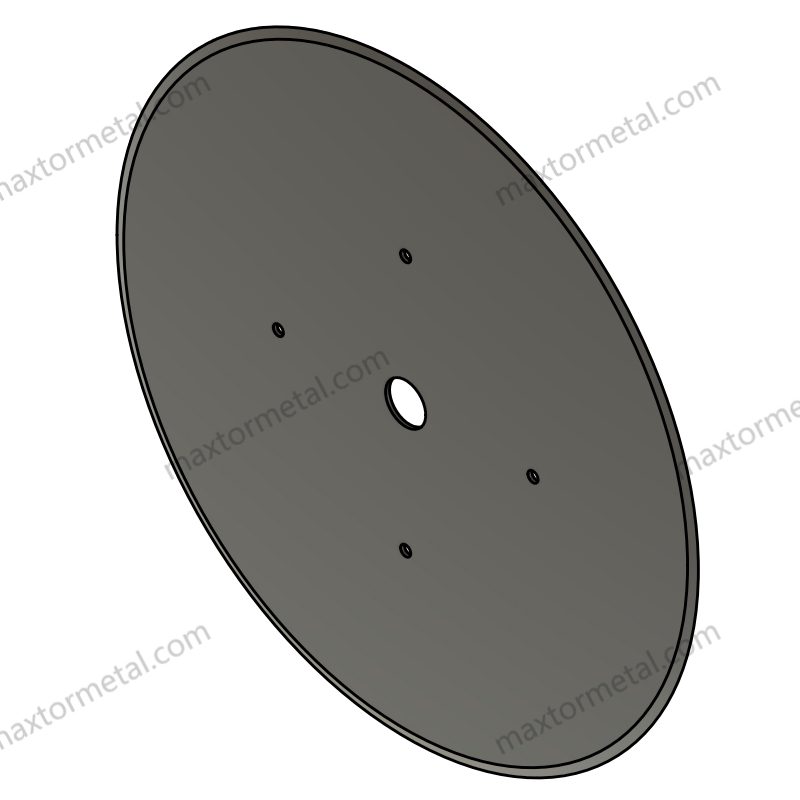
Picking the best material and setup for Coltelli Circolari Industriali helps them work well in any factory. Blade material, edge style, and special coatings should fit the material being cut and what each industry needs. High-speed steel, tungsten carbide, ceramic, and special coatings all have their own good points. Choosing the right one gives cleaner cuts, makes blades last longer, and helps work get done faster.
Punti chiave
- Picking the right blade material, like high-speed steel, tungsten carbide, ceramic, or stainless steel, helps blades cut better and last longer.
- Blade edge styles, such as single bevel, double bevel, or serrated, need to fit the material. This helps make clean cuts and less waste.
- Coatings like TiN, DLC, and TiCN make blades tougher. They also lower friction, stop rust, and help blades last longer.
- Rotary blades cut faster and wear out evenly. They work best for thin materials and fast jobs.
- Custom blades made for special materials and jobs can cut downtime by up to 75%. They also lower scrap rates a lot.
- Taking care of blades by cleaning, sharpening, and storing them keeps them working well and saves money.
- Matching blade material, edge type, and coating to the job makes work faster and costs less.
- Talking to experts or companies like Nanjing Metal can help you pick or design the best blade for your needs.
Risultati chiave
Best Materials
Picking the right blade material is very important for each job. High-speed steel (HSS) is very hard and keeps its sharp edge even when moving fast. Tungsten carbide is very tough and lasts a long time, so it works well in places where blades get used a lot. Ceramic blades stay sharp for a long time and do not rust, which is great for careful cutting in clean or medical places. D2 tool steel and high-carbon steels like 1095 and 52100 are strong and last long, so they are good for cutting rubber and plastics. Stainless steel is best for food, medical, and nonwoven jobs because it does not rust and is easy to clean.
Making blades with high concentricity helps them cut better and last longer. Blades that do not wobble much shake less, last longer, and waste less material. This is very helpful in packaging and food jobs.
Top Configurations
How the Coltelli Circolari Industriali are made changes how well they work and how often you need to fix them. Thin, sharp blades with one bevel are great for cutting film. They make clean cuts and do not waste much material. Double bevel or blunt edges are strong and good for rubber and plastics. They can take hits and do not chip easily. Serrated or wavy edges are good for tough or stretchy things. They help the machine work easier and make cuts more even. Carbide-tipped and ceramic-coated blades last longer and need to be changed less in busy factories.
- Good blade types include:
- Razor slitting blades for thin films and foils
- Score slitting blades for rubber and foam
- Shear slitting blades for paper and cardboard
- Perforating blades for packaging
- Toothed blades for thick or stringy materials
Cleaning, sharpening, and storing blades the right way helps them last longer and work their best.
Application Matrix
The table below shows the best blade materials and edge types for different jobs:
Area di applicazione | Materiali comuni delle lame | Typical Edge Types & Configurations | Performance Considerations |
---|---|---|---|
Film | HSS, Tungsten Carbide | Thin, sharp edge, single bevel | Very exact cuts, fast work, little waste |
Rubber & Plastics | D2 Tool Steel, HSS, Carbide | Double bevel, blunt edge | Very tough, lasts long, can take hits |
Nonwovens (Hygiene) | Stainless Steel, Ceramic | Sharp, clean edge, single bevel | Clean cuts, does not rust, safe for hygiene |
Paper & Foil | HSS, Tool Steel, Carbide | Sharp edge, single or double bevel | Even cuts, less dust, blades last longer |
Lavorazione alimentare | Stainless Steel, Ceramic | Sharp edge, single bevel | Safe for food, does not rust, easy to clean |
Note: Coatings like TiN, CrN, and DLC make blades tougher and help them cut better in all jobs.
Domande frequenti
Which circular blade material is best for cutting multilayer film?
Tungsten carbide or HSS blades with a thin, sharp edge work best for multilayer film. They give clean cuts and do not waste much material.
Can TiCN coating outperform TiN in high speed slitting?
TiCN coatings are harder and last longer than TiN. They are good for fast cutting when you want blades to last longer.
Industrial Circular Knives Overview
Definizione
Industrial circular knives are round tools with sharp edges. They spin to cut, slit, or score many materials in factories. Their spinning makes them good for fast work on production lines. The way the edge is shaped helps make cuts neat and exact. Makers use carbon steel, high-speed steel, alloy tool steel, tungsten carbide, ceramics, and stainless steel for different jobs. Coatings like titanium nitride (TiN) and chromium nitride (CrN) make the knives harder and help them last longer. These coatings also stop rust and lower friction. There are many types of circular knives. Some are solid discs, some have inserted blades, and others are scored, shear cut, perforating, slitting, dished, or toothed knives. Each type is made for a special kind of cutting or material.
Rotary motion, special designs, and edge shapes make industrial circular knives different from other cutting tools. They work well in fast factories and are important for modern manufacturing.
Stili di bordo
The edge style changes how well a circular knife cuts. It also decides what materials it can cut. Picking the right edge shape helps make clean cuts and less waste. The table below shows common edge styles and what they do:
Edge Style | Description & Impact on Cutting Performance | Application Suitability |
---|---|---|
V-style | Standard V shape gives even force. Some V shapes spread force and control pressure. | Good for general cutting with even force |
Smerlato | Has rounded teeth like a saw. Cuts soft or thick things smoothly. | Used for foams, some foods, and soft stuff |
L-style | Not explained | Not explained |
Peg style | Not explained | Not explained |
Slant tooth | Not explained | Not explained |
You need to pick the right edge style for the material’s hardness and thickness. For example, V-style is good for most jobs. Scalloped edges are better for soft or thick things.
Rotary vs. Straight Blades
Rotary and straight blades do different jobs in factories. Rotary blades are round and spin when used. This lets them cut fast and over and over again. They are best for thin sheets, coils, and things that need lots of slitting. Straight blades have a flat edge that does not move. They are used in machines like guillotines to cut thick things like metal sheets or rebar in one go.
Rotary blades get special heat treatments to make them harder and last longer. These treatments include tempering, carburizing, and nitriding. This means rotary blades wear out slower and need less fixing. For example, heat-treated rotary blades can last up to 40% più lungo than ones without treatment. Straight blades can wear out unevenly and need sharpening or changing more often.
Caratteristica | Lame dritte | Rotary Blades |
---|---|---|
Progettazione della lama | Flat edge; used for thick things | Round, spins; cuts thin things over and over |
Meccanismo di taglio | Cuts in one straight move | Spins for fast, repeated cutting |
Cutting Speed & Efficiency | Slower, best for thick or small jobs | Faster, good for big, busy jobs |
Applicazione | Metal sheets, rebar, thick plates | Thin metals, foil, strips, films, paper |
Wear & Maintenance | Wears unevenly; needs sharpening a lot | Wears evenly; needs less fixing |
Durability & Longevity | Depends on what it cuts | Lasts longer with special heat treatment |
Cost & Complexity | Simple, usually cheaper | More parts, costs more because it spins |
Rotary blades wear out evenly and last longer, especially in fast, busy factories. Straight blades are best for thick things that need one strong cut.
Nanjing Metal is a top maker of industrial circular knives. They have made blades for over 20 years. The company can make special blades for different factory needs. Their team checks every blade to make sure it is high quality. If a business needs a special blade, Nanjing Metal offers custom blade services to help.
Impact of Blade Material and Coating on Cost and Efficiency
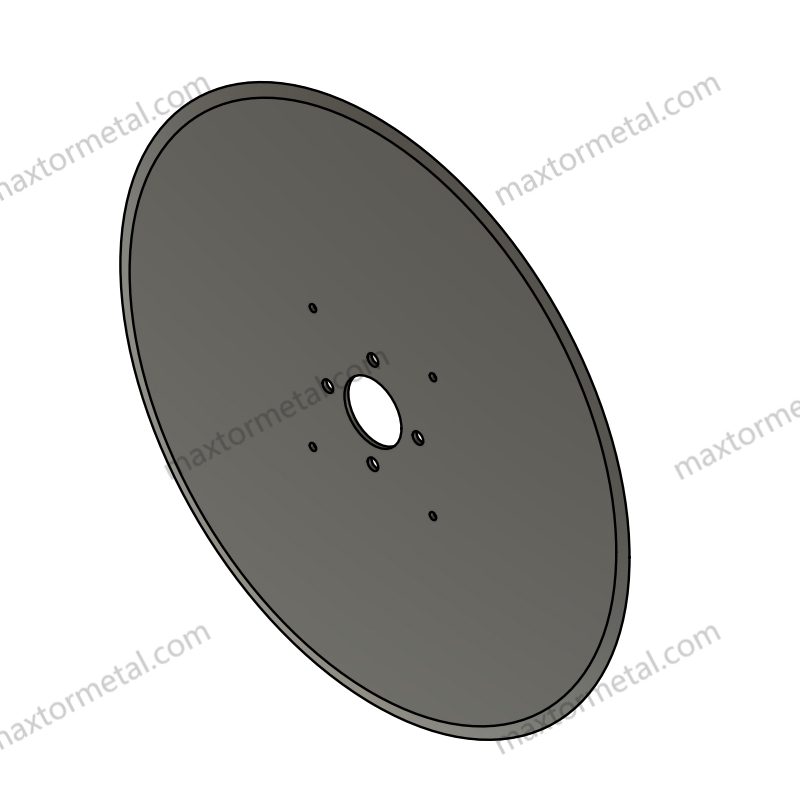
The blade material and coating you pick can change how much money and time a factory spends. Each material works best for certain jobs. Coatings help blades work better by making them last longer and cut smoother.
How Blade Material Affects Cost and Efficiency
Choosing the right blade material saves money and makes cutting better. Harder materials like tungsten carbide and ceramic last longer. They do not need to be changed as often. Stainless steel and HSS are not as hard, but they cost less and still last a good amount of time. The table below shows how different blade materials affect cost and how well they work:
Materiale della lama | Durezza (HRC) | Applicazioni ideali | Impact on Cost & Efficiency |
---|---|---|---|
Acciaio inossidabile | 55–60 | Alimentare, medico, leggero | Medium durability, corrosion resistance, moderate lifespan |
Acciaio ad alta velocità | 60–64 | Carta, legno, plastica | Supports various edge thicknesses, balanced cost and life |
Carburo di tungsteno | 75–85 | Metal, gomma, compositi | High hardness, longer life, reduces blade changes and downtime |
Ceramica | 80–90 | Lamine, microfilm, ottica | Ultra-thin edges but brittle, risk of breakage if misused |
Tungsten carbide and ceramic blades can cut tough things for a long time. This means you do not have to stop and change blades as much. For example, HSS blades for film cutting stay sharp and last long. This is why many factories use them for packaging.
The Role of Coatings in Blade Performance
Coatings like titanium nitride (Stagno), diamond-like carbon (DLC), and titanium carbonitride (TiCN) make blades work better. These coatings make blades harder and smoother. They also stop things from sticking to the blade. The table below shows what each coating does:
Tipo di rivestimento | Vantaggio chiave | Application Areas | Effect on Ownership Cost & Efficiency |
---|---|---|---|
TiN (nitruro di titanio) | Reduces friction, increases hardness | Alimenti, imballaggi, tessili | Extends blade life, reduces friction-related wear |
DLC (carbonio simile al diamante) | Previene l'incollamento, dissipa il calore | Pellicola, plastica, gomma | Increases blade change intervals by 53%, eliminates adhesive buildup |
TiCN (carbonitruro di titanio) | Migliora la resistenza all'usura in condizioni difficili | Metal, compositi | Enhances durability under tough conditions, lowers scrap and downtime |
Tungsten carbide rotary knives with DLC coating can cut sticky or rough things without needing to be cleaned or changed a lot. Ceramic blades for nonwovens stay sharp and do not rust, so they are good for medical and clean jobs.
Real-World Impact: Cost and Efficiency Gains
When factories use the best blade material and coating, they work better. The chart below shows how custom blades help factories:
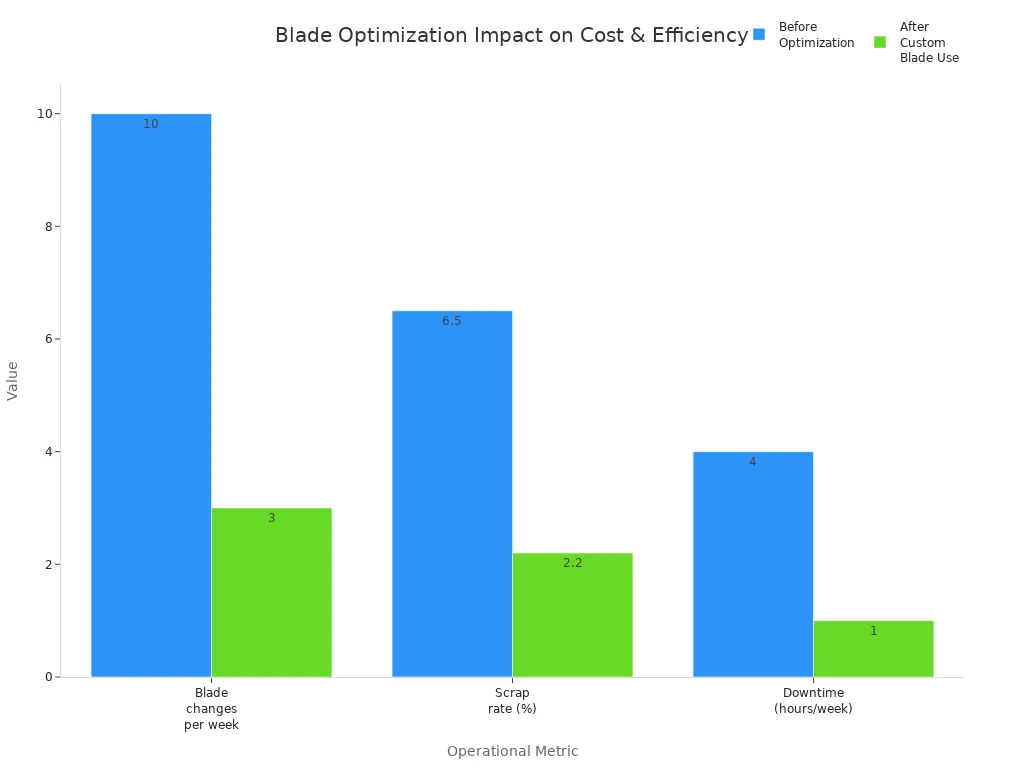
- Blade changes each week went down by 70%.
- Scrap rates dropped by 66%.
- Downtime was cut by 75%.
A food company used custom serrated blades and cut faster by 22%. Their blades lasted from 2 weeks to 6 weeks. Their cuts were also more exact, with less than 0.5 mm difference.
Material and Coating Influence on Blade Stability and Lifespan
Tests show that martensitic stainless steel, like X39Cr13, is very hard and strong. This helps blades last longer and cut better. Coatings put on by PVD, like AlCrN and DLC, make blades last even longer. But if there are hard things like sand in the material, blades can wear out faster. Picking the right blade and coating keeps cutting steady and stops machines from breaking down.
Perché la personalizzazione è importante
Every factory has its own cutting problems. Custom blades made for special jobs help save money and time. Nanjing Metal is a top maker of industrial circular knives. They have made custom blades for over 20 years. Their team offers custom blade services to fit what each customer needs.
Tip: Always pick blade material and coating that match what you are cutting. This helps you save money, work faster, and make blades last longer.
Domande frequenti
How do coatings like DLC and TiN affect blade replacement frequency?
DLC E Stagno coatings make blades harder and smoother. This means blades last longer and need to be replaced less often.
What is the best blade for slitting abrasive rubber?
Tungsten carbide rotary knives with a DLC coating work best for cutting rough rubber. They last the longest and wear out the slowest.
Can custom blades really reduce downtime?
Yes. Custom blades made for special jobs can cut downtime by up to 75% and lower scrap rates.
Want to make your cutting better? Contact Nanjing Metal’s sales engineers for help and advice.
Comprehensive Comparison of Industrial Circular Knife Materials and Their Performance
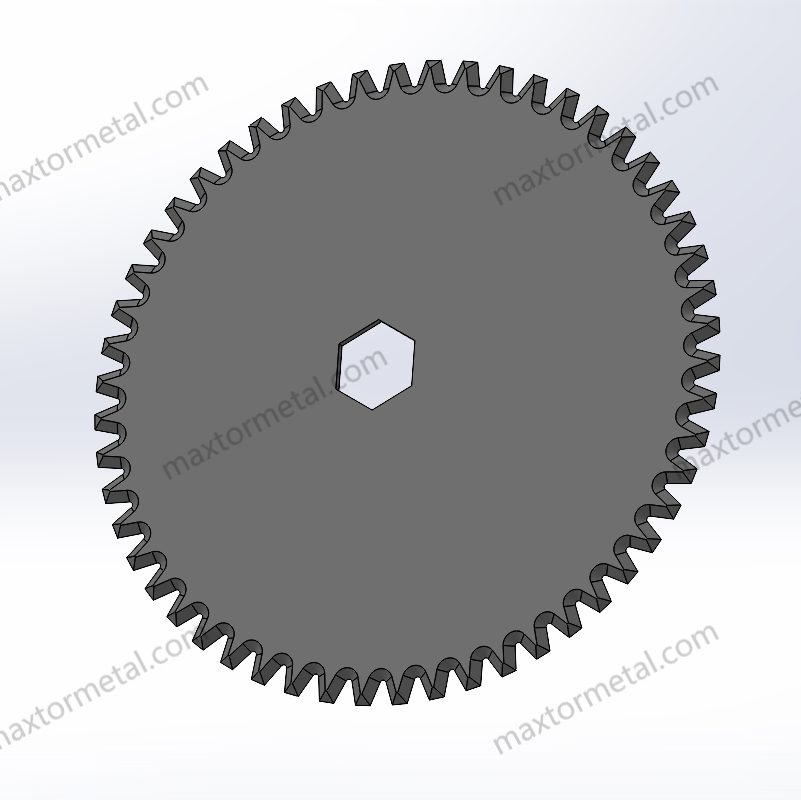
Acciaio per utensili
Caratteristiche del materiale
Tool steel is used a lot because it is hard, tough, and not too expensive. It is made from carbon and alloy steels. These blades are good for places where things do not wear out too fast. Tool steel blades are easy to shape and sharpen. They do not last as long as some other blade materials. But they are a smart pick when you want to save money and do not need the blade to last forever.
The table below shows the main tool steel types, what they are good at, and where they are used:
Tool Steel Type | Key Performance Characteristics | Applicazioni comuni |
---|---|---|
Water-hardening steels | Gets hard in water, stands up to stress and wear | Used for wood and paper cutting |
Shock-resistant steels | Does not crack or break when hit hard | Used for chisels, punches, and tools that get hit |
High-speed steels | Stays hard and strong even when hot | Used for fast cutting and drilling |
Cold-work steels | Tough and does not wear out fast at room temperature | Used for tools that cut or shape things for a long time |
Hot-work steels | Stays hard and tough when hot | Used for forging, die casting, and hot tools |
D2 steel is a kind of tool steel with lots of carbon and chromium. It is very hard and keeps its edge well after heat treatment. It can get up to 60-62 HRC. Tool steel knives are used in paper, packaging, food, plastics, and metalworking. The type of steel you pick depends on how hard, tough, or easy to sharpen you need it to be, and how much you want to spend.
Tool steel blades are best when you care more about saving money than making the blade last the longest.
Lame HSS
Caratteristiche del materiale
High-Speed Steel (HSS) blades work better than regular tool steel. HSS blades stay hard and sharp even when they get hot. This makes them great for fast and busy cutting jobs. They last longer and do not need to be changed as much. This helps workers get more done.
The table below compares HSS blades and lame in carburo di tungsteno:
Parametro | High-Speed Steel (HSS) Blades | Lame in Carburo di Tungsteno |
---|---|---|
Hardness (Vickers) | 700 – 900 HV | 1600 – 2200 HV |
Velocità di taglio | About 70 m/min (steel) | About 160 m/min (alloy steel) |
Tool Life | Good, but not as long | Lasts 5–10 times longer |
Resistenza al calore | Up to 500°C | Up to 1000°C |
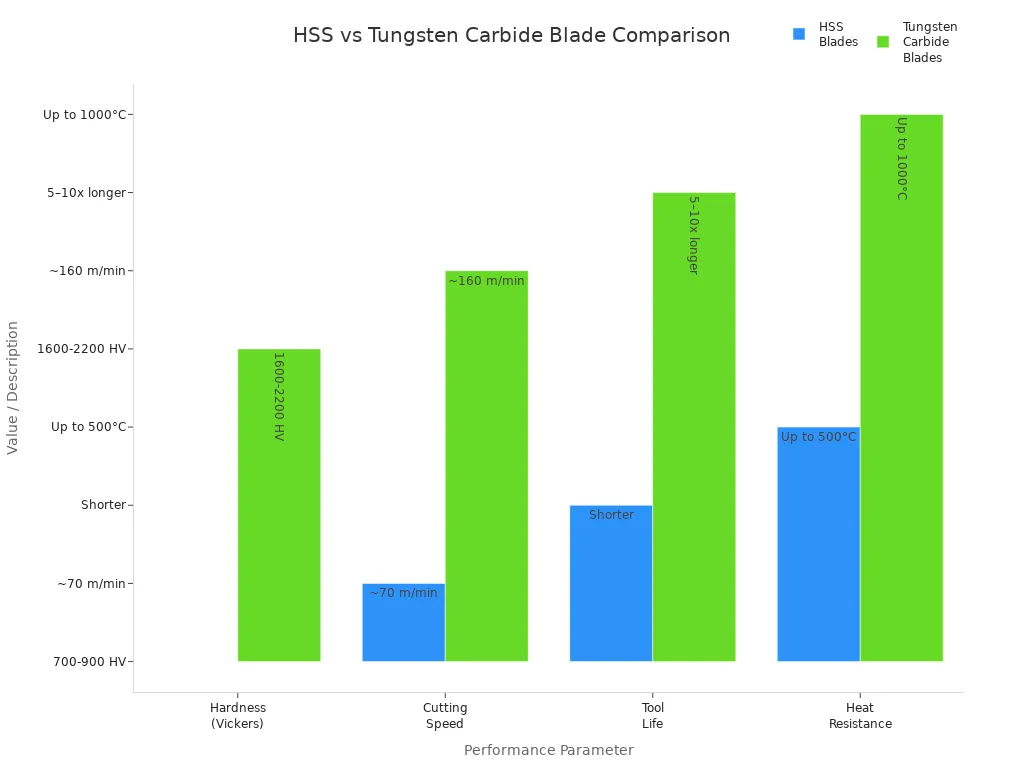
HSS blades are tough and can take hits without breaking. They are easier to sharpen and cost less than tungsten carbide blades. This makes them good for softer things and jobs that are not too rough. In paper factories, HSS blades are used a lot for cutting and slitting. They need to be sharpened more often than carbide blades.
HSS blades are a good mix of lasting long, not costing too much, and being easy to fix. That is why many people use them for industrial circular knives.
Lame in Carburo di Tungsteno
Caratteristiche del materiale
Tungsten carbide blades are the hardest and last the longest. They keep their sharp edge much longer than tool steel or HSS. This is true when cutting hard or rough things. Because they are so hard, they can cut faster and last longer. This is very helpful in busy places that need exact cuts.
The table below shows how tungsten carbide blades are different from HSS and tool steel blades:
Attribute | Lame in Carburo di Tungsteno | HSS and Tool Steel Blades |
---|---|---|
Durezza | Much harder, the hardest | Not as hard as carbide |
Mantenimento del bordo | Stays sharp much longer, even with rough stuff | Needs sharpening more often |
Abrasive Wear Resistance | Best at not wearing out, great for rough things | Wears out faster, gets dull quicker |
Robustezza | More likely to chip if hit | Tougher, can take hits and shakes |
Resistenza al calore | Handles more heat, can cut faster | Cannot take as much heat, gets soft above 600°C |
Costo | Costs more at first but saves money later | Cheaper at first, easier and cheaper to sharpen |
Applicazioni adatte | Best for lots of cutting and tough jobs | Good for normal jobs and softer things |
- Tungsten carbide tips keep their edge and last longer, even with tough or thick things.
- Carbide blades stay hard at very high heat (over 1100°C), so they can cut faster and last longer.
- Carbide is harder but can break easier than HSS if hit or shaken.
- Carbide blades are best for fast, exact, and rough cutting. HSS blades are better for normal jobs and when the blade might get hit.
Tungsten carbide blades need to be handled with care because they can chip. But they work so well in tough jobs that many people think they are worth the price. Factories that cut rubber, composites, or layered films often pick tungsten carbide for its sharpness and long life.
If you want your blades to last the longest and stop work less, tungsten carbide blades are the best.
Nanjing Metal is a top maker of industrial circular knives. They have made custom blades for over 20 years. Their team can make special blades for many jobs. If you need a special blade, you can look at custom blade services to help your work.
Domande frequenti
Which circular blade material is best for cutting abrasive composites?
Tungsten carbide blades are best for cutting rough composites because they are very hard and do not wear out fast.
Are HSS blades suitable for high-speed slitting of paper and film?
Yes, HSS blades stay sharp at high speeds and work well for cutting paper and film. But they need to be sharpened more often than carbide blades.
Want to make your cutting better? You can ask Nanjing Metal’s sales engineers for help.
Lame in Ceramica
Caratteristiche del materiale
Ceramic blades are very hard and keep their sharp edge for a long time. They are made from special ceramic materials like zirconia or alumina. These blades have a Mohs hardness of 8.2, which is much harder than steel. Because of this, ceramic blades can stay sharp up to ten times longer than steel blades. Workers like that ceramic blades do not rust or corrode. This makes them great for clean places like food factories, medical plants, and hygiene product lines.
Ceramic blades are light, so workers do not get tired as fast. Since they are not metal, they do not react with sensitive things. But, because they are so hard, ceramic blades can break or chip if hit from the side. That is why factories use ceramic blades mostly for careful cutting of soft or gentle materials like films, nonwovens, and special papers.
Proprietà | Lame in Ceramica | Lame in acciaio |
---|---|---|
Hardness (Mohs) | 8.2 (very hard) | 5–6 |
Mantenimento del bordo | Stays sharp up to 10 times longer | Needs sharpening often |
Fragilità | High (can chip or crack easily) | Low (more bendy and strong) |
Durata | Hard but can break | Tough and bends more |
Note: You need diamond tools to sharpen ceramic blades. They cost more at first, but you do not have to change or fix them as much.
Comparative Summary: Lifespan and Wear Resistance
Ceramic blades are the best at staying sharp and not wearing out. Their hardness lets them keep a sharp edge for a long time, even when cutting soft or rough things. Compared to tool steel, HSS, and tungsten carbide, ceramic blades do not rust and are not hurt by chemicals.
IL table below shows how the main blade materials compare:
Materiale | Durezza (HRC) | Resistenza all'usura | Resistenza alla corrosione | Stabilità termica | Applicazioni tipiche |
---|---|---|---|---|---|
Acciaio ad alto tenore di carbonio | 55–62 | Moderare | Basso | Moderare | General cutting, saves money |
Acciaio per utensili D2 | 58–62 | Alto | Moderare | Alto | Exact cutting, tough jobs |
Acciaio rapido M2 | 60–65 | Molto alto | Moderare | Molto alto | Fast, hot cutting work |
Carburo di tungsteno | 75–80 | Estremamente alto | Alto | Molto alto | Hard jobs, lasts a long time |
Ceramica | 85+ | Alto | Molto alto | Basso | Super exact, non-metal jobs |
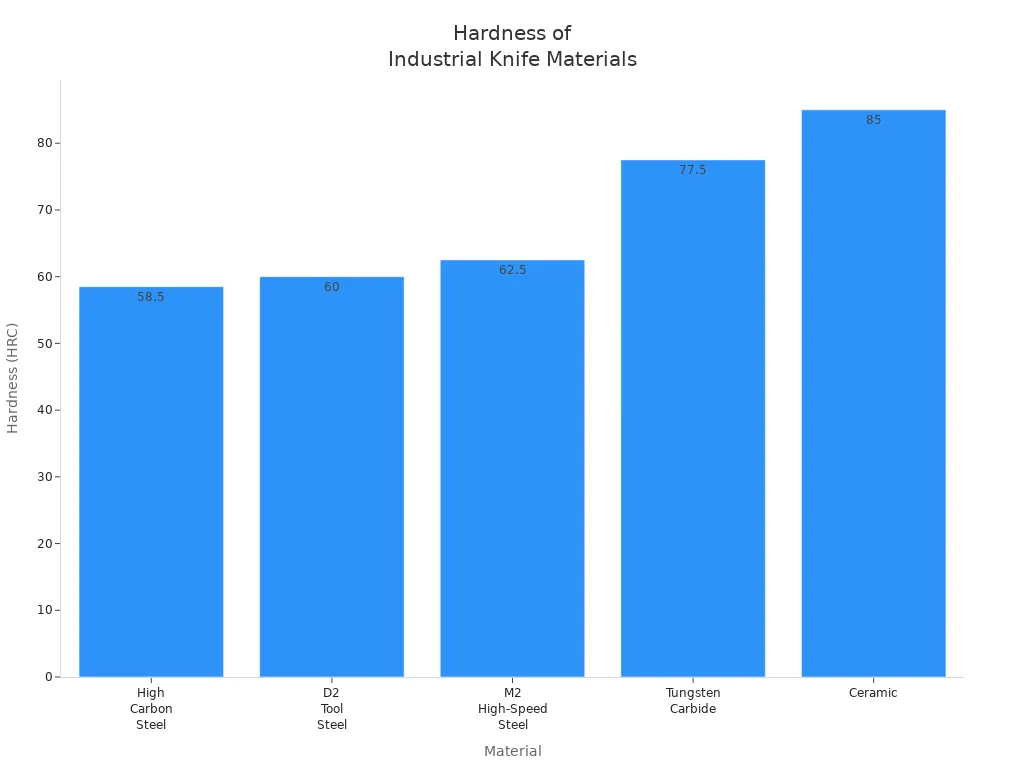
- Ceramic blades stay sharp much longer than steel or carbide blades.
- They are good for jobs where you do not want to change blades a lot.
- But, they do not handle heat well, so they are not good for hot cutting.
- Because they can break, they are not used for heavy or rough jobs.
Summary: Ceramic blades are great for careful, long-lasting cuts on soft or rough things, but you must be careful not to chip them.
Domande frequenti
Are ceramic blades suitable for cutting abrasive nonwovens or hygiene products?
Yes. Ceramic blades stay sharp and make clean cuts in nonwovens and hygiene materials. This means you do not have to change blades as often.
Can ceramic blades be used for high-speed slitting of films?
Ceramic blades can cut thin films quickly, but you must be careful not to hit them from the side or they might chip.
What is the main limitation of ceramic blades in industrial use?
The biggest problem is that they can chip or crack if they get hit from the side or dropped.
Comprehensive Analysis of Blade Coatings and Their Impact on Industrial Circular Knife Performance
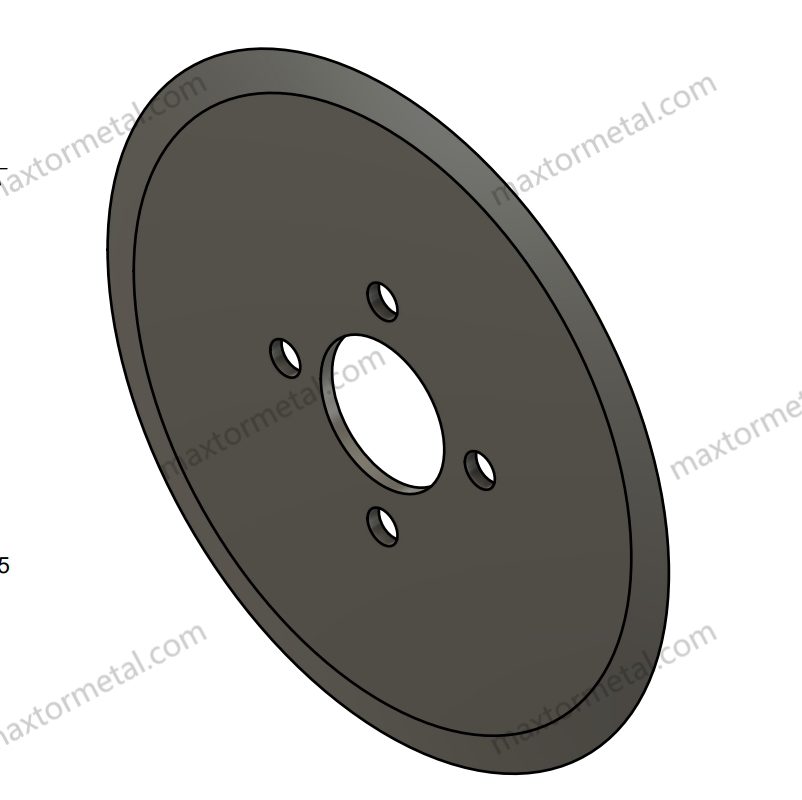
Common Coating Types
Blade coatings help cutting tools work better and last longer. Makers use special coatings to solve problems like wear, friction, and rust. Here are some common coatings:
- Diamond Coating: Keeps blades sharp longer and stops wear. This means less time spent changing blades.
- Nitruro di cromo (CrN): Sticks well to blades, fights rust, and lowers friction. This keeps blades cool.
- Zirconium Nitride (ZrN): Makes blades very hard and stops rust. It helps blades make cleaner cuts.
- Chrome Coating: Makes blades harder and helps them last longer. It protects against rust and wear.
- Teflon (PTFE) Coating: Stops things from sticking to blades. It also helps with heat and friction.
- Nitruro di titanio (TiN): This hard ceramic coating is put on by PVD. It makes blades harder, tougher, and smoother.
- Teflon Black Nonstick: This FDA-approved coating stops sticky stuff from building up. It also fights rust and wear, which is good for food jobs.
- Titanium Carbon Nitride (TiCN): Has titanium, carbon, and nitrogen. It makes blades harder and stops rust. It is good for fast cutting.
- Cromo duro: Helps steel blades fight rust and wear. It also makes them last longer.
- Carbonio simile al diamante (DLC): Makes blades very hard and smooth. It also helps blades handle heat and tough jobs.
- PolyTetraFluoroEthylene (PTFE): This coating bends easily, does not react with chemicals, and has a high melting point.
- Electroless Nickel Plating: Makes blades smoother and fights rust and wear. But it does not make blades harder.
Coatings make blades harder, lower friction, stop rust, and help blades last longer.
TiN (Titanium Nitride) Coating
TiN coating is gold and very hard. Makers use PVD to put it on blades. TiN makes blades about 25% harder. It also lowers friction and helps blades last longer. TiN stops blades from rusting. It is used for cutting soft metals like aluminum and copper. Blades with TiN last 20–30% longer than blades without it.
TiAlN (Titanium Aluminum Nitride) Coating
TiAlN is even harder than TiN and can take more heat. This makes it good for fast, hot cutting jobs, like cutting hard metals. TiAlN can help blades last up to 35% longer. It looks dark gray or black and protects blades from heat and wear.
DLC (Diamond-Like Carbon) Coating
DLC coating is very hard and super smooth. It stops things from sticking to blades. It helps blades work better, especially when cutting fast or sticky things. DLC-coated blades are great for soft metals and sticky jobs. They can last up to 50% longer, so they are good for tough places.
Performance Enhancements from Coatings
Wear Resistance and Friction Reduction
Blade coatings help blades fight wear and lower friction. TiN, TiAlN, and DLC each have special strengths:
Tipo di rivestimento | Hardness (HV) | Vantaggi principali | Applicazioni tipiche | Blade Life Improvement |
---|---|---|---|---|
TiN (nitruro di titanio) | ~2200-2400 HV | Makes blades harder, lowers friction, stops rust | Soft metals like aluminum and copper | 20-30% longer |
TiAlN (nitruro di titanio e alluminio) | Up to 3200 HV | Even harder, takes more heat, good for fast cutting | Hard metals, metal coil slitting | Up to 35% longer |
DLC (carbonio simile al diamante) | 1000-2400 HV | Very hard, super smooth, stops sticking | Soft metals, fast cutting | Up to 50% longer |
These coatings help blades stay sharp, keep cool, and cut smoothly. For example, DLC makes blades less sticky and gives cleaner cuts. TiAlN can take more heat, so it is good for fast, hot jobs.
Coated blades last longer, cut better, and need to be changed less often.
Corrosion Protection
Many coatings also keep blades from rusting. Chromium Nitride (CrN), Hard Chrome, and PTFE protect blades from water and chemicals. This is important in food, hygiene, and medical jobs where blades must stay clean. Teflon and Teflon Black Nonstick also stop sticky stuff from building up and make cleaning easier.
Comparative Table: Wear Resistance and Cost
Coated blades cost more at first, but save money later. They need less fixing and last longer. Here is a table that shows how coatings compare:
Tipo di rivestimento | Resistenza all'usura | Corrosion Protection | Riduzione dell'attrito | Costo iniziale | Estensione della durata della lama |
---|---|---|---|---|---|
Stagno | Alto | Moderare | Moderare | Moderare | 20-30% |
TiAlN | Molto alto | Moderare | Moderare | Alto | Up to 35% |
DLC | Eccezionale | Alto | Molto alto | Alto | Up to 50% |
CrN | Alto | Alto | Alto | Moderare | 20-30% |
PTFE/Teflon | Moderare | Alto | Molto alto | Moderare | 10-20% |
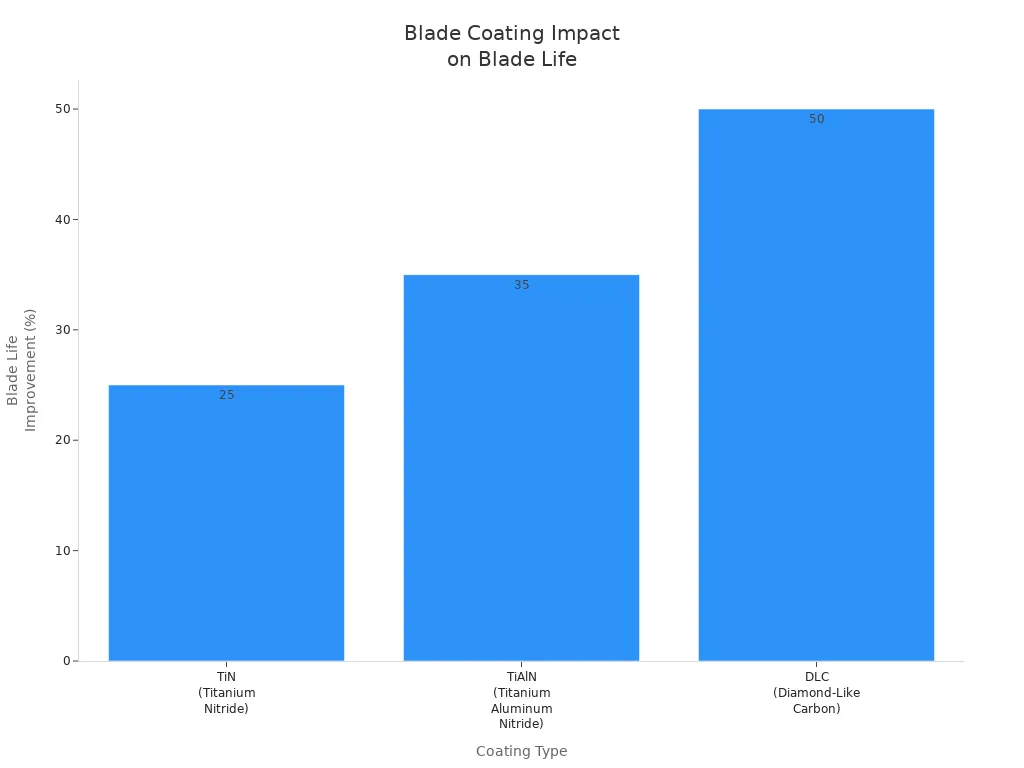
Top coatings like TiN and TiCN can make blades last up to 40% longer. They also cut fixing time by 30%. DLC coatings give the best wear resistance and smoothness. They are good for tough or sticky jobs. Even though coated blades cost more at first, they save money over time by lasting longer and working better.
Better coatings help blades last longer and make products better by cutting faster and making fewer mistakes.
A textile factory switched from carbon steel to stainless steel blades with coatings. They changed blades 30% less often and made 12% more products. Coated blades also wasted less fabric and cut faster.
Domande frequenti
Which coating is best for cutting sticky or adhesive materials?
DLC and PTFE coatings are best for sticky things. They stop stuff from sticking and keep blades clean.
How do TiN and TiAlN coatings compare for high-speed metal slitting?
TiAlN is harder and takes more heat than TiN. It is better for fast, hot cutting of hard metals.
Do coated blades really save money in the long run?
Yes. Coated blades last longer, need less fixing, and cut better. This saves money over time.
Industrial Circular Knives Applications Across Key Industries
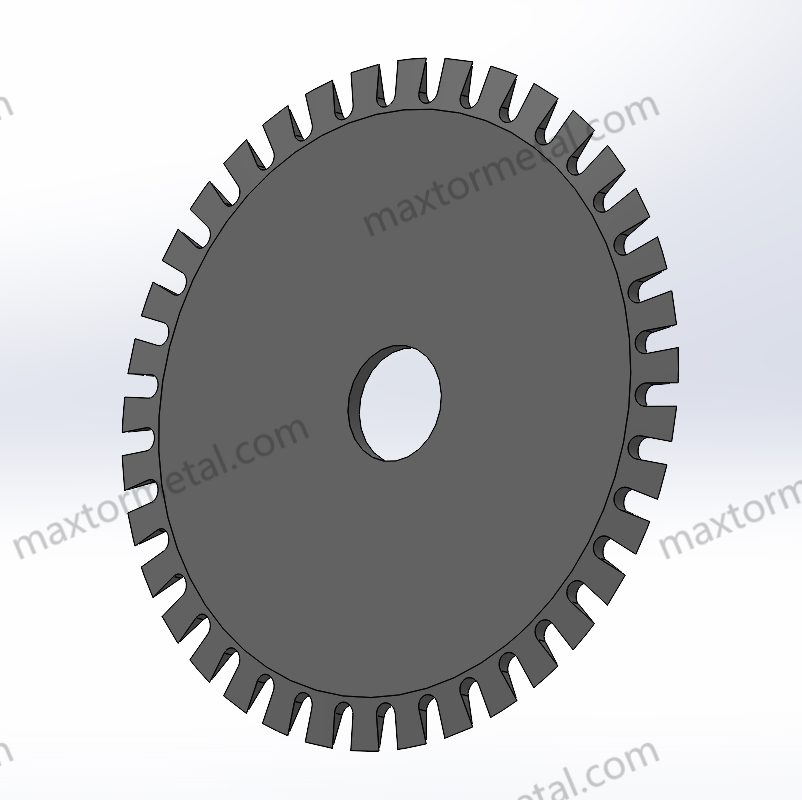
Film Slitting
Film slitting needs blades that make smooth, clean cuts fast. Factories cut thin plastic films and packaging. The blade must stay sharp and not wear out quickly. It should also not build up static. Picking the right material and coating is very important.
Recommended Material and Coating Combinations
The best materials for film slitting are tungsten carbide, high-speed steel, and hardened steel. These materials are hard and tough. They do not wear out fast. Factories use coatings like Titanium Nitride (TiN), Titanium Aluminum Nitride (TiAlN), and Diamond-Like Carbon (DLC). These coatings help blades last longer and cut smoother.
Performance Requirement | Descrizione |
---|---|
Durezza | Keeps the blade sharp for clean film cuts |
Robustezza | Stops the blade from chipping or breaking |
Resistenza all'usura | Makes the blade last longer in busy work |
Ductility | Lets the blade bend a bit without breaking |
Purity | Makes sure the blade works the same every time |
Materiale | Application and Benefits |
---|---|
Carburo di tungsteno | Very strong, cuts tough films, lasts long |
Acciaio ad alta velocità | Good mix of hard and tough, works well |
Acciaio temprato | Heat-treated to be strong and last longer |
Tipo di rivestimento | Vantaggi principali | Quantified Improvement |
---|---|---|
Nitruro di titanio (TiN) | Makes blades harder, lowers friction | Up to 45% less wear |
Titanium Aluminum Nitride (TiAlN) | Handles heat, fights rust, lasts longer | Works well at high speeds |
Carbonio simile al diamante (DLC) | Cuts smoother, stops sticking | Can cut force by over 50% |
Rivestimenti ceramici | Hard, non-metal, fights rust and wear | Good for wet or rough jobs |
Multi-layer Nano Coatings | Many thin layers, less friction | Makes blades last longer and cut better |
Changing blade shape and edge can make blades last up to 40% longer. It can also cut maintenance time by 30%. Factories can make 15-25% more products and waste less material, dropping waste from 5% to 2%.
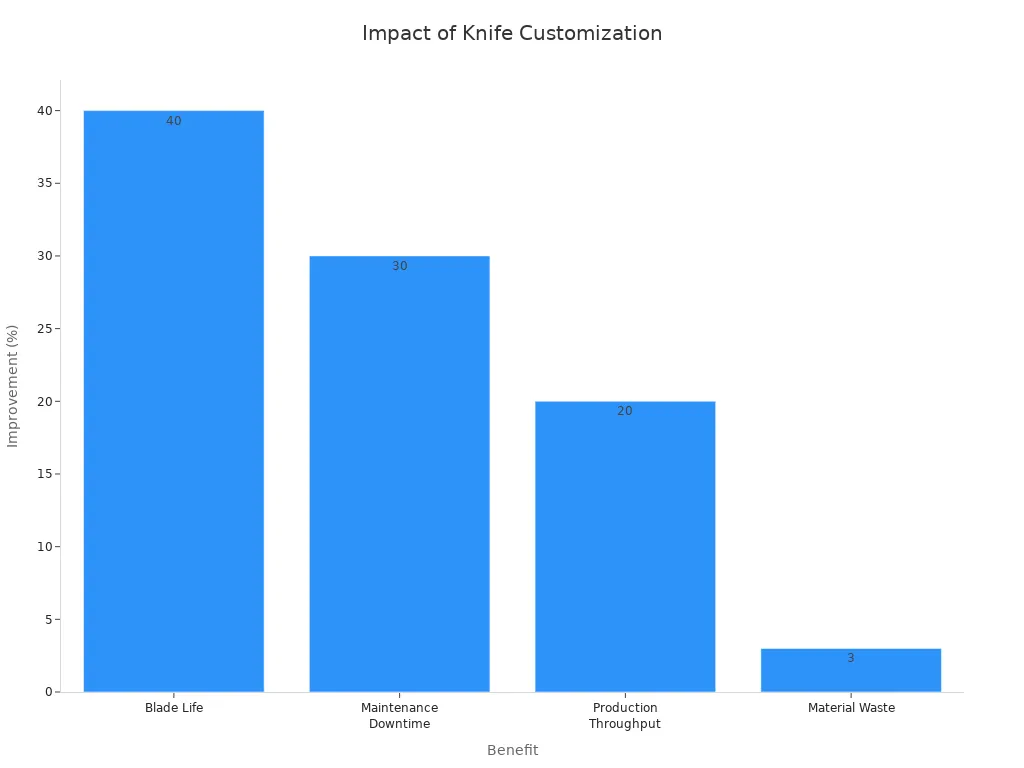
Top Recommendations:
- HSS with TiN coating: Great for fast film cutting, less friction and sticking.
- Tungsten carbide with DLC coating: Best for tough or layered films, lasts longest.
- Multi-layer nano coatings: Helps with special films, makes blades more exact and last longer.
Tip: Factories should match blade height and speed to the film. A 5 mm blade height and 370 rpm speed often work best.
Rubber Slitting
Rubber slitting is hard on blades. Rubber is thick and stretchy. It can stick to the blade and cause problems. Blades must not gum up, must stay sharp, and must handle lots of rubbing. The right material and coating help blades last and cut better.
Recommended Material and Coating Combinations
Tungsten carbide and high-speed steel are best for rubber slitting. These materials are tough and keep their edge. Coatings like DLC and TiAlN help blades not stick and last longer.
Materiale | Benefits for Rubber Slitting |
---|---|
Carburo di tungsteno | Cuts rough rubber, stays sharp, does not wear out fast |
Acciaio rapido (HSS) | Tough and not too costly, good for most rubber jobs |
Acciaio per utensili D2 | Very hard, good for less rough rubber |
Coating | Vantaggio chiave |
---|---|
DLC | Stops sticking, lowers friction, makes blades last longer |
TiAlN | Handles heat, helps blades last in tough jobs |
Stagno | Good for normal rubber jobs, balances cost and work |
Top Recommendations:
- Tungsten carbide with TiAlN coating: Best for cutting rough, tough rubber.
- HSS with TiN coating: Good for most rubber jobs, saves money and lasts.
- Tungsten carbide with DLC coating: Great for sticky or high-friction rubber.
Note: The right blade and coating mean fewer blade changes and smoother work.
Nonwovens and Textiles
Cutting nonwovens and textiles needs blades that stop fraying and make neat cuts. These materials can be soft, fake, or layered. The blade must stay sharp and not pull at the fibers.
Recommended Material and Coating Combinations
Factories use D2 tool steel, M2 high-speed steel, tungsten carbide, and ceramic for these jobs. These materials are very hard and keep their edge. Coatings like TiN, TiCN, TiAlN, and DLC help blades last longer and cut better.
Material / Coating | Proprietà chiave | Benefits for Nonwoven/Textile Cutting |
---|---|---|
Acciaio per utensili D2 | Very hard, fights wear | Blades last long and stay sharp |
M2 High-Speed Steel (HSS) | Hard and tough | Good for tough textile jobs |
Carburo di tungsteno | Super hard, fights wear | Lasts longer, cuts rough materials cleanly |
Ceramica | Very hard, low friction | Makes neat cuts, less heat and wear |
Nitruro di titanio (TiN) | Harder, fights wear | Blades last longer, cuts stay neat |
Carbonitruro di titanio (TiCN) | Fights wear very well | Blades last longer in tough jobs |
Titanium Aluminum Nitride (TiAlN) | Handles heat well | Stays hard in fast cutting |
Carbonio simile al diamante (DLC) | Very hard, low friction | Less friction and wear, blades last longer |
Chrome Plating | Fights rust, smooth finish | Protects blade, less friction |
- Use strong steel and carbide for blades that last.
- Blades are made sharp and smooth to stop fraying.
- Factories can get custom blades for special jobs.
- Careful making of blades means neat, even cuts.
- Special knives are made for nonwovens and textiles, like straight, round, or toothed shapes.
- Blade edge shape and tight rules help stop fraying and make good cuts.
Top Recommendations:
- Ceramic blades: Stay sharp and make clean cuts, great for soft or fake fibers.
- HSS with TiN coating: Lasts longer and stops fiber pulling, good for fast textile work.
- Tungsten carbide with DLC coating: Best for rough nonwovens and long jobs.
Domande frequenti
Which circular blade material is best for cutting multilayer film?
Tungsten carbide or HSS blades with a thin, sharp edge are best for multilayer film. They make clean cuts and waste less.
Can TiCN coating outperform TiN in high-speed slitting?
TiCN coatings are harder and last longer than TiN. They are great for fast and tough cutting.
How do custom blades help in textile and nonwoven cutting?
Custom blades make better cuts, stop fraying, and lower downtime. Factories get better results and save on fixing costs.
Paper and Foil
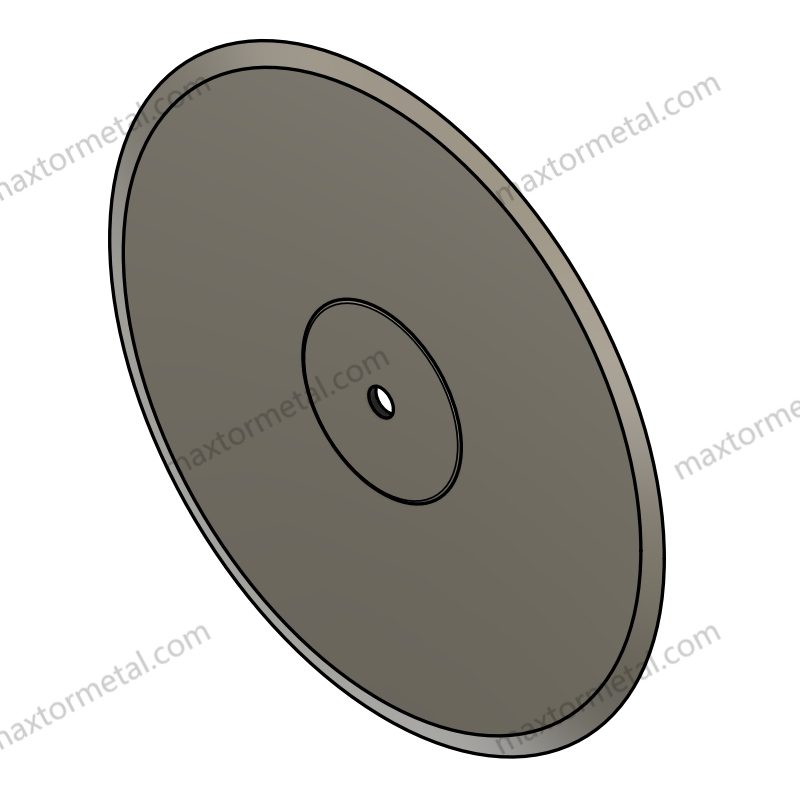
Recommended Material and Coating Combinations
Cutting paper and foil is tricky. Workers need to stop dust, keep blades sharp, and make clean cuts for a long time. Picking the right blade material and coating helps blades work better and saves money.
- D2 steel blades are good for many jobs and do not cost much. They are easy to sharpen and last a long time when cutting paper or plastic.
- M2 steel blades are even tougher. They work well with rough paper and last longer, so workers do not have to stop as much.
- CPM 10V steel is super tough and does not wear out fast. It is best for cutting many layers or rough materials and can be used for a long time.
- Carbide inlay blades stay sharp all day and night. They are great for rough paper and foil and help workers change blades less often.
- Split bottom knives let workers change blades quickly. This means they do not have to take out the whole set, so work does not stop for long.
- Making the blade edge between 10 and 20 micrometers keeps it sharp and strong. This helps make less dust and makes blades last longer.
- Coatings like Titanium Nitride (TiN) and Diamond-Like Carbon (DLC) make blades harder and smoother. These coatings help blades last longer and cut better.
- Setting the nip point right and using strong blade holders is important. This stops blades from wearing out too fast and keeps them sharp.
A paper company used a blade with a 20 micrometer edge and saw blades last 25% longer. Their cuts got 15% better. Other reports show 20% fewer blade changes and 18% less dust with a 15–20 micrometer edge.
Best Practices for Paper and Foil Slitting:
- Pick D2 or M2 steel for most paper and foil jobs.
- Use CPM 10V or carbide inlay blades for rough or layered materials.
- Put TiN or DLC coatings on blades to help them last and cut better.
- Keep blades sharp to stop dust and avoid losing products.
- Teach workers how to set up and care for blades to get the best results.
Materiale della lama | Vantaggio chiave | Typical Use Case |
---|---|---|
D2 Steel | Good for many jobs, easy to sharpen | Cutting paper or plastic |
M2 Steel | Tough, lasts longer | Rough paper, coated paper |
CPM 10V | Super tough, lasts longest | Many layers, rough materials |
Carbide Inlay | Stays sharp, works all day | Rough paper or foil |
Coating | Beneficio |
---|---|
Stagno | Makes blades harder, less friction |
DLC | Blades last longer, cleaner cuts |
Tip: Always check if blade holders are tight and set right. This keeps blades sharp and makes less dust.
Domande frequenti
- Which blade material is best for long paper slitting runs?
CPM 10V or carbide inlay blades last the longest and work best for long jobs. - How can operators reduce dust during foil slitting?
Use blades with a 15–20 micrometer edge and put on TiN or DLC coatings to make less dust and get better cuts.
Other Industries
Recommended Material and Coating Combinations
Many jobs need special blades and coatings. Picking the right one helps machines work better, keeps people safe, and makes good products.
- Lame in acciaio inossidabile are best for food jobs. They do not rust and are safe to use with food.
- Tool steel blades are strong and tough. They are good for cars and metal work because they stay sharp even when used a lot.
- Carbon steel blades are hard and keep their edge. They are used for cutting metal, paper, and plastic.
- Special materials like solid carbide, ceramic, CPM 10V, 52100, M-2, and D-2 steels are very hard and can take heat. They are good for tough jobs like cutting fiberglass, composites, or medical things.
- Coatings like TiN, DLC, and PTFE help blades stay sharp and last longer. These coatings are great for sticky or rough materials.
- Different edge shapes, like Standard V, Vari-Depth V, Hi/Low V, Scalloped, Peg Style, and Slant Tooth, help blades cut better and make machines work easier.
- Custom blades and picking the right material help with special jobs and tough cuts.
Industria | Recommended Blade Material/Coating | Vantaggio chiave |
---|---|---|
Lavorazione alimentare | Stainless Steel, PTFE Coating | Does not rust, safe for food |
Automotive/Metal | Tool Steel, DLC/TiN Coating | Tough, does not wear out fast |
Plastics/Composites | Solid Carbide, Ceramic, DLC Coating | Very hard, makes clean cuts |
Medical/Hygiene | Ceramic, Stainless Steel | Safe, does not react with chemicals |
Fiberglass/Advanced | CPM 10V, Carbide, Protective Coating | Lasts long, stays sharp, takes heat |
Note: Custom blades help factories do their jobs better, save time, and stop machines from breaking down.
Nanjing Metal is a top maker of industrial circular knives with over 20 years of experience. The company is known for its skilled team and good designs. Nanjing Metal makes custom blades for many different jobs. People can look at custom blade choices with this custom blade services link.
Domande frequenti
- Which blade material is best for food processing?
Stainless steel with a PTFE coating is best because it is safe and does not rust. - What is the best option for cutting fiberglass or composites?
CPM 10V or solid carbide blades with coatings last long and stay sharp. - How do custom blades help in specialized industries?
Custom blades fit each job, make better cuts, and help machines run longer.
Selection Guide
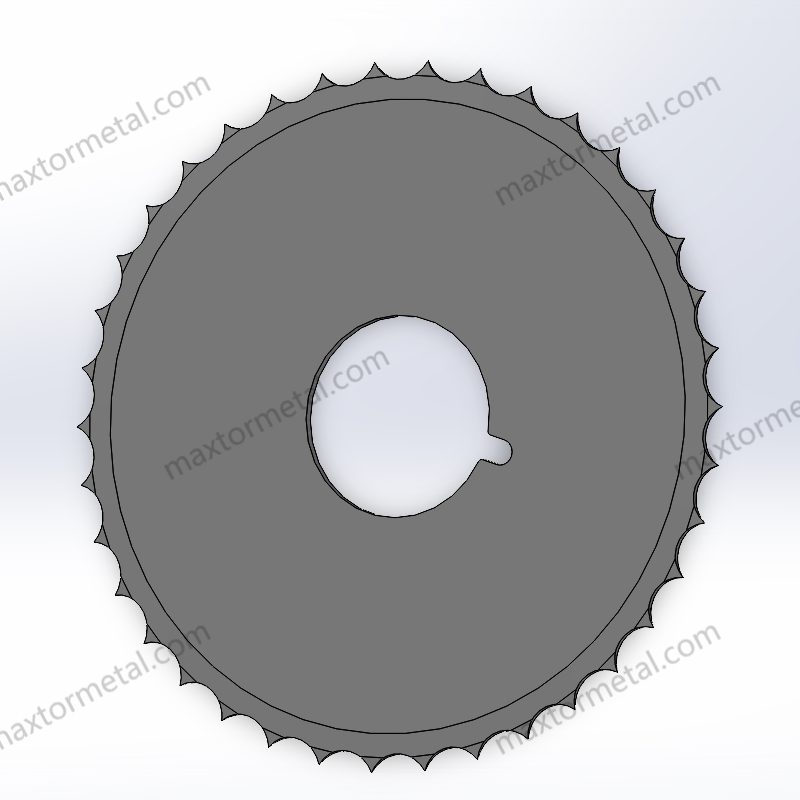
Material Matching
To pick the right blade material, you first need to know what you are cutting. Every material is different and changes how the blade works. Here is a simple way to match the blade to the job:
- Assess the Material to Be Cut
Find out what you are cutting. Check if it is thick, thin, soft, or hard. Soft plastics, rough composites, and sticky rubber all need different blades. - Define the Application Requirements
Decide what the blade will do. Will it slit, score, slice, or make holes? Each job needs a different kind of blade. - Select the Blade Material
- Pick high-carbon steel if you need a strong blade for lots of use.
- Use stainless steel if the blade will get wet or touch food, because it does not rust.
- Choose solid carbide for very hard jobs, like cutting rough or layered films.
- Go with ceramic if you want a blade that does not need to be changed much, or if you cut things for medical or clean jobs.
- Choose the Edge and Tooth Geometry
Match the edge shape to what you are cutting. A square edge is good for most jobs. Scalloped or slant tooth edges work better for soft or stringy things. - Consult with Experts or Manufacturers
Talk to engineers or the blade maker if you are not sure. They can help you pick or design a special blade. - Reverse Engineer When Replacing Blades
If you are changing an old blade, look at how it wore out. This helps you pick a better blade next time.
Tip: Always think about where the blade will be used. Heat, water, and chemicals can change how long a blade lasts.
Edge Type Choice
The edge type decides how the blade cuts. Picking the right edge makes cuts cleaner, wastes less, and helps the blade last longer. Here are some common edge types and what they are best for:
Tipo di bordo | Descrizione | Il migliore per |
---|---|---|
Square Edge | Flat and sharp | Slitting, paper, film |
Singolo smusso | One side slanted, one side flat | Careful cuts, thin things |
Double Bevel | Both sides slanted | Tough stuff, rubber, foam |
Serrated/Toothed | Saw-like teeth | Textiles, nonwovens, hard jobs |
Smerlato | Rounded teeth, smooth cut | Soft things, food, foam |
Dente obliquo | Angled teeth for tough jobs | Thick or stringy things |
- Use square or single-bevel edges for neat, straight cuts in films and foils.
- Pick double-bevel or toothed edges for thick or rough things.
- Choose scalloped or slant tooth edges for soft, stretchy, or stringy stuff.
Note: The wrong edge can make cuts messy or cause dust. Always match the edge to what you are cutting.
Coating Selection
Blade coatings help blades last longer and cut better. The right coating makes blades smoother, harder, and keeps them from rusting. Here is how to pick the best coating:
- Identify the Main Cutting Challenge
Figure out what is hardest about the job. Is it wear, sticking, heat, or rust? - Select a Coating Based on Need
- Use Titanium Nitride (TiN) to make blades last longer and cut smoother, especially for fast or tough jobs.
- Pick Diamond-Like Carbon (DLC) for extra hardness and to stop sticky stuff from building up.
- Try nano-coatings if the blade gets hot and cold a lot, because these coatings protect against heat changes.
- Match Coating to Blade Material
Put DLC on tungsten carbide for hard jobs. Use TiN on High-Speed Steel for softer things. - Maintain Blades Properly
Clean, oil, and store blades the right way to keep coatings working well. - Consider Custom Solutions
If you have a special job, ask the blade maker for custom coatings or blade shapes.
Picking the right coating and making blades carefully keeps them sharp and working well, even in tough places.
Domande frequenti
- What is the most important factor when matching blade material to the application?
The most important thing is what you are cutting, like how hard, rough, or wet it is. - How does edge type affect blade life?
The right edge shape helps the blade last longer and makes better cuts, so you do not have to fix it as much. - Can coatings really make a difference in blade performance?
Yes. The right coating can make blades last up to half again as long, cut smoother, and stop sticking or rust.
Cost vs. Performance
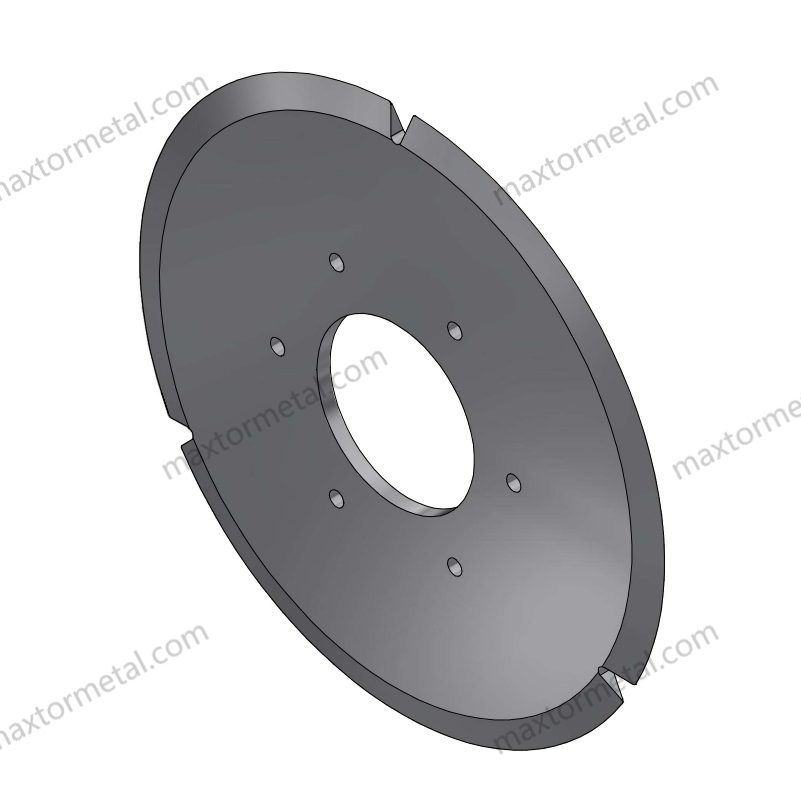
Picking the right blade is about more than price. You have to think about what you pay now and what you save later. Some people only look at the price tag. But the real cost comes from how often you change blades, how much time machines stop, and how much fixing is needed. The best blade depends on the job, what you are cutting, and where you work.
Comparing Material Investments
Each blade material has its own cost and how well it works:
- Acciaio ad alto tenore di carbonio: This blade costs less at first. But it wears out fast. You will need to buy new blades a lot, which costs more over time.
- Acciaio inossidabile: This blade costs more when you buy it. It does not rust and works well in wet or chemical places. It lasts longer, so you save money later.
- Acciaio legato: These blades cost more at the start. They last longer and help machines run without stopping. They are good for busy factories.
- Lame in Ceramica: These blades cost the most at first. They almost never need fixing and last a long time. If you need careful and fast work, they are the best value in the long run.
Material Cost-Benefit Table
Materiale della lama | Costo iniziale | Frequenza di sostituzione | Esigenze di manutenzione | Valore a lungo termine |
---|---|---|---|---|
Acciaio ad alto tenore di carbonio | Basso | Alto | Alto | Basso |
Acciaio inossidabile | Medio | Medio | Basso | Medium-High |
Acciaio legato | Alto | Basso | Basso | Alto |
Ceramica | Molto alto | Very Low | Very Low | Highest |
Tip: Spending more at first can mean fewer blade changes, less machine stopping, and lower total costs later.
The Impact of Advanced Treatments
Special blade treatments can change cost and how long blades last. Cryogenic treatment is one example. It makes blades last longer and wear out slower. The table below shows the difference:
Aspetto | Trattamento termico regolare | Cryogenically Treated |
---|---|---|
Resistenza all'usura (cicli) | 1,000 | 2,500 |
Durata media della vita (mesi) | 6 | 12 |
Tasso di usura (mm³/ora) | 0.15 | 0.05 |
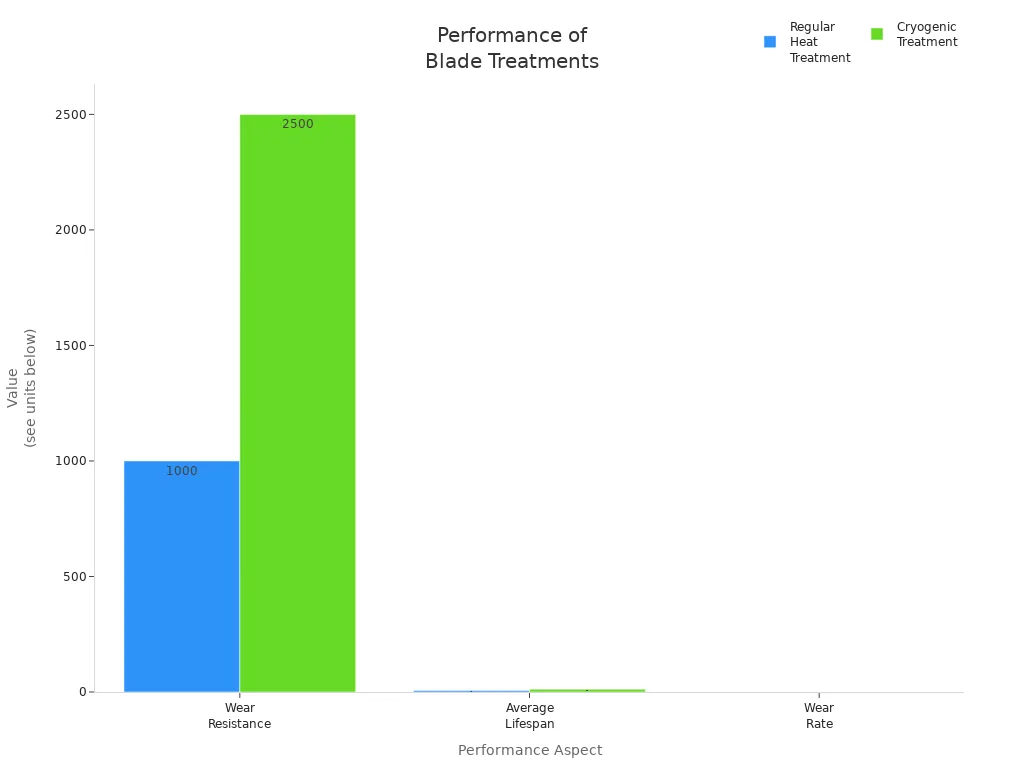
Cryogenic treatment can make blades last twice as long. It also makes them wear out slower. This can lower total costs by up to 30%. You will need fewer new blades and less fixing, so you can make more products and waste less.
Mistakes to Avoid
- Only looking at the lowest price can cost more later.
- Not thinking about the work area (like wet, chemicals, or sand) can make blades wear out fast.
- Not using special coatings or treatments can mean more downtime and more waste.
Tips for Maximizing Value
- Pick the blade material that fits your job and work area.
- Buy coatings or treatments that help your factory.
- Keep track of how long blades last and when you change them. This helps you find ways to save money.
Why Manufacturer Expertise Matters
A good blade maker can help you pick the best blade. Nanchino Metal is a top maker with 20 years of experience. Their team makes custom blades for many jobs. They offer custom blade services to help you get the most for your money.
For advice or to talk about your needs, contact Nanjing Metal’s sales engineers with this contact link.
Domande frequenti
How does blade material affect total cost of ownership?
Blade material changes how often you need new blades and how much time machines stop. Harder blades cost more at first but save money later.
Is cryogenic treatment worth the extra cost?
Yes. Cryogenic treatment can make blades last twice as long and wear out less, so you spend less on new blades and fixing.
When should a company choose ceramic blades?
Ceramic blades are best for careful, fast jobs where you want blades to last a long time and not need much fixing.
Picking the right material, edge style, and coating changes how well industrial circular knives work. When companies match blade hardness and edge type to what they are cutting, blades last longer and work better. This means fewer blade changes and more work done.
Fattore | How It Helps the Blade |
---|---|
Materiale | Makes blades last and stops rust |
Edge Style | Helps make clean cuts and fits the job |
Coating | Blades last longer, need less fixing |
To get the best results, people should:
- Tell suppliers all about what they need and any cutting problems.
- Try out sample blades before buying a lot.
- Ask experts for help making special blades for tricky jobs.
Domande frequenti
What is the best industrial circular knife material for slitting multilayer film?
Tungsten carbide or high-speed steel blades with a sharp, thin edge make the cleanest cuts in multilayer film. These materials do not wear out fast and keep their sharp edge even when cutting quickly.
Can TiCN coating last longer than TiN in high-speed cutting?
Yes. TiCN coatings are harder and fight wear better than TiN. This means they are great for fast cutting jobs where you want blades to last longer.
How does edge style affect cutting performance?
Edge style changes how well a blade cuts and how neat the cut is. A single-bevel edge makes very clean cuts in thin things. Serrated or toothed edges work better for tough or stringy things. They help the blade move easier and make cuts more even.
When should a company choose ceramic blades?
Ceramic blades are best when you need blades to stay sharp for a long time and not react with chemicals. They are great for hygiene, medical, and food jobs where changing blades often is hard.
What are the main benefits of using coated circular knives?
Coated blades last longer, slide smoother, and do not rust. Coatings like DLC or TiN stop sticky stuff from building up and help blades last longer between changes. This saves money and helps workers get more done.
How can custom industrial knives improve production efficiency?
Custom blades are made for special jobs and materials. They help make better cuts and stop machines from stopping as much.
Vedi anche
Trova le Lame di Granulazione Perfette per le Tue Esigenze di Lavorazione della Plastica
I 10 migliori consigli per far durare più a lungo le lame del tuo rasoio circolare
Cosa sono i coltelli Crush Cut e come funzionano nell'industria
Come scegliere le lame per taglierine circolari giuste per prestazioni durature