
Choosing the right knives for Découpe par Écrasement can change how well slitting works. Blade radius, angle, and type all help the knives cut materials like adhesive, rubber, and film. Workers notice changes in speed, how long blades last, and how good the cuts look when they pick the right blades. The kind of material, edge needs, and how you care for the knives help you pick the best knives and blades for each job.
Principaux points à retenir
- Pick the right blade radius and angle for your material. This helps you get better cuts and makes the blade last longer. – Crush cutting is best for tough, sticky, or thick things like rubber and adhesive tapes. Shear cutting works better for thin or delicate materials. – Use good blade materials and coatings, such as tungsten carbide and Titanium Nitride. These make the blade stronger and help it slide better. – Clean, oil, and check knives often to keep them sharp. This stops damage and bad cuts. – Use the right pressure and line up the blade correctly. This gives you clean cuts and keeps the blade and anvil from wearing out.
What is Crush Cutting
Comment ça marche
Crush cutting is a helpful way to slit materials in factories. This method uses a round blade with a dull edge. The blade pushes down on a hard anvil roll. The pressure from the blade crushes and breaks the material instead of slicing it. Pneumatic systems often help move the blade and control the pressure. This makes the process quick and easy to repeat.
Le blade’s rounded edge spreads out the force. This helps the blade and anvil last longer. The anvil roll is harder than the blade, so the blade wears out first. This keeps the anvil safe. Operators can change the pressure for different materials. This gives them more options when working. Crush slitting works well for tough, sticky, or fibrous materials that are hard to cut with regular blades.
Conseil: Make sure the blade and anvil line up well. Good alignment gives clean cuts and stops the material from bending or tearing.
Key Applications
Many industries use crush cutting because it is simple and saves money. This method is common when companies need to cut big rolls into smaller pieces. It works on many types of materials, even thick or non-woven ones. Laminates, paper, and fabrics also work well with this method.
Crush slitting is good for materials that change in thickness or stiffness. Operators use it to cut adhesive tapes, laminates, nonwovens, foils, rubber, and abrasive papers. The cuts are rougher than with other methods, but setup is fast and costs less. Packaging, textile, and label companies use crush cutting for hard or rough materials.
- Common materials processed with crush cutting:
- Adhesive tapes
- Laminates
- Nonwoven fabrics
- Rubber sheets
- Abrasive papers
- Thick paper and board
Note: Crush cutting is flexible, so many manufacturers like it when they need to slit materials quickly and easily.
Crush Cutting vs Shear Cutting
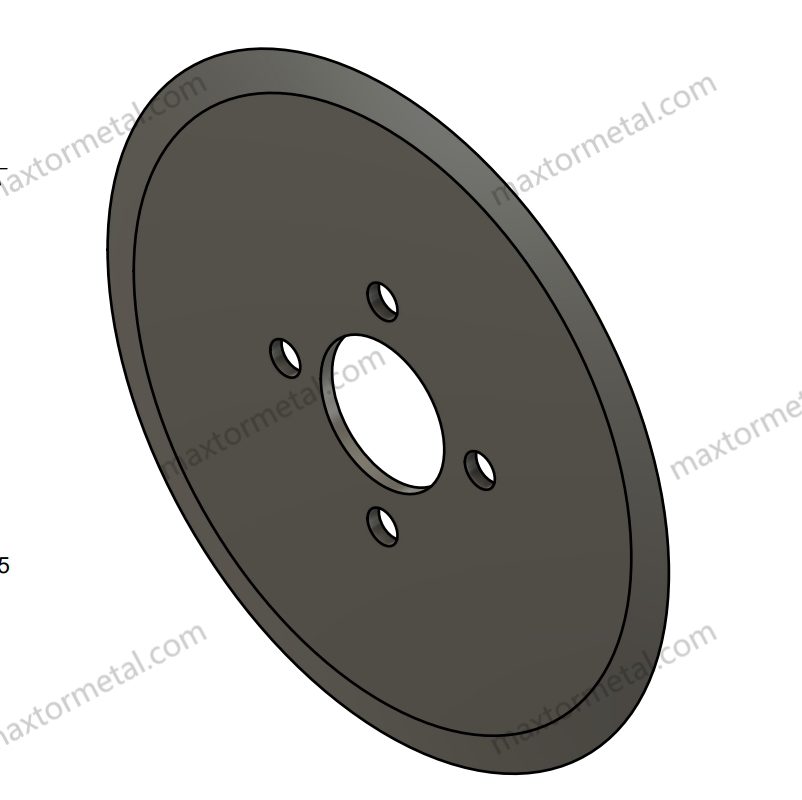
Pros and Cons
Crush Cutting – Pros
Crush cutting is easy to use for many materials. The setup is simple and does not cost much. It uses a round blade that presses on a hard anvil. This works best for soft things like rubber, foams, and adhesive tapes. It is good when you need to switch jobs fast. There is not much maintenance needed. You do not need special skills to line up the blade. Many factories pick this method because it works well for sticky or tough materials.
Crush Cutting – Cons
Crush cutting has some downsides too. The edges can be rougher than with other ways of cutting. Films or brittle materials might get more dust or fuzzy edges. It does not work well for hard or very thin things. Crushing can bend or break these materials. Workers must watch the blade because it can wear out fast if not checked.
Shear Cutting – Pros
Shear cutting uses two rotary knives that cut like scissors. This gives smooth, clean edges and little dust. It works for many materials like films, paper, laminates, textiles, and foils. Shear cutting is good for fast jobs and makes nice cuts. The knives last longer because of the scissor action. Many companies use this way when they need perfect edges.
Shear Cutting – Cons
Shear cutting needs the blades lined up just right. It takes skill and time to set up, especially for wrap shear systems. You have to take care of the knives and sharpen them often. This means more downtime and more work. Operators need training, which can cost more money.
Conseil: Pick the cutting method that fits your material and job. Think about what is good and bad about each way.
Selection Guidelines
Adéquation des matériaux
Engineers should match the cutting way to the material. Crush cutting is best for soft, tough, or bendy things like rubber, abrasive papers, and adhesive tapes. Shear cutting works for more types, like films, foils, paper, and textiles. Crush cutting is good for rough or stretchy materials. Shear cutting is better for thin or delicate things.
Desired Edge Quality
If you want smooth edges, shear cutting is best. The scissor action makes neat, clean cuts with little dust. Crush cutting can leave thicker or rougher edges, especially on stretchy or brittle things. Pick the way that gives the finish you need for your next steps.
Production Speed and Efficiency
Shear cutting is good for fast work and long knife life. This helps with big jobs. Crush cutting is quick to set up and easy to change. This is good if you switch materials a lot or have short runs. Crush cutting is simple, so it saves time and helps many jobs go faster.
Maintenance and Cost Considerations
Crush cutting needs less care and costs less to run. Changing blades is easy and does not need much skill. Shear cutting needs the knives sharpened often and skilled workers. This takes more time and costs more. Shear cutting also has more downtime because it is harder to set up and keep working.
Facteur | Coupe par cisaillement | Découpe par écrasement |
---|---|---|
Mécanisme de coupe | Uses two round knives that cut like scissors. | Uses a round knife pressed on an anvil with force. |
Suitable Materials | Films, paper, laminates, tapes, textiles, foils, and more. | Very tough things like rubber, abrasives, laminates; also tapes, textiles, linoleum, foams, etc. |
Cut Quality | Makes great cuts with less dust. | Can make thicker edges on stretchy things; more dust on brittle things. |
Vitesse de production | Can go fast and knives last long. | Usually slower because of force; blade radius and angle matter. |
Production de poussière | Makes less dust. | Makes more dust, especially with brittle things. |
La vie au couteau | Knives last long because of the scissor action. | Blade life depends on radius and angle; materials and cutting affect wear. |
Besoins d'entretien | Needs knives sharpened and replaced often. | Needs little care; easy to line up blades. |
Temps d'arrêt | More downtime because setup and care are harder. | Less downtime because setup and care are easy. |
Operator Skill | Needs skilled workers for blade setup and care. | Needs less skill; setup is simple. |
Setup Complexity | Hard and takes time, especially for wrap shear. | Simple and not complex. |
Industry Applications | Used in many industries for lots of materials. | Used where only crush cutting works, like sandpaper making. |
Checklist for Engineers and Operators:
- Know the material type and thickness.
- Decide what edge quality you need.
- Think about how much and how fast you need to cut.
- Check what care and skills you have.
- Pick the way that fits your needs best.
If you need special blades for slitting, Nanjing Metal is a trusted maker. They have over 20 years of experience. Nanjing Metal makes Lames Sur Mesure for many uses. Their team helps design and make blades that work well and last long.
Crush Cutter Knives: Blade Geometry
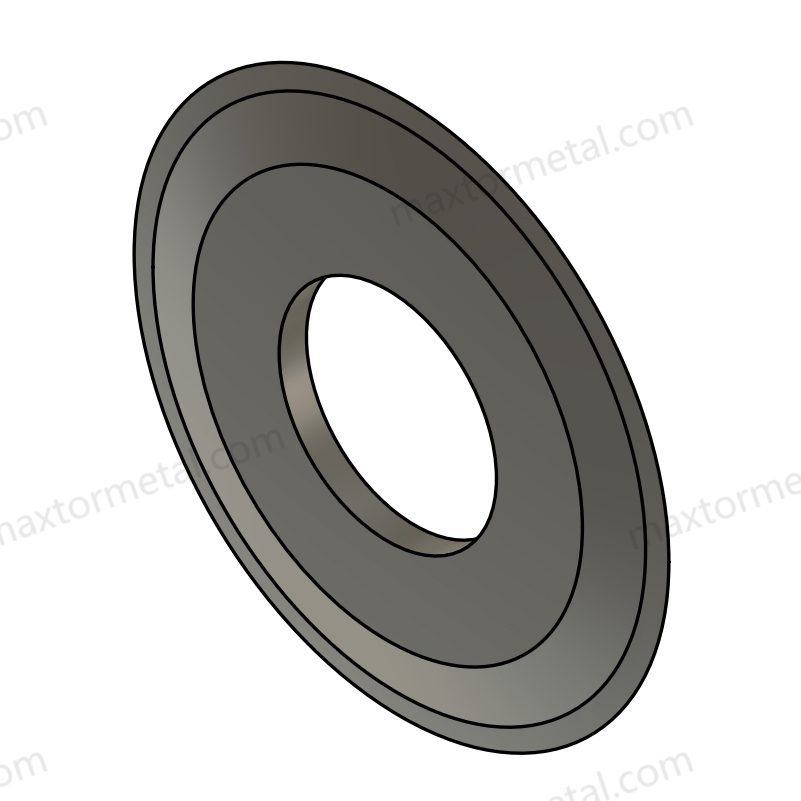
Picking the right shape for crush cutter knives is very important. The radius, angle, and what the blade is made of all matter. These things help the knives work better. Operators can make cuts look nicer and help blades last longer if they know about these parts. This guide gives tips for picking the best blade for adhesive, rubber, and film jobs.
Blade Radius
Blade radius is how round the edge is where it touches the material. A small radius makes a sharper edge. This is good for cutting soft or sticky things. For adhesive tape, a radius from 0.2 to 0.5 mm helps make clean cuts and stops sticky drag. Rubber needs a medium radius, about 0.5 to 1.0 mm. This keeps the edge strong and the blade working longer. Rubber is rough, so a bigger radius stops chips and helps the blade last. Film cutting works best with a bigger radius, like 1.0 to 1.5 mm. This stops tearing and makes smooth edges.
Choosing the best radius is key for good cuts and long blade life. The crush cutting blades angle and radius guide says to change the radius for different thickness and roughness. A bigger radius makes the blade last longer but may not cut as sharp. Operators should pick the radius that fits each job.
Conseil: For rough things like rubber, use a bigger blade radius. This helps the edge last longer.
Angle de la lame
Blade angle changes how sharp, strong, and long-lasting the blade is. A small angle, like 20° to 25°, makes the edge sharper. This helps the blade cut thin films and soft adhesives with less force. The cuts are cleaner. But, sharper angles can break or wear out faster, especially with tough or rough materials.
A middle angle, about 25° to 30°, is a good mix of sharpness and strength. This works well for most rubber jobs. It cuts well and keeps the edge strong. For thick or hard things, a bigger angle, like 30° to 35°, makes the blade stronger and last longer. These angles need more force but stop chipping and rolling.
Here is a table that shows the best radius and angle for common materials:
Type de matériau | Recommended Blade Radius | Recommended Blade Angle |
---|---|---|
Adhesive Tape | 0.2 – 0.5 mm | 20° – 25° |
Industrie du Caoutchouc | 0.5 – 1.0 mm | 25° – 30° |
Film | 1.0 – 1.5 mm | 20° – 25° |
UN small blade angle puts more force in one spot. This makes the blade sharper and helps it cut better. But, this edge can break more easily. Bigger angles make the blade last longer but need more force and may not cut as well. Operators should change the blade angle for each material, as the crush cutting blades angle and radius guide says.
Note: Always try to balance sharpness and strength when picking blade angles for crush knife jobs.
Material and Coating
What the blade is made of and its coating are very important for how well it works. Tungsten carbide blades are very tough and great for cutting rough things like rubber. They are hard and last a long time, even in hard jobs. High-speed steel (HSS) blades are good for softer things and jobs that are not rough.
Coatings make blades work even better. Titanium Nitride (TiN) coatings can help blades last up to 40% longer by lowering friction and wear. Diamond-Like Carbon (DLC) coatings make blades harder and lower friction, so they last longer in hot jobs. Nano-coatings protect blades from heat damage in fast or hot work.
- Tungsten carbide blades are best for rough cutting jobs.
- HSS blades are good for soft or easy-to-cut things.
- TiN and DLC coatings help blades last longer and stop sticky stuff from building up.
- Cleaning and oiling blades helps them last longer.
Picking the right blade material and coating is key for good cuts and saving time. The right blade means fewer changes and steady results.
Application Recommendations
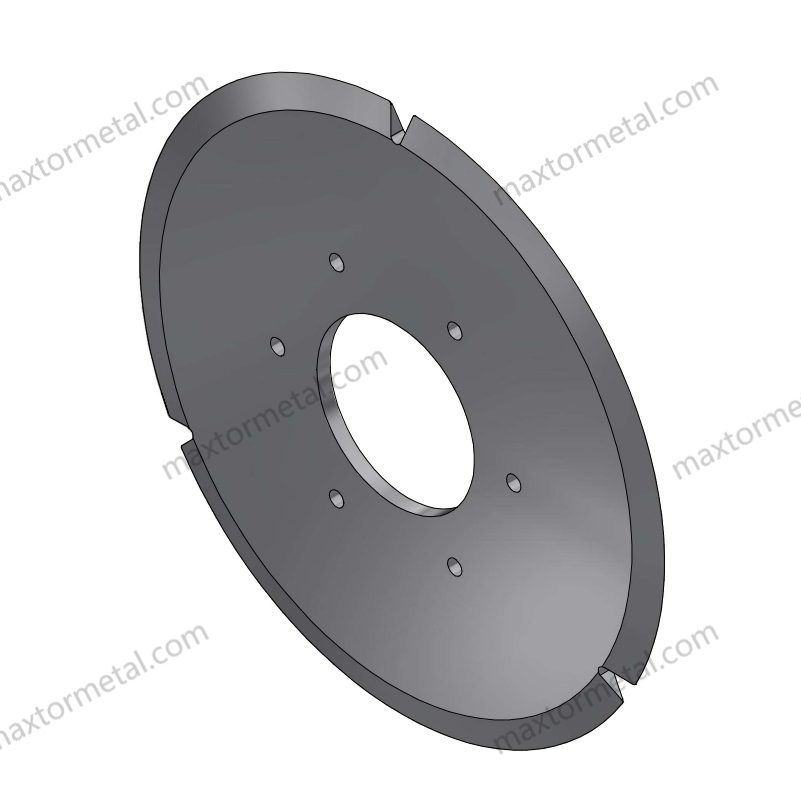
Adhesive Slitting
Picking the right knives for adhesive slitting helps things run well and gives good results. Adhesive materials can be hard to cut because they drag, stick, and sometimes have bad edges. Operators can follow these tips to get the best cuts:
- Use thin-profile knives (≤0.5 mm thick) with a small tip radius. This gives cleaner cuts and less drag from the adhesive.
- Pick double bevel knives with bevels between 20° and 25°. These cut well and make the job easier.
- Put low-friction coatings like Titanium Nitride (TiN) or Teflon on the knives. This stops glue from sticking to the blade.
- Choose blade materials like D2, M2, or carbide. These are tough and last longer, especially for sticky adhesives.
- Keep knives sharp and clean. Clean them often with blade-safe degreasers and lint-free cloths.
- Make sure blades are lined up right. If not, friction goes up and you get bad edges.
- Check both the knives and the anvil often. This stops damage that can make adhesive drag worse and cuts look bad.
- Utiliser just enough blade pressure for a clean cut. Too much pressure wears out the blade. Too little leaves frayed edges.
Conseil: Always check knives for chips, dents, or glue buildup. Clean or change them when needed to keep slitting quality high.
Rubber Slitting
Rubber slitting needs knives that are strong and cut well. Rubber is rough and can wear out normal blades fast, so picking the right knife is important. The table below shows what works best:
Matériau de la lame | Dureté (HRC) | Edge Radius (µm) | Application | Avantages |
---|---|---|---|---|
Carbure de tungstène | 85–90 | 20–50 | Thick rubber, abrasive materials | Lasts longer, less chipping |
Other tips for rubber slitting:
- Use knives with a medium to large edge radius (20–30 µm). This stops sticking and lowers friction.
- Pick knives with a slightly rounded edge. This spreads out the cutting force and helps the knife last longer.
- Add coatings like Titanium Nitride (TiN) to make the knife harder and last longer.
- Make sure the knife holder is stable and tension is right. This helps the knife work better.
- Change the cutting angle and pressure to fit the rubber’s thickness and how hard it is.
Operators should always check that knives are lined up and machine settings are right before starting. This stops uneven wear and keeps cuts even.
Film Slitting
Film slitting needs knives that make clean, exact cuts without tearing or making dust. Thin films are easy to damage if the pressure or blade shape is wrong. Operators can get the best cuts by following these steps:
- Use thin, sharp knives with a low bevel angle (10°–20°) for soft or thin films. This keeps the knife sharp and strong.
- Pick flat straight-edge knives with ground bevels for the best cutting.
- Use low-friction coatings like TiN or Teflon to stop sticking and lower drag.
- Choose stainless steel or carbide knives. These last longer and do not wear out fast.
- Use the right knife pressure. Too much can hurt the film. Too little can leave the cut unfinished.
- Keep the film steady while cutting. This stops it from moving and keeps cuts straight.
- Check and clean knives often. This stops material from building up and keeps cuts sharp.
Note: For laminated films, thin-profile knives help stop too much squeezing and keep the edge nice.
Maintenance and Setup
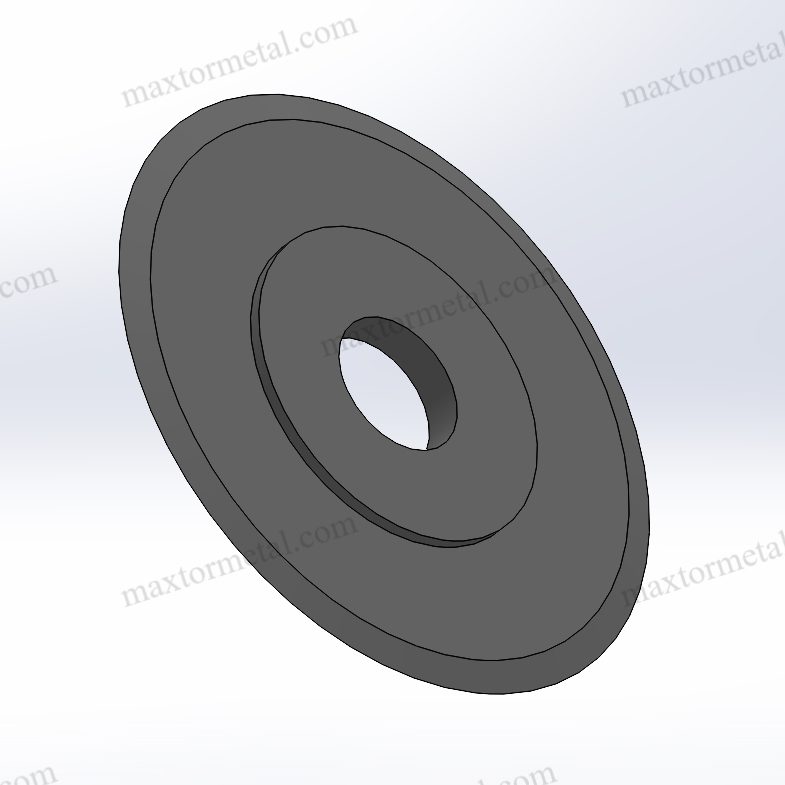
Pressure and Holder Selection
Setting the right pressure and picking the right holder are very important for crush cutting knives. Operators need to use enough pressure to make clean cuts and help knives last longer. If there is too much pressure, the knife can chip or wear out fast. If there is not enough pressure, the material might not cut all the way through. Most composite materials need a nip force between 50,000 and 150,000 psi. Laminated materials sometimes need up to 200,000 psi. Operators should always check the manufacturer’s advice for each job.
Knife holders must keep the knives steady and lined up during cutting. A strong holder stops shaking and keeps cuts even. When putting in new knives, operators should start slow before going full speed. This helps the edge get used to cutting and lowers the chance of damage. The tension and angle must also be set right. If knives are not put in correctly, the edge can chip or the anvil roll can get grooves.
Problems like chipping or rough edges often happen when setup is wrong. Using the wrong blade radius or too much pressure can cause these problems. Operators should listen for strange sounds or look for deep grooves on the anvil roll. If the groove is deeper than 0.05 mm, the anvil needs to be replaced or fixed. Checking and changing pressure settings often helps keep cuts good every time.
Conseil: Always make sure the knife and anvil roll have the right hardness. The anvil should be a little harder than the knife. This helps the knife last longer.
Cleaning and Blade Care
Cleaning and taking care of knives helps them work better and last longer. Cleaning every day gets rid of plastic and sticky stuff that can make the knife dull. Operators should use safe cleaners and soft cloths for this job. Lubricating the knives every week makes cutting smoother and stops wear.
Checking knives often helps find cracks or chips early. Operators should look at knives every week or two, depending on how much they cut. Cleaning and checking every 2–4 weeks keeps knives in good shape. Adding oil during these times also helps the edge stay sharp.
Blades can fail if they are not cared for, not fitted right, or are low quality. Operators can stop these problems by buying good knives from trusted makers. Getting blades reground by pros also helps them last longer. If cutting gets worse, sharpening the blade quickly brings back the edge and saves time.
Operators should not use cheap, basic blades. Good, OEM-equivalent knives last longer and cut better. Fitting and tightening knives the right way stops chipping and uneven wear. Running new knives slowly at first helps the edge settle and keeps them from breaking early.
- Best Practices for Knife Care:
- Clean knives every day to stop buildup.
- Oil knives every week to lower friction and wear.
- Check knives every 1–2 weeks for cracks or dull spots.
- Do maintenance every 2–4 weeks.
- Use only good knives from trusted brands.
- Sharpen blades quickly if they stop cutting well.
- Watch for strange sounds or deep grooves on the anvil roll.
🛠️ Doing regular care and setting up knives the right way helps them work better and saves money on slitting.
For expert help or special solutions, readers can contact Nanjing Metal’s sales engineers for advice and support ici.
Myths and Facts
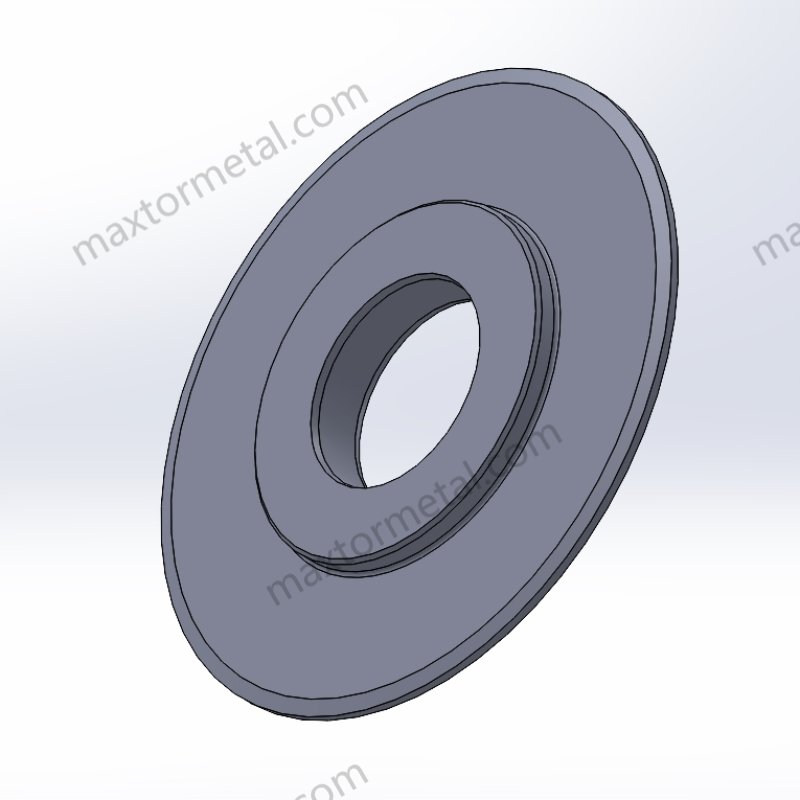
Sharpness vs Bluntness
Some people think a sharper rotary knife always works better for slitting. This makes many workers pick very sharp blades for every job. But new studies and real-life work show that too much sharpness can make blades wear out faster, especially when cutting rough things like rubber. Sharp blades can chip easily and need to be replaced more often. The CATRA method is used to test how sharp a blade is and how long it stays sharp. It shows that blade shape, like the angle and tip width, is very important for how long a blade lasts and how well it cuts.
Workers should pick blade sharpness based on what they are cutting. For soft adhesives and thin films, a sharper edge gives a clean cut. For tough or rough materials, a less sharp edge helps the blade last longer and stops chipping. On one line cutting rubber, using a less sharp blade made blade changes happen 30% less often, and the work stayed good. Some people think the grain in steel or needing grinders matters, but new facts show this is not true. Files are still a good way to fix blades, and heat treatment takes away most problems from forging.
Conseil: Always pick blade sharpness that matches the material and job. This helps blades last longer and work better.
Cut Quality and Dust Control
Another myth says that sharper blades always make cleaner cuts and less dust. But if the blade shape is wrong or too sharp, it can make the edges messy and create more dust, especially with films and adhesives. Blade shape, thickness, and how smooth the edge is all change how much dust is made. Good blades with the right shape make cleaner cuts and less dust between film layers.
Blunt or badly sharpened blades, wrong cutting angles, and blades that move too much make more dust. Special coatings like ceramic can help lower dust and let you cut faster. Keeping the blade steady is very important for less dust. In one film cutting job, changing the blade angle and pressure made 40% less dust and better edges. Taking care of blades and setting the right pressure also helps control dust.
Picking the right blade shape for crush cutting helps you get the best results. You should think about a few important things:
- Make sure the blade radius fits the material’s thickness. This gives you more control and helps the blade last longer.
- Pick the bevel angle by thinking about how sharp you want the blade and how strong the edge should be.
- Choose the tooth type and blade material that match what you need to cut.
- Take care of your blades often. This makes them last longer and work better.
Matériau de la lame | Efficacité de coupe | Résistance à l'usure | Meilleur cas d'utilisation |
---|---|---|---|
Acier inoxydable | Haut | Haut | Humid or wet environments |
Carbure de tungstène | Très élevé | Très élevé | Abrasive, high-volume cutting |
FAQ
What is the ideal blade radius for slitting adhesive tape?
A small edge radius, usually from 0.2 mm to 0.5 mm, works best for cutting adhesive tape. This size helps make neat cuts and stops the tape from dragging on the blade. Operators should change the radius if the tape is thicker or stickier.
Can crush cutting handle abrasive materials like rubber?
Yes, crush cutting works well for tough materials such as rubber. Using a medium or large edge radius and a strong blade material, like tungsten carbide, helps the blade last longer and keeps the cuts good.
How does blade angle affect knife life in crush cutting?
A sharper angle, like 20° to 25°, makes cleaner cuts but the blade wears out faster. A blunter angle, such as 30° to 35°, makes the blade last longer. Operators should pick the angle based on how tough the material is and how smooth they want the edge.
Where can engineers find custom rotary knives for special slitting needs?
Engineers can get custom rotary knives from Nanjing Metal, a trusted company with 20 years of experience. The company offers Lames Sur Mesure made for cutting adhesive, rubber, and film.
Voir aussi
How To Select The Ideal Pelletizer Knife For Machines
Understanding Perforating Blades And Their Common Applications
Que sont les couteaux à écrasement et comment fonctionnent-ils dans l'industrie ?
Couteaux Circulaires Industriels: Comparaison des Performances et des Matériaux
Comment choisir les lames de refendeuse circulaire adaptées pour des performances durables
Comment choisir les lames circulaires adaptées à votre application : un guide complet
Comment garder la lame de votre couteau circulaire tranchante et durable