Dalam produksi industri, setiap potongan penting. Baik Anda memotong kertas, makanan, plastik, atau logam, satu faktor memegang peranan penting dalam keberhasilan Anda: Geometri bilah.
Geometri bilah — bentuk, sudut, ketebalan, dan desain tepi pisau atau bilah — memiliki dampak langsung pada efisiensi pemotongan, kualitas produk, dan biaya operasional. Namun, banyak pabrik masih mengabaikannya. Memilih geometri bilah yang tepat dapat meningkatkan kecepatan pemotongan, mengurangi keausan bilah, dan meningkatkan presisi setiap pemotongan.
Dalam artikel ini, kami mengeksplorasi bagaimana berbagai aspek geometri bilah memengaruhi kinerja di berbagai industri dan menawarkan panduan tentang cara memilih atau sesuaikan pisau yang tepat untuk proses Anda.
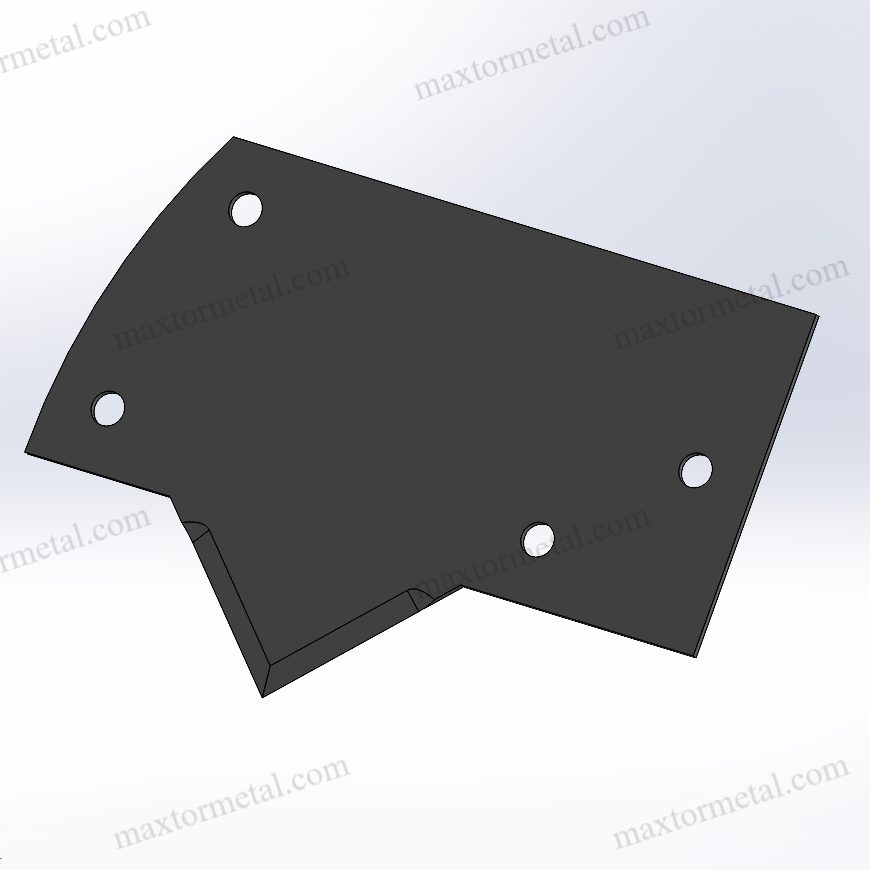
1. Faktor Geometri Bilah Utama yang Mempengaruhi Performa
Dalam pemotongan industri, kinerja bilah sangat bergantung pada kesesuaian geometrinya dengan tuntutan material dan proses. Geometri bilah yang salah dapat menyebabkan sobek, panas berlebih, keausan dini, dan bahkan kerusakan pada mesin. Di bawah ini, kami membahas empat elemen geometri paling penting dan bagaimana elemen-elemen tersebut secara langsung memengaruhi kinerja pemotongan, efisiensi biaya, dan kualitas produk.
1.1 Sudut dan Ketajaman Ujung Pemotong
🔍 Ikhtisar Teknis:
Itu sudut ujung tajam (juga disebut sudut miring) menentukan seberapa tajam atau kuatnya bilah pisau. Tingkat ketajamannya diukur dalam derajat — semakin kecil sudutnya, semakin tajam dan rapuh bilahnya; semakin besar sudutnya, semakin kuat dan tahan lama bilahnya.
- Tepi sudut rendah (10°–20°): sangat tajam tapi mudah terkelupas
- Tepi sudut tinggi (25°–40°): tahan lama, dapat menangani material yang lebih keras tetapi membutuhkan lebih banyak tenaga
📊 Perbandingan Kinerja:
Jenis Tepi | Sudut Bevel (°) | Aplikasi | Bahan Pisau | Umur Khas* | **Indeks Kekuatan Pemotongan** |
Sangat tajam | 10–15 | Film, foil, tekstil tipis | Keramik, SS420 | 2–3 hari | Rendah |
Potongan presisi | 16–25 | Kertas, kemasan, makanan lunak | Besi tahan karat | 5–7 hari | Sedang |
Tugas berat | 26–35 | Karet, plastik, lembaran baja | Tungsten karbida | 10–15 hari | Tinggi |
* Berdasarkan operasi industri harian 8 jam
** Indeks relatif: Rendah = kekuatan minimal yang dibutuhkan; Tinggi = kekuatan signifikan yang dibutuhkan
🧪 Wawasan Penelitian:
- Institut Pemotongan Industri (2021) menemukan bahwa mengurangi sudut bevel hanya dengan 5 derajat meningkatkan ketajaman awal dengan 38%, tetapi mengurangi retensi tepi sebesar 45%.
- Dunia Pengemasan (2022) melaporkan suatu Penurunan tingkat scrap 22% pada jalur berkecepatan tinggi setelah beralih ke bilah dengan geometri bevel yang dioptimalkan.
✅ Ringkasan:
Gunakan bilah bersudut rendah untuk pemotongan bersih pada material lunak atau tipis. Untuk material keras atau abrasif, tingkatkan sudut tepi untuk memperpanjang masa pakai bilah dan mengurangi kerusakan.
1.2 Geometri dan Pitch Gigi
Pisau bergerigi mengandalkan desain gigi, jarak (pitch), Dan tinggi untuk mengontrol cara mereka menggunakan material. Geometri memengaruhi kedalaman gigitan, jarak bebas serpihan, getaran, dan pembuangan panas.
📐 Parameter Utama:
- Nada gigi – jarak antar ujung gigi
- Profil gigi – segitiga (umum), berlekuk (makanan), kait (karet), gelombang (tekstil)
- Tenggorokan – lembah di antara gigi; kerongkongan yang lebih besar meningkatkan penghilangan serpihan
Jenis Lapangan | Jarak (mm) | Ideal untuk | Keunggulan Utama |
Bagus | 0,5–1,5 | Roti, busa, film lembut | Robekan minimal |
Sedang | 2–4 | Daging, kertas, papan bergelombang | Kontrol dan kecepatan yang seimbang |
Kasar | 5–8 | Karet, kabel, komposit | Pembuangan panas yang lebih baik |
🔍 Sorotan Data:
- Beralih dari bilah lurus ke bilah bergerigi bergigi halus dalam pemotongan busa mengurangi robekan permukaan dengan 43% (Laporan FoamTech, 2022).
- Di fasilitas daur ulang, pisau kait bergigi kasar memotong strip karet berukuran 10 mm 15% lebih cepat dan bertahan lama 20% lebih panjang.
⚙️ Tips Optimasi:
Sesuaikan pitch dan profil dengan kepadatan material dan putaran per menit mesin. Operasi kecepatan tinggi diuntungkan oleh desain gigi yang halus dan stabil; gigi yang kasar cocok untuk pemotongan beban berat dengan kecepatan rendah.
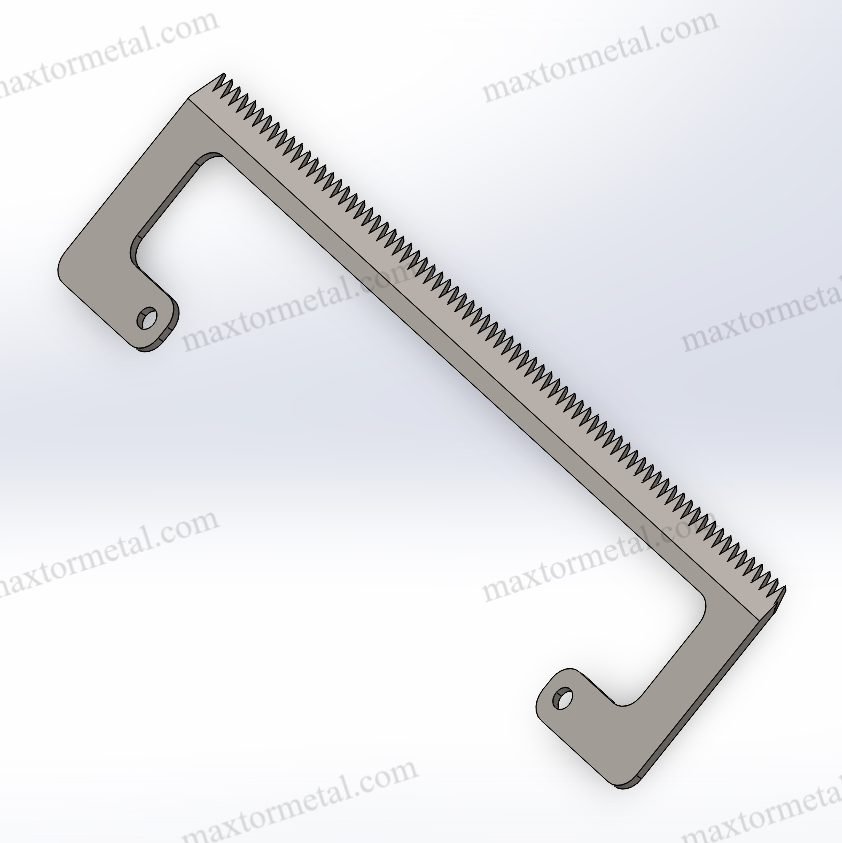
1.3 Ketebalan dan Lebar Bilah
Bilah ketebalan mempengaruhi kekakuan, ketahanan terhadap kelenturan, dan efisiensi energi. Mata pisau yang lebih tipis menghasilkan potongan yang lebih tajam dan bersih, tetapi lebih rentan terhadap defleksi dan deformasi termal.
📊 Data Dunia Nyata:
Ketebalan Bilah | Kecepatan Pemotongan (m/menit) | Waktu henti (per minggu) | Sampah Material (%) |
0,4 mm | 180 | 2 jam | 1.8% |
0,6 mm | 160 | 1,2 jam | 2.5% |
1,0 mm2 | 140 | 0,8 jam | 3.1% |
(Data dari BladeTech Solutions, 2023 – Aplikasi pengemasan)
🧠 Poin-poin Utama:
- Pisau tipis ideal untuk film dan label
- Ketebalan sedang paling cocok untuk kertas dan tekstil
- Pisau tebal cocok untuk daur ulang, plastik, dan karet
1.4 Kompatibilitas Material dan Geometri Blade
Sebuah pisau komposisi bahan menentukan geometri mana yang praktis dan berapa lama bilah akan bekerja secara efektif di bawah tekanan.
🧪 Perbandingan Material:
Bahan Pisau | Kekerasan (HRC) | Kasus Penggunaan Ideal | Pertimbangan Geometris |
Besi tahan karat | 55–60 | Makanan, medis, tugas ringan | Bevel sedang, tahan korosi |
Baja Berkecepatan Tinggi | 60–64 | Kertas, kayu, plastik | Mendukung tepi tipis atau tebal |
Karbida Wolfram | 75–85 | Metal, karet, komposit | Terbaik untuk bagian tepi yang keras dan tebal |
Keramik | 80–90 | Foil, mikrofilm, optik | Tepi sangat tipis, rapuh |
⚠️ Risiko Kesalahan Penyelarasan:
Penggunaan geometri ultra tipis dengan bahan rapuh seperti keramik sering kali menghasilkan ujung patah dalam beberapa ratus potongan. Selalu sesuaikan geometri dengan batas fisik bilah.
2. Geometri Bilah dan Presisi Pemotongan
Presisi pemotongan yang tinggi sangat penting dalam aplikasi seperti perangkat medis, elektronik, dan tekstil. Presisi ini mengurangi limbah, meningkatkan kualitas produk akhir, dan memastikan kepatuhan terhadap keselamatan.
2.1 Konsistensi Geometri = Akurasi Pemotongan
Presisi bergantung pada lebih dari sekadar ketajaman bilah. Presisi memerlukan geometri konsistensi, tahan getaran, Dan kontrol termal.
🌡️ Distorsi Termal:
Penumpukan panas menyebabkan deformasi bilah. Jurnal MetCut (2021) melaporkan bahwa bilah beroperasi di atas 120 derajat celcius menghasilkan deviasi dimensi hingga ±0,3 mm2 saat memotong film polietilena.
⚙️ Gangguan Toleransi:
Masalah Geometri | Masalah yang Dihasilkan |
Sudut bevel tidak rata | Potongan asimetris, gerinda |
Ketebalan tidak konsisten | Pemotongan berlebih/kurang, pengacauan |
Tepi tidak sejajar | Ketidakselarasan, peningkatan skrap |
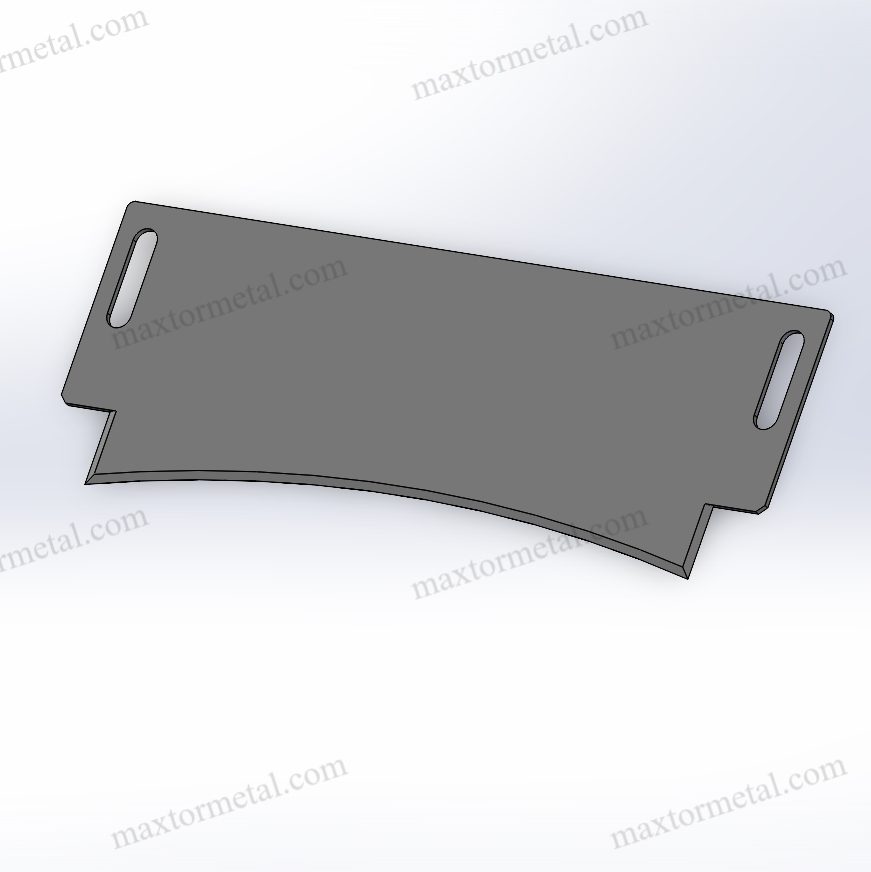
2.2 Kualitas Permukaan dan Tepi
Geometri bilah yang tepat menghasilkan potongan halus dan bebas gerinda, meminimalkan atau menghilangkan kebutuhan untuk pasca-pemrosesan. Geometri yang buruk dapat menyebabkan:
- Tepi film atau label bergerigi
- Permukaan plastik yang terbakar
- Tekstil yang berjumbai atau berbulu
📊 Hasil Aplikasi:
- Jalur pengemasan mengurangi waktu pemolesan pasca pemotongan sebesar 17% setelah mengadopsi bilah baja tahan karat tepi-tanah.
- Pabrik tekstil yang menggunakan bilah poles halus menurunkan kerontokan serat sebesar 29%, meningkatkan kualitas produk dan keseragaman pewarna.
2.3 Tolok Ukur Toleransi Industri
Industri | Toleransi Pemotongan yang Diperlukan | Geometri Bilah yang Direkomendasikan |
Kertas/Label | ± 0,2 mm2 | Tipis, tepi lurus, bevel rendah |
Pemotongan Tekstil | ±0,5 mm2 | Tepi halus, bevel dipoles |
Lembaran Plastik | ±0,3 mm2 | Pisau berlapis, bevel sedang |
Kertas Foil Metal | ± 0,1 mm2 | Kaku, karbida, sudut bevel tinggi |
🧰 Praktik Terbaik:
- Menggunakan Pisau yang digiling CNC untuk memastikan toleransi geometri yang ketat
- Gabungkan geometri bilah yang tepat dengan umpan mesin stabil
- Periksa simetri bilah setiap 8–12 jam dalam garis presisi
3. Aplikasi Geometri Bilah di Dunia Nyata
Industri yang berbeda memiliki tuntutan yang berbeda pada bilah dan pisau. Geometri harus sesuai tidak hanya dengan material, tetapi juga persyaratan penggunaan akhir — termasuk kebersihan, kecepatan, ketepatan, dan daya tahan. Mari kita uraikan bagaimana geometri bilah disesuaikan untuk setiap sektor, didukung oleh data aplikasi nyata dan hasil yang terbukti.
A. Industri Makanan: Kebersihan, Akurasi, dan Hasil
⚙️ Tantangan:
- Mencegah deformasi material (misalnya menghancurkan roti atau daging)
- Mengurangi kontaminasi silang
- Menjaga potongan yang bersih dan rata untuk konsistensi visual dan kemasan
🔧 Rekomendasi Geometri:
- Pisau bergerigi (pitch 2–4 mm) untuk makanan berkerak atau berserat seperti roti atau daging
- Pisau bermata lurus yang dipoles untuk barang lunak seperti sayur dan buah
- Sudut bevel rendah (10–15°) untuk kompresi minimal
📊 Data Industri:
Produk | Geometri Bilah | Manfaat yang Dicapai |
Roti lapis | Bergerigi, pitch 3 mm, SS420 | Sobekan berkurang, irisan seragam 99% |
Dada ayam | Tepi lurus, bevel 12° | Bentuk tetap terjaga, proses lebih cepat |
Selada | Pisau lurus tipis, lapisan DLC | Peningkatan umur simpan sebesar 8–10% |
(Sumber: Jurnal Pengolahan Pangan, 2021)
💡 Wawasan Utama:
Menggunakan baja tahan karat yang aman untuk makanan dengan transisi bevel yang halus membantu menghindari perangkap bakteri dan menjaga potongan tetap bersih. Bahkan ketidaksempurnaan mikro dalam geometri tepi dapat kontaminan pelabuhan dan melanggar standar keselamatan seperti Sistem Informasi Keselamatan dan Kesehatan Kerja (HACCP) dan Peraturan CFR 21 dari FDA.
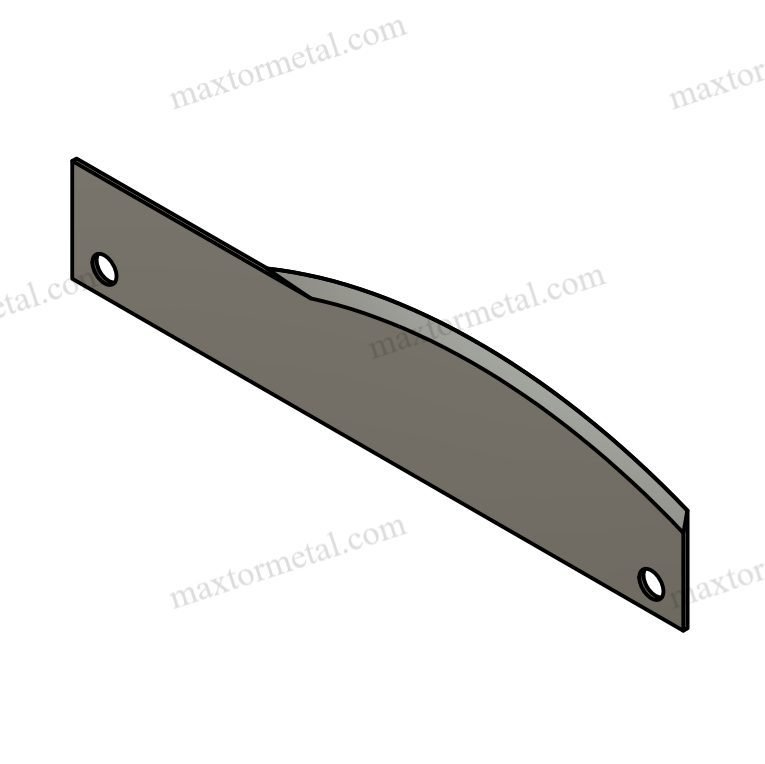
B. Industri Kertas dan Tekstil: Hasil Potongan Rapi Tanpa Rusak
⚙️ Tantangan:
- Menghindari serat tercabut dan tepian yang berjumbai
- Mencapai toleransi dimensi yang ketat
- Mengelola timbulnya debu selama pemotongan berkecepatan tinggi
🔧 Rekomendasi Geometri:
- Pisau bergerigi mikro (0,5–1 mm pitch) untuk kertas dan label berlapis
- Desain tepi gelombang atau bergerigi untuk tekstil tenun
- Bevel dengan ketajaman tinggi (15–20°), lapisan yang sangat halus untuk mengurangi hambatan
📊 Keuntungan Produksi:
Bahan | Tipe Geometri | Hasil Kinerja |
Kertas kerajinan | Pisau bergerigi mikro 0,5 mm | 26% sobekan tepi lebih sedikit, 15% potongan lebih bersih |
Kapas | Bevel dipoles, berlekuk | 18% mengurangi limbah kain |
Label termal | Potongan gelombang tipis, lapisan DLC | 21% waktu aktif mesin lebih tinggi |
(Data dari Survei Tolok Ukur TextileMach 2022)
🧠 Catatan Ahli:
Debu dari pemotongan kertas dapat terkumpul pada sensor dan rol. Penggunaan geometri tepi yang dioptimalkan mengurangi pembentukan partikel pada sumbernya.
C. Daur Ulang dan Pengelolaan Sampah: Kekuatan Berpadu dengan Daya Tahan
⚙️ Tantangan:
- Memotong bahan yang tercampur atau terkontaminasi
- Tahan terhadap benturan berat, bahan abrasif, dan logam tertanam
- Meminimalkan waktu henti dan penggantian bilah
🔧 Rekomendasi Geometri:
- Pisau tebal yang diperkuat dengan Kemiringan 35–40°
- Geometri bergerigi bergigi kait untuk merobek karet dan karpet
- Konstruksi berujung karbida atau bimetal
📊 Dampak Pemeliharaan:
Geometri Bilah | Rata-rata Waktu Aktif Per Set | Pengurangan Pemeliharaan |
Tepi datar standar | 6 jam | – |
Bevel lebar + gigi kait | 10,5 jam | –42% panggilan pemeliharaan |
(Sumber: Tinjauan Peralatan Limbah Global, 2023)
🧠 Wawasan Lapangan:
Saluran pembersihan sendiri dan lembah gigi yang lebih besar dapat mengurangi secara drastis penyumbatan bilah, masalah umum saat memotong bahan lengket seperti ban atau kabel berlapis PVC.
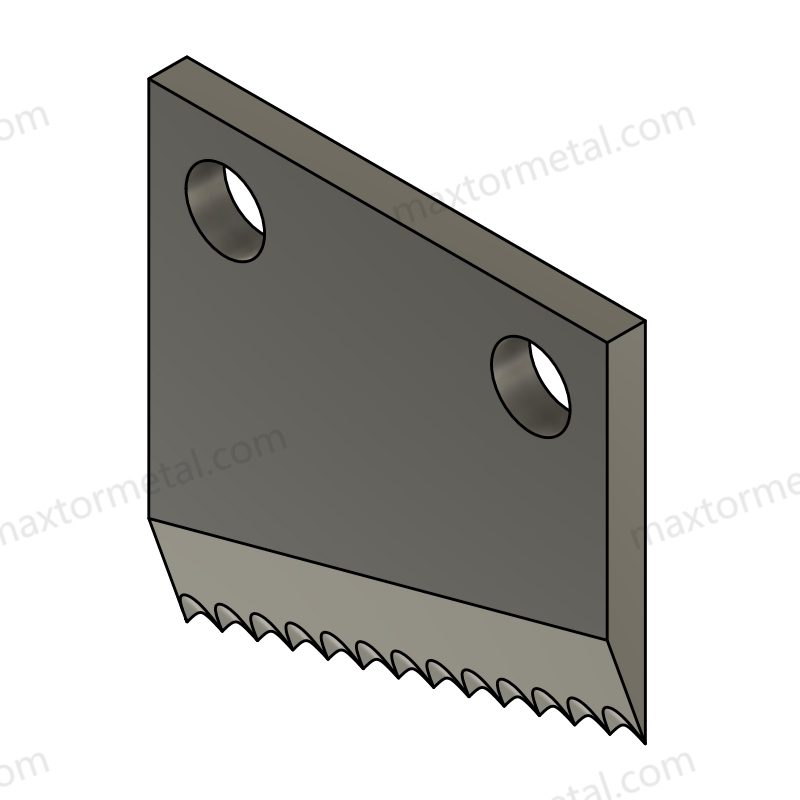
D. Industri Pengemasan: Presisi dengan Kecepatan
⚙️ Tantangan:
- Pemotongan berkecepatan tinggi (hingga 300+ gerakan/menit)
- Bahan film tipis atau multilayer yang rentan robek
- Kebutuhan akan tepi yang sangat bersih untuk menghindari kegagalan penyegelan
🔧 Rekomendasi Geometri:
- Pisau bermata lurus datar dengan Bevel dengan permukaan tanah yang presisi 20–25°
- Pelapis gesekan rendah menyukai Timah atau Kain untuk mencegah lengket
- Pisau profil tipis (≤0,5 mm) untuk film laminasi
📊 Studi Kasus – Klien Nanjing Metal:
Sebelum Penyesuaian | Setelah Optimasi Geometri |
Pergantian mata pisau: 3× per hari | Pergantian bilah: Sekali setiap 2 hari |
Kantong tidak sejajar: 7% | Kantong tidak sejajar: <1% |
Waktu henti saluran: 2 jam/minggu | Waktu henti saluran: <30 menit/minggu |
Peningkatan ini berasal dari menyesuaikan ketebalan bilah dan sudut tepi, tanpa perubahan perangkat keras mesin — hanya geometri bilah yang lebih cerdas.
E. Metal Pengolahan: Stabilitas di Bawah Tekanan
⚙️ Tantangan:
- Ketahanan pemotongan tinggi
- Risiko bilah terkelupas atau terlalu panas
- Kebutuhan akan presisi dimensi pada substrat keras
🔧 Rekomendasi Geometri:
- Pisau tebal dan kaku dengan sudut bevel curam (30–40°)
- Karbida atau HSS (baja kecepatan tinggi) bahan dengan lapisan tahan panas
- Desain yang diperkuat tulang belakang untuk mencegah pembengkokan
📊 Keuntungan Hasil:
Bahan | Geometri yang Digunakan | Peningkatan Efisiensi |
Lembaran aluminium | Tebal 1 mm, tepi karbida 35° | 22% lebih banyak pemotongan per shift |
Besi tahan karat | Bilah bimetal, bevel 30° | Umur bilah meningkat 3× |
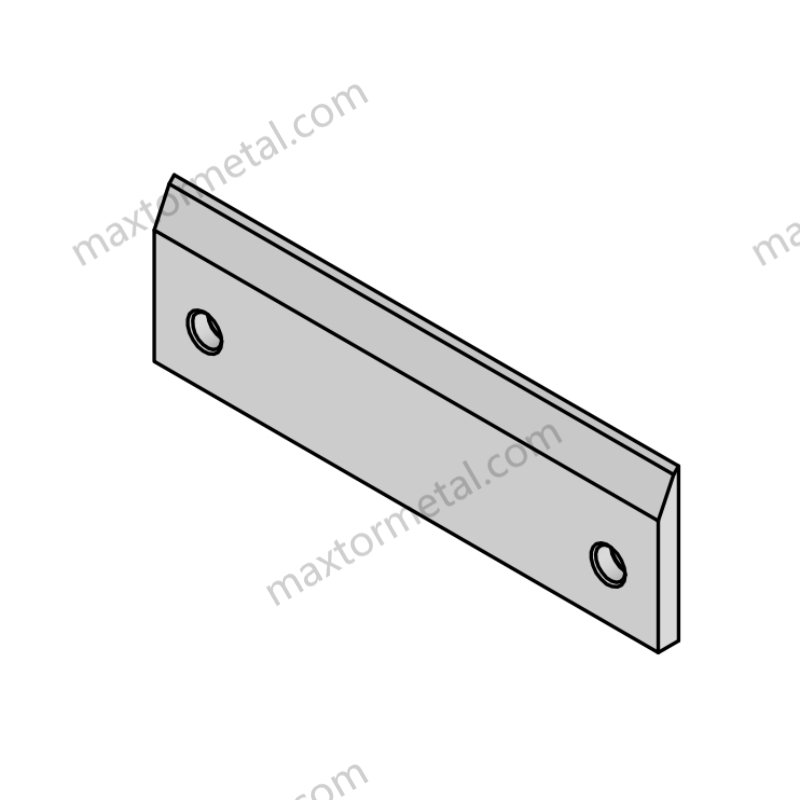
4. Cara Meningkatkan Efisiensi Pemotongan Saat Ini
Bahkan geometri bilah terbaik pun akan gagal jika bilah disalahgunakan, dirawat dengan buruk, atau dioperasikan dalam kondisi yang salah. Berikut adalah strategi yang terbukti untuk memaksimalkan nilai geometri bilah Anda investasi.
A. Perawatan Rutin Membuat Geometri Tahan Lama
Pemeliharaan rutin sangat penting untuk menjaga integritas tepi dan kinerja yang konsisten.
🛠️ Praktik Terbaik Pemeliharaan:
- Pisau bersih dengan sistem pelarut atau ultrasonik setelah setiap shift
- Mengasah atau mengganti pisau berdasarkan kekerasan material dan panjang lintasan
- Periksa sudut tepi menggunakan pembesaran atau sensor profil otomatis
- Mencatat data keausan bilah untuk memprediksi interval penggantian yang optimal
🧪 Menurut survei tahun 2022 oleh CutPro Analytics, pabrik yang menerapkan rencana pemeliharaan bilah proaktif mengurangi waktu henti terkait bilah sebesar 38% dan menghemat rata-rata $5.200/bulan.
B. Mengoptimalkan Kondisi Pemotongan
Geometri pemotongan Anda hanya dapat bekerja sebaik yang dimungkinkan oleh lingkungan mesin Anda.
📐 Variabel Operasional Kritis:
- Kecepatan pemotongan:Kecepatan yang lebih tinggi memerlukan tepi yang lebih halus dan resistansi yang lebih rendah
- Tekanan umpan: Tekanan yang berlebihan menyebabkan keausan dini dan deformasi
- Penyelarasan bilah:Kesalahan penyelarasan meningkatkan beban samping dan keausan bevel
Gunakan pengaturan mesin khusus untuk bilah. Bilah yang dioptimalkan untuk kecepatan 150 m/menit mungkin tidak berfungsi dengan baik pada kecepatan 300 m/menit tanpa dukungan yang tepat.
C. Memilih Geometri Bilah yang Tepat – Panduan Referensi Cepat
Jenis Bahan | Geometri yang Direkomendasikan | Pemikiran |
Plastik | Pitch lebar, sudut bevel tinggi | Mengurangi gesekan, menghindari pencairan |
Kertas | Profil tipis bergerigi mikro | Potongan bersih, meminimalkan robekan |
Daging/Roti | Bergerigi, tahan karat, sudut bevel rendah | Menjaga tekstur, menghindari noda |
Industri Karet | Tulang belakang diperkuat, tepi gigi lebar | Tahan terhadap abrasi dan benturan |
Logam | Karbida, badan tebal, bevel curam | Tahan terhadap resistensi, umur panjang |
Dengan menyelaraskan geometri ke baik karakteristik material dan perilaku mesin, produsen dapat memperoleh keuntungan signifikan dalam kinerja pemotongan, penghematan energi, dan kualitas produk. Ini bukan sekadar penyempurnaan teknis — ini adalah pengoptimalan laba bersih.
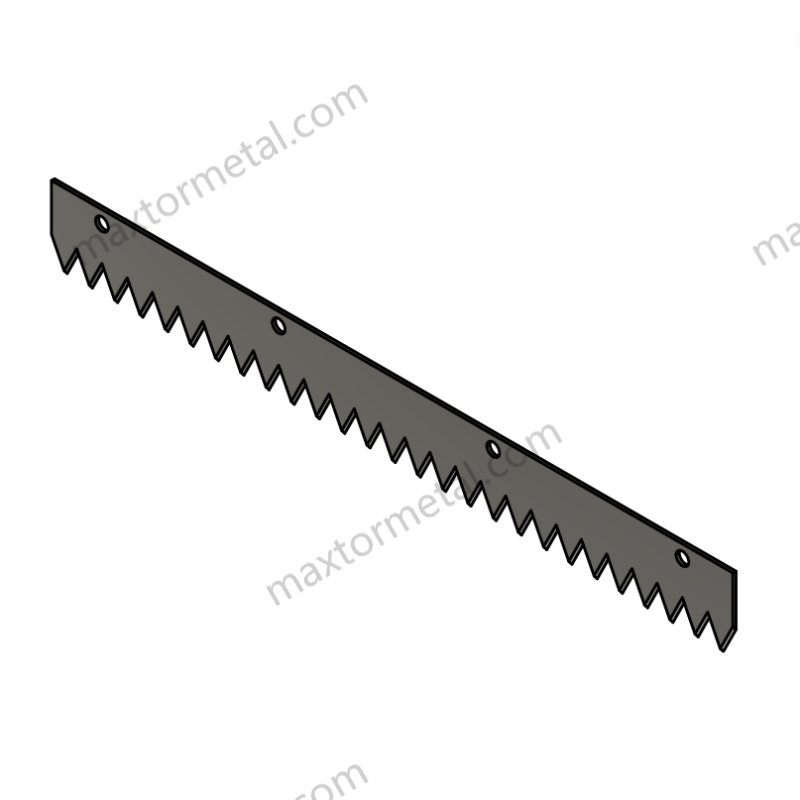
5. Mengapa Geometri Bilah Kustom Menang
Desain yang Disesuaikan = Efisiensi Lebih Tinggi
Anda tidak hanya mendapatkan kinerja yang lebih baik — Anda mendapatkan biaya kepemilikan total yang lebih rendah.
Dampak Geometri Kustom pada Biaya Operasional:
Metrik | Sebelum Kustomisasi | Setelah Nanjing Metal Custom Blade | Peningkatan |
Pergantian bilah per minggu | 10 | 3 | –70% |
Rata-rata tingkat pemotongan skrap | 6.5% | 2.2% | –66% |
Waktu henti karena keausan bilah | 4 jam/minggu | 1 jam/minggu | –75% |
(Sumber: Laporan pelanggan Nanjing Metal, 2023)
Studi Kasus: Pisau Kustom dari Nanjing Metal
Seorang klien di sektor makanan beralih ke pisau bergerigi khusus dari Nanjing Metal. Hasilnya?
- Kecepatan pemotongan ditingkatkan dengan 22%
- Umur bilah diperpanjang dari 2 minggu menjadi 6 minggu
- Ketepatan pemotongan meningkat (varians < 0,5 mm)
Mengapa Nanjing Metal?
Dengan pengalaman lebih dari 18 tahun, Nanjing Metal menyediakan pisau industri yang direkayasa secara presisi di berbagai sektor. Tim kami menawarkan:
- Desain dan pembuatan prototipe internal
- Pemilihan material khusus
- Waktu tunggu singkat dan dukungan ahli
6. Masa Depan Geometri Bilah
Gelombang pemotongan industri berikutnya tidak hanya lebih tajam — tetapi juga lebih pintarKemajuan dalam bidang material, simulasi, dan manufaktur digital mengubah cara bilah dirancang, diuji, dan digunakan.
Material dan Pelapis Generasi Berikutnya
Teknologi permukaan baru memperpanjang umur bilah pisau sekaligus meningkatkan kualitas pemotongan.
Jenis Pelapisan | Manfaat Utama | Aplikasi |
TiN (Titanium Nitrida) | Mengurangi gesekan, meningkatkan kekerasan permukaan | Makanan, kemasan, tekstil |
DLC (Karbon Mirip Berlian) | Mencegah lengket, menghilangkan panas | Film, plastik, karet |
TiCN (Titanium Karbonitrida) | Meningkatkan ketahanan aus dalam kondisi yang keras | Metal, komposit |
📈 Studi Kasus: Pelanggan pengemasan yang menggunakan bilah berlapis DLC melihat interval penggantian bilah meningkat sebesar 53%, dengan tidak ada penumpukan perekat lebih dari uji coba 4 minggu.
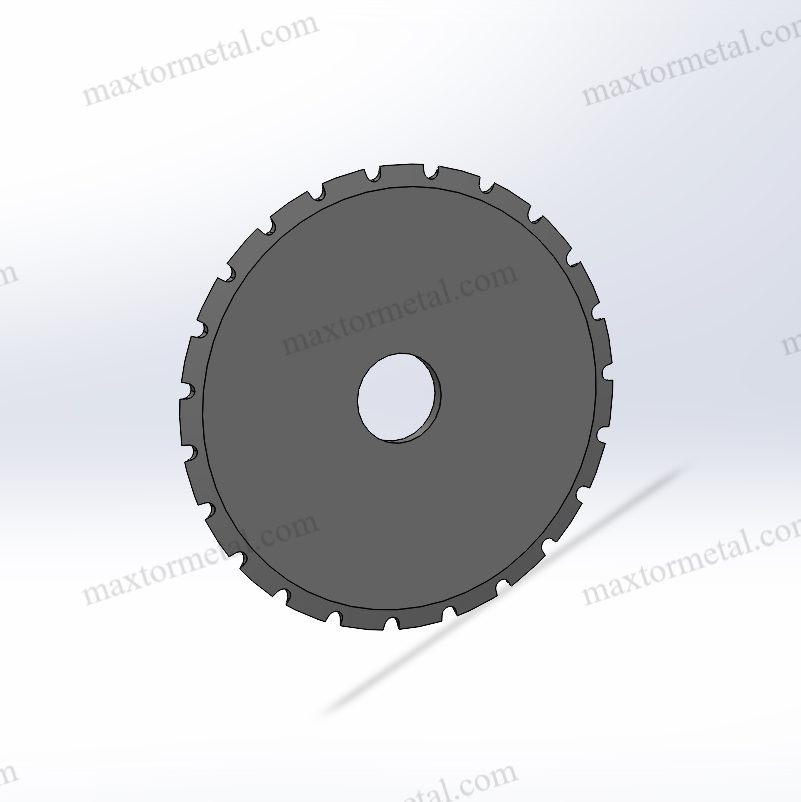
Manufaktur Cerdas & Geometri Berbasis Simulasi
Pengembangan bilah pisau beralih dari coba-coba ke desain berbasis data.
🔍 Tren Utama:
- Analisis Elemen Hingga (FEA) membantu mensimulasikan distribusi tegangan di seluruh geometri bilah
- Prototipe CNC memungkinkan pengujian cepat penyesuaian mikro pada bevel dan pitch
- Optimasi berbantuan AI diterapkan untuk mencocokkan desain bilah dengan mode kegagalan historis
- Pisau uji cetak 3D memungkinkan umpan balik lapangan yang lebih cepat tanpa proses produksi penuh
🧪 Penelitian dari Laboratorium Inovasi Pisau Industri (2023) menunjukkan bahwa penyesuaian geometri berbasis simulasi mengurangi konsentrasi tegangan tepi sebesar 27%, secara signifikan meningkatkan umur bilah di bawah beban.
Menuju Kinerja Pemotongan Prediktif
Masa depan juga mencakup:
- Pisau yang tertanam sensor untuk pemantauan keausan
- Blade sebagai layanan (BaaS) model di mana data kinerja mendorong penataan ulang otomatis
- Kembaran digital sistem pemotongan untuk pemeliharaan prediktif dan penjadwalan bilah
Pisau tidak akan lagi menjadi sekadar alat pasif — pisau akan menjadi bagian dari ekosistem cerdas yang memprediksi keausan, mengoptimalkan kondisi pemotongan, dan memberikan masukan data ke dalam perbaikan desain.
Geometri yang Lebih Baik, Potongan yang Lebih Baik
Geometri bilah pisau lebih dari sekadar detail teknis — ini adalah alat strategis untuk meningkatkan kinerja. Geometri pisau yang tepat dapat:
- Meningkatkan kecepatan output
- Mengurangi sampah
- Memperpanjang umur bilah
- Meningkatkan kualitas produk
Jangan puas dengan bilah standar. Biarkan Nanjing Metal membantu Anda mendesain bilah yang tepat untuk aplikasi Anda.
👉 Hubungi teknisi kami untuk konsultasi gratis hari ini.
Sumber & Referensi
- Wawasan Teknologi Manufaktur, “Tren dalam Desain Bilah Industri,” 2022
- BladeTech Solutions: Laporan Kinerja Internal, 2023
- Jurnal Pengolahan Makanan, “Mengoptimalkan Pemotongan di Jalur Kecepatan Tinggi,” 2021