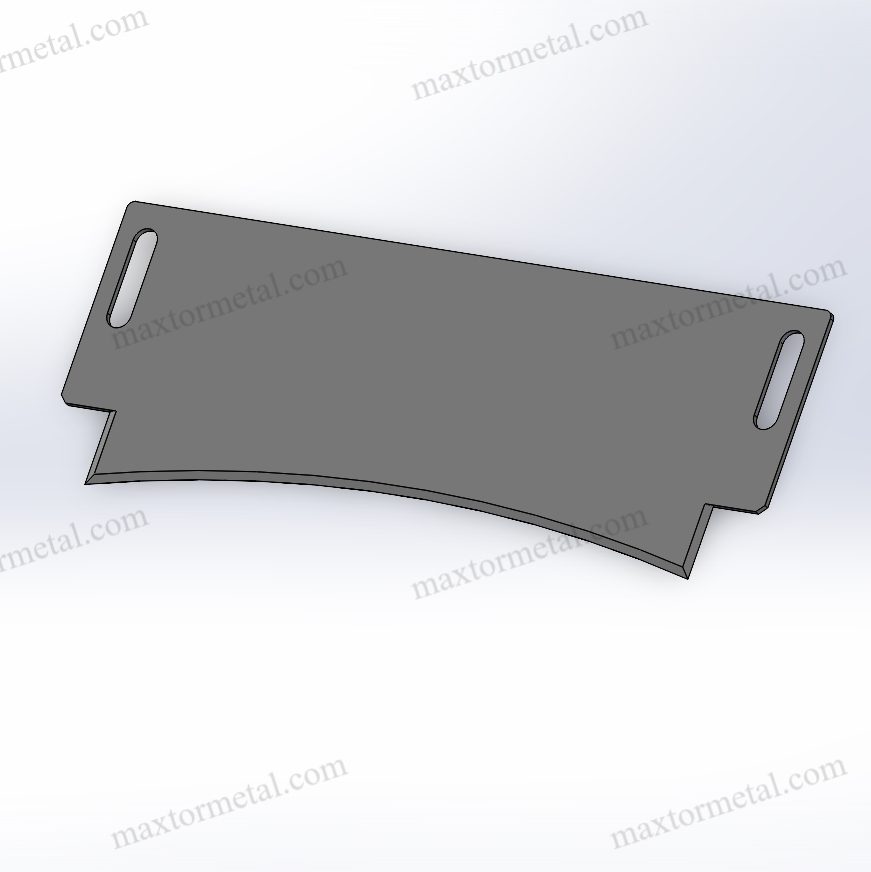
8.3 Surface Finish
The finish of the blade surface, including whether it is polished, coated, or treated, impacts its performance. Blades with a polished oder coated surface experience less friction, leading to reduced wear and smoother cuts.
- Coated Blades: Many tire manufacturing blades are coated with Zinn (Titanium Nitride) or Diamantähnlicher Kohlenstoff (DLC) coatings, which reduce friction and improve wear resistance. These coatings enhance cutting efficiency, especially in high-temperature operations, and reduce the frequency of sharpening.
8.2 Relationship Between Geometry and Cutting Efficiency
Blade geometry not only affects the cutting speed but also determines how cleanly the material is cut and how minimally the blade wears. By optimizing the blade geometry, tire manufacturers can achieve a substantial boost in efficiency while reducing operational costs:
- Energieeffizienz: A blade with optimized geometry (correct angle and edge design) requires less force to cut through rubber, thus reducing energy consumption.
- Precision and Waste: Precision cutting ensures the production of high-quality tires with minimal material waste. Cleaner cuts lead to better tire performance and aesthetics, which is critical in the competitive tire industry.
- Operational Cost Savings: Minimizing wear, reducing friction, and prolonging blade life result in fewer replacements and less downtime for blade maintenance. This translates into cost savings and increased production uptime.
9. Die entscheidende Rolle von Blades bei der Reifenherstellung
Blades play an integral role in ensuring tire production is efficient, precise, and cost-effective. By understanding the different blade materials, types, and applications, you can optimize your production line for maximum output and minimal downtime.
At Nanjing Metal, we specialize in providing high-quality, durable blades that meet the demanding needs of tire manufacturers. Whether you require standard blades or custom-made solutions, we have the expertise to support your business’s growth and success.
To learn more about how Nanjing Metal’s blades can improve your tire manufacturing process, contact us today.