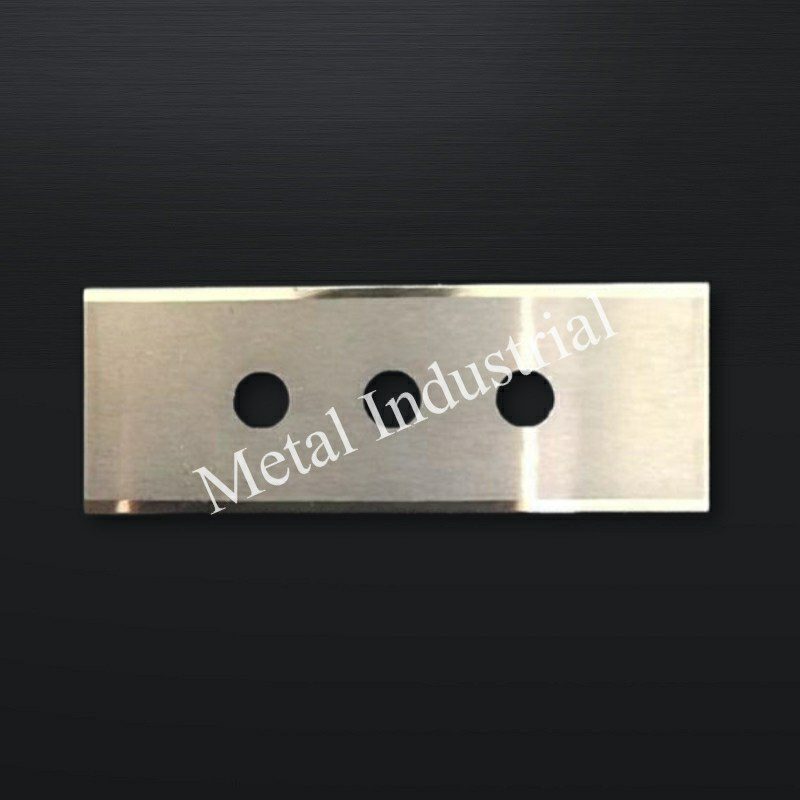
Cuchillas para proceso de película Desempeñan un papel crucial en las fábricas, especialmente cuando se requiere un corte preciso de películas, láminas y materiales blandos. Estas cuchillas garantizan bordes limpios y minimizan el desperdicio, lo que las hace esenciales en diversas aplicaciones industriales. Muchas fábricas ahora exigen... cuchilla personalizada Para manejar materiales únicos y tareas especializadas. El recubrimiento adecuado de la cuchilla no solo prolonga la vida útil de la hoja, sino que también reduce la fricción y mantiene una calidad de corte superior. Con la creciente automatización y los avances en la tecnología de recubrimiento de cuchillas, la demanda de cuchillas para el procesamiento de películas aumenta constantemente. Se espera que el mercado de cuchillas de guillotina industriales crezca de... USD 1.200 millones en 2023 a USD 2.100 millones en 2032.
Métrica/Segmento | Detalles/Estadísticas |
---|---|
Tamaño del mercado (2024) | 1.500 millones de dólares |
Tamaño proyectado del mercado (2033) | 2.500 millones de dólares |
Tasa de crecimiento anual compuesta (TCAC) (2026-2033) | 6.2% |
Participación en los ingresos de las aplicaciones clave | Embalaje: 30%, Metal Procesamiento: 45% |
Factores impulsores del crecimiento | Automatización, recubrimiento avanzado de cuchillas, crecimiento industrial. |
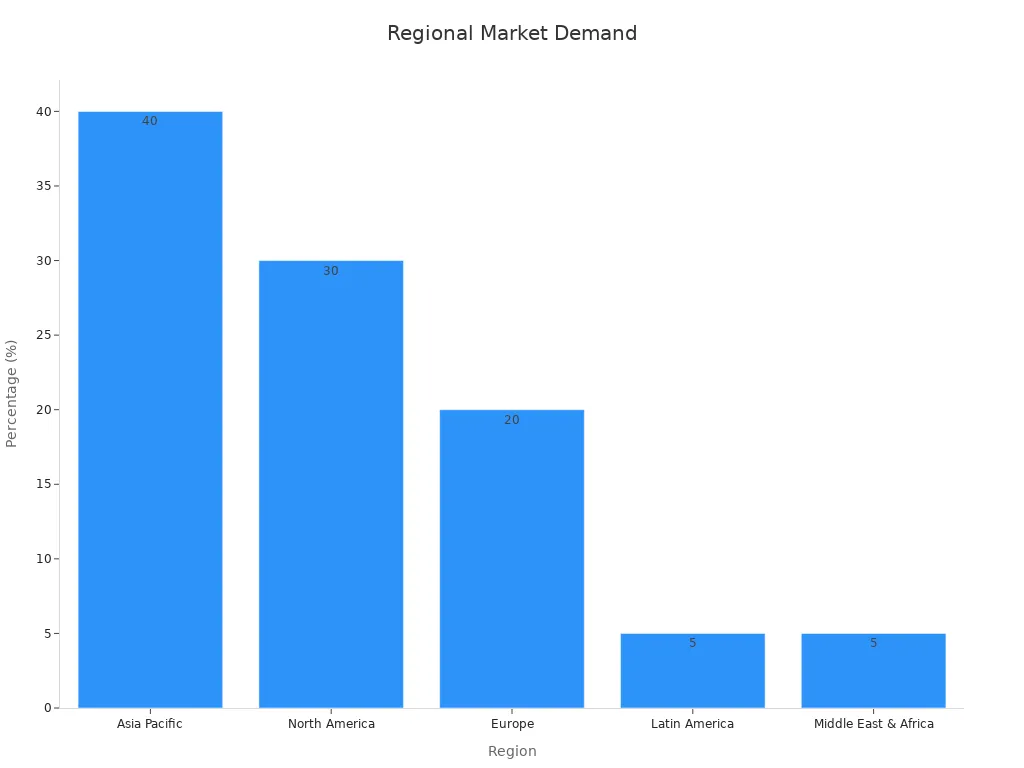
Para empresas que buscan soluciones personalizadas, Nanjing Metal Ofrece opciones de cuchillas personalizadas diseñadas para satisfacer requisitos industriales específicos. Para obtener más información sobre sus productos o hablar sobre sus necesidades, por favor... póngase en contacto con Nanjing Metal directamente. La elección de las cuchillas de procesamiento de película adecuadas, su correcto mantenimiento y el uso de tecnologías de recubrimiento innovadoras son factores clave que ayudan a las empresas a mejorar la eficiencia y la calidad de sus productos.
Puntos clave
- Elegir la cuchilla y el revestimiento adecuados para el proceso de película ayuda a que el corte funcione mejor, produce menos desperdicio y permite que las cuchillas duren más.
- Hay diferentes tipos de cuchillos y recubrimientos para determinados materiales y trabajos, por lo que utilizar el cuchillo adecuado para la película hace que el trabajo sea más rápido y preciso.
- Cuidar los cuchillos, limpiarlos bien y manipularlos de forma segura los mantiene afilados, fuertes y seguros a los trabajadores.
- Los recubrimientos especiales como el nitruro de titanio y el carbono similar al diamante generan menos fricción, evitan el desgaste y ayudan a que los cuchillos duren mucho tiempo.
- Los cuchillos personalizados fabricados para materiales y trabajos especiales ayudan a fabricar más productos, evitar demoras y ahorrar dinero.
Descripción general de las cuchillas para el procesamiento de películas
Tipos
Las fábricas utilizan diferentes cuchillas industriales para el procesamiento de películas. Cada tipo de cuchilla realiza una función específica. A continuación, se presentan algunos tipos comunes:
- Cuchillas rotativas Gira rápido y corta la película suavemente.
- cuchillos rectos Se mueven en línea recta y son buenos para recortar.
- cuchillos circulares Son redondas y cortan la película con mucha precisión.
- Cuchillas de perforación hacer pequeños agujeros o líneas en la película.
- Cuchillos de corte aplastado Presione hacia abajo para cortar películas blandas fácilmente.
Cada tipo de cuchillo ayuda a las fábricas a obtener los mejores resultados para sus productos.
Características
Los cuchillos industriales requieren ciertas características para funcionar correctamente. Las más importantes son:
- Dureza Ayuda a que los cuchillos se mantengan afilados y corten limpiamente.
- Tenacidad evita que los cuchillos se rompan o se astillen.
- Resistencia al desgaste significa que los cuchillos duran más con mucho uso.
- Ductilidad Permite que los cuchillos se doblen sin romperse bajo tensión.
- Pureza significa que los cuchillos fabricados sin malos materiales funcionan mejor.
Los fabricantes utilizan tratamientos térmicos para hacer los cuchillos más resistentes. Por ejemplo, tratamiento térmico al vacío Mantiene los cuchillos limpios y resistentes. Nuevos recubrimientos como el nitruro de titanio y Carbono similar al diamante Estos recubrimientos endurecen los cuchillos. Además, reducen la fricción y previenen la oxidación. Los cuchillos recubiertos duran más y cortan mejor la película.
Consejo: El recubrimiento adecuado de la cuchilla ayuda a que sus herramientas de corte duren más y mejora el corte de la película.
Diseños de cuchillas
El diseño de la cuchilla es importante para un buen corte de la película. Los diferentes diseños varían la profundidad, la velocidad y la limpieza del corte. Algunos aspectos importantes del diseño son:
- Forma de la hoja Puede ser recta, curva o tener dientes para diferentes películas.
- Geometría del borde significa que los bordes afilados y delgados cortan limpiamente, los bordes gruesos son más fuertes.
- Proyección y velocidad asunto. A Proyección de hoja de 5 mm y velocidad de 370 rpm Funciona mejor para cortar.
- Tipo de movimiento Es importante. Algunos cuchillos alternan entre girar y moverse hacia adelante y hacia atrás.
- Retirada de escombros Ayuda a mantener los restos alejados para que el corte se mantenga suave.
Un buen diseño de cuchilla corta la película al tamaño adecuado y reduce el desperdicio. Además, mantiene el buen funcionamiento de las líneas de producción. Las fábricas ahora utilizan materiales resistentes como acero de alta velocidad y carburo de tungsteno. Algunas incluso utilizan recubrimientos nanoestructurados para un mejor rendimiento. La automatización y las máquinas inteligentes facilitan el ajuste rápido de las cuchillas, lo que aumenta la eficiencia.
Cuchillas para procesamiento de películas Aplicaciones industriales
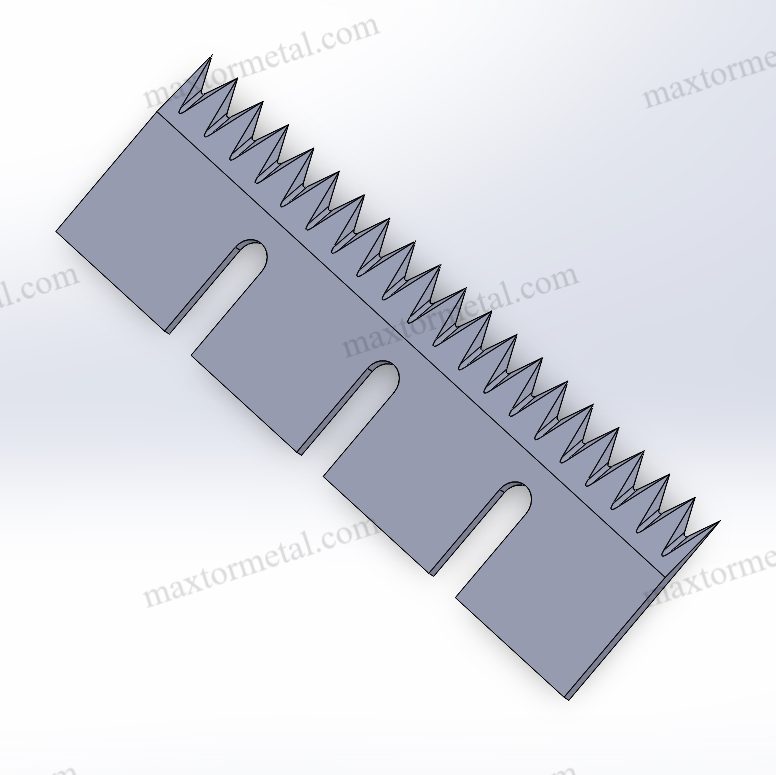
Fabricación de películas
Aplicaciones típicas
Las fábricas utilizan cuchillas industriales para cortar y dar forma a películas de plástico. Los trabajadores manipulan materiales como poliéster y polipropileno en la línea de producción. Estas cuchillas ayudan a fabricar rollos de película delgada para electrónica y embalaje.
Tipos y características de cuchillos comunes
Los operadores eligen cuchillas de corte rotativas, rectas y circulares. Estas cuchillas trabajan con rapidez y pueden funcionar todo el día. Tienen bordes afilados y cuerpos robustos. Muchas cuentan con un recubrimiento especial para evitar la fricción y el desgaste. Algunas cuchillas tienen dientes diminutos para sujetar mejor las películas delgadas.
Principales desafíos técnicos
La fabricación de películas presenta numerosos problemas que resolver. Las máquinas deben cortar de forma limpia y rápida. Las películas delgadas se rompen o arrugan con mucha facilidad. Las fábricas buscan reducir los desperdicios y mantener cada corte impecable. Cortar muchas capas a la vez es aún más difícil.
Soluciones y mejoras
Los fabricantes utilizan hojas muy afiladas y resistentes con un recubrimiento avanzado. Los sistemas automatizados ayudan a mantener cortes rectos y precisos. Las revisiones y cambios de hoja regulares previenen problemas antes de que surjan. Los recubrimientos especiales, como el nitruro de titanio, prolongan la vida útil de los cuchillos y optimizan el corte.
Nota: El recubrimiento adecuado de la cuchilla ayuda a reducir el tiempo de inactividad y hace que el trabajo sea más fluido.
Ejemplo
Al fabricar películas ópticas para teléfonos, se necesitan cuchillas de precisión. Estas cuchillas mantienen el tamaño exacto y la superficie lisa, lo que previene defectos en el producto final.
Embalaje
Aplicaciones típicas
Los cuchillos industriales son importantes en el embalaje. Los trabajadores los utilizan para cortar, perforar y rayar películas y láminas. Estos materiales protegen alimentos, medicamentos y otros productos.
Tipos y características de cuchillos comunes
Los cuchillos en zigzag, las hojas de perforación y los cuchillos de sellado térmico se utilizan con frecuencia. Muchos cuchillos tienen recubrimientos antiadherentes para que nada se les pegue. Las hojas de acero inoxidable ayudan a mantener la limpieza en las fábricas de alimentos.
Principales desafíos técnicos
Las líneas de envasado deben ser rápidas. Las máquinas deben cortar muchos materiales sin atascarse. Los cortes limpios son importantes para la seguridad. La higiene es fundamental, especialmente con los alimentos. Los materiales pegajosos y los cortes ásperos pueden ralentizar el proceso.
Soluciones y mejoras
El recubrimiento antiadherente de los cuchillos y las hojas de acero inoxidable ayudan a mantener la limpieza. Los cortadores ajustables permiten cambiarlos según el grosor del material. Limpiar y revisar las hojas con frecuencia garantiza un funcionamiento óptimo.
Consejo: El cuchillo y el recubrimiento adecuados hacen que el envasado sea más rápido y seguro.
Ejemplo
En las líneas de envasado de snacks, se utilizan cuchillos especiales que cortan con rapidez y limpieza. Estos cuchillos eliminan los gérmenes y mantienen los alimentos seguros para las personas.
Conversión de Papel
Aplicaciones típicas
Las plantas de conversión utilizan cuchillas para cortar, rebobinar y laminar películas y láminas. Los trabajadores procesan películas adhesivas para productos electrónicos y automóviles. A menudo manipulan películas delgadas y materiales mixtos.
Tipos y características de cuchillos comunes
Aquí son comunes las cuchillas de corte, las cuchillas de corte por aplastamiento y las hojas de afeitar. Los soportes modulares y los sistemas de cambio rápido facilitan el cambio de cuchillas. Muchas cuchillas cuentan con un recubrimiento avanzado para una mayor durabilidad.
Principales desafíos técnicos
Cambiar los materiales con frecuencia puede ralentizar la línea. Los trabajadores deben mantener cortes uniformes con muchos tipos de materiales. Detenerse para cambiar las cuchillas puede suponer una pérdida de tiempo.
Soluciones y mejoras
Las fábricas utilizan soportes modulares y sistemas de cambio rápido para ahorrar tiempo. Los mejores materiales de las hojas y el recubrimiento de los cuchillos prolongan su vida útil. La revisión y el cuidado de los cuchillos los mantienen afilados y listos para usar.
Alerta: Los sistemas de cuchillas de cambio rápido ayudan a las plantas a cortar muchos materiales con menos espera.
Ejemplo
En electrónica, las líneas de conversión utilizan cuchillas afiladas para películas adhesivas. Estas cuchillas cortan con gran precisión y desperdician menos material.
Otros sectores
Aplicaciones típicas
Los cuchillos industriales también se utilizan en fábricas médicas, automotrices y textiles. Los trabajadores cortan materiales delicados, como paquetes estériles y telas especiales.
Tipos y características de cuchillos comunes
Se utilizan cuchillos con formas personalizadas, hojas microdentadas y recubrimientos especiales. Algunos cuchillos tienen recubrimientos de cerámica o carbono tipo diamante para mayor resistencia.
Principales desafíos técnicos
El corte de materiales sensibles o controlados requiere normas estrictas. Las fábricas deben mantener la limpieza y los productos en perfectas condiciones. Algunos materiales son duros o ásperos y desgastan las cuchillas rápidamente.
Soluciones y mejoras
Los fabricantes colaboran con cuchilleros para diseñar hojas personalizadas. Los materiales resistentes y el recubrimiento prolongan la vida útil de los cuchillos. Se realizan inspecciones minuciosas para garantizar que cada cuchillo cumpla con las normas.
Recordatorio: Los cuchillos personalizados con el recubrimiento adecuado ayudan a las fábricas a seguir las reglas y fabricar buenos productos.
Ejemplo
En los envases médicos, las cuchillas para film deben cortar con precisión y mantenerse estériles. Estas cuchillas ayudan a las empresas a cumplir con las normas sanitarias y a mantener la seguridad de sus productos.
Cuchillas para proceso de película: selección y mantenimiento
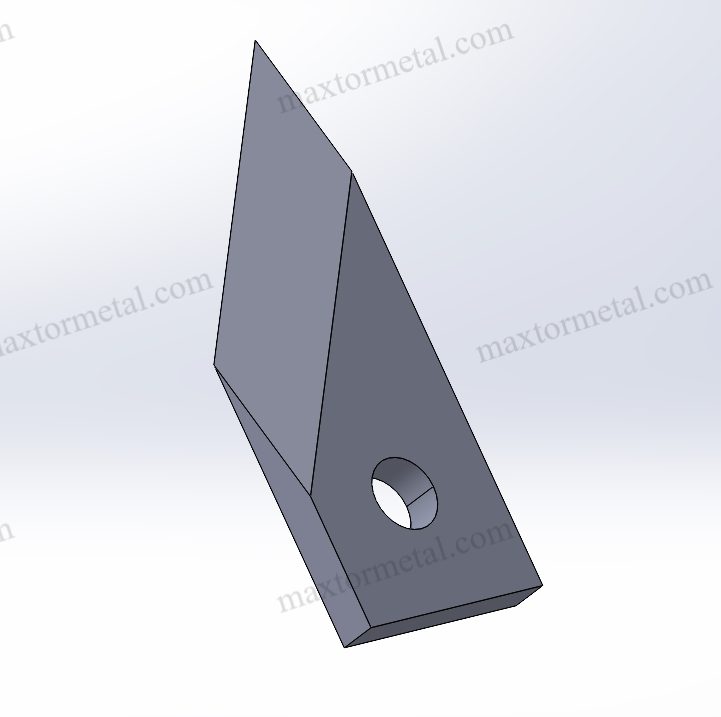
Compatibilidad de materiales
Tipos de materiales comunes
Las fábricas utilizan diversos materiales de película. Estos incluyen películas plásticas como el polietileno y el polipropileno. También utilizan láminas metálicas como el aluminio. Algunas películas son compuestas y tienen capas para usos especiales. Cada material difiere en dureza, grosor y flexibilidad. Algunas películas son puras, pero otras tienen contenido reciclado o mixto.
Recomendaciones para la selección de cuchillos
Es importante elegir la cuchilla adecuada para cada película. Las cuchillas de alta dureza son ideales para películas limpias y vírgenes. Estas cuchillas se mantienen afiladas durante más tiempo. Para películas recicladas o mixtas, utilice cuchillas de menor dureza y mayor tenacidad. Estas cuchillas no se astillan tan fácilmente y duran más. Los fabricantes suelen utilizar acero endurecido o carburo para cuchillas resistentes. Un recubrimiento especial para cuchillas, como el nitruro de titanio o el carbono tipo diamante, prolonga su vida útil y requiere menos mantenimiento. Modificar la geometría de la cuchilla, como usar un ángulo de ataque de 60° para películas delgadas, ayuda a evitar que la película se doble. Los recubrimientos antiadherentes evitan que las películas pegajosas se adhieran a la cuchilla.
Caso práctico
Una planta de envasado cambió su cuchilla de acero convencional por una de carburo con revestimiento antiadherente para cortar papel de aluminio. La nueva cuchilla 30% duró más y tuvo menos tiempo de inactividad. La planta tuvo menos atascos y cortes más limpios, lo que mejoró la calidad del producto.
Asesoramiento operativo
Los operadores deben revisar los filos de los cuchillos para detectar desgaste o astillamiento. Para un rendimiento óptimo, utilice el material y el recubrimiento del cuchillo adecuados para el tipo de película. Revise y limpie las hojas con frecuencia con disolventes de pH neutro y cepillos suaves. Guarde los cuchillos en lugares secos, con clima controlado y cubiertos.
Errores comunes a evitar
- Utilizar un cuchillo duro sobre una película blanda puede provocar daños y desperdicio.
- No utilizar el recubrimiento adecuado hace que los cuchillos se desgasten más rápido.
- La no coincidencia de la geometría de la cuchilla con el tipo de película provoca malos cortes y más desperdicio.
Precisión
Importancia de la precisión en el corte de películas
La precisión es importante en el corte de película. Ayuda a crear buenos productos y a ahorrar material. Las tolerancias estrictas garantizan que cada pieza cumpla su función. Una precisión deficiente puede causar bordes irregulares, desperdicio de película y productos rechazados. En las líneas automatizadas, las cuchillas de alta precisión ayudan a reducir el tiempo de inactividad y a mantener el sistema en funcionamiento.
Selección de cuchillos para una alta precisión
El filo y la geometría del filo son importantes para la precisión. Los cuchillos con filos finos y uniformes cortan limpio y producen menos rebabas. El recubrimiento avanzado, como el Carbono Tipo Diamante, ayuda a que los cuchillos se mantengan afilados durante más tiempo. El cambio de hoja sin herramientas y las funciones de autoafilado también ayudan a mantener cortes precisos.
Caso práctico
Una empresa de electrónica utilizó cuchillos de alta precisión con un recubrimiento especial para cortar películas adhesivas. El tiempo de inactividad se redujo en 18% El rendimiento aumentó de 89% a 97%. Las cuchillas produjeron filos más suaves y menos desperdicio.
Asesoramiento operativo
Los operadores deben calibrar las máquinas con frecuencia y revisar las cuchillas con lupa cada dos semanas. Ajuste la velocidad de avance y la refrigeración para mantener la superficie en buen estado. La refrigeración por aire suele ofrecer la mejor combinación de velocidad y calidad de corte.
Errores comunes a evitar
- No estar atento al desgaste de la cuchilla da lugar a malos cortes y productos de mala calidad.
- Saltarse la calibración puede provocar errores de tamaño.
- El uso de un recubrimiento de cuchillo incorrecto reduce la precisión y significa más reparaciones.
Durabilidad
Causas comunes del desgaste de los cuchillos
Las cuchillas se desgastan por abrasión, corrosión y uso inadecuado. Cortar películas ásperas o sucias desgasta el filo más rápido. Usar limpiadores abrasivos o guardar las cuchillas en lugares húmedos puede causar oxidación y dañar el recubrimiento. Sobrecargar la cuchilla o usar una velocidad incorrecta la somete a tensión y la acelera.
Consejos de mantenimiento y longevidad
- Limpie los cuchillos todos los días con disolventes suaves y con pH neutro.
- Utilice cepillos suaves o paños de microfibra para proteger el revestimiento.
- Guarde los cuchillos en habitaciones secas, con clima controlado y baja humedad.
- Revise los bordes con un aumento de 10x cada dos semanas.
- Calibre el torque cada 500 horas de uso.
- Siga las normas ISO 16090 para que las cuchillas duren hasta 40% más.
- Utilice aceite protector para un almacenamiento prolongado si es seguro para el cuchillo.
Caso práctico
Una planta de electrónica flexible implementó un estricto plan de mantenimiento para sus cuchillas de corte circular. La planta utilizaba cuchillas con recubrimiento avanzado y cumplía con la norma ISO 16090. La vida útil de la cuchilla pasó de 600.000 a 1.200.000 cortes., y los desechos arrojados por 18%.
Asesoramiento operativo
Los operadores deben usar cubiertas al mover las cuchillas y evitar golpes. Las herramientas predictivas, como los comprobadores de vibración, pueden detectar el desgaste prematuro. Considere recubrir las cuchillas si la hoja aún está en buen estado, pero el recubrimiento está desgastado.
Errores comunes a evitar
- Ignorar los primeros signos de desgaste puede provocar fallas repentinas.
- El uso de abrasivos fuertes o lana de acero puede dañar el revestimiento del cuchillo.
- Guardar los cuchillos en lugares húmedos o con temperaturas cambiantes provoca oxidación y acorta su vida útil.
Seguridad
Protocolos y equipos de seguridad
La seguridad es fundamental con las cuchillas de procesamiento de película. Los operadores deben usar EPI, como guantes y gafas de seguridad. Las protecciones de la máquina deben estar siempre instaladas. La capacitación sobre manejo y cuidado seguros ayuda a prevenir accidentes. Las guías paso a paso ayudan a los operadores a realizar las tareas correctamente.
Asesoramiento operativo
Los operadores nunca deben saltarse los enclavamientos de seguridad ni retirar las protecciones. Siempre utilicen un sistema de elevación seguro y lleven los cuchillos cubiertos. La capacitación regular mantiene a todos al día en materia de seguridad.
Caso práctico
Una planta de empaque inició una capacitación en seguridad y utilizó protectores de maquinaria para todo el trabajo con cuchillos. Se redujeron los accidentes y los trabajadores se sintieron más seguros. La empresa también tuvo menos cuchillos dañados gracias a un mejor manejo.
Errores comunes a evitar
- Saltarse los bloqueos de seguridad aumenta el riesgo de sufrir lesiones.
- No utilizar EPP pone a los trabajadores en riesgo de sufrir cortes y otros peligros.
- La falta de formación da lugar a un mal manejo y a más accidentes.
🛡️ Consejo: Un manejo seguro y una capacitación regular garantizan la seguridad tanto de los trabajadores como de los cuchillos.
Recubrimiento de cuchillos e innovaciones
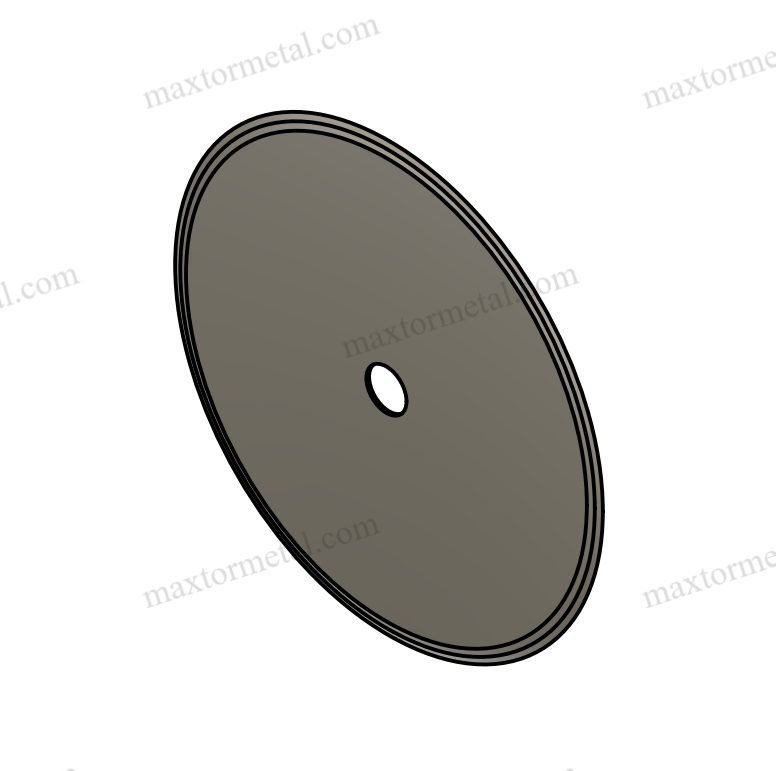
Tipos de recubrimiento
Recubrimiento de nitruro de titanio (TiN)
El recubrimiento de nitruro de titanio le da al cuchillo un aspecto dorado y una gran dureza. Este recubrimiento proporciona una capa resistente a la hoja. Ayuda a prevenir el desgaste y mantiene el cuchillo afilado. El TiN es ideal para cortar películas de plástico y láminas. Muchas fábricas eligen este recubrimiento por su larga duración.
Recubrimiento de nitruro de titanio y aluminio (TiAlN)
El recubrimiento de nitruro de titanio y aluminio protege los cuchillos del calor y la oxidación. Este recubrimiento prolonga la vida útil de las hojas, incluso con movimientos rápidos. El TiAlN se utiliza en el corte de películas, donde las superficies se calientan rápidamente. El espesor del recubrimiento se ajusta para mantener la hoja afilada y resistente.
Recubrimiento de carbono tipo diamante (DLC)
El revestimiento de carbono tipo diamante hace que el cuchillo sea muy duro y suave.Este recubrimiento reduce la fricción y evita que se adhieran las películas pegajosas. Los recubrimientos DLC ayudan a los cuchillos a cortar bien y a durar más. El recubrimiento es delgado pero resistente, ideal para cortes precisos.
Recubrimientos cerámicos
Los recubrimientos cerámicos aplican una capa dura, no metálica, al cuchillo. Este recubrimiento ayuda a prevenir el desgaste y evita que la hoja se oxide. Los recubrimientos cerámicos funcionan bien en ambientes húmedos o agresivos. El grosor del recubrimiento puede variar según el tipo de corte.
Recubrimientos nano multicapa
Los nanorrecubrimientos multicapa utilizan muchas capas delgadas para optimizar el rendimiento de las cuchillas. Cada capa del recubrimiento aumenta la resistencia, reduce la fricción y previene el desgaste. Estos recubrimientos permiten que las cuchillas realicen trabajos exigentes y duren más. Las fábricas los utilizan para el corte de películas que requiere alta precisión.
Beneficios de rendimiento
Resistencia al desgaste mejorada
El recubrimiento de las cuchillas ayuda a que resistan el desgaste. Por ejemplo, el recubrimiento de TiN puede reducir el desgaste en 45%. Esto significa que la cuchilla se mantiene afilada y corta más película antes de cambiarla.
Adhesión y fricción reducidas
El recubrimiento de cuchillas, como el DLC, reduce la fricción y evita la acumulación de películas pegajosas. Esto permite un corte más suave y rápido. Los recubrimientos TFMG pueden reducir la fuerza de corte en más de 50%, por lo que los cuchillos se mueven más fácilmente a través de materiales duros.
Mayor vida útil del cuchillo
Un buen recubrimiento de cuchillos prolonga la vida útil de la hoja. Algunos recubrimientos, como el cromo duro, pueden triplicar la vida útil de los cuchillos. Esto se traduce en menos tiempo de inactividad y ahorro de dinero.
Calidad de corte mejorada
El recubrimiento de los cuchillos ayuda a que las hojas realicen cortes más limpios. Las pruebas demuestran que los cuchillos recubiertos ofrecen filos más suaves y menos desperdicio. Un recubrimiento con el grosor adecuado mantiene la hoja afilada y firme.
Protección contra la corrosión
El recubrimiento de los cuchillos protege contra la oxidación y los daños causados por el agua. Los recubrimientos de níquel químico pueden duplicar la vida útil de las herramientas en entornos húmedos. Esto es importante para los cuchillos utilizados en la industria alimentaria o cerca del mar.
🛠️ Consejo: Elegir el recubrimiento y el grosor adecuados de la cuchilla puede hacer que el corte de la película sea mejor y más rápido.
Tipo de recubrimiento | Beneficio de rendimiento | Mejora cuantificada | Contexto de aplicación |
---|---|---|---|
Estaño | Resistencia al desgaste | 45% reducción del desgaste | Aplicaciones de corte |
TiCN | Extensión de la vida útil de la cuchilla | 40% aumento de la vida útil de la cuchilla | Mecanizado de acero endurecido |
Cromo duro | Prolongación de la vida útil | Vida útil 3 veces más larga | Fabricación de automóviles |
Teflón | Mejora del tiempo de actividad y reducción de atascos | 15-20% mayor tiempo de actividad; 50% reducción en la adherencia del material | Corte de películas plásticas y materiales adhesivos |
Níquel químico | Resistencia a la corrosión y vida útil de la herramienta | Hasta 50% mayor vida útil de la herramienta en entornos marinos | Entornos propensos a la corrosión |
Tendencias
Recubrimientos multicapa y nanoestructurados
Las fábricas ahora utilizan nanorrecubrimientos multicapa para mejorar los cuchillos. Estos recubrimientos, con múltiples capas finas, ofrecen mayor resistencia y menor fricción. El proceso de recubrimiento utiliza nueva tecnología para controlar el grosor y la calidad.
Recubrimientos autocurativos
Algunos recubrimientos nuevos para cuchillos pueden reparar pequeños arañazos por sí solos. Esto mantiene el cuchillo afilado y prolonga su vida útil. Los recubrimientos autocurativos son nuevos, pero podrían ser importantes próximamente.
Recubrimientos inteligentes y responsivos
Los recubrimientos inteligentes pueden detectar cambios de calor o presión. Estos recubrimientos se adaptan para proteger el cuchillo durante el corte. Las fábricas utilizan estos recubrimientos para que el corte sea más seguro y eficaz.
Tecnologías de recubrimiento ecológicas y sostenibles
Muchas empresas ahora buscan procesos de recubrimiento de cuchillos ecológicos. Consumen menos energía y utilizan materiales más seguros. Estos recubrimientos protegen el planeta y cumplen con las nuevas normativas.
Perspectivas de aplicación futuras
El mercado del recubrimiento de cuchillos está en rápido crecimiento. Los expertos creen que se duplicará en diez años. Nuevos métodos de recubrimiento, recubrimientos inteligentes e ideas ecológicas marcarán el camino. Las fábricas obtendrán mejores resultados, menos desperdicio y cuchillos más resistentes.
Soluciones personalizadas
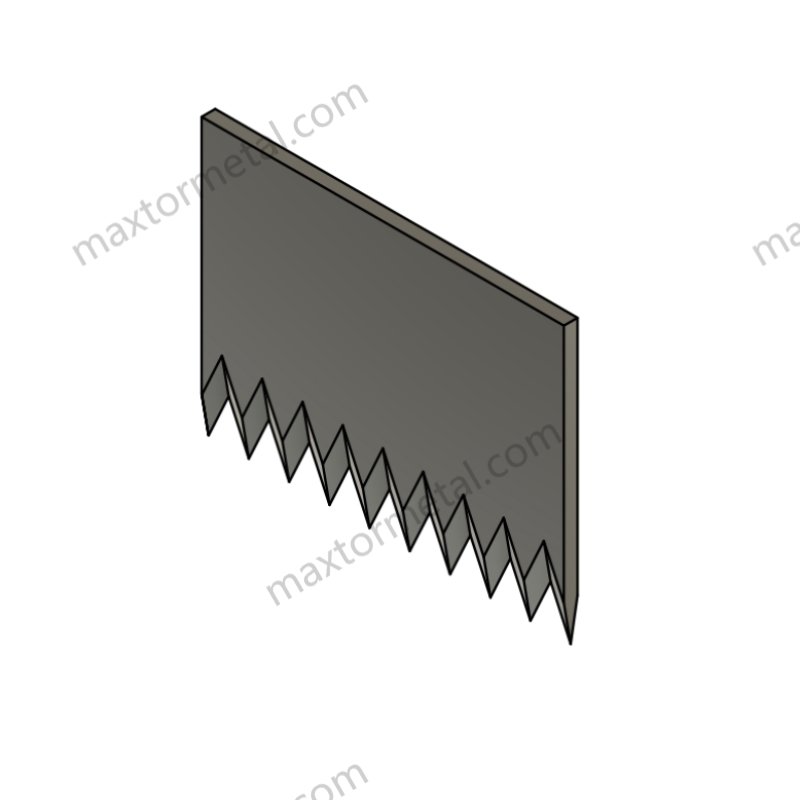
Cuchillos personalizados
Muchas fábricas necesitan cuchillas diseñadas específicamente para ellas. Las cuchillas convencionales no siempre son compatibles con materiales nuevos o especiales. Las cuchillas personalizadas para el procesamiento de películas solucionan estos problemas. Las empresas pueden elegir la forma de la cuchilla, el estilo de filo y el recubrimiento para cada trabajo. Esto permite a las fábricas cortar películas complejas, en capas o ecológicas con gran éxito.
- El El mercado de envases inteligentes está creciendo y alcanzará los 1.500 millones de T/T en 2030..
- Los cuchillos personalizados ayudan a las fábricas a producir más productos, hasta 20% más, y reducen el tiempo de inactividad en 18%.
- Recubrimientos especiales como nitruro de titanio y carbono similar al diamante ayudan a que los cuchillos duren más.
- Los bordes endurecidos con láser mantienen los cuchillos afilados para más de 50.000 cortes.
- Los revestimientos antiadherentes evitan que el pegamento se pegue, por lo que las películas adhesivas son más fáciles de cortar.
- Los cuchillos giratorios rápidos pueden cortar más de 3000 veces por minuto y mantenerse afilados.
Los cuchillos personalizados ayudan a las fábricas a cumplir con las estrictas normas de embalaje ecológico. También contribuyen a la producción de una gran cantidad de productos y a mantener una alta calidad.
Cuándo personalizar
Las fábricas deberían adquirir cuchillas personalizadas si utilizan materiales nuevos, cambian las hojas con frecuencia o necesitan una calidad muy alta. Las cuchillas personalizadas también son ideales para cortar películas recicladas o mixtas. Las nuevas normativas, como el Plan de Acción para la Economía Circular de la UE, implican que las empresas necesitan cuchillas para materiales ecológicos. Las cuchillas personalizadas pueden reducir los costes de cumplimiento normativo hasta en un 20%.
Métrica | Mejora con cuchillas de proceso de película personalizadas | Impacto medible / beneficio financiero |
---|---|---|
Vida útil de la cuchilla | Aumento de hasta 40% | Mayor vida útil operativa, menores costos |
Tiempo de inactividad por mantenimiento | Reducción 30% | Menos tiempo de inactividad para cambios de cuchillas |
Tiempo de ciclo | Reducción 20% | 15.000 unidades más producidas cada mes |
Rendimiento de producción | Aumento de 15-25% | Mayor volumen de salida |
Desperdicios materiales | Reducido de 5% a 2% | Ahorra $150,000 anualmente |
Falta del tiempo | Reducción 50% | $80.000 ganancias anuales de productividad |
Los cuchillos personalizados ayudan a las empresas a ahorrar dinero, desperdiciar menos y trabajar más rápido.
Nanjing Metal
Nanjing Metal es un fabricante de confianza de cuchillas para el procesamiento de películas. La empresa lleva más de 20 años fabricando cuchillas. Su equipo diseña y fabrica cuchillas personalizadas para diversos trabajos. Nanjing Metal utiliza materiales resistentes como carburo de tungsteno y acero de alta velocidad. Sus hojas tienen filos afilados y recubrimientos especiales para cada uso.
Métrica | Hoja estándar | Hoja personalizada |
---|---|---|
Vida útil de la cuchilla | ~10 días | Más de 40 días |
Reducción del tiempo de inactividad | Base | 65% menos tiempo de inactividad |
Reparaciones de emergencia | Base | 70% menos reparaciones |
Costo de reemplazo anual | $25,000 | $9,500 |
Nanjing Metal cuchillos personalizados Corten más limpio, duran más y ayudan a las fábricas a trabajar más rápido. Muchas fábricas confían en esta empresa para obtener cuchillos buenos y resistentes.
Elegir la cuchilla adecuada para el proceso de película y cuidarla adecuadamente facilita cortes precisos y mantiene la producción en marcha. El uso de recubrimientos avanzados, como el de cuchillas, prolonga la vida útil de las cuchillas y mantiene los bordes de la película lisos. Afilar las cuchillas con frecuencia y usar los mejores métodos de afilado las hace más afiladas y ofrece una mejor superficie. Las fábricas que utilizan buenos recubrimientos y cuidan sus cuchillas obtienen menos desperdicio y mejores resultados.
- Las investigaciones muestran que los recubrimientos como AlCrBN pueden hacer que los cuchillos duren más el doble de largo y corte 18% más afilado.
- El recubrimiento de la cuchilla ayuda a detener la fricción y el desgaste, incluso al cortar la película rápidamente.
- Enfriar y moler de la manera correcta mantiene los bordes de los cuchillos afilados para trabajar con películas.
- El afilado con herramientas CBN permite a los trabajadores hacer más y mantiene la superficie en buen estado.
- La forma en que se ve el filo del cuchillo después de afilarlo cambia la eficacia con la que corta la película.
Preguntas frecuentes
¿Cuál es el propósito principal de las cuchillas de procesamiento de película en las fábricas?
Las cuchillas para el procesamiento de películas se utilizan para cortar películas y láminas con gran precisión. Ayudan a las fábricas a obtener bordes lisos y a desperdiciar menos material. Muchas empresas utilizan estas cuchillas para fabricar mejores productos y trabajar más rápido.
¿Cómo mejora un recubrimiento el rendimiento del cuchillo?
Un recubrimiento recubre la superficie del cuchillo con una capa resistente. Esta capa lo hace más resistente y prolonga su vida útil. Además, reduce la fricción, lo que permite un corte más suave y un afilado más duradero.
¿Por qué las fábricas eligen diferentes recubrimientos para sus cuchillos?
Las fábricas eligen los recubrimientos según lo que necesitan cortar. Algunos son mejores para películas pegajosas. Otros protegen contra la oxidación o las altas temperaturas. El recubrimiento adecuado ayuda a que el cuchillo funcione mejor en cada tarea.
¿Con qué frecuencia deben los operadores revisar o reemplazar las cuchillas revestidas?
Los operadores deben revisar las cuchillas recubiertas a diario para detectar daños o desgaste. Revisarlas con frecuencia ayuda a prevenir problemas antes de que surjan. Cambiar la cuchilla cuando el recubrimiento desaparece garantiza cortes seguros y limpios.
¿Pueden los cuchillos personalizados con recubrimientos especiales ayudar con los nuevos materiales?
Las cuchillas personalizadas con recubrimientos especiales pueden ser útiles con materiales nuevos o difíciles de cortar. Estas cuchillas se fabrican según las necesidades de cada fábrica. Facilitan el corte de películas nuevas, materiales reciclados o productos en capas.
Ver también
Cuchilla de Corte de Película Delgada para Baterías de Litio
Los 10 mejores consejos para que tus hojas de afeitar circulares duren más
¿Qué son las cuchillas de corte por aplastamiento y cómo funcionan en la industria?
Cómo elegir la cuchilla perforadora adecuada para su material
Mantenimiento de las cuchillas divisoras de rollos de papel para una máxima eficiencia