Zusammenfassung:
Präzision beim Schneiden ist für Industrien, die Kreisschlitzklingen, die sich auf alles auswirken, von der Materialeffizienz bis zur Produktqualität. Dieser Artikel untersucht effektive Möglichkeiten zur Verbesserung der Schnittgenauigkeit durch Auswahl des richtigen Klingenmaterials, Optimierung des Setups, Aufrechterhaltung des Klingenzustands und Auswahl eines zuverlässiger Lieferant.
1. Warum Schnittgenauigkeit wichtig ist
In Branchen, in denen Präzisionsschneiden unverzichtbar ist, ist die Genauigkeit eines Kreisschlitzklinge kann die Produktivität und Produktqualität erheblich beeinflussen. Präzise Schnitte reduzieren den Materialabfall und sorgen für einen reibungslosen, effizienten Herstellungsprozess, insbesondere in Branchen wie Papier, Verpackung und Metall. Laut einer Studie des Institute of Manufacturing Technology kann sogar eine Verbesserung der Klingenpräzision um 5% den Materialabfall um bis zu 10% pro Jahr senken. Das Verständnis der Faktoren, die die Klingenpräzision beeinflussen, und die Umsetzung von Strategien zur Verbesserung der Genauigkeit kommen Unternehmen direkt zugute, da Kosten gesenkt und die Ausgabequalität verbessert wird.
2. Faktoren, die die Schnittpräzision beeinflussen Kreisschlitzklingen
Die Präzision wird von verschiedenen Faktoren beeinflusst, darunter das Material der Klinge, ihre Schärfe, ihr Verschleißgrad und die Genauigkeit der Einstellung. Jeder dieser Bereiche kann die Schneidleistung einer Kreisschneideklinge entweder verbessern oder verringern. Das Verständnis und die Optimierung dieser Faktoren ist entscheidend, um eine hohe Genauigkeit beizubehalten, Materialabfälle zu reduzieren und die Betriebseffizienz zu steigern.
2.1 Klingenmaterial
Das Material von Kreissägeblättern spielt eine wichtige Rolle bei der Bestimmung der Schnittpräzision. Schnellarbeitsstahl (HSS) und Hartmetall sind zwei der am häufigsten verwendeten Materialien. HSS-Sägeblätter bieten hervorragende Flexibilität und sind schlagfest, was sie ideal für weichere Materialien wie Papier oder Kunststoffe macht. Hartmetall-Sägeblätter hingegen bieten mit einer Härte von etwa 90 HRC (Rockwell-Härteskala) eine außergewöhnliche Haltbarkeit und sind besser für härtere Materialien wie Metall und Verbundwerkstoffe geeignet. Studien zeigen, dass Hartmetall-Sägeblätter bei abrasiven Anwendungen bis zu 10-mal länger halten als Standard-Stahl-Sägeblätter, was die Häufigkeit des Austauschs verringert und die Schnittkonsistenz im Laufe der Zeit verbessert.
Darüber hinaus verbessern Materialien wie Wolframkarbid, die extreme Härte und Widerstandsfähigkeit gegenüber hohen Temperaturen vereinen, die Schnittgenauigkeit weiter, insbesondere bei der Bearbeitung anspruchsvoller oder hitzeempfindlicher Materialien. Beim Schneiden von rostfreiem Stahl beispielsweise kann mit hartmetallbestückten Sägeblättern eine höhere Präzision erreicht werden als mit Sägeblättern aus Schnellarbeitsstahl, da sie unter Belastung länger scharf bleiben.
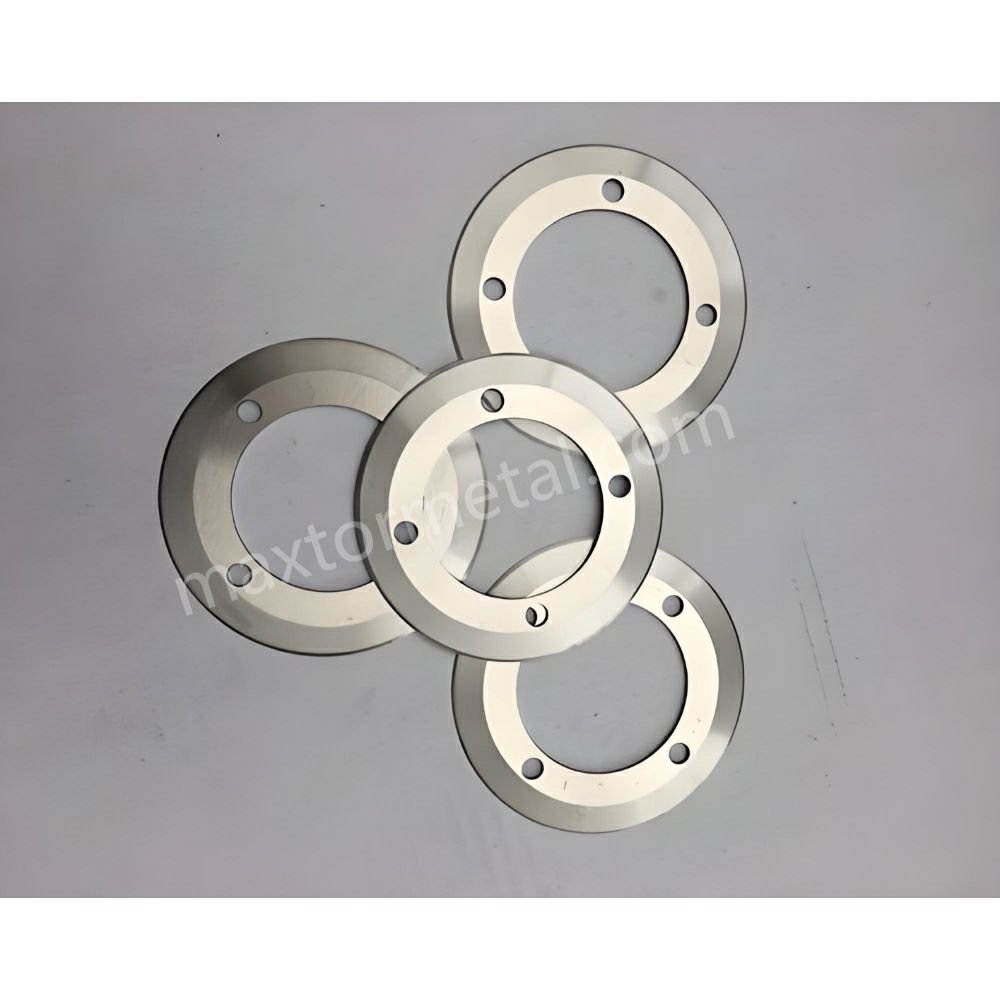
2.2 Schärfe und Abnutzungsgrad
Die Schärfe der Klinge hat direkte Auswirkungen auf die Schnittgenauigkeit. Eine Studie der Precision Metalforming Association ergab, dass Schnittfehler um bis zu 25 % zunehmen können, wenn die Klingenabnutzung 20 % überschreitet. Eine stumpfe Klinge erfordert mehr Druck, um einen sauberen Schnitt zu erzielen, wodurch das Risiko von Materialverschiebungen, Kantenausfransungen oder unbeabsichtigten Biegungen steigt. Um solche Probleme zu vermeiden, ist die Implementierung eines Wartungsplans, der das routinemäßige Schärfen oder Ersetzen der Klinge nach einer bestimmten Anzahl von Schnitten vorsieht, von entscheidender Bedeutung. Wenn Sie beispielsweise einen Schärfplan alle 50.000 Schnitte für Standardmaterialien und alle 20.000 Schnitte für härtere Materialien festlegen, können Sie eine gleichbleibend scharfe Kante gewährleisten.
Darüber hinaus sorgen verbesserte Klingenbeschichtungen wie Titannitrid (TiN) und diamantähnlicher Kohlenstoff (DLC) für eine längere Schärfe und weniger Verschleiß. TiN-beschichtete Klingen haben beispielsweise in hochintensiven Schneidumgebungen eine längere Lebensdauer gezeigt, da die Präzision über längere Zeiträume erhalten bleibt, ohne dass die Klingenschneide beeinträchtigt wird.
2.3 Präzision bei Rotorblattaufbau und -montage
Die Art und Weise, wie ein Kreisschneideblatt montiert wird, hat einen großen Einfluss auf die Schnittpräzision. Schon eine Fehlausrichtung von 0,1 mm kann zu ungleichmäßigen Schnitten und Materialverschwendung führen. Eine ordnungsgemäße Installation mit Laserausrichtungswerkzeugen kann die Fehlerquote um 20 % senken und die Produktionsgenauigkeit verbessern. Beispielsweise wurde in Metallschneideanlagen, in denen laserausgerichtete Kreisschneideblätter verwendet werden, eine Reduzierung der Kantenfehler um 15 % und eine Verbesserung der Schnittgeschwindigkeit um 10 % gemeldet.
Die Balance des Sägeblatts ist ein weiterer kritischer Faktor. Ein Sägeblatt, das auch nur leicht aus dem Gleichgewicht geraten oder lose montiert ist, vibriert, was die Präzision beeinträchtigt und die Gefahr mechanischer Abnutzung erhöht. Um eine ausgewogene Sägeblattmontage zu erreichen, sind häufig Präzisionshalter mit einer Spannkrafttoleranz von weniger als 0,5 mm erforderlich. Solche Anpassungen sind zwar geringfügig, können aber bei hochpräzisen Einstellungen einen erheblichen Unterschied machen.
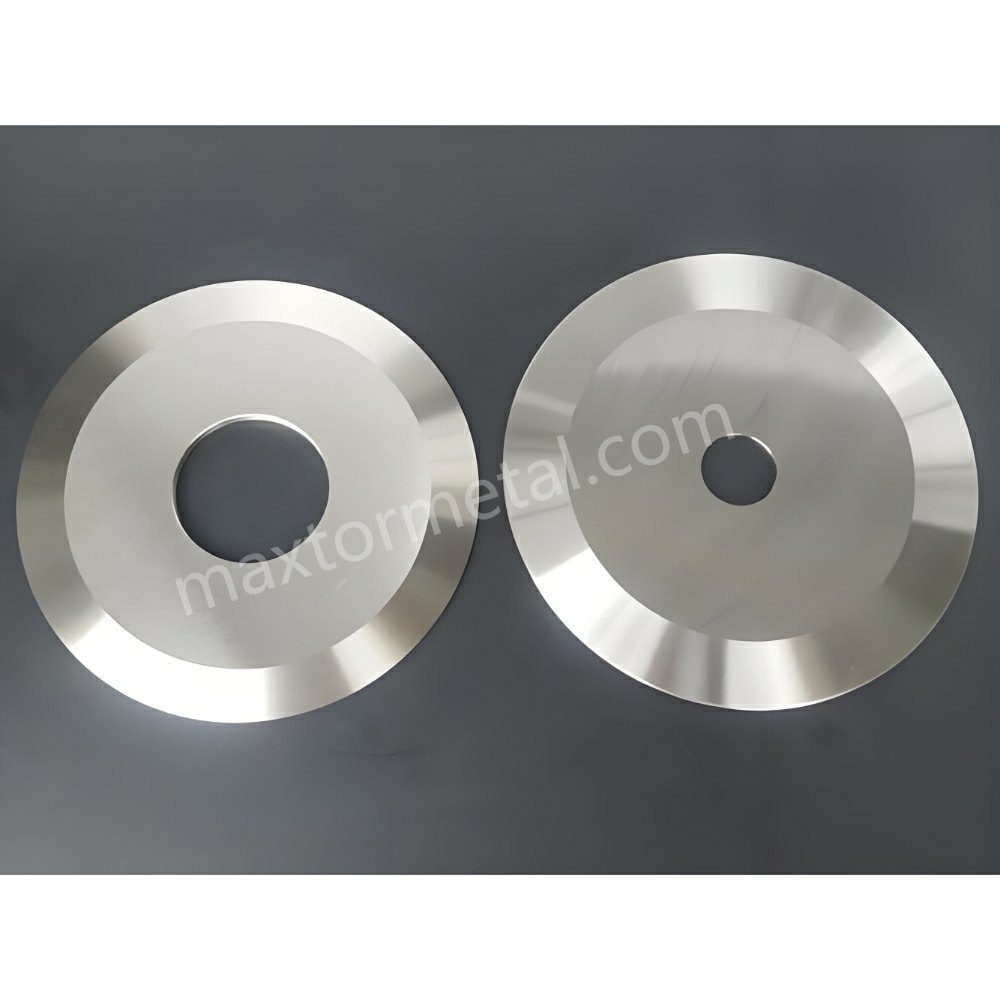
3. Praktische Tipps zur Verbesserung der Schnittpräzision
Um die Genauigkeit von Kreisschneideklingen zu verbessern, müssen Sie den richtigen Klingentyp auswählen, die Ausrüstung und Klingenpassung optimieren und moderne Technologien nutzen. Diese Schritte verringern die Wahrscheinlichkeit von Ungenauigkeiten und verbessern die Gesamteffizienz des Produktionsprozesses.
3.1 Auswahl des richtigen Klingentyps und der richtigen Spezifikationen
Die Auswahl des geeigneten Klingendurchmessers, der richtigen Dicke und des richtigen Kantenwinkels für jeden Materialtyp ist von entscheidender Bedeutung. Beim Schneiden weicher Materialien wie Schaumstoff oder Gummi kann beispielsweise eine dünnere Klinge mit einem schärferen Kantenwinkel den Widerstand minimieren, was zu glatteren Schnitten führt. Umgekehrt sind für härtere Materialien wie Stahl oder Glas dickere, haltbarere Klingen vorzuziehen. Studien zeigen, dass die Verwendung richtig spezifizierter Klingen für das jeweilige Material die Schnittpräzision um bis zu 25% erhöhen kann.
Darüber hinaus beeinflusst die Geometrie der Klingenkante die Schnittgenauigkeit. Beispielsweise sind abgeschrägte Kanten ideal zum Schneiden von Schichtmaterialien, da sie den Widerstand minimieren. Eine beidseitig abgeschrägte Klinge mit einem Winkel von 30 Grad auf jeder Seite liefert optimale Ergebnisse beim Präzisionsschneiden von Kunststoffen und verbessert die Schnittqualität im Vergleich zu einseitig abgeschrägten Kanten um etwa 20 %.
3.2 Optimierung der Ausrüstung und der Blattpassung
Eine präzise Passung der Klinge an die Maschine reduziert Vibrationen, eine häufige Ursache für Schnittungenauigkeiten. So reduzieren Anpassungen der Klingenstabilisierung die Abweichung bei Hochgeschwindigkeitsanwendungen um bis zu 18 %. Viele Industrieanlagen erreichen dies durch den Einsatz von Klingenhaltern mit hydraulischen Klemmsystemen, die im Vergleich zu mechanischen Klemmen eine höhere Stabilität bieten. Eine Studie der Internationale Vereinigung of Industrial Cutting hat herausgefunden, dass hydraulische Spannsysteme die Schnittstabilität um bis zu 25% verbessern und so saubere, präzise Schnitte gewährleisten.
Darüber hinaus kann die Verwendung von Stoßdämpfern in der Montageanordnung das Sägeblatt zusätzlich stabilisieren. Stoßdämpfer reduzieren Schwingungen und helfen, einen gleichmäßigen Sägeblattdruck aufrechtzuerhalten, was insbesondere bei Hochgeschwindigkeitsanwendungen von Vorteil ist, bei denen selbst geringe Vibrationen zu Materialverlust führen können.
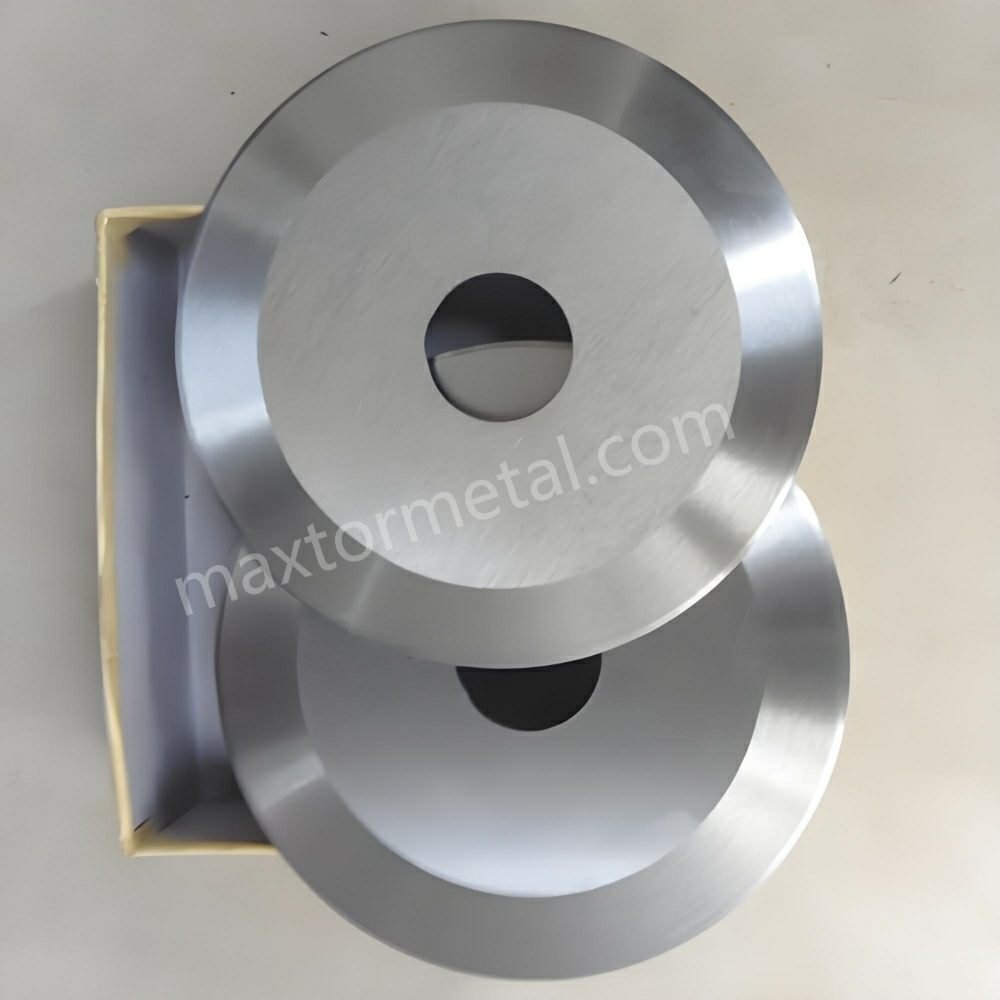
3.3 Fortschrittliche Schneidtechnologie für höhere Präzision
Annahme fortschrittliche Technologien wie automatische Klingenpositionierung oder lasergesteuerte Schneidsysteme verbessern die Präzision erheblich. Automatische Systeme passen die Position der Klinge mit äußerster Genauigkeit an und berücksichtigen selbst geringfügige Abweichungen in der Materialstärke. Diese Systeme sind besonders effektiv in der Metallverarbeitung und der Automobilindustrie, wo die Toleranzen oft innerhalb von ±0,05 mm liegen müssen. Anlagen, die diese Technologie verwenden, haben eine Verbesserung der Genauigkeit durch 30% gemeldet und gleichzeitig eine Reduzierung des Materialabfalls erreicht.
Lasergeführte Systeme sind ein weiteres wertvolles Werkzeug, insbesondere zum Schneiden ungleichmäßiger Materialien oder zum Arbeiten mit empfindlichen Substraten. Die Laserführung verbessert nicht nur die optische Ausrichtung, sondern hilft auch, eine Fehlausrichtung der Klinge zu vermeiden, was zu präziseren Schnitten und weniger Nacharbeit führt. In der Textilherstellung, wo die Präzision der Stoffkanten entscheidend ist, reduzieren lasergeführte Kreisklingen Fehler um bis zu 15 %.
4. Klingenwartung: Lebensdauer verlängern und Genauigkeit gewährleisten
Die Aufrechterhaltung des Zustands Ihrer Kreisschneideklinge ist wichtig, um die Präzision aufrechtzuerhalten und kostspielige Ersatzklingen zu vermeiden. Richtige Wartungsroutinen und planmäßige Ersatzklingen minimieren Ausfallzeiten und verbessern die Betriebseffizienz.
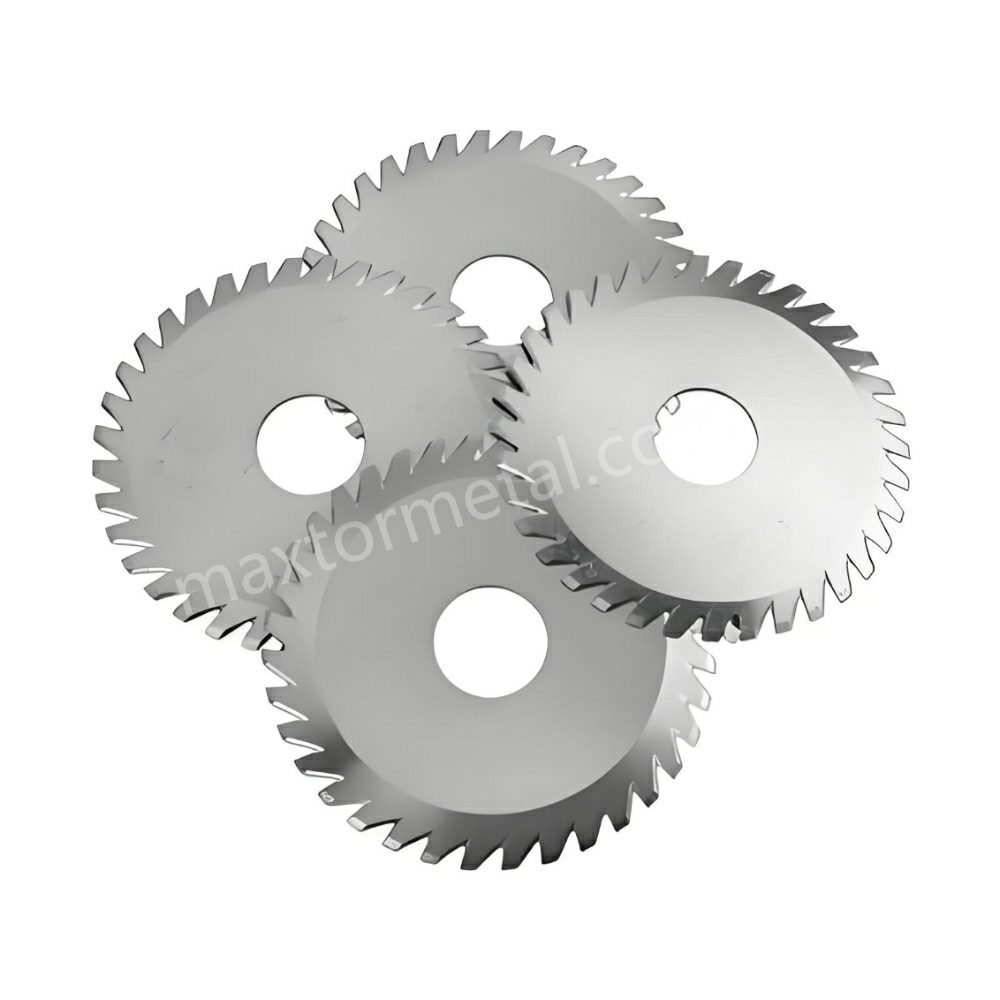
4.1 Regelmäßige Wartung und Inspektion
Regelmäßige Inspektion und Wartung sind für optimale Leistung entscheidend. Studien zeigen, dass regelmäßige Reinigung und Schmierung die Lebensdauer der Klinge um bis zu 40% verlängern kann. Staub-, Schmutz- und Rückstandsansammlungen können die Klinge schneller stumpf machen und ihre Effizienz verringern. Beispielsweise hat sich bei Lebensmittelverpackungsanwendungen, bei denen Klingen häufig durch klebende Materialien schneiden, gezeigt, dass das Reinigen der Klinge nach jeweils 10.000 Schnitten die Schnittgenauigkeit aufrechterhält, die Hygiene verbessert und den Verschleiß verringert.
Darüber hinaus verringert die Anwendung von Schmiermitteln die Reibung und verlängert die Schärfe der Klinge. Beim Metallschneiden verringert regelmäßiges Schmieren den Verschleiß um etwa 25 % und ermöglicht so glattere Schnitte und geringere Ersatzkosten.
4.2 Planmäßiger Klingenwechsel
Jede Klinge hat eine begrenzte Lebensdauer, unabhängig von der Wartung. Klingen, die über ihre optimale Verschleißgrenze hinaus verwendet werden, erzeugen häufig unregelmäßige Schnitte, was die Produktionsqualität beeinträchtigen und Material verschwenden kann. Industriestandards empfehlen, Klingen alle drei Monate oder nach einer bestimmten Anzahl von Schnitten auszutauschen – je nachdem, was zuerst eintritt. Eine kürzlich durchgeführte Branchenumfrage ergab, dass Unternehmen, die einen 90-tägigen Klingenaustauschplan einhalten, weniger Schnittfehler machen, wodurch kostspielige Nacharbeiten minimiert und die Effizienz verbessert wird.
5. Auswahl eines hochwertigen Rundschlitzgeräts Klingenlieferant
Die Wahl des Lieferanten ist entscheidend für die Gewährleistung einer gleichbleibenden Klingenqualität. Qualitativ hochwertige Lieferanten liefern in der Regel getestete Materialien, die strengen Industriestandards entsprechen, und können Beratung zu den besten Klingentypen für bestimmte Anwendungen bieten.
5.1 Bewertung der Qualitätssicherung und Compliance
Achten Sie bei der Auswahl eines Lieferanten auf Qualitätszertifikate wie Zertifizierung nach ISO 9001, was auf ein Engagement für Qualität und Konsistenz hinweist. Lieferanten mit ISO-Zertifizierung weisen aufgrund strenger Qualitätskontrollprozesse häufig niedrigere Fehlerquoten auf. Beispielsweise berichteten Produktionsstätten, die ausschließlich mit ISO-zertifizierten Lieferanten zusammenarbeiten, von einer um 15% höheren Produktionsgenauigkeit aufgrund der Zuverlässigkeit ihrer Klingen.
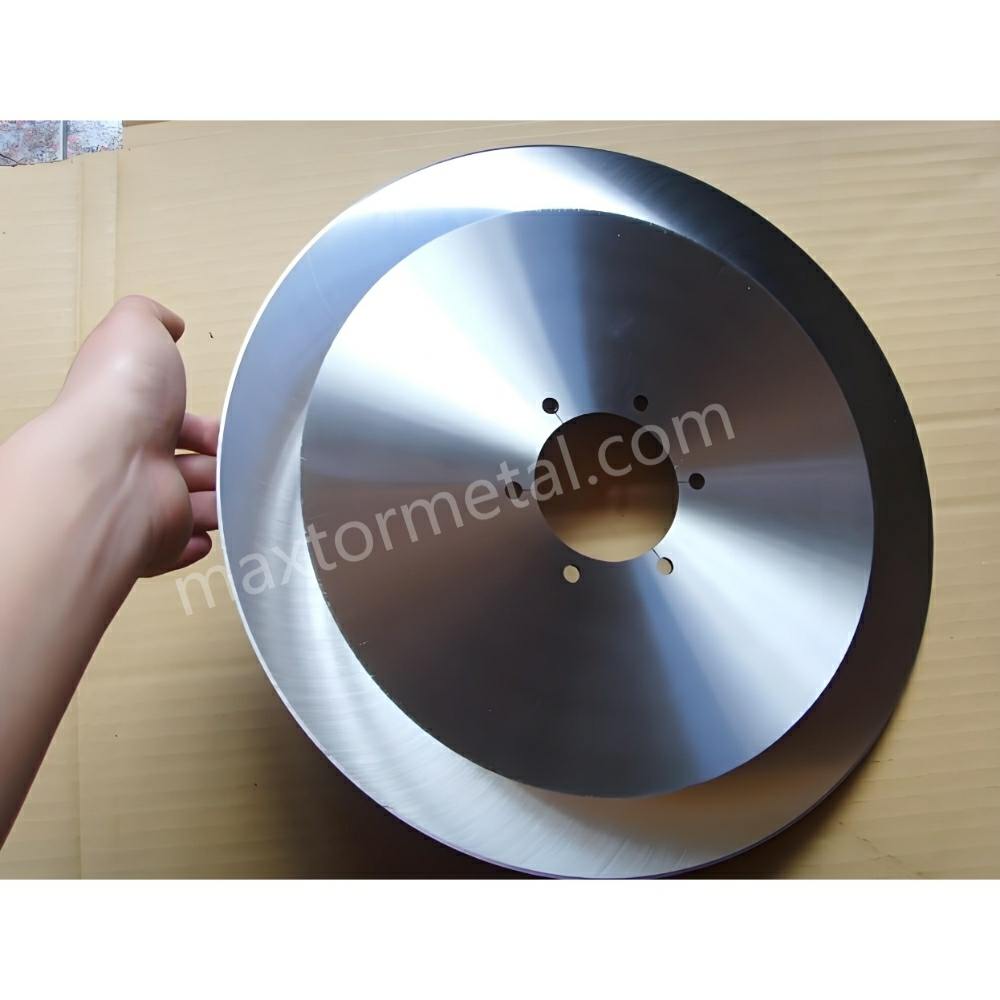
5.2 Priorisierung von Technologie und Innovation
Ein Lieferant, der in fortschrittliche Fertigungstechnologien investiert, kann Klingen mit überragender Haltbarkeit und Präzision anbieten. Moderne Produktionsmethoden wie CNC-Bearbeitung und Laserschneidtechnologien stellen sicher, dass Klingen mit hohen Toleranzen hergestellt werden. Studien zeigen, dass mit CNC-Bearbeitung hergestellte Klingen eine um 20% höhere Haltbarkeit aufweisen und über einen längeren Zeitraum präzisere Schnitte ermöglichen.
5.3 Kundensupport und Servicegarantien
Zuverlässiger Kundendienst ist ein wesentlicher Aspekt. Lieferanten, die umfassende After-Sales-Services anbieten, darunter Klingenanpassung und technischen Support, bieten einen Mehrwert, der den Kunden hilft, bessere Schneidergebnisse zu erzielen. Unternehmen mit engagiertem Kundendienst und Klingenaustauschservices verzeichnen eine 10%-Steigerung der Produktionseffizienz aufgrund reduzierter Ausfallzeiten und sofortiger Lösungen für alle Klingenprobleme.
6. Fazit: Effizienzsteigerung durch Präzision
Verbessern Sie die Präzision Ihrer Kreisschlitzklinge Abläufe können Ihre Gesamteffizienz, Produktqualität und Materialnutzung erheblich verbessern. Durch die Auswahl der geeigneten Klingenmaterialien, die Sicherstellung einer genauen Einrichtung und die regelmäßige Wartung der Klingen können Unternehmen eine längere Klingenlebensdauer und eine verbesserte Schnittgenauigkeit erzielen.
Partnerschaft mit ein qualitativ hochwertiger Lieferant stellt außerdem sicher, dass Sie zuverlässige, langlebige Klingen erhalten, die für Ihre spezifischen Anforderungen geeignet sind, was zu gleichbleibender Präzision in der Produktion führt. Für Unternehmen, die auf präzise Schneidprozesse angewiesen sind, sind diese Strategien unerlässlich, um wettbewerbsfähig zu bleiben und außergewöhnliche Qualität zu liefern.