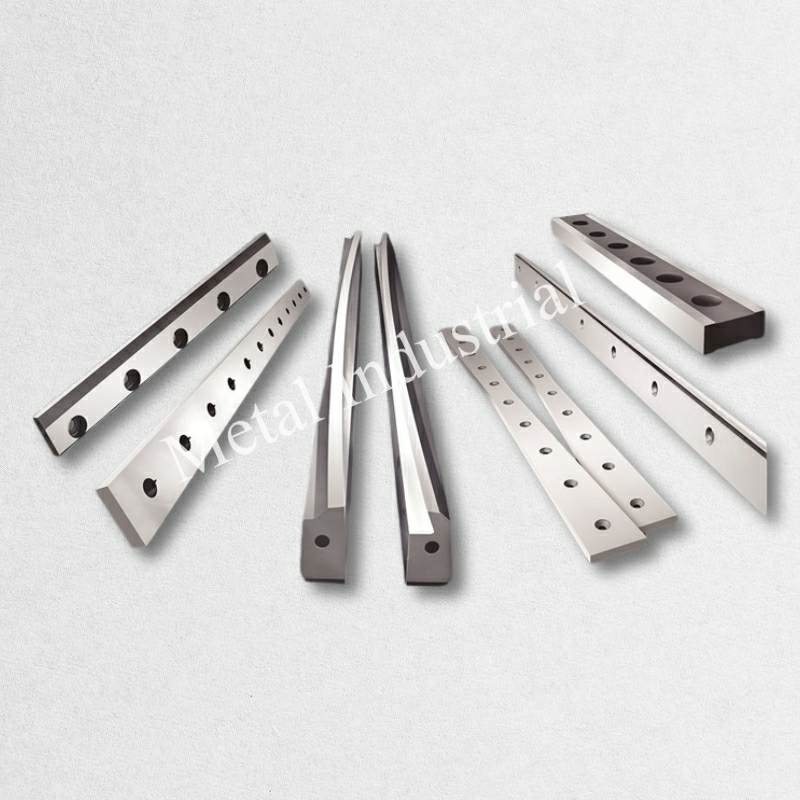
1. Warum die Wahl der richtigen Industrie-Schneidklinge wichtig ist
Industrielle Schneidklingen sind unverzichtbare Werkzeuge in der Fertigung und formen Materialien präzise und effizient. Die richtige Klinge kann die Produktion rationalisieren, Abfall reduzieren und die Produktqualität verbessern.
Ein Bericht von Grand View-Forschung schätzt, dass der globale Markt für Schneidwerkzeuge bis 2030 ein Volumen von $42,4 Milliarden erreichen wird und ab 2023 eine durchschnittliche jährliche Wachstumsrate von 5,1% erreicht. Dieses Wachstum unterstreicht die zunehmende Abhängigkeit von modernen Schneidklingen zur Deckung des steigenden Produktionsbedarfs.
Dieser Leitfaden bietet Ihnen detaillierte Einblicke in Klingentypen, wichtige Auswahlfaktoren, Wartungstipps und Lieferantenempfehlungen. Lesen Sie weiter und erfahren Sie, wie die richtige Schneidklinge Ihren Betrieb transformieren und die Rentabilität steigern kann.
2. Arten von industriellen Schneidklingen
Industrielle Schneidklingen gibt es in verschiedenen Ausführungen, die jeweils auf spezifische Anwendungen zugeschnitten sind. Die Kenntnis dieser Typen ist entscheidend für die richtige Wahl.
2.1 Kreissägeblätter
- Anwendungen: Diese Sägeblätter eignen sich ideal zum Schneiden von Metallblechen, Holzplatten und Verbundwerkstoffen.
- Vorteile: Kreissägeblätter sind für ihre hohe Schnittgeschwindigkeit, gleichbleibende Präzision und lange Lebensdauer bekannt.
- Technische Merkmale:
- Material: Oft aus Schnellarbeitsstahl (HSS) oder Hartmetall hergestellt.
- Kantengeometrie: Kann flache oder gezahnte Kanten für unterschiedliche Schneidanforderungen enthalten.
- Nutzungsdaten: In einer Studie von Cutting Edge Technology verbesserten Kreissägeblätter die Schnittgeschwindigkeit in einem Stahlverarbeitungswerk um 25%.
2.2 Sägeblätter
- Anwendungen: Bandsägeblätter eignen sich hervorragend zum präzisen Schneiden von Metallen, Kunststoffen und Holz.
- Vorteile: Ihre dünnen Profile ermöglichen detaillierte, komplizierte Schnitte ohne Materialverschwendung.
- Technische Merkmale:
- Zahnmuster: Zähne mit variabler Teilung verbessern die Vielseitigkeit und reduzieren Vibrationen beim Schneiden.
- Material: Hergestellt aus Bimetall oder hartmetallbestücktem Stahl für lange Haltbarkeit.
2.3 Schermesser
- Anwendungen: Wird zum Schneiden dicker Metallbleche oder schwerer Materialien verwendet.
- Vorteile: Diese Klingen sind äußerst langlebig und halten extremen Belastungen stand.
- Technische Merkmale:
- Materialzusammensetzung: Oft aus gehärtetem legiertem Stahl hergestellt.
- Einblick in die Haltbarkeit: Scherblätter in Metallverarbeitungsbetrieben halten bei Wärmebehandlung typischerweise 15% länger als Standardblätter.
2.4 Schneidklingen
- Anwendungen: Unverzichtbar für Hochgeschwindigkeitsvorgänge in der Papier-, Film- und Folienindustrie.
- Vorteile: Schneidklingen sorgen für saubere, präzise Schnitte und minimieren den Materialverlust.
- Technische Merkmale:
- Anpassung: Kann für verschiedene Durchmesser und Schnittwinkel zugeschnitten werden.
- Dateneinblick: Laut Packaging World steigerten kundenspezifische Schneidklingen die Effizienz einer Verpackungslinie um 18%.
Klingentyp | Anwendungen | Material | Hauptvorteile |
Kreissägeblätter | Metal, Holz, Verbundwerkstoffe | HSS, Hartmetall | Hohe Geschwindigkeit, lange Lebensdauer |
Bandsägeblätter | Präzisionsschneiden | Bimetall, Hartmetallbestückt | Vielseitig, weniger Materialabfall |
Schermesser | Hochleistungsschneiden | Gehärteter legierter Stahl | Extreme Haltbarkeit |
Schneidklingen | Hochgeschwindigkeitsverarbeitung | Anpassbare Legierungen | Saubere, effiziente Schnitte |
Jeder Klingentyp bietet einzigartige Eigenschaften, weshalb es wichtig ist, die Klinge an Ihre Anwendungsanforderungen anzupassen.
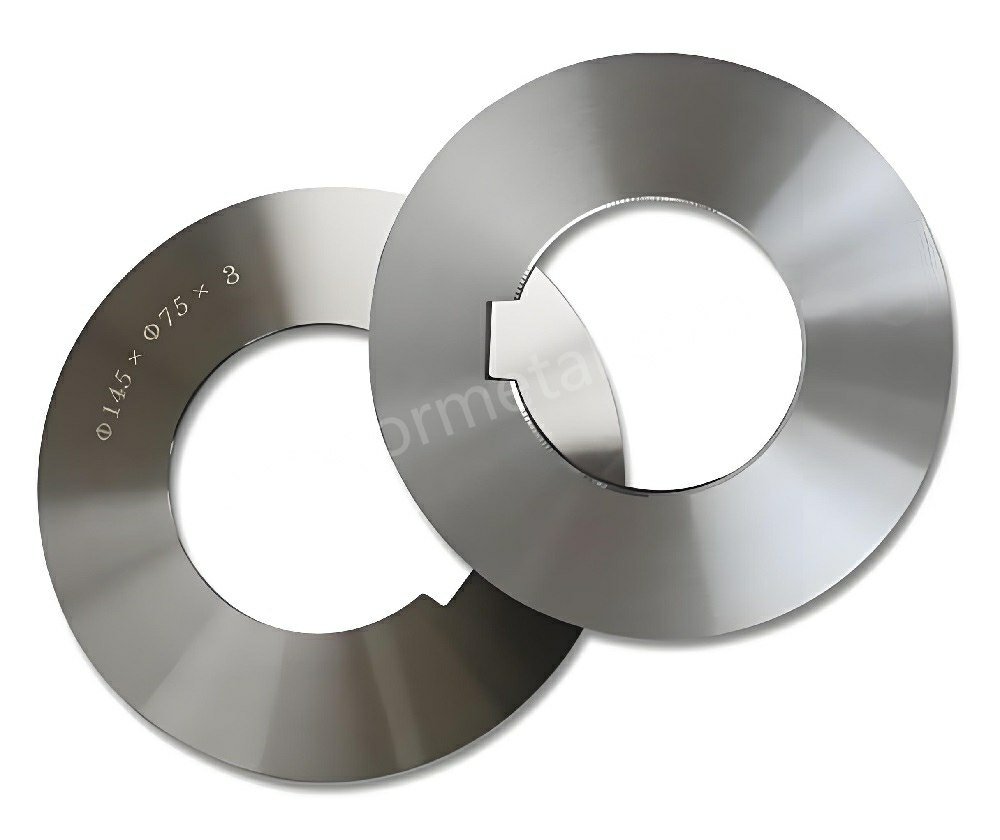
3. Wichtige Faktoren bei der Auswahl einer Schneidklinge
Um das richtige Industrieschneidblatt auszuwählen, müssen Sie mehrere Faktoren verstehen, die sich direkt auf Leistung und Kosteneffizienz auswirken.
3.1 Materialverträglichkeit
- Material der Klinge: Das Material muss mit dem Werkstück übereinstimmen. Zum Beispiel:
- Hartmetallklingen: Am besten für Metalle wie Stahl und Aluminium.
- Diamantbestückte Klingen: Perfekt für abrasive Materialien wie Verbundwerkstoffe.
- Dateneinblick: Eine Umfrage der Tooling Association aus dem Jahr 2022 ergab, dass Hartmetallklingen die Werkzeugwechselzeit bei Bearbeitungsvorgängen um 30% verkürzen.
3.2 Schaufelgeometrie und -design
- Zahnkonfiguration: Weniger Zähne ermöglichen schnellere Schnitte, können aber die Präzision verringern. Mehr Zähne sorgen für glattere Oberflächen.
- Dicke und Breite: Dünne Klingen eignen sich für detaillierte Schnitte; dicke Klingen bieten Haltbarkeit für schwere Lasten.
3.3 Betriebsumgebung
- Temperaturbeständigkeit: Ziehen Sie zum Schneiden bei hohen Temperaturen Klingen mit hitzebeständiger Beschichtung in Betracht.
- Nasse vs. trockene Bedingungen: Klingen aus rostfreiem Stahl sind ideal zum Nassschneiden, da sie korrosionsbeständig sind.
3.4 Kosten vs. Leistung
Die Investition in hochwertige Klingen kann langfristig Geld sparen. Hochwertige Klingen reduzieren beispielsweise Ausfallzeiten durch eine längere Lebensdauer. Eine Studie von Einblicke in die Fertigung zeigte, dass Premium-Sägeblätter die Betriebskosten über zwei Jahre um 15% senken.
4. Der Herstellungsprozess von industriellen Schneidklingen
4.1 Materialauswahl
Die Grundlage jeder industriellen Schneidklinge ist ihr Material. Die richtige Legierung oder der richtige Verbundwerkstoff sorgt für Haltbarkeit, Effizienz und Präzision.
- Schnellarbeitsstahl (HSS): HSS ist für seine Zähigkeit und Hitzebeständigkeit bekannt und wird häufig für Klingen verwendet, die häufig mit hoher Geschwindigkeit bearbeitet werden müssen.
- Beispiel: HSS-Klingen bleiben in Umgebungen mit hohen Temperaturen 20% länger scharf als Standardstahl.
- Hartmetall: Dieses Material bietet eine außergewöhnliche Härte und Verschleißfestigkeit und eignet sich daher zum Schneiden von Metallen und abrasiven Materialien.
- Dateneinblick: Studien zeigen, dass Hartmetallklingen in der Metallverarbeitung bis zu fünfmal länger halten als HSS-Klingen.
- Diamantbestückte Klingen: Sie sind die ultimative Wahl zum Schneiden von Verbundwerkstoffen oder extrem harten Materialien wie Keramik.
- Marktdaten: Diamantbestückte Klingen machen 151.000 Tonnen des Umsatzes mit Industrieklingen aus, da sie in der Hochpräzisionsindustrie zunehmend zum Einsatz kommen.
4.2 Schmieden und Formen
Die Klingen werden geschmiedet und geformt, um strenge Maßtoleranzen einzuhalten.
- CNC-Bearbeitung: CNC-Maschinen (Computerized Numerical Control) erreichen eine Genauigkeit von ±0,005 mm, was für in der Präzisionsindustrie verwendete Klingen unerlässlich ist.
- KI-gesteuerte Prozesse: KI optimiert Werkzeugwege und reduziert den Abfall beim Formen, wodurch eine kosteneffiziente Fertigung gewährleistet wird.
- Schmiedetechniken: Durch fortschrittliches Schmieden wird eine gleichmäßige Kornstruktur gewährleistet, die die Festigkeit und Langlebigkeit der Klinge verbessert.
Verfahren | Vorteile | Anwendungsfälle |
CNC-Bearbeitung | Hohe Präzision, reduzierte Fehler | MetalVerarbeitung, Kunststoffe |
KI-gesteuerte Prozesse | Optimierter Materialeinsatz, schnellere Produktion | Großserienfertigung |
Schmieden | Verbesserte strukturelle Integrität, verbesserte Verschleißfestigkeit | Schwerlastanwendungen |
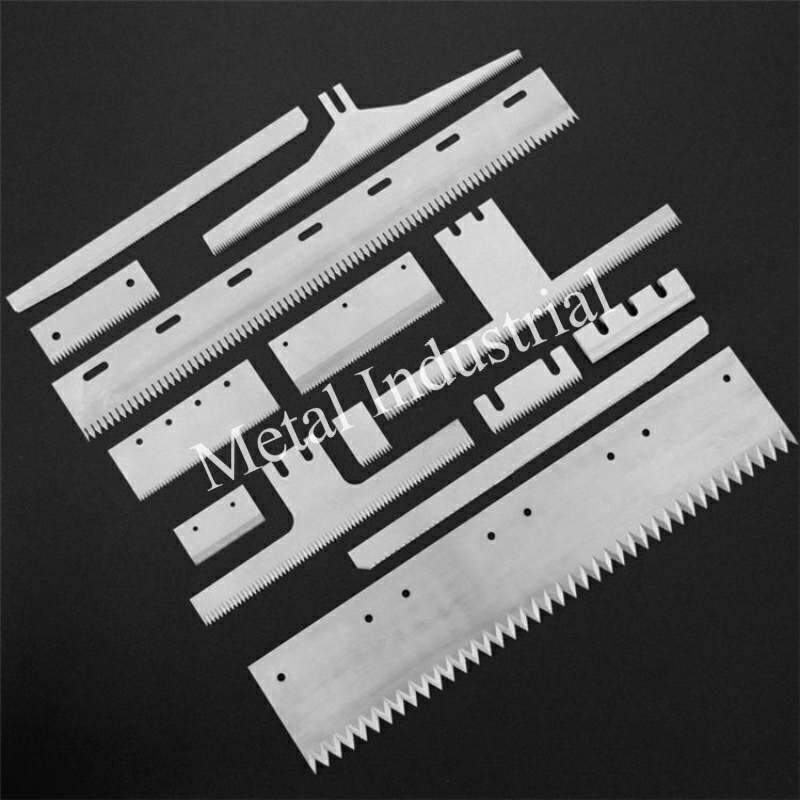
4.3 Wärmebehandlung und Anlassen
Wärmebehandlungsprozesse sind entscheidend, um das ideale Gleichgewicht zwischen Härte und Flexibilität zu erreichen.
- Anlassen: Kontrolliert die Sprödigkeit und stellt sicher, dass die Klinge der Belastung beim Schneiden standhält.
- Einsatzhärten: Erhöht die Oberflächenhärte für eine verbesserte Verschleißfestigkeit, während der weichere Kern für mehr Flexibilität erhalten bleibt.
- Dateneinblick: Laut Branchenforschung können ordnungsgemäß gehärtete Klingen im Vergleich zu nicht gehärteten Klingen 25% mehr Belastung aushalten.
4.4 Kantenschleifen und Finishing
Der Präzisionsschliff bestimmt die Schärfe und Schneidleistung der Klinge.
- Diamantschleifen: Wird für ultrafeine Kanten verwendet, insbesondere bei Klingen mit Hartmetall- und Diamantspitze.
- Oberflächenbeschichtungen: Reibungsmindernde Beschichtungen wie Titannitrid verbessern die Schneidleistung und verringern den Verschleiß.
- Studienhighlight: Klingen mit Titannitrid-Beschichtungen weisen im Hochgeschwindigkeitsbetrieb einen geringeren Verschleiß auf als 30%.
4.5 Qualitätskontrolle und Prüfung
Jede Klinge wird strengen Tests unterzogen, bevor sie den Kunden erreicht.
- Härteprüfung: Stellt sicher, dass die Klinge die gewünschten Rockwell-Härtegrade erreicht.
- Überprüfung der Maßgenauigkeit: Überprüft, ob die Klinge enge Toleranzen einhält, normalerweise innerhalb von ±0,01 mm.
- Haltbarkeitstests: Simuliert reale Bedingungen, um die Lebensdauer zu bewerten.
- Industriestandards: Für Qualitätshersteller ist die Einhaltung der Normen ISO 9001 und ISO 14001 verpflichtend.
5. Branchenübergreifende Anwendungen industrieller Schneidklingen
5.1 Metalarbeitende Industrie
Metalworking verlässt sich bei Schneid-, Scher- und Schlitzarbeiten auf langlebige Klingen.
- Anwendungen: Schneiden von Stahlblechen, Besäumen von Aluminiumprofilen und Aufschlitzen von Coils.
- Fallstudie: Ein Fertigungsbetrieb stellte auf Hartmetallklingen um und steigerte seine Produktion um 30%, wodurch durch die Verringerung der Ausfallzeiten jährlich $50.000 eingespart wurden.
5.2 Holzverarbeitende Industrie
Die Holzbearbeitung erfordert Präzision und Langlebigkeit der Sägeblätter.
- Anwendungen: Holzplatten zuschneiden, Furniere beschneiden und Möbel herstellen.
- Tipps:
- Verwenden Sie für Harthölzer Sägeblätter mit Hartmetallzähnen, um den Verschleiß zu verringern.
- Reinigen Sie Harzablagerungen regelmäßig, um die Schneidleistung aufrechtzuerhalten.
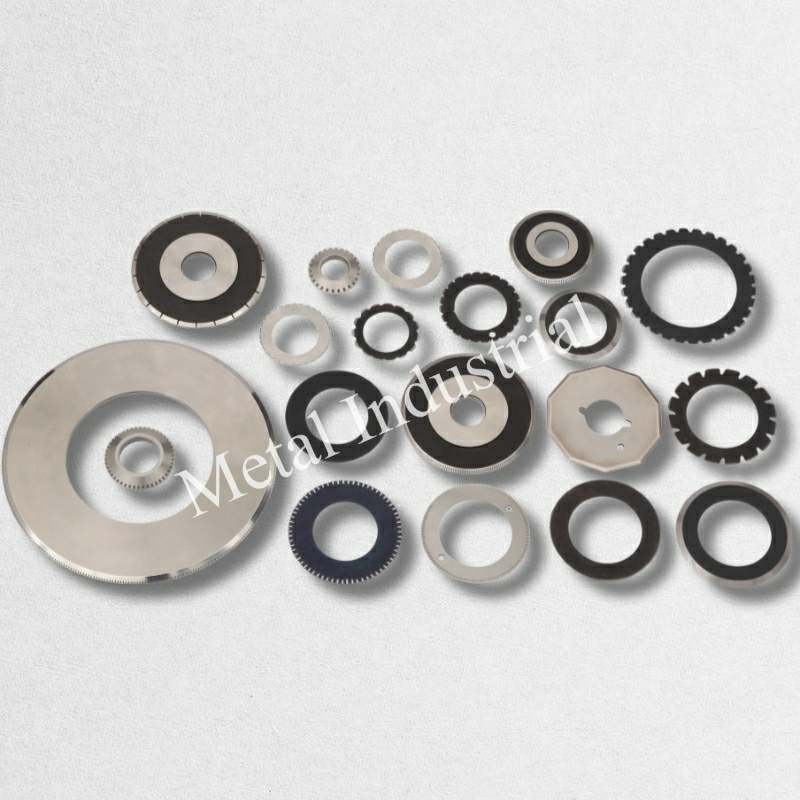
5.3 Kunststoffe und Verbundwerkstoffe
In diesen Branchen müssen die Klingen saubere, gratfreie Schnitte gewährleisten.
- Herausforderungen: Kunststoffe können durch Reibung schmelzen, während Verbundwerkstoffe ausfransen können.
- Lösungen:
- Verwenden Sie für Verbundwerkstoffe diamantbestückte Klingen.
- Tragen Sie reibungsmindernde Beschichtungen auf, um ein Schmelzen zu verhindern.
5.4 Lebensmittelindustrie
Hygiene und Präzision sind bei der Lebensmittelverarbeitung von entscheidender Bedeutung.
- Anwendungen: Schneiden von Brot, Fleisch und abgepackten Lebensmitteln.
- Einhaltung: Klingen müssen den FDA- oder gleichwertigen Standards für Hygiene und Materialsicherheit entsprechen.
6. Kundenspezifische industrielle Schneidklingendienste von Nanjing Metal Industrie
6.1 Warum wählen Kundenspezifische Klingen?
Maßgefertigte Klingen lösen einzigartige Schneidprobleme und verbessern die Effizienz.
- Vorteile:
- Maßgeschneiderte Materialien für spezifische Anwendungen.
- Optimierte Designs für maximalen Durchsatz.
6.2 Unser Anpassungsprozess
- Beratung: Verstehen Sie die Bedürfnisse des Kunden.
- Prototyping: Entwickeln Sie testbare Modelle.
- Präzisionsfertigung: Liefern Sie Hochleistungsblätter mit engen Toleranzen.
6.3 Fallstudien: Nachgewiesene Ergebnisse
- Beispiel: Ein Kunde aus der Papierindustrie reduzierte seinen Abfall um 201 TP4T und sparte durch den Einsatz unserer Schneidklingen jährlich 1 TP5T40.000.
6.4 Vorteile einer Partnerschaft mit uns
- Expertise in der Herstellung von Hochleistungsklingen.
- Schnelle Bearbeitungszeiten und wettbewerbsfähige Preise.
- Engagierter Kundensupport und Kundendienst.
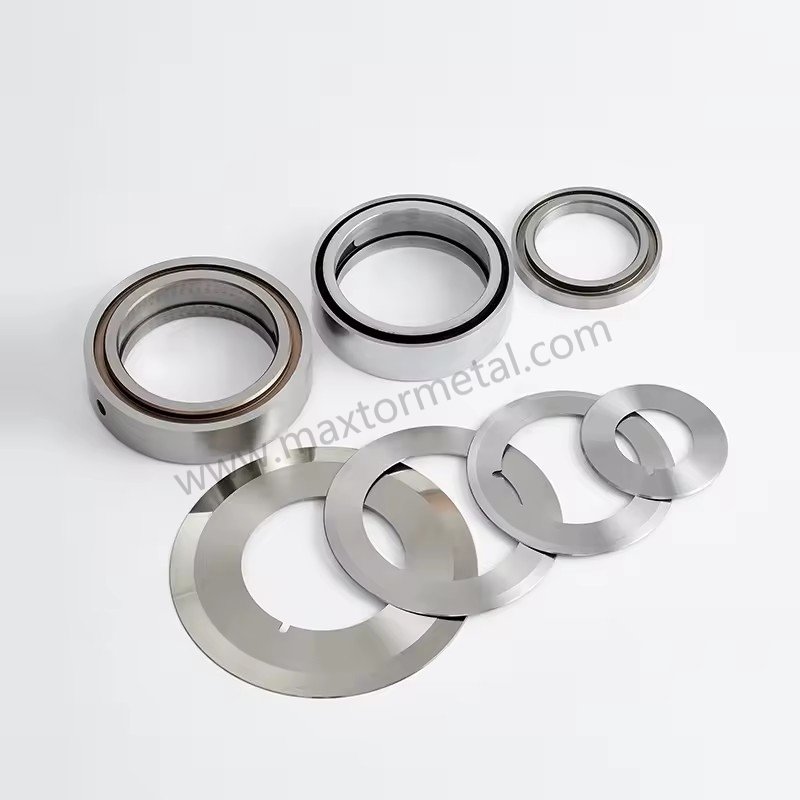
7. Wartungstipps zur Verlängerung der Lebensdauer Ihrer Schneidklingen
7.1 Regelmäßige Reinigung und Inspektion
- Verwenden Sie alkoholbasierte Reiniger, um Rückstände zu entfernen.
- Überprüfen Sie wöchentlich, ob Risse oder stumpfe Kanten vorhanden sind.
7.2 Sachgemäße Lagerung
- Bewahren Sie die Klingen in einem trockenen, geordneten Gestell auf, um Rost zu vermeiden.
7.3 Schärfen vs. Ersetzen
- Schärfen Sie die Klingen, wenn der Schnitt ungleichmäßig wird. Ersetzen Sie sie, wenn das Schärfen die Leistung nicht mehr verbessert.
Indikator | Aktion |
Stumpfe Kanten | Schärfen |
Ungleichmäßige Schnitte | Schärfen |
Anhaltendes Absplittern | Ersetzen |
8. So wählen Sie den richtigen Lieferanten für Ihre Schneidklingen
8.1 Bewertung von Qualität und Zertifizierungen
- Suchen Sie nach ISO-zertifizierten Lieferanten, um eine gleichbleibende Qualität sicherzustellen.
8.2 Anpassungsoptionen und technischer Support
- Wählen Sie Lieferanten, die maßgeschneiderte Designs und Kundendienst anbieten.
8.3 Kundenrezensionen und Fallstudien
- Lesen Sie Erfahrungsberichte und Erfolgsgeschichten, um den Ruf des Anbieters einzuschätzen.
8.4 Warum Nanjing Metal Industrial heraussticht
- Wir bieten Kompetenz, Zuverlässigkeit und kundenorientierten Service.
Die richtige Wahl für Ihre Schneidanforderungen
Die Wahl des richtigen Industrieschneidblatts erfordert ein Verständnis Ihrer Anforderungen, der Eigenschaften des Blatts und seiner Anwendung. Ob Standard- oder Sonderlösung – Nanjing Metal Industrial bietet Ihnen das Know-how, um Ihre Herausforderungen zu meistern.
Kontaktieren Sie uns uns zuTag für eine kostenlose Beratung oder ein Angebot!