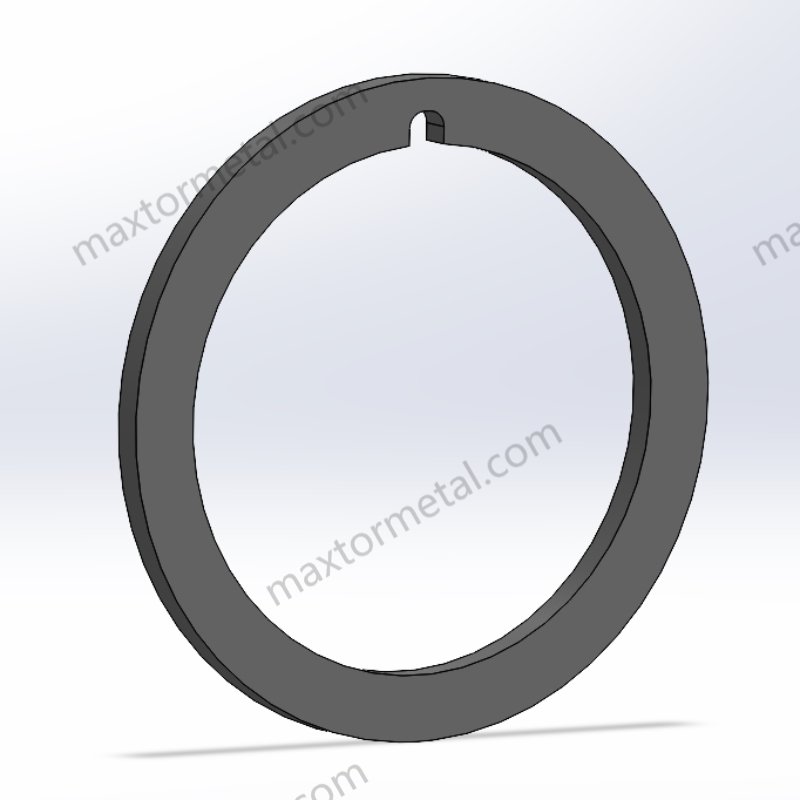
Nanjing Metal, un fabricant professionnel de Lames industrielles Fort de 18 ans d'expérience, nous nous engageons à fournir des lames et des solutions de haute qualité pour répondre aux besoins de découpe industrielle. Les entreprises sont souvent confrontées à des défis tels que des temps d'arrêt accrus dus aux remplacements fréquents de lames, des coûts d'usure élevés et la contrainte financière liée à l'achat de nouvelles lames. Le réaffûtage des lames industrielles offre une solution pratique pour répondre à ces problématiques.
En restaurant les lames usées à leur tranchant et à leur précision d'origine, le réaffûtage réduit non seulement la fréquence de remplacement, mais minimise également les perturbations opérationnelles et les dépenses à long terme.
Dans ce guide, nous explorerons les avantages multiformes de l'affûtage des lames industrielles, les techniques et technologies impliquées, et comment les entreprises peuvent maximiser leur investissement dans les outils de coupe industriels grâce à des stratégies de maintenance intelligentes.
1. Les avantages du réaffûtage des lames industrielles
Prolonger la durée de vie des outils grâce à un réaffûtage de précision
L'affûtage des lames industrielles joue un rôle essentiel pour optimiser l'utilité des outils haute performance. Ce processus consiste à remodeler et à affûter le tranchant afin de restaurer les caractéristiques d'origine de la lame. Des rectifieuses à commande numérique par ordinateur (CNC) de pointe garantissent un enlèvement de matière minimal à chaque affûtage, préservant ainsi l'intégrité structurelle de la lame et permettant plusieurs cycles d'affûtage.
Par exemple, les lames en carbure de haute qualité peuvent souvent subir jusqu'à 5 à 8 cycles de réaffûtage, doublant voire triplant leur durée de vie par rapport aux lames à usage unique. Une étude menée par l'International Tooling Institute (ITI) a révélé que le réaffûtage peut prolonger la durée de vie des outils jusqu'à 200% pour les couteaux industriels courants.
Détails techniques du réaffûtage :
- Angles de meulage:La restauration des angles de biseau optimaux garantit des performances de coupe précises.
- Raffinement des bords:Des techniques avancées comme le micro-polissage améliorent la douceur des bords, réduisant ainsi la friction de coupe et l'usure.
- Traitements de surface: Des revêtements tels que TiN (nitrure de titane) ou DLC (carbone de type diamant) peut être réappliqué lors du réaffûtage pour améliorer la durabilité.
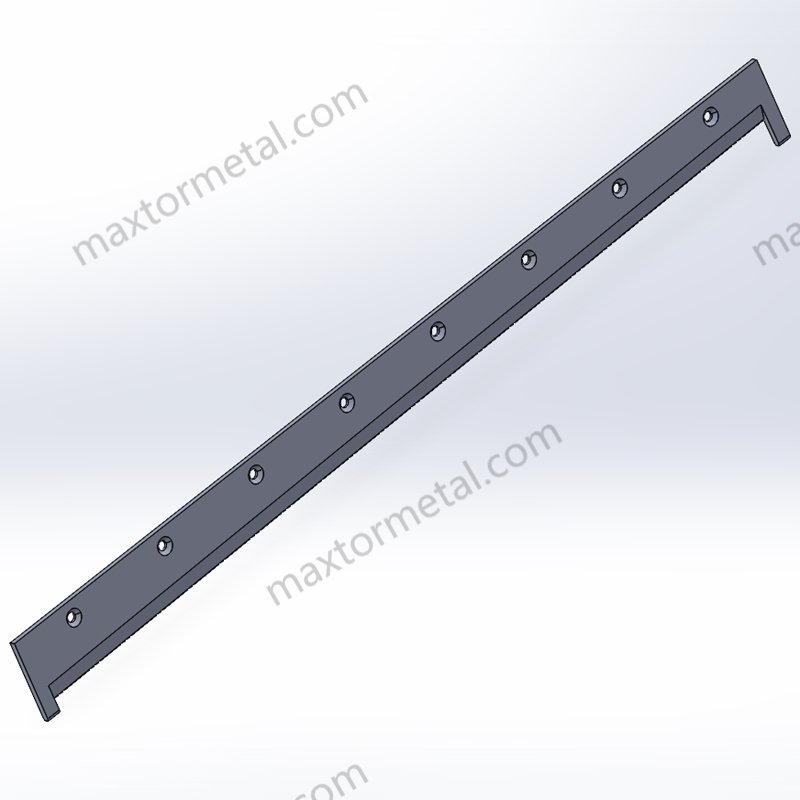
Réduction des coûts : une perspective axée sur les données
Les avantages économiques du réaffûtage figurent parmi ses principaux atouts. Le coût du réaffûtage est généralement inférieur de 50 à 70 TP4T à celui d'une lame neuve, mais les économies réalisées vont au-delà des dépenses immédiates. La réduction des temps d'arrêt, la diminution des déchets de matériaux et l'allongement des intervalles entre les achats contribuent à d'importantes économies de coûts d'exploitation.
Étude de cas : industrie de transformation des aliments
Une usine agroalimentaire de taille moyenne utilisant 300 lames de trancheuse en acier inoxydable dépense environ 150 000 TPT par an en nouvelles lames (à raison de 150 000 TPT par lame). En adoptant une stratégie de réaffûtage :
- Coûts annuels de réaffûtage : $36 000 ($120 par lame).
- Économies par an : $54 000 (60% de réduction des dépenses en lames).
Type de lame | Coût de la nouvelle lame | Coût de réaffûtage | Économies annuelles |
Lame de trancheuse circulaire | $300 | $120 | $54,000 |
Sur une période de 5 ans, cette facilité pourrait permettre d’économiser $270 000, une somme qui peut être réinvestie dans d’autres domaines critiques de l’entreprise.
Améliorer la précision de coupe grâce à des techniques avancées
Maintenir la précision de coupe est essentiel dans les secteurs où les performances des lames ont un impact direct sur la qualité des produits. Par exemple :
- Dans production de papier, des lames émoussées peuvent provoquer des coupes inégales, entraînant un gaspillage de matériau et une augmentation des coûts de traitement.
- Dans fabrication métallique, le manque de précision peut entraîner des bords irréguliers et des composants de mauvaise qualité.
L'affûtage restaure le tranchant tout en améliorant l'uniformité du tranchant. Les méthodes d'affûtage CNC modernes permettent des tolérances aussi serrées que ± 0,01 mm, garantissant ainsi des lames offrant des performances de qualité usine, voire supérieures.
Données justificatives :
Selon un rapport de l'Industrial Blade Association, l'affûtage de précision a permis d'améliorer le rendement des matériaux de 15 à 201 TP4T lors des opérations de découpe dans les industries du plastique et du papier. Cela met en évidence non seulement des avantages en termes de coûts, mais aussi des gains d'efficacité opérationnelle.
2. Avantages et inconvénients du réaffûtage des lames
Avantages
- Rapport coût-efficacité:
- Le réaffûtage réduit le besoin d’achats fréquents de nouvelles lames.
- Les entreprises qui utilisent beaucoup de lames, comme les usines d'emballage, peuvent économiser jusqu'à 60% par an.
- Avantages environnementaux:
- Réduction des déchets : une seule installation réaffûtant 500 lames par an peut économiser plus d’une tonne de déchets d’acier.
- Le rebroyage soutient l’économie circulaire, minimisant l’extraction des ressources et l’impact environnemental.
- Personnalisation:
- Lors du réaffûtage, les lames peuvent être modifiées pour s'adapter à de nouvelles applications ou améliorer leur compatibilité avec différents matériaux. Par exemple, les angles de biseau peuvent être ajustés pour les tâches de coupe plus difficiles.
Désavantages
- Limites d'utilisation:
- Le nombre de réaffûtages dépend du matériau et de l'épaisseur de la lame. Les lames en acier à haute teneur en carbone peuvent supporter 3 à 5 cycles, tandis que les lames en carbure premium peuvent en supporter 5 à 8.
- Variations de qualité:
- Un affûtage irrégulier peut entraîner des bords irréguliers ou un traitement thermique compromis, réduisant ainsi la durée de vie de la lame.
- Solution : Partenariat avec des services de rectification certifiés équipés de machines CNC de pointe.
- Délai de mise en œuvre:
- Le réaffûtage peut prendre de 3 à 7 jours, selon le volume et les spécifications de la lame.
- Atténuation : L’établissement de stratégies de gestion des stocks garantit un temps d’arrêt minimal pendant les cycles de réaffûtage.
Perspectives du monde réel
Une étude réalisée par Machinery Insights Quarterly a révélé que 751 fabricants utilisant des services de réaffûtage ont réalisé des économies annuelles moyennes de 50 000 à 150 000 $, selon l'ampleur de leurs activités. De plus, plus de 901 fabricants ont constaté une amélioration de la précision de coupe et une réduction des déchets de matériaux.
En investissant dans des services de réaffûtage de haute qualité et en alignant les calendriers de maintenance sur les exigences de production, les entreprises peuvent obtenir un avantage concurrentiel en termes de contrôle des coûts et de qualité des produits.
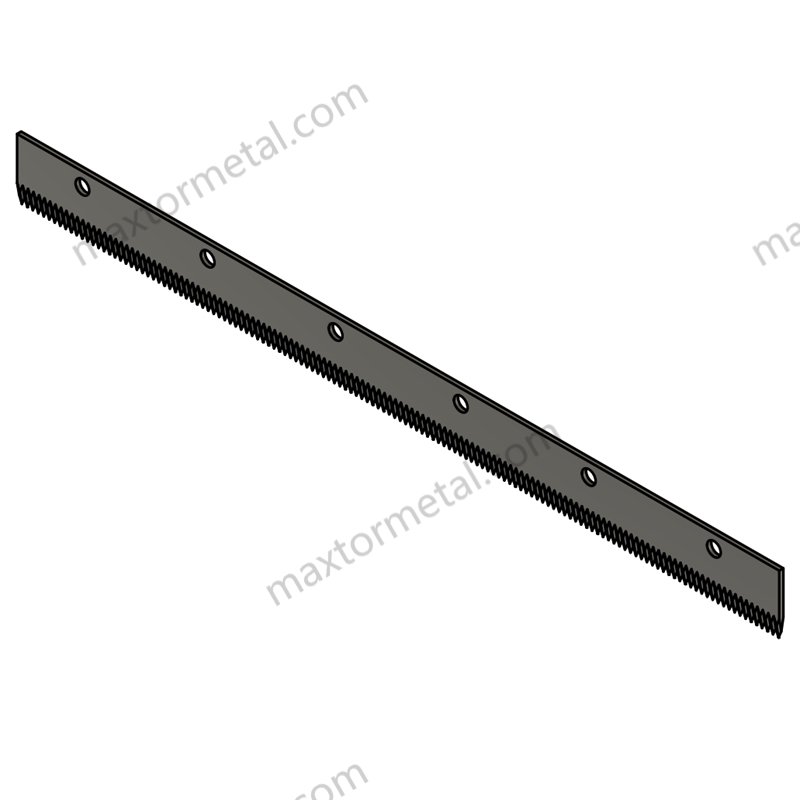
3. Comment déterminer si les lames peuvent être affûtées
Pour déterminer si une lame peut être réaffûtée, il faut évaluer soigneusement son état, la composition de ses matériaux et son historique d'utilisation. Vous trouverez ci-dessous un guide détaillé pour aider les entreprises à prendre des décisions éclairées :
Usure des lames : identifier les dommages et la détérioration
- Inspection visuelle:
- Recherchez les entailles, les éclats et les fissures le long du tranchant. Une usure mineure peut souvent être corrigée par un réaffûtage, mais des dommages importants peuvent compromettre l'intégrité de la lame.
- Mesurer l'épaisseur de la lame : si la lame est amincie au-delà des niveaux recommandés, le réaffûtage peut ne pas être sûr.
- Indicateurs de performance:
- Évaluez les résultats de coupe récents. Des problèmes tels que des coupes irrégulières, une perte de matière accrue ou un frottement excessif pendant le fonctionnement peuvent indiquer un émoussement qui peut être corrigé par un réaffûtage.
- Forme de la lame:
- Une déformation de la lame, comme un gauchissement, indique qu'un simple affûtage ne suffit pas à restaurer sa fonctionnalité. Dans ce cas, un remplacement peut s'avérer nécessaire.
Matériau et structure : aptitude au réaffûtage
- Matériau de la lame:
- Lames en acier à haute teneur en carbone et en carbure sont des candidats idéaux pour le réaffûtage en raison de leur durabilité et de leur capacité à conserver des bords tranchants pendant plusieurs cycles.
- Les lames fabriquées à partir de matériaux cassants comme les alliages de qualité inférieure peuvent ne pas résister au processus.
- Conception de la lame:
- Les lames fines ou très complexes nécessitent un équipement et une expertise spécialisés pour éviter tout dommage lors du réaffûtage.
- Les lames avec des revêtements comme le nitrure de titane (TiN) peuvent être réaffûtées, mais une réapplication du revêtement peut être nécessaire pour restaurer les propriétés d'origine.
Historique d'utilisation : suivi de l'usure et de l'entretien
- Fréquence de réaffûtage:
- Les lames ayant fait l'objet d'un réaffûtage régulier doivent être évaluées afin de déterminer s'il reste du matériau utilisable. Un amincissement excessif peut réduire la durée de vie des lames.
- Conditions opérationnelles:
- Tenez compte des types de matériaux que la lame a coupés. Les matériaux abrasifs provoquent une usure plus importante et peuvent réduire le nombre de cycles de réaffûtage possibles.
Liste de contrôle d'adéquation des lames :
Critères | Question d'évaluation | Action |
Usure de la lame | Y a-t-il des fissures visibles ou des déformations importantes ? | Remplacer si grave ; rectifier si mineur. |
Composition du matériau | La lame est-elle en acier à haute teneur en carbone ou en carbure ? | Procéder au réaffûtage. |
Historique d'utilisation | La lame a-t-elle déjà été affûtée plusieurs fois ? | Évaluer la durée de vie restante. |
Précision de coupe | La lame coupe-t-elle toujours proprement avec un minimum d’effort ? | Affûter pour restaurer la netteté. |
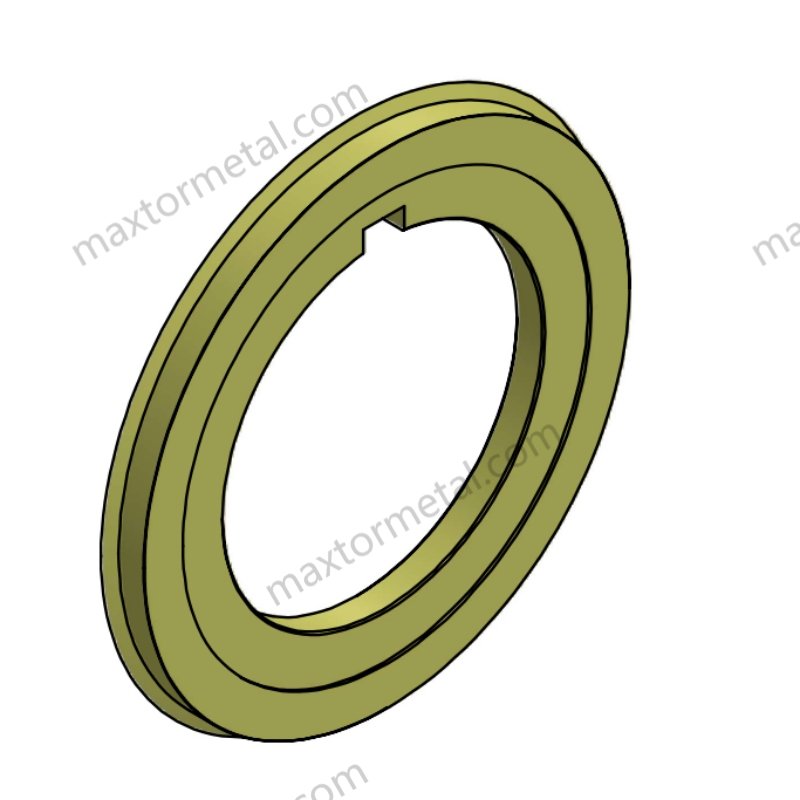
4. Prévenir la baisse des performances après le réaffûtage
Pour maximiser les avantages du réaffûtage, les entreprises doivent mettre en œuvre les meilleures pratiques pour maintenir la qualité et la performance des lames. Voici des stratégies détaillées :
Choisir des services de réaffûtage réputés
- Évaluer l'expertise:
- Vérifiez que le prestataire de services utilise des matériaux cassants pour plus de précision et de cohérence.
- Recherchez des certifications telles que ISO 9001 pour garantir le respect des normes de qualité.
- Capacités techniques:
- Assurez-vous que le fournisseur possède de l’expérience avec les matériaux et les conceptions de lames spécifiques utilisés dans vos opérations.
- Confirmez qu'ils peuvent gérer les traitements post-broyage comme le revêtement, si nécessaire.
- Avis des clients:
- Recherchez des témoignages ou des études de cas soulignant la fiabilité et le succès du fournisseur dans la restauration des performances des lames.
Mise en œuvre d'une maintenance régulière
- Protocoles de nettoyage:
- Éliminez les résidus et les débris après chaque utilisation. Par exemple, les lames utilisées dans la transformation des aliments doivent être nettoyées avec des détergents non corrosifs pour éviter l'oxydation.
- Évitez d’utiliser des outils de nettoyage abrasifs qui peuvent endommager le tranchant.
- Solutions de stockage:
- Stockez les lames dans un environnement sec et à température contrôlée pour éviter la rouille et la déformation.
- Utilisez des manchons ou des couvercles de protection pour les lames afin de réduire les dommages accidentels lors de la manipulation.
Savoir quand remplacer les lames
- Suivi des performances:
- Tenez un journal des mesures de performance de la lame, y compris l'efficacité de coupe et la qualité du produit, pour identifier quand le réaffûtage n'est plus efficace.
- Seuil matériel:
- Remplacez les lames lorsque leur matériau s'est aminci en dessous mminimums recommandés par le fabricant pour éviter les bris ou les accidents.
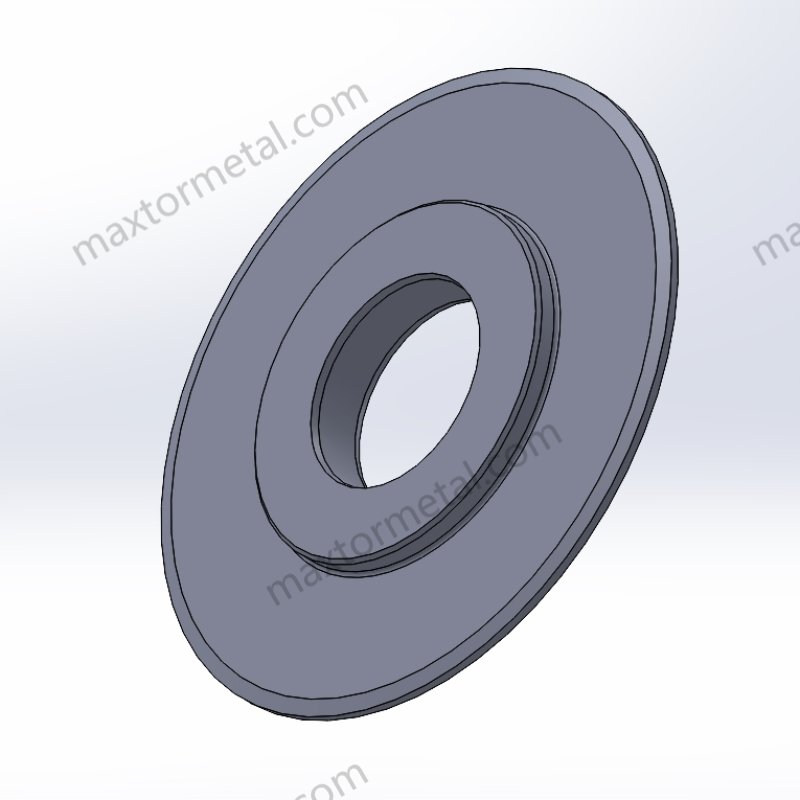
5. Meilleures pratiques d'utilisation et d'entretien des lames
L'entretien des lames industrielles réduit non seulement le besoin de réaffûtage fréquent, mais prolonge également leur durée de vie. Voici quelques bonnes pratiques :
Utilisation appropriée de la lame
- Suivre les directives opérationnelles:
- Utilisez la lame adaptée au matériau à couper. Par exemple, les lames en acier à haute teneur en carbone sont plus adaptées aux matériaux plus durs, tandis que les lames en acier inoxydable sont idéales pour les applications alimentaires.
- Évitez la surcharge:
- Ne dépassez pas la vitesse ou la force de coupe recommandées par le fabricant. Une surcharge peut entraîner une usure prématurée et des dommages.
- Surveiller la production de chaleur:
- Une chaleur excessive pendant le fonctionnement peut affaiblir la trempe de la lame et accélérer son usure. Utilisez des systèmes de refroidissement adaptés pour la coupe de matériaux à forte friction.
Conseils d'entretien
- Inspections de routine:
- Effectuez des contrôles hebdomadaires pour vérifier le tranchant, l'alignement des lames et l'usure. Résoudre les petits problèmes dès le début peut éviter des baisses de performances importantes.
- Applications de revêtement:
- Appliquez des revêtements protecteurs, tels que des sprays anticorrosion ou des traitements résistants à la chaleur, pour améliorer la durabilité.
- Équilibrage périodique:
- Recalibrez les lames pour garantir une usure uniforme et des performances constantes.
Optimisation de la fréquence de maintenance
- Industries à forte consommation (par exemple, emballage, papier) : Inspectez les lames quotidiennement et planifiez un réaffûtage toutes les 2 à 4 semaines.
- Industries à usage modéré (par exemple, transformation des aliments) : inspecter chaque semaine, avec un nouveau broyage toutes les 6 à 8 semaines.
Liste de contrôle de maintenance :
Tâche | Fréquence | But |
Nettoyage des lames | Après chaque utilisation | Empêche l’accumulation de débris et la corrosion. |
Inspection visuelle | Hebdomadaire | Identifie les premiers signes d’usure ou de dommage. |
Revêtement protecteur | Mensuel | Améliore la durée de vie et les performances de la lame. |
Évaluation du réaffûtage | Basé sur les journaux d'utilisation | Détermine quand un réaffûtage est nécessaire. |
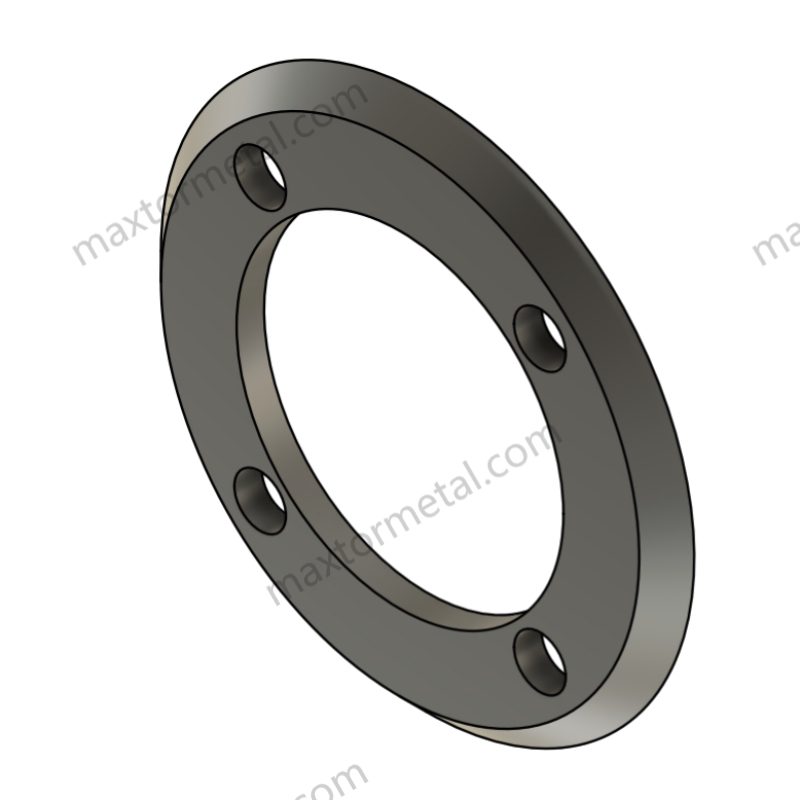
6. Technologies émergentes dans le réaffûtage des lames industrielles
Progrès révolutionnaires dans la technologie de rectification CNC
L'introduction de Rectifieuses à commande numérique par ordinateur (CNC) a transformé le processus de réaffûtage des lames, établissant de nouvelles normes de précision, d'efficacité et de régularité. Contrairement aux méthodes de réaffûtage traditionnelles, la technologie CNC s'appuie sur l'automatisation et les commandes logicielles pour produire des résultats non seulement plus précis, mais aussi hautement reproductibles. Voici un aperçu de la manière dont la technologie de réaffûtage CNC redéfinit le réaffûtage des lames :
Principales caractéristiques des rectifieuses CNC avancées
- Précision au micron près
- Contrôle multi-axes automatisé
- Technologie de meulage adaptative
- Systèmes de refroidissement intégrés
- Améliorations du polissage des bords
Technologies émergentes complétant la rectification CNC
- Surveillance activée par l'IoT
- Profilage assisté par laser
- Rectification assistée par ultrasons (UAG)
Impact des données sur la CNC et les technologies connexes
- Gains d'efficacité matérielle
- Améliorations de la productivité
- Coûts de maintenance réduits
Tendances de l'industrie et développements futurs
- L'IA et l'apprentissage automatique dans le broyage
- Initiatives de développement durable Initiatives de développement durable
- Systèmes CNC modulaires
Avantages concrets pour les industries
Les technologies de réaffûtage avancées, en particulier celles basées sur des systèmes CNC, offrent des avantages quantifiables dans tous les secteurs :
Industrie | Défi | Solution par Advanced CNC Grinding | Impact |
Transformation des aliments | Lames émoussées provoquant des tranches inégales | Rectification CNC de précision avec bords polis | Réduction du gaspillage alimentaire, amélioration de l’efficacité. |
Fabrication Metal | Déchets de matériaux dus à des bords de lame de mauvaise qualité | Rectification adaptative pour matériaux durs | 20% rendement supérieur dans les matériaux transformés. |
Recyclage du plastique | Usure élevée due aux matériaux abrasifs | Broyage assisté par ultrasons | Durée de vie de la lame plus longue, coûts de maintenance réduits. |
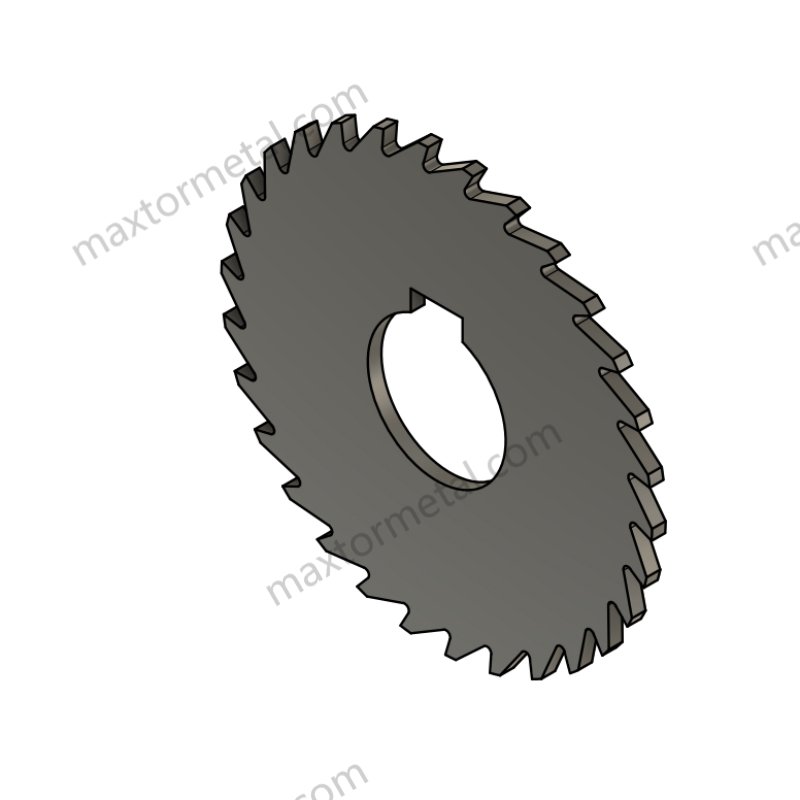
7. Questions fréquemment posées (FAQ)
Q1 : À quelle fréquence les lames doivent-elles être affûtées ?
A1 : La fréquence de réaffûtage dépend de l'application, du matériau à couper et de l'environnement d'utilisation. Pour la plupart des lames, un réaffûtage est recommandé après 50 à 100 heures d'utilisation active. Cependant, les industries manipulant des matériaux abrasifs, comme le recyclage du plastique ou la découpe du métal, peuvent nécessiter un réaffûtage plus fréquent pour maintenir des performances optimales. Des inspections régulières des lames peuvent vous aider à identifier rapidement les bords émoussés ou les baisses de performance, garantissant ainsi un réaffûtage rapide.
Q2 : Tous les matériaux peuvent-ils être broyés ?
A2: La plupart des matériaux de lames industrielles, tels que l'acier à haute teneur en carbone, l'acier à outils et le carbure de tungstène, se prêtent bien au réaffûtage en raison de leur durabilité et de leur résistance à l'usure. Cependant, les matériaux extrêmement fragiles, comme les alliages de faible qualité, peuvent se fissurer ou s'écailler pendant le processus, ce qui les rend moins adaptés au réaffûtage. De plus, les lames revêtues, comme celles avec nitrure de titane (TiN), peut être rebroyé, mais le revêtement peut devoir être réappliqué pour conserver ses avantages.
Q3 : Le réaffûtage réduira-t-il les performances de la lame ?
A3: Réalisé par des professionnels utilisant un équipement de pointe, le réaffûtage restaure la lame à ses performances d'origine, voire à un niveau supérieur. Des angles d'affûtage, un polissage et un affinage du tranchant appropriés garantissent le maintien de la précision de coupe. De fait, certaines techniques de réaffûtage avancées, comme l'affûtage CNC, peuvent améliorer la régularité du tranchant et prolonger la durée de vie de la lame.
Q4 : Combien de temps dure le réaffûtage ?
A4: La durée dépend de facteurs tels que la taille de la lame, le matériau et les compétences du prestataire. En moyenne, le processus de réaffûtage prend de 3 à 7 jours ouvrés. Les installations à haut volume ou celles équipées de systèmes de rectification CNC avancés peuvent offrir des délais d'exécution plus courts. Pour les entreprises dont les calendriers de production sont critiques, le maintien d'un stock de lames de secours peut minimiser les perturbations pendant la période de réaffûtage.
Conclusion
L'affûtage des lames industrielles est une pratique essentielle pour toute entreprise souhaitant améliorer son efficacité opérationnelle et réduire ses coûts. En restaurant les lames à leurs performances d'origine, voire en améliorant leur fonctionnalité, l'affûtage minimise les temps d'arrêt, prolonge la durée de vie des outils et favorise des pratiques durables grâce à la réduction des déchets. Associé à des technologies avancées comme l'affûtage CNC et à des stratégies de maintenance régulière, l'affûtage devient un outil puissant pour optimiser les processus de production.
Nanjing Metal est un partenaire de confiance dans l'industrie des lames industrielles, offrant solutions personnalisées Pour répondre à divers besoins de coupe. Que vous recherchiez de nouvelles lames conçues pour la précision et la durabilité ou des conseils d'experts sur l'entretien de vos lames, nous sommes là pour vous aider. Contactez-nous aujourd'hui pour une consultation et un devis gratuits, et découvrez comment nous pouvons contribuer au succès de votre entreprise.
Une réponse